Home>diy>Building & Construction>What Is The Modern Method Of Construction?
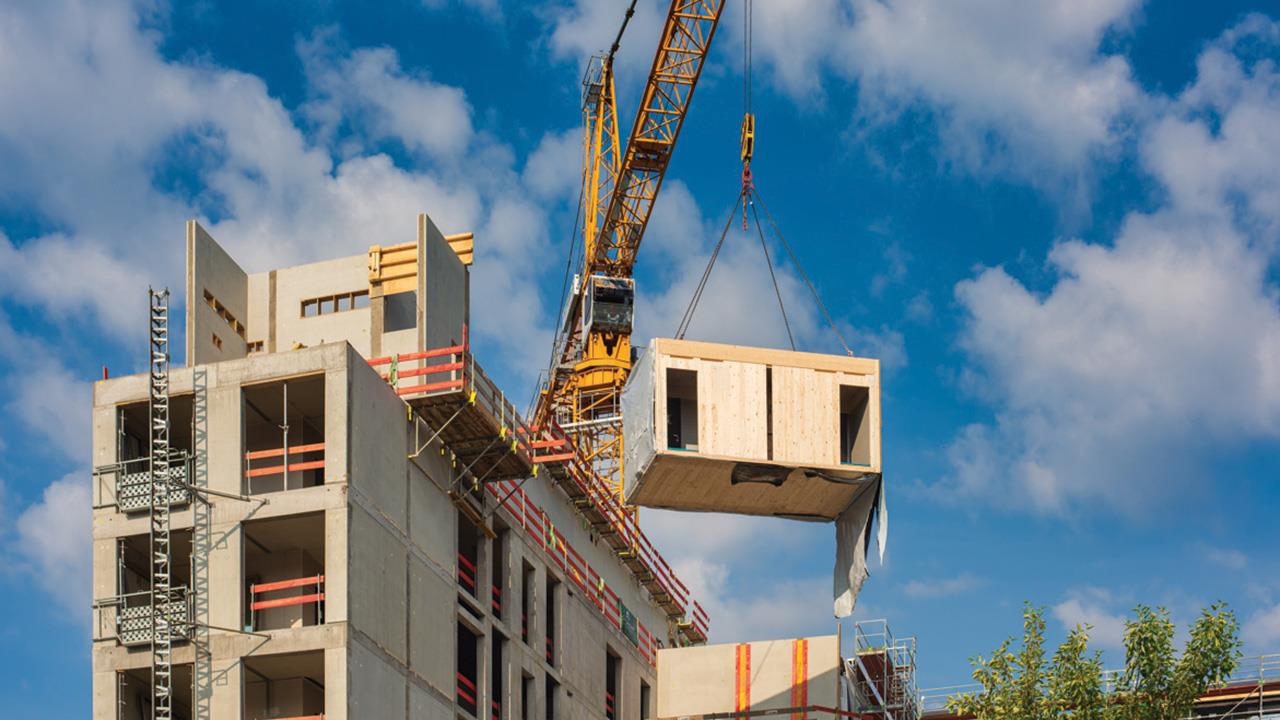
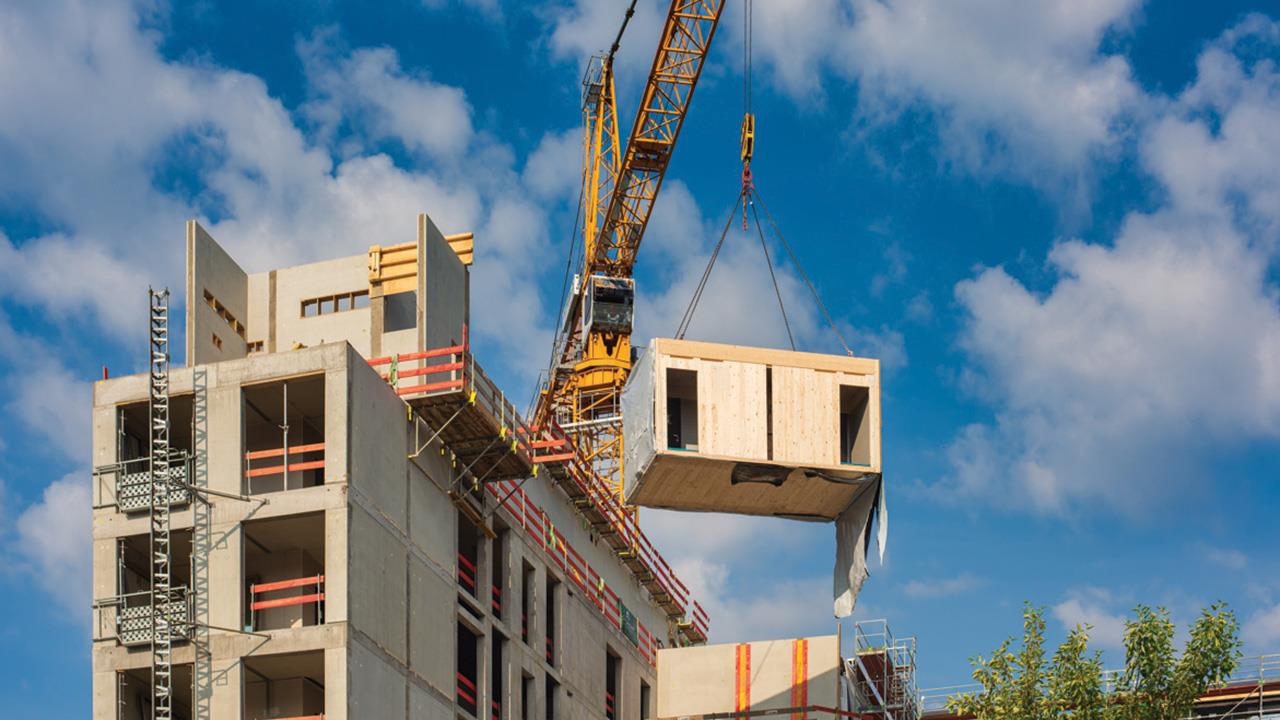
Building & Construction
What Is The Modern Method Of Construction?
Modified: January 6, 2024
Discover the modern method of construction and how it revolutionizes building and construction industry. Explore the benefits and techniques behind this innovative approach in building-construction.
(Many of the links in this article redirect to a specific reviewed product. Your purchase of these products through affiliate links helps to generate commission for Storables.com, at no extra cost. Learn more)
Introduction
Construction is an ever-evolving industry, constantly adopting new methods and technologies to improve efficiency, sustainability, and cost-effectiveness. One such advancement is the Modern Method of Construction (MMC) which has gained popularity in recent years. MMC refers to the use of innovative techniques, materials, and processes to construct buildings offsite, resulting in faster construction times, reduced waste generation, and enhanced quality control.
This article aims to delve into the world of Modern Method of Construction, exploring its different types, advantages, challenges, and its future outlook in the construction industry.
So, let’s buckle up and take a deeper look into the fascinating world of Modern Method of Construction!
Key Takeaways:
- Modern Method of Construction (MMC) revolutionizes the industry with offsite techniques, offering faster construction, enhanced quality control, reduced waste, and design flexibility. Collaboration and training are vital for overcoming challenges and maximizing MMC’s potential.
- The future of MMC looks promising, driven by technological advancements, sustainability, scalability, collaboration, and workforce development. MMC offers efficient, sustainable, and customizable solutions, shaping a greener future for construction.
Definition of Modern Method of Construction (MMC)
