Home>diy>Building & Construction>How To Improve Productivity In Construction Industry
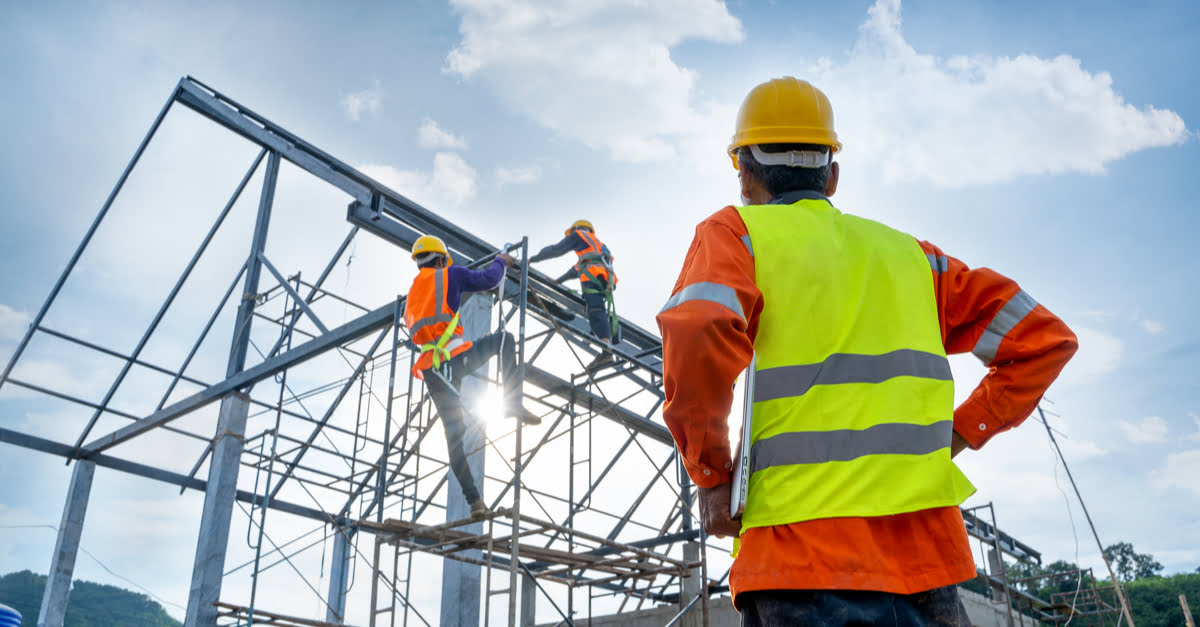
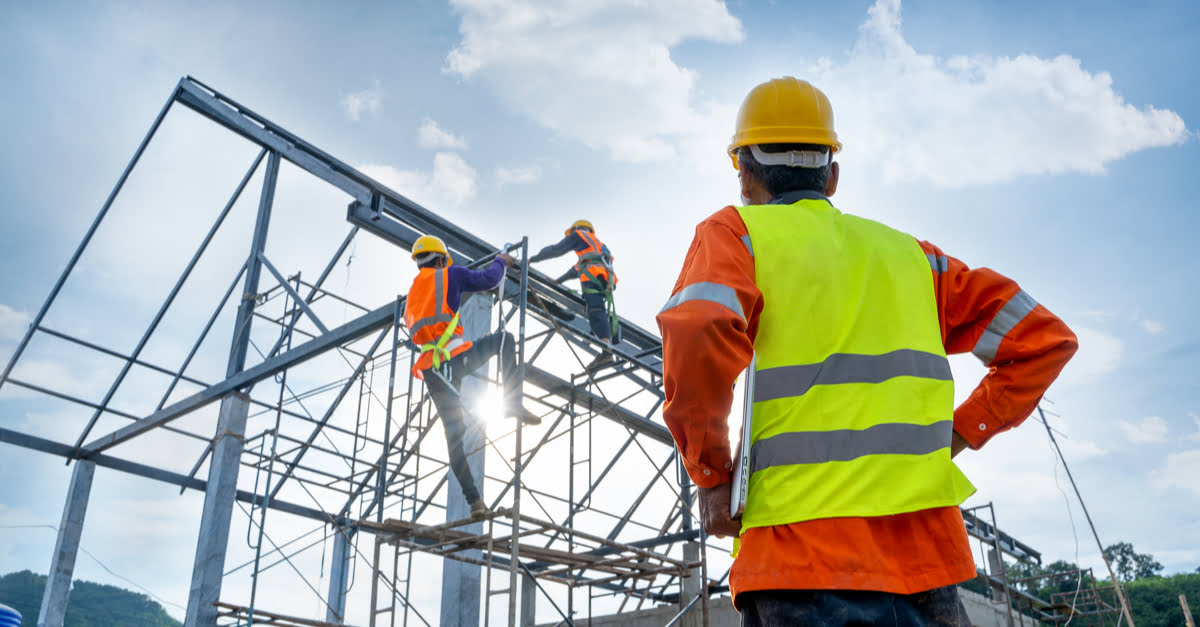
Building & Construction
How To Improve Productivity In Construction Industry
Modified: December 7, 2023
Learn effective strategies and techniques to enhance productivity in the building construction industry. Implement these tips to optimize your project management and boost overall efficiency.
(Many of the links in this article redirect to a specific reviewed product. Your purchase of these products through affiliate links helps to generate commission for Storables.com, at no extra cost. Learn more)
Introduction
Welcome to the fascinating world of construction, where buildings take shape and dreams become a reality. The construction industry is an essential sector that drives economic growth and development. However, like any industry, it faces numerous challenges, including the need for improved productivity.
Productivity is the key to success in the construction industry. It determines how efficiently resources, such as labor, equipment, and materials, are utilized to complete projects on time and within budget. Higher productivity results in reduced costs, increased profitability, and improved customer satisfaction. In a highly competitive market, improving productivity is crucial for construction companies to stay ahead of the curve.
In this article, we will explore strategies to enhance productivity in the construction industry. We will identify areas for improvement, discuss the implementation of technology solutions, explore lean construction principles, and delve into workforce training and development. Additionally, we will discuss the importance of streamlined communication, improved supply chain management, enhanced safety measures, and the significance of measuring and monitoring productivity.
So, whether you are a construction professional seeking ways to optimize performance or a stakeholder looking to understand the dynamics of the industry, this article will provide valuable insights into improving productivity in the construction industry.
