Home>diy>Building & Construction>How To Control Construction Dust
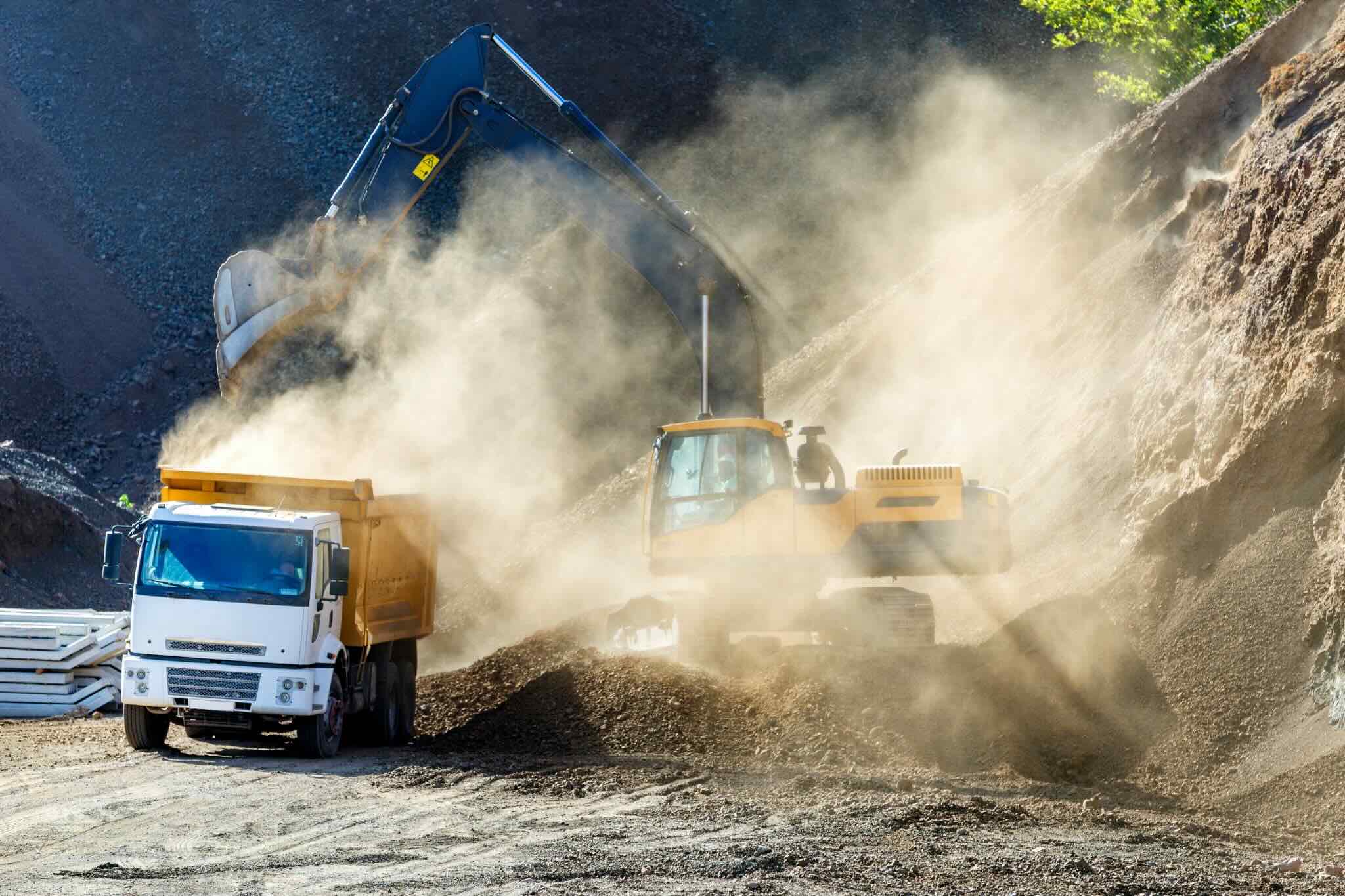
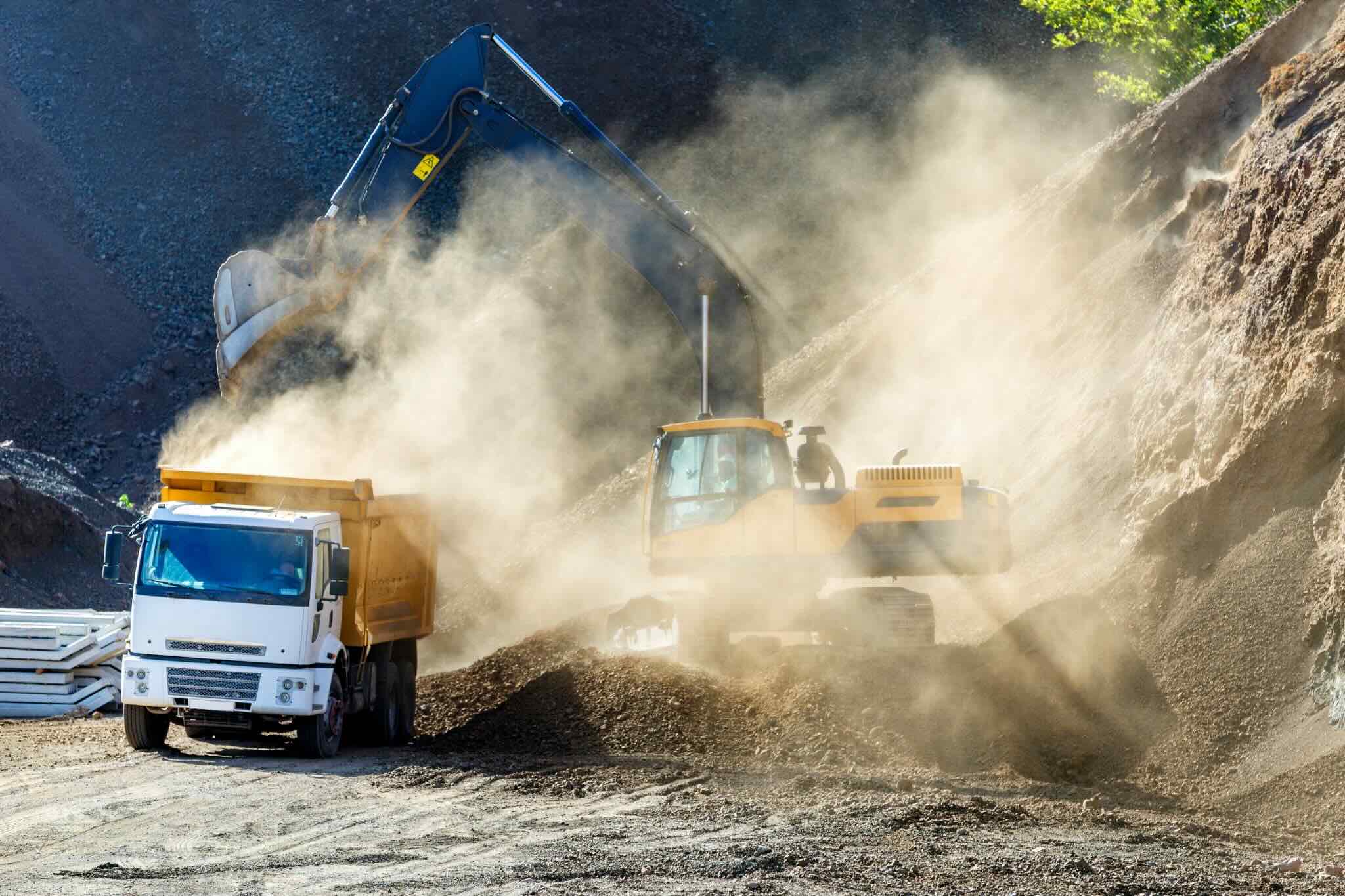
Building & Construction
How To Control Construction Dust
Modified: January 24, 2024
Learn effective methods to control construction dust during building construction projects. Minimize health risks and maintain a clean and safe working environment.
