Home>diy>Building & Construction>What Is A Modular Construction
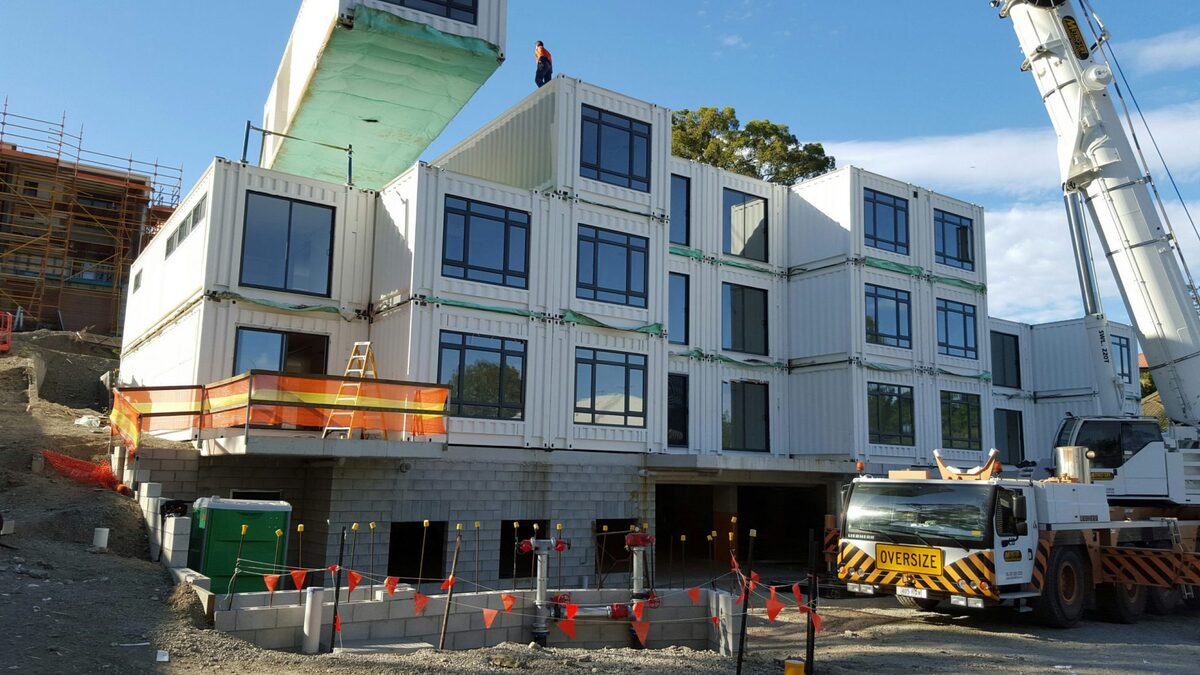
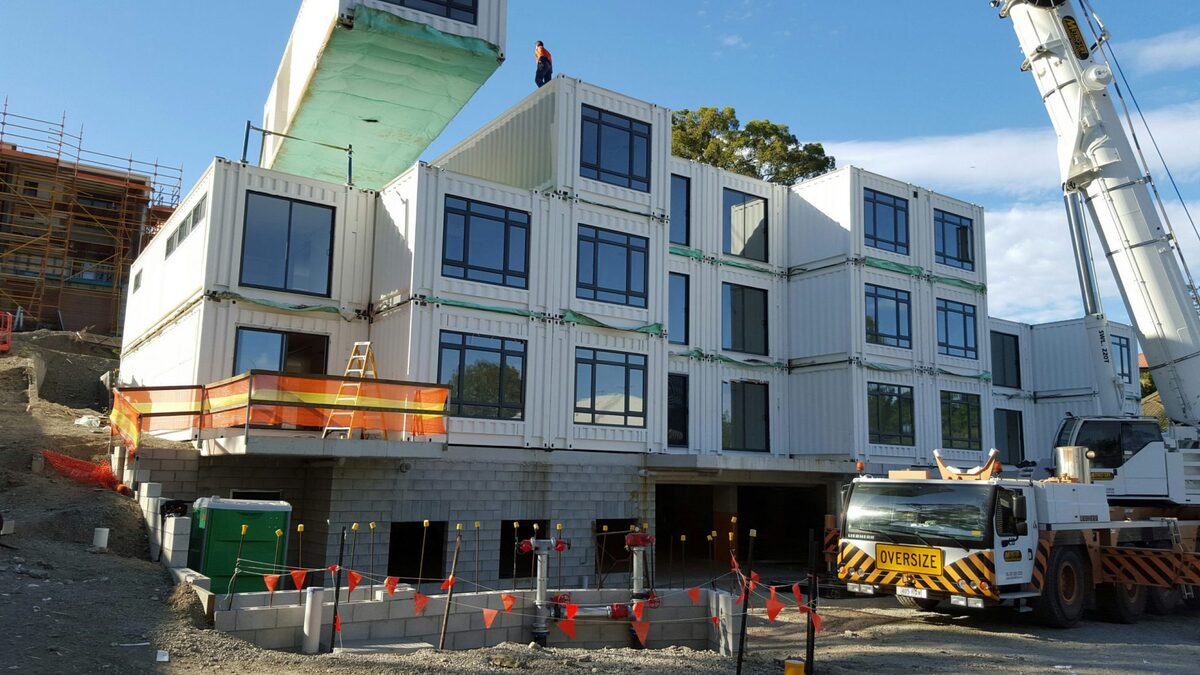
Building & Construction
What Is A Modular Construction
Modified: December 7, 2023
Discover the benefits of modular construction and how it revolutionizes the building construction industry. Enhance efficiency, speed, and cost-effectiveness with this innovative construction method.
(Many of the links in this article redirect to a specific reviewed product. Your purchase of these products through affiliate links helps to generate commission for Storables.com, at no extra cost. Learn more)
Introduction
Building construction is an intricate and essential industry that shapes the modern world. From towering skyscrapers to cozy homes, every structure has a unique blend of design, engineering, and construction techniques. One method that has gained significant attention in recent years is modular construction.
Modular construction, also known as off-site construction or prefabrication, is a process that involves assembling building components or modules in a controlled factory environment. These modules are then transported to the construction site and pieced together to create the final structure. This innovative approach to construction offers numerous benefits and is increasingly being adopted in various industries.
In this article, we will delve into the world of modular construction, exploring its definition, the advantages it offers, the process involved, and the industries that can benefit from it. Furthermore, we will discuss the considerations, challenges, and future trends associated with modular construction projects.
Key Takeaways:
- Modular construction revolutionizes building with faster, cost-effective, and sustainable methods. Its versatility spans residential, commercial, healthcare, and educational sectors, offering unique solutions to diverse needs.
- While modular construction presents challenges like design constraints and transportation logistics, future trends promise exciting advancements. Integration of BIM, automation, sustainability, and smart technologies will shape a more efficient and innovative construction landscape.
Read more: What Is Modular Construction Methods
Definition of Modular Construction
Modular construction is a method of building where the construction process is divided into off-site manufacturing and on-site assembly. The primary characteristic of modular construction is the production of building components, also known as modules, in a factory setting. These modules are then transported to the construction site, where they are assembled to form the final structure.
Each module is manufactured with high precision and quality control measures, ensuring consistency and efficiency in construction. These modules can be customized and designed to fit specific project requirements, making modular construction a versatile option for a wide range of building types, including residential, commercial, and industrial structures.
The modules used in modular construction can vary in size and complexity, from simple prefabricated walls to fully finished rooms or even entire building sections. The manufacturing process takes place in a controlled environment, allowing for improved quality control, reduced construction waste, and enhanced worker safety.
Modular construction is often associated with prefabricated construction, but there is a subtle difference between the two. Prefabricated construction involves the manufacturing of building components off-site, but these components are typically not designed to be assembled into modules. In contrast, modular construction involves the creation of self-contained modules that can be easily transported and assembled on-site.