Key Takeaways:
- Prioritizing productivity in the construction industry is crucial for cost efficiency, project timelines, competitive advantage, and safety. Streamlining processes, embracing technology, and investing in workforce development are key strategies for improvement.
- Measuring and monitoring productivity provides valuable insights for decision-making and process improvement. Establishing KPIs, utilizing technology for data collection and analysis, and fostering a culture of continuous improvement are essential for driving success in construction projects.
The Importance of Productivity in the Construction Industry
Productivity is a critical factor in the success of any industry, and the construction sector is no exception. A highly productive construction industry is vital for economic growth, infrastructure development, and the overall societal well-being. Here are some key reasons why productivity is of utmost importance in the construction industry:
- Cost Efficiency: Improving productivity directly translates to cost savings. When projects are completed efficiently, less time and resources are wasted, leading to reduced costs. This cost efficiency not only benefits construction companies but also clients and end-users, who can enjoy high-quality buildings and infrastructure at a reasonable cost.
- Project Timelines: Time is of the essence in construction projects. Delays can have a ripple effect, causing inconvenience to all stakeholders involved. By focusing on productivity improvements, projects can be completed on time, ensuring timely delivery and minimizing disruptions to other projects or activities.
- Competitive Advantage: In a competitive market, construction companies with higher productivity levels have a clear advantage. They can bid more competitively, secure more projects, and attract top talent. Enhanced productivity also improves a company’s reputation, leading to repeat business and referrals.
