Home>Articles>What Is Used To Cool An Air-To-Air Charge Air Cooler?
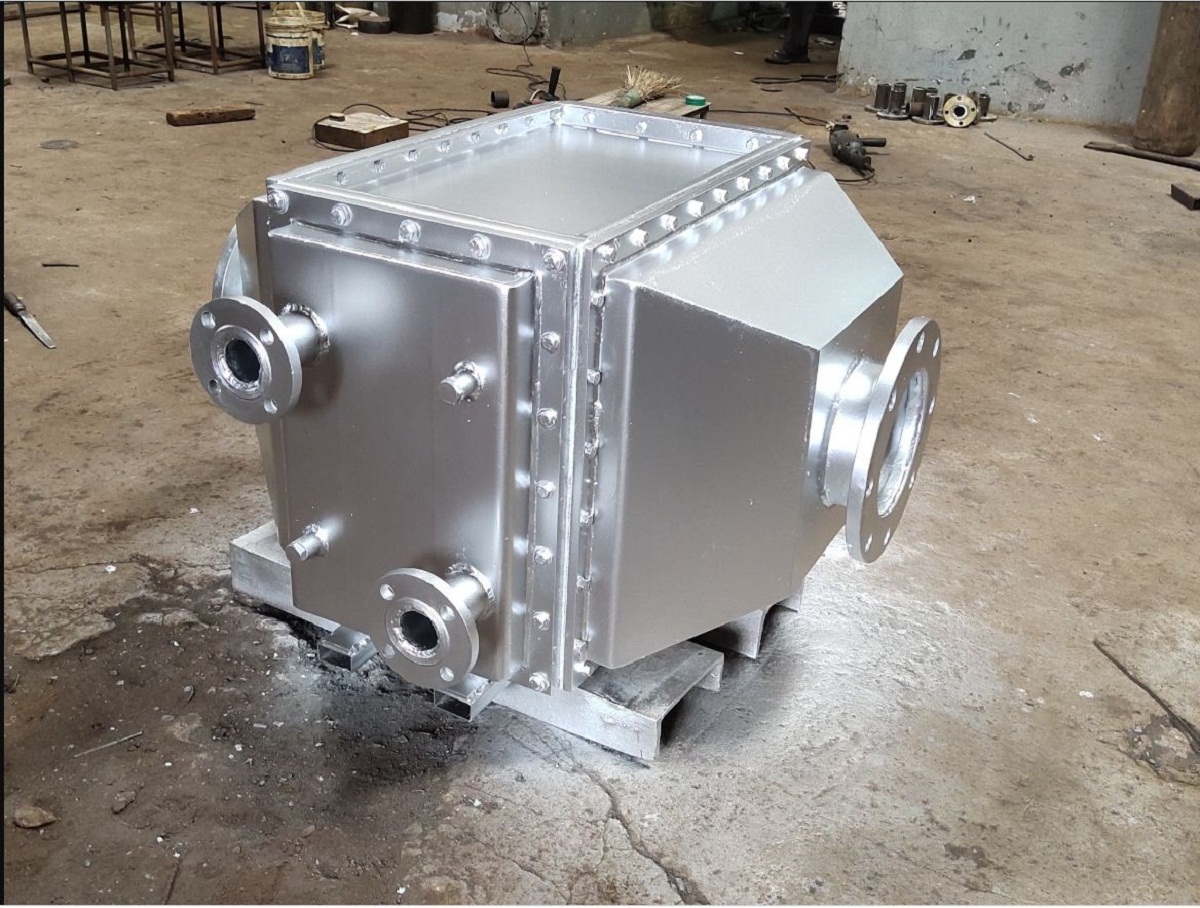
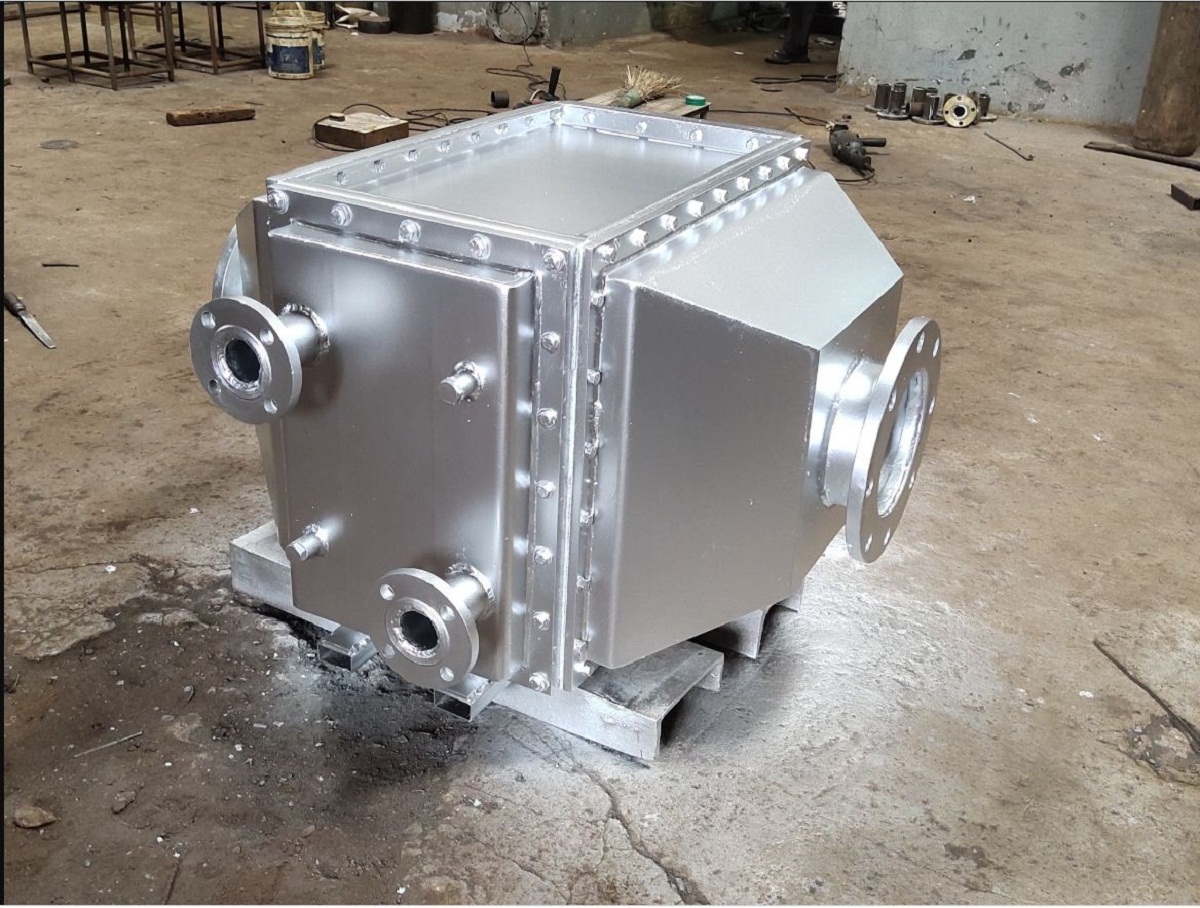
Articles
What Is Used To Cool An Air-To-Air Charge Air Cooler?
Modified: December 6, 2023
Discover the top articles on what is used to cool an air-to-air charge air cooler. Learn about the different cooling methods and techniques used in these systems.
(Many of the links in this article redirect to a specific reviewed product. Your purchase of these products through affiliate links helps to generate commission for Storables.com, at no extra cost. Learn more)
Introduction
When it comes to cooling an air-to-air charge air cooler, there are several options that can be used effectively. The proper cooling of these components is essential to ensure optimal performance and prevent overheating. In this article, we will explore the various methods used to cool an air-to-air charge air cooler and take a closer look at the different types of cooling mediums that can be employed.
An air-to-air charge air cooler, also known as an intercooler, is an essential component in high-performance engines, particularly in turbocharged or supercharged applications. Its primary function is to cool the compressed air before entering the engine’s intake manifold. This cooling process increases air density, leading to improved combustion efficiency and increased power output.
To achieve efficient cooling, it is crucial to select the appropriate cooling medium. In the case of air-to-air charge air coolers, the cooling medium is none other than… air itself. Air has proven to be an excellent cooling medium due to its abundance, accessibility, and ability to dissipate heat effectively.
There are different types of air-to-air charge air coolers available in the market, such as air-to-air intercoolers, air-to-air aftercoolers, and air-to-air heat exchangers. These coolers vary in design and application but share the same fundamental principle of cooling compressed air using ambient air.
