Home>diy>Building & Construction>What Is Safety In Construction
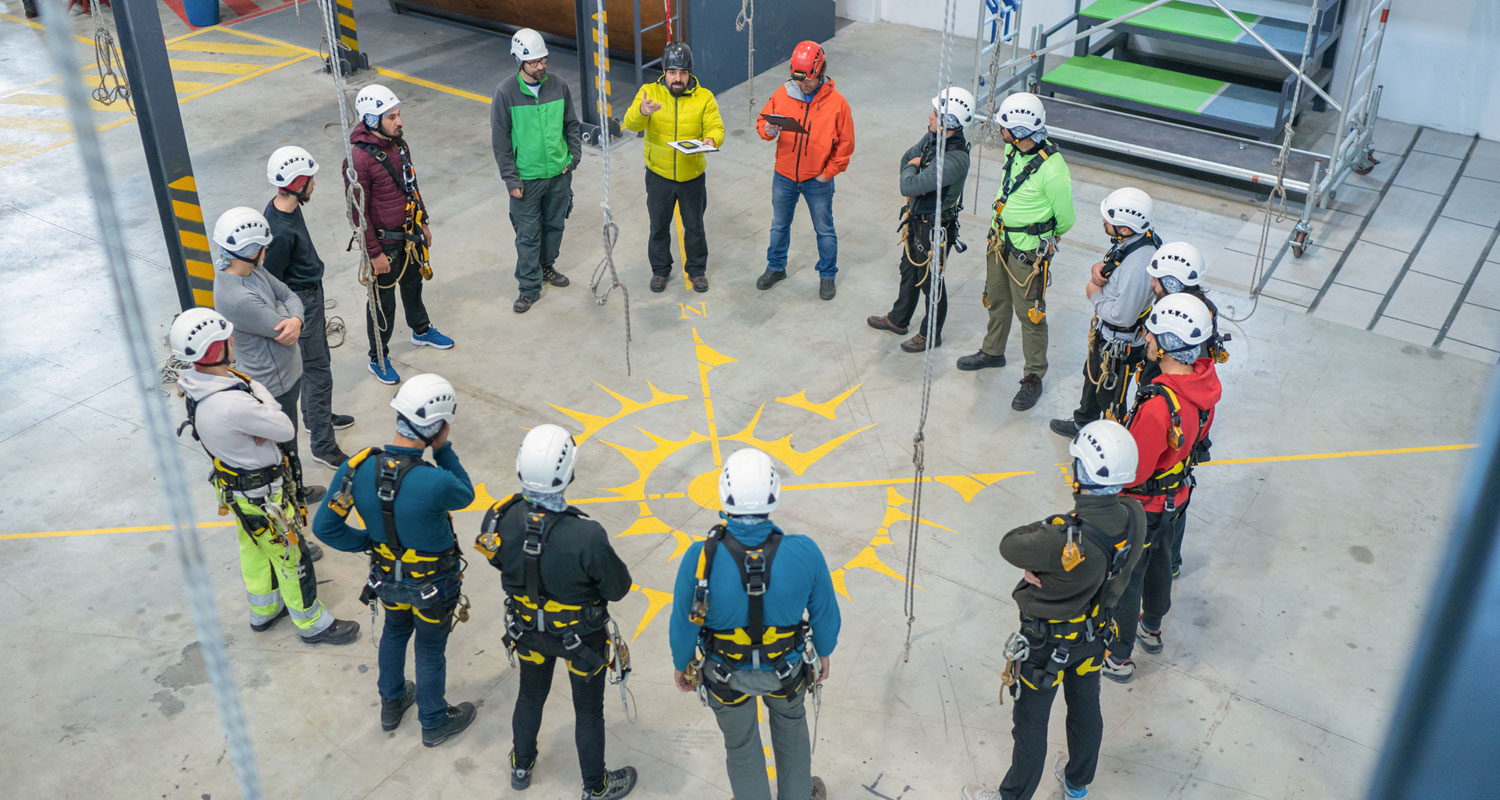
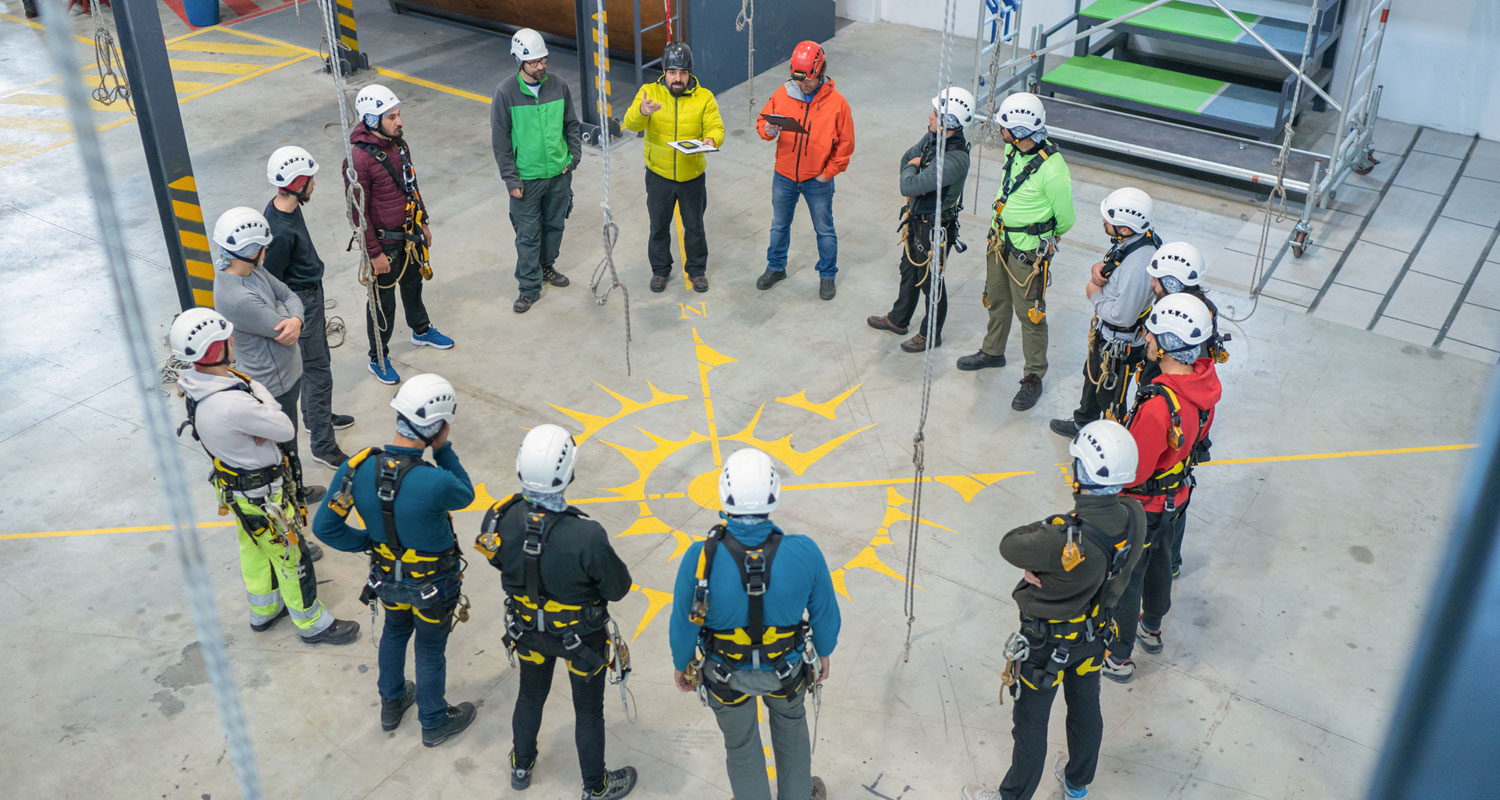
Building & Construction
What Is Safety In Construction
Modified: March 6, 2024
Learn about safety in building construction and how it plays a crucial role in preventing accidents and ensuring the well-being of workers and the public.
(Many of the links in this article redirect to a specific reviewed product. Your purchase of these products through affiliate links helps to generate commission for Storables.com, at no extra cost. Learn more)
Introduction
Welcome to the exciting world of construction! With its towering skyscrapers, bustling construction sites, and innovative engineering marvels, the construction industry plays a vital role in shaping our cities and infrastructure. However, amidst the hustle and bustle of construction activities, there is a crucial aspect that should never be overlooked – safety.
Safety in construction is of utmost importance, not only for the well-being and welfare of the construction workers, but also for the successful completion of projects. In this article, we will explore the significance of safety in construction, the legal requirements and regulations that govern it, the common hazards encountered on construction sites, and the safety measures and procedures that must be implemented to ensure a safe working environment.
Key Takeaways:
- Safety is crucial in construction to protect workers, prevent accidents, and ensure project success. It requires commitment from everyone involved to create a culture of safety and continuous improvement.
- Employers and employees both play vital roles in maintaining a safe working environment. By prioritizing safety, following procedures, and actively participating, construction companies can protect their workers and achieve safety excellence.
