Home>diy>Building & Construction>What Is QA/QC In Construction
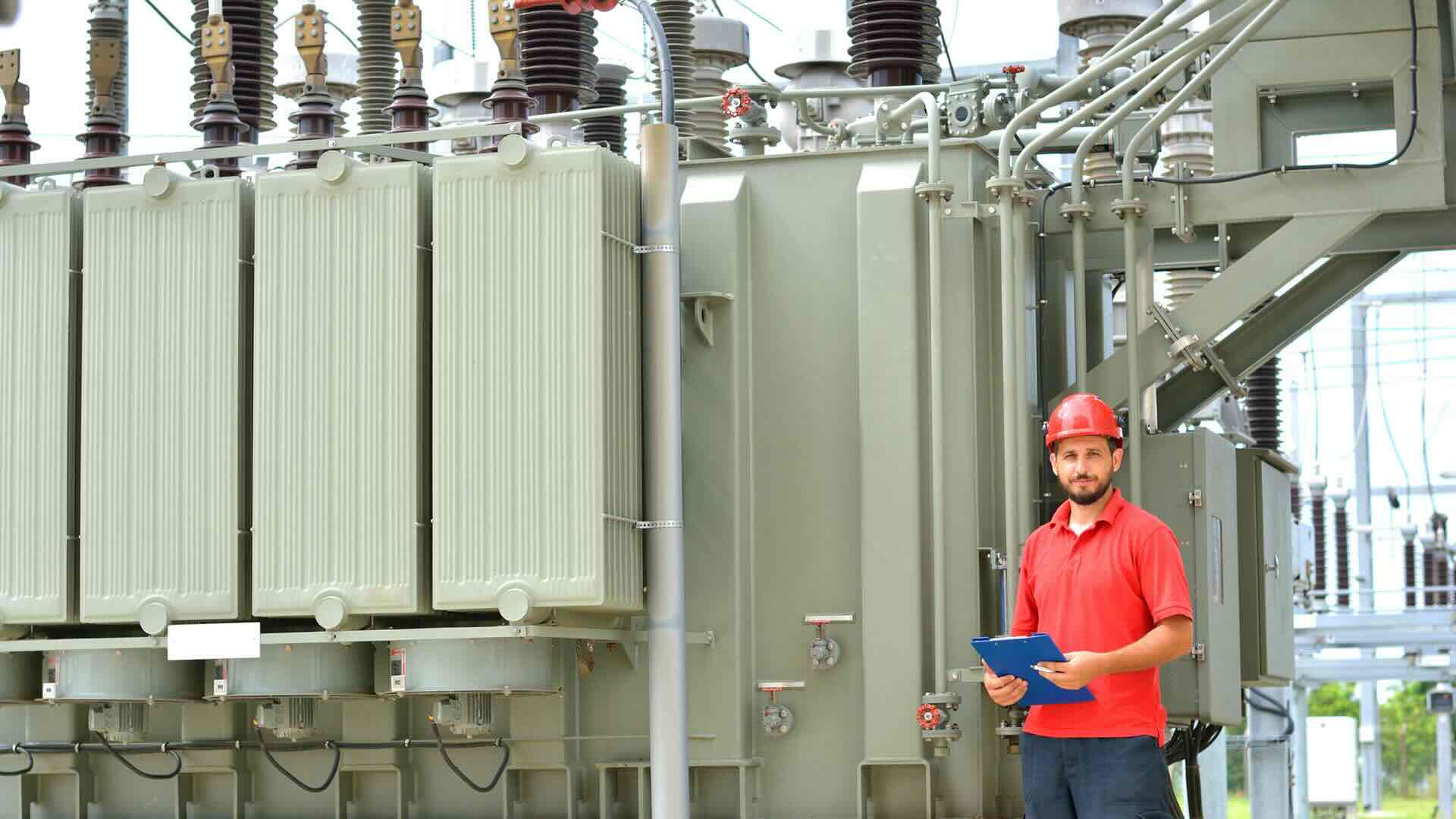
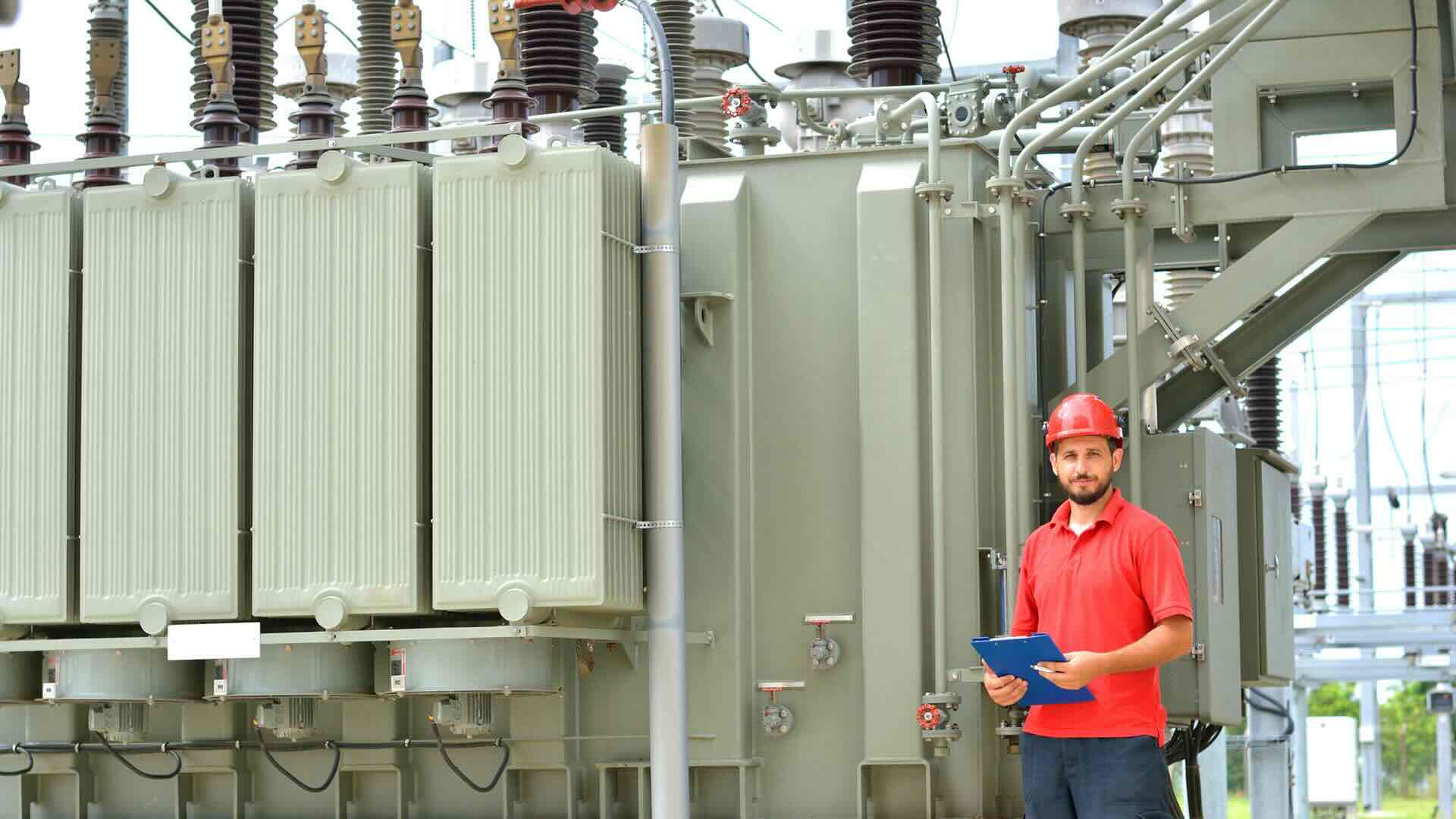
Building & Construction
What Is QA/QC In Construction
Modified: January 20, 2024
Learn about the importance of QA/QC in building construction and how it ensures quality standards are met, ensuring a successful project.
