Home>diy>Building & Construction>What Is A Mock-Up In Construction
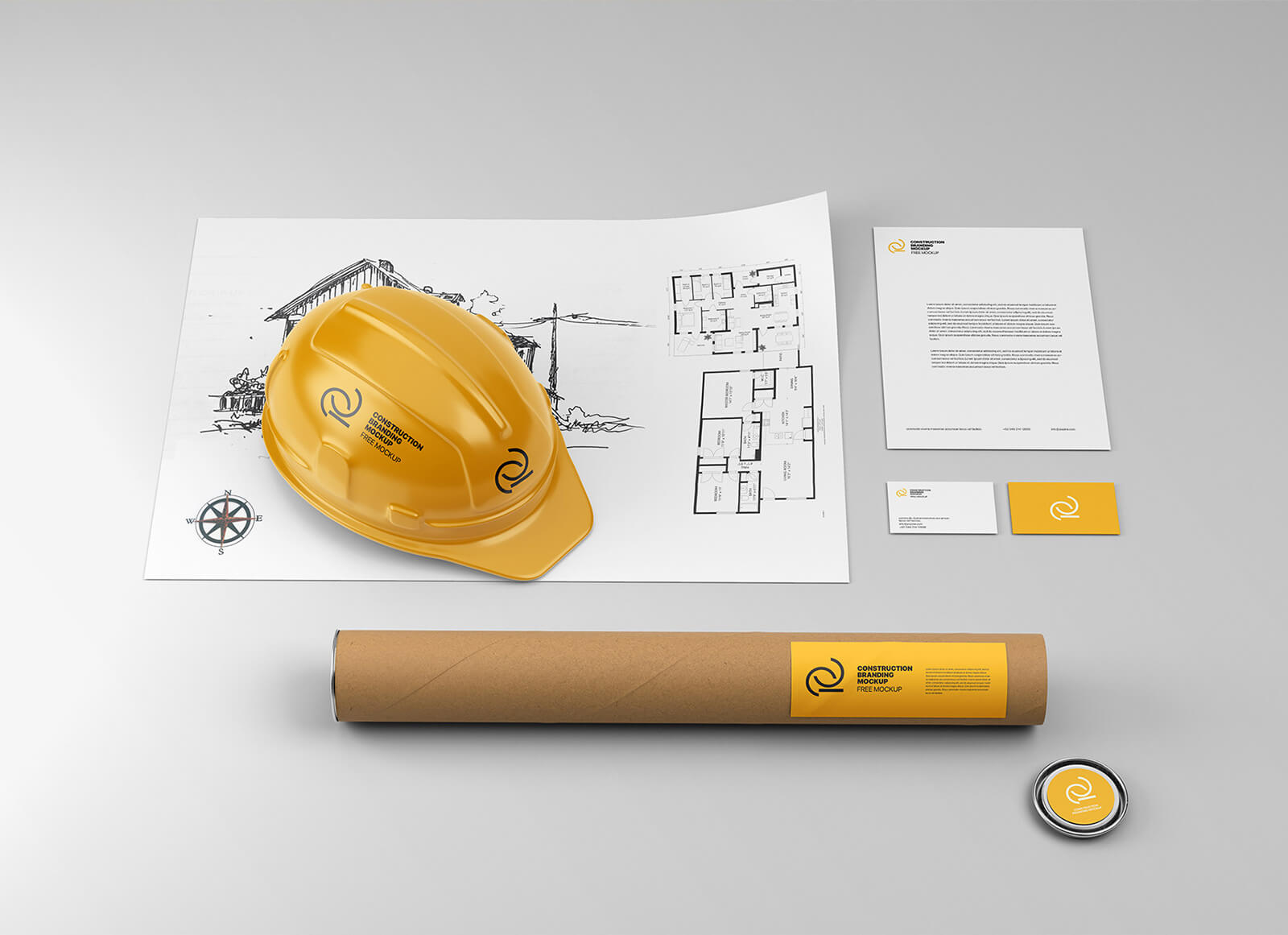
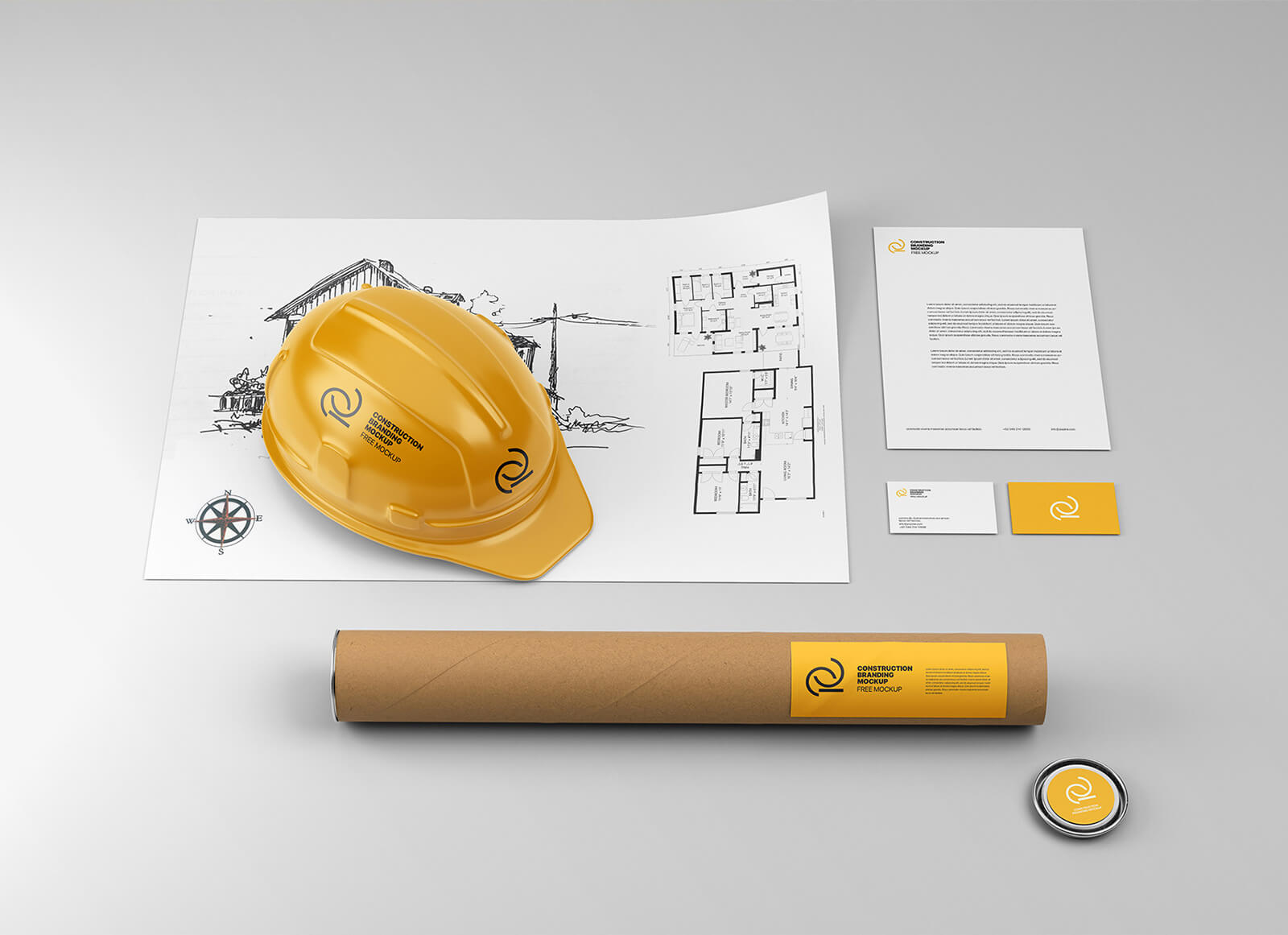
Building & Construction
What Is A Mock-Up In Construction
Modified: January 5, 2024
Learn what a mock-up is in the context of building construction and how it can be used to test design concepts and identify potential issues. Gain insights into the importance of mock-ups for successful construction projects.
