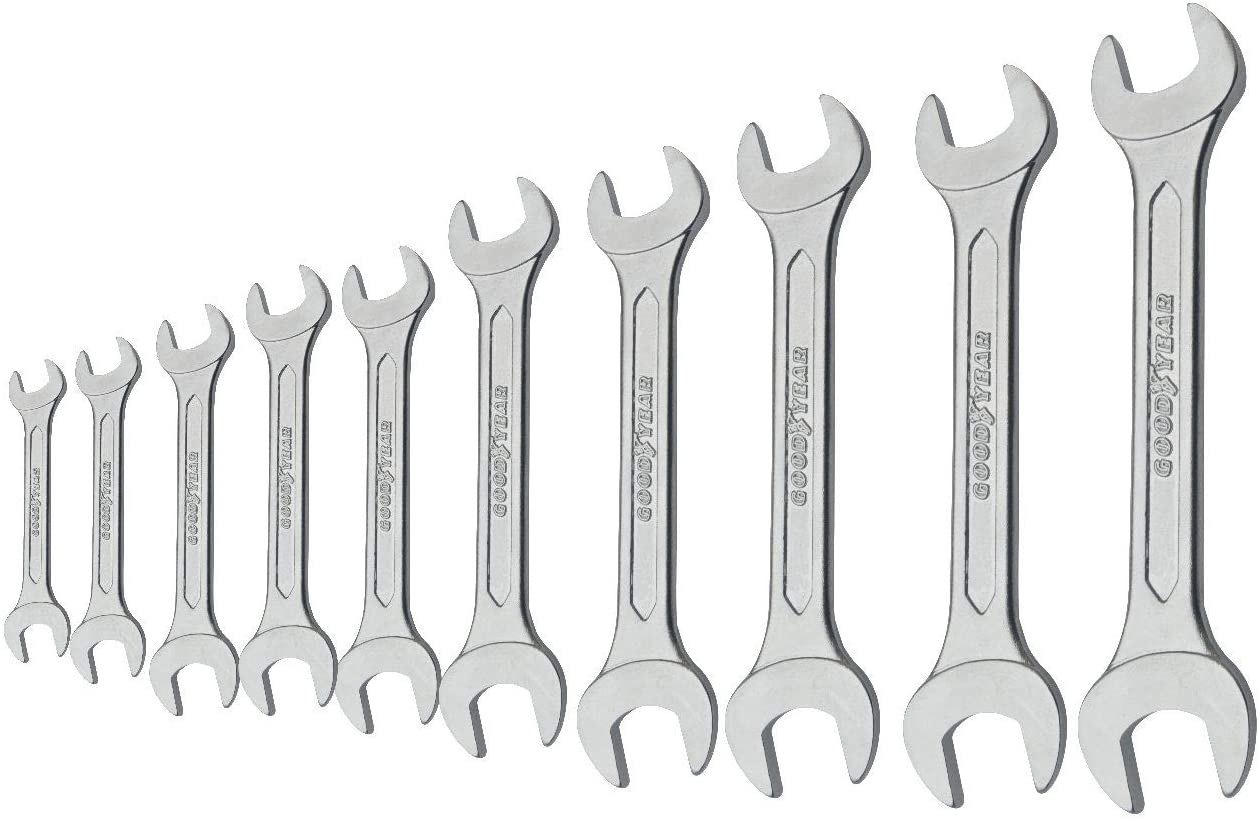
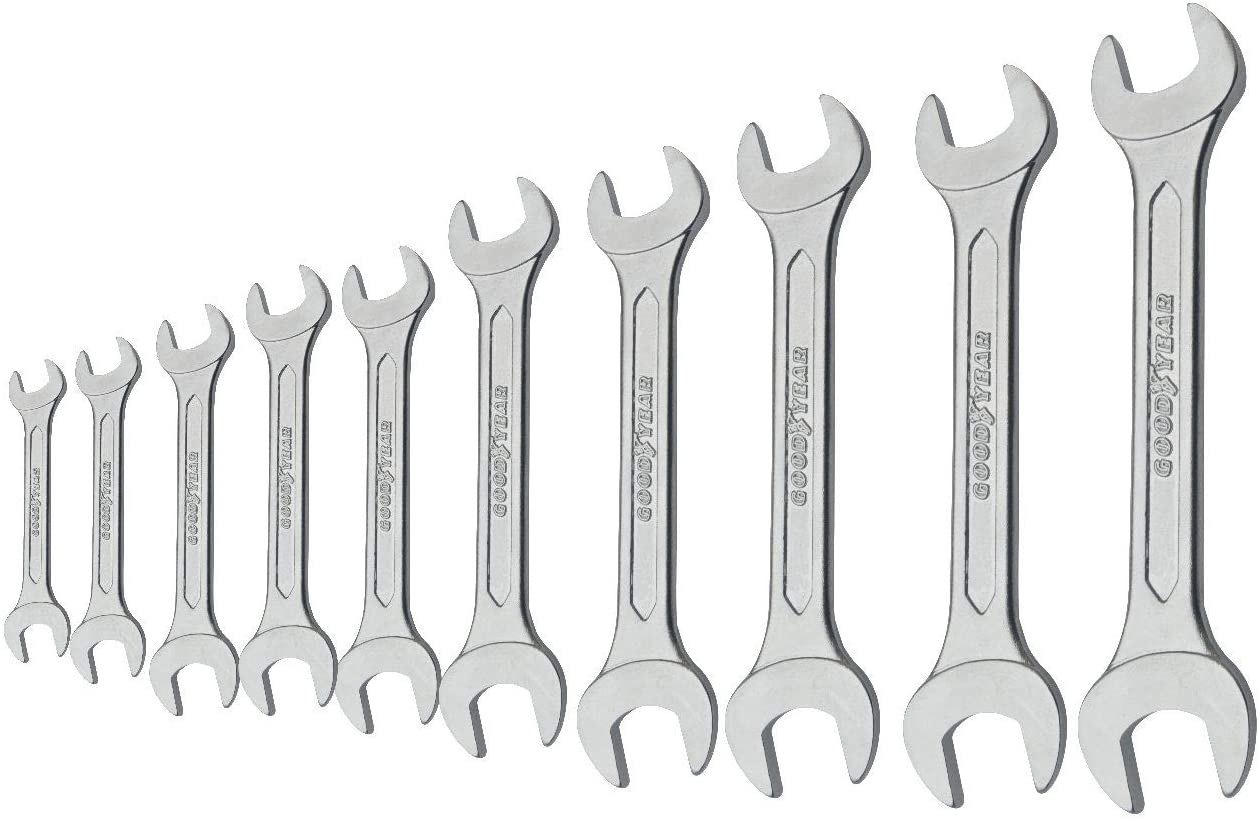
Articles
What Kind Of Steel Is Used In Hand Tools
Modified: December 7, 2023
Discover the different types of steel used in hand tools in this informative article. Learn about the properties and benefits of each steel alloy.
(Many of the links in this article redirect to a specific reviewed product. Your purchase of these products through affiliate links helps to generate commission for Storables.com, at no extra cost. Learn more)
Introduction
Hand tools are essential for various tasks, whether it’s fixing something around the house, woodworking, or working on projects. These tools are designed to be versatile, durable, and reliable, and one crucial factor contributing to their strength and longevity is the material they are made from. In the case of hand tools, steel is the most common material used due to its exceptional properties.
Steel is an alloy consisting primarily of iron with a small percentage of carbon and other elements. With the right combination of these elements and specific manufacturing processes, different types of steel can be created, each with its own unique characteristics and applications.
Understanding the different types of steel used in hand tools can provide valuable insights into their durability, performance, and suitability for specific tasks. Whether it’s carbon steel, alloy steel, high-speed steel, stainless steel, or tool steel, each has its own set of properties and benefits.
In this article, we will explore the various types of steel used in hand tools, their composition, manufacturing processes, and most importantly, the common hand tools made from them. So, let’s dive in and uncover the world of steel and its significance in the realm of hand tools.
Key Takeaways:
- Steel is a versatile material for hand tools, offering unique properties such as strength, durability, and corrosion resistance. Understanding the different types of steel used in hand tools can provide valuable insights into their performance and suitability for specific tasks.
- Heat treatment is crucial in enhancing the properties of steel for hand tools. Techniques such as annealing, normalizing, hardening, tempering, and case hardening allow for precise control over the hardness, toughness, and wear resistance of steel, ensuring optimal performance in various applications.
Read more: What Kind Of Oil Can You Use On Hand Tools
Steel Composition
Steel is primarily composed of iron, which makes up the majority of its composition. However, the addition of other elements in varying quantities gives steel its distinct properties. One crucial element that significantly affects the characteristics of steel is carbon.
