Home>diy>Building & Construction>What Is Modular Construction Methods
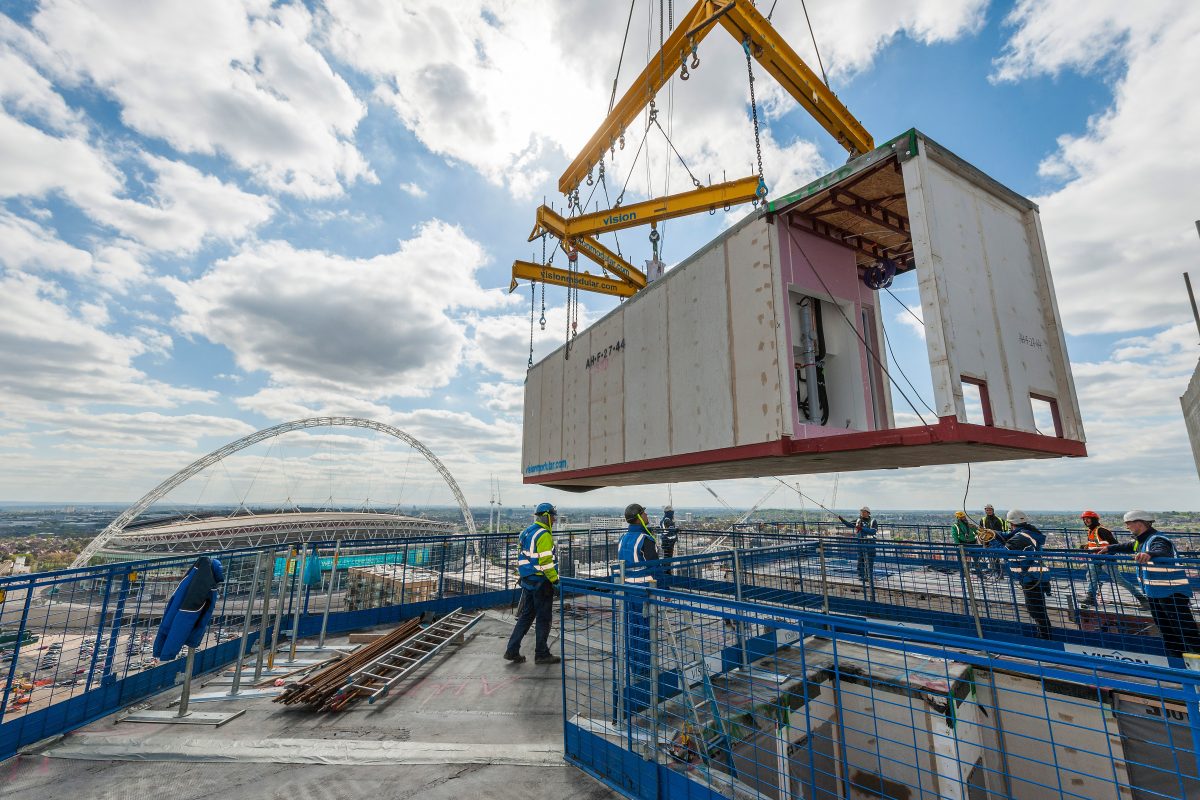
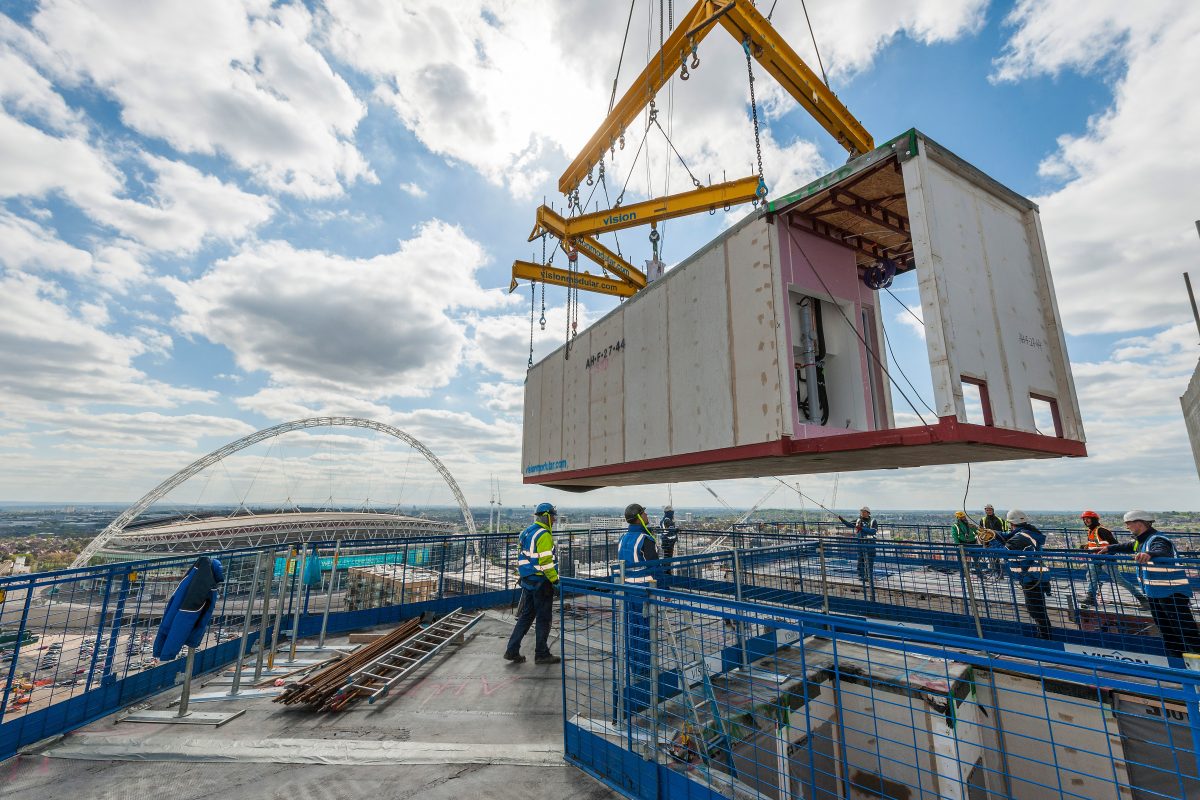
Building & Construction
What Is Modular Construction Methods
Modified: January 24, 2024
Discover the benefits and process of modular construction methods in the building construction industry. Explore how this innovative approach saves time and resources, while maintaining high quality and sustainability.
(Many of the links in this article redirect to a specific reviewed product. Your purchase of these products through affiliate links helps to generate commission for Storables.com, at no extra cost. Learn more)
Introduction
Modular construction has emerged as an innovative and efficient method in the building construction industry. It offers numerous benefits over traditional construction methods, making it a popular choice for both residential and commercial projects.
So, what exactly is modular construction? In simple terms, it involves the fabrication of building components or modules off-site in a controlled factory environment, which are then transported to the construction site and assembled together to create the final structure. This method deviates from the conventional practice of constructing a building entirely on-site.
The popularity of modular construction is primarily driven by the many advantages it offers. This article will delve into the various benefits of modular construction, its different methods, the off-site and on-site construction processes, factors to consider, challenges and limitations, comparison with traditional methods, case studies of successful projects, and future trends and innovations.
One of the key advantages of modular construction is the reduced construction time. Since the modules are fabricated simultaneously off-site, site preparation and modular production can occur concurrently, significantly speeding up the overall construction process. Moreover, the controlled factory environment eliminates weather-related delays, boosting project efficiency.
Another benefit of modular construction is cost savings. Factory production allows for tighter quality control, reducing the risk of rework and minimizing material waste. The standardized manufacturing process also enables economies of scale, resulting in cost efficiencies. Additionally, reduced labor requirements and faster completion translate into lower labor costs.
In terms of sustainability, modular construction is a greener option. The off-site production process enables better utilization of materials, as well as more efficient energy and resource management. Moreover, the factory setting allows for the incorporation of sustainable practices and technologies that may not be feasible on a traditional construction site.