(Many of the links in this article redirect to a specific reviewed product. Your purchase of these products through affiliate links helps to generate commission for Storables.com, at no extra cost. Learn more)
Introduction
Welcome to the world of construction, where incredible structures are brought to life. However, amidst the hustle and bustle of building construction, there’s an often overlooked enemy that lurks in the air – construction dust. Dust is an inevitable byproduct of construction activities, but if left unchecked, it can pose serious health hazards to both workers and the surrounding environment.
Construction dust consists of fine particles that are released into the air during activities such as cutting, drilling, sanding, and demolishing materials like concrete, bricks, and wood. These tiny particles, often invisible to the naked eye, can contain harmful substances such as silica, lead, asbestos, and other toxic materials.
The health effects of construction dust can be detrimental. Prolonged exposure can lead to respiratory diseases, lung damage, cancer, and other serious health conditions. This is why controlling construction dust is not just a matter of compliance with regulations, but also a moral responsibility to protect the health and well-being of workers and the community.
In this comprehensive guide, we will delve into the world of construction dust and explore effective strategies for its control. We will discuss regulatory guidelines, dust control measures, equipment selection, best practices, and the importance of training and education. So, let’s put on our dust masks and embark on this journey to understand how to control construction dust effectively.
Key Takeaways:
- Prioritizing the health and safety of construction workers is crucial in controlling construction dust, which contains hazardous substances like silica and asbestos. Compliance with regulatory guidelines, effective dust control measures, and ongoing monitoring are essential for creating a safer working environment.
- Training and education play a vital role in empowering construction workers to actively contribute to dust control efforts. By providing hazard awareness training, guidance on control measures, and ongoing monitoring, construction companies can ensure a dust-free and safe future in the industry.
Read more: How To Reduce Construction Dust
Understanding the Hazards of Construction Dust
Construction dust may seem innocuous, but it can have serious consequences for those exposed to it. Understanding the hazards associated with construction dust is crucial for implementing effective control measures.
Respiratory Diseases
One of the most significant health risks posed by construction dust is the development of respiratory diseases. When workers inhale dust particles, they can penetrate deep into the lungs and cause irritation, inflammation, and scarring. Over time, this can lead to conditions such as occupational asthma, bronchitis, and chronic obstructive pulmonary disease (COPD).
Silica Dust
One of the most common and dangerous types of construction dust is silica dust. Silica is a natural mineral found in materials such as sand, concrete, and stone. When these materials are cut, crushed, or drilled, silica dust is released into the air. Prolonged exposure to silica dust can cause silicosis, a debilitating lung disease that can be fatal.
Asbestos
While the use of asbestos has been largely phased out, it can still be found in older buildings and structures. When disturbed, asbestos fibers become airborne and can be inhaled. Asbestos exposure is linked to serious diseases such as lung cancer, mesothelioma, and asbestosis.
Read more: How To Remove Dust After Construction
Lead
Construction activities that involve lead-based paint or lead pipes can lead to the release of lead dust. Ingesting or inhaling lead dust can cause lead poisoning, which can have severe health effects, especially in children. Symptoms can include neurological damage, developmental delays, and organ damage.
Biological Contaminants
Construction sites can also harbor biological contaminants, such as mold, bacteria, and fungi. These contaminants can thrive in damp and poorly ventilated areas and can cause respiratory issues, allergic reactions, and other health problems.
By understanding the hazards associated with construction dust, we can take the necessary steps to mitigate these risks and protect the health and safety of construction workers and the surrounding environment. In the next section, we will explore the regulatory guidelines and compliance requirements for controlling construction dust.