Heat transfer plays a crucial role in air-to-air charge air cooling. It involves the transfer of thermal energy from the hot compressed air to the cooler ambient air. This transfer is accomplished through conduction, convection, and radiation mechanisms.
Now, let’s delve deeper into the various cooling methods that can be employed to cool an air-to-air charge air cooler.
Key Takeaways:
- Air serves as the ideal cooling medium for air-to-air charge air coolers due to its abundance, thermal properties, and natural convective flow, making it a reliable and efficient choice for cooling applications.
- Combining liquid cooling and air cooling through a hybrid system can optimize heat dissipation and temperature control, offering enhanced cooling capacity, improved temperature regulation, and increased flexibility.
Read also: 13 Amazing Air Cooler Fan for 2024
Air as a Cooling Medium
When it comes to cooling an air-to-air charge air cooler, air itself serves as the primary cooling medium. Air has several advantages that make it an ideal choice for cooling applications. Firstly, it is readily available and abundant in the environment. This makes it a cost-effective option as there is no need for external equipment or fluid circulation systems.
Air is also an excellent conductor of heat. It has a relatively low thermal conductivity, which allows it to efficiently absorb and carry away heat from hot surfaces. This property is essential in cooling applications where the goal is to transfer heat from a higher temperature source, such as compressed air, to a lower temperature sink, such as ambient air.
In addition to its thermal conductivity, air relies on the process of convection to aid in heat transfer. As hot air comes into contact with a cooler surface, it absorbs the heat and rises, creating a natural flow that facilitates convective heat transfer. This flow of air promotes cooling by continuously introducing fresh, cooler air to the charge air cooler, helping to dissipate heat and maintain optimal operating temperatures.
Air is also a relatively safe and environmentally friendly cooling medium. Unlike liquid coolants, there is no risk of leaks or spills, which can lead to damage or contamination. Additionally, air does not pose the same concerns regarding disposal or environmental impact.
However, air also has its limitations as a cooling medium. Its effectiveness depends on the ambient temperature and humidity levels. In hot and humid conditions, the cooling capacity of air decreases, reducing the overall efficiency of the charge air cooler. This is why it is essential to consider the operating environment and potential ambient temperature fluctuations when designing and selecting air-to-air charge air cooling systems.
Overall, air serves as an excellent cooling medium for air-to-air charge air coolers. Its accessibility, thermal properties, and natural convective flow make it a reliable and efficient choice for cooling applications. When combined with proper design considerations, air cooling can effectively dissipate heat from the compressed air, ensuring optimal performance and longevity of the charge air cooler.
Types of Air-to-Air Charge Air Coolers
Air-to-air charge air coolers come in various designs and configurations, each tailored to specific applications and requirements. Understanding the different types of charge air coolers can help in selecting the most suitable option for a particular engine or system. Let’s explore some of the common types of air-to-air charge air coolers:
- Air-to-Air Intercoolers: Air-to-air intercoolers are the most widely used type of charge air cooler. They are typically positioned between the turbocharger or supercharger outlet and the engine intake. These intercoolers use ambient air to cool down the compressed air from the forced induction system before it enters the engine. They have a core design consisting of tubes or fins that increase the heat transfer surface area. Air-to-air intercoolers are lightweight, cost-effective, and relatively easy to install.
- Air-to-Air Aftercoolers: Air-to-air aftercoolers, also known as post-coolers, are similar to intercoolers in function. However, they are used in applications where the compressed air is only cooled after it has gone through the primary cooling process. Aftercoolers are often employed in multi-stage forced induction systems, particularly in heavy-duty diesel engines, to further reduce the temperature of the compressed air before it enters the engine. They are typically larger in size and provide additional cooling capacity.
- Air-to-Air Heat Exchangers: Air-to-air heat exchangers are more versatile and can be used for both cooling and heating applications. These coolers consist of a heat exchanger core that can transfer thermal energy between two air streams. In charge air cooling systems, one air stream carries the compressed hot air from the turbocharger, while the other air stream provides the cooling medium. The heat exchanger core facilitates efficient heat transfer between the two streams, effectively cooling down the charge air. Air-to-air heat exchangers are widely used in applications where precise temperature control is required, such as in industrial processes or specialized engine systems.
Each type of air-to-air charge air cooler has its advantages and considerations in terms of cooling efficiency, space requirements, and cost. It is crucial to evaluate the specific requirements of the engine or system and choose the appropriate cooler type that best meets those needs.