Read more: What Is Pre-Construction In Construction
Importance of Safety in Construction
Safety is the cornerstone of any construction project. It is not just a legal obligation, but also a moral responsibility of employers, contractors, and workers. The construction industry is known for its inherent risks and hazards, making safety a critical aspect that cannot be overlooked or compromised.
Ensuring safety in construction is essential for several reasons:
1. Preserving human life and well-being: Construction sites can be dangerous environments with the potential for accidents and injuries. By implementing proper safety measures, workers are protected from harm, minimizing the risk of accidents, injuries, or even fatalities. Prioritizing safety shows a commitment to protecting the welfare of everyone involved in the construction process.
2. Enhancing productivity: Safety and productivity go hand in hand. When workers feel safe and secure in their working environment, they can focus on their tasks without the fear of accidents or injuries. This creates a positive work atmosphere that boosts motivation and productivity, resulting in efficient project completion and reduced downtime due to accidents.
3. Minimizing financial losses: Construction accidents can lead to significant financial losses for construction companies. Workers’ compensation, medical expenses, legal fees, project delays, and damaged equipment are just a few of the costs that can arise from accidents. By prioritizing safety, companies can mitigate the risk of accidents and the subsequent financial burden.
4. Meeting legal obligations: The construction industry is heavily regulated, with specific laws and regulations in place to ensure the safety and well-being of workers. By adhering to these legal requirements, construction companies can avoid penalties, fines, legal disputes, and damage to their reputation.