(Many of the links in this article redirect to a specific reviewed product. Your purchase of these products through affiliate links helps to generate commission for Storables.com, at no extra cost. Learn more)
Introduction
Welcome to the world of construction, a complex and ever-evolving industry that brings visions to life. From towering skyscrapers to intricate residential developments, the construction process involves meticulous planning, precise execution, and attention to detail. One crucial aspect of any construction project is the creation of a mock-up.
A mock-up, in the context of construction, is a representation or prototype of a structure or component that is built prior to the actual construction process. It serves as a tangible model, giving stakeholders, architects, engineers, and contractors a visual and physical understanding of the final product.
In this article, we will delve into the definition, importance, types, benefits, considerations, case studies, challenges, and limitations of using mock-ups in construction. Let’s dive in!
Key Takeaways:
- Mock-ups in construction provide tangible representations, enhancing visualization, identifying design flaws, and involving clients for successful project outcomes.
- Despite challenges, mock-ups offer invaluable benefits, including improved communication, quality assurance, and risk reduction in construction projects.
Read more: What Is Tilt-Up Construction
Definition of a Mock-Up in Construction
In the realm of construction, a mock-up refers to a scaled or full-scale replica of a building or its components that is constructed prior to the actual construction process. It is a tangible representation of the final product, providing stakeholders, such as architects, engineers, contractors, and clients, with a clear understanding of how the structure will look and function.
A mock-up can take various forms, depending on the specific project and its requirements. It can be a section of a building, a single room, an entire façade, or even a mock-up of mechanical, electrical, or plumbing systems. The purpose of creating a mock-up is to validate and test design concepts, construction methods, materials, finishes, and functionality.
Mock-ups are typically constructed using the same materials and techniques that will be employed in the actual construction process. This enables stakeholders to assess the aesthetic appeal, durability, compatibility, and performance of the chosen materials and finishes. It also allows for any necessary adjustments or modifications to be made early in the design phase, reducing the risk of costly changes during the construction phase.
Mock-ups can be temporary or permanent structures, depending on the project requirements. Temporary mock-ups are often dismantled or demolished once they have served their purpose, while permanent mock-ups may be incorporated into the final construction as a showcase or reference.
Overall, the aim of a mock-up in construction is to minimize uncertainties, enhance the decision-making process, and mitigate potential risks and issues that may arise during construction. It enables stakeholders to experience the physical aspects of the project and make informed decisions, resulting in a higher quality and more successful final product.
Importance of Mock-Ups in Construction Projects
Mock-ups play a crucial role in construction projects, providing numerous benefits and addressing challenges that arise during the design and construction process. Here are some key reasons why mock-ups are important:
- Visual Representation and Clarity: Mock-ups offer a clear visual representation of the final product, allowing stakeholders to understand the design intent and spatial relationships. This helps in ensuring that everyone involved is on the same page, reducing potential misunderstandings and design errors.
- Testing Design Concepts and Functionality: Mock-ups allow designers and builders to test design concepts, materials, and finishes in a real-world context. This helps in identifying any potential design flaws or functional issues early on, saving time and money in the long run.
- Material and Finish Selection: Mock-ups enable stakeholders to assess the appearance, durability, and compatibility of different materials and finishes. It allows for side-by-side comparisons, ensuring that the selected materials and finishes meet the desired aesthetic and functional requirements.
- Client Visualization: Mock-ups provide clients with a tangible representation of the project, enabling them to visualize the final outcome and make informed decisions. This helps in achieving client satisfaction, as they have a clear understanding of what to expect.
- Safety and Risk Mitigation: By constructing a mock-up, potential safety hazards and risks can be identified and addressed before the actual construction begins. This ensures a safer work environment and minimizes the chance of accidents during the construction process.
- Coordination and Collaboration: Mock-ups facilitate effective communication and collaboration among project stakeholders. It allows architects, engineers, contractors, and clients to interact and provide feedback, leading to improved coordination and a better understanding of project requirements.
Overall, mock-ups enhance the decision-making process, reduce costly changes and rework, improve communication, and ultimately result in a higher quality and successful construction project. By investing in mock-ups, construction professionals can mitigate risks, save time and money, and deliver projects that meet or exceed client expectations.
