Home>diy>Building & Construction>What Is A Construction Takeoff
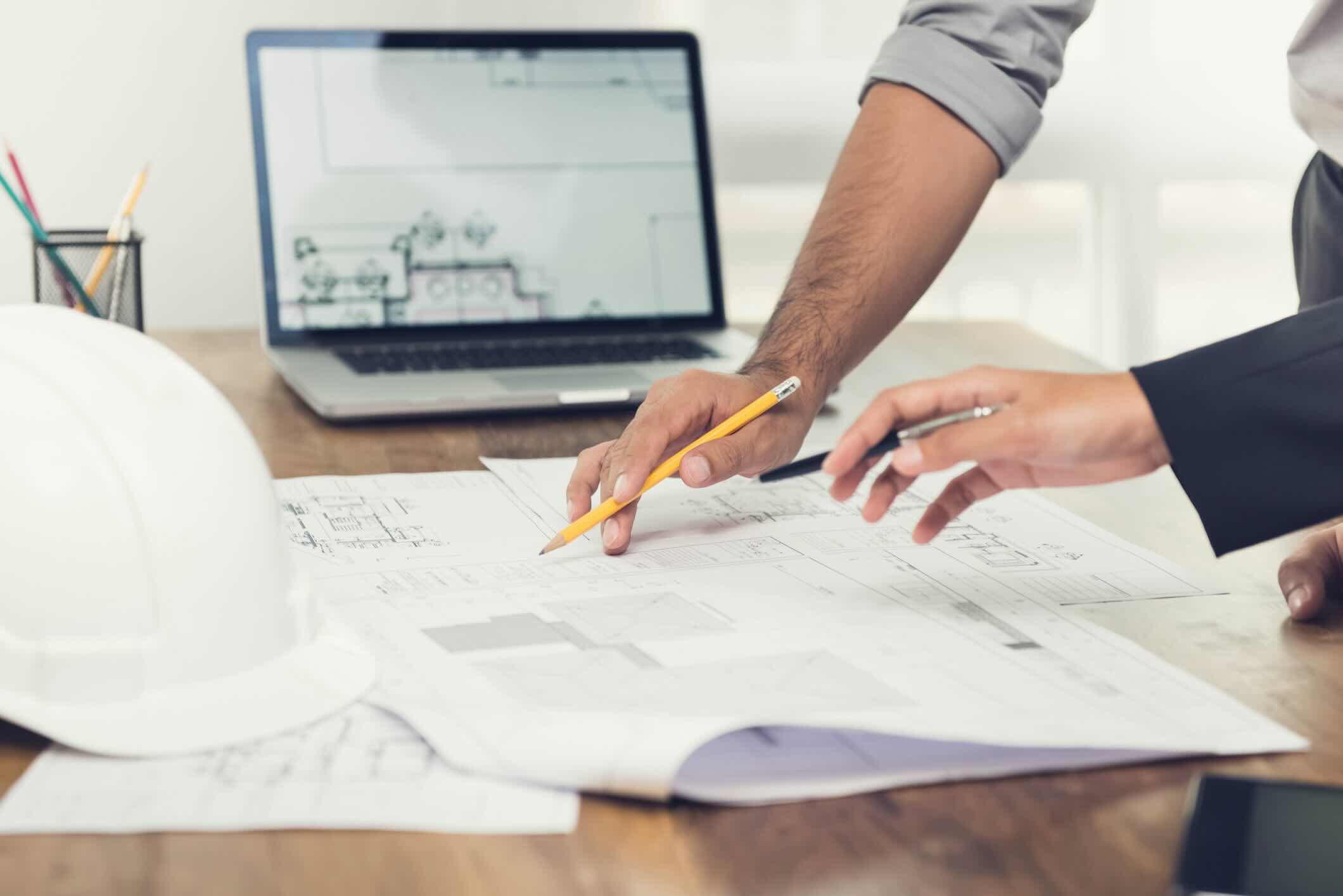
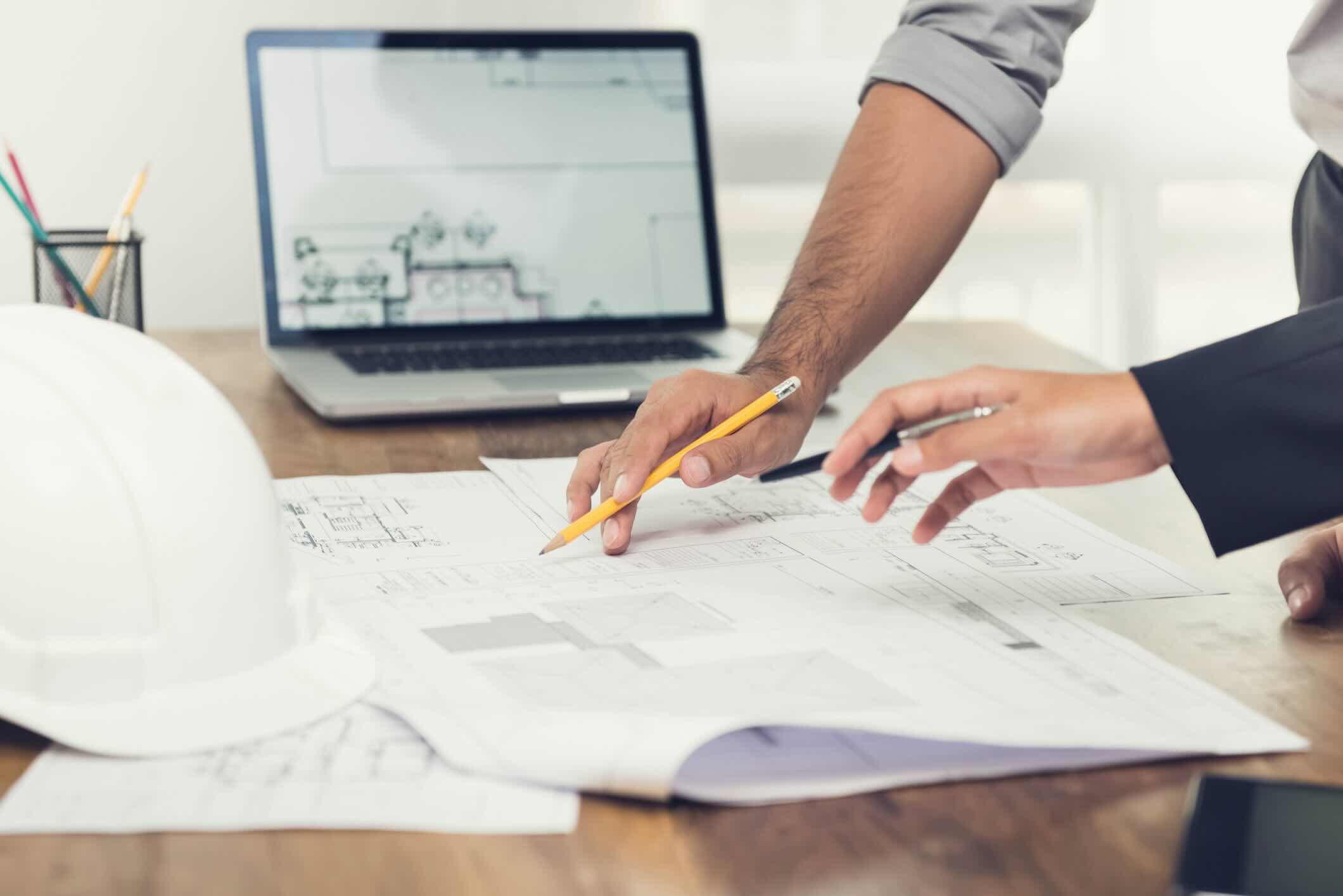
Building & Construction
What Is A Construction Takeoff
Modified: January 24, 2024
Discover what a construction takeoff is and why it is a crucial part of the building construction process. Learn how to accurately estimate materials and costs.
(Many of the links in this article redirect to a specific reviewed product. Your purchase of these products through affiliate links helps to generate commission for Storables.com, at no extra cost. Learn more)
Introduction
Welcome to the world of construction takeoff! In the construction industry, accurate and detailed planning is crucial for the success of any project. Construction takeoff plays a pivotal role in this process. It is a fundamental step that involves quantifying and estimating the materials and quantities required for a construction project.
