Home>diy>Architecture & Design>What Are Blueprint Takeoffs
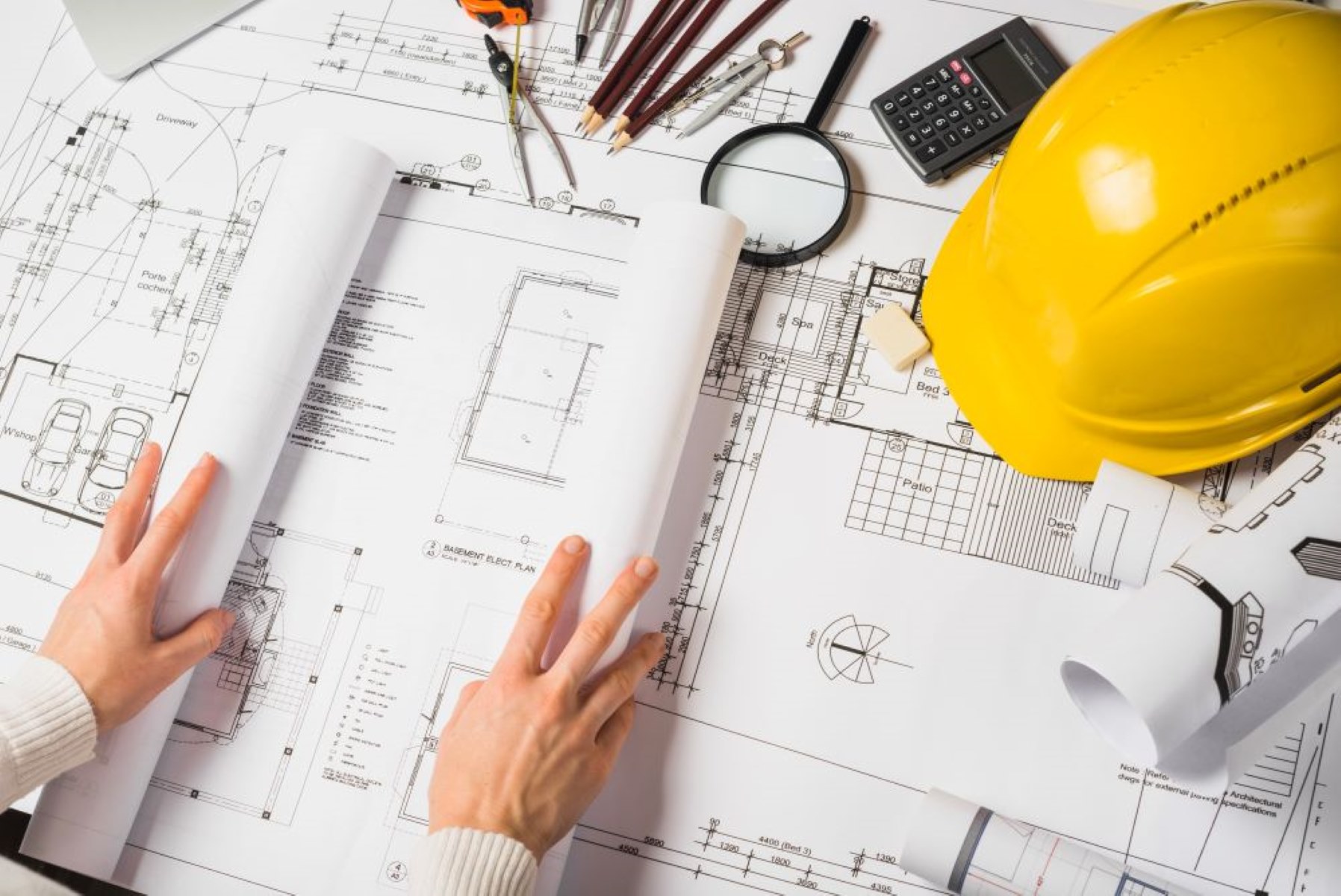
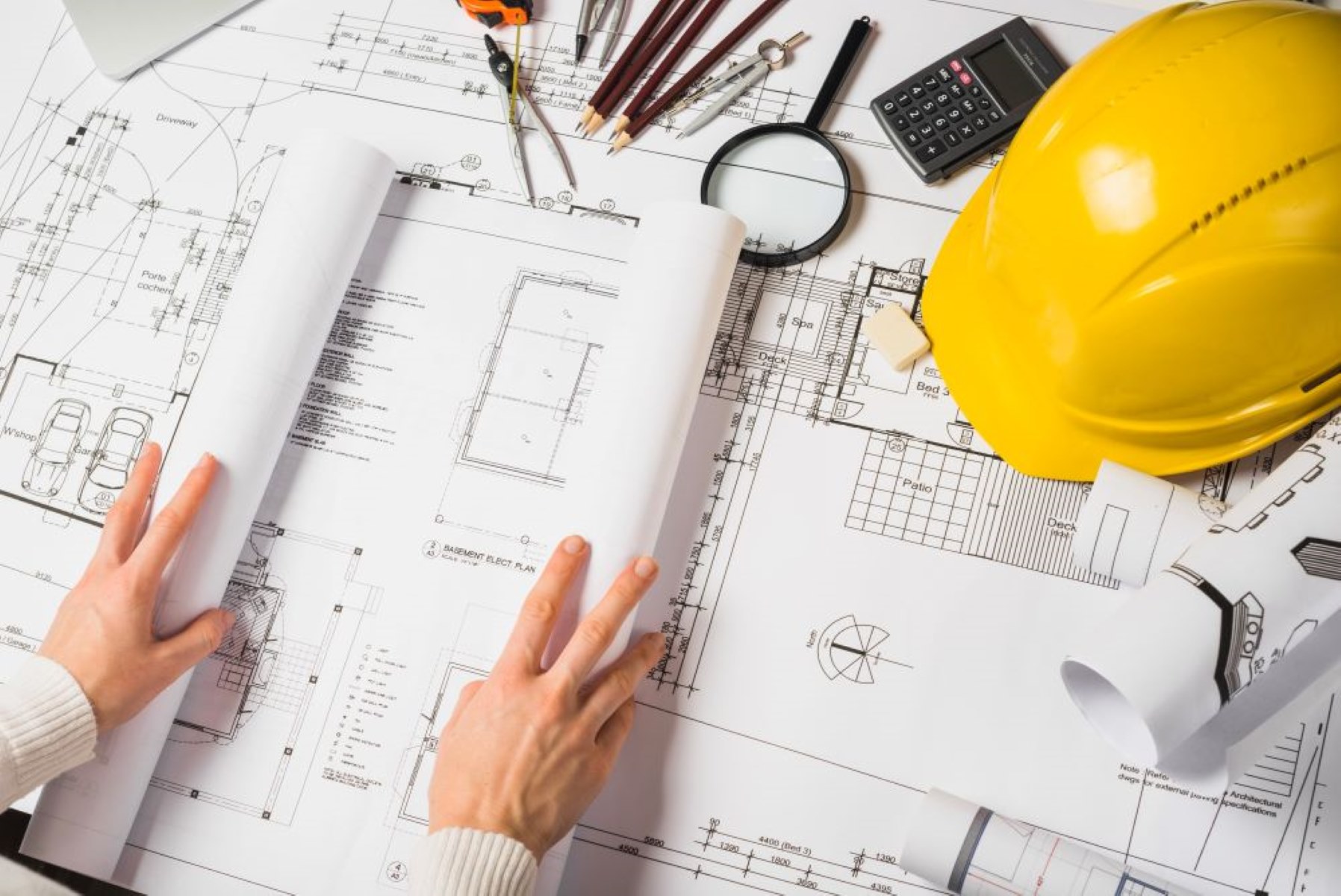
Architecture & Design
What Are Blueprint Takeoffs
Modified: January 6, 2024
Learn what blueprint takeoffs are in the world of architecture and design. Understand how this process is used to estimate project costs and quantities accurately.
(Many of the links in this article redirect to a specific reviewed product. Your purchase of these products through affiliate links helps to generate commission for Storables.com, at no extra cost. Learn more)
Introduction
When it comes to architecture and design projects, one crucial aspect is the accurate measurement and analysis of blueprints. This process, known as blueprint takeoffs, plays a vital role in ensuring the successful execution of a project. In this article, we will explore the ins and outs of blueprint takeoffs, including what they are, why they are important, how to perform them, and the tools available to assist in the process.
Blueprints serve as the foundation of any architectural project. They are detailed technical drawings that outline the specifications, dimensions, and overall design of a structure. Architects and designers rely on blueprints to communicate their vision to contractors, engineers, and other stakeholders involved in the construction process.
