Home>diy>Building & Construction>How To Figure Out How Much A Construction Project Will Cost
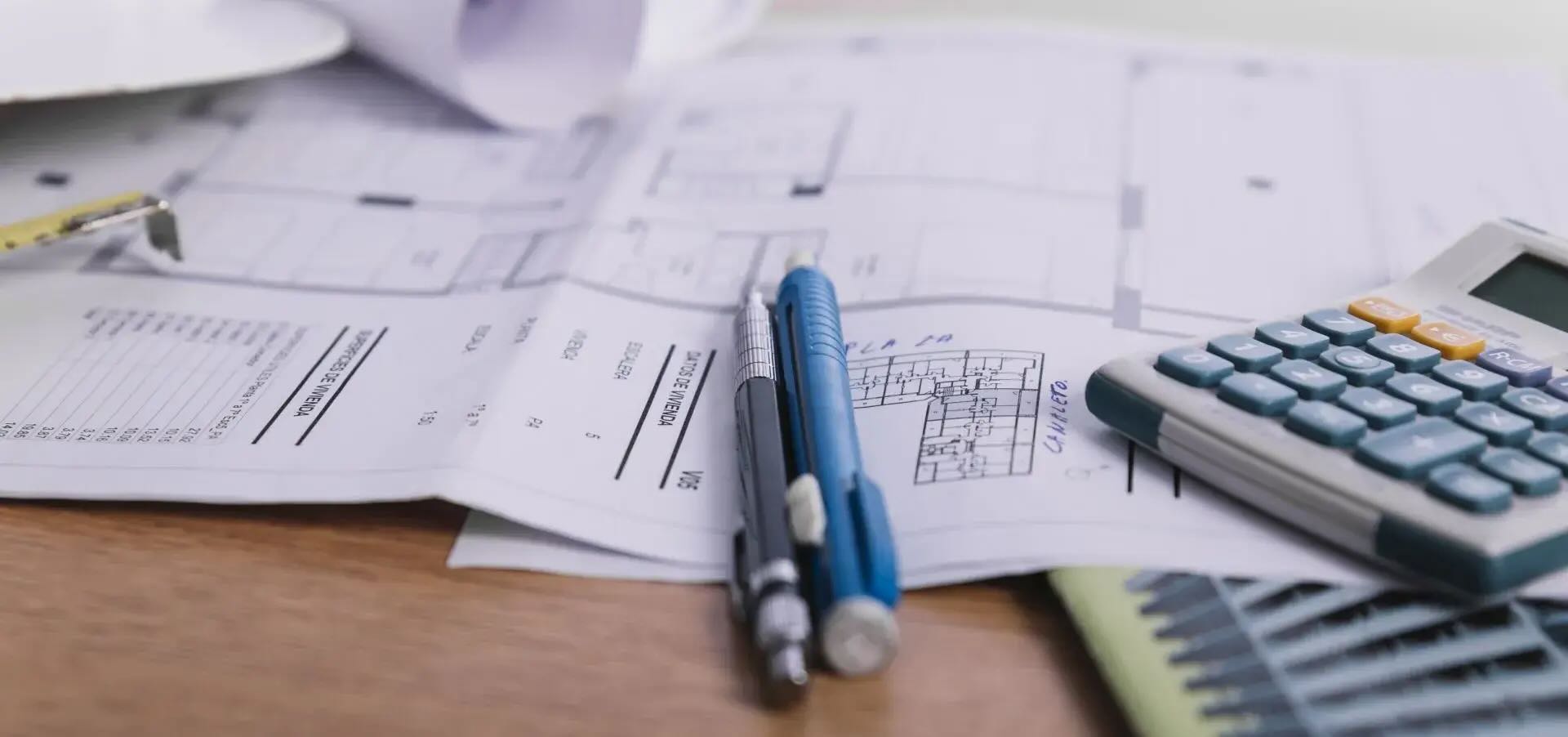
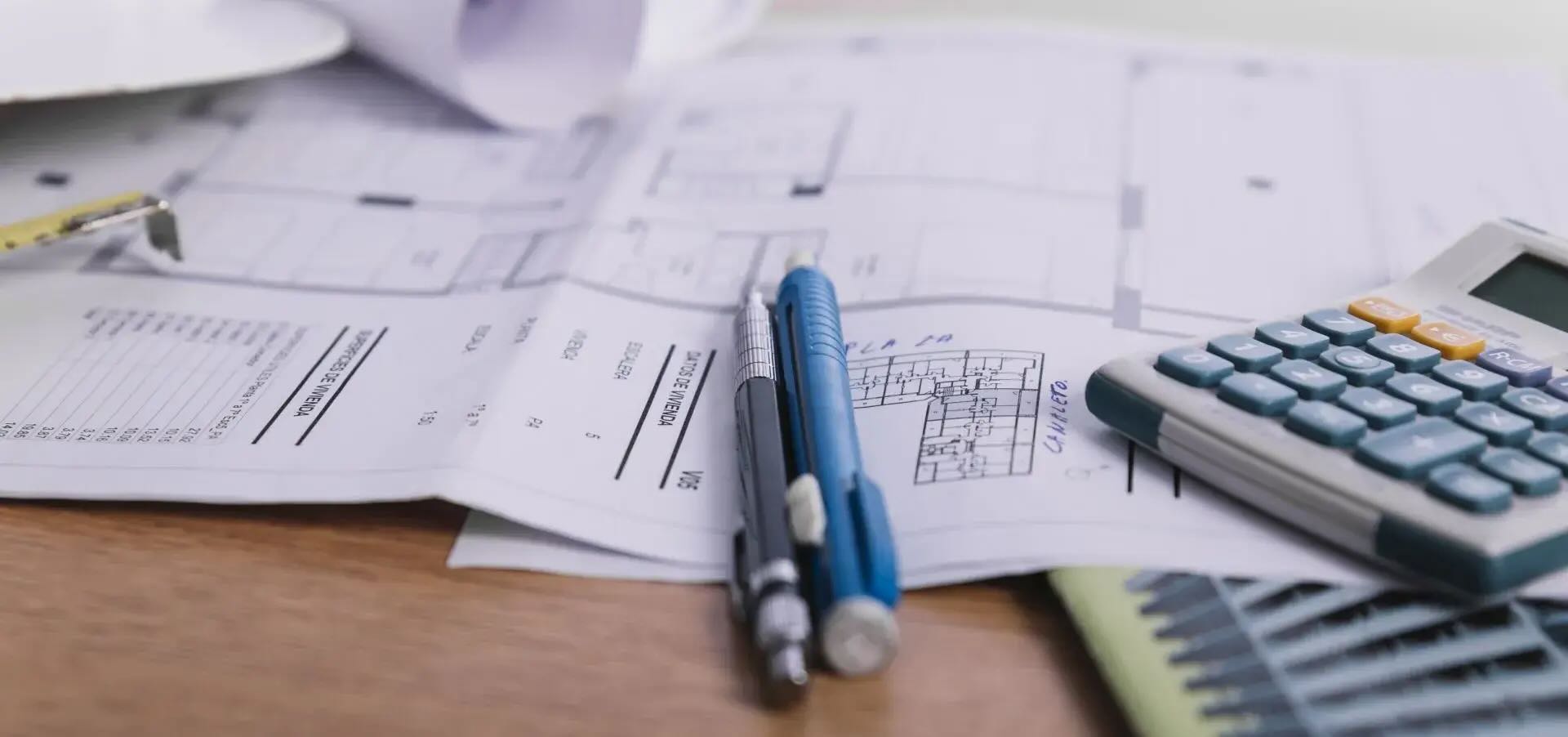
Building & Construction
How To Figure Out How Much A Construction Project Will Cost
Modified: January 6, 2024
Discover the best ways to calculate the cost of your building construction project with our comprehensive guide. Get accurate estimates and avoid unexpected expenses.
(Many of the links in this article redirect to a specific reviewed product. Your purchase of these products through affiliate links helps to generate commission for Storables.com, at no extra cost. Learn more)
Introduction
Welcome to the world of construction, where dreams are turned into reality. Building something from scratch is a true testament to human ingenuity and skill. Whether it’s a small home renovation or a massive infrastructure project, construction requires meticulous planning and execution. One of the crucial aspects of any construction project is determining how much it will cost.
Estimating the cost of a construction project is a complex task that involves considering various factors such as materials, labor, equipment, and additional expenses. The accuracy of cost estimation is crucial to ensure that the project stays within budget and is completed successfully.
In this article, we will dive deep into the process of figuring out how much a construction project will cost. We will explore the factors that influence construction costs and discuss how to estimate material, labor, and equipment expenses. We will also touch on additional costs that need to be considered and provide insights into budgeting and contingency planning.
