Home>diy>Building & Construction>What Does GWB Stand For In Construction
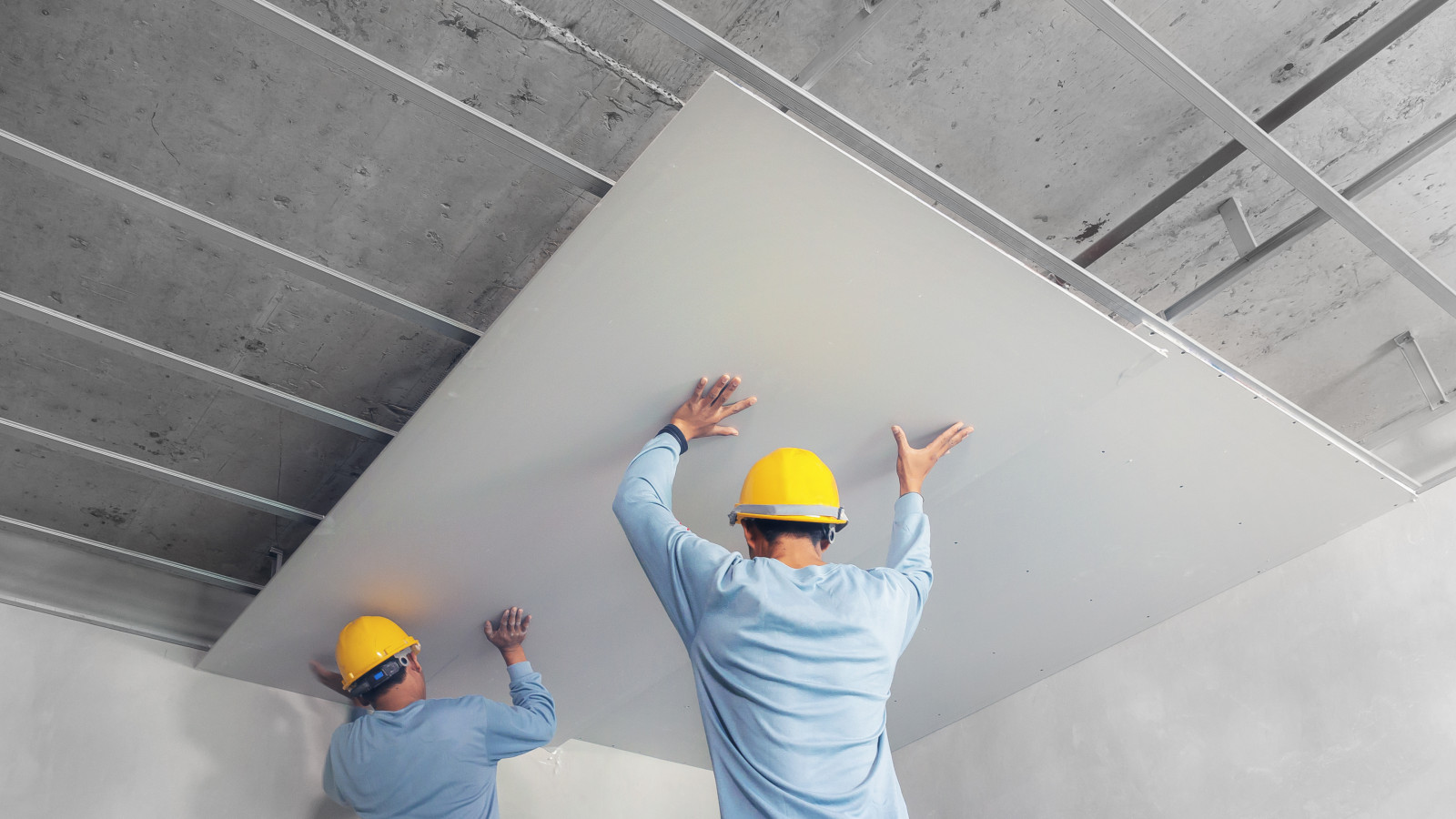
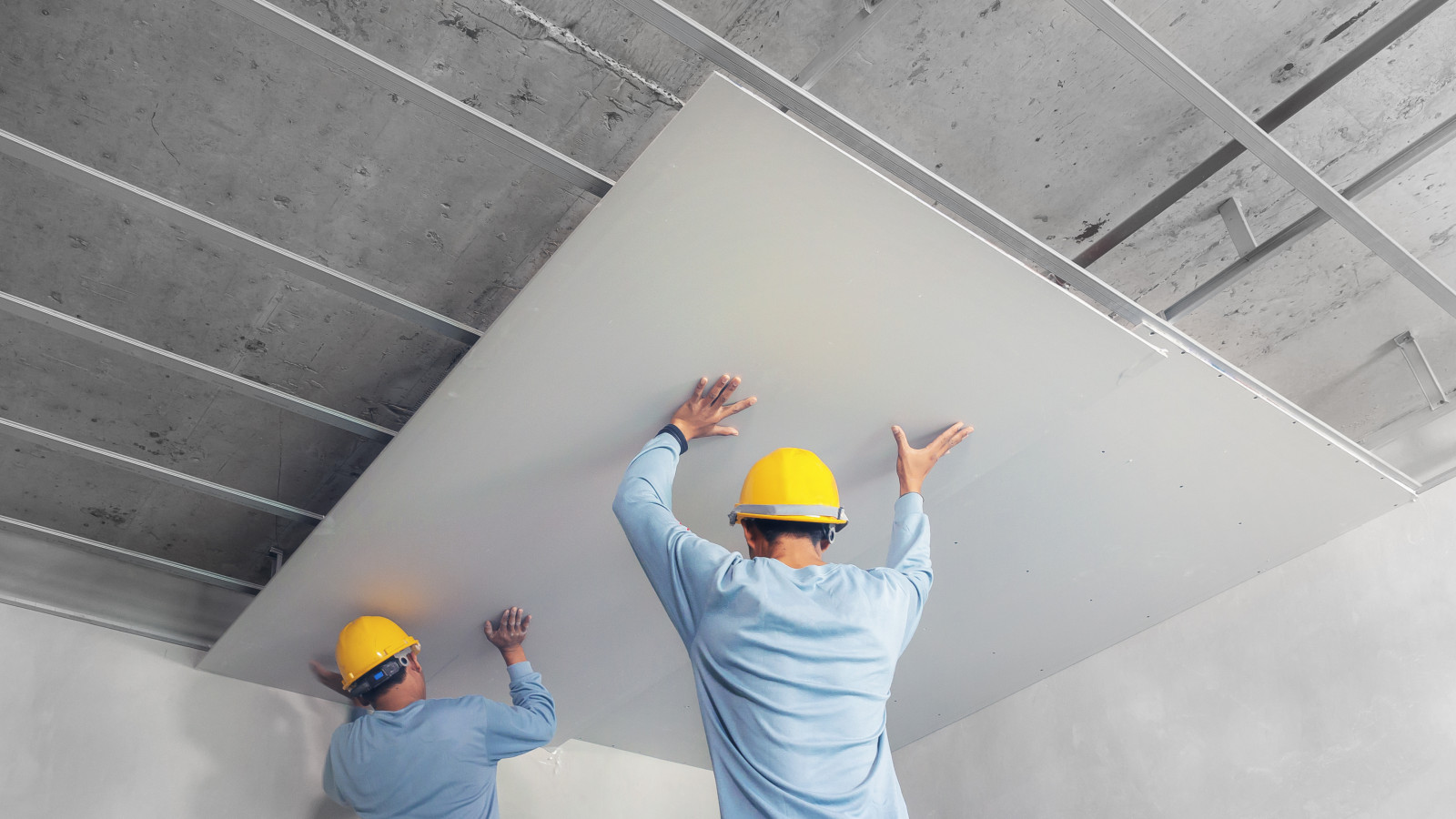
Building & Construction
What Does GWB Stand For In Construction
Modified: December 7, 2023
Find out what GWB stands for in the construction industry. Discover the meaning of GWB and its significance in building construction.