Overall, modular construction offers a more efficient and streamlined approach to building construction. It enables faster project completion, as the manufacturing and site preparation can occur simultaneously. Additionally, the controlled environment of the factory allows for improved quality control, resulting in buildings that meet high standards of durability and energy efficiency.
Benefits of Modular Construction
Modular construction offers numerous benefits that make it an attractive option for both builders and clients alike. Let’s explore some of the key advantages of choosing modular construction for your next project:
- Speed and Efficiency: One of the greatest benefits of modular construction is its ability to significantly reduce construction time. Since the modules are manufactured off-site while site preparation occurs simultaneously, project timelines are shortened. This faster construction process allows for quicker occupancy and a faster return on investment.
- Cost Savings: Modular construction can also lead to cost savings compared to traditional construction methods. The controlled factory environment reduces material waste, and efficient manufacturing processes lead to economies of scale. Additionally, reduced construction time means fewer labor costs, site management expenses, and fewer disruptions to nearby businesses or residents.
- Quality Control: The factory-controlled environment of modular construction ensures high-quality building components. Since modules are constructed using standardized techniques and advanced technology, there is greater precision and consistency in their production. Quality control measures, including rigorous inspections and testing, result in buildings that meet or exceed industry standards.
- Sustainability: Modular construction is inherently more sustainable compared to traditional construction methods. The off-site manufacturing process reduces material waste, and any waste generated during construction is managed more efficiently. Additionally, modules can be designed with green building principles in mind, reducing energy consumption and incorporating eco-friendly materials and systems. Lastly, modular construction allows for easier deconstruction and reuse, promoting the circular economy.
- Flexibility and Customization: Modular construction offers a great deal of flexibility and customization options. The modules can be easily modified to meet specific design requirements and building codes. This adaptability allows for flexibility in layout, size, and configuration while maintaining the quality and integrity of the structure.
- Reduced Disruption: Since a significant portion of the construction process occurs off-site, modular construction minimizes disruptions to the surrounding environment and neighboring buildings. This is particularly beneficial in densely populated areas or projects located in sensitive locations where noise, dust, and disturbance must be kept to a minimum.
These benefits make modular construction a compelling choice for a wide range of projects, whether it’s a residential home, a commercial building, or an industrial facility. The speed, cost savings, quality control, sustainability, flexibility, and reduced disruption make modular construction a forward-thinking and efficient approach to building construction.
Process of Modular Construction
The process of modular construction involves several distinct steps, each contributing to the efficient and precise assembly of the building modules. Let’s take a closer look at the key stages involved in the process:
- Design and Engineering: The first step in modular construction is the design and engineering phase. The project’s architects, engineers, and modular construction specialists collaborate to create a detailed plan and design for the modular building. This includes considering factors such as structural integrity, energy efficiency, building codes, and client requirements.
- Module Fabrication: Once the designs are finalized, the manufacturing process begins. The building components or modules are constructed in a controlled factory environment, utilizing advanced machinery and skilled labor. The modules are built to precise specifications, ensuring consistency and quality.
- Transportation: After the modules are completed, they are transported to the construction site. This transportation can be done using various methods, including flatbed trucks or specialized carriers. Careful planning and logistics are essential to ensure the safe and efficient transportation of the modules.
- Site Preparation: While the modules are being fabricated in the factory and transported to the site, site preparation takes place concurrently. This involves clearing the land, preparing the foundation, and establishing the necessary utilities and infrastructure required for the building installation.
- Module Installation: Once the modules arrive at the construction site, they are carefully lifted and positioned into place using cranes or other lifting equipment. The modules are then securely joined together to create the final structure. This assembly process is typically completed with the help of experienced modular construction teams.
- Finishing and Integration: After the modules are installed, the finishing touches are applied. This includes connecting plumbing and electrical systems, installing interior finishes, and incorporating any additional features or fixtures. The goal is to seamlessly integrate the individual modules and create a cohesive and functional living or working space.