Imagine you are embarking on a construction project: whether it’s building a residential home or a commercial establishment, you need to have a clear understanding of the materials, quantities, and costs involved. This is where construction takeoff comes into play. By performing a thorough construction takeoff, you can ensure that you have a detailed list of materials and quantities required, enabling you to estimate costs, create accurate budgets, and plan effectively.
Construction takeoff involves analyzing architectural and engineering drawings, blueprints, and specifications to determine the quantities of materials needed for each aspect of the project. This can include everything from the number of bricks, bags of cement, and tons of steel reinforcement, to the length of electrical wiring and amount of plumbing materials required.
With the advent of digital technologies, construction takeoff has evolved from manual calculations to specialized software and tools. These tools save time, reduce errors, and provide a more efficient way to perform takeoffs. However, even with advanced software, a solid understanding of construction techniques, materials, and processes is still essential for accurate and comprehensive takeoffs.
Throughout this article, we will explore the definition, purpose, importance, process, tools, benefits, and limitations of construction takeoff. By the end, you will have a thorough understanding of how construction takeoff contributes to the success of construction projects and why it is an essential aspect of the construction industry.
Key Takeaways:
- Construction takeoff is the meticulous process of quantifying materials for a construction project, crucial for accurate cost estimation, streamlined procurement, and efficient resource planning, ultimately ensuring project success.
- While construction takeoff offers numerous benefits, it also has limitations such as reliance on accurate plans, subjective waste estimation, and the need for adaptability to site-specific conditions. Careful review and ongoing communication are essential to mitigate these challenges.
Read more: How To Do A Takeoff In Construction
Definition of Construction Takeoff
In the construction industry, a construction takeoff refers to the process of determining the quantities of materials required for a specific project. It involves analyzing architectural drawings, blueprints, and specifications to identify and quantify the materials needed for each component of the project. These materials can include everything from concrete, steel, and lumber to electrical wiring, plumbing fixtures, and HVAC systems.
Construction takeoff is also known as material takeoff or quantity takeoff. It is essentially a detailed measurement of the materials needed for construction, allowing contractors, project managers, and estimators to assess the project’s scope and associated costs accurately.
The takeoff process starts with a thorough review of the project plans and specifications, including drawings, schematics, and any other relevant documentation. The goal is to identify and extract all the necessary information to calculate the quantities and types of materials required.
Once the information is gathered, estimators or quantity surveyors use specialized software or manual calculations to perform the takeoff. They break down the project into individual components, such as walls, floors, and roofs, and determine the dimensions and quantities of materials needed for each element.
For instance, in the takeoff process, estimators would identify the number of bricks, bags of cement, and gallons of paint required for the exterior walls of a building. They would also calculate the amount of electrical cable, switchboards, and light fixtures needed for the electrical system.
The culmination of a construction takeoff is a comprehensive list or schedule that outlines the quantities and specifications of each material required. This document serves as a foundation for creating accurate cost estimates, ordering materials, and developing construction schedules.
Furthermore, the construction takeoff is not a one-time activity. It evolves throughout the various stages of a project, from the initial bidding and estimation phase to the detailed planning and execution stages. As the project progresses, the takeoff may be revised and refined to reflect any changes or modifications to the scope of work.
In summary, a construction takeoff is the process of quantifying and estimating the materials needed for a construction project. It involves analyzing drawings and specifications, breaking down the project into components, and calculating the quantities of materials required for each element. The resulting material takeoff serves as a vital tool for accurate budgeting, procurement, and planning throughout the entire construction process.
Purpose of Construction Takeoff
The purpose of construction takeoff is multi-faceted, serving crucial functions in the construction project lifecycle. Let’s explore the key purposes of construction takeoff:
- Cost Estimation: Construction takeoff plays a significant role in accurate cost estimation. By quantifying the materials required, contractors and estimators can calculate the costs associated with purchasing, transporting, and installing those materials. This information enables them to create realistic budgets for the project, ensuring that all expenses are accounted for. Without an accurate takeoff, cost estimates may be inflated or underestimated, potentially leading to financial issues during project execution.