Regulatory Guidelines and Compliance
Controlling construction dust is not only essential for the health and safety of workers but also a legal requirement. Various regulatory bodies and organizations have established guidelines and standards to ensure the effective management of construction dust. Understanding and complying with these regulations is crucial for construction companies and contractors.
Occupational Safety and Health Administration (OSHA)
In the United States, the Occupational Safety and Health Administration (OSHA) sets guidelines and regulations for worker safety. OSHA’s Respirable Crystalline Silica Standard aims to protect workers from the dangers of silica dust exposure by establishing permissible exposure limits and requiring employers to implement control measures, provide training, and conduct monitoring and medical surveillance.
Read more: What Is A Controller In Construction
Construction Dust Control Association (CDCA)
In the UK, the Construction Dust Control Association (CDCA) works to promote best practices and raise awareness about the hazards of construction dust. They provide guidance on controlling dust from various activities, including cutting and drilling concrete, and offer resources for contractors to ensure compliance with legal requirements and industry standards.
European Union (EU) Regulations
The European Union has also implemented regulations to protect workers from the risks of construction dust. The Control of Substances Hazardous to Health (COSHH) regulations require employers to assess and control exposure to hazardous substances, including construction dust. Additionally, the European Agency for Safety and Health at Work provides guidance on preventing and managing occupational risks, including dust exposure.
Local Regulations and Building Codes
It is important to note that regulations and building codes regarding construction dust control may vary by country, state, or even local municipality. Construction companies must familiarize themselves with specific requirements in their jurisdiction and ensure compliance to avoid penalties and legal consequences.
Compliance with these regulations involves implementing appropriate control measures, providing necessary personal protective equipment (PPE) to workers, conducting regular monitoring and evaluation of dust levels, and educating workers about the hazards of dust exposure and the importance of following proper safety procedures.
By staying up-to-date with regulatory guidelines and ensuring compliance, construction companies can create a safer working environment and safeguard the health of their workers. In the next section, we will explore the various measures and strategies for implementing effective dust control on construction sites.
Implementing Effective Dust Control Measures
Controlling construction dust requires a proactive approach and the implementation of effective measures to minimize its generation and spread. By implementing the right control measures, construction companies can reduce worker exposure to dust and protect the surrounding environment. Here are some essential dust control measures:
Read more: How To Control Quality In Construction
1. Engineering Controls
Engineering controls involve modifying equipment or processes to minimize dust generation. This can include using wet methods, such as wet cutting or wet grinding, to keep dust particles from becoming airborne. Additionally, enclosing work areas and using local exhaust ventilation systems can capture dust at the source and prevent its dispersion into the air.
2. Administrative Controls
Administrative controls focus on establishing policies and procedures to reduce dust exposure. This includes rotating workers to minimize prolonged exposure, scheduling tasks during low-traffic periods to minimize the impact on nearby areas, and implementing thorough cleaning protocols to remove dust from surfaces and equipment.
3. Personal Protective Equipment (PPE)
While engineering and administrative controls are the primary methods of dust control, the use of personal protective equipment (PPE) is essential to provide an additional layer of protection for workers. This can include respirators, goggles, gloves, and protective clothing, selected based on the specific hazards present on the construction site.
4. Proper Waste Management
Proper waste management is crucial to prevent the spread of dust and ensure the safe disposal of hazardous materials. Contaminated waste should be properly contained and disposed of in accordance with local regulations. Implementing a waste management plan can help track and manage hazardous materials and minimize the risk of dust exposure during disposal.
Read more: How To Clean House After Construction Dust
5. Site Monitoring and Regular Inspections
Regular monitoring and inspections of the construction site are vital to identify potential dust hazards and evaluate the effectiveness of control measures. This can involve conducting air quality monitoring, using dust meters to measure particulate levels, and inspecting equipment to ensure proper maintenance and functionality.