- Safety: Productivity and safety go hand in hand. When construction processes are efficient and well-planned, it reduces the potential for accidents and injuries. By prioritizing productivity, companies can create a safer working environment for their employees, boosting morale and reducing costly downtime due to accidents.
It is important to note that productivity in the construction industry is not just about completing tasks quickly; it is about working smarter, identifying areas for improvement, and implementing strategic measures to optimize performance. By focusing on productivity, construction companies can achieve better outcomes, higher profitability, and increased customer satisfaction.
Identifying Areas for Improvement
In order to improve productivity in the construction industry, it is crucial to identify areas that are in need of improvement. By identifying these areas and addressing them, construction companies can streamline their processes, optimize resource allocation, and enhance overall efficiency. Here are some key areas to consider:
- Workflow Optimization: Reviewing and analyzing the workflow is essential to identify any bottlenecks or inefficiencies. This includes assessing the sequence of tasks, dependencies, and the flow of information. By streamlining the workflow, construction companies can maximize productivity and minimize delays.
- Equipment and Technology: Evaluate the existing equipment and technology being used in construction processes. Outdated or inefficient equipment can significantly hamper productivity. Investing in modern, advanced equipment and technologies can not only improve productivity but also enhance the quality of work and safety standards.
- Materials Sourcing and Management: The timely availability of construction materials is crucial for seamless project execution. Improving the sourcing and management of materials ensures that construction projects are not delayed due to material shortages or delays in delivery.
- Communication and Collaboration: Effective communication and collaboration among all stakeholders, including architects, engineers, contractors, and subcontractors, are vital for successful project delivery. Identifying and adopting efficient communication channels and tools can enhance collaboration and minimize misunderstandings or errors that can lead to delays or rework.
- Project Planning and Risk Management: Thorough project planning and risk management are essential for timely and successful project completion. Identifying potential risks and developing mitigation strategies can prevent costly setbacks and ensure that projects stay on track.
- Workforce Management: An efficient workforce plays a significant role in improving productivity. Analyze labor allocation, skills gaps, and training needs. By investing in workforce training and development, construction companies can enhance skills, efficiency, and employee morale.
- Quality Control Procedures: Implementing stringent quality control procedures is crucial for maintaining high-quality standards. By focusing on quality from the early stages of a project, rework and costly errors can be minimized, leading to improved productivity and customer satisfaction.
Identifying and addressing these areas for improvement can significantly enhance the productivity and efficiency of construction projects. However, it is important to remember that each construction company is unique, so it is essential to conduct a thorough assessment to identify specific areas for improvement tailored to your organization’s needs.
Implementing Technology Solutions
Technology plays a transformative role in the construction industry, revolutionizing traditional processes and offering innovative solutions to enhance productivity. By implementing technology solutions, construction companies can streamline operations, improve communication, and maximize efficiency. Here are some key technology solutions that can be implemented:
- Building Information Modeling (BIM): BIM is a powerful digital technology that enables the creation of 3D models of buildings, infrastructure, and construction projects. It allows for enhanced collaboration, improved visualization, and efficient project coordination. BIM enables teams to identify and resolve potential clashes or conflicts before construction, reducing costly changes during the construction phase.
- Construction Management Software: Construction management software provides a centralized platform for project planning, scheduling, cost control, and document management. By automating processes, managing resources effectively, and providing real-time project visibility, construction management software improves project efficiency and facilitates better decision-making.
- Mobile Apps and Cloud Computing: Mobile apps allow field workers to access and update project information, communicate in real-time, and submit reports from the construction site. Cloud computing enables secure storage, easy collaboration, and access to project data from anywhere, facilitating streamlined communication and improving efficiency.