Flexibility is another advantage offered by modular construction. The modular components can be easily disassembled and relocated, facilitating future expansion or reconfiguration. This flexibility makes modular construction a popular choice for temporary structures, such as schools or healthcare facilities, as well as for projects in remote or challenging locations.
Additionally, modular construction can contribute to improved quality. The controlled factory environment ensures that the modules are built with precision and adhere to rigorous quality standards. The standardized manufacturing process also reduces the risk of human error and ensures consistent quality across all modules.
As modular construction gains momentum, it is crucial to understand the different methods used in this approach. The next section will explore the various types of modular construction methods in more detail.
Key Takeaways:
- Modular construction offers faster project completion, cost savings, and sustainability benefits compared to traditional construction methods. It revolutionizes the industry with efficient off-site fabrication and assembly processes, shaping the future of building construction.
- The future of modular construction is promising, with trends such as digitalization, robotics, advanced materials, and hybrid construction paving the way for enhanced efficiency, sustainability, and design flexibility. Modular construction is redefining the construction landscape with innovative advancements.
Read more: What Is A Modular Construction
Definition of Modular Construction
Modular construction, also known as prefabrication, is a construction method that involves the creation of building components or modules off-site in a controlled factory environment. These modules are then transported to the construction site, where they are assembled to create a complete structure. This differs from traditional construction methods, where buildings are constructed entirely on-site.
The modules used in modular construction are typically pre-designed and manufactured according to standardized specifications. They can range from individual rooms or sections of a building to entire floors or even complete standalone structures. Each module is built with precision and attention to detail, ensuring consistent quality across all components.
Modular construction can be categorized into two main types: volumetric construction and panelized construction.