(Many of the links in this article redirect to a specific reviewed product. Your purchase of these products through affiliate links helps to generate commission for Storables.com, at no extra cost. Learn more)
Introduction
Welcome to the world of construction, where every project is a masterpiece in the making. Whether you are a seasoned professional or just starting out in the industry, understanding the various materials and techniques used in construction is essential. In this article, we will explore one such material that plays a crucial role in building construction: GWB.
GWB stands for Gypsum Wallboard, also known as drywall or plasterboard. It is a widely used material that serves as an interior wall surface finish. GWB panels are made of a core of gypsum, a natural mineral, sandwiched between two layers of paper or fiberglass mats. This combination creates a lightweight but strong surface that is easy to install and provides a smooth and flat finish.
Now that we have defined GWB, let’s delve into its uses in construction and why it has become a popular choice among builders and contractors.
Key Takeaways:
- GWB, or Gypsum Wallboard, is a versatile and cost-effective material used in construction for interior walls, ceilings, and fire-rated assemblies, offering advantages such as fire resistance, sound insulation, and quick installation.
- Understanding the different types of GWB and following safety measures during installation can help maximize its benefits while mitigating limitations such as moisture sensitivity and impact vulnerability.
Read more: What Does BIM Stand For In Construction
Definition of GWB
GWB, or Gypsum Wallboard, is a type of building material used for interior wall surfaces in residential and commercial construction. It is commonly referred to as drywall or plasterboard. GWB consists of a gypsum core, which provides fire resistance, sandwiched between two layers of paper or fiberglass mats. These layers give the GWB panel its durability and stability.
The gypsum core in GWB is made from a naturally occurring mineral called gypsum, which is processed into a fine powder and then mixed with water. When the gypsum powder is hydrated, it forms a paste-like substance that is poured onto a continuous moving sheet of paper or fiberglass. As the sheet moves along the production line, the gypsum paste evenly spreads across the surface, and another layer of paper or fiberglass is added on top. The result is a panel of GWB with a consistent thickness and smooth finish.
GWB panels come in various sizes and thicknesses, with the most common thicknesses being 1/2 inch and 5/8 inch. The panels are typically available in standard sizes such as 4 feet by 8 feet, although custom sizes can also be manufactured to suit specific project requirements. The edges of GWB panels are either tapered or squared, with the tapered edges allowing for smoother transitions between panels and easier finishing.
Overall, GWB is a versatile and cost-effective building material that has revolutionized the construction industry. Its ease of installation, durability, fire resistance, and cost efficiencies have made it a popular choice for creating interior walls and ceilings.
Uses of GWB in Construction
GWB, or Gypsum Wallboard, finds extensive use in various aspects of construction. Its versatility and ease of installation make it a preferred choice for builders and contractors. Here are some common uses of GWB in construction:
- Interior Walls: GWB is primarily used as a surfacing material for interior walls in residential, commercial, and institutional buildings. It provides a smooth and even finish that is ready for painting or wallpapering. The panels can be easily cut and installed, allowing for quick and efficient construction.
- Partition Walls: GWB is employed to create partition walls that separate different areas within a building, such as rooms, hallways, or offices. These walls serve as a non-load-bearing structure and can be easily relocated or modified as per changing needs.
- Ceilings: GWB is also used for creating suspended ceilings or dropped ceilings. These ceilings consist of a metal grid framework suspended from the main ceiling, with GWB panels fitted into the grid. Suspended ceilings help with sound insulation, hide electrical and mechanical components, and provide easy access for maintenance.
- Firmer Walls: To enhance the strength and rigidity of interior walls, GWB is often used in conjunction with other structural components. For example, GWB panels are installed on metal or wooden studs that act as a framework for the wall. This combination results in sturdier walls, capable of supporting fixtures, shelves, and heavy items.
