Home>diy>Building & Construction>How To Control Quality In Construction
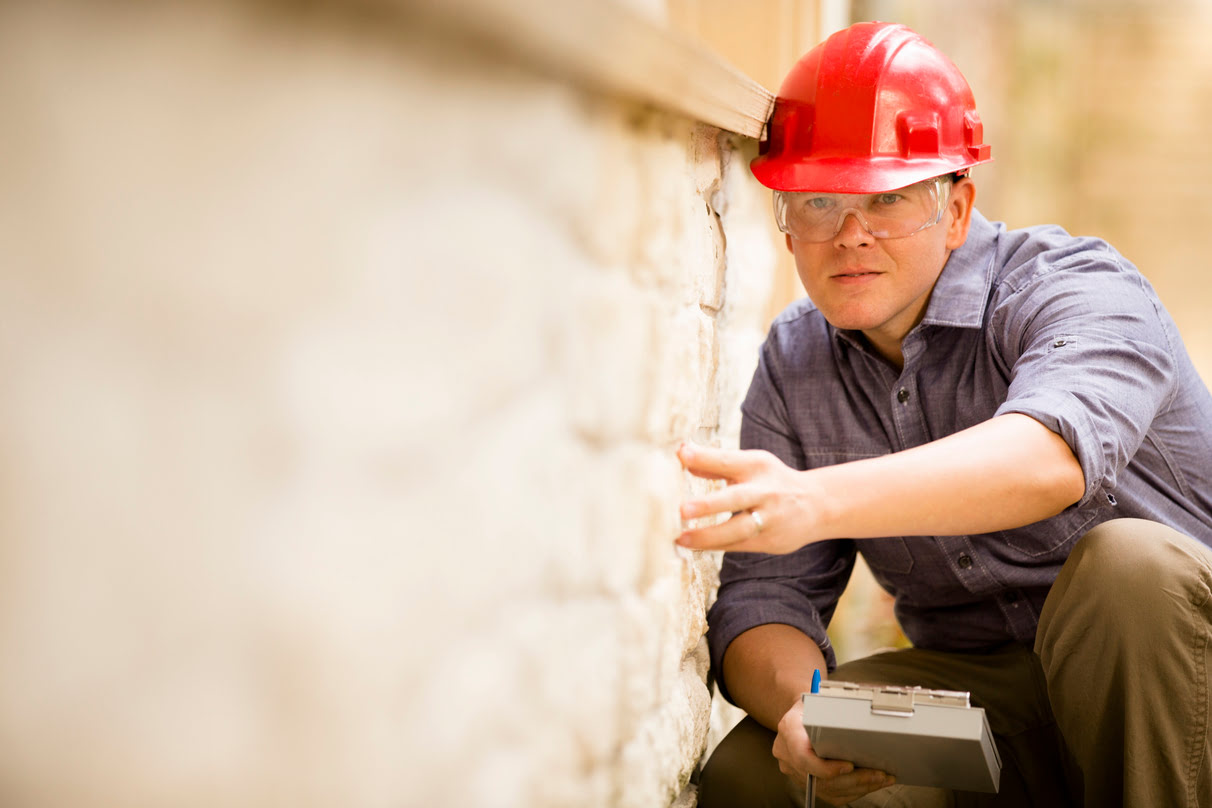
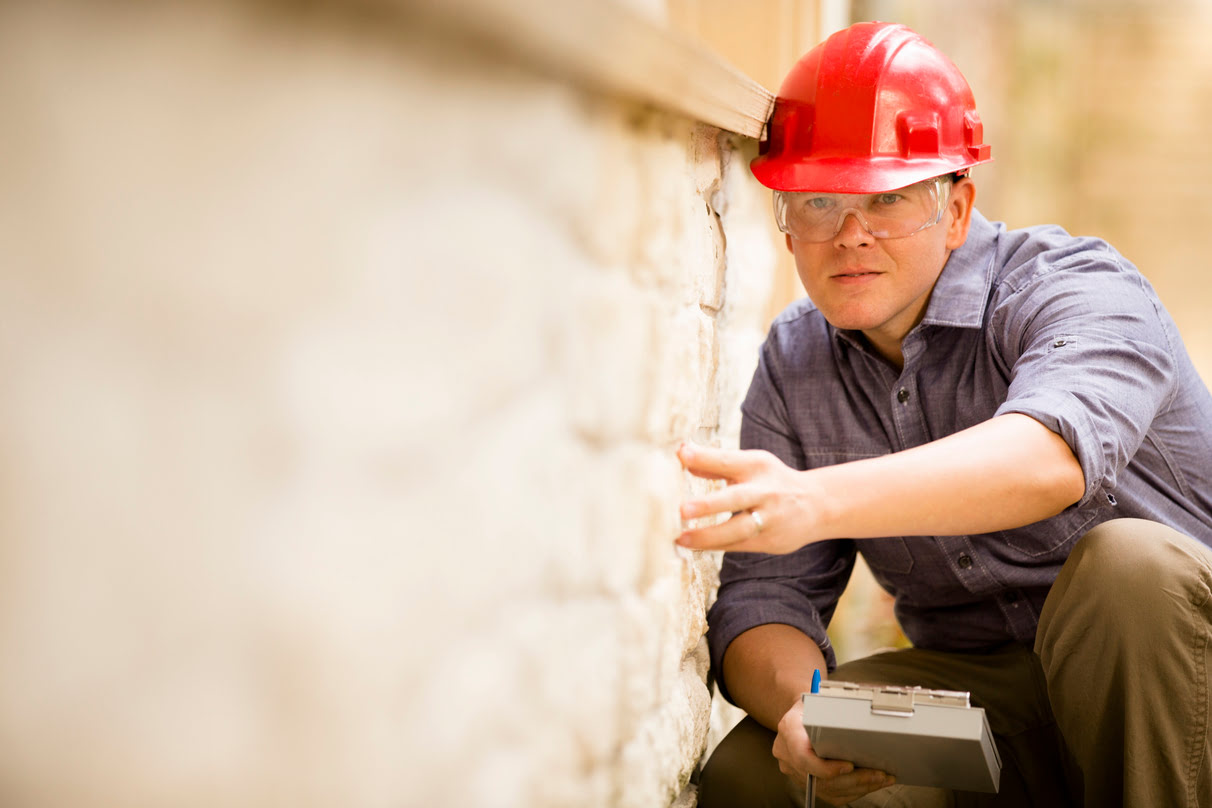
Building & Construction
How To Control Quality In Construction
Modified: March 6, 2024
Learn effective strategies to control quality in building construction. Explore quality assurance techniques, inspection methods, and quality control processes.
(Many of the links in this article redirect to a specific reviewed product. Your purchase of these products through affiliate links helps to generate commission for Storables.com, at no extra cost. Learn more)
Introduction
Quality control plays a crucial role in the construction industry, ensuring that projects are built to meet the highest standards of safety, durability, and functionality. From residential buildings to large-scale infrastructure projects, adhering to stringent quality control measures is essential to deliver projects that meet the expectations of clients, regulatory authorities, and end-users.
Construction projects involve numerous materials, technologies, and processes, all of which must be carefully managed to ensure the desired outcomes. Quality control in construction encompasses a range of practices designed to monitor, assess, and improve the quality of every aspect of a project, from design and materials procurement to the construction process and final completion.
By implementing effective quality control measures, construction companies can minimize the risk of defects, rework, delays, and cost overruns. Emphasizing quality control also enhances the reputation of construction firms, fosters client satisfaction, and ultimately leads to greater success in a highly competitive industry.
In this article, we will explore the importance of quality control in construction and discuss the key principles and best practices that can be applied to ensure optimal project outcomes. From establishing quality metrics and goals to training construction staff and implementing quality assurance processes, we will delve into the essential steps that contribute to successful quality control.