The Modern Method of Construction (MMC) refers to a range of construction techniques that utilize innovative processes, materials, and technologies to create buildings more efficiently and sustainably than traditional construction methods. The key distinguishing feature of MMC is the emphasis on offsite construction, where components or modules of a building are manufactured in a controlled factory environment and then transported to the construction site for assembly.
MMC has gained traction as a viable alternative to traditional construction due to its numerous benefits. By shifting parts of the construction process to the controlled environment of a factory, MMC allows for increased precision, quality control, speed of construction, and reduction of waste. The use of standardized components and prefabricated elements further streamlines the construction process while reducing reliance on skilled labor.
Furthermore, MMC allows for greater design flexibility as it enables the creation of bespoke, customized components that can be seamlessly integrated into the building structure. This flexibility extends to various construction types, from residential homes and commercial buildings to educational facilities and healthcare structures.
It is important to note that MMC is not a one-size-fits-all approach. Instead, it encompasses a range of techniques that can be tailored to specific project requirements. From offsite construction and hybrid construction to panelized construction and volumetric construction, each method offers its own unique advantages and considerations.
Advantages of MMC
The adoption of Modern Method of Construction (MMC) brings forth numerous advantages that make it an attractive option for builders, developers, and clients alike. Let’s explore some of the key benefits:
- Improved Construction Speed: MMC techniques enable faster construction times compared to traditional methods. With offsite construction, the simultaneous manufacturing of building components and site preparation can significantly reduce project timelines. This not only leads to early project completion but also allows for quicker occupancy or utilization of the building.
