Home>diy>Building & Construction>How To Reduce Construction Cost
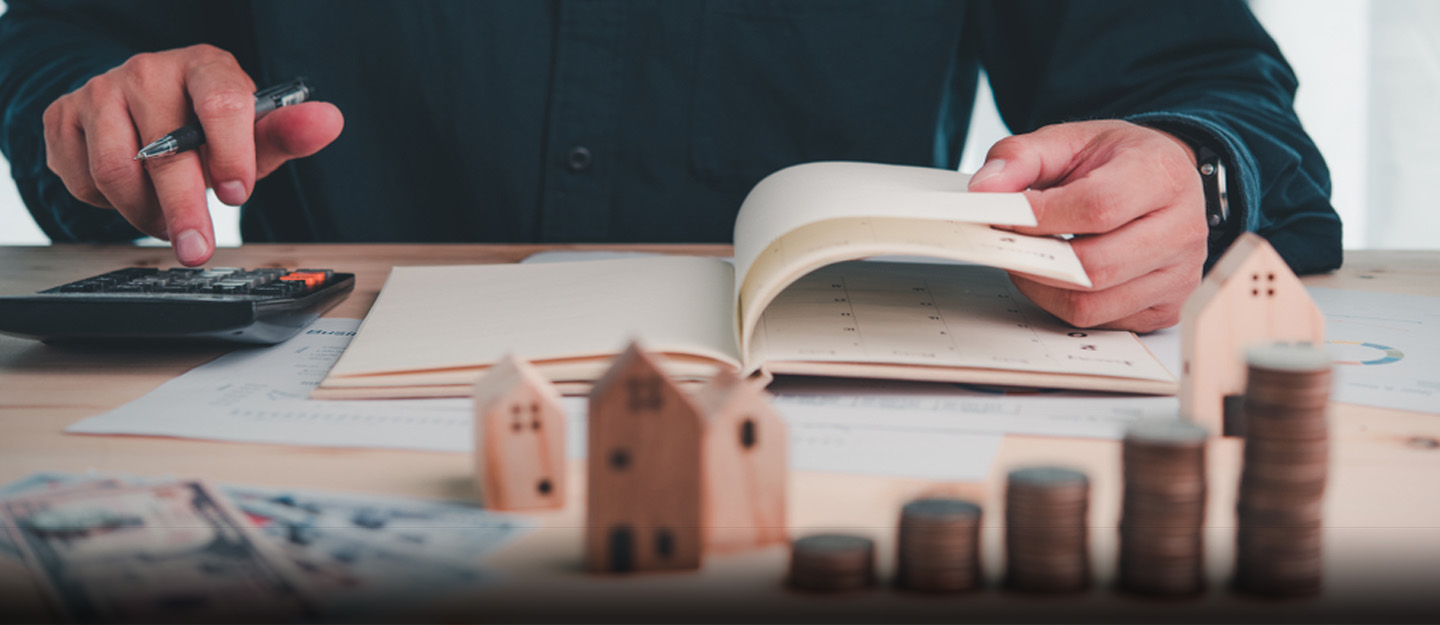
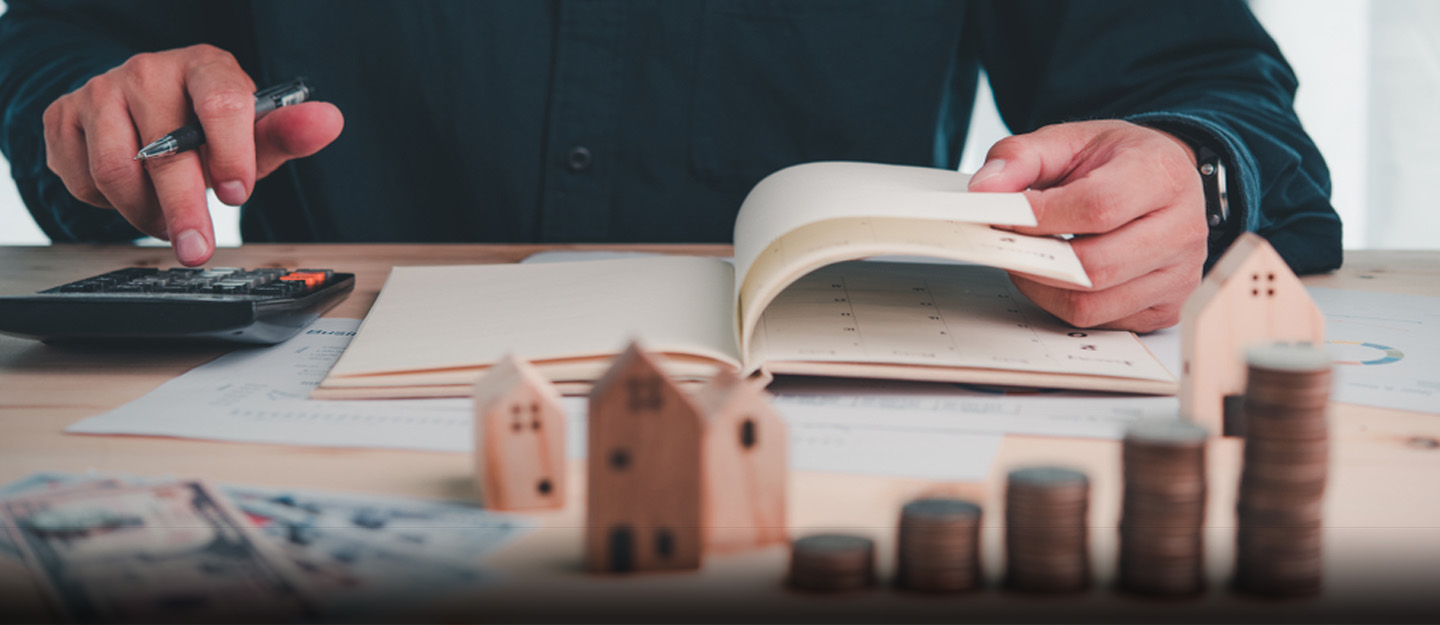
Building & Construction
How To Reduce Construction Cost
Modified: December 7, 2023
Learn effective strategies to minimize building construction costs and maximize your budget with our comprehensive guide on reducing construction expenses.
(Many of the links in this article redirect to a specific reviewed product. Your purchase of these products through affiliate links helps to generate commission for Storables.com, at no extra cost. Learn more)
Introduction
Construction projects can often come with hefty price tags, making it essential for builders and project managers to find ways to reduce construction costs. By employing efficient planning, value engineering, material optimization, and leveraging technology, construction professionals can effectively minimize expenses without compromising on quality.
In this article, we will delve into various strategies that can help you reduce construction costs without sacrificing the integrity and safety of the project. Whether you are embarking on a residential, commercial, or industrial construction project, these techniques can make a significant difference in your bottom line.
By analyzing project requirements, efficiently planning and designing, optimizing materials, streamlining construction processes, implementing sustainable practices, utilizing effective project management, and leveraging technology advancements such as prefabrication and modular construction, you can achieve substantial cost savings.
So, let’s dive into the details of each strategy and explore how they can be implemented successfully to reduce construction costs.
Key Takeaways:
- Efficient planning, value engineering, material optimization, and leveraging technology are crucial for reducing construction costs without compromising quality. Thorough analysis, sustainable practices, and prefabrication also contribute to significant cost savings.
- Embracing innovative technologies like BIM, drones, and automation, along with prefabrication and modular construction, streamlines processes, reduces labor costs, and improves project efficiency, leading to substantial cost savings.
Read more: How To Reduce Construction Noise
Analyzing Project Requirements
The first step in reducing construction costs is a thorough analysis of project requirements. Understanding the scope, scale, and unique specifications of the project allows you to make informed decisions throughout the construction process. Conducting a detailed feasibility study, site survey, and environmental impact assessment can help identify potential challenges and cost-saving opportunities.
By understanding the project requirements from the start, you can develop accurate cost estimates and allocate resources more efficiently. This includes assessing the type of materials, labor requirements, equipment, and machinery needed for the project. It’s crucial to consider factors such as site accessibility, local building regulations, and any specific customization requests from the client.
Efficient Planning and Design
Efficient planning and design are essential to reduce construction costs. Collaborate with architects, engineers, and design professionals to create cost-effective and practical design solutions. Emphasize functionality, practicality, and avoid unnecessary complexities that may inflate project costs.
Consider using Building Information Modeling (BIM) software to create 3D digital models that allow you to visualize the project and identify potential clashes or conflicts before construction begins. BIM also helps in accurate scheduling, quantity take-offs, and cost estimation.