Whether you are a homeowner planning a renovation or a professional in the construction industry, understanding the cost estimation process is essential for project success. So, let’s roll up our sleeves and get ready to unravel the mysteries of construction cost estimation. By the end of this article, you’ll have the knowledge and tools to confidently plan and budget for your next construction endeavor.
Before we dive into the specifics, it’s important to note that construction costs can vary significantly depending on various factors such as location, project scope, market conditions, and economic factors. Therefore, treat the following as a general guide, and always consult with professionals for accurate cost estimates specific to your project.
Now, let’s explore the key factors that influence construction costs and delve deeper into the estimation process.
Key Takeaways:
- Accurate cost estimation in construction projects involves thorough research, consideration of various factors, and collaboration with industry professionals to ensure a realistic budget and successful project execution.
- Understanding material, labor, and equipment costs, along with additional expenses and contingency planning, is essential for effective financial management and the overall success of construction projects.
Read more: How To Figure Out Home Repair Costs
Factors Affecting Construction Costs
Construction costs can be influenced by a variety of factors, and understanding these factors is crucial for accurate cost estimation. Here are some key factors that can significantly impact the overall cost of a construction project:
1. Project Scope: The size and complexity of the project play a significant role in determining the cost. Larger projects require more materials, labor, and time, which can increase the overall cost.
2. Location: The geographic location of the project can affect construction costs. Factors such as local labor rates, availability of materials, transportation costs, and permitting requirements can vary from one location to another.
3. Building Materials: The choice of building materials can have a significant impact on the cost. High-end materials or specialized materials may be more expensive, while utilizing cost-effective materials can help reduce expenses.
4. Site Conditions: The condition and accessibility of the construction site can affect costs. Sites with challenging terrain, poor soil conditions, or limited access may require additional resources and equipment, leading to higher costs.
5. Labor Costs: Labor is a significant component of construction costs. The cost of labor can vary depending on factors such as local labor rates, union requirements, project duration, and the skill level required for the job.
6. Seasonality: Construction costs can be influenced by the time of year the project takes place. Some materials may experience price fluctuations depending on seasonal demand, and weather conditions can impact construction timelines and costs.
7. Design Complexity: Projects with intricate or unique designs may require specific expertise, specialized materials, and additional labor, which can increase costs.
8. Regulatory Requirements: Compliance with building codes, permits, and other regulatory requirements can impact construction costs. Meeting these requirements often involves additional expenses such as inspections, fees, and documentation.
9. Market Conditions: Construction costs can be influenced by market conditions, such as supply and demand dynamics, inflation, and economic factors. Fluctuations in material and labor prices can impact project budgets.
It’s important to carefully consider these factors when estimating construction costs. Consulting with experienced professionals, such as architects, contractors, and estimators, can provide valuable insights and ensure accurate cost estimation.
In the next sections, we will explore how to estimate material, labor, and equipment costs – three key components of construction expenses. By understanding these aspects, you will have a solid foundation for determining the overall project cost.
Estimating Material Costs
Accurately estimating material costs is essential for determining the overall budget of a construction project. Here are some steps to help you effectively estimate material expenses:
1. Create a Bill of Materials: Start by creating a detailed bill of materials (BOM) that includes all the materials required for the project. This list should be comprehensive and specific, including quantities, measurements, and specifications for each item.
2. Research Material Prices: Once you have a complete BOM, research the current prices of the materials needed. Look for prices from suppliers, local vendors, and online sources. Keep in mind that prices can vary based on location and market conditions, so it’s important to gather information specific to your project’s area.
3. Consider Material Alternatives: Explore different material options that meet the project requirements but may be more cost-effective. For example, you might find similar products with different brands or grades that offer a suitable alternative at a lower cost.
4. Factor in Waste and Overages: It’s crucial to account for waste and overages when estimating material costs. Construction projects often generate waste, and it’s important to ensure you have enough materials to account for mistakes, breakage, and unexpected changes. Typically, a 5-10% overage is recommended.
5. Calculate Material Quantities: Use the BOM and project plans to calculate the quantities of each material required. Consider the dimensions, area, and volume of the project to determine accurate quantities. Use formulas, takeoffs, or specialized software to assist in the calculation process.
6. Summarize Material Costs: Multiply the quantities by the corresponding prices for each material to calculate the individual costs. Sum up the costs of all materials to get the total material cost for the project.