We will also emphasize the importance of communication, collaboration, and compliance with quality standards and regulations. By highlighting case studies and real-life examples, we will illustrate the tangible benefits of effective quality control and showcase the best practices that industry leaders have adopted.
Whether you are a construction professional seeking to enhance your knowledge of quality control or a client looking to understand the measures taken to ensure project excellence, this article will provide valuable insights into the world of quality control in construction.
Key Takeaways:
- Quality control in construction ensures safe, durable, and high-quality projects by setting clear goals, promoting communication, and complying with standards and regulations.
- Implementing effective quality assurance processes, training construction staff, and continuously improving practices are crucial for successful quality control in construction.
Read more: What Is A Controller In Construction
Importance of Quality Control in Construction
Quality control is of paramount importance in the construction industry due to the complex nature of construction projects and the long-term impact they have on individuals and communities. Here are some key reasons why quality control is crucial in construction:
- Ensuring Safety: Construction sites can be hazardous environments, with potential risks to workers and the public. Quality control measures help ensure that construction materials, structural components, and processes adhere to safety standards, minimizing the risk of accidents and promoting a safe working environment.
- Delivering Durability: Buildings and infrastructure projects are expected to have a long lifespan. Quality control ensures that construction materials and techniques are chosen and implemented to meet the required level of durability. This includes assessing the quality of materials, performing rigorous testing, and adhering to industry standards.
- Meeting Functional Requirements: Quality control ensures that construction projects meet their intended purpose and functional requirements. Whether it’s a residential building or a transportation infrastructure project, quality control measures help identify and rectify any deficiencies that could hinder the functionality and usability of the finished structure.