However, blueprints alone are not sufficient for actual construction. Contractors and estimators need to analyze these drawings accurately to determine the quantities of materials required, estimate costs, and create a detailed project plan. This is where blueprint takeoffs come into play.
A blueprint takeoff involves carefully measuring and quantifying various elements within the blueprint, including walls, windows, doors, flooring, and more. This allows for a precise calculation of material requirements and cost estimations. It provides an accurate roadmap for the construction process, saving time, money, and ensuring the project stays on track.
The accuracy of a blueprint takeoff is crucial to the success of a project. An error in measurement or calculation can lead to delays, budget overruns, and even structural issues down the line. Therefore, it is essential to follow a systematic approach and utilize the right tools to ensure precision during the takeoff process.
In the following sections, we will delve deeper into the steps involved in performing a blueprint takeoff, explore the software and tools that can assist in the process, discuss some common challenges, and provide tips for accurate takeoffs. By the end of this article, you will have a comprehensive understanding of blueprint takeoffs and be better equipped for your next architecture or design project.
Key Takeaways:
- Accurate blueprint takeoffs are crucial for successful construction projects, providing insights into materials, costs, and project planning. Thorough review, collaboration, and digital tools enhance precision and efficiency.
- Overcoming challenges in blueprint takeoffs requires proactive communication, attention to detail, and adaptability. Seeking clarification, maintaining consistency, and continuous learning are key for accurate and efficient takeoffs.
Read more: What Is A Construction Takeoff
What is a Blueprint?
A blueprint is a detailed technical drawing that provides a visual representation of an architectural or design project. It serves as a roadmap for constructing buildings, bridges, infrastructure, and other structures. Blueprints are created by architects, engineers, and designers to communicate their vision and specifications to contractors, builders, and other professionals involved in the construction process.
Before the advent of digital design tools, blueprints were created using a manual drafting process. Architects would meticulously draw the plans by hand, using instruments like T-squares, rulers, compasses, and drafting pencils. These drawings would be made on blue-tinted paper, hence the name “blueprints.”
In modern times, blueprints have transitioned from manual drafting to digital formats. Computer-aided design (CAD) software allows architects and designers to create precise and intricate blueprints with ease. These digital blueprints can be easily shared, edited, and stored in electronic format, reducing the need for physical copies.
Blueprints are essential in the construction industry as they provide detailed information about the structure, dimensions, materials, and other specifications. They include various types of drawings, such as floor plans, elevations, sections, and details. Each of these drawings focuses on different aspects of the project, providing a comprehensive view of the design.
Floor plans outline the layout of each level of the building, indicating the arrangement of walls, rooms, doors, and windows. Elevations show the exterior view of the building from different angles, providing details about the façade, roofline, and openings. Sections depict a vertical cut through the building, revealing interior details, such as the ceiling height and structural elements. Details zoom in on specific areas of the design, such as staircases, windows, or unique features, providing additional information that cannot be easily conveyed in other drawings.
Blueprints also include dimensions, which allow contractors and builders to accurately interpret the scale of the design and determine the positioning of various elements. Symbols and notations are used to represent different materials, fixtures, and finishes, enabling a clear understanding of the proposed construction.
Overall, blueprints are a crucial component of the construction process, serving as a vital communication tool between architects and builders. They provide the necessary information to transform a design concept into a physical structure, ensuring that the final result aligns with the original vision.
What is a Takeoff?
In the world of architecture, engineering, and construction, a takeoff refers to the process of quantifying and estimating the materials and quantities needed for a project based on the information provided in the blueprints. It involves meticulously calculating the dimensions, quantities, and specifications of various elements, such as walls, floors, doors, windows, and more.
Takeoffs play a critical role in the planning and budgeting phases of a construction project. They provide estimators, contractors, and suppliers with detailed information on the amount of materials required, allowing for accurate budgeting, cost estimation, and procurement. It also helps in identifying any potential discrepancies or issues in the design early on, reducing the risk of delays or budget overruns.
The process of performing a takeoff involves carefully analyzing the blueprints and systematically measuring the relevant dimensions. This can be done manually by using rulers, measuring tapes, and calculators, or with the help of specialized takeoff software programs that enable digital measurements and calculations.