7. Account for Delivery and Storage Costs: Don’t forget to include delivery and storage costs in your material estimation. Determine the cost of transportation, handling, and any storage fees associated with large quantities of materials.
8. Check for Price Fluctuations: Keep in mind that material prices can change over time. Double-check your material estimations periodically to ensure the accuracy of your cost calculations, especially for projects that span several months or longer.
Remember, accuracy is key when estimating material costs. It’s always a good idea to consult with suppliers, contractors, or experienced professionals to validate your estimates and obtain more accurate pricing information specific to your project. By diligently estimating material costs, you can avoid cost overruns and ensure a smoother construction process.
Estimating Labor Costs
Estimating labor costs is an essential component of construction cost estimation. Here are some key steps to help you effectively estimate labor expenses for your project:
1. Define Labor Requirements: Start by clearly defining the labor requirements for your project. Identify the specific tasks, trades, and skills that will be needed to complete the project successfully. This could include carpenters, electricians, plumbers, painters, and more.
2. Determine Labor Hours: For each task or trade, estimate the number of labor hours required. Consider the complexity and size of the project, as well as any specific challenges that may affect labor productivity. Use historical data, industry standards, or consult with experienced professionals to get accurate estimates.
3. Research Labor Rates: Research the prevailing labor rates for each trade in your project’s location. Labor rates can vary based on factors such as experience, skill level, trade unions, and market conditions. Gather information from labor unions, contractors, and industry resources to obtain accurate rates.
4. Account for Overtime Rates: Construction projects often require overtime work, which can be subject to higher labor rates. Factor in the potential need for overtime and adjust labor costs accordingly. Additionally, be aware of any legal requirements or union regulations regarding overtime pay.
5. Consider Labor Productivity Factors: Labor productivity can be influenced by several factors, such as site conditions, weather, project complexity, and worker experience. Take into account any productivity factors that might affect labor efficiency and adjust your estimates accordingly.
6. Factor in Labor Burden: In addition to labor rates, consider the labor burden, which includes costs such as payroll taxes, insurance, benefits, and other overhead expenses. These costs typically add a percentage on top of the direct labor costs and vary based on the employer’s policies.
7. Account for Coordination and Supervision: Don’t forget to allocate labor costs for coordination and supervision. Project managers, supervisors, and administrative staff play a crucial role in ensuring the smooth operation of the construction site and should be accounted for in the labor estimation.
8. Summarize Labor Costs: Multiply the labor hours for each task or trade by the corresponding labor rates. Sum up the costs for all labor categories to obtain the total labor cost for the project.
9. Consider Subcontractor Costs: Be mindful of any subcontractor work that might be required for specialized tasks. Obtain quotes from subcontractors and factor in their costs when estimating labor expenses. Remember to account for their labor rates, labor hours, and any additional coordination or supervision fees.
Estimating labor costs accurately is essential for managing project budgets and ensuring that the necessary workforce is available throughout the construction process. Consult with experienced construction professionals to validate your labor estimates and obtain industry-specific labor rate information for the most accurate estimates possible. Through careful labor cost estimation, you can plan for an efficient and cost-effective construction project.
Before starting a construction project, gather detailed quotes from contractors, factor in materials, labor, permits, and contingency funds to accurately estimate the total cost.
Calculating Equipment Costs
Equipment costs are an important aspect of construction projects, as they involve the use of tools, machinery, and other equipment necessary to complete the work. Here are some steps to help you calculate equipment costs for your project:
1. Identify Required Equipment: Start by identifying the specific equipment needed for your project. This can include heavy machinery like excavators, cranes, or bulldozers, as well as smaller tools and equipment such as jackhammers, drills, or power saws. Make a comprehensive list of all the equipment required.
2. Research Equipment Rental Rates: Research the current rental rates for the equipment on your list. Rates can vary depending on the type of equipment, size, age, availability, and rental duration. Contact equipment rental companies, consult online platforms, or seek advice from industry professionals to get accurate rental rate information.
3. Determine Equipment Usage Duration: Estimate the number of hours or days that each piece of equipment will be needed for your project. Consider factors such as project duration, work schedule, and equipment utilization efficiency. This estimate will help determine the rental duration and associated costs.
4. Factor in Fuel and Maintenance Costs: In addition to the rental rates, consider fuel and maintenance costs associated with equipment usage. Fuel expenses can vary depending on the equipment’s fuel efficiency and the project’s requirements. Maintenance costs may include routine upkeep, repairs, and any operator training requirements.