Value Engineering
Value engineering is a systematic approach to evaluate and improve the value and functionality of a project while reducing costs. It involves analyzing each component of the project to identify potential alternatives that can achieve the same or better results at a lower cost.
During the value engineering process, professionals from various disciplines collaborate to brainstorm cost-saving ideas. This can include exploring alternative materials, construction methods, or equipment that offer comparable performance at a reduced price. By implementing value engineering techniques, you can maximize project value while keeping costs under control.
Material Optimization
Optimizing material usage is another effective strategy for reducing construction costs. Wasted or excess materials can significantly impact the project budget. Conduct a thorough inventory of materials, plan material deliveries to coincide with construction timelines, and manage waste effectively.
Consider sourcing materials from local suppliers as this can help reduce transportation costs. Additionally, explore opportunities to reuse or recycle materials from demolition or construction waste, reducing the need for new materials.
Key Takeaways:
- Efficient planning, value engineering, material optimization, and leveraging technology are crucial for reducing construction costs without compromising quality. Thorough analysis, sustainable practices, and prefabrication also contribute to significant cost savings.
- Embracing innovative technologies like BIM, drones, and automation, along with prefabrication and modular construction, streamlines processes, reduces labor costs, and improves project efficiency, leading to substantial cost savings.
Read more: How To Reduce Construction Noise
Analyzing Project Requirements
The first step in reducing construction costs is a thorough analysis of project requirements. Understanding the scope, scale, and unique specifications of the project allows you to make informed decisions throughout the construction process. Conducting a detailed feasibility study, site survey, and environmental impact assessment can help identify potential challenges and cost-saving opportunities.
By analyzing project requirements from the start, you can develop accurate cost estimates and allocate resources more efficiently. This includes assessing the type of materials, labor requirements, equipment, and machinery needed for the project. It’s crucial to consider factors such as site accessibility, local building regulations, and any specific customization requests from the client.
During the analysis phase, it’s important to engage in open communication with stakeholders, including the client, architects, engineers, and subcontractors. By understanding their expectations and goals for the project, you can align your construction plans and make informed decisions that optimize costs.
A feasibility study is a critical part of project analysis. It involves evaluating the technical, economic, and legal aspects of the project to determine its viability. This includes assessing factors such as market demand, financial projections, and potential risks. By conducting a comprehensive feasibility study, you can identify any red flags or opportunities to optimize costs at an early stage.
Another aspect of project analysis is conducting a site survey. This involves assessing the site’s characteristics, including topography, soil condition, accessibility, and any potential environmental constraints. Understanding the site’s unique features allows you to plan construction activities more efficiently and avoid costly surprises.
An environmental impact assessment is crucial, especially for large-scale construction projects. It helps identify potential environmental risks and ensures compliance with environmental regulations. By addressing environmental concerns upfront, you can avoid costly fines or delays during the construction process.
Furthermore, consider collaborating with local authorities and stakeholders to gain insights into any specific building regulations or permits required for the project. By staying informed of local regulations, you can avoid costly violations and ensure a smooth construction process.
By investing time and effort into thoroughly analyzing project requirements, you can make informed decisions that optimize costs and mitigate potential risks. It sets a solid foundation for the next steps in the construction process, ultimately contributing to the overall success of the project.
Efficient Planning and Design
Efficient planning and design are essential to reduce construction costs. By collaborating with architects, engineers, and design professionals, you can create cost-effective and practical design solutions. The goal is to emphasize functionality, practicality, and avoid unnecessary complexities that may inflate project costs.
During the planning phase, it’s important to establish clear project objectives and goals. This includes understanding the client’s vision, budget constraints, and desired timeline. By aligning everyone’s expectations from the outset, you can ensure that the planning and design process is focused on meeting those goals while minimizing costs.
Consider conducting regular design review meetings to evaluate the progress and feasibility of the design. By involving key stakeholders, such as contractors or subcontractors, you can gain valuable insights and identify potential cost-saving ideas at an early stage.
The use of Building Information Modeling (BIM) software is becoming increasingly popular in the construction industry. BIM allows for creating 3D digital models that provide a comprehensive understanding of the project. This technology enables collaboration across different disciplines, improves coordination, and enhances communication between the project team members.
By utilizing BIM, you can identify clashes or conflicts between different building systems (e.g., electrical and plumbing) before construction begins. This minimizes the need for costly on-site revisions and ensures a smoother construction process.