(Many of the links in this article redirect to a specific reviewed product. Your purchase of these products through affiliate links helps to generate commission for Storables.com, at no extra cost. Learn more)
Introduction
When it comes to the construction industry, ensuring quality and maintaining high standards is of paramount importance. This is where Quality Assurance and Quality Control, commonly referred to as QA/QC, play a crucial role. QA/QC in construction is a process that focuses on ensuring that the project meets the specified requirements and standards, enhancing the overall quality and reliability of the construction project.
QA/QC involves implementing systematic procedures and measures to monitor and evaluate various aspects of the construction project, from design and material selection to construction and final inspection. By implementing QA/QC processes, construction companies can minimize errors, defects, and delays while enhancing productivity, safety, and customer satisfaction.
In this article, we will explore the concept of QA/QC in construction, its importance, the different processes involved, and the role it plays in construction projects. We will also discuss the challenges faced in implementing QA/QC and provide possible solutions.
Key Takeaways:
- QA/QC in construction ensures compliance, minimizes errors, enhances safety, and improves customer satisfaction. It’s crucial for optimizing resource allocation, building a strong reputation, and delivering successful projects.
- Implementing QA/QC processes involves setting standards, conducting inspections, and addressing challenges. Overcoming resistance, coordinating effectively, and investing in training are essential for successful QA/QC implementation in construction.
Read more: What Is Pre-Construction In Construction
Definition of QA/QC in Construction
Quality Assurance (QA) and Quality Control (QC) are two essential components of the construction process that ensure the delivery of a high-quality end product. While the terms QA and QC are often used interchangeably, they have distinct meanings and functions in the construction industry.
Quality Assurance (QA) refers to the proactive and systematic activities implemented to ensure that the construction project adheres to specified requirements and standards. It involves the development and implementation of policies, procedures, guidelines, and the establishment of quality objectives. QA focuses on preventing defects and errors by constantly evaluating and improving the construction processes. The goal of QA is to deliver a project that meets or exceeds the client’s expectations while maintaining compliance with local regulations and industry standards.
On the other hand, Quality Control (QC) is the process of inspecting, testing, and monitoring the construction project to ensure that the established quality standards are met. It involves conducting inspections, tests, and audits at different stages of the construction process to identify and rectify any non-conformities, defects, or deviations from the specified requirements. QC ensures that the construction activities are carried out correctly and that the final product meets the desired quality standards.
Together, QA and QC work hand in hand to ensure the overall quality of the construction project. QA focuses on preventing issues and optimizing processes, while QC focuses on identifying and correcting issues during the construction process.
By implementing a robust QA/QC system, construction companies can establish a culture of quality, improve project outcomes, and minimize risks and costly rework. QA/QC acts as a continuous feedback loop, allowing construction teams to learn from past mistakes, refine their processes, and enhance the quality of future projects.
Importance of QA/QC in Construction Projects
Quality Assurance and Quality Control (QA/QC) play a crucial role in construction projects. Implementing QA/QC processes and standards is essential for various reasons:
- Ensuring Compliance: QA/QC ensures that the construction project complies with the specified requirements, building codes, regulations, and industry standards. This helps to minimize legal and regulatory risks and avoid penalties or delays in project completion.
- Minimizing Errors and Defects: By implementing rigorous QA/QC processes, construction companies can identify and rectify errors and defects early in the construction process. This helps to reduce rework, increase productivity, and mitigate unnecessary costs.
- Enhancing Safety: QA/QC includes monitoring and evaluating safety procedures and protocols throughout the construction project. It helps to identify potential safety hazards, implement corrective measures, and ensure a safe working environment for all workers and stakeholders.
- Improving Customer Satisfaction: QA/QC ensures that the finished project meets or exceeds the client’s expectations in terms of quality, functionality, and aesthetics. This leads to higher customer satisfaction, positive reviews, and potential for future business opportunities and referrals.
