Home>diy>Building & Construction>What Does JSA Stand For In Construction
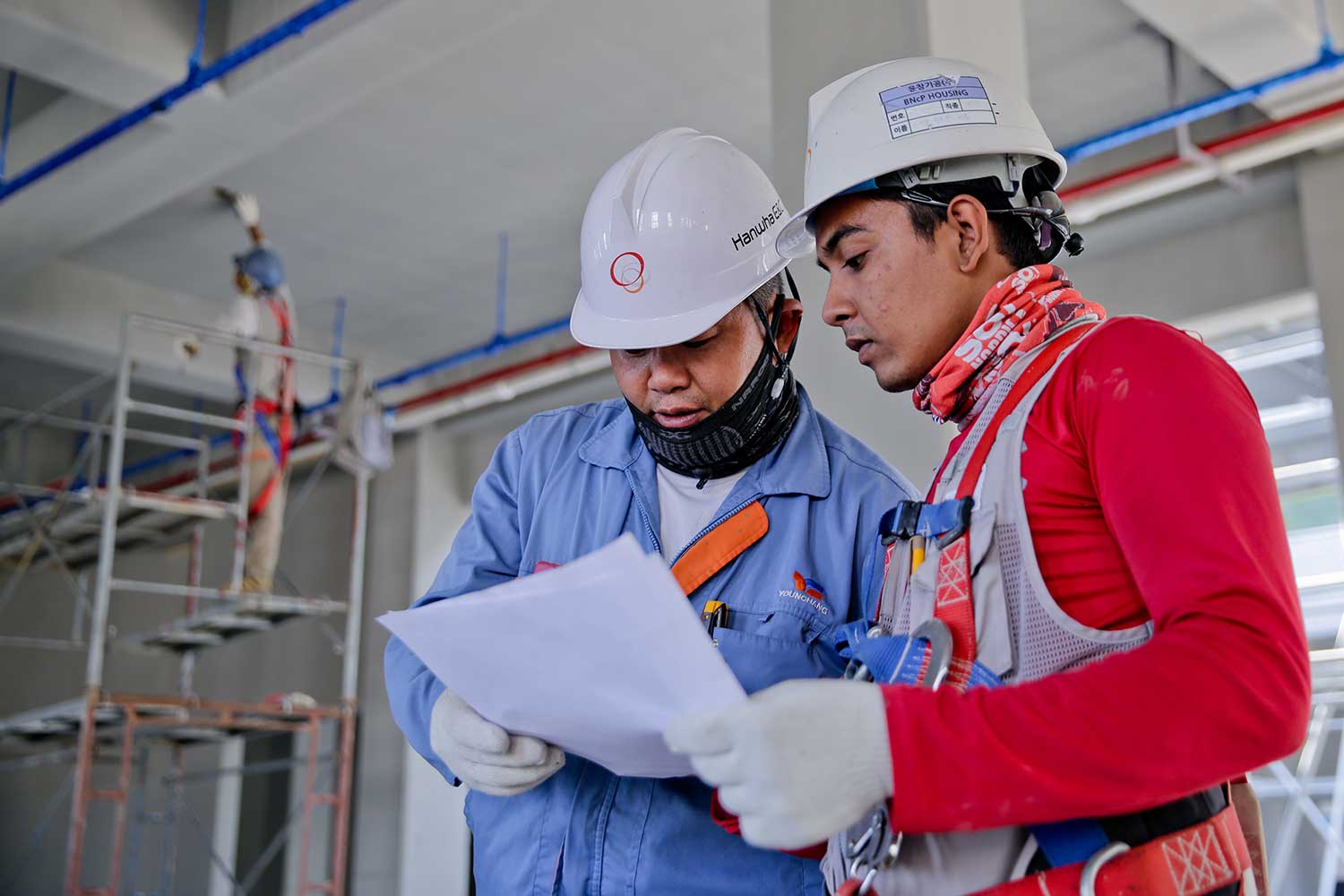
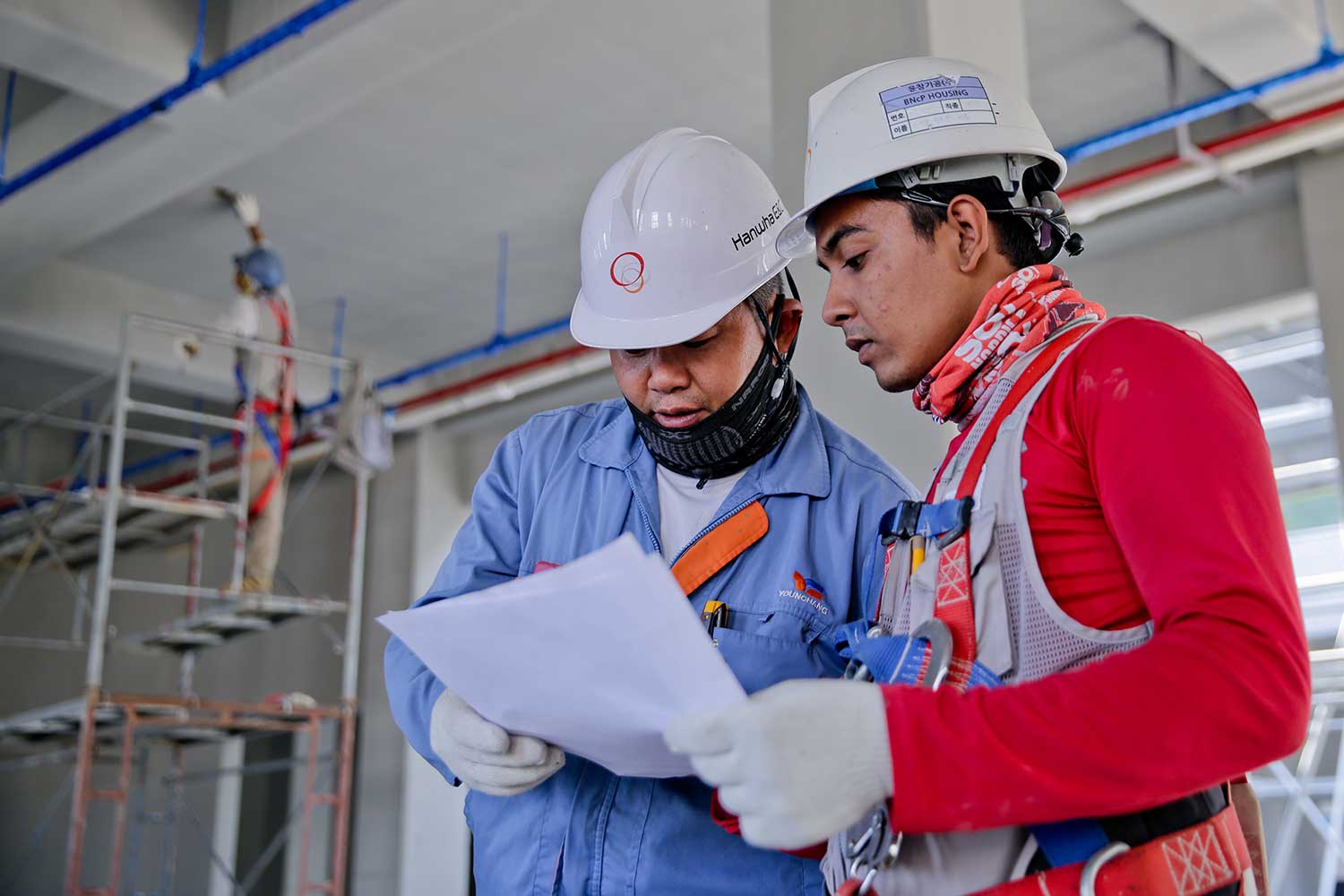
Building & Construction
What Does JSA Stand For In Construction
Modified: March 6, 2024
Discover what JSA stands for in the context of building construction and its importance in ensuring safety and compliance.