- Automated Equipment and Robotics: Implementing automated equipment and robotics in construction processes can significantly improve productivity by reducing manual labor, increasing precision, and enhancing safety. Robotic systems can be utilized for tasks such as bricklaying, concrete pouring, and demolition, leading to faster project completion and reduced labor costs.
- Drones and 3D Scanning: Drones and 3D scanning technology have revolutionized surveying and site inspections. Drones can capture aerial images and videos, providing valuable data for project planning and progress monitoring. 3D scanning enables accurate as-built documentation, reducing errors and improving construction accuracy.
- Internet of Things (IoT) and Sensors: IoT devices and sensors can be utilized to monitor and optimize construction operations. They can track the location of equipment and materials, monitor environmental conditions, and improve safety measures. IoT provides real-time data for informed decision-making and proactive management.
- Virtual and Augmented Reality: Virtual and augmented reality technologies offer immersive visualization and simulation capabilities. They allow stakeholders to experience projects before construction, aiding in design validation, client communication, and identifying potential issues early on, ultimately improving project outcomes.
These are just a few examples of the technology solutions available to enhance productivity in the construction industry. The key is to carefully assess the specific needs of your organization and select technologies that align with your goals and objectives. By embracing technology and innovation, construction companies can drive productivity, optimize processes, and stay ahead in a rapidly evolving industry.
Embracing Lean Construction Principles
Lean construction is a management philosophy and approach that aims to maximize value and minimize waste in construction projects. By embracing lean construction principles, construction companies can improve productivity, enhance project efficiency, and deliver high-quality results. Here are key principles of lean construction:
- Collaboration and Integrated Project Delivery: Lean construction emphasizes collaboration among all stakeholders, including owners, designers, contractors, and suppliers. By involving all parties early in the project and fostering a culture of trust and cooperation, project delivery can be streamlined, communication improved, and conflicts minimized.
- Value Stream Mapping: Value stream mapping is a technique used to analyze and improve the flow of information, materials, and processes within a construction project. By identifying non-value-added activities and eliminating waste, construction companies can optimize productivity and enhance overall project performance.
- Continuous Improvement and Kaizen: Lean construction encourages a culture of continuous improvement and incremental changes. Through the concept of “kaizen,” construction teams actively seek ways to improve processes, eliminate inefficiencies, and enhance productivity. Small improvements made consistently over time can result in significant gains.
- Just-in-Time (JIT) Delivery: JIT delivery involves delivering materials and resources to the construction site at the exact time they are needed, reducing inventory and waste. By ensuring a smooth flow of materials, construction companies can minimize delays, optimize space utilization, and enhance productivity.
- Pull Planning and Last Planner System: Pull planning involves bringing together all project stakeholders to collaboratively plan out the project timeline, tasks, and dependencies. The Last Planner System focuses on empowering front-line workers to plan and execute their work efficiently. By involving those closest to the work in the planning process, construction companies can improve productivity and accountability.
- Standardization and Lean Tools: Standardizing processes and using lean tools, such as 5S (Sort, Set in Order, Shine, Standardize, Sustain) and visual management, can improve organization, productivity, and safety. These tools ensure that workspaces are clean, organized, and efficient, reducing wasted time searching for tools or materials.
- Quality at the Source: Lean construction focuses on ensuring quality at the source, rather than relying on inspections or rework. By empowering workers to take ownership of quality control and empowering them to address issues immediately, construction companies can eliminate costly rework, improve productivity, and enhance customer satisfaction.
Embracing lean construction principles requires a shift in mindset and a commitment to continuous improvement. By adopting these principles and integrating them into construction workflows, companies can create a culture of efficiency, eliminate waste, and optimize productivity throughout all stages of the project.
Read more: What Is The Construction Industry
Enhancing Workforce Training and Development
The success of any construction project heavily relies on the skills and expertise of the workforce. To improve productivity in the construction industry, it is crucial to prioritize workforce training and development. By investing in continuous learning and professional development, construction companies can enhance their workforce’s skills, efficiency, and overall performance. Here are key strategies for enhancing workforce training and development:
- Identifying Skill Gaps: Conduct thorough assessments to identify skill gaps within the workforce. This can be done through performance evaluations, skills assessments, and feedback from supervisors. By understanding areas that require improvement, targeted training programs can be developed.