BIM can also help with accurate scheduling, quantity take-offs, and cost estimation. By having a detailed digital representation of the project, you can more accurately estimate the quantities of materials, labor, and equipment required. This reduces the risk of over or underestimating project costs and allows for better budget planning.
During the planning and design phase, it’s crucial to consider the lifecycle costs of the building. This includes evaluating the long-term operational and maintenance costs of the structure. By incorporating energy-efficient design principles and selecting durable materials, you can reduce future expenses and improve the overall sustainability of the building.
Additionally, explore opportunities for value engineering during the design phase. Value engineering involves analyzing each component of the design to identify potential alternatives that offer the same or better results at a lower cost. By engaging in value engineering discussions, you can optimize the design while minimizing expenses.
Efficient planning and design go hand-in-hand in reducing construction costs. By prioritizing functionality, utilizing BIM technology, considering lifecycle costs, and exploring value engineering opportunities, you can create a cost-effective and practical design that meets the project’s objectives while keeping expenses under control.
Value Engineering
Value engineering is a systematic approach to evaluate and improve the value and functionality of a project while reducing costs. It involves analyzing each component of the project to identify potential alternatives that can achieve the same or better results at a lower cost.
Value engineering is typically conducted during the planning and design phase of a construction project. It brings together professionals from various disciplines, including architects, engineers, contractors, and subcontractors, to brainstorm cost-saving ideas and explore innovative solutions.
The goal of value engineering is not to compromise on the quality or integrity of the project but to find more efficient ways to achieve the desired outcomes. By challenging conventional approaches, value engineering aims to optimize resources and minimize waste.
During the value engineering process, the project team evaluates various aspects of the project, such as materials, construction methods, systems, or equipment. By considering different options, they can identify opportunities to reduce costs without sacrificing functionality or performance.
One of the key principles of value engineering is to focus on the value provided by a particular component or system rather than solely on its cost. By understanding the benefits and functions of each element, the team can determine if there are alternative options that can deliver the same value at a lower cost.
For example, the team may explore alternative construction materials that offer the same structural integrity but at a lower cost. They may also consider different construction methods or systems that are more efficient and cost-effective without compromising on quality or safety.
During the value engineering process, it’s important to consider the long-term cost implications. While a particular option may be cheaper upfront, it may result in higher maintenance or operational costs over the life cycle of the building. Evaluating these factors helps ensure that cost savings are sustainable in the long run.
Effective communication and collaboration are critical in value engineering. By involving key stakeholders from different disciplines, you can leverage their expertise and insights to identify cost-saving opportunities. Open discussions and brainstorming sessions allow for the exploration of diverse perspectives, leading to innovative and cost-effective solutions.
Value engineering is an ongoing process that should be integrated throughout the entire project lifecycle. By regularly reviewing and evaluating the project, you can identify new opportunities to optimize costs and improve value.
By implementing value engineering techniques, construction professionals can maximize the value of a project while keeping costs under control. This approach promotes innovation, collaboration, and efficiency, ultimately leading to successful and cost-effective construction projects.
Read more: How To Reduce Construction Dust
Material Optimization
Optimizing material usage is a crucial strategy for reducing construction costs. Wasted or excess materials can significantly impact the project budget. By implementing material optimization techniques, construction professionals can minimize waste, reduce costs, and improve overall project efficiency.
One of the first steps in material optimization is conducting a thorough inventory of the required materials. By accurately estimating the quantities needed, you can avoid overordering or underordering materials, both of which can lead to unnecessary expenses.
Plan material deliveries in line with the construction schedule. Ordering materials just in time can help minimize storage costs and reduce the risk of theft or damage. Work closely with suppliers and subcontractors to coordinate deliveries and ensure that materials are available when needed.
Consider using standardized material sizes and dimensions whenever possible. Standardization allows for more efficient use of materials, reduces waste from cutting or trimming, and simplifies the construction process. It also facilitates easier and quicker replacements in case of damage or repairs.
Explore opportunities to reuse or recycle materials whenever feasible. For example, salvaging materials from demolition sites or repurposing excess materials from one project to another can significantly reduce costs. Implementing waste management strategies, such as sorting and recycling, helps minimize landfill waste and contributes to a more sustainable construction process.
Using alternative materials is another way to optimize costs. Research and consider materials that are more cost-effective, readily available, or require fewer resources for installation. However, it’s essential to ensure that the alternative materials meet the project’s quality and performance requirements.