- Minimizing Cost Overruns: Poor quality can lead to costly rework, delays, and increased project expenses. Effective quality control processes help identify and address potential issues early on, minimizing the risk of budget overruns and ensuring that construction projects are completed within budget.
- Enhancing Client Satisfaction: Clients have high expectations for the quality of construction projects. By implementing robust quality control measures, construction firms can consistently deliver projects that meet or exceed client expectations. This not only fosters client satisfaction but also leads to positive recommendations and repeat business.
- Meeting Regulatory Requirements: Compliance with building codes, safety regulations, and environmental standards is essential in the construction industry. Quality control processes ensure that construction projects meet all necessary regulatory requirements, preventing costly legal issues and ensuring adherence to ethical and legal standards.
In summary, quality control is vital in construction to ensure safety, durability, functionality, and client satisfaction. By implementing effective quality control measures, construction firms can deliver successful projects, minimize risks and costs, and uphold their reputation for excellence in the industry.
Key Principles of Quality Control in Construction
Successful quality control in construction requires a systematic and proactive approach. Here are the key principles that underpin effective quality control in the construction industry:
- Leadership and Commitment: Quality control starts at the top. Strong leadership and commitment from management are crucial to creating a culture of quality within the organization. Leaders must prioritize quality, set clear expectations, and provide the necessary resources and support to implement quality control processes.
- Planning and Coordination: Quality control should be integrated into the project planning phase. It involves identifying quality requirements, establishing quality objectives, and developing a comprehensive quality plan. Coordination between different stakeholders, including designers, contractors, and suppliers, is essential to ensure a consistent approach to quality control throughout the project.
- Clear Communication: Effective communication is vital to ensure that quality expectations are understood and met by all parties involved. Clear channels of communication should be established, allowing for the transparent exchange of information and the timely resolution of quality-related issues.
- Standardization and Documentation: Standardization of processes and documentation helps ensure consistency and traceability in quality control. This includes developing standard operating procedures, checklists, and documentation templates to capture and track quality-related activities throughout the construction process.
- Supplier and Material Management: Quality control extends beyond the construction site. It involves selecting reliable suppliers and ensuring that construction materials meet the required quality standards. Supplier audits, material testing, and quality assurance agreements play a crucial role in maintaining the quality of materials used in construction projects.
- Risk Assessment and Mitigation: Risk assessment is essential to identify potential quality risks and develop appropriate mitigation strategies. This includes conducting thorough risk assessments at each stage of the project, implementing preventive measures, and establishing contingency plans to address any unforeseen quality issues.
- Quality Assurance Process: Quality assurance processes involve regular inspections, testing, and monitoring to verify that construction activities adhere to the established quality standards. This includes conducting inspections at various stages of construction, conducting material testing, and engaging third-party quality assurance providers when necessary.
- Continuous Improvement: Quality control is an ongoing process. Emphasizing continuous improvement allows for the identification of areas for enhancement and the implementation of corrective measures. Regular evaluation and feedback loops are essential to drive improvements in quality control practices.
By adhering to these key principles, construction companies can establish a robust quality control framework that ensures consistent project performance, minimizes risks, and delivers high-quality construction projects that meet or exceed client expectations.
Establishing Quality Metrics and Goals
Establishing clear quality metrics and goals is an essential step in achieving effective quality control in construction. By defining specific metrics and goals, construction companies can objectively measure performance and track progress towards quality objectives. Here are some key considerations in establishing quality metrics and goals:
- Define Measurable Metrics: Quality metrics should be quantifiable and measurable to provide meaningful insights. These metrics can include parameters such as defect rates, rework percentages, customer satisfaction scores, or on-time delivery rates. By using objective metrics, construction companies can assess performance accurately and identify areas for improvement.
- Align Metrics with Project Requirements: The chosen quality metrics should align with the specific requirements and characteristics of the construction project. Different projects may have unique quality considerations, such as structural integrity, environmental sustainability, or aesthetic appeal. Aligning the metrics with project requirements ensures that the quality goals are relevant and address project-specific needs.
- Set Realistic and Achievable Goals: Quality goals should be set based on a realistic assessment of the project’s scope and constraints. Setting overly ambitious or unattainable goals can lead to frustration and demotivation. It is essential to balance high quality aspirations with practical considerations to ensure that goals are achievable within the project’s timeframe and available resources.
- Consider Stakeholder Expectations: Stakeholder expectations play a crucial role in defining quality goals. This includes the expectations of clients, end-users, regulatory authorities, and other relevant parties. Conducting thorough stakeholder analysis and incorporating their perspectives helps ensure that the established quality metrics align with their expectations.