- Optimizing Resource Allocation: By implementing QA/QC processes, construction companies can optimize the allocation of resources, including materials, equipment, and manpower. This helps to prevent wastage, improve efficiency, and maintain project timelines.
- Facilitating Quality Control Tools: QA/QC provides a framework for implementing various quality control tools and techniques, such as inspections, audits, testing, and documentation. These tools help in identifying deviations, non-conformities, and potential issues that need to be addressed to maintain the desired quality standards.
- Building a Reputation: A strong commitment to QA/QC builds a reputation for the construction company as a reliable and quality-focused organization. This can lead to increased opportunities for future projects, partnerships, and client trust.
In summary, QA/QC is essential for achieving successful construction projects. It ensures compliance, reduces errors and defects, enhances safety, improves customer satisfaction, optimizes resource allocation, facilitates quality control tools, and builds a strong reputation. By implementing and maintaining a robust QA/QC system, construction companies can uphold high-quality standards, mitigate risks, and deliver superior outcomes for their clients.
QA/QC Processes in Construction
The implementation of QA/QC processes in construction projects involves several key steps and procedures to ensure the desired quality standards are met. Here are some of the common QA/QC processes in construction:
- Design Review: The QA/QC process begins with a thorough review of the project design plans and specifications. This step involves checking for errors, inconsistencies, and compliance with relevant codes and regulations. Design reviews help identify potential issues that may impact the quality and functionality of the project.
- Materials Testing and Approval: QA/QC includes the testing and approval of construction materials to ensure they meet the required quality standards. This involves conducting laboratory tests, inspecting samples, and verifying certifications. Materials testing ensures that only approved and high-quality materials are used in the construction process.
- Quality Inspections: Quality inspections are conducted at various stages of the construction process to monitor compliance with design specifications, industry standards, and safety regulations. Inspections may include structural elements, electrical and plumbing systems, finishes, and overall workmanship. Inspectors check for defects, deviations, and non-conformities and provide corrective actions to ensure quality standards are met.
- Documentation and Record Keeping: QA/QC requires meticulous documentation and record keeping to track project progress, inspections, tests, and any deviations from the specified requirements. This documentation helps in identifying patterns, trends, and areas that may require improvement or corrective action. It also serves as a reference for future projects or audits.
- Quality Control Tools and Techniques: Implementing various quality control tools and techniques is an integral part of QA/QC in construction. This may include non-destructive testing, statistical process control, root cause analysis, and quality management software. These tools help in identifying issues, analyzing data, and implementing corrective measures to maintain quality standards.
- Audits and Reviews: Regular audits and reviews are conducted to evaluate the effectiveness of the QA/QC processes and identify areas for improvement. Internal audits and third-party reviews provide an independent assessment of the quality management system and help in identifying gaps, non-compliance, and opportunities for enhancement.
- Training and Education: QA/QC involves providing training and education to construction teams to ensure they have the necessary knowledge and skills to carry out their tasks in compliance with quality standards. This includes training on safety protocols, quality control techniques, and best practices. Ongoing training helps in fostering a culture of quality and continuous improvement.
By implementing these QA/QC processes, construction companies can ensure consistent quality, minimize errors and defects, enhance safety, and deliver successful construction projects that meet or exceed client expectations.
Key Differences between QA and QC in Construction
Although Quality Assurance (QA) and Quality Control (QC) are closely related and often used together, they have distinct roles and responsibilities in the construction industry. Here are the key differences between QA and QC in construction:
- Focus: QA focuses on preventing issues and ensuring that the construction project meets the specified requirements and standards. QC, on the other hand, focuses on detecting and correcting issues during the construction process to maintain the desired quality standards.
- Proactive vs. Reactive: QA is a proactive process that involves establishing policies, procedures, and guidelines to prevent quality issues. It focuses on implementing preventive measures and continuously improving the construction processes. QC, on the other hand, is a reactive process that involves inspecting, testing, and monitoring the construction project to identify and correct deviations from the specified requirements.