Volumetric Construction:
In volumetric construction, entire rooms or sections of a building are manufactured as fully enclosed modules. These modules, also known as “volumetric units” or “modules,” are complete and self-supporting structures that are equipped with all necessary fixtures, fittings, and finishes. They can include interior partitions, plumbing, electrical systems, HVAC units, and even furniture.
Volumetric modules are typically constructed with steel or timber frames, and their dimensions are often limited by transportation considerations, such as the maximum width and height of road transportation. Once manufactured, they are transported to the construction site and lifted into place using cranes, forming the entire structure. The interconnection of the modules is completed on-site, including the installation of utilities and the sealing of joints to ensure structural integrity.
Panelized Construction:
Panelized construction involves the creation of building components in the form of panels. These panels are usually made of wood, steel, or concrete, and they are manufactured off-site to precise measurements and specifications. The panels can include exterior walls, interior partitions, floor systems, and roof components.
Once the panels are produced, they are transported to the construction site and assembled together to form the overall structure. The interconnection of the panels is achieved through various methods, such as bolting, welding, or using adhesives. Additional steps, such as the installation of insulation, electrical wiring, and plumbing, are completed on-site.
Both volumetric and panelized construction methods have their advantages and are suited to different project requirements. Volumetric construction offers a higher degree of completeness and requires less on-site assembly, making it ideal for projects with tight schedules or those in remote locations. Panelized construction, on the other hand, allows for flexibility in customization and can be more cost-effective for certain building types.
In the next section, we will explore the numerous benefits of modular construction in more detail.
Benefits of Modular Construction
Modular construction offers a multitude of advantages over traditional construction methods, making it a preferred choice for many developers, architects, and contractors. The following are some key benefits of modular construction:
Read more: What Is A Modular Brick
1. Reduced Construction Time:
Modular construction can significantly reduce the overall construction time compared to traditional methods. With off-site fabrication and on-site preparation happening simultaneously, projects can be completed in a fraction of the time. The controlled factory environment eliminates weather-related delays, ensuring consistent progress regardless of external conditions. This not only saves time but also allows for faster occupancy or quicker return on investment.
2. Cost Savings:
Modular construction can lead to cost savings throughout the project lifecycle. Factory production allows for tighter quality control, minimizing rework and material wastage. The standardized manufacturing process enables economies of scale, resulting in cost efficiencies. Additionally, the reduced labor requirements and faster completion time translate into lower labor costs. Overall, modular construction offers a more cost-effective alternative to traditional construction methods.
3. Sustainability and Environmental Benefits:
Modular construction is inherently more sustainable compared to traditional construction. The off-site production process allows for better utilization of materials, reducing waste. Moreover, the controlled factory setting enables efficient energy and resource management, promoting sustainability. The modular units can also be designed to incorporate green building practices, such as energy-efficient systems and materials, further reducing environmental impact.
4. Enhanced Quality:
Modular construction ensures a high level of quality and precision. The modules are built in a controlled factory environment, adhering to rigorous quality standards. The standardized manufacturing process reduces the risk of human error and ensures consistent quality across all modules. Additionally, the use of advanced technology and automation in the production process further enhances the quality and accuracy of the components.
Read more: What Is The Cost Of Building A Modular Home
5. Flexibility and Versatility:
Modular construction offers flexibility and versatility in design and functionality. The building modules can be easily disassembled and relocated, allowing for future expansion or reconfiguration. This flexibility makes modular construction an ideal choice for projects where adaptability is required, such as temporary structures, educational facilities, or healthcare centers. Modular construction can also be used in various building types, from residential houses to commercial buildings.
6. Improved Safety:
The controlled factory environment of modular construction promotes better safety conditions for workers. Standardized processes and protocols are followed, reducing the risk of accidents and injuries. Additionally, the reduced on-site construction activities minimize potential hazards and hazards related to construction activities. This focus on safety ensures a safer working environment for construction personnel and contributes to a positive project experience.
These benefits make modular construction an attractive option for developers and contractors looking to optimize construction efficiency, cost-effectiveness, sustainability, and overall project outcomes.
In the subsequent sections, we will explore the different types of modular construction methods and the processes involved in off-site and on-site modular construction.
Types of Modular Construction Methods
Modular construction encompasses various methods that can be utilized depending on the specific project requirements. The two main types of modular construction methods are volumetric construction and panelized construction.
Volumetric Construction:
Volumetric construction, also known as unitized or modular volumetric construction, involves the creation of complete and self-supporting modules that are manufactured off-site. These modules are fully enclosed structures that can include walls, floors, ceilings, and even built-in fixtures and finishes.
In volumetric construction, the modules are fabricated to precise specifications in controlled factory conditions. This includes the installation of electrical systems, plumbing, HVAC units, and other necessary components. Once completed, the modules are transported to the construction site and assembled to form the final structure. The interconnection of the modules is completed on-site, including the integration of utilities and the sealing of joints to ensure structural integrity.