Collaborate with suppliers to negotiate pricing and explore discounts or bulk-buying options. Building strong relationships with suppliers can lead to cost savings and better overall material management.
Additionally, consider using recycled or reclaimed materials in construction. This not only helps reduce project costs but also promotes sustainability and environmental stewardship. Strategies such as using recycled concrete or reclaimed wood can significantly lower material expenses without compromising structural integrity.
Efficient storage and inventory management systems are crucial for material optimization. Proper organization and tracking of materials can help avoid losses, theft, or spoilage. It enables easy identification, reduces the risk of duplicate orders, and ensures that materials are used efficiently.
Investigate alternatives to traditional construction materials. For example, lightweight and high-performance materials may have higher upfront costs but can lead to long-term savings by reducing labor, transportation, and energy expenses.
Regularly review the construction plans and adjust material requirements accordingly. As the project progresses, there may be opportunities to fine-tune material quantities or substitute materials based on evolving needs. Regular communication with the project team is vital to ensure that material optimization strategies are implemented effectively.
By implementing material optimization techniques, construction professionals can effectively reduce waste, lower project costs, and enhance the overall efficiency of the construction process. Making strategic decisions about material selection, storage, and usage contributes to sustainable construction practices and improved project profitability.
Consider using alternative materials or construction methods that are cost-effective without compromising quality and safety. Additionally, efficient project management and careful planning can help reduce unnecessary expenses.
Streamlining Construction Process
Streamlining the construction process is a crucial step in reducing costs and improving overall project efficiency. By optimizing workflow, eliminating inefficiencies, and improving coordination, construction professionals can minimize delays, reduce labor costs, and maximize productivity.
Effective project scheduling is key to streamlining the construction process. Create a detailed construction schedule that outlines the sequence of activities, dependencies, and deadlines. This allows for better resource allocation and helps identify potential bottlenecks or conflicts that could delay the project. Regularly review and update the schedule to ensure that it remains accurate and aligned with the project’s needs.
Collaboration and communication among project team members are vital for streamlining the construction process. Foster a culture of open communication and encourage regular meetings or coordination sessions to discuss project progress, address challenges, and make timely decisions. Use technology tools, such as project management software or cloud-based platforms, to facilitate communication and information sharing.
Implementing lean construction principles can also help streamline the construction process. Lean construction focuses on eliminating waste, improving productivity, and maximizing value for the client. This approach involves analyzing and optimizing every step of the construction process to minimize non-value-added activities, such as waiting time, rework, or excessive handling of materials.
Standardizing construction processes and utilizing prefabrication or modular construction techniques can significantly streamline the construction process. Prefabrication involves constructing building components off-site and then assembling them at the construction site. This allows for better quality control, faster construction, and reduced labor costs. Modular construction, on the other hand, involves assembling pre-made modules to create a complete structure. This technique offers similar benefits, including faster construction and minimized on-site labor requirements.
Proactive risk management is another important aspect of streamlining the construction process. Identify potential risks and develop contingency plans to mitigate them. By identifying and addressing challenges ahead of time, you can minimize delays, unexpected costs, and disruptions to the construction schedule.
Continuous improvement is a key principle of streamlining construction processes. Encourage feedback from the project team and subcontractors to identify areas for improvement. Regularly review project performance and analyze data to identify trends or patterns that can inform future process enhancements. This cycle of learning and improvement ensures that construction processes become more efficient over time.
Investing in training and skills development for project team members is essential for streamlining the construction process. Ensure that workers have the necessary skills and knowledge to perform their tasks efficiently. Regularly provide training sessions to enhance technical skills, promote safety, and improve overall productivity.
Implementing technology tools and software can also help streamline construction processes. Consider using project management software, digital document management systems, and mobile apps that allow for real-time communication and access to project information. Automation of repetitive tasks and the use of digital tools can reduce manual errors, improve accuracy, and increase productivity.
By streamlining the construction process through effective scheduling, collaboration, lean principles, prefabrication or modular construction, risk management, continuous improvement, training, and technology adoption, construction professionals can reduce costs, enhance productivity, and deliver projects more efficiently.
Implementing Sustainable Practices
Implementing sustainable practices in construction is not only beneficial for the environment but can also lead to cost savings and increased efficiency. By focusing on environmentally friendly and resource-efficient strategies, construction professionals can reduce waste, minimize energy consumption, and enhance the long-term sustainability of the project.