5. Upholding a good reputation: Safety is a crucial factor in building and maintaining a positive reputation in the construction industry. Clients, investors, and stakeholders are more likely to trust and engage with companies that prioritize safety, as it demonstrates professionalism, reliability, and a commitment to quality.
6. Ensuring project success: Safety is an integral part of project management. It helps in identifying and mitigating potential risks and hazards, thereby minimizing or preventing delays, rework, and cost overruns. A safe working environment enables smooth and uninterrupted project progress, ensuring timely completion and client satisfaction.
Clearly, safety in construction is not just an option, but a necessity. It is a key factor in protecting lives, enhancing productivity, minimizing financial losses, meeting legal obligations, upholding a good reputation, and ensuring the success of construction projects. It is the responsibility of everyone involved in construction, from employers and contractors to workers, to prioritize safety and make it an integral part of their daily operations.
Legal Requirements and Regulations
The construction industry is subject to numerous legal requirements and regulations to ensure the safety and well-being of workers. These laws vary by country, state, and jurisdiction, but generally aim to establish a framework for safe construction practices. Let’s take a look at some of the common legal requirements and regulations in the construction industry:
1. Occupational Health and Safety Act: Most countries have a dedicated Occupational Health and Safety (OHS) Act or similar legislation that sets out the basic rights and responsibilities of employers, contractors, and workers in ensuring a safe working environment. These acts typically outline the duty to provide a safe workplace, the responsibility for conducting risk assessments, and the requirement to implement safety measures and procedures.
2. Building Codes and Regulations: Building codes are regulations that govern the design, construction, and maintenance of buildings and structures. They often include provisions for fire safety, structural integrity, accessibility, and other essential safety considerations. Compliance with building codes is essential to ensure that construction projects meet safety standards and are structurally sound.
3. Site-Specific Permits and Licensing: Depending on the nature of the construction project, specific permits and licenses may be required to ensure compliance with safety regulations. Permits may include excavation permits, scaffolding permits, hot work permits, and confined space permits, among others. These permits are typically obtained from local authorities and ensure that appropriate safety measures are in place for specific tasks or conditions.
4. Hazardous Material Regulations: Construction often involves the use of hazardous materials such as asbestos, lead, chemicals, and flammable substances. Regulations exist to govern the handling, storage, transportation, and disposal of these materials to protect both workers and the environment. Compliance with these regulations is crucial to prevent exposure to harmful substances and the associated health risks.
5. Electrical Safety Standards: Construction sites commonly involve electrical work, which poses a high risk of electrical accidents and injuries. Electrical safety standards dictate the proper installation, use, and maintenance of electrical systems. Compliance with these standards is crucial to prevent electrical hazards, such as electrical shocks, fires, and electrocutions.
6. Fall Protection Regulations: Falls from heights are one of the leading causes of construction-related fatalities and injuries. Fall protection regulations provide guidelines for the use of guardrails, safety nets, and personal fall arrest systems to prevent falls and protect workers working at elevated heights.
7. Environmental Regulations: Construction activities can have a significant impact on the environment. Environmental regulations govern issues such as erosion control, air quality, noise pollution, waste management, and protection of sensitive habitats. Compliance with these regulations is essential to minimize the environmental footprint of construction projects.
It is important for employers, contractors, and workers to familiarize themselves with the legal requirements and regulations that apply to their specific construction projects. Compliance with these laws not only ensures the safety of workers but also protects construction companies from legal liabilities, penalties, and reputational damage. Regular monitoring, updates, and adherence to these regulations are crucial to maintain a safe and legally compliant construction site.
Common Hazards in Construction
The construction industry is inherently hazardous, with numerous potential risks and hazards present on construction sites. Being aware of these hazards is crucial for all individuals involved in construction to take proactive measures to prevent accidents and injuries. Here are some of the common hazards encountered in construction:
1. Falls: Falls from heights are a significant cause of injuries and fatalities in construction. Working on scaffolding, ladders, roofs, or elevated platforms without proper fall protection can lead to severe consequences. It is essential to ensure the use of guardrails, safety harnesses, and other fall protection systems to prevent falls.
2. Electrocution: Electrical hazards pose a serious threat to construction workers. Contact with live wires, faulty electrical equipment, or improper use of electrical tools can lead to electrocution. Following electrical safety standards, such as proper grounding, insulation, and using appropriate personal protective equipment, is crucial to prevent accidents.
3. Struck By Objects: Construction sites involve the use of heavy machinery, equipment, and materials. Workers are at risk of being struck by falling objects, moving machinery, or material mishandling. Wearing appropriate head protection, implementing proper storage and lifting procedures, and maintaining clear work zones can help prevent these accidents.
4. Caught Between Objects: Construction workers may get caught between heavy machinery, equipment, or structures. Excavation work, trenching, and working in confined spaces can also pose a risk of entrapment. Adequate safety measures, such as proper barricading, trench supports, and diligent supervision, should be implemented to prevent these incidents.
5. Hazardous Substances: Construction often involves the use of hazardous substances such as asbestos, lead, chemicals, and solvents. Exposure to these substances can lead to serious health issues. Proper training, handling protocols, and personal protective equipment should be provided to mitigate the risks associated with hazardous substances.
6. Manual Handling: Construction involves heavy lifting, pushing, and carrying loads, which can lead to musculoskeletal injuries. Incorrect lifting techniques, overexertion, and inadequate training can put strain on workers’ bodies. Implementing proper manual handling techniques, using equipment like forklifts or cranes for heavy loads, and providing training on lifting methods can prevent such injuries.