- Soundproofing: GWB can contribute to soundproofing within a building. Additional layers of GWB, along with insulation material, can help reduce sound transmission between rooms, providing a quieter and more peaceful environment.
These are just a few of the common uses of GWB in construction. Its versatility allows it to be applied in various building types, including residential homes, offices, retail spaces, schools, hospitals, and more. The ease of installation and ability to create smooth, finished surfaces make GWB an integral part of modern construction practices.
Advantages of GWB
GWB, or Gypsum Wallboard, offers numerous advantages that make it a popular choice in the construction industry. Here are some key advantages of using GWB in building projects:
- Fire Resistance: One of the significant advantages of GWB is its fire resistance. The gypsum core in GWB contains crystallized water, which acts as a natural fire barrier. In the event of a fire, the water content is gradually released as steam, effectively reducing the spread of flames. This property makes GWB an essential safety feature, providing valuable time for occupants to evacuate and firefighters to respond.
- Sound Insulation: GWB panels have excellent sound-dampening properties, helping to reduce noise transmission between rooms and floors. By adding additional layers of GWB or incorporating sound-absorbing insulation, the acoustic performance can be further improved, creating a more peaceful and comfortable living or working environment.
- Durability: GWB panels are highly durable and resistant to wear and tear. They can withstand impact, abrasion, and everyday use. This durability ensures that interior walls maintain their integrity and aesthetics over time, minimizing the need for repairs or replacements.
- Quick Installation: GWB panels are relatively simple and quick to install, reducing construction time and costs. The lightweight nature of the panels makes them easy to handle and transport, resulting in efficient installation. This benefit is especially appealing for time-sensitive projects or tight construction schedules.
- Smooth and Flat Finish: GWB provides a smooth and flat surface, ready for painting or wallpapering. The seamless finish enhances the appearance of interiors, creating an aesthetically pleasing environment. The smoothness of GWB also allows for easy and efficient installation of baseboards, moldings, and other decorative elements.
- Cost-effectiveness: GWB is cost-effective compared to other wall surface finishes like plaster or stucco. The material itself is affordable, and the quick installation time translates into lower labor costs. Additionally, the durability and longevity of GWB reduce maintenance expenses in the long run.
These advantages highlight why GWB is a preferred choice in construction. Its fire resistance, sound insulation, durability, ease of installation, aesthetic appeal, and cost-effectiveness make it a reliable and efficient material for interior wall surfaces in various building types.
Disadvantages of GWB
While GWB, or Gypsum Wallboard, has numerous advantages, there are also a few disadvantages to consider when using this material in construction projects. Here are some common disadvantages of GWB:
- Moisture Sensitivity: GWB is highly susceptible to moisture, which can cause the gypsum core to swell or deteriorate. Excessive moisture can lead to mold or mildew growth, compromising the structural integrity of the panels. Therefore, it is crucial to use GWB in appropriate areas and take necessary precautions to prevent moisture infiltration.
- Not Suitable for Wet Areas: Due to its moisture sensitivity, GWB is not recommended for areas prone to water exposure, such as bathrooms, kitchens, or laundry rooms. In these spaces, alternative materials like cement board or water-resistant drywall should be used to prevent water damage and mold growth.
- Prone to Impact Damage: While GWB is generally durable, it can be susceptible to impact damage. Heavy objects or accidental hits can dent or puncture the surface of the panels, requiring repairs or replacements. Extra care should be taken during construction and maintenance activities to avoid damaging the GWB.
- Limited Load-bearing Capacity: GWB is not designed to bear heavy loads. It functions as a non-structural material and relies on the framing or studwork behind it for support. If heavy objects or fixtures need to be mounted on walls, additional reinforcement or structural components should be used to distribute the weight properly.
- Requires Skilled Installation: While GWB installation can be relatively simple, achieving a professional-quality finish requires skills and experience. Proper installation techniques, including taping, mudding, and sanding, are necessary to create seamless joints and a smooth surface. Beginners may struggle to achieve the desired result without prior knowledge or assistance from professionals.