Volumetric construction offers a high degree of completeness and minimizes on-site construction activities. It is often used for projects where speed and efficiency are paramount, such as hotels, student accommodation, and healthcare facilities. The factory-built modules are designed for easy transportation and installation, making this method ideal for projects with limited accessibility or challenging site conditions.
Panelized Construction:
Panelized construction involves the creation of building components in the form of panels, which are manufactured off-site and transported to the construction site for assembly. These panels can include exterior walls, interior partitions, floor systems, and roof components.
Panelized construction begins with the fabrication of panels in a controlled factory environment. These panels are typically made of materials such as wood, steel, or concrete, depending on the project requirements. They are manufactured with precision, including cutouts for doors, windows, and other openings. The panels are then transported to the construction site and assembled together, forming the structure.
The interconnection of the panels is achieved through various methods, such as bolting, welding, or using adhesives. Additional on-site construction activities, such as the installation of insulation, electrical wiring, and plumbing, are completed once the panels are in place. Panelized construction offers flexibility in design and customization, as each panel can be tailored to specific requirements.
This method is commonly used for residential buildings, commercial structures, and low-rise buildings. It allows for efficient material usage, reduces on-site waste, and offers cost savings compared to traditional construction methods. Panelized construction also offers design versatility, enabling architects and designers to create unique structures while maintaining efficiency and construction speed.
These two modular construction methods provide flexibility and efficiency in the construction process, allowing for faster completion times, cost savings, and sustainable building practices. In the following sections, we will explore the off-site and on-site processes involved in modular construction.
Off-Site Modular Construction Process
Off-site modular construction involves the fabrication and assembly of building components or modules in a controlled factory environment, away from the actual construction site. This process offers numerous advantages, such as increased efficiency, improved quality control, and reduced construction time.
The off-site modular construction process can be broken down into several key stages:
1. Design and Engineering:
The off-site modular construction process begins with the design and engineering phase. Architects and engineers work together to develop a comprehensive design that meets the project requirements. The design takes into account factors such as structural integrity, functionality, and aesthetics.
Advanced computer-aided design (CAD) technology is commonly employed during this stage to create precise 3D models of the modules. These models help visualize the final product and ensure that all elements are accurately incorporated.
2. Production of Modules:
Once the design is finalized, the fabrication of the modules takes place in the factory. The modules are constructed according to the specifications determined in the design phase. Skilled craftsmen and technicians work to fabricate the walls, floors, ceilings, and other components of the modules with meticulous precision.
The manufacturing process may include activities such as cutting and shaping materials, installation of plumbing and electrical systems, and application of finishes. Quality control measures are implemented throughout the production process to ensure the modules meet the required standards and specifications.
3. Transportation to the Construction Site:
After the modules are completed, they are transported to the construction site. Depending on their size and weight, they may be transported by trucks, flatbed trailers, or even by rail or sea for larger projects. Specialized equipment and logistics are utilized to safely transport the modules to the construction site, taking into consideration road regulations and site-specific requirements.
4. Assembly and Installation:
Once the modules arrive at the construction site, they are lifted and maneuvered into position using cranes or other lifting equipment. The modules are then precisely aligned and connected to form the final structure. This involves integrating the modules with the building’s foundation and connecting utilities such as plumbing, electrical, and HVAC systems.
On-site construction activities, such as the completion of interior finishes and the installation of exterior cladding, take place after the modules are in position. The goal is to seamlessly blend the modular components with any on-site construction elements to create a cohesive and visually appealing structure.
5. Finalization and Handover:
Once the modules are assembled and the necessary on-site construction is completed, the finalization stage begins. This includes conducting thorough inspections and quality checks to ensure that all aspects of the construction meet the required standards and specifications.
Any necessary adjustments or modifications are made, and final finishes are applied to the modules as needed. Once the project is deemed complete, it is handed over to the client or end-user for occupancy or immediate use.
The off-site modular construction process offers significant advantages in terms of speed, quality control, and efficiency. By fabricating the modules in a controlled factory environment, construction time is minimized, and the risk of weather-related delays is eliminated. The next section will delve into the on-site modular construction process and the factors to consider during modular construction projects.
On-Site Modular Construction Process
The on-site modular construction process involves the final stages of assembling the modular components on the construction site to create a fully functional structure. This process requires coordination, skilled labor, and careful integration of the modules with on-site construction elements to ensure a seamless and cohesive final product.
The on-site modular construction process can be broken down into several key stages:
1. Site Preparation:
The first step in the on-site modular construction process is preparing the construction site. This includes clearing the site of any existing structures, debris, or obstacles that may hinder the assembly of the modular components. It also involves leveling the ground, installing temporary utilities, and ensuring the site is ready to receive the modules.
2. Foundation Work:
Once the site is prepared, the foundation work begins. The foundation acts as the base on which the modular components will be installed. Depending on the project and site requirements, this may involve laying a concrete slab, constructing footings, or installing piers or piles to support the structure.