7. Collapses and Structural Failures: Structural collapses, whether due to incomplete structures or inadequate support, pose a serious risk to workers on construction sites. Regular inspections, adherence to building codes and regulations, and proper engineering and construction practices are essential to prevent such accidents.
8. Noise and Vibration: Construction sites can be noisy environments with excessive levels of noise and vibration. Prolonged exposure to high noise levels can lead to hearing loss, while constant vibration exposure can lead to hand-arm vibration syndrome. Appropriate hearing protection and anti-vibration gloves should be provided, and measures such as noise barriers and equipment maintenance should be implemented to reduce exposure.
These are just a few examples of the many hazards that exist on construction sites. It is crucial for employers, contractors, and workers to identify, assess, and control these hazards to ensure a safe working environment. Regular safety training, proper use of personal protective equipment, implementation of safety procedures, and continuous hazard monitoring are essential to prevent accidents and create a culture of safety in construction.
Safety Measures and Procedures
Implementing effective safety measures and procedures is paramount in ensuring the well-being of workers and maintaining a safe construction site. By adhering to best practices and following industry standards, construction companies can significantly reduce the risk of accidents and injuries. Here are some essential safety measures and procedures to consider:
1. Risk Assessment: Conducting a thorough risk assessment is crucial before commencing any construction project. Identify potential hazards, evaluate their severity and likelihood, and develop strategies to eliminate or mitigate them. This assessment should be regularly reviewed and updated as the project progresses.
2. Site Safety Plan: Develop a comprehensive site safety plan that outlines all safety procedures, protocols, and responsibilities. This plan should cover areas such as fall protection, hazard communication, emergency response, and proper equipment usage. Ensure that all personnel on the site are familiar with and follow the safety plan.
3. Hazard Communication: Clearly communicate potential hazards to workers and ensure they understand the associated risks. Implement signage, labels, and color-coded systems to identify hazardous areas. Conduct regular safety meetings and toolbox talks to address specific hazards and remind workers of safe work practices.
4. Equipment Safety: Regularly inspect and maintain all machinery, tools, and equipment to ensure they are in proper working condition. Train workers on the correct usage, maintenance, and safety precautions for equipment. Provide guards, lockout/tagout systems, and appropriate safety devices to prevent accidents.
5. Housekeeping: Maintain a clean and organized construction site. Keep walkways, access points, and work areas clear of debris, materials, and equipment. Regularly remove waste and provide proper disposal facilities. Good housekeeping practices contribute to better visibility, reduced tripping hazards, and a safer work environment overall.
6. Emergency Preparedness: Develop and communicate emergency procedures to workers. Identify assembly points, evacuation routes, and the location of fire extinguishers, first aid stations, and emergency contact information. Conduct regular drills to ensure workers’ familiarity with emergency protocols.
7. Work at Heights: Implement proper fall protection measures for any work performed at heights. Provide and enforce the use of personal fall arrest systems, guardrails, safety nets, and anchor points. Train workers on proper use and inspection of fall protection equipment.
8. Personal Protective Equipment (PPE): Ensure that workers have access to and use appropriate personal protective equipment (PPE) for the specific hazards present on the construction site. This may include hard hats, safety goggles, gloves, hearing protection, high-visibility clothing, respiratory protection, and protective footwear.
9. Regular Safety Inspections: Conduct routine safety inspections to identify potential hazards, assess the effectiveness of safety measures, and address any issues promptly. Encourage workers to report safety concerns or near-miss incidents. Corrective actions should be taken to ensure a safe working environment.
10. Training and Education: Provide comprehensive safety training to all workers, regardless of their experience or role. Cover topics such as hazard recognition, equipment usage, emergency procedures, and safe work practices. Offer refresher training as needed and encourage ongoing education on safety topics.
Remember, safety is a collective effort that requires the commitment of everyone involved in the construction project. By implementing these safety measures and procedures, construction companies can create a culture of safety, protect their workers, and promote a positive and productive work environment.
Read more: What Is A Home Safety Walkthrough
Personal Protective Equipment (PPE)
Personal Protective Equipment (PPE) is an essential component of ensuring the safety and well-being of construction workers. PPE refers to equipment and clothing specifically designed to protect workers from hazards and minimize the risk of injury or illness. Here are some key aspects of PPE in the construction industry:
1. Head Protection: Hard hats or safety helmets are crucial for protecting the head from falling objects, electrical hazards, or striking against fixed structures. They should comply with safety standards and be worn by workers on construction sites at all times.
2. Eye and Face Protection: Safety glasses, goggles, or face shields protect the eyes and face from flying debris, chemical splashes, dust, and sparks. Workers involved in tasks such as cutting, grinding, welding, or using chemicals should wear appropriate eye and face protection.
3. Hearing Protection: Construction sites are often noisy environments, exposing workers to prolonged periods of high noise levels. Earplugs or earmuffs should be provided and worn by workers to prevent noise-induced hearing loss and protect against other hearing hazards.
4. Hand and Arm Protection: Gloves are essential in construction to protect hands and arms from cuts, abrasions, chemicals, burns, and punctures. The type of glove required will depend on the specific task and potential hazards involved. Examples include cut-resistant gloves, chemical-resistant gloves, and heat-resistant gloves.