- Process vs. Product: QA is concerned with the overall construction process, from design to completion. Its goal is to ensure that the processes, materials, and techniques used in construction are of high quality and follow industry standards. QC, on the other hand, is concerned with inspecting and testing the final product to ensure it meets the desired quality standards.
- Prevention vs. Detection: QA focuses on preventing potential quality issues by implementing quality control measures and verifying compliance with standards throughout the construction process. QC, on the other hand, focuses on detecting and correcting quality issues through inspections, tests, and audits.
- Long-term vs. Short-term Perspective: QA takes a long-term perspective and aims to prevent issues in future projects by identifying and addressing root causes. It focuses on continuous improvement to optimize quality and efficiency. QC has a short-term perspective and is concerned with ensuring the current project meets the desired quality standards.
- Role of Personnel: QA is the responsibility of everyone involved in the construction project, from project managers to subcontractors and workers. It requires a collective effort to maintain quality standards. QC is typically carried out by dedicated quality control personnel or inspectors who are responsible for conducting inspections, tests, and audits.
- Process Monitoring vs. Product Inspection: QA involves monitoring the construction process and evaluating the effectiveness of various procedures and activities. It focuses on ensuring that the processes are carried out correctly to maintain quality standards. QC involves inspecting and testing the final product to verify its compliance with the specified requirements.
Both QA and QC are crucial for achieving high-quality construction projects. By implementing effective QA processes, construction companies can prevent quality issues and maintain consistency throughout the project. Utilizing QC processes ensures that the final product meets the desired quality standards by detecting and correcting any deviations. Both QA and QC work together in a complementary manner to achieve excellence in construction projects.
QA/QC in construction refers to the processes and procedures put in place to ensure that the quality of the construction meets the required standards and specifications. This includes regular inspections, testing, and documentation to identify and address any issues early on.
Read more: What Is Construction
QA/QC Standards and Codes in Construction
In the construction industry, adherence to standards and codes is essential to ensure the quality, safety, and compliance of the constructed assets. Various organizations and regulatory bodies have established QA/QC standards and codes that govern construction practices. Here are some prominent QA/QC standards and codes in construction:
- ISO 9001: ISO 9001 is an international standard for quality management systems. It provides a framework for implementing and maintaining a robust quality management system, including QA/QC processes. ISO 9001 focuses on customer satisfaction, continuous improvement, and the prevention of defects by establishing processes and procedures to ensure consistent quality throughout the construction project.
- ASTM International: ASTM International is a globally recognized organization that develops and publishes technical standards for a wide range of materials, products, and systems. Their standards cover aspects such as materials testing, construction practices, and building codes. Compliance with ASTM standards ensures that materials used in construction meet specific quality and performance requirements.
- National Building Codes: Many countries have national building codes that specify the minimum standards for the design, construction, and occupancy of buildings. These codes provide guidelines on structural integrity, fire safety, electrical systems, plumbing, and other critical aspects of construction. Compliance with national building codes is essential to ensure safety and quality in construction projects.
- Occupational Safety and Health Administration (OSHA) Standards: OSHA is a regulatory body in the United States that sets and enforces standards for occupational safety and health. Their standards cover a wide range of construction-related hazards, including fall protection, electrical safety, scaffolding, and excavation. Compliance with OSHA standards ensures a safe working environment and minimizes risks for construction workers.
- LEED Certification: LEED (Leadership in Energy and Environmental Design) is a green building certification program that focuses on sustainable design and construction practices. Projects seeking LEED certification must adhere to specific criteria related to energy efficiency, water conservation, indoor air quality, and materials selection. Compliance with LEED standards ensures environmentally responsible construction practices.
- British Standards (BS): British Standards are a set of technical standards and codes of practice developed by the British Standards Institution (BSI). These standards cover a wide range of construction-related disciplines, including structural design, materials testing, civil engineering, and electrical systems. Compliance with British Standards ensures the quality and reliability of construction projects in the United Kingdom and other countries that adopt these standards.