(Many of the links in this article redirect to a specific reviewed product. Your purchase of these products through affiliate links helps to generate commission for Storables.com, at no extra cost. Learn more)
Introduction
In the field of construction, safety should always be of paramount importance. Construction sites are inherently hazardous places, with potential risks and dangers lurking at every corner. To ensure the safety of workers and minimize the occurrence of accidents, proper planning and risk assessment are crucial. That’s where a Job Safety Analysis (JSA) comes into play.
A JSA is a systematic approach to identifying and mitigating risks associated with specific tasks or activities in a construction project. By breaking down a job into its individual steps, a JSA provides a comprehensive analysis of the potential hazards and the appropriate control measures to prevent accidents from occurring.
The primary purpose of a JSA is to enhance safety on construction sites and protect the well-being of workers. It serves as a tool to identify hazards, assess risks, and establish appropriate safety procedures. With its detailed analysis and planning, a JSA helps to create a safer working environment and reduce the likelihood of accidents, injuries, and even fatalities.
Key Takeaways:
- JSA, or Job Safety Analysis, is a crucial tool in construction that helps identify and minimize potential hazards, ensuring the safety of workers and creating a culture of safety awareness.
- Implementing JSA in construction projects not only reduces accidents and injuries but also improves efficiency, worker empowerment, and overall project outcomes.
Read more: What Does SD Stand For In Construction
Definition of JSA
A Job Safety Analysis (JSA), also known as a Job Hazard Analysis (JHA), is a systematic process used to identify potential hazards and mitigate risks associated with a specific job or task. It involves breaking down a job into sequential steps and analyzing each step to identify potential hazards and develop control measures to eliminate or minimize them.
The key objective of a JSA is to identify the potential risks and hazards involved in a task, assess the severity and likelihood of those risks and hazards, and determine the appropriate control measures to prevent accidents or injuries. By performing a JSA, construction professionals can proactively identify potential hazards and take measures to prevent them, ensuring the safety of workers and promoting a culture of safety within the construction industry.
A JSA typically consists of detailed documentation that includes a step-by-step breakdown of the job or task, the potential hazards associated with each step, and the recommended control measures to mitigate those hazards. This documentation serves as a valuable resource for workers to understand the risks involved in their tasks and the necessary precautions to take.
It is important to note that a JSA is not a one-time activity, but an ongoing process. As construction projects evolve and new tasks are undertaken, it is essential to review and update the JSA to reflect any changes in the job or associated hazards. Regular JSA updates ensure that workers are aware of the most current safety procedures and that any emerging risks are properly addressed.
By conducting a JSA, construction companies can prioritize safety, protect their workers, and maintain compliance with safety regulations. It is a proactive approach to identify and control hazards before they cause accidents or injuries, ultimately leading to a safer and more productive work environment on construction sites.
Importance of JSA in Construction
Job Safety Analysis (JSA) plays a vital role in the construction industry by ensuring the safety of workers and reducing the risk of accidents and injuries. The importance of JSA can be seen in the following ways:
- Identification of Hazards: A JSA helps construction professionals identify potential hazards associated with specific tasks or activities. By breaking down a job into its individual steps, workers can better recognize the potential risks involved and take appropriate precautions.
- Risk Assessment: With a JSA, construction professionals can assess the severity and likelihood of the identified hazards. This evaluation enables them to prioritize the most critical risks and allocate resources to implement the necessary control measures.
- Preventive Measures: The primary goal of a JSA is to develop control measures to eliminate or minimize hazards. By identifying potential risks in advance, construction companies can implement preventive measures, such as adding safety barriers, providing personal protective equipment (PPE), or implementing administrative controls.
- Worker Awareness: JSA documentation serves as a valuable resource for workers to understand the potential hazards associated with their tasks. By providing workers with this information, they can be more aware of the risks and take greater care in executing their work, resulting in a safer environment.
- Training Purposes: A JSA can be used as a training tool for new employees or as a refresher for existing workers. By referencing the JSA, workers can receive proper training on the identified hazards and the required safety procedures to mitigate them.
- Compliance with Regulations: Many countries have regulations and standards in place to ensure workplace safety. By conducting a JSA, construction companies can demonstrate their commitment to following these regulations and maintaining a safe working environment.