- Providing Technical and Safety Training: Offer technical training programs to enhance workers’ knowledge and expertise in specific areas such as construction techniques, equipment operation, and building codes. Equally important is providing comprehensive safety training to ensure workers understand and adhere to safety protocols, preventing accidents and injuries.
- Offering Apprenticeships and Mentorship Programs: Implement apprenticeship programs to provide hands-on, on-the-job training for newcomers in the industry. Pairing experienced workers with apprentices through mentorship programs enhances knowledge transfer and skill development.
- Encouraging Continuous Learning: Foster a culture of continuous learning by encouraging workers to pursue professional development opportunities. This can include attending industry conferences, webinars, and workshops, as well as obtaining certifications or advanced degrees in construction-related fields.
- Implementing Cross-Training Initiatives: Cross-training employees in different roles within the construction process helps to broaden their skill sets and creates a more versatile workforce. This enables better collaboration and the ability to seamlessly transition between different tasks as project needs fluctuate.
- Utilizing Technology-Based Training: Incorporate technology-based training methods, such as e-learning platforms and virtual reality simulations, to provide interactive and engaging learning experiences. These methods can effectively train workers on new technologies, software applications, and safety procedures.
- Recognizing and Rewarding Achievement: Acknowledge and reward employees for their training achievements and professional development milestones. This not only encourages individual growth but also creates a positive work environment and motivates others to pursue training opportunities.
Enhancing workforce training and development requires a long-term commitment from construction companies. By investing in the growth and skill development of the workforce, companies can cultivate a highly skilled and motivated workforce. This ultimately leads to improved productivity, higher-quality work, and increased employee satisfaction and retention.
Implementing lean construction practices can improve productivity in the construction industry. This includes reducing waste, improving communication, and optimizing workflow.
Streamlining Communication and Collaboration
Smooth and effective communication is essential for productivity in the construction industry. With various stakeholders involved in a project, including architects, engineers, contractors, subcontractors, and suppliers, streamlining communication and fostering collaboration is crucial. Here are key strategies to enhance communication and collaboration in the construction industry:
- Clear Communication Channels: Establish clear communication channels within the organization and across project teams. This can include regular project meetings, utilizing communication tools such as emails, instant messaging, and project management software, and clearly defining roles and responsibilities for each team member.
- Shared Project Documentation: Utilize cloud-based platforms to centralize project documentation and ensure all stakeholders have access to the latest information. This allows for real-time collaboration and reduces the risk of miscommunication or outdated documents.
- Regular Progress Reporting: Implement regular progress reporting mechanisms to keep all stakeholders informed about the project’s status. This can include weekly or monthly update meetings, project dashboards, or reports that outline completed tasks, upcoming deadlines, and any potential issues.
- Collaborative Project Planning: Involve key stakeholders in the project planning phase to ensure that all perspectives and requirements are considered. Collaborative planning allows for better coordination, identification of potential conflicts or constraints, and proactive problem-solving.
- Integrated Technology Platforms: Utilize construction management software that integrates communication tools and project management functionalities. This allows for seamless collaboration, instant sharing of information, and tracking project progress in real-time.
- Regular Team Meetings and Site Visits: Schedule regular team meetings and site visits to encourage face-to-face interaction and strengthen relationships among team members. These interactions provide an opportunity to address any concerns, clarify expectations, and foster a sense of teamwork and shared goals.
- Effective Change Management: Establish a clear change management process to handle any modifications or alterations to the project plans. Clearly communicate changes to all relevant parties, outline the impact on timelines and budgets, and involve the necessary stakeholders in decision-making.