- International Building Codes (IBC): The International Building Codes are a set of model building codes developed by the International Code Council (ICC). These codes provide comprehensive regulations for the design, construction, and maintenance of buildings. They cover various aspects, including fire safety, structural integrity, accessibility, and energy efficiency. Compliance with IBC ensures that buildings meet minimum safety and quality requirements.
Adhering to these QA/QC standards and codes is essential for construction companies to ensure quality, safety, and compliance with industry best practices. They provide guidelines, specifications, and benchmarks that help in delivering construction projects of high quality and reliability.
Role of QA/QC in Construction Projects
The role of Quality Assurance (QA) and Quality Control (QC) in construction projects is crucial to ensuring the successful execution of projects and achieving the desired quality standards. Here are some key roles of QA/QC in construction:
- Setting Quality Standards: QA/QC establishes the quality standards and requirements that need to be met throughout the construction project. This includes defining specifications, codes, regulations, and industry standards. Clear and well-defined quality standards provide a benchmark for the entire construction process.
- Implementing Quality Assurance Processes: QA focuses on implementing proactive processes to prevent quality issues and ensure compliance with the established standards. This includes developing and documenting quality plans, procedures, and guidelines. QA processes help in identifying potential risks, improving construction methods, and ensuring a systematic approach to quality management.
- Performing Quality Control Inspections and Tests: QC is responsible for conducting inspections, tests, and audits at various stages of the construction project. It ensures that the work being carried out aligns with the specified quality standards and meets the desired requirements. This includes inspecting materials, verifying installations, conducting functional tests, and assessing workmanship.
- Identifying and Addressing Non-Conformities: QA/QC plays a vital role in identifying non-conformities, defects, and deviations from the quality standards. The QA/QC team works closely with project stakeholders to communicate and rectify the issues. This involves developing corrective action plans, documenting non-conformities, and ensuring timely resolution to maintain quality standards.
- Documentation and Record Keeping: QA/QC maintains comprehensive documentation and record keeping throughout the construction project. This includes recording inspection results, test reports, quality control data, and any corrective actions taken. Documentation provides a historical record of the project progress, deviations, and remedial actions.
- Continuous Improvement: QA/QC strives for continuous improvement in construction practices. It involves analyzing data, reviewing processes, and identifying areas for enhancement. Lessons learned from previous projects are incorporated to refine construction procedures, optimize resource utilization, and improve project outcomes.
- Ensuring Compliance and Safety: QA/QC ensures compliance with relevant codes, regulations, and safety standards. This includes monitoring construction activities for safety hazards, implementing safety protocols, and ensuring the use of approved materials and methods. QA/QC helps in creating a safe working environment and minimizing risks for workers and stakeholders.
- Client Satisfaction: Ultimately, the role of QA/QC is to ensure client satisfaction by delivering a high-quality construction project. By maintaining consistent quality, meeting or exceeding client expectations, and minimizing defects and issues, QA/QC contributes to positive client experiences and long-term relationships.
QA/QC is an essential part of construction project management, ensuring that projects are executed with precision, adherence to standards, and a commitment to quality. By fulfilling their roles effectively, QA/QC teams contribute to the successful completion of construction projects that meet the established quality standards, safety requirements, and client expectations.
Challenges and Solutions in QA/QC Implementation in Construction
The implementation of Quality Assurance (QA) and Quality Control (QC) in construction projects can come with various challenges. However, with careful planning and proactive measures, these challenges can be overcome. Here are some common challenges and their potential solutions in QA/QC implementation in construction:
- Lack of Awareness and Training: One challenge is the lack of awareness and training among construction personnel regarding QA/QC processes and standards. Solution: Providing comprehensive training programs and workshops to educate and train all stakeholders on the importance of QA/QC and how to implement it effectively can address this challenge.