- Continuous Review and Adjustment: Quality metrics and goals should not be set in stone. Regular review and adjustment are necessary to account for any changes in project objectives, client requirements, or industry standards. Projects evolve over time, and quality control metrics and goals should be adjusted accordingly to remain relevant and effective.
- Measure and Track Performance: Once quality metrics and goals are established, it is essential to implement a system for measuring and tracking performance. This may involve conducting regular inspections, carrying out quality audits, and collecting relevant data to assess progress. The data collected can be analyzed to identify trends, areas of improvement, and to make data-driven decisions.
- Share and Communicate Goals: Transparency and communication are key to ensuring everyone involved in the construction project understands the quality goals. Sharing the established metrics and goals with project stakeholders, including contractors, subcontractors, and suppliers, fosters a collective commitment to achieving and maintaining high-quality standards throughout the project.
By establishing clear quality metrics and goals, construction companies can focus their efforts on achieving and improving quality outcomes. The defined metrics and goals provide a roadmap for quality control activities, enabling the identification of areas for improvement and ensuring that the project aligns with the desired quality standards.
Implementing Quality Assurance Processes
Quality assurance processes are vital in ensuring that construction projects meet the desired quality standards. These processes involve systematic inspections, testing, and monitoring activities that verify compliance with specifications and regulations. Here are key steps in successfully implementing quality assurance processes:
- Develop a Quality Assurance Plan: A comprehensive quality assurance plan serves as a roadmap for implementing quality control measures. It outlines the specific activities, responsibilities, and timelines for inspections, tests, and monitoring throughout the project lifecycle. The plan should be tailored to the project’s unique requirements and align with industry best practices.
- Perform Regular Inspections: Regular inspections are crucial to identify any deviations from the project specifications and to ensure that construction activities are carried out in accordance with approved plans and standards. Inspections should cover all key stages of the construction process, including site preparation, foundation work, structural components, mechanical and electrical installations, finishing work, and final completion.
- Conduct Material Testing: Material testing is a fundamental aspect of quality assurance. It involves assessing the quality and performance of construction materials, such as concrete, steel, aggregates, and insulation. Testing should be carried out by qualified technicians using accredited laboratories to ensure accurate and reliable results.
- Implement Quality Control Checkpoints: Establishing quality control checkpoints at critical stages of the construction process helps catch any potential quality issues early on. These checkpoints should include thorough assessments of construction methods, compliance with design specifications, and the proper installation and integration of various components and systems.
- Utilize Technology and Automation: Implementing technology solutions and automation can enhance the effectiveness of quality assurance processes. Building Information Modeling (BIM), drones for aerial inspections, and sensors for real-time monitoring are examples of technologies that can improve data accuracy, efficiency, and provide valuable insights into the quality performance of construction projects.
- Engage Independent Third-Party Providers: In some cases, it is beneficial to engage independent third-party providers to conduct quality assurance activities. These providers offer unbiased assessments and can bring specialized expertise and experience to ensure robust quality control. Engaging third-party providers can provide an added layer of assurance and increase confidence in project outcomes.
- Implement Non-Conformance Reporting: Non-conformance reporting is a critical aspect of quality assurance. It involves documenting any deviations from project specifications and standards and implementing appropriate corrective actions. Non-conformance reports serve as a tool for tracking and addressing quality issues and are essential for continuous improvement.
- Train and Empower Construction Staff: Effective quality assurance requires well-trained and knowledgeable construction staff. Investing in training programs that focus on quality control principles, inspection techniques, and industry standards is imperative. Empowerment of staff to identify and address quality issues in real-time also contributes to a strong quality culture within the organization.
By implementing robust quality assurance processes, construction companies can enhance project outcomes, minimize risks, and ensure compliance with quality standards and regulations. These processes provide the necessary checks and balances to deliver construction projects that meet the desired quality requirements.
Read more: How To Control Construction Dust
Training and Development of Construction Staff
The training and development of construction staff play a vital role in ensuring the successful implementation of quality control measures. Well-trained and knowledgeable staff are equipped to adhere to quality standards, follow established processes, and contribute to the overall quality culture within the organization. Here are key considerations in training and developing construction staff:
- Identify Training Needs: Conduct a thorough assessment of the existing skills and knowledge of construction staff to identify any gaps or areas that require improvement. This can be done through performance evaluations, self-assessments, or feedback from project managers. The identified training needs will serve as the basis for designing targeted training programs.
- Provide Technical and Quality Training: Construction staff should receive technical training related to their specific job roles and responsibilities. This can include training on construction methods, material handling, equipment operation, safety protocols, and building codes. Additionally, providing specific training on quality control principles, inspection techniques, and relevant industry standards is crucial to develop a strong understanding of quality requirements and the ability to implement effective quality control measures.