Carbon Steel: Carbon steel is a type of steel with the highest carbon content, typically ranging from 0.05% to 2.0%. The higher carbon content makes carbon steel stronger and harder than other types of steel. It is known for its durability and resistance to wear and tear. However, it is not resistant to corrosion, making it susceptible to rust.
Alloy Steel: Alloy steel is made by adding various alloying elements such as manganese, chromium, molybdenum, vanadium, and nickel to the steel. These elements enhance the strength, hardness, and toughness of the steel, making it suitable for high-temperature applications, shock resistance, and improved corrosion resistance.
High-Speed Steel: High-speed steel (HSS) is a type of alloy steel that is specifically designed for high-speed machining and cutting applications. It contains additional elements such as tungsten, cobalt, vanadium, or molybdenum, which give it superior heat resistance, hardness, and wear resistance. HSS is commonly used in drill bits, milling cutters, and other cutting tools.
Stainless Steel: Stainless steel is a highly corrosion-resistant type of steel. It is made by adding chromium and other alloying elements to the steel, which forms a protective layer that prevents rust and corrosion. Stainless steel is highly durable, easy to clean, and resistant to staining, making it ideal for tools used in wet or corrosive environments.
Tool Steel: Tool steel is a specialized type of steel that is specifically designed for making cutting tools, drills, dies, and other similar tools. It has excellent hardness, toughness, and wear resistance properties. Tool steel is often alloyed with elements such as tungsten, molybdenum, and vanadium to enhance these properties even further.
The specific composition and combination of these elements in each type of steel determine its unique properties, such as strength, hardness, toughness, corrosion resistance, and heat resistance. Manufacturers carefully select the type of steel based on the intended application of the hand tool to ensure optimum performance and longevity.
Carbon Steel
Carbon steel is a widely used type of steel in the manufacturing of hand tools. It is primarily composed of iron and carbon, with a carbon content ranging from 0.05% to 2.0%. The higher carbon content gives carbon steel its exceptional strength and hardness, making it suitable for applications that require durability and resistance to wear and tear.
One of the main advantages of carbon steel is its affordability. It is relatively inexpensive compared to other types of steel, making it a popular choice for a wide range of hand tools. Carbon steel is easy to work with and can be shaped into various forms, allowing manufacturers to create diverse tool designs that cater to specific tasks.
Carbon steel possesses excellent strength, making it ideal for tools that require forceful applications. It can withstand heavy-duty tasks without deformation or breakage. This property makes carbon steel hand tools suitable for applications such as construction, woodworking, and automotive repairs.
However, carbon steel is not resistant to corrosion, and it is prone to rust when exposed to moisture or certain environments. Therefore, it is important to apply protective coatings or keep carbon steel hand tools properly oiled to prevent rust and extend their lifespan.
In terms of sharpening and maintenance, carbon steel hand tools can typically be easily sharpened with the help of sharpening stones or other suitable tools. The hardness of carbon steel allows for sharpening that retains a sharp edge for an extended period, making it efficient for cutting and slicing tasks.
It is worth noting that the carbon content in carbon steel can significantly impact its properties. Low carbon steel, containing around 0.05% to 0.25% carbon, is more ductile and easily formed, while high carbon steel, with carbon content above 0.6%, is harder and more challenging to shape. The choice of carbon content depends on the intended purpose and application of the hand tool.
Some common hand tools made from carbon steel include wrenches, hammers, chisels, screwdrivers, and gardening tools like pruners and shears. These tools benefit from the strength, hardness, and affordability of carbon steel, making them reliable companions for various tasks.
Overall, carbon steel is a versatile and popular choice for hand tools due to its strength, hardness, and affordability. However, it is important to take proper care to prevent rust and corrosion, ensuring the longevity and performance of carbon steel hand tools.
Alloy Steel
Alloy steel is a type of steel that is created by adding various alloying elements to the base iron. The addition of these elements modifies the composition and properties of the steel, resulting in improved strength, hardness, toughness, and resistance to wear and tear.
One of the significant advantages of alloy steel is its versatility. By adjusting the composition of alloying elements, manufacturers can tailor the steel’s characteristics to match specific requirements. Some common alloying elements used in alloy steel are manganese, chromium, molybdenum, vanadium, and nickel.