During a takeoff, various elements in the blueprint are evaluated to determine the required quantities. For example, in the case of flooring, the area of each room is measured and multiplied by the quantity needed per square foot or yard. Similarly, for walls, the length and height of each wall segment are calculated to estimate the necessary quantities of materials such as studs, drywall, insulation, and paint.
Takeoffs are not limited to just materials. They also encompass other aspects of a project, such as the estimation of labor costs and equipment requirements. For example, takeoffs for electrical systems might involve evaluating the number of outlets, switches, and fixtures, as well as estimating the lengths of wiring and conduit needed.
Accurate takeoffs are crucial to the success of a project, as they directly impact project planning, cost estimation, and ultimately, the construction process. It is essential to meticulously review the blueprints, ensure all measurements are precise, and double-check calculations to minimize errors and discrepancies. Taking the time to perform a thorough takeoff can prevent costly and time-consuming issues during the construction phase.
In summary, a takeoff is the process of quantifying and estimating the materials, labor, and equipment needed for a construction project based on the information provided in the blueprints. It is a meticulous task that requires attention to detail and accuracy to ensure successful project execution.
Importance of Blueprint Takeoffs
Blueprint takeoffs are a crucial step in the construction process and hold significant importance for several reasons. Let’s explore why blueprint takeoffs are essential and the benefits they bring to architectural and design projects.
Accurate Cost Estimation: One of the primary reasons for performing blueprint takeoffs is to estimate the costs of a project. By analyzing the blueprints and quantifying the materials needed, contractors, estimators, and project managers can accurately determine the cost of materials, labor, and equipment. This allows for a more precise budgeting process and helps prevent cost overruns or underestimations, ensuring the project stays within its financial boundaries.
Material Requirements: Blueprint takeoffs provide accurate insights into the quantities of materials required for a construction project. This information is invaluable during the procurement process, as it helps contractors and suppliers order the right amount of materials at the right time. Avoiding unnecessary material shortages or excess inventory reduces waste and optimizes resource allocation, ultimately leading to cost savings.
Project Planning and Scheduling: A comprehensive blueprint takeoff enables project managers to plan and schedule the construction process efficiently. By knowing the precise quantities and dimensions of various elements, construction teams can create detailed project plans, set realistic timelines, and allocate resources effectively. This level of planning ensures smooth project execution, minimizes delays, and enhances overall productivity.
Risk Mitigation: Blueprint takeoffs help identify potential issues and discrepancies in the design early on. By meticulously evaluating the blueprints, estimators can spot any errors or inconsistencies that could lead to costly problems during construction. This early detection allows for necessary revisions and ensures that the project proceeds smoothly without unexpected obstacles or rework, reducing risks and associated costs.
Collaboration and Communication: Blueprint takeoffs serve as a common language that facilitates effective communication between architects, designers, contractors, subcontractors, and suppliers. The detailed information provided in the takeoff ensures that everyone involved has a clear understanding of the project requirements. This alignment minimizes confusion, prevents misinterpretations, and promotes collaborative decision-making, fostering a more efficient and seamless construction process.
Client Confidence: Accurate blueprint takeoffs inspire confidence in clients and stakeholders. When clients see a detailed and well-calculated takeoff, they gain a clear understanding of the project scope, costs, and timelines. This transparency builds trust and enhances client satisfaction, as they can rest assured that the project is meticulously planned and executed with their best interests in mind.
The importance of blueprint takeoffs cannot be overstated. They are a critical component of successful construction projects, ensuring accurate cost estimation, efficient resource allocation, risk mitigation, and effective collaboration. By investing time and effort into performing thorough blueprint takeoffs, project teams set themselves up for success and create a solid foundation for a smooth and successful construction process.
How to Perform a Blueprint Takeoff
Performing a blueprint takeoff requires a systematic approach and attention to detail. By following these steps, you can conduct a thorough and accurate takeoff for your architectural or design project:
Step 1: Gather the necessary tools and resources: Before starting the takeoff process, ensure you have all the tools and resources you need. This may include physical tools like rulers, calculators, and measuring tapes, or digital tools such as takeoff software or CAD programs. Make sure you have access to the latest version of the blueprints and any additional documentation that may be required.
Step 2: Familiarize yourself with the blueprints: Spend time thoroughly reviewing the blueprints and gaining a strong understanding of the design and layout. Pay close attention to the dimensions, symbols, and notations used. Familiarize yourself with the different types of drawings, such as floor plans, elevations, sections, and details, as each will provide specific information relevant to the takeoff process.