- Offer Continuing Education Opportunities: Continuous learning is essential in a rapidly evolving industry. Offering opportunities for construction staff to participate in workshops, seminars, conferences, and professional development courses allows them to stay updated with the latest industry trends, technologies, and best practices. Continuing education enhances their skills and knowledge, enabling them to contribute to the continuous improvement of quality control processes.
- Hands-on Training and Mentoring: Incorporate hands-on training and mentoring programs to provide practical experience and guidance to construction staff. On-the-job training enables staff to apply theoretical knowledge to real-world construction scenarios, develop practical skills, and learn from experienced mentors. This approach promotes a culture of knowledge sharing and skill development within the organization.
- Promote Cross-Training and Multiskilling: Encourage cross-training and multiskilling of construction staff to enhance their versatility and adaptability. Exposure to different job roles and responsibilities allows staff to gain a broader understanding of the construction process. It enables them to appreciate the interconnectedness of various tasks and develop a holistic perspective on quality control.
- Emphasize Safety Training: Safety is a critical aspect of quality control in construction. Ensure that construction staff receive comprehensive safety training, covering topics such as hazard identification, emergency procedures, proper use of personal protective equipment, and safe work practices. Safety training promotes a culture of risk awareness and fosters a safer working environment.
- Encourage Continuous Improvement: In addition to initial training, construction staff should be encouraged to engage in continuous learning and improvement. This can be achieved through regular feedback sessions, performance evaluations, and ongoing professional development opportunities. Emphasizing a culture of continuous improvement fosters a proactive approach to quality control and encourages staff to seek innovative solutions.
Investing in the training and development of construction staff is essential for maintaining a strong quality culture within the organization. By equipping staff with the necessary skills, knowledge, and resources, construction companies can enhance quality control practices, improve project outcomes, and establish a reputation for excellence in the industry.
Regularly inspect and test materials and workmanship to ensure they meet quality standards. Keep detailed records of inspections and address any issues promptly to maintain high quality in construction.
Documentation and Reporting
Documentation and reporting are critical components of effective quality control in construction. Proper documentation ensures that critical information, processes, and activities are recorded and available for reference. Reporting provides insights into the status of quality control measures and facilitates decision-making for continuous improvement. Here are key considerations for documentation and reporting in construction:
- Create a Document Management System: Implement a document management system to organize and store quality-related documents, such as project specifications, design drawings, inspection reports, test results, and Non-conformance Reports (NCRs). This system should allow for easy retrieval and access to documentation by relevant stakeholders.
- Standardize Documentation Templates: Develop standardized templates for various quality control documents, such as inspection checklists, testing procedures, and NCR forms. This ensures consistency in documenting quality-related activities and facilitates accurate reporting and analysis.
- Record Inspection and Testing Results: Document the results of inspections, tests, and audits in a systematic manner. This includes capturing information about the date, location, responsible personnel, findings, and any corrective actions taken. Accurate and detailed records provide a historical reference and serve as evidence of compliance with quality standards.
- Track Non-Conformance Reports (NCRs): Non-conformance reports document any deviations from project specifications or quality standards. Develop a process for reporting, documenting, and tracking NCRs, including the identification of root causes and the implementation of corrective actions. This helps identify trends, recurring issues, and areas for improvement.
- Implement Change Control Procedures: Construction projects often undergo changes during the course of their lifecycle. Implement a change control procedure to document and track any modifications or revisions to project specifications, designs, or quality control processes. This ensures that all changes are properly evaluated, approved, and communicated to relevant parties.
- Regular Reporting and Analysis: Establish a reporting schedule to provide updates on the status of quality control measures. This may include weekly or monthly reports that summarize key quality metrics, highlight any significant findings or trends, and identify areas requiring attention. Regular analysis of these reports helps identify successes, areas for improvement, and opportunities for optimizing quality control processes.
- Ensure Clarity and Accuracy: Documentation and reporting should be clear, concise, and accurate. Use standardized terminology, clearly define abbreviations, and avoid ambiguity. Make sure that the information provided is complete and reflects the actual state of quality control activities.
- Share Documentation and Reports: Share relevant documentation and reports with appropriate stakeholders, including project managers, quality control team members, clients, and regulatory authorities. This ensures transparency and fosters collaborative decision-making based on accurate and up-to-date information.
- Retain Documentation for Future Reference: Retain all quality-related documentation for an appropriate period, as per industry regulations and legal requirements. This allows for future reference, audits, and resolving any disputes that may arise after project completion.
Effective documentation and reporting provide a comprehensive record of quality control activities, facilitate analysis and decision-making, and contribute to the overall success of construction projects. By implementing robust documentation and reporting practices, construction companies can ensure compliance with quality standards, maintain accountability, and drive continuous improvement in quality control processes.
