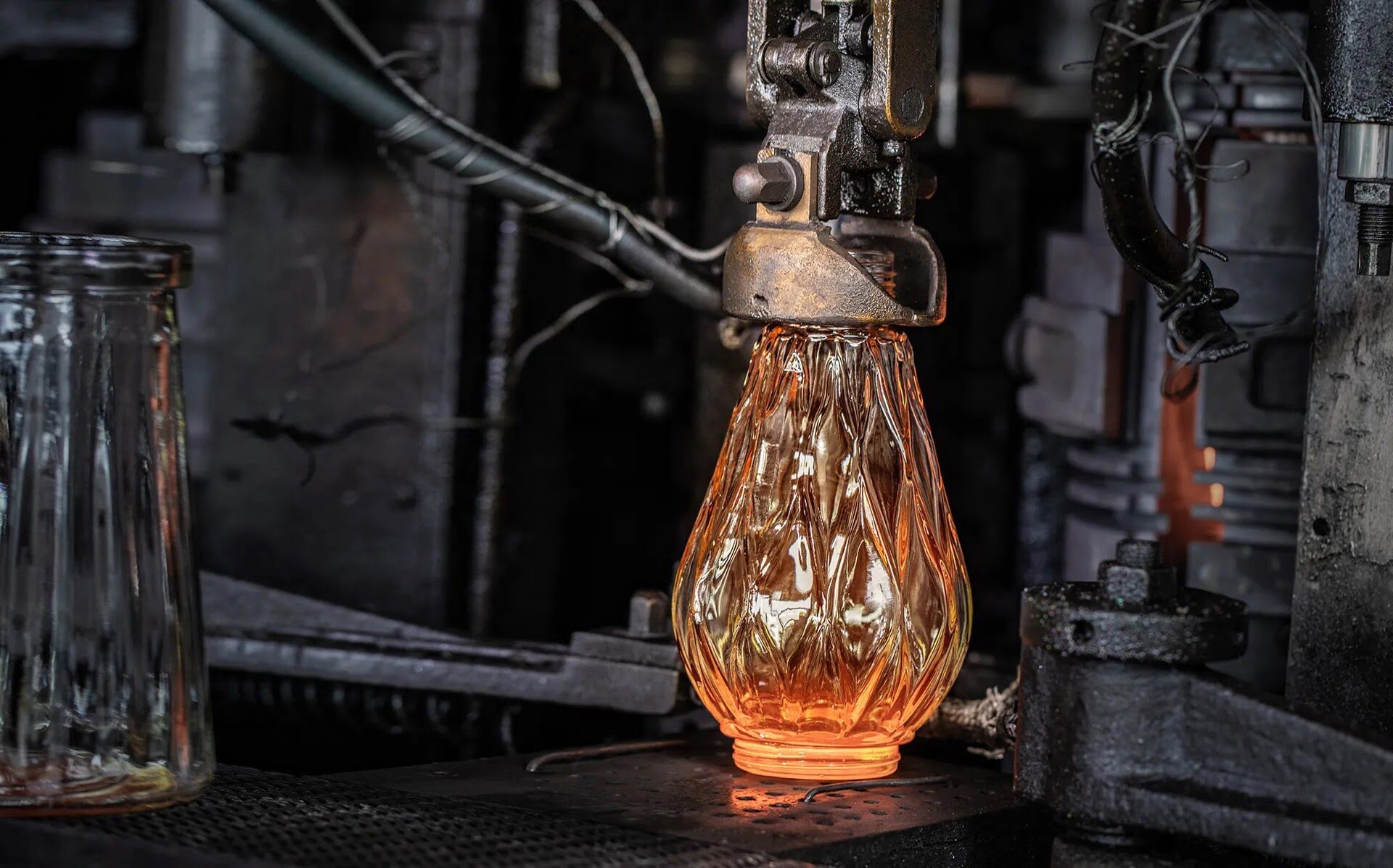
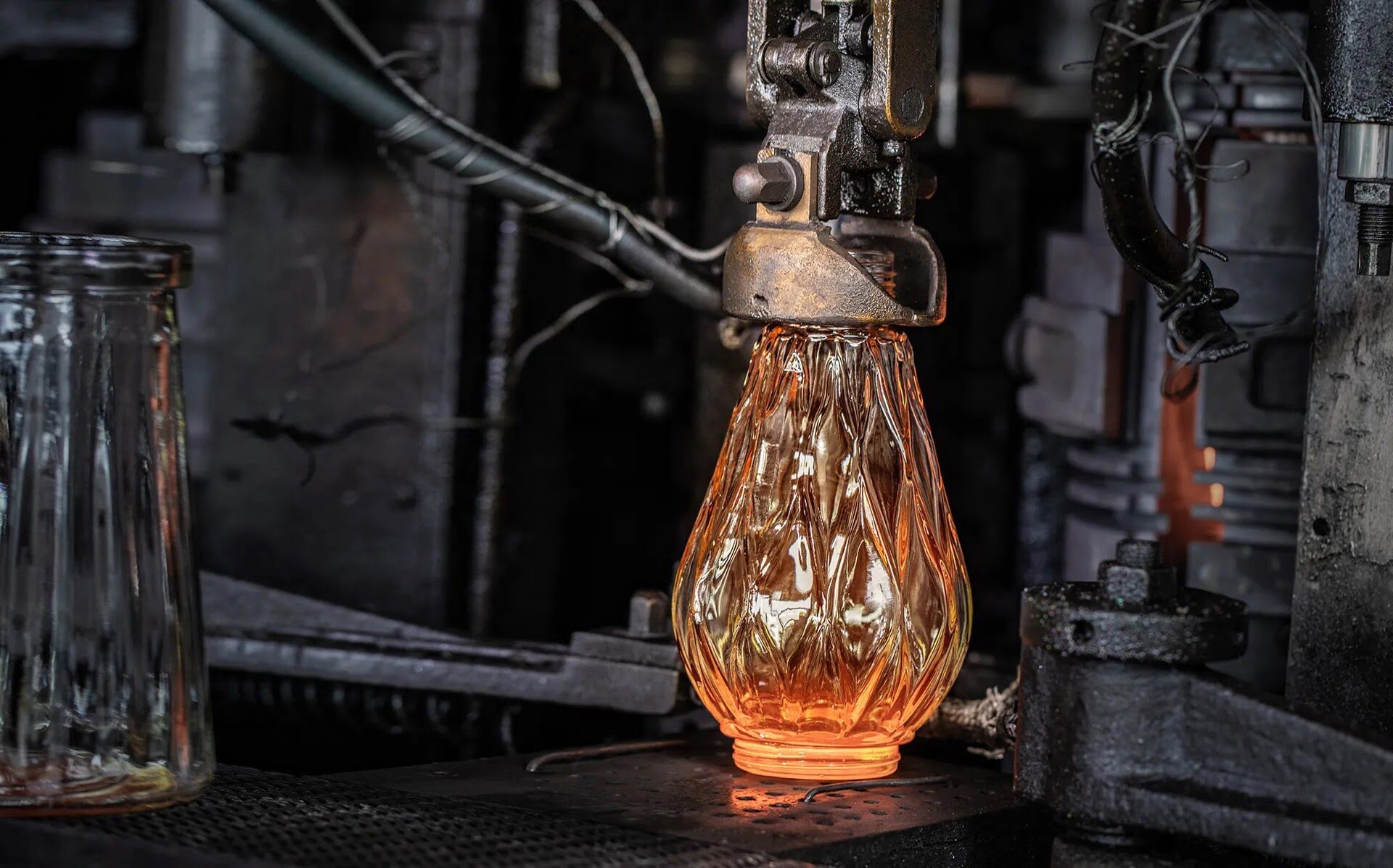
Tableware
How Is Glassware Made
Modified: February 4, 2024
Discover the fascinating process of how glassware is made, from molten glass to stunning tableware creations. Explore intricate techniques and skilled craftsmanship in this insightful guide.