Step 3: Determine the scale: Find the scale of the blueprints to ensure accurate measurements. This information is typically provided in the drawings and will help you convert measurements from the blueprint to real-world dimensions. Use a scaling ruler or digital scaling tools if necessary.
Step 4: Start with a specific element: Begin the takeoff process by focusing on one specific element or material, such as walls, windows, or flooring. This approach helps maintain clarity and prevents confusion during calculations.
Step 5: Measure and quantify: Use the appropriate tools and techniques to measure and quantify the relevant dimensions for the chosen element. Depending on the element, this may involve measuring lengths, widths, areas, or quantities. Use the scale and conversion factors to convert the measured values to real-world dimensions.
Step 6: Calculate quantities: Once you have the measurements, calculate the quantities of materials required. This may involve multiplying the measured dimensions by the appropriate unit conversions or referencing specific notations and symbols on the blueprints. Double-check all calculations to ensure accuracy.
Step 7: Document and organize: Record the measured values and calculated quantities in a systematic manner. This may involve creating spreadsheets, takeoff forms, or utilizing takeoff software to keep track of the data. Organize the information based on different elements or materials for easy reference and future use.
Step 8: Repeat for other elements: Continue the takeoff process by repeating steps 4 to 7 for each element or material in the blueprints. Be thorough and meticulous to ensure no details are missed. Take breaks when needed to maintain focus and accuracy.
Step 9: Review and cross-reference: Once the takeoff is complete, review the calculations and quantities to ensure accuracy and consistency. Cross-reference the takeoff with the blueprints to verify that no elements or materials have been overlooked or duplicated.
Step 10: Communicate the results: Share the completed takeoff with relevant parties, such as contractors, estimators, and suppliers. Clearly communicate the quantities, dimensions, and other relevant information to facilitate accurate cost estimation, procurement, and project planning.
By following these steps and maintaining precision throughout the process, you can conduct a comprehensive blueprint takeoff that provides accurate measurements, quantities, and estimations. Remember to stay organized, double-check calculations, and seek clarification from architects or designers if needed. A carefully executed takeoff sets the stage for a successful and well-executed construction project.
When conducting a blueprint takeoff, make sure to carefully review all dimensions, notes, and symbols on the plans to ensure accurate material and labor estimates.
Read more: What Is Blueprint App
Tools and Software for Blueprint Takeoffs
In today’s digital age, technology has greatly enhanced the process of blueprint takeoffs, making it more efficient and accurate. There are various tools and software available that can assist in performing detailed and precise takeoffs. Here are some of the commonly used ones:
1. Takeoff Software: Specialized takeoff software simplifies the process of performing measurements and calculations. These software applications allow users to digitally mark, measure, and quantify elements directly on the electronic blueprints. Some popular takeoff software options include Bluebeam Revu, On-Screen Takeoff, PlanViewer, and Autodesk Quantity Takeoff.
2. Computer-aided Design (CAD) Software: CAD software is widely used in the architecture and engineering fields and provides the capability to create, edit, and analyze complex blueprints digitally. CAD tools such as AutoCAD, ArchiCAD, and SketchUp allow for precise measurements, 3D modeling, and easy integration with takeoff software.
3. Digital Takeoff Tools: Digital takeoff tools are hardware devices that enable digital measurements directly on physical blueprints. These devices use laser scanning technology to capture accurate measurements and quickly transfer data to software for calculations. Examples of digital takeoff tools include the PlanWheel, Scalex Planwheel, and On-Screen Digitizer.
4. Spreadsheet Applications: Traditional spreadsheet applications like Microsoft Excel or Google Sheets can be used to record measurements, quantities, and other data during a blueprint takeoff. Spreadsheets provide a flexible and customizable format for organizing, calculating, and analyzing the information. They are also commonly used for cost estimations and budgeting.
5. Measuring Tools: Although digital tools have become prevalent, traditional measuring tools are still essential for performing manual measurements during a takeoff. Tools like rulers, measuring tapes, scaling rulers, calipers, and laser measuring devices are used to measure dimensions accurately both on paper and in the physical environment.
6. Cloud Storage and Collaboration Tools: Cloud storage platforms like Dropbox, Google Drive, and Microsoft OneDrive are extremely valuable for storing and sharing blueprint files across teams. These platforms ensure that everyone involved in the project has access to the latest version of the blueprints, facilitating collaboration and communication.