5. Consider Insurance and Security Deposits: Some equipment rental companies require insurance coverage and security deposits. Take into account the associated costs and ensure that you have appropriate insurance coverage in place for the equipment.
6. Account for Equipment Transport: If the equipment needs to be transported to the construction site, consider the transportation costs. This can include charges for delivery and pickup, as well as any transportation permits or escort requirements.
7. Calculate Total Equipment Costs: Multiply the rental rates by the rental duration to calculate the rental cost for each equipment item. Sum up the costs for all the equipment on your list to obtain the total equipment cost for the project.
8. Evaluate Equipment Purchase vs. Rental: Depending on the project’s duration and equipment needs, it may be more cost-effective to purchase certain equipment rather than renting it. Evaluate the long-term cost implications and consider factors such as future use, maintenance, and depreciation when making this decision.
Remember to regularly review and update your equipment cost estimates throughout the project, taking into account any changes in rental rates, project timeline, or equipment requirements. This will help ensure that your budget accurately reflects the true equipment costs for the construction project.
By accurately calculating equipment costs, you can plan and budget more effectively, making informed decisions regarding the equipment needed for successful project execution. Seek advice from equipment experts and rental companies to validate your estimates and obtain specific information based on your project’s requirements.
Read more: How To Figure Out How Much Siding You Need
Additional Costs to Consider
In addition to material, labor, and equipment costs, there are several other expenses to consider when estimating the total cost of a construction project. These additional costs can have a significant impact on your budget, so it’s important to factor them in. Here are some common additional costs to consider:
1. Permits and Inspections: Obtaining necessary permits and undergoing inspections is a crucial part of the construction process. These fees can vary depending on the project’s scope, location, and permit requirements. Make sure to research and include these costs in your budget.
2. Design and Engineering Fees: If you’re working with architects, engineers, or design consultants, you’ll need to account for their fees. These professionals play a vital role in the planning and design stages of the project. Their expertise and services come at a cost, which should be included in your overall budget.
3. Legal and Insurance Expenses: Construction projects often require legal assistance and insurance coverage. Legal fees may be incurred for contract reviews, permits, or any legal disputes that arise during the project. Insurance costs include general liability insurance, builder’s risk insurance, or any other specific coverage required by the project.
4. Utilities and Temporary Services: During construction, you may need to provide temporary services such as electricity, water, and sanitation facilities. These utility costs should be factored into your budget, as they are necessary for the construction site’s operation and the comfort of the workers.
5. Site Preparation and Demolition: If the construction site requires preparation work or demolition of existing structures, these expenses need to be accounted for. This might include clearing debris, grading the land, or removing hazardous materials.
6. Landscaping and Exterior Finishes: The final touches on a construction project often involve landscaping, exterior finishes, and site cleanup. These costs can vary depending on the project’s complexity and design requirements. Consider factors such as planting, paving, fencing, and any additional exterior features when estimating these costs.
7. Contingency Fund: It’s advisable to allocate a contingency fund for unforeseen circumstances or changes that may arise during the construction process. This fund can help cover unexpected expenses, design modifications, or any unforeseen site conditions. The amount for the contingency fund is typically a percentage of the overall project cost.
8. Financing Costs: If you’re obtaining financing for your construction project, there may be additional expenses such as loan origination fees, interest charges, or project management fees. Make sure to include these costs in your budget, as they can add up throughout the project duration.
By considering these additional costs, you can create a more comprehensive and accurate budget for your construction project. Actively monitoring and reviewing these expenses during the construction process will help you stay on track and mitigate any financial surprises.
It’s important to note that these additional costs can vary depending on the specific requirements of your project. Consulting with professionals, such as construction managers, estimators, or industry experts, will provide invaluable insights and ensure you have a thorough understanding of the additional costs associated with your construction project.
Budgeting and Contingency Planning
Budgeting and contingency planning are crucial aspects of construction project management. Developing a comprehensive budget and having a contingency plan in place can help ensure that your project stays on track financially and can withstand unexpected challenges. Here are some key steps to consider when budgeting and creating a contingency plan:
1. Establish a Realistic Budget: Start by setting a realistic budget for the entire project. This includes estimating all costs we discussed earlier, such as materials, labor, equipment, and additional expenses. Make sure to account for all known costs and factor in a contingency for unforeseen circumstances.