Continuous Improvement and Evaluation
Continuous improvement and evaluation are essential aspects of successful quality control in the construction industry. By striving for ongoing improvement and regularly evaluating quality control processes, construction companies can enhance project outcomes and ensure the delivery of high-quality construction projects. Here are key considerations for continuous improvement and evaluation:
- Promote a Culture of Continuous Improvement: Foster a culture within the organization that encourages and rewards continuous improvement. This includes instilling a mindset that embraces change, innovation, and the pursuit of excellence. Encourage employees at all levels to contribute ideas and suggestions for improving quality control processes.
- Establish Key Performance Indicators (KPIs): Define and track key performance indicators related to quality control. These KPIs can measure metrics such as defect rates, rework percentages, customer satisfaction scores, or on-time delivery rates. Regularly monitor and analyze these KPIs to identify areas for improvement and track progress over time.
- Conduct Root Cause Analysis: When quality issues arise, perform thorough root cause analysis to identify the underlying causes. This involves investigating the contributing factors, understanding why they occurred, and developing appropriate corrective actions. Analyzing root causes helps prevent the recurrence of issues and facilitates continuous improvement.
- Implement Lessons Learned Sessions: Hold regular lessons learned sessions to capture and share knowledge from past projects. These sessions provide an opportunity to reflect on successes, challenges, and opportunities for improvement. Encourage open and honest discussions, and identify best practices that can be applied to future projects.
- Engage in Process Optimization: Continuously evaluate and optimize quality control processes to streamline workflows, eliminate waste, and boost efficiency. Seek input from employees and stakeholders to identify bottlenecks, pain points, and areas for improvement. Implement process improvements that lead to more effective quality control and increased productivity.
- Encourage Feedback and Suggestions: Create channels for employees, subcontractors, and other stakeholders to provide feedback and suggestions related to quality control. This can be done through regular feedback sessions, suggestion boxes, or online platforms. Actively solicit and consider input from those involved in the construction process.
- Regularly Review and Update Quality Control Procedures: Quality control procedures should not be static but instead should evolve with industry advancements and changing project requirements. Regularly review and update quality control procedures to incorporate lessons learned, industry best practices, and emerging technologies. Ensure that all stakeholders are informed and trained on any updates or changes.
- Empower Employees to Drive Improvement: Empower employees to take ownership of quality control and drive improvement initiatives. Encourage them to identify and solve problems, propose innovative solutions, and take initiative in implementing improvements. Recognize and reward employees for their contributions to continuous improvement efforts.
- Seek External Feedback and Benchmarking: Look for opportunities to seek external feedback and engage in benchmarking activities. This can involve collaborating with industry associations, attending conferences and seminars, and participating in industry benchmarking programs. Learning from others and understanding industry best practices can inspire new ideas and foster continuous improvement.
Continuous improvement and evaluation ensure that quality control in construction remains effective and aligned with industry best practices. By embracing the mindset of continuous learning and improvement, construction companies can achieve higher quality standards, mitigate risks, and consistently deliver successful construction projects.
Importance of Communication and Collaboration in Quality Control
Effective communication and collaboration are fundamental to achieving successful quality control in the construction industry. Clear and open lines of communication facilitate the exchange of information, promote understanding, and foster collaboration among project stakeholders. Here’s why communication and collaboration are crucial in quality control:
- Shared Understanding of Quality Requirements: Effective communication ensures that all stakeholders have a clear understanding of the quality requirements and standards for the construction project. By conveying expectations and specifications clearly, everyone involved can work towards a common goal, ensuring consistency and alignment in quality control efforts.
- Early Issue Identification and Resolution: Strong communication channels enable prompt identification and resolution of quality-related issues. Regular communication among project teams, subcontractors, and suppliers allows for the early detection of potential quality concerns, giving stakeholders the opportunity to address them before they escalate into more significant problems or impact project outcomes.
- Cross-Functional Collaboration: Quality control in construction involves multiple disciplines and stakeholders working together towards a common objective. Collaboration ensures that different teams and specialists can seamlessly coordinate their efforts, share their expertise, and address quality-related challenges collectively. It promotes efficiency and a holistic approach to quality control.
- Supplier and Subcontractor Alignment: Effective communication and collaboration with suppliers and subcontractors are essential to ensure the quality of materials and services provided. Open lines of communication enable clear expectations to be set, specifications to be clarified, and potential issues to be addressed proactively, ultimately fostering a mutually beneficial relationship based on shared quality goals.
- Transparency and Accountability: Transparent communication builds trust among stakeholders and fosters a sense of accountability for quality control. Openly sharing information and progress updates allows everyone involved to stay informed and take ownership of their respective roles and responsibilities. This facilitates effective problem-solving, timely decision-making, and the ability to address quality-related issues collectively.