One of the most common applications of alloy steel in hand tools is in their sockets and ratchets. The alloying elements enhance the strength and durability of these tools, ensuring they can withstand high torque and repetitive use without breaking or deforming. Alloy steel sockets and ratchets are widely used in automotive repairs, construction, and other heavy-duty applications.
Alloy steel’s resistance to corrosion is another notable feature, making it suitable for hand tools used in demanding environments. Stainless steel is a type of alloy steel with a high chromium content, which forms a protective layer that prevents rust and corrosion. It is often used in hand tools that will be exposed to moisture or corrosive substances, such as wrenches, pliers, and cutters.
Another significant advantage of alloy steel is its heat resistance. Tools made from high-alloy steel, such as chromium-vanadium steel or chromium-molybdenum steel, can withstand high temperatures without losing their strength and hardness. This makes them ideal for applications that involve high heat, such as working with hot metal or in welding and fabrication.
Alloy steel can be more challenging to work with compared to carbon steel due to its increased hardness. However, the benefits it provides in terms of strength, durability, and resistance to wear make it a popular choice for hand tools that require longevity and reliable performance.
Some common hand tools made from alloy steel include wrenches, sockets, ratchets, pliers, cutting tools like shears and snips, and various types of screwdrivers. These tools benefit from the enhanced properties of alloy steel, allowing users to tackle demanding tasks with confidence.
Overall, alloy steel is a versatile and durable material choice for hand tools. Its ability to be tailored to specific requirements, resistance to corrosion, and heat resistance make it a preferred option in various applications. Whether it’s in automotive repairs, construction, or other trades, alloy steel hand tools provide the strength and reliability required to get the job done.
High-Speed Steel
High-speed steel (HSS) is a specialized type of alloy steel that is specifically designed for high-speed machining and cutting applications. It is renowned for its exceptional hardness, heat resistance, and wear resistance, making it the preferred choice for tools that encounter intense heat and friction during operation.
The composition of high-speed steel typically includes additional alloying elements such as tungsten, cobalt, vanadium, or molybdenum. These elements contribute to its unique properties, allowing HSS tools to maintain their hardness and sharpness even under extreme conditions.
One of the key advantages of HSS is its remarkable hardness. The high carbon content and the alloying elements create a material with excellent resistance to deformation and wear. This hardness allows HSS tools to cut through tough materials like stainless steel, cast iron, and hardened steel without losing their cutting edge.
Another important property of HSS is its exceptional heat resistance. HSS tools can withstand high temperatures generated during the cutting process without losing their hardness. This makes them highly suitable for applications that involve high-speed machining, such as drilling, milling, and lathe operations in metalworking industries.
High-speed steel also possesses excellent wear resistance, allowing the tools to maintain their cutting performance even after extended periods of use. This reduces the frequency of tool replacements, resulting in cost savings and increased productivity.
Due to its hardness, heat resistance, and wear resistance, high-speed steel is commonly used in the manufacturing of cutting tools such as drill bits, milling cutters, taps, reamers, and saw blades. These tools are essential in industries such as aerospace, automotive, and metal fabrication, where precision and efficiency are paramount.
When using high-speed steel tools, it is important to follow proper cooling and lubrication techniques to dissipate heat and reduce friction. This helps to prolong the life of the tools and maintain their performance.
Overall, high-speed steel is a specialized type of alloy steel known for its exceptional hardness, heat resistance, and wear resistance. Its ability to withstand high-speed and high-temperature applications makes it an invaluable material choice for cutting tools in various industries.
Stainless Steel
Stainless steel is a type of alloy steel that is highly corrosion-resistant. It is composed of iron, chromium, and other alloying elements, such as nickel and manganese, depending on the specific grade. The addition of chromium forms a protective layer on the surface of the steel, known as chromium oxide, which prevents rust and corrosion.
One of the most significant properties of stainless steel is its corrosion resistance. This makes it extremely durable and suitable for hand tools that will be exposed to moisture, humidity, or corrosive substances. Stainless steel hand tools are ideal for outdoor use, plumbing applications, and working in wet or corrosive environments.
Another advantage of stainless steel is its aesthetic appeal. It has a clean and polished appearance that is both visually appealing and easy to clean. Stainless steel hand tools are resistant to staining, making them practical for applications where cleanliness is essential, such as in the food industry or medical field.