- Enhanced Quality Control: Building components manufactured offsite undergo strict quality control measures before they are transported to the construction site. As a result, there is improved consistency in the manufacturing process and reduced risk of quality issues. The controlled factory environment also minimizes the impact of adverse weather conditions, ensuring higher quality construction.
- Reduced Waste and Environmental Impact: MMC promotes sustainable construction practices by reducing waste generation and minimizing the environmental impact. The use of precise cutting and manufacturing techniques minimizes on-site wastage, and the ability to recycle or repurpose components further reduces waste sent to landfills. Additionally, the controlled factory environment allows for better energy efficiency and waste management.
- Cost Efficiency: While the upfront cost of MMC might be slightly higher compared to traditional construction, the long-term cost savings are significant. The reduced construction time and increased quality control lead to lower maintenance and repair costs over the life cycle of the building. Moreover, the faster completion time translates into earlier revenue generation for developers.
- Flexibility and Customization: MMC offers design flexibility and customization options. With the ability to create bespoke components, buildings can be tailored to meet specific requirements and architectural visions. This flexibility extends to various building types and designs, allowing for innovative and creative solutions.
These advantages have made MMC an appealing choice for projects ranging from residential homes to large-scale commercial buildings. The ability to deliver high-quality buildings efficiently and sustainably has positioned MMC as a frontrunner in the construction industry.
Types of Modern Method of Construction
The Modern Method of Construction (MMC) encompasses various techniques that can be employed to construct buildings more efficiently and sustainably. Let’s explore some of the different types of MMC:
- Offsite Construction: Offsite construction involves the manufacturing of various building components, such as walls, floors, and roof panels, in a factory-controlled environment. These components are then transported to the construction site for assembly. Offsite construction can significantly reduce on-site labor requirements, minimize construction time, and enhance quality control.
- Hybrid Construction: Hybrid construction combines elements of both offsite and on-site construction. In this method, some building components are manufactured offsite, while others are constructed on-site. This approach offers flexibility, allowing for the use of both standard and custom components. Hybrid construction enables faster assembly on-site while still benefiting from the precision and quality control of offsite manufacturing.
- Panelized Construction: Panelized construction involves the fabrication of large panels offsite, typically consisting of pre-engineered walls, floors, and roofs. These panels are then transported to the construction site and assembled to form the building structure. Panelized construction allows for efficient transportation and installation, ensuring faster construction times and improved quality control.
- Volumetric Construction: Volumetric construction, also known as modular construction, takes the concept of offsite manufacturing to the next level. In this method, entire modular units or “modules” are manufactured in a controlled factory environment. These modules, complete with interior finishes, plumbing, electrical, and even furniture, are then transported to the site and assembled to create the final building. Volumetric construction offers rapid construction, reduced on-site labor, and high-quality finishes.
It’s important to note that these types of MMC are not mutually exclusive and can be combined or customized to suit specific project requirements. The choice of MMC method depends on factors such as project size, budget, location, and desired level of customization.
Now that we have explored the various types of MMC, let’s move on to examine the benefits and challenges associated with these construction techniques.
Offsite Construction
Offsite construction is a prominent type of Modern Method of Construction (MMC) that involves the manufacturing of building components in a factory-controlled environment before transporting them to the construction site for assembly. This method offers several advantages over traditional on-site construction, making it increasingly popular in the industry.
Offsite construction follows a systematic process: first, the building design is translated into detailed manufacturing drawings. Then, the components, such as walls, floors, roofs, and even entire room modules, are precision-engineered and assembled in the factory using specialized machinery and skilled labor. The completed components are then delivered to the construction site, where they are swiftly assembled to form the final structure.
There are several key advantages to offsite construction:
- Speed and Efficiency: Offsite construction significantly reduces the construction time compared to traditional methods. The parallel processes of manufacturing components in a controlled factory environment and preparing the construction site result in faster project completion and quicker occupancy.
- Quality Control: One of the biggest advantages of offsite construction is the improved quality control. Manufactured components undergo rigorous quality checks at every stage of the production process, ensuring consistency, precision, and adherence to industry standards. The controlled factory environment minimizes the risk of errors and defects caused by adverse weather conditions, ensuring a high-quality end product.
- Reduced Disruption: Offsite construction minimizes disruption to the surrounding community and the construction site. With the majority of manufacturing processes taking place offsite, noise, dust, and traffic disturbances are significantly reduced, resulting in a more pleasant construction experience for all parties involved.
- Sustainability: Offsite construction promotes sustainability by minimizing waste generation. The controlled factory environment allows for precise material usage, reducing onsite wastage. Furthermore, any waste that is generated during the manufacturing process can be recycled or repurposed, contributing to a cleaner and greener construction industry.