5. Foot Protection: Steel-toe boots or safety shoes provide protection against falling objects, crushing hazards, and slips and trips. They should be fitted properly and have slip-resistant soles to prevent injuries due to falls or foot hazards, such as nails or sharp objects.
6. Respiratory Protection: Construction activities may generate dust, fumes, gases, or vapors that can be hazardous when inhaled. Respiratory protective equipment, such as dust masks, respirators, or supplied air systems, should be worn to protect against respiratory hazards and ensure clean air supply.
7. High Visibility Clothing: Construction sites often have heavy machinery and vehicles in operation, making it important for workers to be easily visible. High visibility clothing, such as reflective vests or jackets, helps improve visibility, especially in low-light conditions, reducing the risk of accidents due to poor visibility.
When it comes to PPE, it is essential to ensure that the equipment is properly selected, maintained, and used. Here are some key considerations:
1. Fit and Comfort: PPE should be well-fitted and comfortable to wear, allowing workers to move freely and perform their tasks without hindrance. Ill-fitting or uncomfortable PPE can result in reduced effectiveness or worker non-compliance.
2. Training and Education: Workers should be properly trained on the correct usage, maintenance, and limitations of PPE. They should understand when and how to use each type of equipment and how to store and care for it properly.
3. PPE Inspection: Regular inspection of PPE is crucial to ensure its effectiveness. Check for signs of wear, damage, or deterioration and replace any damaged or expired equipment. Encourage workers to report any concerns regarding the condition of their PPE.
4. PPE Storage: Proper storage of PPE is important to prevent damage and contamination. Provide designated storage areas that protect PPE from exposure to sunlight, chemicals, extreme temperatures, or crushing.
5. Compliance with Standards: PPE should meet relevant safety standards and regulations. Ensure that all PPE is certified and labeled accordingly to ensure its reliability and performance.
Personal Protective Equipment plays a crucial role in safeguarding workers from hazards in the construction industry. By providing and promoting the proper use of PPE, employers can create a safer working environment and reduce the risk of accidents and injuries.
Training and Education
Training and education are essential components of creating a culture of safety in the construction industry. Properly trained and knowledgeable workers are better equipped to identify hazards, understand safety procedures, and take preventive measures to mitigate risks. Effective training and education programs ensure that workers are equipped with the necessary skills and knowledge to work safely on construction sites. Here are some key aspects of training and education in the construction industry:
1. General Safety Training: All workers, regardless of their role or experience level, should receive general safety training before starting work on a construction site. This training should cover topics such as hazard recognition, proper use of personal protective equipment (PPE), emergency procedures, and safe work practices.
2. Task-Specific Training: Training should be provided for specific tasks or processes that require specialized knowledge or skills. For example, training might be needed for operating machinery, working at heights, handling hazardous materials, or performing specialized construction techniques. Task-specific training ensures that workers have the necessary expertise to carry out their responsibilities safely and efficiently.
3. Equipment Training: Proper training on the safe use, operation, and maintenance of construction equipment is essential. Workers should be familiar with the specific equipment they will be using, including any associated hazards and safety precautions. Training should include instructions on starting, stopping, and emergency procedures, as well as proper care and storage of equipment.
4. Ongoing Education: Safety education should be an ongoing process. Regular updates and refreshers on safety procedures, new regulations, and emerging hazards help workers stay up to date and maintain a high level of safety consciousness. Ongoing education can be provided through safety meetings, toolbox talks, workshops, and online resources.
5. Supervisor and Management Training: Training should not be limited to workers alone. Supervisors and managers play a pivotal role in ensuring a safe working environment. They should receive training on effective safety management, leadership techniques, hazard identification, incident reporting, and communication. Equipping supervisors and managers with the necessary knowledge allows them to effectively promote and enforce safety practices.
6. Site-Specific Training: Each construction site may have unique hazards and safety considerations. Site-specific training familiarizes workers with the specific hazards present at their worksite and the corresponding safety protocols. This helps workers understand the risks they may encounter and how to mitigate them effectively.
7. Evaluation and Assessment: Regular assessment of training effectiveness is crucial to ensure that workers are retaining and applying their knowledge. Implement evaluation methods, such as quizzes or practical demonstrations, to assess comprehension and identify any gaps that may require additional training or reinforcement.
8. Collaboration and Communication: Encourage open communication and collaboration on safety matters. Establish a culture where workers feel comfortable reporting safety concerns or near-miss incidents. Foster a team environment where information and best practices are shared, promoting a collective commitment to safety.
Training and education are investments in the well-being of workers and the overall success of construction projects. By providing comprehensive and ongoing training programs, construction companies can empower their workers with the necessary skills, knowledge, and confidence to work safely, reduce the risk of accidents, and create a safer working environment in the construction industry.
Always wear the proper personal protective equipment (PPE) on a construction site, including hard hats, safety glasses, and steel-toed boots to protect yourself from potential hazards.
Role of Employers in Ensuring Safety
Employers play a crucial role in ensuring the safety and well-being of workers on construction sites. They have a legal and moral obligation to provide a safe working environment and implement measures to prevent accidents and injuries. Here are some key responsibilities and actions that employers should take to prioritize safety:
1. Establishing a Safety Culture: Employers should foster a culture of safety within the organization, where safety is embedded in all aspects of the business. This involves setting clear safety goals and expectations, encouraging employee participation in safety initiatives, and recognizing and rewarding safe behaviors. Safety should be a top priority and integrated into all work processes and decision-making.