- Material Procurement: A comprehensive construction takeoff provides a detailed list of materials needed for the project. This list assists in the procurement process, enabling project managers to order materials in the correct quantities and at the appropriate time. By having a clear understanding of the materials required, they can optimize procurement strategies, negotiate better prices with suppliers, and ensure timely delivery of materials to the construction site. Efficient material procurement minimizes project delays and avoids costly disruptions due to material shortages.
- Resource Planning: Construction takeoff allows project managers and contractors to plan their resources effectively. By knowing the quantities and types of materials required, they can allocate labor, equipment, and machinery accordingly. This ensures that the right resources are available at the right time, preventing delays and optimizing productivity. With accurate resource planning, construction teams can complete tasks efficiently and meet project timelines.
- Project Scheduling: The quantities and durations derived from construction takeoff assist in creating realistic construction schedules. By understanding the materials needed for each phase of the project, project managers can allocate appropriate timeframes and set achievable milestones. This enables effective coordination of tasks, reduces conflicts, and ensures that the project progresses in a smooth and organized manner.
- Material Waste Reduction: Construction takeoff allows for precise material calculations, which helps minimize waste on the construction site. By knowing the exact quantities needed, contractors can avoid excess material purchases, reduce overordering, and optimize material utilization. This not only reduces project costs but also contributes to sustainable construction practices by minimizing unnecessary waste generation.
In summary, the purpose of construction takeoff is to support accurate cost estimation, optimize material procurement, facilitate resource planning, aid project scheduling, and reduce material waste. It serves as a critical tool for effective project management, ensuring that construction projects are completed on time, within budget, and with minimal disruptions.
Importance of Construction Takeoff
Construction takeoff plays a vital role in the success of construction projects, offering several important benefits. Let’s explore the key reasons why construction takeoff is of utmost importance:
- Accurate Cost Estimation: One of the primary benefits of construction takeoff is its ability to provide accurate cost estimates. By quantifying the materials needed for each aspect of the project, contractors and estimators can calculate the associated costs more precisely. This ensures that budgets are realistic, minimizing the risk of financial overruns and ensuring that projects remain profitable.
- Better Project Planning: Construction takeoff enables project managers to plan construction projects more effectively. With a thorough understanding of the materials required, they can allocate resources, create timelines, and coordinate tasks more efficiently. This leads to improved project planning, reducing delays, streamlining workflows, and ensuring that projects are completed on time.
- Optimized Material Procurement: The accurate quantity calculations from construction takeoff help optimize material procurement. By knowing the exact quantities of materials needed, project managers can order materials in the correct amounts, preventing over- or under-ordering. This reduces waste, minimizes storage requirements, and improves cash flow. Additionally, optimized procurement leads to better negotiation of prices with suppliers, resulting in cost savings for the project.
- Enhanced Resource Management: Construction takeoff allows for effective resource management. With detailed quantity calculations, project managers can allocate labor, equipment, and machinery based on the project’s needs. This ensures that resources are utilized efficiently, minimizing idle time and maximizing productivity. By having the right resources at the right time, construction projects can progress smoothly and prevent bottlenecks.
- Improved Communication and Collaboration: Construction takeoff promotes effective communication and collaboration amongst project stakeholders. The detailed takeoff documents provide a common understanding of the project’s requirements, allowing for clear communication between architects, engineers, contractors, and suppliers. This minimizes misunderstandings, prevents errors, and fosters collaboration throughout the project lifecycle.
- Risk Mitigation: By performing a thorough construction takeoff, potential risks and challenges can be identified upfront. The detailed analysis of the project’s materials and quantities allows for proactive risk mitigation strategies to be implemented. Any discrepancies or uncertainties in the takeoff can be addressed and resolved before construction begins, reducing the likelihood of costly errors or delays during project execution.
Overall, the importance of construction takeoff lies in its ability to provide accurate cost estimation, facilitate better project planning, optimize material procurement, enhance resource management, improve communication and collaboration, and mitigate potential risks. By leveraging construction takeoff effectively, construction professionals can ensure the successful delivery of projects while maximizing efficiency and profitability.