- Resolving Conflicts Promptly: Address conflicts or disagreements promptly and constructively. Encourage open and honest communication, actively listen to each party’s concerns, and work towards finding mutually beneficial solutions. Timely resolution of conflicts minimizes disruptions and enhances collaboration.
Streamlining communication and fostering collaboration require proactive efforts from all project participants. By implementing effective communication strategies and leveraging technology tools, construction companies can enhance teamwork, minimize misunderstandings, and ensure all stakeholders are aligned towards the project’s goals. By promoting a culture of open communication and collaboration, construction projects can run smoothly, efficiently, and achieve higher levels of productivity and success.
Improving Supply Chain Management
A well-managed and efficient supply chain is critical to the success of construction projects. Effective supply chain management ensures the timely availability of materials, minimizes disruptions, and optimizes resource utilization. By improving supply chain management, construction companies can enhance productivity and streamline project execution. Here are key strategies for improving supply chain management:
- Supplier Evaluation and Selection: Conduct thorough evaluations of potential suppliers to ensure they have a track record of reliability, quality, and timely delivery. Select suppliers that can meet project requirements and consistently deliver materials and components on time.
- Clear Procurement Processes: Establish clear procurement processes that document and standardize the purchasing and ordering procedures. This ensures consistency, reduces errors, and improves efficiency in sourcing materials.
- Collaborative Relationships with Suppliers: Foster strong relationships with suppliers based on trust, open communication, and mutual goals. Regularly communicate project requirements, forecasts, and any changes to ensure suppliers can plan and deliver accordingly.
- Effective Inventory Management: Implement efficient inventory management practices to avoid stockouts or excess inventory. Regularly review inventory levels, forecast future needs, and optimize storage and handling to minimize waste and ensure materials are available when needed.
- Streamlined Transportation and Logistics: Evaluate transportation and logistics processes to ensure timely and cost-effective delivery of materials to the construction site. Collaborate with logistics providers to optimize routes, minimize transportation costs, and reduce delivery lead times.
- Standardization of Materials and Components: Adopt standardization practices to reduce the number of different materials and components used in projects. Standardization simplifies procurement, storage, and handling processes, improves compatibility, and reduces waste.
- Real-Time Tracking and Visibility: Utilize technology tools, such as barcode scanning, RFID tagging, or GPS tracking, to achieve real-time tracking and visibility of materials and equipment throughout the supply chain. This minimizes the risk of lost or misplaced items, improves accountability, and enhances overall efficiency.
- Risk Management: Identify potential risks and develop contingency plans to mitigate disruptions in the supply chain. This includes having alternative suppliers, monitoring market conditions, and implementing strategies to handle unexpected events such as natural disasters or supplier bankruptcies.
- Continuous Improvement and Performance Evaluation: Regularly assess the performance of suppliers and the supply chain as a whole. Identify areas for improvement, such as delivery reliability, quality, or cost-effectiveness, and work collaboratively with suppliers to implement necessary changes.
Improving supply chain management requires a strategic and holistic approach. By implementing these strategies, construction companies can optimize material flow, minimize delays, reduce costs, and enhance overall productivity. It is important to continuously review and refine supply chain processes to adapt to changing project requirements and market conditions, ensuring a seamless and efficient construction process.
Enhancing Safety Measures
Safety is of paramount importance in the construction industry. Enhancing safety measures not only protects the well-being of workers but also plays a significant role in improving productivity. By prioritizing safety, construction companies can minimize accidents, reduce downtime, and create a positive work environment. Here are key strategies for enhancing safety measures in the construction industry:
- Developing a Safety Culture: Promote a strong safety culture throughout the organization by emphasizing the importance of safety in all aspects of construction projects. Encourage open communication, empower employees to report hazards or near misses, and provide regular safety training and educational resources.
- Risk Assessments and Hazard Identification: Conduct thorough risk assessments to identify potential hazards specific to each construction site. Regularly evaluate work areas and procedures to ensure compliance with safety regulations and industry best practices.