2. Developing and Implementing Safety Policies and Procedures: Employers should establish comprehensive safety policies and procedures that align with legal requirements and industry best practices. These policies should address hazard identification, risk assessment, emergency procedures, incident reporting, and preventive measures. Clear communication and training on these policies are essential.
3. Providing Resources and Training: Employers should allocate resources for effective safety programs, including training, education, and the provision of appropriate personal protective equipment (PPE). Training programs should be comprehensive, tailored to the specific needs of the workers, and regularly updated to reflect changes in regulations and new industry standards.
4. Conducting Regular Safety Inspections: Employers should conduct regular safety inspections to identify potential hazards, unsafe working conditions, or practices. Inspections should be carried out by qualified individuals who have a thorough understanding of construction safety requirements. Identified issues should be addressed promptly to ensure a safe working environment.
5. Engaging in Hazard Prevention and Control: Employers should proactively identify and control hazards in the workplace. This may involve implementing engineering controls, such as installing guardrails or safety barriers, using safer equipment and materials, or modifying work processes to minimize risks. Regular monitoring and evaluation of control measures are necessary to maintain an effective hazard prevention system.
6. Promoting Worker Involvement and Communication: Employers should encourage worker involvement in safety matters by providing platforms for workers to voice their concerns and suggestions. Regular safety meetings, toolbox talks, and open-door policies foster effective communication between management and workers. Employers should also establish incident reporting procedures and investigate all reported incidents to identify root causes and prevent future occurrences.
7. Ensuring Compliance with Legal Requirements and Regulations: Employers must stay updated with the latest legal requirements and regulations pertaining to construction safety. They should ensure compliance with these standards and enforce safe work practices throughout the organization. Failure to comply with legal requirements can result in legal consequences, fines, and damage to the company’s reputation.
8. Continuous Improvement and Training: Employers should strive for continuous improvement in safety performance. This involves regularly reviewing and evaluating safety programs, conducting safety audits, and seeking feedback from workers. Learning from incidents and near-misses helps in identifying areas for improvement and implementing necessary corrective actions.
Employers have a significant responsibility in ensuring the safety of their workers. By prioritizing safety, creating a culture of safety, providing appropriate resources and training, and actively managing hazards, employers can protect their most valuable asset – their workers – and establish a strong foundation for successful construction projects.
Role of Employees in Maintaining Safety
While employers have a primary responsibility for ensuring safety in the workplace, employees also play a crucial role in maintaining a safe working environment. Workers have a responsibility to follow safety protocols, recognize hazards, and actively contribute to the overall safety culture. Here are some key responsibilities and actions that employees should take to prioritize safety:
1. Familiarize themselves with Safety Policies and Procedures: Employees should thoroughly read and understand the safety policies and procedures established by the employer. This includes knowing the correct use of personal protective equipment (PPE), emergency procedures, and reporting mechanisms for incidents or hazards.
2. Participate in Safety Training and Education: Employees should actively engage in safety training and education programs provided by the employer. This includes attending safety meetings, toolbox talks, and workshops to enhance their knowledge and skills in hazard recognition, risk assessment, and safe work practices.
3. Adhere to Safe Work Practices: Employees should consistently follow safe work practices and procedures established by the employer. This includes using the correct tools and equipment for the task at hand, operating machinery in accordance with safety guidelines, and properly storing and handling materials to prevent accidents or injuries.
4. Use Personal Protective Equipment (PPE) Appropriately: Employees must wear and use appropriate PPE as directed by the employer. This includes wearing safety helmets, goggles, gloves, ear protection, and high-visibility clothing when necessary. PPE should be worn consistently and properly maintained to ensure its effectiveness.
5. Report Hazards and Safety Concerns: Employees should actively report any hazards or safety concerns they observe in the workplace to their supervisors or safety representatives. This could include identifying unsafe conditions, malfunctioning equipment, or potential hazards that could lead to accidents. Timely reporting allows for prompt action and preventive measures.
6. Engage in Communication and Collaboration: Employees should actively participate in safety communication and collaboration efforts. This involves sharing valuable safety insights, suggestions for improvement, and lessons learned from near-miss incidents. Effective communication helps create a culture of safety and promotes continuous improvement.
7. Practice Good Housekeeping: Maintaining a clean and organized work area is essential for preventing accidents and injuries. Employees should keep their workspaces clear of clutter, materials, and obstructions. Additionally, they should promptly clean up spills, debris, or any other potential hazards, reporting any maintenance or cleanliness issues to the appropriate personnel.
8. Support and Comply with Safety Inspections: Employees should cooperate during safety inspections conducted by management or external agencies. They should actively participate and provide accurate information regarding safety practices, potential hazards, and any necessary corrective actions. Employees should view inspections as opportunities to improve workplace safety.
9. Take Responsibility for Personal Safety: Each employee should take personal responsibility for their own safety and the safety of their coworkers. This involves being mindful of their actions, following safety procedures without taking shortcuts, and encouraging others to prioritize safety. Each individual must actively contribute to a safe working environment.
Employees play a vital role in maintaining safety at the workplace. By adhering to safety policies and procedures, using PPE correctly, reporting hazards, and actively participating in safety efforts, employees contribute to a culture of safety, protecting themselves and their colleagues from accidents and injuries.