- Knowledge Sharing and Learning: Effective communication and collaboration create an environment conducive to knowledge sharing and continuous learning. Through open discussions, sharing lessons learned, and exchanging best practices, project teams can enhance their knowledge and skills, leading to improved quality control practices and better project outcomes.
- Feedback and Continuous Improvement: Communication channels provide opportunities for stakeholders to provide feedback on quality control practices. By actively seeking input and encouraging constructive criticism, construction companies can gather valuable insights that lead to continuous improvement of quality control processes, driving better outcomes in future projects.
- Client Satisfaction and Relationship Building: Communication and collaboration directly impact client satisfaction. Regular updates, clear communication of quality control measures, and timely resolution of any concerns enhance client trust and confidence. Positive client experiences foster strong relationships, repeat business, and positive referrals, ultimately contributing to the long-term success of construction companies.
- Adherence to Regulatory Requirements: Effective communication ensures that all stakeholders are aware of and comply with applicable regulatory requirements and quality standards. By sharing information about codes, regulations, and industry best practices, construction companies can avoid costly rework, delays, and legal complications related to non-compliance.
In summary, communication and collaboration are vital in quality control within the construction industry. By fostering open and effective communication channels and promoting collaboration among project stakeholders, construction companies can achieve better quality outcomes, enhance relationships, and drive project success.
Read more: How To Work Thermostat Controls
Ensuring Compliance with Quality Standards and Regulations
Compliance with quality standards and regulations is a critical aspect of effective quality control in the construction industry. Adhering to established standards and regulations ensures that construction projects meet the required quality benchmarks, achieve regulatory approval, and mitigate risks. Here are important considerations for ensuring compliance with quality standards and regulations:
- Stay Up-to-Date with Standards and Regulations: Stay informed about the latest industry standards and regulations relevant to the construction project. Regularly monitor updated codes, guidelines, and best practices to ensure ongoing compliance and to incorporate any necessary changes into quality control processes.
- Understand Applicable Quality Standards: Familiarize yourself with the quality standards applicable to the specific construction project. This includes national, international, and industry-specific standards that govern various aspects of construction, such as materials, design, construction techniques, and safety protocols.
- Establish Procedures to Ensure Compliance: Develop procedures and checklists to ensure that quality standards and regulations are followed throughout the construction process. These procedures should outline the specific requirements, documentation, inspections, and testing protocols necessary to demonstrate compliance.
- Engage Relevant Stakeholders: Involve all relevant stakeholders, including design professionals, contractors, subcontractors, suppliers, and regulatory authorities, to ensure that everyone is aware of and accountable for complying with quality standards and regulations. Effective communication and regular collaboration with stakeholders promote a shared understanding and commitment to compliance.
- Regular Inspections and Audits: Conduct regular inspections and audits throughout the construction process to monitor compliance with quality standards and regulations. Inspections should encompass all critical aspects of construction, including materials, workmanship, safety protocols, and adherence to approved plans and specifications.
- Documentation of Compliance: Maintain accurate documentation that records compliance with quality standards and regulations. This includes maintaining records of inspections, test results, certificates of compliance, permits, and other necessary documentation. Proper documentation serves as evidence of compliance and facilitates regulatory audits, project reviews, and dispute resolution.
- Training and Education on Compliance: Ensure that all personnel involved in the construction project receive adequate training and education on the relevant quality standards and regulations. This includes training on proper construction techniques, the use of approved materials, safety procedures, and documentation practices. Regularly educate staff on updates and changes to standards and regulations.
- Maintain a Culture of Compliance: Foster a culture that prioritizes compliance with quality standards and regulations. Emphasize the importance of following established processes and requirements to protect the safety and well-being of stakeholders and to maintain the integrity of the construction project. Promote a sense of responsibility and accountability for upholding quality standards throughout the organization.
- Engage Third-Party Experts: Consider engaging independent third-party experts to provide objective assessments and validation of compliance. Third-party experts can conduct audits, inspections, and testing to ensure that quality standards and regulatory requirements are met. Their expertise adds credibility and impartiality to the compliance verification process.
- Continuous Monitoring and Improvement: Continuously monitor compliance with quality standards and regulations throughout the project. Regularly review and evaluate compliance performance, identify any gaps or areas for improvement, and implement corrective actions. Good compliance practices should be incorporated into lessons learned, shared with the team, and used to refine future quality control processes.
By ensuring compliance with quality standards and regulations, construction companies can demonstrate their commitment to delivering high-quality projects, protect the interests of stakeholders, and mitigate risks associated with non-compliance. Adhering to established standards contributes to the overall success and reputation of the construction company in the industry.