Types of Mock-Ups in Construction
Mock-ups in construction can take various forms, depending on the specific project requirements and the elements being simulated. Here are some common types of mock-ups used in the construction industry:
- Full-Scale Mock-Ups: These mock-ups replicate the entire structure or a significant portion of it at full scale. They provide a comprehensive representation of the building’s size, shape, and spatial arrangement. Full-scale mock-ups are particularly useful for evaluating the overall aesthetics, functionality, and usability of the space.
- Façade Mock-Ups: Façade mock-ups focus specifically on the exterior appearance of the building. They replicate the façade elements, such as cladding, windows, and architectural details, to assess their visual appeal, durability, and performance. Façade mock-ups are commonly used for large-scale projects, such as commercial buildings or high-rise structures.
- Room Mock-Ups: Room mock-ups are smaller-scale representations of individual rooms or areas within a building. They allow stakeholders to evaluate the layout, finishes, lighting, and spatial functionality of a specific space. Room mock-ups are commonly used in projects where interior design plays a significant role, such as hotels, restaurants, or residential developments.
- Component Mock-Ups: Component mock-ups focus on specific building components, such as doors, windows, stairs, or structural elements. They provide an opportunity to test the performance, functionality, and compatibility of these components within the larger construction context. Component mock-ups are particularly useful in complex or unique building designs.
- System Mock-Ups: System mock-ups simulate the operation and integration of various mechanical, electrical, or plumbing systems within a building. These mock-ups allow for testing and fine-tuning of systems, such as HVAC, lighting, or fire suppression, ensuring their proper functionality and efficiency.
It’s important to note that the types of mock-ups used in a construction project can vary based on specific needs and project requirements. In some cases, multiple types of mock-ups may be utilized to achieve a comprehensive understanding of the design and construction aspects.
By employing different types of mock-ups, construction professionals can assess design feasibility, materials compatibility, system integration, and spatial functionality, ensuring a successful and well-executed construction project.
Benefits of Using Mock-Ups in Construction
The utilization of mock-ups in construction projects offers a wide range of benefits for all stakeholders involved. From architects and engineers to contractors and clients, here are some key advantages of using mock-ups:
- Enhanced Visualization: Mock-ups provide stakeholders with a tangible representation of the final product, allowing for a clearer visualization of the design intent and spatial relationships. This helps in avoiding misinterpretations or miscommunications, leading to a more accurate and successful end result.
- Early Identification of Design Flaws: By creating mock-ups, design flaws or functional issues can be identified and addressed early in the design phase. This reduces the risk of costly changes and rework during the construction process, saving time and resources.
- Improved Material and Finish Selection: Mock-ups enable stakeholders to test and evaluate different materials and finishes in a real-world context. This helps in ensuring that the chosen materials meet the desired aesthetic, durability, and performance requirements before committing to them on a larger scale.
- Client Involvement and Satisfaction: Mock-ups allow clients to physically experience and interact with the project before the actual construction begins. This involvement enhances client satisfaction as they have a better understanding of the final outcome and can provide valuable feedback for any necessary adjustments or modifications.
- Effective Problem Solving: Mock-ups serve as a platform for creative problem-solving. They provide an opportunity to explore various design alternatives, evaluate their implications, and make informed decisions. This helps in finding the most efficient and practical solutions for construction challenges.
- Streamlined Coordination and Collaboration: Mock-ups encourage effective communication and collaboration among project stakeholders. They facilitate discussions, feedback exchanges, and decision-making processes, resulting in improved coordination and a shared understanding of project requirements.
- Risk Reduction: By constructing mock-ups, potential safety hazards and risks can be identified and addressed prior to the actual construction phase. This proactive approach significantly reduces the likelihood of accidents, ensuring a safer work environment for construction personnel.
- Quality Assurance: Through the use of mock-ups, the quality of construction can be assured. Stakeholders can test and evaluate the mock-ups for compliance with design specifications, building codes, and industry standards. This helps in achieving a higher level of quality and reducing post-construction defects.
Overall, the utilization of mock-ups in construction projects leads to improved decision-making, enhanced communication, reduced risks, and higher-quality end results. By investing in mock-ups, construction professionals can save time and resources, optimize project outcomes, and ultimately deliver a successful construction project.