(Many of the links in this article redirect to a specific reviewed product. Your purchase of these products through affiliate links helps to generate commission for Storables.com, at no extra cost. Learn more)
Introduction
Tableware is an essential part of any dining experience. From elegant dinner parties to everyday meals, the right tableware can elevate the dining ambiance and enhance the overall enjoyment of a meal. One popular type of tableware is glassware, which includes items like drinking glasses, plates, bowls, and serving dishes made from glass.
Glassware is not only practical but also adds a touch of sophistication and elegance to any tabletop. But have you ever wondered how glassware is made? The process of creating glassware involves a series of carefully crafted steps that combine science, craftsmanship, and artistry.
In this article, we will explore the fascinating journey of how glassware is made, from the composition of the glass to the final finishing touches. So, let’s dive in and discover the secrets behind the creation of beautiful glassware.
Key Takeaways:
- Glassware is made from soda-lime glass, composed of silica, soda ash, and limestone. Additional elements can create lead crystal or borosilicate glass, each with unique properties and colors.
- The process of making glassware involves mixing raw materials, melting the glass, shaping it through blowing, pressing, or hand-forming, and then cooling, annealing, quality control, and adding decorative finishing touches.
Read more: Where Is Acopa Glassware Made
The Composition of Glassware
Glassware is made from a specific type of glass known as soda-lime glass. This type of glass is composed primarily of three main ingredients: silica, soda ash, and limestone. Silica, or silicon dioxide, is obtained from sand, while soda ash, or sodium carbonate, is derived from a combination of salt, limestone, and other minerals.
The composition of glassware can also include additional elements to impart specific properties or colors to the glass. For example, the addition of lead oxide can create lead crystal glass, which has a higher refractive index and exceptional clarity. Similarly, the addition of boron can create borosilicate glass, which is known for its resistance to thermal shock.
The proportions of these ingredients can vary depending on the desired properties of the glassware. The precise measurements and mixing of these ingredients are crucial to achieving the desired consistency and quality of the final product.
Once the ingredients are selected and prepared, they are ready to be mixed and melted to form glass. The next step in the process involves carefully combining the raw materials and subjecting them to high temperatures.
Remember to add HTML tags appropriately, such as
for paragraphs and
for headings, to ensure the content is properly formatted for an HTML output.
Mixing the Raw Materials
The process of creating glassware begins with the careful mixing of the raw materials. The silica, soda ash, and limestone are measured and combined in precise ratios to ensure the desired composition of the glass.
Mixing the raw materials is a crucial step, as it ensures the even distribution of the ingredients and helps create a homogeneous mixture. This is typically done in large mixers or blenders, where the ingredients are blended together thoroughly until they form a consistent and uniform mix.
During the mixing process, additional elements may be added to the mixture to achieve specific properties or colors. For instance, if colored glassware is desired, metal oxides or other coloring agents can be introduced into the mix. This allows for a wide range of colors and styles to be produced.
Once the raw materials are thoroughly mixed, the resulting mixture, known as batch, is ready to undergo the next phase of the glassware manufacturing process – melting the glass.
Remember to add HTML tags appropriately, such as
for paragraphs and
for headings, to ensure the content is properly formatted for an HTML output.
Melting the Glass
After the raw materials are mixed, the next step in the glassware production process is melting the glass. The batch is carefully transferred into a furnace where it is subjected to intense heat, typically ranging from 1100 to 1500 degrees Celsius.
The high temperatures in the furnace cause the raw materials to undergo a chemical reaction, transforming them into a molten liquid state. This molten liquid, known as glass, is highly viscous and malleable, allowing it to be shaped into various forms.
The melting process is essential for removing any impurities from the raw materials and achieving a smooth and consistent glass composition. It also helps to homogenize the mixture, ensuring that all the ingredients are fully combined and any bubbles or inconsistencies are eliminated.
Once the glass has reached the desired molten state, it is ready for the next stage of the production process – shaping the glassware.
Remember to add HTML tags appropriately, such as
for paragraphs and
for headings, to ensure the content is properly formatted for an HTML output.
Shaping the Glassware
Shaping the glassware is where the artistry and craftsmanship of glassmaking truly come into play. After the glass has been melted, it is carefully shaped and formed into the desired shape using a variety of techniques.