3. Module Delivery and Placement:
Once the foundation is in place, the modules are delivered to the construction site. The transportation and lifting of the modules require specialized equipment, such as cranes or hydraulic lifts. Each module is carefully maneuvered into position and aligned according to the predetermined design and layout.
During the placement process, it is crucial to ensure that the modules are properly supported and leveled on the foundation. This may involve the use of leveling devices or shims to achieve precise alignment and structural integrity.
4. Integration and Connection:
After the modules are placed, the integration and connection phase begins. This involves joining the modules together to create a cohesive structure. Connections between the modules are made using various methods, such as bolts, welding, or adhesives, depending on the specific project requirements and the materials used in the construction.
Utilities, such as electrical wiring, plumbing lines, and HVAC systems, are also integrated and connected between the modules. This includes ensuring proper alignment and installation of these systems to ensure functionality and efficiency.
Read also: 15 Best Modular Storage For 2024
5. On-Site Construction and Finishing:
Once the modules are securely connected and integrated, on-site construction and finishing works can commence. This includes completing interior finishes such as flooring, wall cladding, painting, and installation of fixtures and fittings. Exterior finishes, such as cladding, roofing, and landscaping, are also carried out to achieve the desired aesthetics and functionality.
6. Final Inspection and Completion:
As the construction nears completion, a final inspection is conducted to ensure that all aspects of the modular construction meet the required standards and specifications. This includes assessing the structural integrity, functionality of utilities, compliance with building codes, and overall quality of the construction.
Once the project passes the final inspection, it is considered complete, and the structure is ready for occupancy or immediate use.
The on-site modular construction process requires skilled labor, effective coordination, and adherence to safety protocols. It ensures the seamless integration of the modular components with on-site construction elements, resulting in a fully functional and visually appealing structure.
In the next section, we will explore the factors to consider during modular construction projects and the challenges and limitations associated with this construction method.
Factors to Consider for Modular Construction
When considering modular construction for a project, there are several key factors that need to be carefully evaluated to ensure a successful and seamless implementation. These factors encompass various aspects of the project, including design considerations, site conditions, logistics, and project management. Understanding and addressing these factors is essential in maximizing the benefits and overcoming any challenges associated with modular construction.
1. Design and Planning:
Effective design and planning are critical in modular construction. The design should take into account the modular nature of the construction method, allowing for easy transportation, assembly, and integration of the modules. It is important to work closely with architects, engineers, and module manufacturers to ensure that the design is compatible with modular construction techniques, maximizing efficiency and functionality.
Read more: What Is Construction
2. Site Conditions and Logistics:
The site conditions play a crucial role in the success of modular construction. Factors such as site access, utilities availability, soil conditions, and space constraints need to be carefully evaluated and addressed early in the planning stage. Additionally, logistics, including transportation of the modules and access for heavy lifting equipment, must be considered to ensure a smooth and efficient construction process.
3. Module Manufacturing:
Choosing the right module manufacturer is vital for a successful modular construction project. It is important to consider their experience, expertise, and track record in delivering high-quality modules. Evaluating their production capacity, quality control processes, and ability to meet project timelines is essential in selecting a reliable and capable manufacturer.
4. Collaboration and Communication:
Collaboration and open communication between all project stakeholders are key factors in modular construction. Building strong relationships and fostering effective communication channels facilitate the proper coordination of design, logistics, and construction processes. Regular meetings and collaboration efforts ensure that everyone involved in the project is aligned with the project goals and milestones.
5. Building Codes and Regulations:
Compliance with building codes and regulations is of utmost importance in modular construction projects. It is essential to ensure that the design and construction of the modules meet all relevant building codes and regulations in the intended location. Engaging with local authorities and obtaining the necessary permits and approvals early in the process is essential to avoid any delays or complications during the construction phase.
Read also: 8 Amazing Modular Wine Rack For 2024
6. Quality Control and Inspection:
Ensuring high-quality construction is crucial in modular projects. Implementing a robust quality control process throughout the manufacturing and assembly stages helps maintain the desired level of quality. It is important to conduct regular inspections to verify that the modules meet the required standards and specifications. This helps identify and address any issues or defects before final installation and completion.
7. Project Management and Scheduling:
Effective project management and scheduling are essential for a successful modular construction project. Developing a detailed project plan, assigning responsibilities, and establishing clear milestones and timelines allows for efficient coordination between off-site module manufacturing and on-site assembly. Regular monitoring and adjustments to the schedule help ensure a smooth workflow and timely completion of the project.
By carefully considering these factors, developers, architects, and contractors can optimize the benefits of modular construction and mitigate potential challenges. In the next section, we will explore the challenges and limitations associated with modular construction.
Challenges and Limitations of Modular Construction
While modular construction offers numerous benefits, it also comes with its own set of challenges and limitations that need to be considered when utilizing this construction method. Understanding and addressing these challenges is crucial for ensuring a successful modular construction project.