- Continuous Improvement: A JSA is not a one-time exercise. It should be regularly reviewed and updated to reflect changes in the job or the construction project. This continuous improvement ensures that workers are up to date with the latest safety procedures and that emerging hazards are promptly addressed.
In summary, the importance of JSA in construction is undeniable. By conducting a thorough analysis of tasks and identifying potential hazards, construction companies can prioritize safety, protect their workers, and create a culture of safety that promotes efficiency and productivity on construction sites.
Components of a JSA
A Job Safety Analysis (JSA) consists of several key components that collectively provide a comprehensive understanding of the potential hazards associated with a specific job or task in the construction industry. The primary components of a JSA include:
- Job Description: The JSA begins with a clear and detailed description of the job or task being analyzed. This includes information such as the equipment required, the sequence of steps involved, and the expected outcome.
- Job Steps: The next component of a JSA involves breaking down the job into its individual steps. Each step should be clearly described, outlining the specific actions that need to be taken to complete the task successfully. It is essential to be thorough and precise in detailing each step to ensure accurate hazard identification.
- Hazard Identification: In this component, potential hazards associated with each job step are identified. These hazards can be physical, chemical, biological, or ergonomic in nature. Construction professionals should carefully examine each step to determine the potential risks that workers may encounter during the task.
- Risk Assessment: After identifying the potential hazards, the next step is to assess the level of risk associated with each hazard. This includes evaluating the likelihood and severity of an incident occurring due to the hazard. This component helps prioritize the hazards and determine the appropriate control measures.
- Control Measures: This component focuses on developing control measures to eliminate or minimize the identified hazards. Control measures can include engineering controls, administrative controls, or the use of personal protective equipment (PPE). The aim is to mitigate the risks and create a safer working environment.
- Responsibilities: The JSA should clearly define the roles and responsibilities of individuals involved in the job or task. This ensures that everyone understands their obligations in maintaining a safe working environment and performing their tasks safely.
- Review and Sign-Off: Once the JSA is developed, it is essential to have it reviewed by relevant stakeholders such as supervisors, safety managers, and workers. Their input and feedback can help ensure that all potential hazards and control measures are adequately addressed. Once reviewed, the JSA should be signed off by responsible parties to acknowledge their understanding and commitment to follow the safety procedures outlined.
By incorporating these components into a JSA, construction professionals can systematically identify hazards, assess risks, and implement appropriate control measures. This comprehensive approach helps create a safer working environment and protects the well-being of all individuals involved in the construction project.
Process of Developing a JSA
Developing a Job Safety Analysis (JSA) involves a systematic and collaborative approach to identify potential hazards, assess risks, and establish control measures. The process typically follows the following steps:
- Select the Job or Task: Choose a specific job or task within the construction project that requires a JSA. It is essential to identify tasks that have a higher risk potential or have a history of accidents or injuries.
- Break Down the Job: Analyze the selected job or task and break it down into its individual steps. Ensure that each step is clearly defined and provides a complete understanding of the actions involved in completing the task.
- Identify the Hazards: For each step of the job, identify the potential hazards that workers may encounter. Consider both the immediate hazards and the long-term risks associated with the task. The input from workers who have first-hand experience with the task is valuable in identifying potential hazards.
- Assess the Risks: Evaluate the level of risk associated with each identified hazard. Assess the severity and likelihood of incidents occurring due to the hazards. This risk assessment enables prioritization and allocation of resources to control the most critical risks first.
- Develop Control Measures: Based on the identified hazards and risk assessment, develop appropriate control measures to eliminate or minimize the risks. Consider engineering controls (such as barriers or ventilation systems), administrative controls (such as training or procedures), and the use of personal protective equipment (PPE).
- Communicate and Train: Ensure that all workers involved in the job or task are aware of the identified hazards and the necessary control measures. Communicate the information effectively through training sessions, safety meetings, or toolbox talks. Provide clear instructions on how to implement the control measures.
- Implement and Monitor: Put the control measures into action during the execution of the job or task. Supervisors and safety professionals should monitor the implementation to ensure compliance and effectiveness. Regular inspections and observations can help identify any gaps or areas for improvement.