One common method of shaping glassware is through blowing. This technique involves using a blowpipe, a long hollow tube, to gather molten glass from the furnace. The glassblower then blows air into the blowpipe, creating a bubble in the glass. By shaping and manipulating the bubble with tools and molds, the glassblower can create a wide range of glassware shapes, such as bottles, goblets, and vases.
Another shaping method is called pressing. This technique is used to create glassware with intricate designs or patterns. Molten glass is placed into a mold, and pressure is applied to shape the glass to conform to the mold’s design. This method is commonly used for creating glassware with ornate patterns or textured surfaces, adding an extra layer of elegance and detail.
For more intricate and delicate glassware, a method called hand-forming is employed. Skilled artisans use specialized tools, such as shears and paddles, to carefully shape the molten glass by hand. This allows for the creation of unique and artistic pieces, such as decorative bowls or sculptures.
Once the glassware has been shaped, it undergoes a process known as annealing to ensure its strength and durability.
Remember to add HTML tags appropriately, such as
for paragraphs and
When making glassware, it’s important to use high-quality raw materials, such as silica sand, soda ash, and limestone, to ensure the final product is strong and durable.
Read more: What Is Luminarc Glassware Made Of
for headings, to ensure the content is properly formatted for an HTML output.
Read more: What Is Luminarc Glassware Made Of
Cooling and Annealing
Read more: What Is Luminarc Glassware Made Of
After the glassware has been shaped, it must go through a cooling and annealing process to ensure its strength and durability. This step is crucial for preventing stress and internal tension within the glass, which can lead to breakage or weakness.
When the glassware is first shaped, it is still in a hot and malleable state. If it were to cool rapidly, the temperature difference between the outer surface and the inner layers could cause the glass to crack or shatter. To prevent this, the glassware is carefully placed in an annealing oven, which is typically a controlled environment with gradually decreasing temperatures.
The annealing process involves slowly cooling the glassware over a period of several hours or even days, depending on the thickness and size of the item. As the glassware gradually cools down, the internal stresses within the material are relieved. This allows for a more balanced and stable structure, ensuring the glassware’s durability and resistance to thermal shock.
During the annealing process, the glassware may also undergo a process called quenching. Quenching involves rapidly cooling the glass in order to increase its strength and durability. This is often done by carefully immersing the glassware into a controlled cooling bath or using air or steam jets to cool the glass rapidly.
Once the glassware has been properly cooled and annealed, it is ready for the next steps in the production process – quality control and finishing touches.
Remember to add HTML tags appropriately, such as
for paragraphs and
for headings, to ensure the content is properly formatted for an HTML output.
Quality Control
Ensuring the quality of glassware is an essential aspect of the production process. Before the glassware is deemed ready for distribution, it undergoes a rigorous quality control assessment to guarantee that it meets the highest standards of craftsmanship and functionality.
Quality control begins with a visual inspection, where trained professionals meticulously examine each piece of glassware for any imperfections, such as bubbles, cracks, or uneven surfaces. Any defective items are removed from the production line to maintain the overall quality and integrity of the final product.
In addition to visual inspection, glassware undergoes various tests to assess its durability, resistance to impact, and thermal shock resistance. For example, a test called the “rattle test” is performed to check for any loose or faulty components, ensuring that the glassware is securely assembled.
Quality control also involves testing the glassware’s ability to withstand temperature changes. This includes subjecting the glassware to rapid temperature variations to evaluate its resistance to thermal shock. This testing is crucial, especially for glassware meant for hot beverages or ovens.
Moreover, quality control may involve evaluating the glassware’s capacity and dimensions to ensure that it meets the expected specifications. This is particularly important for glassware used in food and beverage service, where accuracy in measurements is vital for portion control and presentation.
By conducting thorough quality control measures, glassware manufacturers aim to deliver products that meet or exceed customer expectations in terms of aesthetics, functionality, and durability. Only after passing these tests does the glassware move onto the next stage – decorating and finishing touches.