1. Design Limitations:
The modular construction process requires considering certain design limitations. Since modules are fabricated off-site and transported, their dimensions are limited by transportation restrictions, such as maximum widths and heights. This can impact the overall design and layout of the building. Additionally, incorporating complex architectural features or customized designs may pose challenges in modular construction.
2. Transportation and Site Access:
The transportation and delivery of modules to the construction site can present logistical challenges. Site access, road conditions, and potential obstacles can impact the efficiency and cost-effectiveness of transportation. In some cases, specialized transportation equipment may be required to safely and efficiently deliver the modules. Addressing these concerns early in the planning stage is crucial to avoid delays and additional costs.
3. Site Preparation and Foundations:
Site preparation for modular construction requires careful consideration. Preparing the site to accommodate the modules, including leveling the ground and ensuring proper utilities access, can be challenging, particularly for sites with uneven terrain or restricted space. Additionally, the type of foundation required may vary depending on the project’s location and specific requirements, adding complexity to the site preparation process.
4. Design and Production Coordination:
Collaboration and coordination between architects, engineers, and module manufacturers is essential in modular construction. Ensuring a seamless integration of design and production requires clear communication and collaboration throughout the project. Coordinating design changes and addressing any design-related issues during the manufacturing process can be more challenging compared to traditional construction methods.
5. Limited On-Site Customization:
Modular construction’s prefabricated nature limits on-site customization compared to traditional construction. While customization to a certain extent is possible during module fabrication, significant changes to the design or modifications once the modules are on-site may be more challenging and costly. Therefore, careful consideration and detailed planning during the design phase are crucial to accommodate project-specific customization.
Read more: What Is A Construction Painter
6. Financing and Insurance:
Securing financing and insurance for modular construction projects might present challenges. Traditional lenders and insurance providers may have limited experience with modular construction and may require additional documentation or information to assess the project’s viability and risk. It is important to engage with lenders and insurance providers who are familiar with modular construction and can provide the necessary support and guidance.
7. Perceptions and Misconceptions:
Despite the growing popularity of modular construction, there may still be misconceptions and skepticism surrounding its quality and durability compared to traditional construction methods. Addressing these perceptions and educating stakeholders about the benefits and advancements in modular construction is essential to build trust and confidence in the approach.
By acknowledging and proactively addressing these challenges and limitations, project teams can maximize the success of modular construction projects. With careful planning, effective collaboration, and proper management, modular construction can deliver efficient, high-quality, and sustainable buildings.
In the next section, we will compare modular construction with traditional construction methods to further understand its advantages and potential applications.
Comparison with Traditional Construction Methods
Modular construction offers several advantages compared to traditional construction methods, revolutionizing the building industry. Understanding the differences between these two approaches can help stakeholders make informed decisions when selecting the most suitable construction method for their projects. Here is a comparison of modular construction with traditional construction methods:
1. Construction Time:
Modular construction significantly reduces construction time compared to traditional methods. The off-site fabrication of modules allows for concurrent activities, such as site preparation and module production. This parallel workflow accelerates the overall construction process, resulting in faster project completion and earlier occupancy. In contrast, traditional construction methods are typically sequential, requiring each phase to be completed before moving on to the next, leading to longer construction durations.
Read more: What Is A Scribe In Construction
2. Cost Efficiency:
Modular construction can offer cost savings over traditional methods. The controlled factory environment ensures efficient material usage, minimizes waste, and enables economies of scale through standardized manufacturing processes. Additionally, the reduced construction time in modular construction leads to lower labor costs. On the other hand, traditional construction methods often involve on-site labor-intensive activities and may incur additional costs due to weather-related delays, rework, and material waste.
3. Quality Control:
Modular construction ensures consistent quality control throughout the manufacturing process, as modules are built in a factory setting under strict guidelines. The controlled environment allows for precision in construction and adherence to standardized manufacturing processes, reducing the risk of human error. Traditional construction methods, on the other hand, may be subject to variations in workmanship, weather-related constraints, and the potential for inconsistencies due to different teams working on-site.
4. Flexibility and Customization:
Modular construction provides flexibility and customization options for building design. The modules can be easily reconfigured, expanded, or relocated to accommodate changing needs. This makes modular construction suitable for projects that require adaptability and flexibility, such as temporary structures or those with potential future expansions. Traditional construction methods, on the other hand, may be less flexible and require more extensive and costly modifications to adapt to changing requirements or future expansions.
5. Sustainability:
Modular construction exhibits greater sustainability compared to traditional methods. The factory-controlled environment allows for better waste management, as material usage is optimized, and scrap and debris are minimized. Precise manufacturing processes also reduce the energy consumption associated with on-site construction activities. Additionally, modular construction facilitates the incorporation of energy-efficient systems and green building practices, promoting sustainable design and operation. Traditional construction methods may generate more waste, require additional on-site energy usage, and be less accommodating to green building practices.