- Environmental Impact: The production of GWB involves mining gypsum, which has its environmental implications. The extraction and processing of raw materials can contribute to habitat disruption and the release of greenhouse gases. However, efforts are being made to reduce the environmental impact by improving manufacturing practices and promoting sustainable alternatives.
Despite these disadvantages, GWB remains a widely used material in construction due to its many advantages. By understanding its limitations and taking appropriate measures, such as proper installation, moisture management, and using alternative materials in wet areas, these challenges can be mitigated, allowing for successful integration of GWB in building projects.
GWB stands for “Gypsum Wallboard,” which is also known as drywall or sheetrock. It is a common building material used for interior walls and ceilings in construction.
Read more: What Does SD Stand For In Construction
Common GWB Applications in Construction
GWB, or Gypsum Wallboard, is a versatile material that finds a wide range of applications in construction. From residential homes to commercial buildings, GWB is used in various ways to create functional and visually appealing spaces. Here are some common applications of GWB in construction:
- Interior Walls: The most prevalent use of GWB is for interior walls. It provides a smooth and seamless surface that is ready for paint, wallpaper, or other decorative finishes. GWB panels are easy to install and can be cut to fit any shape or size. Whether it’s a living room, bedroom, or office, GWB creates a clean and finished look for interior walls.
- Ceilings: GWB is also widely used for creating ceilings, both in residential and commercial settings. Suspended ceilings, also known as dropped ceilings, are constructed using GWB panels supported by a grid system. This type of ceiling allows for easy access to electrical and mechanical components and improves sound insulation. GWB ceilings provide a clean and modern appearance to any space.
- Partition Walls: GWB is often used to construct partition walls that divide interior spaces. These walls can be seen in offices, retail stores, and other commercial environments. GWB’s versatility allows for easy installation and modification of partition walls to accommodate changing spatial requirements.
- Fire-Rated Assemblies: Given its inherent fire resistance, GWB is widely used in fire-rated assemblies. These assemblies are designed to prevent the spread of fire and provide a safe exit route for occupants in case of emergency. GWB is applied to walls, ceilings, and shaft enclosures to create fire-rated barriers that meet building code requirements.
- Acoustic Solutions: GWB is commonly utilized to improve the acoustic performance of interior spaces. Multiple layers of GWB, combined with sound insulation material, can help reduce noise transmission between rooms. This application is especially crucial in theaters, recording studios, classrooms, and other noise-sensitive environments.
- Exterior Soffits: In certain construction projects, GWB is used for exterior soffits, which are the undersides of roof overhangs or balconies. GWB provides a clean and consistent surface that can be painted or finished to match the overall building design.
These are just a few examples of the common applications of GWB in construction. The material’s versatility, ease of installation, and ability to create smooth, finished surfaces make GWB an essential component in creating functional and visually appealing spaces.
Different Types of GWB
GWB, or Gypsum Wallboard, comes in various types, each designed to suit specific construction needs and requirements. Understanding the different types of GWB can help ensure that the right product is selected for a particular project. Here are some common types of GWB:
- Regular Drywall: Regular drywall is the most commonly used type of GWB. It is typically white in color and is suitable for most residential and commercial interior walls. Regular drywall is available in different thicknesses, such as 1/2 inch and 5/8 inch, and comes in standard sizes of 4 feet by 8 feet or 4 feet by 12 feet.
- Moisture-Resistant Drywall: Moisture-resistant drywall, also known as green board or MR board, is designed for use in areas with high moisture levels, such as bathrooms, kitchens, and laundry rooms. It has a water-resistant core that helps prevent damage from moisture exposure. While moisture-resistant drywall is more resistant to water than regular drywall, it is not suitable for direct water contact.
- Fire-Resistant Drywall: Fire-resistant drywall, also referred to as Type X drywall, is designed to provide enhanced fire resistance. It contains special additives that increase its ability to withstand flames and heat. Fire-resistant drywall is typically used in fire-rated assemblies, such as walls and ceilings, to meet building code requirements for fire protection.