Read more: What Is Construction
Safety Inspections and Audits
Safety inspections and audits are essential components of maintaining a safe working environment in the construction industry. These processes involve systematic and thorough evaluations of the workplace to identify potential hazards, assess safety practices, and ensure compliance with safety regulations and standards. Here are some key aspects of safety inspections and audits:
1. Purpose of Safety Inspections and Audits: Safety inspections and audits serve multiple purposes, including:
- Identifying potential hazards and risks in the workplace
- Evaluating the effectiveness of safety policies and procedures
- Assessing compliance with legal requirements and industry standards
- Identifying areas for improvement and implementing corrective actions
- Promoting a culture of safety and accountability
- Preventing accidents, injuries, and property damage
2. Regularity and Frequency: Safety inspections and audits should be conducted on a regular basis, depending on the size and complexity of the construction project. They can occur daily, weekly, monthly, or at specific project milestones. Regular inspections ensure that hazardous conditions or unsafe practices are promptly identified and addressed.
3. Conducting Inspections: Inspections should be carried out by qualified individuals who have a good understanding of construction safety requirements. Inspectors may include dedicated safety officers, supervisors, or external consultants. Inspections should cover all areas of the construction site, including work areas, equipment, materials storage, access routes, and welfare facilities.
4. Inspection Checklist: An inspection checklist is a helpful tool to ensure thoroughness and consistency during inspections. The checklist should include items relating to hazard identification, compliance with safety regulations, availability and condition of personal protective equipment (PPE), housekeeping practices, and proper handling and storage of materials and equipment.
5. Documentation and Reporting: Safety inspections and audits should be properly documented, including findings, corrective actions, and recommendations. Report any hazardous conditions or safety violations to management or site supervisors. Ensure that all relevant employees and stakeholders have access to inspection reports to facilitate continuous improvement and accountability.
6. Implementing Corrective Actions: It is essential to implement prompt and effective corrective actions following safety inspections and audits. Any identified hazards or deficiencies should be addressed and resolved as quickly as possible. This may involve providing additional training, improving signage, repairing or replacing equipment, or updating safety procedures.
7. Continuous Monitoring and Improvement: Safety inspections and audits are not one-time events. They should be part of an ongoing process of continuous monitoring and improvement. Regularly reassess the effectiveness of safety measures, track progress, and analyze trends to identify recurring issues or emerging risks. Actively involve workers in the improvement process through open communication and feedback mechanisms.
8. External Audits and Certifications: In addition to internal inspections and audits, construction companies may undergo external audits or seek certifications to validate their commitment to safety. These audits may be performed by regulatory agencies, certification bodies, or clients to ensure compliance with specific safety standards or contractual requirements.
Safety inspections and audits are critical tools in maintaining a safe and compliant working environment. By conducting regular evaluations, addressing identified hazards, and continuously improving safety practices, construction companies can minimize risks, prevent accidents, and protect the well-being of their workers.
Reporting and Investigating Incidents
Reporting and investigating incidents is a crucial part of maintaining safety in the construction industry. Accidents, near-misses, and other incidents should be promptly reported, thoroughly investigated, and appropriate corrective actions implemented to prevent similar incidents from occurring in the future. Here are some key aspects of reporting and investigating incidents:
1. Incident Reporting: Encourage all workers to report any incidents, accidents, injuries, or near-miss events, regardless of their severity. Establish a reporting system that makes it easy for workers to report incidents, ensuring their confidentiality and protection from retaliation. Timely reporting allows for prompt action and investigation.
2. Immediate Response: Upon receiving an incident report, provide immediate first aid, medical assistance, or necessary emergency response as required. Ensure the well-being and safety of those involved and secure the area to prevent further incidents or injuries.
3. Incident Investigation Team: Assign a competent investigation team consisting of personnel with experience and knowledge in construction safety practices. The team should be trained in incident investigation techniques and should have no prior involvement in the incident being investigated.
4. Investigation Process: The investigation process should be conducted promptly, preferably within 24 hours of the incident occurrence. It involves gathering factual information, interviewing witnesses and involved parties, collecting evidence, and analyzing the root causes of the incident.
5. Root Cause Analysis: A thorough root cause analysis is essential to identify the underlying factors that contributed to the incident. This involves looking beyond immediate causes and examining systemic issues, such as equipment failures, lack of training, inadequate supervision, or flawed work processes. Identifying root causes helps prevent similar incidents from happening again in the future.
6. Corrective Actions: Based on the findings of the incident investigation, develop and implement appropriate corrective actions. These actions should address the identified root causes and eliminate or minimize the risks associated with similar incidents. Corrective actions may include revising safety procedures, providing additional training, improving equipment maintenance, or enhancing supervision.
7. Documentation: Document all aspects of the incident, investigation, and corrective actions taken. Maintain accurate records of incident reports, witness statements, investigation findings, and the implementation of corrective actions. This documentation helps track trends, monitor progress, and demonstrate compliance with legal requirements.
8. Communication and Learning: Communicate the investigation findings and the implemented corrective actions to all workers, management, and stakeholders. Establish a culture of learning from incidents, promoting open communication about lessons learned, and sharing best practices. Encourage workers to actively contribute to incident prevention through their insights and suggestions.
9. Continuous Improvement: Incident investigations should lead to continuous improvement in safety practices. Regularly assess the effectiveness of corrective actions, monitor trends, and update safety procedures accordingly. Incorporate incident investigation findings into safety training programs to raise awareness and prevent similar incidents in the future.