Read more: What Is A Skid In Construction
6. Quality of Living:
Modular construction ensures a high-quality living or working environment. The modules are constructed with precision and adherence to building codes and standards. The controlled factory environment allows for the integration of advanced technologies and systems that may be more challenging to implement in traditional construction. Components, such as electrical and plumbing systems, also undergo thorough testing before installation. Traditional construction methods, while meeting building codes, may have variations in workmanship and require additional inspections to achieve the same level of quality as modular construction.
Considering these factors, modular construction is a viable alternative to traditional construction methods, offering a more efficient, cost-effective, and sustainable approach to building construction. However, it is important to evaluate the specific project requirements and constraints to determine the most suitable construction method.
In the next section, we will explore case studies of successful modular construction projects, highlighting their benefits and real-world applications.
Case Studies of Successful Modular Construction Projects
Modular construction has gained significant traction in recent years, and several successful projects serve as testament to its benefits and potential applications. The following case studies highlight notable examples of successful modular construction projects:
1. Brooklyn Navy Yard, Building 77 – New York, USA:
The redevelopment of Building 77 in the Brooklyn Navy Yard showcases the possibilities of modular construction for large-scale commercial projects. The historic building was transformed into a modern, efficient, and sustainable workspace using modular construction methods. The project involved the production of over 1,100 modular components, including office spaces, common areas, and retail space. The use of modular construction reduced construction time by nearly 50% compared to traditional methods. The project achieved LEED Platinum certification, highlighting the sustainability benefits of modular construction.
2. Tower Hotel – London, UK:
The Tower Hotel, located in the heart of London, exemplifies how modular construction can be used for fast-paced hotel projects. The hotel underwent a major expansion using off-site modular construction methods. Over 400 modules were produced and installed, resulting in an additional 130 guest rooms and a new rooftop bar. The use of modular construction minimized disruption to hotel operations, reduced construction time by 25%, and allowed for faster revenue generation. The project received the Offsite Construction Award for Hotel of the Year.
Read more: What Is Girder In Construction
3. Acute Hospital – Cambridge, UK:
The Acute Hospital project in Cambridge showcases the benefits of modular construction for healthcare facilities. The project involved the construction of a state-of-the-art hospital using off-site modular construction methods. The modular components, including patient rooms, operating theaters, and support facilities, were manufactured off-site and transported to the construction site. The use of modular construction reduced the construction schedule by several months, allowing for earlier patient care and cost savings. The project also achieved high sustainability standards and received BREEAM Excellent certification.
4. Stack Apartments – Seattle, USA:
The Stack Apartments project in Seattle demonstrates how modular construction can be utilized for residential projects. The project involved the construction of a 17-story apartment building using volumetric modular construction methods. The modules, complete with kitchens, bathrooms, and finishes, were fabricated off-site and installed on-site using a tower crane. The use of modular construction significantly reduced construction time, with the project completed 40% faster compared to traditional construction methods. The apartments offer high-quality living spaces with modern amenities and achieved LEED Platinum certification.
5. Apple Campus 2 – Cupertino, USA:
The Apple Campus 2, also known as Apple Park, is a groundbreaking example of modular construction for large corporate campuses. The project involved the construction of the iconic circular building using panelized construction methods. The building components, including walls, floors, and roof elements, were manufactured off-site and assembled on-site. The modular construction approach allowed for faster construction, increased efficiency, and minimized material waste. The result is a cutting-edge, energy-efficient campus designed to inspire creativity and collaboration.
These case studies highlight the diverse range of successful modular construction projects, spanning commercial, residential, healthcare, and corporate sectors. The projects showcase the benefits of modular construction, including reduced construction time, cost savings, sustainability, and high-quality construction.
In the next section, we will explore future trends and innovations in modular construction, highlighting the potential advancements that can further revolutionize the industry.
Future Trends and Innovations in Modular Construction
As modular construction continues to gain popularity, there are several exciting future trends and innovations that hold the potential to further revolutionize the construction industry. These advancements aim to enhance efficiency, sustainability, and design flexibility. Here are some key trends to watch for in the future of modular construction:
Read more: What Is Casework In Construction
1. Digitalization and Building Information Modeling (BIM):
Digitalization, along with the adoption of Building Information Modeling (BIM), is shaping the future of modular construction. BIM enables the creation of precise 3D digital models that integrate design, engineering, and construction information. This technology enhances collaboration, reduces errors, and improves project visualization and coordination. As BIM adoption becomes more prevalent, it will further streamline the design, fabrication, and assembly processes in modular construction.
2. Robotics and Automation:
The integration of robotics and automation presents exciting possibilities for modular construction. Robotic systems can streamline various tasks, such as material handling, cutting, welding, and assembly. Automation can improve precision, efficiency, and safety in the manufacturing and assembly processes. Implementing robotic and automated systems in modular construction can reduce labor requirements, enhance consistency, and speed up production without compromising quality.