- Soundproof Drywall: Soundproof drywall, sometimes known as acoustic drywall, is designed to enhance sound insulation in interior spaces. It has additional layers of material or special sound-damping compounds that minimize sound transmission between rooms. This type of drywall is commonly used in recording studios, home theaters, or areas where noise control is essential.
- Impact-Resistant Drywall: Impact-resistant drywall is designed to withstand higher levels of impact and abuse. It has fiberglass or other reinforcing materials embedded in the gypsum core, making it more resistant to denting, puncturing, or scuffing. Impact-resistant drywall is often used in high-traffic areas, such as hallways, schools, or commercial spaces, where the walls may be subject to accidental bumps or hits.
- Flexible Drywall: Flexible drywall, also known as bendable drywall or flex board, is a specialized type of drywall that can be curved or bent to fit unique shapes or designs. It is commonly used in the construction of curved walls, arches, or other custom architectural features. Flexible drywall is available in various thicknesses to accommodate different bending radii.
These are just a few examples of the different types of GWB available in the market. The selection of the appropriate type depends on factors such as the intended application, location, moisture levels, fire requirements, and acoustic considerations. Consulting with a construction professional or supplier can help determine the most suitable type of GWB for a specific project.
GWB Installation Process
GWB, or Gypsum Wallboard, installation is a straightforward process that can be accomplished with basic tools and equipment. While it is always recommended to hire a professional for optimal results, understanding the general installation process can be helpful. Here are the key steps involved in the GWB installation process:
- Preparing the Surface: Before installing GWB, ensure that the wall or ceiling surface is clean, dry, and structurally sound. Remove any existing protrusions, nails, or debris. Inspect the surface for any structural issues or repairs needed.
- Measuring and Cutting: Measure the dimensions of the area where the GWB will be installed. Carefully mark the measurements on the drywall panel using a straight edge and a pencil. Use a utility knife or a drywall saw to cut the panels to the appropriate size. Ensure that the cuts are precise and straight.
- Applying Adhesive: For wall installations, apply construction adhesive on the back of the GWB panels using a caulking gun. Use a zigzag pattern or dots of adhesive, ensuring it is evenly distributed. This helps to create a stronger bond between the panel and the wall surface.
- Attaching the GWB: Lift the cut GWB panel and press it firmly against the wall surface. Carefully align the panel with the marks or adjacent panels. Use drywall screws or nails to secure the panel to the wall or ceiling studs. Drive the screws or nails into the center of each stud, starting from the corners and working towards the center. Install additional screws or nails along the perimeter and in the field of the panel, leaving a slight indentation without breaking the paper surface.
- Finishing the Joints: After all the panels are installed, the next step is to finish the joints. Apply drywall joint compound, often referred to as mud, using a taping knife or a mud pan. Embed drywall tape into the wet joint compound, pressing it firmly into the joint, and remove excess compound. Allow the compound to dry according to the manufacturer’s instructions. Apply additional coats of compound, feathering the edges, until the joint is smooth and seamless.
- Sanding and Finishing: Once the compound is completely dry, sand the surface using fine-grit sandpaper or a sanding block. This helps achieve a smooth and even finish. After sanding, remove dust using a clean cloth or vacuum. The GWB is now ready for paint, wallpaper, or other decorative finishes.
It is important to note that GWB installation requires proper safety precautions, including the use of safety glasses and dust masks when cutting or sanding. Additionally, following local building codes and regulations is crucial to ensure compliance and safety.
While this general overview provides an understanding of the GWB installation process, it is advisable to consult with professionals or refer to specific installation guidelines and manufacturer recommendations for detailed instructions and best practices.
Precautions and Safety Measures for Working with GWB
Working with GWB, or Gypsum Wallboard, requires attention to safety and proper precautions to ensure a successful and safe installation process. Here are some important precautions and safety measures to keep in mind when working with GWB:
- PPE (Personal Protective Equipment): Always wear appropriate personal protective equipment, such as safety glasses, gloves, and dust masks, when working with GWB. Safety glasses protect your eyes from flying debris and dust, gloves provide hand protection, and dust masks help minimize the inhalation of dust particles during cutting, sanding, or working with joint compound.