7. Integration and BIM Software: Building Information Modeling (BIM) software, such as Autodesk’s Revit or Trimble’s Tekla, integrates various aspects of the construction process, including design, estimation, and takeoffs. BIM software allows for more accurate and comprehensive takeoffs by leveraging the data-rich 3D models and information associated with the project.
Using these tools and software streamlines the blueprint takeoff process, reduces manual errors, and improves overall efficiency. The choice of tools depends on the specific requirements of the project, the level of detail needed, and the personal preferences of the estimators and contractors.
It is worth noting that while these tools enhance the takeoff process, they should be used as aids, and manual verification and cross-referencing with the blueprints are still essential to ensure accuracy. The reliability of the tools and software also depends on the quality and clarity of the blueprints, so obtaining clear and detailed drawings from architects or designers is crucial for a successful takeoff process.
Common Challenges in Blueprint Takeoffs
Performing blueprint takeoffs can present a range of challenges that estimators and contractors must navigate. These challenges can impact the accuracy and efficiency of the takeoff process. Here are some common hurdles that are often encountered:
1. Complex and Detailed Drawings: Blueprints can be intricate and contain a vast amount of information. The level of detail in the drawings can sometimes make it challenging to identify and measure specific elements accurately. Estimators may need to invest additional time and effort in deciphering the drawings and understanding the design intent to ensure an accurate takeoff.
2. Incomplete or Inconsistent Drawings: In some cases, blueprints may be incomplete or lack the necessary details required for a thorough takeoff. Missing dimensions, unclear symbols, or inconsistent notations can lead to confusion and errors during the measurement and quantification process. Estimators may need to consult with architects or designers to clarify any discrepancies or seek additional information.
3. Scale and Measurement Issues: Determining the scale of the blueprints accurately is critical. If the scale is not clearly stated or there are variations in scaling throughout the drawings, it can lead to incorrect measurements and calculations during the takeoff. Estimators need to be cautious and double-check the scaling to ensure precise measurements.
4. Interpretation and Assumptions: Blueprint takeoffs require interpretation of the design intent and assumptions about the materials and building methods used. Estimators may encounter situations where certain design elements are not explicitly mentioned or dimensions are marked ambiguously. In such cases, estimators must make educated assumptions based on experience and industry standards while seeking clarification from architects or designers when necessary.
5. Changes and Revisions: Construction projects often undergo changes and revisions, requiring frequent updates to the takeoff. These changes may include modifications to the design, material specifications, or dimensions. Estimators need to stay vigilant and adapt to these changes, ensuring that the takeoff remains accurate and up to date throughout the project’s lifecycle.
6. Time Constraints and Workload: Blueprint takeoffs can be time-consuming, especially for large-scale or complex projects. Estimators may face time constraints and high workloads, which can impact the thoroughness and accuracy of the takeoff. Balancing efficiency with precision becomes crucial in meeting project deadlines while minimizing errors.
7. Communication and Collaboration: Effective communication and collaboration between estimators, architects, and contractors are key to successful blueprint takeoffs. Miscommunication or a lack of clarity in design intent may lead to misunderstandings and inaccuracies in the takeoff. Regular communication and a clear line of contact help ensure that estimators obtain the necessary information and have the opportunity to clarify any doubts or concerns.
Despite these challenges, experienced estimators and contractors develop strategies and techniques to overcome them. Proper coordination with the design team, seeking clarification when needed, and staying up to date with industry standards and best practices can help mitigate potential issues during the blueprint takeoff process.
It is crucial for estimators to approach blueprint takeoffs with meticulous attention to detail, continuous learning, and a mindset for problem-solving. By being proactive, adaptable, and thorough, estimators can minimize challenges and increase the accuracy and efficiency of their takeoffs.
Tips for Accurate Blueprint Takeoffs
Performing accurate blueprint takeoffs is crucial for ensuring the success of construction projects. Here are some tips to help you improve the accuracy and efficiency of your blueprint takeoffs:
1. Thoroughly Review the Blueprints: Take the time to thoroughly review the blueprints before starting the takeoff process. Familiarize yourself with the drawings, symbols, and notations used. Understand the different types of drawings, such as floor plans, elevations, sections, and details. This will give you a solid foundation and help you interpret the information correctly.
2. Seek Clarification: If there are any ambiguities or uncertainties in the blueprints, don’t hesitate to seek clarification from the architects or designers. It is better to clarify any doubts before starting the takeoff rather than making assumptions that could lead to inaccuracies later on.