Case Studies and Best Practices in Quality Control
Examining case studies and best practices in quality control can provide valuable insights and offer guidance on implementing effective quality control measures in the construction industry. Here are a few notable examples:
- The Shard, London, UK: The construction of The Shard, one of London’s iconic skyscrapers, exemplifies effective quality control. The project team implemented a comprehensive quality management system that included regular inspections, testing, and documentation. They collaborated closely with suppliers, contractors, and regulatory authorities to ensure compliance with stringent quality standards. The emphasis on quality control resulted in the successful construction of a landmark building with excellent durability and impressive design.
- Toyota Production System: The Toyota Production System, renowned for its commitment to quality, can serve as a best practice in quality control. The system emphasizes continuous improvement, waste reduction, and employee involvement in identifying and resolving quality issues. By implementing a standardized approach to quality control, Toyota has achieved high levels of efficiency, reliability, and customer satisfaction.
- Lean Construction Principles: Lean construction principles advocate for a proactive approach to quality control, focusing on eliminating waste, optimizing workflows, and maintaining a culture of continuous improvement. It encourages collaboration among project teams, early issue identification, and open communication, all of which contribute to enhanced quality in construction projects.
- ISO 9001:2015 Certification: Many construction companies aim to obtain ISO 9001:2015 certification, an internationally recognized quality management standard. This certification demonstrates a commitment to meeting customer expectations, complying with regulatory requirements, and continuously improving quality control processes. Implementing the standard’s principles and requirements promotes an organized and systematic approach to quality control.
- Building Information Modeling (BIM): BIM is a technology-driven approach that facilitates real-time collaboration and information sharing among project stakeholders. It enables clash detection, visualization, and accurate simulations, reducing errors and enhancing quality control. By utilizing BIM in construction projects, teams can identify and address potential quality issues early on, positively impacting project outcomes.
- Quality Circles: Quality circles are small groups of employees who meet regularly to identify and analyze quality concerns and suggest improvement measures. Encouraging the formation of quality circles fosters employee engagement, collaboration, and ownership of quality control. These circles enable frontline workers to contribute their expertise, promote a culture of continuous improvement, and drive better quality outcomes.
These case studies and best practices demonstrate the importance of implementing robust quality control measures in construction. By adopting proven approaches and principles such as comprehensive quality management systems, lean construction practices, certification standards, advanced technologies like BIM, and employee engagement initiatives like quality circles, construction companies can enhance their quality control efforts and achieve successful project outcomes.
It’s important to note that while these examples have been effective in their respective contexts, each construction project is unique, and organizations should tailor their quality control approaches to suit their specific needs and project requirements.
Conclusion
Quality control is paramount in the construction industry to ensure the delivery of safe, durable, and high-quality projects. By implementing effective quality control measures, construction companies can mitigate risks, minimize costly rework, and enhance client satisfaction. Throughout this article, we have delved into the importance of quality control in construction and discussed key principles and best practices that contribute to successful quality control.
We explored the significance of establishing clear quality metrics and goals to objectively measure performance and track progress. We emphasized the importance of communication and collaboration in quality control, as effective communication fosters shared understanding, early issue identification, and transparency among project stakeholders. Additionally, we highlighted the need for compliance with quality standards and regulations to ensure adherence to industry best practices and maintain the integrity of construction projects.
We discussed the implementation of quality assurance processes, including regular inspections, material testing, and documentation, which verify compliance with specifications and facilitate continuous improvement. We emphasized the importance of training and development of construction staff to equip them with the necessary skills and knowledge for effective quality control.
Furthermore, we explored the significance of documentation and reporting in maintaining accurate records, facilitating analysis, and supporting evidence of compliance. We delved into the importance of continuous improvement and evaluation to drive advancements in quality control practices and achieve better project outcomes.
Lastly, we discussed case studies and best practices in quality control, highlighting examples such as The Shard, the Toyota Production System, lean construction principles, ISO 9001:2015 certification, BIM, and quality circles. These real-world examples showcase successful implementation of quality control measures and underscore the importance of tailoring approaches to project-specific needs.
In conclusion, effective quality control is essential for construction companies to deliver projects that meet or exceed client expectations, comply with regulations, and uphold quality standards. By adhering to the principles and best practices outlined in this article, construction professionals can enhance project outcomes, mitigate risks, and foster a culture of continuous improvement. With a strong dedication to quality control, construction companies can strengthen their reputation, gain a competitive advantage, and contribute to the growth and sustainability of the industry as a whole.
Frequently Asked Questions about How To Control Quality In Construction
Was this page helpful?
At Storables.com, we guarantee accurate and reliable information. Our content, validated by Expert Board Contributors, is crafted following stringent Editorial Policies. We're committed to providing you with well-researched, expert-backed insights for all your informational needs.
0 thoughts on “How To Control Quality In Construction”