Process of Construction Takeoff
The process of construction takeoff involves several sequential steps, each contributing to the detailed quantification of materials required for a construction project. Let’s explore the key stages of the construction takeoff process:
- Review Project Plans and Specifications: The initial step in the construction takeoff process is to thoroughly review the project plans, drawings, blueprints, and specifications. This includes studying architectural and engineering drawings, electrical and mechanical plans, and any other relevant documentation. The goal is to gain a comprehensive understanding of the project’s scope and requirements.
- Identify Building Components: Next, the drawing and specification review enables the takeoff team to identify and break down the project into its individual components. This could include walls, floors, roofs, electrical systems, plumbing systems, and more. Each element is examined separately to ensure a comprehensive assessment.
- Measure Dimensions: After identifying the building components, measurements are taken to determine the dimensions of each element. This involves measuring lengths, widths, heights, areas, and volumes. Accurate measurements are essential for precise quantity calculations.
- Calculate Quantities: Once dimensions are established, the takeoff team calculates the quantities of materials required for each component. This involves applying the appropriate formulas, algorithms, or software to determine the number of units or amounts needed. For example, calculating the number of bricks for a wall or the length of electrical wiring for a floor.
- Account for Waste and Allowances: In addition to calculating exact quantities, the takeoff process accounts for waste and allowances. Certain materials may have a waste factor due to cutting, breakage, or installation considerations. Furthermore, allowances are included for additional materials needed for unforeseen circumstances or variations in construction plans.
- Create Takeoff Schedule: Based on the quantity calculations, the takeoff process involves creating a detailed takeoff schedule. This document outlines the specific quantities, dimensions, and specifications of materials required for each component of the project. It serves as a reference for estimating costs, procuring materials, and managing construction activities.
- Revise and Update: The construction takeoff is not a one-time activity. As the project progresses, there may be changes in plans, designs, or materials. It is essential to revise and update the takeoff continuously to incorporate any modifications. This ensures that the project remains aligned with the updated requirements and avoids discrepancies during construction.
Throughout the construction takeoff process, precision, attention to detail, and a sound understanding of construction practices are crucial. Estimators, quantity surveyors, and other professionals involved in the takeoff process rely on their expertise and industry knowledge to accurately calculate quantities and create comprehensive takeoff schedules.
By following a systematic and meticulous approach, the process of construction takeoff provides an accurate and detailed assessment of the materials needed for a project. This information is invaluable for cost estimation, procurement, resource planning, and project execution.
A construction takeoff is a detailed list of materials and quantities needed for a project. It’s essential for accurate cost estimation and project planning.
Read more: What Are Blueprint Takeoffs
Tools and Techniques Used in Construction Takeoff
Construction takeoff has evolved significantly with the advancement of digital technologies, resulting in the emergence of various tools and techniques to streamline and enhance the process. Let’s explore some of the commonly used tools and techniques in construction takeoff:
- Manual Takeoff: Traditional manual takeoff involves using rulers, scales, and physical drawings to measure and quantify materials. Estimators manually calculate quantities by referencing architectural and engineering drawings, and specifications. While manual takeoff is time-consuming and prone to human error, it can still be used for small-scale projects or as a backup to verify digital takeoffs.
- Spreadsheet Software: Spreadsheet software, such as Microsoft Excel or Google Sheets, is often utilized to perform construction takeoff calculations. Estimators input the dimensions, quantities, and waste factors into predefined formulas to calculate the quantities of materials required. Spreadsheet software allows for organization, customization, and easy manipulation of data, making it a versatile tool for construction takeoffs.
- Digital Takeoff Software: Specialized digital takeoff software has gained popularity in recent years due to its efficiency and accuracy. These software applications, such as Bluebeam, PlanSwift, and On-Screen Takeoff, provide a digital platform for performing takeoff measurements and calculations. They typically include features like measurement markup tools, quantity calculations, cost estimation, and integration with other project management software.
- BIM (Building Information Modeling): BIM software, like Autodesk Revit and ArchiCAD, enables construction professionals to perform takeoffs directly from the 3D models created during the design phase. BIM models contain detailed information about each element of the project, including dimensions, quantities, and specifications. With BIM, estimators can extract data automatically, reducing manual takeoff efforts and enhancing accuracy.