- Final Inspections and Handover: Once the construction is complete, a thorough inspection is conducted to ensure the building meets all necessary quality standards and regulatory requirements. Any necessary adjustments or corrections are made before the final handover to the client. The client is then provided with all relevant documentation and keys to the completed structure.
The modular construction process offers a streamlined approach to building construction, where efficiency, precision, and quality are prioritized. By dividing the process into distinct stages and utilizing advanced manufacturing techniques, modular construction allows for faster project completion, reduced costs, and increased sustainability.
Applications and Industries for Modular Construction
Modular construction has proven to be versatile and applicable in various industries and building types. Let’s explore some of the key applications and industries where modular construction is being successfully implemented:
- Residential Construction: Modular construction is widely utilized in residential projects, including single-family homes, multi-family buildings, and even affordable housing initiatives. The ability to customize designs, shorten construction timelines, and reduce costs has made modular construction an attractive option for homeowners and developers alike.
- Commercial Buildings: Modular construction is also well-suited for commercial buildings such as offices, retail spaces, and hospitality establishments. The efficient construction process allows for quicker occupancy, helping businesses start operations sooner and generate revenue faster.
- Educational Facilities: Schools, colleges, and universities can benefit from modular construction due to the need for flexible and adaptable spaces. Modular classrooms, laboratories, and administrative buildings can be constructed and installed quickly to accommodate student enrollment growth or address temporary space needs.
- Healthcare Facilities: Modular construction has gained traction in the healthcare sector. Modular hospitals, clinics, and medical facilities can be designed to meet specific healthcare standards and regulations while minimizing construction disruption and allowing for faster patient care delivery.
- Industrial and Manufacturing Buildings: Modular construction is ideal for industrial and manufacturing facilities that require large open spaces, optimized workflow, and specialized infrastructure. These buildings can be quickly assembled to meet the specific needs of different industries, including warehousing and logistics, production plants, and research and development centers.
- Hospitality and Leisure: Hotels, resorts, and recreational facilities can benefit from modular construction for their fast-track construction requirements. The modular approach allows for efficient installation of guest rooms, common areas, and amenities, enabling these businesses to start operating and generating revenue sooner.
- Emergency and Disaster Relief: In emergency situations or disaster relief efforts, modular construction can provide timely and efficient solutions. Modular structures can be rapidly deployed to provide temporary housing, medical facilities, and essential infrastructure to affected areas.
These are just a few examples of the many applications and industries that can benefit from modular construction. The versatility, speed, cost savings, and quality control offered by modular construction make it an attractive choice for a broad range of projects, irrespective of the sector or building type.
When considering modular construction, be sure to carefully review the specifications and materials used in the modules to ensure they meet your project’s requirements and local building codes.
Read more: What Is A Modular Brick
Considerations for Modular Construction Projects
While modular construction offers many advantages, there are several important considerations that need to be taken into account when undertaking a modular construction project. These considerations can help ensure a successful and efficient construction process. Let’s explore some key factors to consider:
- Design and Planning: Proper design and planning are crucial for a successful modular construction project. It’s essential to work closely with architects, engineers, and modular construction specialists to ensure that the design is optimized for modular construction methods. This includes considering transportation logistics, module sizes and shapes, and the integration of building services.
- Site Preparation: Adequate site preparation is necessary to accommodate the modular construction process. This includes preparing the foundation, leveling the ground, and ensuring that utilities are in place for the efficient installation of the modules. Additionally, access to the site and any necessary permits and approvals should be arranged ahead of time.
- Supplier Selection: Choosing the right modular construction supplier is crucial. It’s important to consider factors such as experience, reputation, and capability in delivering high-quality modular buildings. Thoroughly evaluating suppliers and reviewing their past projects can help ensure that the chosen supplier can meet the project’s specific requirements.