Reporting and investigating incidents are critical components of a proactive safety program in the construction industry. By encouraging incident reporting, conducting thorough investigations, implementing effective corrective actions, and fostering a learning culture, construction companies can prevent future incidents, protect their workers, and create a safer working environment.
Continuous Improvement in Construction Safety
Continuous improvement is a fundamental concept in construction safety that involves ongoing efforts to enhance safety practices, prevent accidents, and create a culture of safety excellence. By consistently evaluating and refining safety processes, construction companies can achieve higher levels of safety performance and better protect the well-being of their workers. Here are some key aspects of continuous improvement in construction safety:
1. Learning from Incidents: Incidents, accidents, and near-misses provide valuable opportunities for learning and improvement. Conduct thorough investigations of incidents to identify root causes and underlying systemic issues. Use this knowledge to develop and implement corrective actions that address the identified causes and prevent similar incidents from occurring in the future.
2. Tracking Safety Metrics: Establish key safety performance indicators (KPIs) and metrics to track and measure safety performance. Monitor metrics such as incident rates, near-miss reports, compliance with safety procedures, and training completion rates. Regularly analyze and evaluate these metrics to identify areas for improvement and measure the effectiveness of implemented safety initiatives.
3. Proactive Risk Assessments: Conduct regular risk assessments and hazard identification to proactively identify potential hazards and associated risks. This allows for the implementation of appropriate control measures to minimize or eliminate these risks. Regularly review and update risk assessments as conditions change throughout the construction project.
4. Engaging Workers: Encourage active worker involvement in safety initiatives and provide opportunities for workers to contribute to the development and improvement of safety programs. Workers are often closest to the hazards and can provide invaluable insights and suggestions for improvement. Foster a culture where workers feel comfortable reporting safety concerns, contributing to safety discussions, and actively participating in safety inspections and committees.
5. Regular Safety Training and Education: Safety training should not be a one-time event but an ongoing process. Provide regular training and awareness programs on safety procedures, hazard recognition, and safe work practices. Keep workers informed about the latest industry standards, regulations, and best practices to ensure they are equipped with the knowledge and skills needed to work safely.
6. Reviewing Safety Procedures and Policies: Regularly review and update safety procedures and policies to ensure they are up to date, aligned with legal requirements, and reflect best industry practices. Seek input from workers and supervisors who are directly involved in the work processes and incorporate their feedback into the development and improvement of safety procedures.
7. Promoting Communication and Collaboration: Effective communication and collaboration among all levels of the organization are essential for continuous improvement in safety. Promote open dialogue, encourage workers to share safety insights, lessons learned, and best practices. Regular safety meetings, toolbox talks, and safety forums can facilitate communication and foster a collective responsibility for safety.
8. Implementing Safety Incentives and Recognition: Recognize and reward individuals or teams that demonstrate exemplary commitment to safety. Incentives can motivate workers to actively engage in safety initiatives and maintain a high level of safety awareness. Publicly acknowledge safety achievements and use success stories as examples to inspire others.
9. External Benchmarking and Industry Collaboration: Look beyond the organization and industry for inspiration and ideas. Engage in external benchmarking to compare safety practices with other construction companies and industries. Collaborate with industry associations, regulatory bodies, and safety professionals to share knowledge, learn from best practices, and stay updated on emerging safety trends.
Continuous improvement in construction safety is an ongoing process that requires commitment, collaboration, and a proactive approach. By learning from incidents, tracking safety metrics, engaging workers, reviewing procedures, and fostering a culture of communication, construction companies can continuously enhance their safety performance and create a safer working environment for all.
Conclusion
Safety is of paramount importance in the construction industry. It is not just a legal obligation but also a moral responsibility of employers, contractors, and workers. Building a strong safety culture and implementing effective safety measures and procedures is crucial to protect the well-being of construction workers, prevent accidents, and ensure the successful completion of projects.
Throughout this article, we have explored various aspects of construction safety, including the importance of safety, legal requirements and regulations, common hazards, personal protective equipment (PPE), training and education, the roles of employers and employees, safety inspections and audits, incident reporting and investigation, and continuous improvement.
Construction companies must prioritize safety by establishing a culture where safety is at the forefront of all operations. Employers must fulfill their responsibilities by providing resources, training programs, and safety policies while complying with legal requirements and fostering a safe working environment. Employees also play a vital role by following safety procedures, using appropriate PPE, reporting hazards, and actively participating in safety initiatives.
Safety inspections, audits, incident reporting, and investigations are essential processes that help identify hazards, assess compliance, uncover root causes, and implement corrective actions. Through continuous improvement efforts, construction companies can enhance safety practices, proactively identify and address risks, and foster a culture of ongoing learning and improvement.
By prioritizing safety, construction companies can protect workers from potential harm, enhance productivity, minimize financial losses, meet legal obligations, uphold a positive reputation, and ensure the successful completion of projects. Remember, construction safety is a collective effort that requires the commitment and collaboration of everyone involved. Together, we can build a safer construction industry for all.
Frequently Asked Questions about What Is Safety In Construction
Was this page helpful?
At Storables.com, we guarantee accurate and reliable information. Our content, validated by Expert Board Contributors, is crafted following stringent Editorial Policies. We're committed to providing you with well-researched, expert-backed insights for all your informational needs.
0 thoughts on “What Is Safety In Construction”