- Clear Safety Policies and Procedures: Establish clear safety policies and procedures that outline protocols for hazard reporting, personal protective equipment (PPE) usage, emergency response, and safe work practices. Regularly communicate these policies to all workers and enforce adherence to ensure a safe working environment.
- Employee Training and Education: Provide comprehensive safety training to all employees, both new hires and existing staff. This should include general safety protocols, task-specific training, equipment operation training, and emergency response procedures.
- Regular Safety Inspections and Audits: Conduct regular safety inspections and audits to identify potential hazards and ensure compliance with safety standards. Actively address any issues or areas of improvement identified during inspections, and track the progress of corrective actions.
- Promoting Good Housekeeping: Maintain clean and organized work areas to minimize potential tripping hazards and ensure clear pathways for movement. Regularly remove debris, enforce proper waste disposal protocols, and emphasize the importance of cleanliness throughout the construction site.
- Providing Adequate Personal Protective Equipment (PPE): Ensure that all workers have access to and correctly use appropriate PPE for their tasks. Regularly inspect and replace damaged or worn-out PPE, and regularly communicate the importance of PPE usage to all employees.
- Monitoring and Managing Fatigue: Fatigue can lead to accidents and decreased productivity. Implement measures to monitor and manage worker fatigue, such as scheduling regular breaks, providing adequate rest periods, and promoting healthy lifestyle practices.
- Effective Incident Reporting and Investigation: Establish a clear process for incident reporting and investigation. Encourage workers to report incidents, near misses, or hazardous conditions promptly. Investigate incidents thoroughly to identify root causes and implement preventive measures to avoid similar occurrences in the future.
- Continuous Improvement and Safety Feedback Loop: Foster a culture of continuous improvement by actively seeking feedback from workers about potential safety concerns and ideas for improvement. Regularly review safety processes and procedures to identify opportunities for enhancement.
Enhancing safety measures in the construction industry requires a commitment from all levels of the organization. By prioritizing safety, construction companies can create a productive and safe working environment, reducing the risk of accidents, injuries, and costly project setbacks. A strong safety culture contributes not only to the well-being of workers but also to overall project efficiency and success.
Read more: What Type Of Industry Is Construction
Measuring and Monitoring Productivity
In order to improve productivity in the construction industry, it is crucial to measure and monitor performance regularly. Measuring productivity provides valuable insights into the efficiency of processes, identifies areas for improvement, and helps track progress towards project goals. Here are key strategies for measuring and monitoring productivity in the construction industry:
- Establishing Key Performance Indicators (KPIs): Define clear and measurable KPIs that align with project objectives and overall business goals. These KPIs can include metrics such as project completion time, budget adherence, labor productivity, or quality performance.
- Data Collection and Analysis: Implement systems to collect relevant data related to project performance. This can include labor hours, equipment usage, material consumption, or project milestones. Regularly analyze this data to assess productivity levels and identify trends or anomalies that may require attention.
- Comparative Analysis: Compare current project performance against historical data or industry benchmarks to gain a better understanding of how well the project is progressing. This comparison helps identify areas of improvement and highlights any deviations from expected productivity levels.
- Utilizing Technology and Software: Leverage construction management software or project management tools that facilitate data collection, analysis, and reporting. These tools streamline the process of capturing productivity data and provide real-time visibility into project performance.
- Regular Progress Meetings and Reporting: Conduct regular progress meetings to discuss productivity, review KPIs, and track project performance. Generate regular reports that summarize key productivity metrics, highlight achievements, and outline areas for improvement.
- Employee Performance Tracking: Monitor individual employee performance and productivity to identify top performers and areas where additional training or support may be required. Recognize and reward high-performing employees to motivate others and foster a culture of productivity excellence.
- Continuous Feedback and Improvement: Regularly seek feedback from project teams and workers on potential barriers or challenges that hinder productivity. Encourage open communication and collaboration to identify innovative solutions and implement continuous improvement initiatives.