One of the key sustainable practices in construction is optimizing energy efficiency. Incorporate energy-efficient design principles, such as proper insulation, high-performance windows, and efficient HVAC systems. These measures can reduce energy consumption and lower operating costs for the building over its lifetime.
Utilize renewable energy sources wherever feasible. Consider incorporating solar panels, wind turbines, or geothermal systems to generate clean energy for the building. Investing in renewables not only reduces dependence on fossil fuels but also offers potential long-term cost savings through reduced electricity bills.
Water conservation is another important aspect of sustainable construction. Implement water-saving fixtures, such as low-flow toilets, faucets, and showerheads, to reduce water consumption. Harvesting rainwater or implementing greywater recycling systems can also help conserve water and reduce the strain on municipal water supplies.
Promote sustainable material choices by considering environmentally friendly options. Use materials with low embodied energy and a high percentage of recycled content. Select materials that are locally sourced to decrease transportation-related emissions and support the local economy. Additionally, prioritize the use of materials that can be recycled or reused at the end of their lifespan.
Implement waste management strategies to minimize construction waste. Set up recycling stations on-site to separate and recycle materials such as metal, plastic, wood, and concrete. Donate or repurpose surplus materials instead of sending them to the landfill. Proper waste management not only reduces environmental impact but can also lower disposal costs and potentially generate revenue through material reuse or recycling.
Encourage sustainable transportation practices. Provide designated parking areas for bicycles and promote the use of public transportation for both workers and stakeholders. Incorporate electric vehicle charging stations to support the transition to sustainable transportation options.
Consider incorporating green spaces and landscaping in the project. Green roofs, living walls, and vegetation can contribute to improved air quality, reduced heat island effect, and increased biodiversity. These features not only enhance the aesthetic appeal of the building but also provide additional benefits for occupants and the surrounding environment.
Embrace sustainable construction certifications and standards. Seek certifications such as LEED (Leadership in Energy and Environmental Design) or BREEAM (Building Research Establishment Environmental Assessment Method) to demonstrate your commitment to sustainable practices. Green building certifications not only enhance the marketability of the project but also provide guidelines and benchmarks for sustainable design and construction.
Continuously monitor and evaluate the sustainability performance of the project. Conduct regular energy audits to identify opportunities for improving energy efficiency. Analyze water usage and waste generation data to identify trends and areas for improvement. Regularly review sustainability goals and targets to ensure progress is being made.
By implementing sustainable practices in construction, professionals can reduce environmental impact, improve energy efficiency, and promote long-term cost savings. Incorporating energy-efficient design, utilizing renewable energy, conserving water, selecting sustainable materials, practicing waste management, encouraging sustainable transportation, incorporating green spaces, and pursuing green certifications are all steps in the right direction. Sustainable construction is not only beneficial for the planet but can also positively impact the project’s bottom line.
Effective Project Management
Effective project management is paramount to reducing construction costs and ensuring the successful completion of a project. By implementing robust project management techniques, construction professionals can optimize resources, streamline processes, and mitigate risks, leading to improved efficiency and cost savings.
A key aspect of effective project management is thorough planning. Develop a comprehensive project plan that includes clear objectives, deliverables, timelines, and milestones. This plan serves as a roadmap for the project, allowing for better coordination and resource allocation.
Identify and assemble a skilled and experienced project team. Assign roles and responsibilities to ensure each team member understands their tasks and deliverables. Regularly communicate and provide avenues for collaboration to foster a sense of ownership and accountability within the team.
Implement a robust communication strategy to facilitate effective and timely communication throughout the project. Regularly scheduled meetings, progress reports, and well-defined lines of communication ensure that all team members and stakeholders are informed and aligned on project goals and progress. Utilize project management software or collaboration platforms to streamline communication and document sharing.
Implement risk management strategies to identify and mitigate potential obstacles that may lead to increased costs or delays. Conduct regular risk assessments and develop contingency plans to address unforeseen circumstances. Regularly monitor and evaluate project risks to stay proactive in managing potential issues.
Monitor and control project costs throughout the construction process. Regularly review and track expenses against the project budget to identify any deviations or potential cost overruns. Implement cost control measures, such as value engineering, to optimize costs without compromising quality.
Establish strong relationships with suppliers and subcontractors. Negotiate favorable contracts and terms to secure competitive pricing. Regularly communicate with suppliers to ensure timely delivery of materials and equipment, avoiding costly delays or project disruptions.