- Review and Update: Regularly review and update the JSA to incorporate any changes in the job or additional hazards that may emerge. Continuous improvement is essential to ensure that the JSA remains relevant and effective throughout the entire construction project.
By following this process, construction professionals can effectively develop a JSA that addresses the specific hazards and risks associated with a particular job or task. This proactive approach enhances safety, minimizes accidents and injuries, and fosters a culture of risk identification and prevention in the construction industry.
JSA stands for Job Safety Analysis in construction. It’s a process that helps identify and address potential hazards on a job site to ensure the safety of workers.
Read more: What Does PR Stand For In Construction
Implementing JSA in Construction Projects
Implementing a Job Safety Analysis (JSA) in construction projects is crucial to ensure the safety of workers and minimize the risk of accidents and injuries. The following steps can help effectively implement JSA in construction projects:
- Commitment from Management: Management plays a vital role in the successful implementation of JSA. They must demonstrate a strong commitment to safety and provide the necessary resources, training, and support to ensure JSA becomes an integral part of the construction project.
- Establish a JSA Team: Form a team consisting of management, supervisors, safety professionals, and workers. This multi-disciplinary team will collaborate to develop, review, and implement JSA for various tasks throughout the construction project.
- Prioritize High-Risk Jobs: Identify jobs or tasks that pose a higher risk of accidents or injuries. Prioritize these tasks for JSA implementation to ensure that the most critical risks are adequately addressed.
- Involve Workers: Engage workers who have first-hand experience with the tasks in the JSA development process. Their input is valuable in identifying potential hazards and developing practical control measures. Involving workers also promotes a sense of ownership and commitment to safety.
- Document and Communicate: Document the JSA in a clear and concise manner, including job descriptions, step-by-step procedures, identified hazards, and control measures. Communicate the JSA to all relevant personnel through training sessions, toolbox talks, and safety meetings. Ensure that everyone understands their roles and responsibilities in implementing the JSA.
- Provide Training: Offer comprehensive training on the JSA, including hazard identification, risk assessment, and the proper implementation of control measures. Training should be provided to all workers involved in the job or task covered by the JSA.
- Supervision and Monitoring: Supervisors and safety professionals should closely monitor the implementation of JSA on the construction site. Regular inspections, observations, and feedback sessions can help ensure that workers are adhering to the recommended safety procedures and that the JSA remains effective.
- Continuous Improvement: Regularly review and update the JSA as necessary. Incorporate lessons learned, feedback from workers, and emerging hazards to keep the JSA relevant and effective throughout the construction project. Encourage workers to provide input and suggestions for improvement.
- Recognition and Reinforcement: Recognize and reward individuals and teams that consistently follow the JSA and contribute to maintaining a safe working environment. Positive reinforcement reinforces the importance of JSA implementation and encourages a positive safety culture on the construction site.
By implementing JSA in construction projects, companies can improve safety standards, protect workers, and minimize the risk of accidents and injuries. JSA becomes a proactive tool to identify hazards, assess risks, and implement appropriate control measures, ultimately creating a safer working environment for all individuals involved in the construction project.
Benefits of Using JSA in Construction
Implementing a Job Safety Analysis (JSA) in construction projects offers numerous benefits that contribute to a safer work environment and improved overall project outcomes. The following are the key benefits of using JSA in construction:
- Enhanced Safety: The primary benefit of using JSA is the significant improvement in safety on construction sites. By systematically identifying hazards, assessing risks, and implementing control measures, JSA helps prevent accidents and injuries. It creates a culture of safety awareness among workers and fosters a proactive approach to minimizing risks.
- Reduced Incidents: JSA helps to minimize the occurrence of accidents and incidents on construction sites. By identifying potential hazards and implementing appropriate control measures, JSA reduces the likelihood of incidents that could result in injuries, property damage, or project delays.
- Compliance with Regulations: JSA ensures compliance with safety regulations and standards set by relevant governing bodies. By systematically addressing potential hazards and implementing control measures, construction companies can fulfill legal requirements and maintain a safe and compliant work environment.