- Implementing Lean Construction Principles: Adopt lean construction principles to measure productivity based on value-added activities and waste reduction. Techniques such as value stream mapping and pull planning help identify areas where productivity can be enhanced and minimize non-value-added activities.
- Periodic Productivity Audits: Conduct periodic productivity audits to evaluate the effectiveness of processes and identify opportunities for improvement. Engage external experts to provide an unbiased assessment of productivity levels and recommend strategies for enhancement.
- Tracking Customer Satisfaction: Monitor customer satisfaction through surveys or feedback mechanisms to gauge the effectiveness of productivity improvements. Positive customer feedback indicates that productivity enhancements are positively impacting the quality and delivery of projects.
Measuring and monitoring productivity in the construction industry provides valuable insights for decision-making and process improvement. By implementing these strategies, construction companies can identify areas for enhancement, track progress, and make data-driven adjustments to optimize productivity. Regular monitoring ensures that projects stay on track and helps drive continuous improvement within the organization.
Conclusion
Improving productivity in the construction industry is essential for driving success, maximizing profitability, and delivering high-quality projects. By implementing the strategies outlined in this article, construction companies can enhance productivity and make significant strides towards achieving operational excellence. Here is a recap of the key points discussed:
First and foremost, recognizing the importance of productivity in the construction industry is crucial. It directly impacts cost efficiency, project timelines, competitive advantage, and safety. Construction companies must prioritize productivity to stay competitive and meet client expectations.
Identifying areas for improvement is the first step towards enhancing productivity. Analyzing workflows, evaluating equipment and technology, managing materials sourcing, and improving communication and collaboration are all vital areas to focus on. By streamlining these processes, construction companies can eliminate inefficiencies and optimize productivity.
Embracing technology solutions can revolutionize the construction industry. Building Information Modeling (BIM), construction management software, drones, and IoT devices are just a few examples of how technology can streamline operations and enhance collaboration.
Furthermore, lean construction principles emphasize collaboration, value stream mapping, continuous improvement, and waste reduction. By embracing lean principles, construction companies can drive productivity and optimize project performance.
Investing in workforce training and development is key to enhancing productivity. By identifying skill gaps, providing technical and safety training, offering apprenticeships, and promoting continuous learning, construction companies can develop a skilled and efficient workforce.
Streamlining communication and collaboration is crucial for effective project management. Clear communication channels, shared project documentation, regular progress reporting, and collaborative project planning foster efficient collaboration and seamless coordination among all stakeholders.
Improving supply chain management is vital to ensuring timely availability of materials and optimizing resource utilization. Supplier evaluation, clear procurement processes, collaborative relationships, and real-time tracking contribute to a well-managed and efficient supply chain.
Enhancing safety measures safeguards the well-being of workers, minimizes accidents and downtime, and fosters a positive work environment. By developing a safety culture, conducting regular assessments, providing training, and implementing robust incident reporting and investigation procedures, construction companies can prioritize safety and productivity simultaneously.
Finally, measuring and monitoring productivity allows construction companies to track progress, identify areas for improvement, and make data-driven decisions. Establishing KPIs, utilizing technology for data collection and analysis, and conducting regular progress meetings enable effective productivity measurement and continuous improvement.
In conclusion, by implementing these strategies and focusing on enhancing productivity in the construction industry, companies can achieve higher efficiency, cost savings, improved project outcomes, and increased customer satisfaction. Prioritizing productivity not only drives the success of individual construction projects but also contributes to the overall growth and success of the industry as a whole.
Frequently Asked Questions about How To Improve Productivity In Construction Industry
Was this page helpful?
At Storables.com, we guarantee accurate and reliable information. Our content, validated by Expert Board Contributors, is crafted following stringent Editorial Policies. We're committed to providing you with well-researched, expert-backed insights for all your informational needs.
0 thoughts on “How To Improve Productivity In Construction Industry”