In the next section, we will explore the heat transfer mechanisms involved in air-to-air charge air cooling and how they contribute to efficient cooling of the compressed air.
Heat Transfer in Air-to-Air Charge Air Coolers
Heat transfer is a fundamental process in air-to-air charge air cooling. It involves the transfer of thermal energy from the hot compressed air to the cooler ambient air. Understanding the mechanisms of heat transfer can help optimize the design and efficiency of air-to-air charge air coolers.
There are three primary mechanisms of heat transfer in charge air coolers: conduction, convection, and radiation.
Conduction: Conduction is the transfer of heat through direct contact between particles or solids. In charge air coolers, conduction occurs when the hot compressed air comes into contact with the cooler surfaces of the heat exchanger core. The heat from the hot air is conducted through the core material, such as metal fins or tubes, and transferred to the cooler ambient air on the other side. The efficiency of conduction depends on the thermal conductivity of the materials used in the heat exchanger core.
Convection: Convection is the transfer of heat through the movement of fluids or gases. In charge air coolers, convection is a vital mechanism as it aids in the cooling process. As the hot compressed air flows through the cooler, it heats up the adjacent air molecules, causing them to rise. This creates a natural flow of air and promotes convective heat transfer. The hotter air rises, while cooler air replaces it, continuously removing heat from the charge air cooler. This convective flow helps maintain a temperature gradient and enhances the cooling efficiency of the cooler.
Radiation: Radiation is the transfer of heat through electromagnetic waves. While radiation plays a minor role in air-to-air charge air cooling compared to conduction and convection, it should not be neglected. Heat can be radiated from the surfaces of the charge air cooler to the surrounding environment. The emission and absorption of thermal radiation depend on the temperature and emissivity of the surfaces involved. Careful consideration of the material properties and surface finishes can help maximize or minimize radiative heat transfer in the charge air cooler.
The combination of these heat transfer mechanisms ensures effective cooling of the compressed air in air-to-air charge air coolers. However, it is crucial to consider the design elements that enhance these heat transfer processes. Factors such as increasing the surface area of the heat exchanger core, optimizing the airflow path, and utilizing materials with high thermal conductivity play a significant role in improving the cooling efficiency.
In the next section, we will explore the different cooling methods employed in air-to-air charge air coolers to maximize the cooling performance and maintain the temperature within optimal ranges.
Cooling Methods for Air-to-Air Charge Air Coolers
There are two primary cooling methods used in air-to-air charge air coolers: liquid cooling and air cooling. These methods aim to dissipate heat from the compressed air and maintain the temperature within optimal ranges. Let’s take a closer look at each of these cooling methods:
Liquid Cooling: Liquid cooling involves circulating a coolant, typically water or a mixture of water and coolant additives, through a separate system within the charge air cooler. The coolant absorbs heat from the hot compressed air as it passes through the cooler and carries it away. This method offers the advantage of efficient heat transfer, as liquid coolants have higher heat capacities compared to air. It allows for precise temperature control and can handle high heat loads effectively. However, liquid cooling systems require additional components, such as pumps, radiators, and hoses, which can increase complexity, maintenance requirements, and cost.
Air Cooling: Air cooling, as the name suggests, relies solely on the ambient air to remove heat from the charge air cooler. The hot compressed air flows through the cooler, and the surrounding airflow absorbs the heat, cooling down the air. This method is simple, cost-effective, and does not require additional components. However, it is highly dependent on ambient conditions such as temperature, humidity, and airflow. In hot and humid environments, the cooling capacity of air decreases, affecting the overall efficiency of the charge air cooler.
It is important to note that liquid cooling and air cooling are not mutually exclusive methods. They can be combined to create hybrid cooling systems that leverage the benefits of both approaches. Hybrid systems can be designed with liquid-cooled cores and additional air cooling provisions, such as fans or ducting, to maximize cooling performance. This combination provides enhanced heat dissipation capabilities while maintaining the advantages of both liquid and air cooling.
Choosing the right cooling method depends on various factors, including the specific application, space availability, ambient conditions, and budget. The decision should be based on a thorough assessment of these factors to ensure optimal cooling performance and efficient operation of the charge air cooler.
In the next section, we will conclude our exploration of air-to-air charge air coolers and summarize the key points discussed.