3. Double-Check Scaling and Measurements: Ensure that you have accurately determined the scale of the blueprints and double-check all measurements. It is easy to make errors when converting measurements from the blueprint to real-world dimensions. Taking the time to verify the scaling and measurements will help you avoid costly mistakes.
4. Maintain Consistency: Be consistent in your approach to takeoffs. Use the same set of conventions, symbols, and units consistently throughout the process. This will help you avoid confusion and ensure accuracy and uniformity in your calculations.
5. Break Down the Takeoff into Smaller Components: Instead of trying to tackle the entire takeoff in one go, break it down into smaller components or materials. Focus on one element at a time, such as walls, windows, or flooring. This approach helps minimize errors and allows you to maintain clarity and focus during the takeoff process.
6. Utilize Takeoff Software or Tools: Consider using specialized takeoff software or tools to streamline and automate the measurement and quantification process. These tools can help you quickly mark and measure elements directly on the digital blueprints, reducing manual errors and saving time.
7. Create a Systematic Workflow: Develop a systematic workflow for your takeoff process. Start with a checklist of tasks to ensure you cover all necessary elements. Keep your measurements consistent and document them in a structured format. This will help you stay organized and minimize the chances of missing important details.
8. Regularly Update and Cross-Check: As the project progresses and changes occur, ensure that your takeoff remains up to date. Regularly update the quantities and dimensions as per the revised blueprints. Cross-check your calculations and measurements to identify any inconsistencies or errors.
9. Collaborate and Communicate: Maintain open lines of communication with architects, designers, and suppliers throughout the takeoff process. Communicate any concerns or clarifications needed, and collaborate closely to ensure accurate calculations and quantities.
10. Continuously Learn and Improve: Blueprint takeoffs require practice and continuous learning. Stay updated with industry trends, best practices, and new technologies. Attend workshops, webinars, or training sessions to enhance your skills and keep up with the latest advancements in takeoff methodologies and tools.
By incorporating these tips into your blueprint takeoff process, you can improve the accuracy and efficiency of your calculations. Remember that precision and attention to detail are key in ensuring a successful construction project that stays within budget and meets the desired specifications.
Conclusion
Blueprint takeoffs are a critical aspect of the architecture and construction industry, providing valuable insights into the materials, quantities, and costs required for a project. Accurate and thorough blueprint takeoffs lay the foundation for successful project planning, cost estimation, and execution.
In this article, we explored what blueprints are and why they are essential in the construction process. We discussed the concept of takeoffs, which involve quantifying and estimating the materials based on the information provided in the blueprints. We highlighted the importance of blueprint takeoffs, including accurate cost estimation, precise material requirements, efficient project planning, risk mitigation, enhanced collaboration, and client satisfaction.
To perform a blueprint takeoff, we outlined a systematic approach that involves gathering the necessary tools, familiarizing yourself with the blueprints, measuring and quantifying elements, calculating quantities, documenting the information, and cross-referencing for accuracy. We also explored various tools and software available to assist in the takeoff process, such as takeoff software, digital takeoff tools, spreadsheets, and CAD software.
However, performing blueprint takeoffs is not without its challenges. We discussed common challenges such as complex drawings, incomplete information, measurement errors, and changes to the design. It is crucial for estimators and contractors to proactively address these challenges through effective communication, careful interpretation, attention to detail, and adaptability.
To ensure accurate blueprint takeoffs, we provided helpful tips, including thorough review of blueprints, seeking clarification when needed, double-checking scaling and measurements, maintaining consistency, utilizing takeoff software or tools, creating a systematic workflow, regular updating and cross-checking, and continuous learning and improvement.
In conclusion, blueprint takeoffs are an integral part of the construction process, enabling accurate cost estimation, efficient resource allocation, and effective project planning. By following best practices, utilizing the right tools, and staying vigilant, estimators and contractors can perform thorough and accurate takeoffs, setting the stage for successful construction projects.
Frequently Asked Questions about What Are Blueprint Takeoffs
Was this page helpful?
At Storables.com, we guarantee accurate and reliable information. Our content, validated by Expert Board Contributors, is crafted following stringent Editorial Policies. We're committed to providing you with well-researched, expert-backed insights for all your informational needs.
0 thoughts on “What Are Blueprint Takeoffs”