3. Advanced Materials and Sustainable Solutions:
Advancements in materials science offer opportunities for sustainable and energy-efficient modular construction. The development of innovative and eco-friendly materials, such as recycled and bio-based materials, can reduce the environmental impact of construction. Additionally, incorporating energy-efficient systems, such as smart HVAC and lighting, can further enhance sustainability. The use of green building certifications, such as LEED and BREEAM, will likely become more common in modular construction projects as sustainability becomes an increasing priority.
4. Modular Hybrid Construction:
Modular hybrid construction combines modular elements with traditional construction methods to optimize project efficiency and design flexibility. This approach allows for the use of both off-site fabricated modules and on-site construction, leveraging the benefits of both methods. Hybrid construction enables more complex building designs and customization options while still benefiting from the speed and cost savings associated with modular construction. This trend is particularly relevant for larger and more intricate projects.
Read more: What Is RFP In Construction
5. Vertical Modular Construction:
Vertical modular construction, also known as stackable modular construction, is gaining momentum. It involves stacking modular units vertically to create taller structures, such as high-rise buildings. This approach allows for greater density and efficient use of limited urban space. Vertical modular construction presents unique engineering and logistical challenges, but advancements in technologies and construction techniques are enabling its feasibility and introduction into urban landscapes.
6. Off-Site Advanced Manufacturing (OSAM):
Off-Site Advanced Manufacturing (OSAM) is a concept that encompasses the integration of multiple advanced manufacturing technologies into modular construction. This includes additive manufacturing (3D printing), robotics, automation, and digital fabrication techniques. OSAM has the potential to revolutionize modular construction by enabling greater customization, faster production, and the use of unconventional materials. It paves the way for innovative and highly efficient construction techniques and offers unprecedented design possibilities.
These future trends and innovations in modular construction hold immense potential to transform the construction industry. As technologies continue to advance and sustainability becomes increasingly important, modular construction will likely become the go-to method for efficient, cost-effective, and environmentally friendly building construction.
In the concluding section, we will summarize the key points covered in this article and emphasize the benefits and growing relevance of modular construction in today’s construction landscape.
Conclusion
Modular construction has emerged as a game-changer in the building construction industry, offering numerous benefits and reshaping the way we approach construction projects. As discussed in this article, modular construction involves the fabrication of building components or modules off-site in a controlled factory environment, which are then transported to the construction site and assembled together to create the final structure.
The advantages of modular construction are substantial. It reduces construction time, leading to faster project completion and occupancy. The controlled factory environment ensures higher quality control and lower material waste. Modular construction is also cost-effective, allowing for cost savings due to streamlined production and reduced labor requirements. Moreover, it promotes sustainability through efficient material usage and incorporation of green building practices.
There are two main types of modular construction methods: volumetric construction and panelized construction. Volumetric construction involves the production of fully enclosed modules, while panelized construction involves the creation of panels that are assembled on-site. Both methods have their unique advantages and are suited to different project requirements.
The off-site modular construction process involves design, engineering, module production, transportation, assembly, and finishing on-site. Collaborative design, effective coordination, and adherence to building codes are key factors to consider during modular construction projects. Additionally, challenges such as design limitations, transportation logistics, and financing need to be addressed to ensure successful implementation.
Modular construction can be compared to traditional construction methods, highlighting the advantages it brings to the table. Modular construction offers faster construction time, cost savings, improved quality control, flexibility, and sustainability benefits. It provides a high-quality living and working environment, while also adapting to changing needs through easy reconfiguration and customization.
The success of modular construction is evident in numerous case studies, including the redevelopment of Brooklyn Navy Yard’s Building 77, the expansion of the Tower Hotel in London, the construction of the Acute Hospital in Cambridge, the Stack Apartments in Seattle, and the development of the Apple Campus 2 in Cupertino. These projects demonstrate the versatility and efficiency of modular construction across various sectors.
The future of modular construction is promising, with trends and innovations on the horizon. Digitalization, robotics, automation, advanced materials, hybrid construction, vertical construction, and off-site advanced manufacturing are shaping the future landscape of modular construction. These advancements aim to further enhance efficiency, sustainability, and design flexibility in the construction industry.
In conclusion, modular construction is revolutionizing the building construction industry, offering faster construction time, cost savings, enhanced quality control, flexibility, and sustainability benefits. As technology continues to advance and stakeholders recognize the advantages of modular construction, its relevance and adoption are on the rise. Modular construction is paving the way for a more efficient, cost-effective, and sustainable future in construction.
Frequently Asked Questions about What Is Modular Construction Methods
Was this page helpful?
At Storables.com, we guarantee accurate and reliable information. Our content, validated by Expert Board Contributors, is crafted following stringent Editorial Policies. We're committed to providing you with well-researched, expert-backed insights for all your informational needs.
0 thoughts on “What Is Modular Construction Methods”