Read more: How Do Construction Cranes Go Up
Considerations for Creating Effective Mock-Ups
Creating effective mock-ups in construction requires careful planning, attention to detail, and consideration of various factors. Here are some key considerations to keep in mind to ensure the success of mock-up creation:
- Define the Objectives: Clearly define the objectives and purpose of the mock-up. Determine what aspects of the design or construction process you intend to evaluate and communicate through the mock-up.
- Select the Appropriate Scale: Determine the scale of the mock-up based on the objectives and level of detail required. Ensure that the scale accurately represents the intended dimensions of the final product.
- Choose the Right Location: Select a suitable location for constructing the mock-up. Consider factors such as accessibility, visibility, and the impact on other construction activities.
- Involve Relevant Stakeholders: Include the necessary stakeholders in the mock-up creation process. This includes architects, engineers, contractors, and clients, as their expertise and input are vital for making informed decisions.
- Use Realistic Materials and Finishes: Utilize the same or similar materials and finishes that will be used in the actual construction. This ensures that the mock-up accurately represents the final appearance and performance of the project.
- Consider Time and Cost Constraints: Keep in mind the time and cost limitations associated with creating the mock-up. Find a balance between the resources allocated and the level of detail required to achieve the objectives.
- Allow Sufficient Time for Constructing and Evaluating: Allocate enough time for the construction and evaluation of the mock-up. Rushing the process may result in incomplete or inaccurate assessments.
- Document and Communicate Findings: Document the findings and observations from the evaluation of the mock-up. Share this information with relevant parties to facilitate informed decision-making and necessary adjustments.
- Implement Feedback and Refine Designs: Incorporate feedback received from stakeholders and use it to refine and improve the design. This iterative process ensures that the final construction aligns with the desired goals.
- Consider Environmental Impact: Take into account the environmental impact of constructing the mock-up. Use sustainable materials and ensure the proper disposal or reuse of materials after the mock-up serves its purpose.
By considering these factors, construction professionals can create effective mock-ups that accurately represent the project, facilitate effective decision-making and communication, and ultimately contribute to the success of the construction project as a whole.
A mock-up in construction is a full-scale model of a building component used to test design concepts and demonstrate construction techniques. It helps to visualize the final product and identify any potential issues early in the process.
Case Studies: Successful Implementation of Mock-Ups in Construction Projects
Several construction projects have utilized mock-ups with great success, showcasing the importance and value they bring to the overall project outcomes. Here are two case studies highlighting the successful implementation of mock-ups:
Case Study 1: High-Rise Office Tower
In the construction of a high-rise office tower, the project team incorporated a full-scale mock-up of the building’s façade. The purpose was to assess the visual impact and performance of the chosen cladding system.
Through the mock-up, the project team was able to identify design issues related to the installation process, accessibility for maintenance, and thermal performance. By addressing these issues early on, they were able to refine the design and avoid costly modifications during the construction phase.
The mock-up also allowed the client and tenants to experience the proposed appearance of the building. Their feedback led to adjustments in the color and texture of the cladding, resulting in a final design that met their aesthetic preferences.
Case Study 2: Hospital Patient Room
In the construction of a new hospital, a mock-up of a patient room was built to assess the layout, functionality, and ergonomics of the space. The mock-up included full-scale replicas of the bed, furniture, medical equipment, and fixtures.
By using the patient room mock-up, the hospital staff and caregivers were able to identify potential issues with the arrangement of equipment, accessibility for patients with mobility challenges, and lack of storage space. These insights led to modifications in the final design, ensuring that the patient rooms were optimized for safety, efficiency, and comfort.
Furthermore, the mock-up allowed the hospital management to involve patients and their families in the design process. Feedback from patients regarding the room layout and amenities helped to create a more patient-centered environment, enhancing the overall experience and satisfaction.
These case studies highlight the benefits of utilizing mock-ups in construction. By providing a realistic representation of the final product, mock-ups enable early identification of design flaws, improve stakeholder engagement, and enhance decision-making. They contribute to the overall success of construction projects by mitigating risks, improving functionality, and achieving client satisfaction.