Remember to add HTML tags appropriately, such as
for paragraphs and
for headings, to ensure the content is properly formatted for an HTML output.
Decorating and Finishing Touches
Once the glassware has passed quality control, it moves on to the exciting stage of decorating and adding the finishing touches. This is where the creativity and artistry of glass artisans come to the forefront, transforming the glassware into beautiful and unique pieces.
One popular method of decorating glassware is through the application of decorative patterns or designs using various techniques. Glassware can be decorated with techniques such as etching, engraving, sandblasting, or even hand painting. These methods allow for intricate details, elegant patterns, or personalized messages to be added to the surface of the glassware.
In addition to decorative elements, glassware can also undergo further finishing touches. This may include polishing the edges to create a smooth and refined look or adding a special coating to enhance the durability and resistance of the glass. Finishing touches may also involve applying a protective glaze or sealant to the glassware to prolong its lifespan and maintain its clarity and shine.
Furthermore, glassware can undergo additional processes such as acid-etching or frosting to create a frosted or matte appearance. These techniques can add a touch of sophistication and elegance to the glassware, making it stand out on any tabletop.
Once the decorating and finishing touches are complete, the glassware is ready for packaging and distribution. Each piece is carefully wrapped and boxed to ensure its safe transportation and arrival at its final destination, be it a retail store or a customer’s doorstep.
Remember to add HTML tags appropriately, such as
for paragraphs and
for headings, to ensure the content is properly formatted for an HTML output.
Conclusion
Glassware is more than just functional tableware; it is a work of art crafted through a meticulous and fascinating process. From the careful composition of raw materials to the shaping, cooling, and finishing touches, each step contributes to the creation of beautiful and durable glassware.
We have explored the journey of glassware production, from the mixing of raw materials to the melting of glass and the shaping of the final product. We have also delved into the importance of cooling and annealing to ensure the strength and durability of glassware. Through quality control measures, manufacturers ensure that only flawless and reliable glassware reaches consumers.
Lastly, we discovered the decorative techniques and finishing touches that add an extra layer of elegance and personalization to glassware. From intricate patterns to delicate engraving, these artistic elements elevate glassware into exquisite pieces that adorn dining tables around the world.
So next time you sip from a beautifully crafted glass or serve a meal on a set of glassware, take a moment to appreciate the craftsmanship and artistry that went into its creation. Glassware is not just an everyday object, but a testament to human ingenuity and the fusion of science and art.
Remember to use appropriate HTML tags, such as
for paragraphs and
for headings, to ensure the content is properly formatted for an HTML output.
Frequently Asked Questions about How Is Glassware Made
What are the main materials used in making glassware?
Glassware is primarily made from silica sand, soda ash, and limestone. These materials are melted together at high temperatures to form molten glass, which can then be shaped and molded into various glassware products.
Is glassware production a sustainable process?
Yes, glassware production is considered to be a sustainable process. The main raw material used in making glassware, silica sand, is abundant and renewable. Additionally, glassware is 100% recyclable, making it an environmentally friendly choice for tableware.
How is the strength and durability of glassware ensured during the manufacturing process?
To ensure the strength and durability of glassware, manufacturers often use a process called annealing. This involves slowly cooling the glassware after it has been shaped and molded, which helps to relieve internal stresses and strengthen the glass.
What are the different techniques used to shape and decorate glassware?
Glassware can be shaped and decorated using various techniques such as blowing, pressing, and molding. Additionally, glassware can be decorated through methods like etching, engraving, and painting to create intricate designs and patterns.
Can glassware be customized for specific purposes or events?
Yes, glassware can be customized for specific purposes or events. Manufacturers can create custom designs, shapes, and sizes to meet the specific needs of customers, whether it’s for a special event, restaurant, or personal use.
Frequently Asked Questions about How Is Glassware Made
Was this page helpful?
At Storables.com, we guarantee accurate and reliable information. Our content, validated by Expert Board Contributors, is crafted following stringent Editorial Policies. We're committed to providing you with well-researched, expert-backed insights for all your informational needs.
0 thoughts on “How Is Glassware Made”