By combining engineering controls, administrative controls, PPE, proper waste management, and regular monitoring, construction companies can significantly reduce dust levels and protect the health and safety of workers. In the next section, we will discuss how to select the right dust control equipment for construction activities.
Selecting the Right Dust Control Equipment
When it comes to controlling construction dust, having the right equipment is crucial. By selecting the appropriate dust control equipment, construction companies can effectively mitigate dust generation and safeguard the health and safety of workers. Here are some key factors to consider when choosing dust control equipment:
1. Type of Construction Activity
The type of construction activity being performed will dictate the specific dust control equipment needed. For activities such as cutting, grinding, or drilling concrete or masonry, equipment such as wet saws, wet grinding systems, and water suppression attachments can be highly effective in minimizing dust generation.
2. Equipment Compatibility
It is important to choose dust control equipment that is compatible with the existing construction machinery and tools being used on the site. This includes considering factors such as power requirements, size, and ease of integration with the existing equipment.
3. Efficiency and Effectiveness
Assessing the efficiency and effectiveness of dust control equipment is crucial to determine its ability to reduce dust emissions. Look for equipment with features such as high-efficiency particulate air (HEPA) filters, effective water suppression systems, and adjustable airflow settings to ensure optimal performance.
4. Portability and Versatility
Consider the portability and versatility of dust control equipment, especially on construction sites with multiple work areas. Portable units or equipment that can be easily moved and adjusted can provide flexibility, allowing for dust control in various locations and during different construction phases.
5. Maintenance and Durability
Check the maintenance requirements and durability of the equipment to ensure it can withstand the demands of a construction site environment. Look for equipment with features such as easy access for cleaning and maintenance, durable construction materials, and reliable mechanisms for water supply and filtration.
6. Compliance with Regulations
Ensure that the dust control equipment meets regulatory guidelines and compliance requirements. This includes considerations such as filter efficiency, noise levels, and emissions standards set by relevant authorities.
By carefully considering these factors, construction companies can select the right dust control equipment that will effectively minimize dust generation and ensure a safer working environment. In the next section, we will explore best practices for controlling construction dust.
Read more: How To Wash Dust Mop
Best Practices for Controlling Construction Dust
Controlling construction dust requires a comprehensive approach that considers various aspects of the construction process. By implementing best practices, construction companies can minimize dust generation, protect workers, and maintain a clean and safe working environment.
1. Plan Ahead
Before starting any construction activity, develop a dust control plan that outlines the specific measures to be implemented. This includes assessing the potential dust hazards, identifying control methods, and establishing procedures for monitoring and evaluating the effectiveness of the control measures.
2. Use Engineering Controls
Implement engineering controls that focus on eliminating or minimizing dust generation at the source. Utilize water suppression systems, wet cutting or grinding methods, and dust barriers to contain and control dust particles. Enclose work areas as much as possible to prevent dust from spreading to other parts of the construction site.
3. Maintain Equipment and Tools
Regularly inspect and maintain construction equipment and tools to ensure they are in good working condition. Faulty equipment can contribute to increased dust generation and reduce the effectiveness of dust control measures. Keep blades, bits, and cutting edges sharp, as dull tools can generate more dust.
Read more: How To Store Dust Jackets
4. Provide Adequate Ventilation
Ensure proper ventilation in work areas to remove dust and maintain a healthy air quality. Use local exhaust ventilation systems to capture dust at the source and exhaust it safely away from workers. Adequate ventilation helps prevent the build-up of harmful dust particles in the air.
5. Wet Cleaning and Sweeping
Instead of dry sweeping, use wet cleaning methods to minimize the circulation of dust. Mop floors and wet wipe surfaces regularly to remove settled dust. Avoid using compressed air for cleaning, as it can disperse dust into the air and increase the risk of exposure.