2. Monitor Costs Throughout the Project: Regularly monitor and track costs throughout the project’s duration. This will allow you to identify any deviations or potential cost overruns early on, giving you the opportunity to address them before they become major issues. Use project management tools or software to assist in tracking and managing expenses.
3. Allocate Contingency Funds: Set aside a contingency fund within your budget. The amount for the contingency fund can vary, but a common practice is to allocate 10-15% of the total project cost. This fund acts as a buffer to cover unexpected expenses, changes, or delays that may arise during construction.
4. Identify and Assess Risks: Conduct a thorough risk assessment to identify potential risks and challenges that could impact the project’s budget. Some common risks include unforeseen site conditions, design changes, weather delays, labor shortages, or material price fluctuations. Evaluate the likelihood and potential impact of each risk and consider including additional contingency specifically for high-risk items.
5. Regularly Update the Budget and Contingency Plan: As the project progresses and new information becomes available, update your budget and contingency plan accordingly. Adjustments may be necessary due to changes in scope, unforeseen expenses, or unexpected savings. Stay proactive and make sure your budget and contingency plan reflect the most accurate and up-to-date information.
6. Communicate and Collaborate with Stakeholders: Effective communication and collaboration with all project stakeholders are crucial for successful budgeting and contingency planning. This includes contractors, subcontractors, suppliers, project managers, and financial advisors. Keep everyone informed about budget updates, potential risks, and contingency plan details to maintain transparency and alignment.
7. Procure Insurance Coverage: Consider obtaining adequate insurance coverage for your construction project. Insurance policies such as builder’s risk insurance, general liability insurance, and workers’ compensation insurance can provide additional protection against unforeseen events and potential liabilities.
8. Document and Learn from Past Projects: Take note of lessons learned from past construction projects. Assess what went well and areas where costs were underestimated or unexpected expenses occurred. Documenting and analyzing historical data can help improve future budgeting and contingency planning.
By incorporating budgeting and contingency planning into your construction project management approach, you are better prepared to navigate unexpected challenges and ensure the financial success of your project. Regularly reviewing and revising your budget and contingency plan throughout the project’s duration will help you stay on track and minimize the financial impact of unforeseen circumstances. Remember, effective financial management is key to delivering a successful construction project.
Conclusion
Estimating the cost of a construction project is a critical task that requires thorough planning, attention to detail, and knowledge of various factors that influence costs. By understanding the key components of construction costs, such as materials, labor, equipment, and additional expenses, you can create a more accurate budget and ensure the financial success of your project.
Factors such as project scope, location, materials, labor rates, and market conditions all play a role in determining construction costs. It is important to research and gather information specific to your project’s requirements to make accurate estimations.
Estimating material costs involves creating a detailed bill of materials, researching material prices, considering alternatives, factoring in waste and overages, and calculating quantities and costs. Labor costs estimation entails defining labor requirements, determining labor hours, researching labor rates, factoring in productivity factors, and accounting for coordination and supervision.
Calculating equipment costs involves identifying required equipment, researching rental rates, determining usage duration, factoring in fuel and maintenance costs, and considering transportation and insurance expenses. Additionally, there are other expenses to consider, such as permits, inspections, design fees, legal and insurance expenses, utilities, and contingency funds.
When budgeting and creating a contingency plan, it is important to set a realistic budget, monitor costs throughout the project, allocate contingency funds, identify and assess risks, regularly update the budget and contingency plan, communicate with stakeholders, procure insurance coverage, and learn from past projects.
By following these guidelines and consulting with professionals in the construction industry, you can better plan, budget, and manage your construction projects. Accurate cost estimation and effective financial management are essential for successful project execution, ensuring that your vision becomes a reality within the stipulated budget.
Remember, construction costs can vary based on numerous factors, so it is always advisable to seek specific advice and input from experts for your project’s unique requirements. With careful planning and accurate estimation, you can embark on your construction journey with confidence, knowing that you are equipped with the knowledge and tools necessary to navigate the financial aspects of the project.
Frequently Asked Questions about How To Figure Out How Much A Construction Project Will Cost
Was this page helpful?
At Storables.com, we guarantee accurate and reliable information. Our content, validated by Expert Board Contributors, is crafted following stringent Editorial Policies. We're committed to providing you with well-researched, expert-backed insights for all your informational needs.
0 thoughts on “How To Figure Out How Much A Construction Project Will Cost”