Implement a robust change management process to effectively manage changes to the project scope, schedule, and budget. Clearly document and communicate changes to all stakeholders, assessing their impact and managing expectations accordingly. Open and transparent communication during the change management process is vital to avoid cost escalations and ensure stakeholder satisfaction.
Utilize technology tools, such as project management software or mobile apps, to streamline project management processes. These tools can help with scheduling, documentation management, communication, and collaboration, enhancing overall project efficiency and reducing administrative overhead.
Regularly track and monitor project progress against the established timeline and milestones. Identify any bottlenecks or areas of inefficiency and take corrective action promptly. Conduct regular project reviews and lessons learned sessions to identify areas for improvement and implement best practices in future projects.
Lastly, continuously evaluate and assess project performance to identify opportunities for improvement. Regularly communicate with clients to ensure their satisfaction and gather feedback for future enhancement.
Effective project management is essential for reducing construction costs and delivering projects on time and within budget. Thorough planning, strong communication and collaboration, proactive risk management, cost control, supplier management, change management, utilizing technology tools, monitoring progress, and continuous evaluation are all critical components of effective project management in the construction industry.
Leveraging Technology
Leveraging technology is crucial in the construction industry to improve efficiency, reduce costs, and enhance project outcomes. By embracing and utilizing innovative technologies, construction professionals can streamline processes, improve communication and collaboration, and optimize resource utilization.
One of the key technologies transforming the construction industry is Building Information Modeling (BIM). BIM is a digital representation of the physical and functional characteristics of a building or infrastructure. It enables collaboration among project stakeholders, including architects, engineers, contractors, and subcontractors, throughout the project lifecycle.
By utilizing BIM, construction professionals can visualize the project in a 3D digital model, facilitating better coordination and reducing clashes or conflicts between different systems or components. BIM also aids in accurate quantity take-offs, cost estimation, and scheduling, leading to improved project planning and cost control.
The use of drones in construction has become increasingly popular. Drones can capture aerial images and videos of construction sites, offering a unique perspective and enabling efficient monitoring of progress. They can also be used for surveying, mapping, inspections, and safety assessments, reducing manual labor and increasing overall project efficiency.
Real-time communication and collaboration platforms play a crucial role in streamlining project management. Cloud-based project management software allows for easy information sharing, document management, issue tracking, and progress monitoring. This facilitates real-time collaboration, reduces administrative overhead, and enhances overall project coordination.
Advanced project scheduling software enables construction professionals to create detailed and dynamic schedules that take into account the project’s intricacies. These software solutions allow for better resource allocation, identification of critical path activities, and visualization of project timelines. By using these tools, project managers can optimize construction schedules, reduce delays, and improve overall productivity.
Mobile apps tailored to the construction industry offer features such as time tracking, task management, on-site communication, and safety checklists. These apps enhance on-site efficiency, simplify documentation processes, and improve communication between project team members and contractors.
Geo-positioning systems and Global Positioning System (GPS) technology help enhance accuracy and efficiency in tasks such as surveying, mapping, and equipment tracking. By leveraging GPS technology, construction professionals can precisely position equipment, streamline material deliveries, and optimize the utilization of resources.
Construction automation and robotics are transforming traditional construction practices. Automated systems and robots can perform repetitive or labor-intensive tasks with higher precision and efficiency. This reduces the reliance on manual labor, minimizes errors, improves safety, and accelerates construction timelines.
Virtual Reality (VR) and Augmented Reality (AR) technologies offer immersive experiences to visualize and experience the completed project before construction begins. These tools are valuable for architects, engineers, and clients to understand and make informed decisions during the design and planning stages.
Artificial Intelligence (AI) and machine learning algorithms can analyze vast amounts of data, enabling predictive analytics and improved decision-making. AI-powered software solutions can automate mundane tasks and provide valuable insights into project performance, cost estimation, and risk assessment, resulting in optimized construction processes.
By leveraging technology, construction professionals can unlock significant benefits in terms of cost savings, efficiency gains, improved safety, and enhanced project outcomes. Embracing technologies such as BIM, drones, project management software, mobile apps, GPS, automation, VR/AR, and AI empowers construction teams to adapt to industry demands, stay competitive, and thrive in the digital era.
Utilizing Prefabrication and Modular Construction
Prefabrication and modular construction are innovative methods that offer numerous advantages in terms of cost savings, time efficiency, and quality control. By embracing these techniques, construction professionals can streamline processes, reduce construction costs, improve project schedules, and enhance overall project outcomes.