In addition to corrosion resistance, stainless steel is known for its excellent strength and durability. It can withstand heavy loads and tough conditions without deformation or breakage. This makes stainless steel hand tools reliable and long-lasting, reducing the need for frequent replacements.
Stainless steel is a versatile material that can be easily fabricated into various shapes and designs. It allows for the production of hand tools with intricate details and precise dimensions. Whether it’s wrenches, pliers, screwdrivers, or gardening tools, stainless steel provides the strength and versatility required for a wide range of applications.
However, stainless steel is generally softer than other types of steel, such as carbon steel or high-speed steel. While this can be advantageous for certain applications, it may limit the use of stainless steel tools in situations that require extreme hardness or resistance to wear.
Overall, stainless steel hand tools offer a combination of corrosion resistance, durability, and visual appeal. They are widely used in industries such as construction, plumbing, automotive, and food processing, where reliability and cleanliness are crucial.
Hand tools are typically made from high carbon steel, which is strong and durable. This type of steel can withstand the repeated stress and impact of everyday use, making it ideal for hand tool construction.
Tool Steel
Tool steel is a specialized type of steel that is designed to provide exceptional hardness, toughness, and wear resistance. It is commonly used for making cutting tools, dies, drills, and other tools that require durability and high performance in demanding applications.
Tool steel is typically alloyed with elements such as tungsten, molybdenum, vanadium, and chromium, which enhance its properties. These alloying elements improve the steel’s hardness, toughness, and resistance to wear, making it suitable for cutting, shaping, and forming materials.
One of the main characteristics of tool steel is its exceptional hardness. The high carbon content and the presence of alloying elements contribute to its hardness, allowing tool steel to maintain its cutting edge for extended periods. This makes it ideal for applications where precision and sharpness are essential, such as in machining operations or metalworking industries.
Tool steel also possesses excellent toughness, which refers to its ability to withstand impact or shock without breaking or deforming. This toughness is crucial for tools that undergo repetitive use or encounter rough conditions. Tool steel can resist chipping or cracking, ensuring reliable performance and long tool life.
In addition to hardness and toughness, tool steel exhibits excellent wear resistance. It can withstand friction and abrasive forces without significant deterioration, making it suitable for applications that involve repetitive cutting or shaping. Tool steel maintains its sharpness and cutting efficiency, reducing the need for frequent tool replacements.
There are different types of tool steel, each with its own specific composition and properties. For example, high-speed steel (HSS) is a type of tool steel known for its exceptional heat resistance and ability to maintain hardness at high temperatures. Cold work tool steel is designed for applications that involve cutting or forming at low temperatures, while hot work tool steel is suitable for high-temperature applications.
Tool steel is commonly used for making a wide range of hand tools, such as drills, chisels, punches, milling cutters, and dies. These tools benefit from the hardness, toughness, and wear resistance of tool steel, allowing for precise and efficient machining operations.
Overall, tool steel is a specialized type of steel known for its exceptional hardness, toughness, and wear resistance. It is a preferred material choice for manufacturing high-performance cutting tools and other tools that require durability and reliability in demanding applications.
Steel Manufacturing Process
The manufacturing of steel involves several steps to create a material that meets specific requirements in terms of composition, strength, and properties. Here is a general overview of the steel manufacturing process:
1. Iron Making: The first step in steel production is the extraction of iron ore from the earth. Iron ore is then processed in a blast furnace, where it is heated at extremely high temperatures along with coke (a form of coal) and limestone. This process results in the formation of molten iron and impurities called slag.
2. Steelmaking: The molten iron from the blast furnace is then refined further in a steelmaking furnace, such as a basic oxygen furnace (BOF) or an electric arc furnace (EAF). During this stage, scrap metal and other alloys are added to the molten iron to create the desired steel composition. The impurities in the iron are removed through processes like oxidation and desulfurization.
3. Continuous Casting: Once the steel is refined, it is poured into a continuous casting machine, where it solidifies into long rectangular shapes called slabs, blooms, or billets. This continuous casting process allows for efficient and consistent production of steel in large quantities.
4. Steel Forming: The solidified steel is then transformed into various shapes and forms through different processes. This may involve rolling the steel at high temperatures to create sheets, bars, or structural shapes. Alternatively, it may undergo processes like forging, extrusion, or machining to produce specific components or hand tool blanks.