6. Personal Protective Equipment
Provide appropriate personal protective equipment (PPE) to workers to minimize their exposure to dust. This includes respiratory protection such as dust masks or respirators, eye protection, gloves, and protective clothing. Train workers on the proper use and maintenance of PPE.
7. Regular Monitoring and Training
Maintain a system of regular monitoring and evaluation to assess the effectiveness of dust control measures. Conduct air quality testing and monitor dust levels to ensure compliance with regulatory limits. Additionally, provide proper training and education to workers regarding dust hazards, control measures, and the importance of following safe work practices.
By incorporating these best practices into construction processes, companies can create a safer working environment, reduce the risks associated with construction dust, and promote the health and well-being of all workers involved. In the next section, we will explore the importance of training and education in dust control.
Read more: How To Dust Furniture
Training and Education for Dust Control
Training and education play a vital role in the successful implementation of dust control measures in construction. Providing proper training and education to workers ensures that they are knowledgeable about the hazards of construction dust and equipped with the necessary skills to effectively control and minimize its impact. Here are some key aspects to consider when incorporating training and education for dust control:
1. Hazard Awareness
Train workers on the hazards associated with construction dust, including the specific risks posed by silica, asbestos, lead, and other contaminants. Educate them about the health effects, signs of exposure, and the importance of taking preventive measures to protect themselves and others.
2. Control Measures
Teach workers about the various dust control measures that should be implemented on construction sites. This includes engineering controls, administrative controls, and the proper use of personal protective equipment (PPE). Explain the purpose and effectiveness of each measure and provide practical demonstrations to ensure proper implementation.
3. Equipment and Tools
Provide training on the proper usage, maintenance, and cleaning of equipment and tools to minimize dust generation. Workers should understand how to properly set up and use dust control equipment, including ventilation systems, water suppression attachments, and dust collection devices.
Read more: How To Use Dust Mop
4. Safe Work Practices
Emphasize the importance of safe work practices to reduce dust exposure. This includes proper disposal of construction waste, avoiding dry sweeping methods, and using wet cleaning techniques. Train workers on the correct procedures for handling and removing dust-contaminated materials and the importance of proper hygiene, such as washing hands and changing clothes after exposure to dust.
5. Regulatory Compliance
Ensure workers are aware of the applicable regulatory guidelines and compliance requirements related to dust control. Educate them on the specific regulations set forth by relevant authorities, such as OSHA or local building codes. This knowledge will assist workers in understanding their responsibilities and obligations to maintain a safe working environment.
6. Ongoing Training and Reinforcement
Training and education should not be a one-time event. Continuous reinforcement and ongoing training are crucial to keep workers informed about emerging best practices and any changes in regulations. Regularly provide refresher courses, toolbox talks, or safety meetings to reinforce the importance of dust control and address any concerns or questions raised by workers.
By investing in training and education, construction companies can empower their workers with the knowledge and skills required to effectively control and minimize dust exposure. This not only benefits the health and safety of workers but also contributes to a more responsible and sustainable construction industry. In the final section, we will explore the importance of monitoring and evaluation in dust control measures.
Monitoring and Evaluation of Dust Control Measures
Monitoring and evaluating dust control measures is essential to ensure their effectiveness and make necessary adjustments to maintain a safe and healthy work environment. By implementing a systematic approach to monitoring and evaluation, construction companies can identify areas of improvement, track progress, and address any deviations from the desired standards. Here are some key aspects to consider:
Read more: How To Clean Dust Off Blinds
1. Regular Dust Monitoring
Conduct regular dust monitoring to measure and assess the levels of airborne dust particles in the construction site. This can be done using dust monitors or sampling equipment to quantitatively analyze the concentration of dust. Monitoring should be carried out at different stages of the construction process and in various work areas to capture variations and identify potential hotspots of dust generation.
2. Air Quality Testing
Perform air quality testing to determine the overall air quality on the construction site. This can involve analyzing samples for hazardous substances, such as silica, asbestos, lead, and other contaminants, to ensure compliance with regulatory standards. Air quality testing is crucial for identifying any risks to workers’ health and enabling timely corrective actions.