- Transportation and Logistics: Adequate transportation and logistics planning is essential for the successful delivery of the modular components. This includes choosing the right type of transport, considering clearance and weight restrictions, and timing the delivery to minimize disruptions. Working closely with transportation partners is crucial to ensure a smooth and efficient delivery process.
- Site Coordination: Effective on-site coordination is vital to ensure the seamless installation and assembly of the modular components. Clear communication between the construction team, suppliers, and contractors is necessary to coordinate the delivery of modules, site access, and the installation process. Proper project management and coordination can prevent delays and ensure the project stays on schedule.
- Building Codes and Regulations: Compliance with building codes and regulations is essential for any construction project, including modular construction. It’s crucial to work closely with local authorities to ensure that the modular building design and construction methods meet all necessary codes and regulations. This includes fire and safety standards, energy efficiency requirements, and structural integrity.
- Maintenance and Longevity: Consider the long-term maintenance and durability of the modular building. Ensure that the chosen materials and finishes are of high quality and will withstand the desired lifespan of the structure. Additionally, establish a maintenance plan to address any potential issues and ensure the longevity of the modular construction.
By considering these factors, stakeholders can navigate the modular construction process more effectively and ensure a successful outcome. Proper design and planning, site preparation, supplier selection, transportation logistics, site coordination, compliance with building codes, and considerations for long-term maintenance are all crucial components in the overall success of a modular construction project.
Challenges and Limitations of Modular Construction
While modular construction offers numerous benefits, there are also some challenges and limitations that need to be considered when undertaking a modular construction project. These challenges can affect the overall feasibility and success of the project. Let’s explore some of the key challenges and limitations of modular construction:
- Design Constraints: Modular construction requires careful consideration of design constraints. The modules must be accurately designed to fit transportation limits and ensure efficient assembly on-site. This can sometimes limit the architectural creativity and flexibility in design compared to traditional construction methods.
- Transportation and Site Access: Transportation and site access can be challenging, especially for large modular components. Some locations may have limited access or clearance constraints, making it more difficult to transport and deliver the modules. Additionally, remote or congested sites may require advanced planning to ensure timely and efficient delivery.
- Coordination and Communication: Successful modular construction relies heavily on effective coordination and communication between all involved parties. This includes architects, contractors, suppliers, and on-site teams. Poor coordination and miscommunication can lead to delays, errors in assembly, and cost overruns.
- Weather Restrictions: Weather conditions can impact the progress of modular construction projects. Extreme weather events, such as high winds, heavy rain, or snow, may disrupt transportation, delay deliveries, and hinder on-site assembly. Taking into account weather conditions and having contingency plans in place is essential to mitigate potential delays.
- Limited Flexibility for Changes: Once modules are manufactured and delivered to the site, making changes to the design or layout can be challenging and costly. Modifications may require additional fabrication and transportation, potentially causing disruptions and delays in the construction process.
- Initial Investment: Modular construction may require a significant upfront investment in manufacturing facilities, equipment, and skilled labor. This initial investment may deter some builders or developers from choosing modular construction methods, particularly for small-scale projects.
- Site Limitations: Modular construction may not be suitable for every site due to size, zoning restrictions, or site conditions. Sites with limited space or challenging terrain may pose obstacles for the delivery and installation of modular components.
- Perception and Stigma: Despite its benefits, modular construction may still face certain stigmas or assumptions about its quality, durability, or aesthetics. Overcoming these perceptions and educating stakeholders about the advantages and advancements in modular construction is crucial for wider adoption and acceptance.
While these challenges and limitations exist, advances in technology and increased experience in modular construction are helping to overcome these hurdles. By addressing these challenges proactively and working closely with experienced modular construction specialists, it is possible to successfully navigate the obstacles and realize the benefits that modular construction offers.