5. Heat Treatment: To enhance the strength, hardness, and other desired properties of the steel, it undergoes heat treatment. This process involves heating the steel to a specific temperature and then cooling it at a controlled rate. Heat treatment techniques such as annealing, hardening, tempering, and quenching are utilized depending on the desired outcome.
6. Machining and Finishing: After heat treatment, the steel may undergo further machining processes to shape it into final hand tool components. This may involve cutting, grinding, milling, or drilling to achieve the desired dimensions and surface finish. The steel surface may also be treated with coatings or finishes to enhance corrosion resistance or improve aesthetics.
Throughout the steel manufacturing process, quality control and testing play a critical role to ensure that the finished steel meets the required standards. Mechanical and chemical tests are conducted to verify the strength, composition, and other properties of the steel.
It is important to note that different steel manufacturing processes and variations in compositions can result in different types of steel, each with its own specific properties and applications. This allows for the production of steel tailored to the needs of specific industries, including the manufacturing of high-quality hand tools.
The steel manufacturing process is complex and requires careful control of various factors to produce steel of consistent quality. Continuous advancements in technology and processes have led to the development of specialized steels with superior properties, ensuring the production of durable and reliable hand tools.
Heat Treatment of Steel
Heat treatment is an essential process in the manufacturing of steel that involves heating and cooling the material to alter its physical and mechanical properties. By carefully controlling the temperature and cooling rates, heat treatment can significantly enhance the strength, hardness, toughness, and other desired characteristics of steel. Let’s explore some common heat treatment techniques used for steel:
1. Annealing: Annealing is a heat treatment process that involves heating the steel to a specific temperature and then allowing it to cool slowly. This process relieves internal stresses, refines the grain structure, and improves machinability. Annealed steel is softer and more ductile, making it easier to shape or form into hand tool components.
2. Normalizing: Normalizing is similar to annealing, but the cooling process is more rapid. By uniformly cooling the steel in air, the surface becomes slightly harder and the grain size becomes smaller. Normalizing improves the overall strength and toughness of the steel, making it suitable for hand tools that require higher resistance to impact and wear.
3. Hardening: Hardening is a heat treatment process that involves heating the steel to a specific temperature and then rapidly quenching it in a cooling medium such as water or oil. This rapid cooling “freezes” the desired crystal structure, resulting in a hardened steel with improved strength and hardness. Hardened steel is commonly used in cutting tools like drills, chisels, and blades.
4. Tempering: Tempering is a heat treatment process that follows the hardening process. It involves reheating the hardened steel to a lower temperature and allowing it to cool slowly. Tempering reduces the hardness and brittleness of the steel while increasing its toughness and ductility. This process balances the hardness and toughness, making the steel more suitable for hand tools that require a combination of strength and resilience.
5. Quenching and Tempering: Quenching and tempering is a two-step heat treatment process that combines the rapid cooling of hardening with the subsequent tempering. After hardening, the steel is immediately quenched to achieve maximum hardness, and then it is tempered to reduce brittleness and improve toughness. This process is commonly used for hand tools that require a high level of hardness and toughness, such as hammers and wrenches.
6. Case Hardening: Case hardening is a specialized heat treatment process that is used to increase the hardness of the outer surface of the steel while maintaining a relatively softer core. This is achieved by introducing carbon or other alloying elements onto the surface of the steel and then subjecting it to heat treatment. Case hardened steel is commonly used in hand tools that require wear resistance on the surface, such as gears or bearing surfaces.
Heat treatment is a critical step in the manufacturing of steel and plays a vital role in determining the performance and durability of hand tools. By carefully selecting the appropriate heat treatment technique based on the desired properties, manufacturers can create steel with enhanced strength, hardness, toughness, and resistance to wear or deformation, ensuring the production of high-quality hand tools that can withstand demanding applications.
Read more: What Hand Tools To Use For Etching
Common Hand Tools Made from Steel
Steel is a versatile and widely-used material in the manufacturing of hand tools due to its strength, durability, and ability to be shaped into various forms. Here are some common hand tools that are commonly made from steel:
1. Wrenches: Wrenches are essential tools for tightening or loosening nuts and bolts. They are typically made from steel due to its excellent strength and durability. Steel wrenches can withstand high torque without deformation or breakage and are available in different sizes and types to accommodate various applications.
2. Hammers: Hammers are used for striking or driving nails, and their heads are commonly made from steel. The steel head provides the necessary weight and impact force required for driving nails or breaking objects. Steel hammers are available in different types, such as claw hammers, ball-peen hammers, and sledgehammers, each designed for a specific purpose.