3. Worker Exposure Assessment
Assess the level of dust exposure that workers may face during construction activities. This can be done through personal exposure monitoring, where individual workers wear personal sampling devices to measure their actual exposure. Comparing the results with permissible exposure limits can help identify specific tasks or workers that may require additional control measures or changes in work practices.
4. Equipment Performance Evaluation
Evaluate the performance of dust control equipment regularly. This includes assessing whether the equipment is functioning optimally, performing appropriate maintenance and cleaning routines, and ensuring that the equipment is used correctly. Proper equipment performance is crucial to effectively minimize dust generation and protect workers.
Read more: How To Clean Dust From A Fan
5. Incident Reporting and Investigation
Establish a system for incident reporting and investigation to promptly address any dust-related incidents or near misses. Investigate the root causes of such incidents, analyze trends, and take corrective actions to prevent future occurrences. Incident reporting and investigation contribute to continuous improvement and help identify areas for additional training or equipment upgrades.
6. Feedback and Continuous Improvement
Encourage feedback from workers regarding the effectiveness of dust control measures and any concerns they may have. Actively seek suggestions for improvement and evaluate their feasibility and potential impact. Engaging workers in the monitoring and evaluation process fosters a culture of continuous improvement and emphasizes the importance of their input in maintaining a safe working environment.
By implementing a robust system of monitoring and evaluation, construction companies can ensure the effectiveness of their dust control measures, address any deficiencies, and continuously improve dust management practices. This commitment to monitoring and evaluation ultimately contributes to a safer and healthier working environment for all construction personnel.
Conclusion
Controlling construction dust is vital for protecting the health and safety of workers, as well as preserving the surrounding environment. Construction dust, which can contain hazardous substances such as silica, asbestos, lead, and other toxic materials, poses serious risks to those exposed to it. By implementing effective dust control measures, construction companies can mitigate these risks and create a safer working environment.
Understanding the hazards of construction dust is the first step in implementing effective control measures. By recognizing the various health risks associated with dust exposure, including respiratory diseases and the dangers of silica, asbestos, and lead, construction companies can prioritize the protection of their workers.
Compliance with regulatory guidelines and standards is imperative. Regulations set forth by organizations such as OSHA, CDCA, the EU, and local building codes establish clear requirements for dust control. By adhering to these regulations, construction companies ensure legal compliance and demonstrate their commitment to worker safety.
The implementation of effective dust control measures involves a comprehensive approach. This includes engineering controls, administrative controls, proper waste management, site monitoring, and the use of personal protective equipment. By combining these measures, construction companies can minimize dust generation and exposure, reducing the risks associated with construction dust.
Training and education are essential components of dust control. By providing workers with hazard awareness training, instruction on control measures, and guidance on equipment usage and maintenance, construction companies empower their workers to actively contribute to dust control efforts.
Monitoring and evaluation of dust control measures allow construction companies to assess their effectiveness and make necessary adjustments. Regular dust monitoring, air quality testing, worker exposure assessment, and equipment performance evaluation help identify areas for improvement and ensure ongoing compliance with standards.
In conclusion, controlling construction dust is a critical aspect of ensuring the health, safety, and well-being of workers in the construction industry. By understanding the hazards, complying with regulations, implementing effective control measures, providing training and education, and continuously monitoring and evaluating dust control efforts, construction companies can create a safer working environment for all involved. Let’s strive for a dust-free future in the construction industry and prioritize the health and safety of workers.
Frequently Asked Questions about How To Control Construction Dust
Was this page helpful?
At Storables.com, we guarantee accurate and reliable information. Our content, validated by Expert Board Contributors, is crafted following stringent Editorial Policies. We're committed to providing you with well-researched, expert-backed insights for all your informational needs.
0 thoughts on “How To Control Construction Dust”