Using a liquid coolant, such as water or a water-glycol mixture, is commonly used to cool an air-to-air charge air cooler. This coolant absorbs heat from the charged air as it passes through the cooler, helping to lower its temperature.
Read also: 12 Best Fan Cooler for 2024
Liquid Cooling
Liquid cooling is a popular method employed in air-to-air charge air coolers to efficiently dissipate heat from the compressed air. It involves circulating a liquid coolant, typically water or a mixture of water and coolant additives, through a separate cooling system integrated into the charge air cooler.
When the hot compressed air flows through the cooler, the liquid coolant absorbs the heat and carries it away, effectively cooling down the charge air. The coolant passes through coolant passages or tubes within the charge air cooler, which are in direct contact with the hot compressed air, maximizing the transfer of thermal energy from the air to the coolant.
There are several advantages to using liquid cooling in charge air coolers. Firstly, liquid coolants have higher heat capacities compared to air. This means that they can absorb larger amounts of heat per unit volume, resulting in efficient heat transfer. This is particularly beneficial in high-performance or high-heat load applications where there is a need for additional cooling capacity.
Liquid cooling also allows for precise temperature control. By adjusting the flow rate of the coolant or utilizing additional cooling components such as radiators or heat exchangers, the temperature of the charge air can be regulated to maintain optimal operational conditions. This is crucial for achieving consistent performance and preventing overheating of the engine or system.
Another advantage of liquid cooling is its ability to handle high heat loads effectively. The additional heat capacity of the coolant allows for the absorption and dissipation of large amounts of thermal energy. This is especially important in applications where the compressed air is subjected to extreme temperatures or continuous high-demand operations.
However, liquid cooling systems do come with some considerations. They require additional components, such as water pumps, radiators, and hoses, to circulate the coolant within the charge air cooler. This increases the complexity and cost of the cooling system. Maintenance requirements also need to be taken into account, as regular inspection, cleaning, and coolant level checks are necessary to ensure the proper functioning of the liquid cooling system.
In summary, liquid cooling is an efficient and flexible method for cooling air-to-air charge air coolers. It offers higher heat transfer capabilities, precise temperature control, and the ability to handle high heat loads. While there are additional complexities and maintenance considerations, liquid cooling is a valuable option for applications that require optimal cooling performance and temperature regulation.
Air Cooling
Air cooling is a widely used and cost-effective method for cooling air-to-air charge air coolers. It involves utilizing the surrounding ambient air as the cooling medium to dissipate heat from the compressed air.
In air cooling, the hot compressed air from the turbocharger or supercharger passes through the charge air cooler, and the heat is transferred to the surrounding air. The charge air cooler is designed with fins or tubes that increase the surface area, allowing for efficient heat transfer. As the hot air comes into contact with the cooler surfaces, thermal energy is transferred through conduction and convection, resulting in the cooling of the air.
One of the main advantages of air cooling is its simplicity. Unlike liquid cooling systems, air cooling does not require additional components such as pumps, radiators, or coolant circulation. This reduces complexity, maintenance requirements, and overall cost. Air cooling also eliminates the risk of leaks or spills associated with liquid cooling systems, making it a safer and more environmentally friendly option.
Another advantage of air cooling is its reliability. With no dependence on external components, air cooling systems are less prone to failures or malfunctions. The use of air as the cooling medium is also more consistent and stable, as there are no variations in coolant flow or temperature that can impact cooling performance.
However, air cooling does have some limitations. Its effectiveness is highly dependent on ambient conditions, including temperature, humidity, and airflow. In hot and humid environments, the cooling capacity of air decreases, affecting the overall efficiency of the charge air cooler. Lack of proper airflow can also hinder heat dissipation and compromise cooling performance.
To optimize air cooling, several design considerations can be implemented. Ensuring sufficient airflow to the charge air cooler is crucial, and the use of fans or ducting can help enhance cooling efficiency. Utilizing heat exchange surfaces with high thermal conductivity and increased surface area can also improve heat transfer. Regular maintenance, such as cleaning the charge air cooler fins or tubes, is essential to prevent obstructions and maintain optimal airflow and heat transfer.
In summary, air cooling is a cost-effective and reliable method for cooling air-to-air charge air coolers. Its simplicity, safety, and consistency make it a popular choice for various applications. While it is susceptible to ambient conditions, proper design considerations and maintenance can help overcome these limitations and ensure efficient heat dissipation from the compressed air.