Future Trends in Modular Construction
Modular construction is evolving rapidly, driven by advancements in technology and changing construction practices. The future holds several exciting trends that will shape the industry in the coming years. Let’s explore some of the key future trends in modular construction:
- Integration of Building Information Modeling (BIM): Building Information Modeling (BIM) is transforming the construction industry, and modular construction is no exception. BIM allows for better collaboration, visualization, and coordination of building components throughout the entire construction process. The integration of BIM in modular construction will streamline workflows, enhance communication, and improve project outcomes.
- Increased Automation and Robotics: Automation and robotics are revolutionizing construction processes, and modular construction is embracing these technologies. Robotic systems can enhance precision in module manufacturing and modular assembly, increasing efficiency and reducing human error. Automated systems can also improve safety measures and optimize construction timelines.
- Off-Site Digital Manufacturing: The convergence of digital manufacturing technologies and modular construction will revolutionize the industry. Using advanced computer-aided design (CAD) and computer numerical control (CNC) techniques, modules can be customized and manufactured with even greater precision and efficiency. This will result in improved quality control and reduced lead times.
- Modular High-Rise Buildings: While traditionally associated with low-rise construction, modular construction is now being explored for high-rise buildings. Advancements in engineering, transportation, and on-site assembly techniques are making modular high-rise buildings a viable solution. This trend will revolutionize urban construction, providing faster delivery and sustainable solutions for densely populated areas.
- Green and Sustainable Modular Construction: The construction industry is increasingly focusing on sustainable practices, and modular construction is no exception. Modular buildings can be designed to integrate renewable energy systems, sustainable materials, and energy-efficient technologies. This trend will further enhance the environmental benefits of modular construction, reducing the carbon footprint of buildings.
- Modular Additions and Retrofitting: Retrofitting and adding modular components to existing structures will become more prevalent in the future. Modularity allows for seamless integration with existing buildings, providing an efficient and cost-effective solution for expanding or upgrading spaces. This trend will aid in revitalizing older structures and adapting to evolving needs and technologies.
- Modular Smart Buildings: The integration of smart technologies into modular construction will revolutionize the way buildings function. From IoT-enabled systems to energy management and automation, modular smart buildings will enhance user comfort, optimize energy consumption, and improve overall building performance.
These future trends in modular construction indicate an exciting and innovative future for the industry. The adoption of advanced technologies, increased sustainability practices, the expansion into new building types, and the integration of smart systems will further solidify modular construction as a leading and preferred method of construction.
Conclusion
Modular construction is revolutionizing the building industry, offering a faster, more efficient, and more sustainable approach to construction. The process of modular construction, with its off-site manufacturing and on-site assembly, provides numerous benefits, including cost savings, reduced construction time, improved quality control, and increased flexibility.
Modular construction finds applications in various industries, from residential and commercial buildings to healthcare facilities and educational institutions. Its versatility and adaptability make it an attractive choice for a wide range of projects, offering unique solutions to specific needs and requirements.
While the modular construction process offers several advantages, it is essential to consider the challenges and limitations associated with it. Factors such as design constraints, transportation logistics, coordination, and site limitations require careful planning and effective communication between all stakeholders to ensure a successful project outcome.
Looking ahead, the future trends in modular construction are promising. Integration of BIM, increased automation, off-site digital manufacturing, modular high-rise buildings, sustainable practices, retrofitting, and smart building technologies will shape the industry and further enhance the efficiency, quality, and sustainability of the modular construction process.
In conclusion, modular construction is a dynamic and innovative construction method that offers numerous advantages for builders and clients alike. It is revolutionizing the industry by providing faster construction times, cost savings, improved quality, and increased sustainability. As technology continues to advance and the industry embraces new trends, modular construction will continue to evolve and pave the way for a more efficient and sustainable future of building construction.
Frequently Asked Questions about What Is A Modular Construction
Was this page helpful?
At Storables.com, we guarantee accurate and reliable information. Our content, validated by Expert Board Contributors, is crafted following stringent Editorial Policies. We're committed to providing you with well-researched, expert-backed insights for all your informational needs.
0 thoughts on “What Is A Modular Construction”