Prefabrication involves manufacturing building components off-site in a controlled factory environment. These components, such as walls, floors, and entire building modules, are then transported to the construction site for assembly. Prefabrication allows for parallel workstreams, with construction and factory production happening simultaneously, saving valuable time compared to traditional on-site construction.
One of the main advantages of prefabrication is its ability to reduce labor costs. With construction occurring in a factory, tasks can be performed more efficiently with specialized equipment and a skilled workforce. This reduces the reliance on on-site labor and decreases labor-related expenses.
Additionally, the controlled factory environment minimizes the impact of weather conditions on construction activities. This eliminates weather-related delays, allowing for consistent progress and adherence to project schedules. As a result, project timelines are shortened, reducing holding costs and the potential for cost overruns.
Prefabrication also enhances quality control. In a factory setting, builders can closely monitor and maintain consistent quality standards throughout the construction process. Standardization in the manufacturing process ensures that all components meet the same specifications, resulting in higher quality and reduced rework on site.
Modular construction takes prefabrication a step further by assembling pre-made modules to create a complete building. These modules can be manufactured with high precision and efficiently transported to the site for assembly. Modular construction offers similar benefits to prefabrication, including reduced labor costs, shorter timelines, improved quality control, and reduced environmental impact.
Both prefabrication and modular construction provide opportunities for reusing materials. Off-site manufacturing allows for careful management and optimization of material usage, minimizing waste. Surplus materials can be reused in subsequent projects, reducing additional material costs and promoting sustainability.
Furthermore, prefabrication and modular construction can help mitigate disruptions to the surrounding community. Since much of the construction process occurs off-site, noise, dust, and traffic congestion at the construction site are significantly reduced. This can lead to improved relations with neighbors and minimize potential complaints or legal issues.
It’s important to note that integrating prefabrication and modular construction requires careful planning and coordination. Collaboration among architects, engineers, manufacturers, contractors, and subcontractors is crucial to ensure seamless integration of prefabricated components or modules into the overall project design.
By utilizing prefabrication and modular construction, construction professionals can benefit from reduced labor costs, shorter project schedules, improved quality control, increased sustainability, and minimized disruptions. These methods not only enhance project efficiency but also offer cost savings and improved overall project outcomes.
Conclusion
Reducing construction costs requires a comprehensive approach that incorporates efficient planning, value engineering, material optimization, streamlined construction processes, sustainable practices, effective project management, leveraging technology, and utilizing prefabrication and modular construction. By implementing these strategies, construction professionals can achieve significant cost savings without compromising the integrity and quality of the project.
Thoroughly analyzing project requirements and conducting feasibility studies allows for accurate cost estimates and efficient resource allocation. Efficient planning and design emphasize functionality and avoid unnecessary complexities, optimizing construction processes from the outset.
Value engineering techniques explore alternative options to achieve the same or better results at a lower cost. Material optimization minimizes waste, maximizes resource usage, and incorporates sustainable material choices. Streamlining the construction process through effective project management ensures proper coordination, risk mitigation, and cost control.
Leveraging technology tools, such as BIM, drones, project management software, and automation, enhances efficiency and communication. Sustainable practices, including energy efficiency, water conservation, waste management, and green certifications, promote environmental stewardship and long-term cost savings.
Prefabrication and modular construction methods offer advantages in terms of reduced labor costs, shortened timelines, improved quality control, and minimized disruptions. These innovative approaches optimize construction processes, maximize resource usage, and enhance project efficiency.
In conclusion, reducing construction costs is about finding a balance between delivering quality projects within budget constraints. By employing these strategies, construction professionals can achieve significant cost savings, improve project timelines, enhance sustainability, and ensure successful project outcomes.
Adapting to evolving industry needs and embracing innovative approaches is key to staying competitive in the construction industry. By continuously incorporating cost-saving strategies and leveraging technology advancements, construction professionals can navigate the challenges of cost management and deliver successful projects that meet client expectations and industry standards.
Frequently Asked Questions about How To Reduce Construction Cost
Was this page helpful?
At Storables.com, we guarantee accurate and reliable information. Our content, validated by Expert Board Contributors, is crafted following stringent Editorial Policies. We're committed to providing you with well-researched, expert-backed insights for all your informational needs.
0 thoughts on “How To Reduce Construction Cost”