- Improved Communication and Collaboration: JSA encourages better communication and collaboration among workers, supervisors, and management. The process of developing JSA involves the active involvement of workers, their input, and feedback. This collaboration fosters a sense of teamwork and shared responsibility for safety.
- Increased Efficiency: By providing a thorough analysis of tasks and potential hazards, JSA helps identify inefficiencies in work processes. By addressing these inefficiencies, JSA can lead to improved productivity and workflow, resulting in time and cost savings for construction projects.
- Worker Empowerment: JSA empowers workers by providing them with the knowledge and information they need to perform their tasks safely. It increases their awareness of potential hazards, equips them with the necessary skills to identify and mitigate risks, and empowers them to take proactive steps to protect themselves and their colleagues.
- Continuous Improvement: JSA is an ongoing process that promotes continuous improvement in safety practices. Regular review and updating of the JSA allows for the incorporation of lessons learned, emerging hazards, and best practices. This ensures that safety procedures remain up to date and effective throughout the construction project.
- Positive Reputation: By prioritizing safety and implementing JSA in construction projects, companies enhance their reputation as responsible and conscientious organizations. This can lead to increased trust from clients, stakeholders, and the public, which can open up new business opportunities and provide a competitive edge.
By leveraging the benefits of JSA in construction, companies can create a safer working environment, reduce incidents, improve compliance with regulations, enhance communication and collaboration, increase efficiency, empower workers, promote continuous improvement, and cultivate a positive reputation. Overall, JSA contributes to the overall success of the construction project by prioritizing the well-being of workers and promoting a culture of safety.
Common Mistakes to Avoid in JSA Development
Developing a Job Safety Analysis (JSA) requires careful attention to detail and a comprehensive understanding of potential hazards and control measures. To ensure the effectiveness of the JSA, it is important to avoid common mistakes that can compromise safety. Here are some common mistakes to avoid in JSA development:
- Inadequate Job Analysis: One of the most common mistakes is conducting a superficial job analysis. Failing to thoroughly analyze the job or task can lead to incomplete identification of hazards and control measures. Take the time to fully understand each step of the job and the associated risks.
- Excluding Worker Input: Neglecting to involve workers in the JSA development process is a significant mistake. Workers often possess valuable knowledge and insights about potential hazards and effective control measures. Their input and involvement can enhance the accuracy and effectiveness of the JSA.
- Missing Potential Hazards: Overlooking potential hazards is a critical error in JSA development. It is essential to consider all possible hazards associated with each job step. This includes physical, chemical, biological, and ergonomic hazards. Thoroughly analyze the job from different perspectives to ensure that no potential hazards are missed.
- Insufficient Risk Assessment: Inaccurately assessing the severity and likelihood of risks is a common mistake. It is important to evaluate the risks associated with each hazard objectively and consider factors such as frequency of exposure, potential consequences, and available control measures. This ensures that appropriate priority is given to the most critical risks.
- Ineffective Control Measures: Choosing inadequate or ineffective control measures is a significant pitfall in JSA development. Control measures should be practical, feasible, and efficient in mitigating the identified hazards. Always consider a hierarchy of controls and select the most appropriate measures for each hazard.
- Poor Documentation and Communication: Inadequate documentation and communication of the JSA can lead to misunderstandings and improper implementation. Ensure that the JSA documentation is clear, concise, and easily accessible. Communicate the JSA effectively to all personnel involved in the job or task, including workers, supervisors, and safety professionals.
- Lack of Training: Neglecting to provide proper training on the JSA is a common mistake. Workers must receive thorough training on the identified hazards, control measures, and the proper execution of safety procedures. Regular refresher training should also be provided to ensure continuous awareness.
- Failure to Review and Update: Not reviewing and updating the JSA is a significant mistake. Construction projects are dynamic, and new hazards may arise or existing hazards may change. Regularly review and update the JSA to ensure it remains relevant and effective throughout the project duration.
By avoiding these common mistakes, construction professionals can develop a comprehensive and accurate JSA that effectively mitigates hazards and promotes safety. It is crucial to commit to a thorough analysis, involve workers, accurately assess risks, select appropriate control measures, communicate effectively, provide proper training, and maintain regular review and updates to ensure a successful JSA implementation.