3. Screwdrivers: Screwdrivers are indispensable tools for driving screws into or removing them from various materials. The shaft or blade of a screwdriver is typically made from hardened steel to provide durability and resistance to stripping or bending. Steel screwdrivers come in a wide range of sizes and shapes to match different screw types and sizes.
4. Pliers: Pliers are versatile hand tools used for gripping, bending, and cutting wires or other materials. The jaws and cutting edges of pliers are commonly made from steel due to its strength and ability to withstand pressure and cutting forces. Steel pliers are available in different types, including combination pliers, long-nose pliers, and locking pliers.
5. Chisels: Chisels are used for cutting or shaping materials like wood, metal, or stone. The cutting edge of a chisel is typically made from high-carbon or high-speed steel to maintain sharpness and withstand repeated strikes without dulling or chipping. Steel chisels are available in various sizes and types for different tasks, such as wood chisels, cold chisels, and masonry chisels.
6. Saws: Hand saws are commonly used for cutting through wood or other materials. The blades of hand saws are typically made from high-carbon or alloy steel to provide sharpness and rigidity. Steel saw blades are hardened and tempered to maintain their cutting edge and resist bending or breaking during use.
7. Scissors: Scissors are essential cutting tools for various applications, such as crafting, sewing, or gardening. The blades of scissors are generally made from stainless steel to provide corrosion resistance and sharp cutting edges. Steel scissors are available in different sizes and designs for specific tasks, such as fabric scissors, kitchen scissors, and pruning shears.
8. Files: Files are used for shaping, smoothing, or removing material from surfaces. The cutting edges of files are made from hardened steel to withstand the abrasive forces of filing while maintaining sharpness. Steel files come in various shapes and sizes, including flat files, half-round files, and round files, for different filing applications.
These are just a few examples of hand tools made from steel. The strength, durability, and versatility of steel make it an ideal material choice for a wide range of hand tools, ensuring they can withstand the rigors of various applications and provide long-lasting performance.
Conclusion
Steel is a fundamental material in the manufacturing of hand tools, providing the necessary strength, durability, and versatility required for various applications. Whether it’s carbon steel, alloy steel, high-speed steel, stainless steel, or tool steel, each type offers unique properties that contribute to the performance and longevity of hand tools.
Carbon steel, with its exceptional strength, affordability, and ease of shaping, is commonly used in a wide range of hand tools. However, proper care is necessary to prevent rust and corrosion.
Alloy steel, with the addition of various alloying elements, offers enhanced strength, hardness, and resistance to wear and tear, making it ideal for demanding applications.
High-speed steel, with its exceptional hardness, heat resistance, and wear resistance, is specifically designed for high-speed machining and cutting applications. It is commonly used in cutting tools for precision and efficiency.
Stainless steel, with its corrosion resistance, durability, and easy maintenance, is highly suitable for hand tools used in wet or corrosive environments, where cleanliness is essential.
Tool steel, with its exceptional hardness, toughness, and wear resistance, is specifically designed for cutting tools, dies, and other tools that require durability and high performance in demanding applications.
Throughout the steel manufacturing process, heat treatment plays a vital role in enhancing the properties of steel. Annealing, normalizing, hardening, tempering, and other heat treatment techniques allow for precise control over the hardness, toughness, and other desired characteristics of steel for optimal performance in hand tools.
Common hand tools made from steel, such as wrenches, hammers, screwdrivers, pliers, chisels, saws, and scissors, benefit from the strength, durability, and versatility that steel provides. These tools are essential companions for various tasks, from construction and woodworking to plumbing and crafting.
In conclusion, the use of steel in hand tools ensures reliability, durability, and performance. Whether in the form of carbon steel for affordability, alloy steel for enhanced strength, high-speed steel for precision cutting, stainless steel for corrosion resistance, or tool steel for durability and wear resistance, steel is a key material in the manufacturing of hand tools that cater to diverse needs and applications.
Frequently Asked Questions about What Kind Of Steel Is Used In Hand Tools
Was this page helpful?
At Storables.com, we guarantee accurate and reliable information. Our content, validated by Expert Board Contributors, is crafted following stringent Editorial Policies. We're committed to providing you with well-researched, expert-backed insights for all your informational needs.
0 thoughts on “What Kind Of Steel Is Used In Hand Tools”