- Handling and Lifting: GWB panels can be heavy, so it’s important to use proper lifting techniques to avoid strain or injury. When lifting panels, bend at the knees and lift with your legs, keeping your back straight. If panels are too large or heavy, use assistance or mechanical lifting equipment to prevent personal injuries.
- Power Tool Safety: When using power tools, such as drills or power saws, always follow the manufacturer’s instructions and safety guidelines. Ensure that the tools are in good working condition and use appropriate blades or bits for the specific task. Use caution when operating power tools, keeping fingers and clothing away from moving parts.
- Dust Control: Cutting or sanding GWB can generate a significant amount of dust. To minimize dust exposure, use dust containment systems, such as dust collection bags or vacuum attachments, when cutting or sanding the panels. Work in a well-ventilated area and consider using dust barriers or plastic sheeting to isolate the work area from other spaces.
- Fire Safety: Although GWB is fire-resistant, it is still important to maintain fire safety precautions. Keep flammable materials, such as paints, solvents, or adhesives, away from open flames or heat sources. Ensure that electrical outlets and wiring are properly installed and not overloaded. Familiarize yourself with fire extinguisher locations and emergency exits in the work area.
- Mold and Moisture Prevention: GWB is susceptible to moisture and can promote mold growth if exposed to excessive dampness. Take precautions to prevent water infiltration during installation and ensure proper ventilation in areas prone to moisture, such as bathrooms and basements. If water damage occurs, promptly address the issue to prevent further damage and mold growth.
- Proper Waste Disposal: Dispose of GWB waste responsibly and in accordance with local regulations. In some cases, GWB panels may contain additives or coatings that require special handling or disposal methods. Consult with local waste disposal authorities or recycling centers to ensure proper disposal procedures are followed.
By following these precautions and safety measures, you can minimize the risk of accidents, injuries, and potential health hazards when working with GWB. Remember, safety should always be a top priority in any construction project.
Read more: What Does PR Stand For In Construction
Conclusion
GWB, or Gypsum Wallboard, is an indispensable material in the world of construction. Its versatility, ease of installation, and numerous benefits have made it a popular choice for interior wall surfaces. From residential homes to commercial buildings, GWB finds a wide range of applications, providing a smooth and durable finish that enhances the aesthetics and functionality of spaces.
Throughout this article, we have explored the definition of GWB, its uses in construction, and its advantages and disadvantages. We have also discussed the common applications of GWB, the different types available, the installation process, and the precautions to ensure safety during GWB work.
GWB offers distinct advantages such as fire resistance, sound insulation, durability, and cost-effectiveness. However, it is important to consider its limitations, such as moisture sensitivity and impact vulnerability. By understanding these considerations, proper installation techniques, and following safety measures, the full potential of GWB can be realized without compromising the integrity of the construction project.
Whether you are a contractor, builder, or homeowner, knowledge about GWB and its applications can empower you to make informed decisions and facilitate successful construction projects. Working with professionals in the field and adhering to local building codes and regulations will help ensure proper installation and maximize the benefits of GWB.
In conclusion, GWB remains an essential material in the construction industry. Its versatility, durability, and aesthetic appeal make it a go-to option for interior walls, ceilings, partition walls, and fire-rated assemblies. By appreciating the advantages, understanding the limitations, and implementing the proper installation techniques, GWB can help create beautiful, functional, and safe spaces that stand the test of time.
Frequently Asked Questions about What Does GWB Stand For In Construction
Was this page helpful?
At Storables.com, we guarantee accurate and reliable information. Our content, validated by Expert Board Contributors, is crafted following stringent Editorial Policies. We're committed to providing you with well-researched, expert-backed insights for all your informational needs.
0 thoughts on “What Does GWB Stand For In Construction”