Read more: What Is Construction
Challenges and Limitations of Using Mock-Ups in Construction
While mock-ups are valuable tools in construction projects, they do come with certain challenges and limitations. It is important to be aware of these factors to effectively manage expectations and maximize the benefits of using mock-ups. Here are some key challenges and limitations:
- Cost and Time Constraints: Creating mock-ups can be a costly and time-consuming endeavor. The materials, labor, and resources required to construct an accurate representation of the final product can add significant expenses to the project. Additionally, the time needed for the creation and evaluation of mock-ups should be considered as it may impact project scheduling.
- Accuracy and Scope: Ensuring that the mock-up accurately represents the final product poses a challenge. Factors such as scale, materials, finishes, and system integration must be carefully considered to achieve a realistic depiction. It is also important to determine the appropriate scope of the mock-up, as it may not be feasible or necessary to replicate the entire project.
- Logistical Issues: Coordinating the logistics of constructing a mock-up, especially for large-scale or complex projects, can be a challenge. Finding a suitable location, securing necessary permits, and managing the transportation and installation of materials require careful planning and coordination.
- Limitations of Space: In some cases, space constraints may limit the size or scope of the mock-up. This can affect the ability to accurately represent the design, particularly for large buildings or complex architectural elements.
- Representation of Dynamic Elements: Mock-ups may not fully capture dynamic or interactive elements of the final product. For example, the functioning of mechanical, electrical, or plumbing systems may not be accurately replicated in a mock-up. This can affect the evaluation of these systems’ performance and functionality.
- Subjectivity of Evaluation: The evaluation of mock-ups is subjective and open to interpretation. Stakeholders may have differing opinions on design, aesthetics, and functionality. Balancing these perspectives and reaching consensus can be challenging and may require effective communication and negotiation.
- Environmental Considerations: Constructing mock-ups can contribute to waste generation and environmental impact. Care must be taken to ensure proper disposal or reuse of materials used in the mock-up creation and to choose sustainable alternatives wherever possible.
Despite these challenges and limitations, mock-ups remain valuable tools in construction projects. By understanding and addressing these factors, stakeholders can effectively utilize mock-ups to improve communication, identify design flaws, validate concepts, and ultimately deliver successful construction projects. It is important to weigh the benefits against the challenges and carefully consider the cost-effectiveness and suitability of incorporating mock-ups into each specific project.
Conclusion
Mock-ups have become an integral part of the construction industry, offering a multitude of benefits and opportunities for success. From visualizing design concepts to testing materials and finishes, mock-ups provide stakeholders with a tangible representation of the final product, enabling them to make informed decisions and mitigate risks.
Throughout this article, we explored the definition of mock-ups in construction, their importance, various types, benefits, considerations for creating effective mock-ups, and the challenges and limitations associated with their use. We also examined case studies that highlighted successful implementations of mock-ups in construction projects.
Mock-ups serve as powerful tools for enhancing visualization, early identification of design flaws, material and finish selection, and client involvement. They facilitate effective coordination, collaboration, and risk reduction, ultimately leading to improved project outcomes and client satisfaction.
However, it is essential to recognize the challenges and limitations of using mock-ups. Cost and time constraints, accuracy and scope, logistical issues, and the subjectivity of evaluation are factors that need to be carefully managed in order to maximize the benefits of mock-ups in construction projects.
In conclusion, the utilization of mock-ups in construction provides invaluable insights and opportunities for project success. By incorporating mock-ups into the design and construction process, stakeholders can enhance communication, refine design concepts, and ultimately deliver projects that meet or exceed client expectations. The investment in creating effective mock-ups, despite the challenges, is a worthwhile endeavor that leads to better decision-making, improved quality, and successful construction projects.
Frequently Asked Questions about What Is A Mock-Up In Construction
Was this page helpful?
At Storables.com, we guarantee accurate and reliable information. Our content, validated by Expert Board Contributors, is crafted following stringent Editorial Policies. We're committed to providing you with well-researched, expert-backed insights for all your informational needs.
0 thoughts on “What Is A Mock-Up In Construction”