- Resistance to Change: Implementing QA/QC may face resistance from construction teams who are accustomed to traditional practices. Solution: Clearly communicating the benefits of QA/QC, engaging employees in the process, and involving them in decision-making can help overcome resistance and gain buy-in.
- Cost and Time Constraints: Allocating resources, both in terms of time and budget, for the implementation of QA/QC processes can be a challenge. Solution: Proper planning, prioritizing critical QA/QC activities, and integrating them into the overall project schedule and budget can help overcome these constraints.
- Coordination and Communication: Construction projects involve multiple teams and stakeholders, making coordination and effective communication challenging. Solution: Establishing clear communication channels, holding regular meetings, and utilizing collaborative project management tools can enhance coordination, ensuring everyone is aligned with QA/QC requirements and expectations.
- Inadequate Documentation: Insufficient documentation and record keeping can hinder QA/QC efforts, making it difficult to track and analyze project progress and identify areas for improvement. Solution: Implementing a robust documentation system and utilizing digital tools for data collection and storage can ensure accurate and organized documentation throughout the project.
- Interpretation of Standards: Different interpretations of standards and codes by different parties involved in the project can lead to inconsistencies and conflicts. Solution: Clearly defining and communicating the interpretation of standards, providing training on their application, and promoting open dialogue among stakeholders can help align expectations and minimize misunderstandings.
- Challenges with Third-Party Inspections: Relying on third-party inspections can introduce challenges related to availability, qualifications, and consistency of inspections. Solution: Carefully vetting and selecting reputable third-party inspection agencies, establishing clear expectations, and conducting regular performance evaluations can help ensure the quality and reliability of third-party inspections.
- Monitoring Subcontractors and Suppliers: The quality control and assurance of subcontracted work and materials provided by suppliers can be a challenge. Solution: Implementing a robust supplier qualification process, conducting regular audits, and clearly defining quality requirements in subcontract agreements can help ensure the quality of work and materials from subcontractors and suppliers.
Addressing these challenges requires a proactive approach, effective communication, and collaboration among all project stakeholders. By implementing appropriate solutions, construction companies can overcome these challenges, enhance the effectiveness of QA/QC implementation, and deliver high-quality construction projects that meet or exceed client expectations.
Conclusion
Quality Assurance (QA) and Quality Control (QC) form the backbone of construction projects, ensuring the delivery of high-quality, safe, and compliant results. Throughout the construction process, QA/QC processes and standards play a crucial role in preventing defects, minimizing errors, and optimizing overall project performance.
The implementation of QA/QC in construction involves setting rigorous quality standards, implementing proactive processes, conducting thorough inspections and tests, and continuously improving construction practices. By doing so, construction companies can enhance compliance with codes and regulations, reduce risks, improve customer satisfaction, optimize resource allocation, and build a strong reputation in the industry.
However, implementing QA/QC in construction also comes with its set of challenges. These challenges can be overcome through proper training and education, effective communication and coordination, allocation of sufficient resources, and the utilization of technology to aid documentation and data management. By addressing these challenges head-on, construction companies can maximize the benefits of QA/QC implementation and overcome potential obstacles.
In conclusion, QA/QC is not just a process; it is a mindset and commitment to achieving excellence in every aspect of construction projects. By establishing a culture of quality, incorporating QA/QC processes into the project lifecycle, and continuously striving for improvement, construction companies can deliver projects that meet or exceed the expectations of clients, stakeholders, and regulatory authorities.
With the ever-increasing demand for high-quality construction projects, the importance of QA/QC cannot be overstated. By investing in QA/QC and prioritizing quality throughout the construction process, companies can position themselves as leaders in the industry, while ensuring the safety, longevity, and value of the built environment.
Frequently Asked Questions about What Is QA/QC In Construction
Was this page helpful?
At Storables.com, we guarantee accurate and reliable information. Our content, validated by Expert Board Contributors, is crafted following stringent Editorial Policies. We're committed to providing you with well-researched, expert-backed insights for all your informational needs.
0 thoughts on “What Is QA/QC In Construction”