Combining Cooling Methods
In some cases, combining different cooling methods can offer enhanced cooling performance and temperature control for air-to-air charge air coolers. By combining the advantages of liquid cooling and air cooling, a hybrid cooling system can be created to optimize heat dissipation and maintain optimal operating conditions.
Hybrid cooling systems typically involve using liquid cooling as the primary method and incorporating additional air cooling provisions. The liquid coolant circulates through coolant passages or tubes within the charge air cooler, absorbing heat from the compressed air. This coolant is then circulated to external components like radiators or heat exchangers, where it exchanges heat with the ambient air.
By incorporating air cooling provisions alongside liquid cooling, the hybrid system benefits from the high heat transfer capabilities of the coolant and the natural convective cooling provided by ambient air. Additional cooling components such as fans or ducts can be included to enhance airflow and increase heat dissipation from the charge air cooler.
The combination of liquid cooling and air cooling in a hybrid system offers several advantages. Firstly, it provides greater cooling capacity by leveraging the superior heat transfer properties of liquid coolants. The liquid coolant can absorb more heat from the compressed air, reducing the overall temperature more effectively compared to air cooling alone.
Secondly, the additional airflow provided by air cooling components enhances convective heat transfer. It helps to remove heat from the coolant and maintain lower overall temperatures, especially in high-demand or high-temperature applications.
Furthermore, the hybrid cooling system allows for greater flexibility and adaptability. The coolant flow rate and cooling provisions can be adjusted to meet specific cooling requirements, allowing for precise temperature control. This is particularly beneficial in applications where maintaining consistent thermal conditions is vital for optimal engine or system performance.
Despite the advantages, hybrid cooling systems do require additional components and more complex design considerations. Proper integration and coordination between the liquid cooling and air cooling components are crucial to ensure efficient heat transfer and avoid potential conflicts or inefficiencies. Maintenance and monitoring of both cooling systems is also important to ensure their proper functioning and to address any issues promptly.
In summary, combining cooling methods through a hybrid cooling system can optimize heat dissipation and temperature control in air-to-air charge air coolers. By leveraging the advantages of liquid cooling and incorporating additional air cooling provisions, the hybrid system offers enhanced cooling capacity, improved temperature regulation, and increased flexibility in meeting specific cooling requirements.
Conclusion
Air-to-air charge air coolers play a crucial role in maintaining the optimal performance and reliability of high-performance engines. Effective cooling of the compressed air is essential to improve combustion efficiency and increase power output. Throughout this article, we have explored the various methods used to cool air-to-air charge air coolers and the importance of selecting the right cooling medium.
Air itself serves as the primary cooling medium in air-to-air charge air coolers. Its abundance, accessibility, and ability to dissipate heat effectively make it an ideal choice. We have discussed the different types of air-to-air charge air coolers, including intercoolers, aftercoolers, and heat exchangers, each suited to specific applications and requirements.
Heat transfer is a fundamental process in air-to-air charge air cooling, involving conduction, convection, and radiation mechanisms. Understanding these mechanisms allows for optimized design and efficient heat dissipation from the compressed air to the surrounding air.
We have also delved into the two primary cooling methods: liquid cooling and air cooling. Liquid cooling offers higher heat transfer capabilities, precise temperature control, and the ability to handle high heat loads, while air cooling is cost-effective, reliable, and easy to implement. The combination of these methods through a hybrid cooling system allows for even greater cooling performance and adaptability.
In conclusion, selecting the right cooling method for an air-to-air charge air cooler depends on several factors, including the specific application, space availability, ambient conditions, and budget. It is crucial to assess these factors and consider the advantages and limitations of each cooling method to ensure optimal cooling performance and maintain the temperature within optimal ranges.
By effectively cooling air-to-air charge air coolers, we can enhance engine performance, reduce the risk of overheating, and prolong the lifespan of the engine. With the right cooling approach in place, air-to-air charge air coolers can deliver improved combustion efficiency, increased power output, and overall enhanced engine performance.
Frequently Asked Questions about What Is Used To Cool An Air-To-Air Charge Air Cooler?
Was this page helpful?
At Storables.com, we guarantee accurate and reliable information. Our content, validated by Expert Board Contributors, is crafted following stringent Editorial Policies. We're committed to providing you with well-researched, expert-backed insights for all your informational needs.
0 thoughts on “What Is Used To Cool An Air-To-Air Charge Air Cooler?”