- Digitized Plans: Scanned or digitized copies of architectural and engineering plans allow for faster and more accurate measurements during takeoff. Digital plans facilitate zooming, panning, and annotating, making it easier to locate and measure dimensions. They also offer the advantage of easy sharing and collaboration among project stakeholders.
- Integrated Software Solutions: Some construction management software platforms offer integrated takeoff capabilities. These solutions combine digital takeoff tools with other project management functions, such as cost estimation, procurement, scheduling, and document management. By integrating these capabilities, construction professionals can streamline workflows and ensure data consistency across different project tasks.
When selecting tools and techniques for construction takeoff, it is essential to consider factors such as project size, complexity, available resources, and budget. Each tool and technique has its own benefits and limitations, so it is crucial to choose the one that best suits the specific requirements of the project.
By leveraging the power of digital tools and techniques, construction professionals can enhance the efficiency, accuracy, and productivity of their construction takeoff processes. These advancements contribute to improved cost estimation, resource planning, and project execution, ultimately leading to successful project outcomes.
Benefits of Construction Takeoff
Construction takeoff brings forth a range of benefits that greatly impact the success of construction projects. Let’s explore some of the key advantages of implementing construction takeoff:
- Accurate Cost Estimation: By performing a comprehensive construction takeoff, contractors and estimators can generate accurate cost estimates. The detailed quantification of materials allows for precise calculations of material costs, labor costs, and other associated expenses. Accurate cost estimation enhances financial planning, prevents cost overruns, and ensures profitability throughout the project.
- Improved Project Planning: Construction takeoff supports effective project planning by providing a clear understanding of materials and quantities required. This information allows project managers to develop detailed schedules, allocate resources appropriately, and coordinate tasks efficiently. Improved project planning minimizes delays, optimizes productivity, and enhances overall project management.
- Enhanced Material Procurement: The detailed material quantities obtained through construction takeoff aid in optimized procurement. Project managers can order materials in the correct quantities, preventing over- or under-ordering. This minimizes waste, reduces storage requirements, and ensures timely availability of materials, minimizing project delays and disruptions.
- Streamlined Resource Allocation: Construction takeoff facilitates effective resource allocation by providing accurate data on material quantities. Project managers can allocate labor, equipment, and machinery based on the requirements of each component. This ensures that resources are utilized efficiently, reducing costs and improving productivity.
- Reduced Material Waste: Construction takeoff helps minimize material waste on construction sites. Precise quantity calculations prevent over-ordering of materials, leading to reduction in waste resulting from excess quantities. This contributes to sustainability goals by reducing the environmental impact of construction activities.
- Enhanced Communication and Collaboration: Construction takeoff serves as a common reference point for all project stakeholders. The detailed takeoff schedules foster effective communication, ensuring everyone involved is on the same page in terms of materials and quantities required. This helps prevent misunderstandings, reduces errors, and enhances collaboration among architects, engineers, contractors, and suppliers.
- Better Project Control: Construction takeoff provides a comprehensive overview of the project’s materials and quantities, enabling better control and monitoring. Project managers can track the progress of work, verify that the correct materials are being used, and identify any deviations or discrepancies. This enhances quality control and ensures adherence to project specifications.
- Increased Profitability: By accurately estimating costs, optimizing material procurement, and enhancing resource allocation, construction takeoff contributes to increased project profitability. It minimizes costly errors, prevents rework, and improves overall project efficiency. Ultimately, improved profitability helps businesses thrive in a competitive construction industry.
In summary, construction takeoff delivers a range of benefits, including accurate cost estimation, improved project planning, enhanced material procurement, streamlined resource allocation, reduced material waste, better communication and collaboration, increased project control, and increased profitability. Incorporating construction takeoff into construction project workflows is essential for achieving successful project outcomes.
Limitations of Construction Takeoff
While construction takeoff offers numerous benefits, it is important to recognize its limitations as well. Understanding these limitations helps project stakeholders make informed decisions and implement strategies to mitigate any potential challenges. Let’s explore some of the key limitations of construction takeoff:
- Dependence on Accuracy of Plans: Construction takeoff heavily relies on the accuracy and completeness of project plans, drawings, and specifications. Any errors or omissions in the documentation can lead to inaccurate quantity calculations and subsequent project issues. It is crucial to carefully review and validate the accuracy of plans before conducting a takeoff.