Legal Requirements and Compliance with JSA
In the construction industry, ensuring compliance with legal requirements is of utmost importance to maintain a safe working environment and protect the well-being of workers. Job Safety Analysis (JSA) plays a vital role in meeting these legal requirements. Here’s how compliance with JSA can be achieved:
- Regulatory Standards: Different countries have regulatory bodies that establish safety standards for the construction industry. It is essential to familiarize yourself with the specific regulations and standards applicable to your region. Compliance with these standards often requires the implementation of a JSA or a similar risk assessment process.
- Legislation and Laws: In addition to regulatory standards, there may be specific legislation and laws related to workplace safety and health. Compliance with these laws is crucial for construction companies. Failure to comply can result in severe penalties, legal actions, and damage to the company’s reputation.
- Industry-Specific Requirements: Certain construction projects may have industry-specific regulations or requirements. For example, working on hazardous materials, confined spaces, or high-risk construction sites may have additional rules and protocols that need to be followed. Developing a JSA tailored to these specific requirements ensures compliance and mitigates risks.
- Worker Protection: Compliance with JSA is essential to protect the well-being of workers. Laws and regulations prioritize worker safety and require employers to provide a safe workplace. Implementing and enforcing a JSA demonstrates a commitment to worker protection and helps minimize the risk of accidents and injuries.
- Documentation and Records: Compliance with JSA often necessitates documentation and record-keeping. It is crucial to maintain accurate and up-to-date records of JSAs, including hazard identification, risk assessments, control measures, and training records. These records serve as evidence of compliance and can be requested during regulatory inspections.
- Training and Education: Compliance with JSA involves providing adequate training and education to workers. It is essential to ensure that workers receive proper instruction on the identified hazards, control measures, and safety procedures outlined in the JSA. Regular training sessions should be conducted to keep workers updated on safety protocols.
- Supervision and Enforcement: Compliance with JSA requires active supervision and enforcement of the safety protocols established in the JSA. This includes regular monitoring of adherence to the JSA, prompt corrective actions, and disciplinary measures for non-compliance. Supervisors play a critical role in ensuring compliance and maintaining a safe working environment.
Non-compliance with JSA and related legal requirements not only puts workers at risk but also puts the construction company at risk of legal consequences and reputational damage. By actively implementing, monitoring, and enforcing JSA compliance, construction companies can meet legal obligations, protect workers, and create a safe working environment.
Read more: What Does BIM Stand For In Construction
Conclusion
Job Safety Analysis (JSA) plays a crucial role in the construction industry, ensuring the safety of workers and minimizing the risk of accidents and injuries. By systematically identifying hazards, assessing risks, and implementing control measures, JSA helps create a safe and productive work environment on construction sites.
Throughout this article, we have explored the definition of JSA, the importance of its implementation in construction projects, and the key components involved in its development. We have also highlighted the process of developing a JSA, the benefits of using JSA in construction, common mistakes to avoid, and the legal requirements for compliance.
By diligently conducting JSA and involving workers in the process, construction companies can identify potential hazards, assess risks, and develop effective control measures. Proper implementation of JSA leads to enhanced safety, reduced incidents, compliance with legal requirements, and improved communication and collaboration among workers, supervisors, and management.
It is crucial to remember that JSA is an ongoing process and should be regularly reviewed and updated to address emerging hazards and reflect changes in job tasks. Continuous improvement, training, and proper documentation are essential factors in maintaining JSA effectiveness and compliance with legal obligations.
Ultimately, by prioritizing safety and embracing JSA in construction projects, companies can protect the well-being of their workers, enhance productivity, and maintain a positive reputation. As the construction industry continues to evolve, the implementation of JSA remains an indispensable tool in creating safer work environments and fostering a culture of safety.
Frequently Asked Questions about What Does JSA Stand For In Construction
Was this page helpful?
At Storables.com, we guarantee accurate and reliable information. Our content, validated by Expert Board Contributors, is crafted following stringent Editorial Policies. We're committed to providing you with well-researched, expert-backed insights for all your informational needs.
0 thoughts on “What Does JSA Stand For In Construction”