- Subjectivity in Estimating Waste Factors: Construction takeoff involves estimating waste factors for materials, which can be subjective. The accuracy of waste factors relies on the experience and expertise of the estimator. Different estimators may have different interpretations and approaches to calculating waste, leading to variations in material quantities and costs.
- Inability to Account for Site Conditions: Construction takeoff is typically based on general assumptions and standard construction practices. It does not account for site-specific conditions that may affect material quantities and requirements. Factors such as terrain, accessibility, weather conditions, and unforeseen obstacles can impact actual material usage, making it critical to adapt takeoff quantities accordingly during the construction phase.
- Risk of Human Error: Construction takeoff involves manual data entry and calculations, which introduces the risk of human error. Estimators must be diligent and meticulous, ensuring accurate measurements and calculations. Even with digital takeoff tools, errors can still occur if input data is incorrect or misunderstood. Regular quality checks and verification are necessary to minimize errors and inaccuracies.
- Limited Scope of Takeoff: Construction takeoff typically focuses on the quantification of materials but may not encompass all aspects of a construction project. Other important factors such as labor, equipment, permits, and overhead costs are often not included in the takeoff. This limitation necessitates the integration of takeoff data with other project management tools to provide a comprehensive understanding of project costs and requirements.
- Changes in Project Scope: Construction projects are dynamic, and project scopes often undergo modifications throughout the lifecycle. As plans change, the initial construction takeoff may become outdated, leading to discrepancies between the planned quantities and required quantities. Regular revisiting and updating of the takeoff are necessary to adapt to changes and ensure accuracy.
- Variances in Material Yield and Availability: Construction takeoff relies on predetermined material quantities based on industry standards. However, variances in material yield and availability can occur, impacting the actual material usage. For example, variations in material thickness, size, or quality can affect the quantities required. It is essential to account for these variances during the procurement and construction phases.
- Risks of Over- or Under-ordering: Construction takeoff aims to minimize material waste by ordering the correct quantities. However, there is still a risk of over or under-ordering materials based on the accuracy of the takeoff and unforeseen changes during construction. Over-ordering leads to unnecessary expenses and excessive waste, while under-ordering can result in delays, additional costs, and disruptions to the project.
Despite these limitations, construction takeoff remains a valuable tool in the construction industry. With careful planning, verification processes, and ongoing communication among project stakeholders, potential issues arising from these limitations can be managed effectively, ensuring successful project outcomes.
Conclusion
Construction takeoff is a critical process that plays a key role in the success of construction projects. It involves quantifying and estimating the materials and quantities required for a specific project, enabling accurate cost estimation, streamlined resource allocation, optimized material procurement, and enhanced project planning.
Throughout this article, we explored the definition of construction takeoff and its purpose in the construction industry. We discussed the importance of construction takeoff in providing accurate cost estimation, improving project planning, and minimizing material waste. We also examined the process of construction takeoff, the tools and techniques used, and the benefits it offers to project stakeholders.
However, it is important to recognize the limitations of construction takeoff, such as its dependency on accurate plans, subjectivity in estimating waste factors, and the need for adaptability to site-specific conditions. It is crucial for project stakeholders to address these limitations through careful review, verification, and ongoing communication to ensure the accuracy and reliability of the takeoff process.
In conclusion, construction takeoff serves as a crucial step in the construction project lifecycle. By quantifying and estimating materials accurately, construction professionals can make informed decisions, manage costs effectively, optimize resource allocation, and execute projects efficiently. Implementing construction takeoff methodologies and utilizing advanced digital tools can significantly contribute to the success and profitability of construction projects.
Frequently Asked Questions about What Is A Construction Takeoff
Was this page helpful?
At Storables.com, we guarantee accurate and reliable information. Our content, validated by Expert Board Contributors, is crafted following stringent Editorial Policies. We're committed to providing you with well-researched, expert-backed insights for all your informational needs.
0 thoughts on “What Is A Construction Takeoff”