- Flexibility and Customization: Offsite construction techniques offer design flexibility and customization options. Components can be manufactured to precise specifications, allowing for bespoke solutions to meet specific project requirements. This flexibility extends to architectural designs, as offsite construction can accommodate a wide range of building styles and aesthetics.
While offsite construction brings numerous benefits, it’s important to be aware of the challenges it may present. These include transportation costs, logistical considerations, site access limitations, and the need for careful coordination between the offsite manufacturing facility and the onsite assembly team.
Overall, offsite construction is revolutionizing the construction industry, offering faster construction times, enhanced quality control, and improved sustainability. With the continued advancement of technology and manufacturing techniques, offsite construction is set to play a vital role in shaping the future of the construction industry.
Read more: What Is Modern Style Home Decor
Hybrid Construction
Hybrid construction is a type of Modern Method of Construction (MMC) that combines elements of both offsite and on-site construction methods. It offers a flexible approach that allows for the use of both standardized and customized components, offering the best of both worlds in terms of efficiency and customization.
In hybrid construction, certain building components are manufactured offsite in a factory-controlled environment, while others are constructed on-site. This approach allows for the advantages of offsite construction, such as enhanced quality control and reduced construction time, while also providing the flexibility to cater to unique project requirements.
The offsite manufactured components in hybrid construction generally include elements that can be efficiently produced and transported to the construction site. These components can include walls, floors, roofs, and pre-engineered structural elements. By manufacturing these components ahead of time, construction time on-site is significantly reduced, resulting in faster project completion.
The on-site construction aspect of hybrid construction often involves the assembly and integration of the offsite-manufactured components along with other on-site construction activities. This includes the installation of electrical and plumbing systems, finishing works, and the connection of utilities.
The advantages of hybrid construction are numerous:
- Faster Assembly: Hybrid construction allows for the quick assembly of offsite-manufactured components on-site, reducing construction time compared to traditional on-site methods. This can result in earlier project completion and faster occupancy of the building.
- Quality Control: Components manufactured in a controlled factory environment undergo strict quality control measures, ensuring consistency and adherence to standards. The integration of these high-quality components with on-site construction activities enhances overall quality control.
- Flexibility: Hybrid construction offers flexibility in design and customization. Standardized components can be utilized alongside custom-made elements, allowing for architectural creativity and the incorporation of unique design features.
- Cost-Effective: Hybrid construction strikes a balance between the cost efficiencies achieved through offsite manufacturing and the cost-saving potential of on-site construction. The use of standardized components can reduce material costs, while on-site labor can be optimized for maximum efficiency.
- Reduced Site Disruption: Similar to other MMC methods, hybrid construction minimizes the disruption typically associated with traditional on-site construction. With some portions of the project being manufactured offsite, noise, dust, and other disturbances are reduced, creating a more pleasant and efficient construction experience for all stakeholders.
Hybrid construction offers a versatile solution that combines the benefits of offsite construction and on-site construction. This method is particularly suitable for projects that require a balance between customization and efficiency, making it a popular choice across various construction sectors.
As the construction industry continues to embrace MMC techniques, hybrid construction is expected to see increased adoption and further refinement, contributing to improved construction practices and enhanced project outcomes.
Panelized Construction
Panelized construction is a type of Modern Method of Construction (MMC) that involves the offsite fabrication of large panels, which are then transported to the construction site for assembly. These panels typically consist of pre-engineered walls, floors, and roofs, and are manufactured in a controlled factory environment.
In panelized construction, the manufacturing process begins with the creation of detailed designs and specifications. These designs are then translated into manufacturing drawings, ensuring precise and accurate fabrication of the panels. The construction materials, such as timber, steel, or concrete, are cut and assembled according to the design specifications, incorporating windows, doors, insulation, and other necessary components.
Once the panels are complete, they are transported to the construction site and swiftly assembled, with connections and seals applied to ensure structural integrity and weather resistance. Depending on the complexity of the project, panelized construction can be used for both residential and commercial buildings.
The advantages of panelized construction are numerous:
- Speed and Efficiency: Panelized construction can significantly reduce construction time compared to traditional on-site building methods. The offsite fabrication of panels allows for parallel processes—while site preparation is underway, panels are being manufactured concurrently. This results in faster project completion and reduced labor requirements on-site.
- Quality Control: Manufacturing panels in a controlled factory environment allows for enhanced quality control. The precision-cut components, standardized assembly procedures, and strict quality checks ensure consistent and high-quality panels. This can result in improved overall building quality and durability.
- Design Flexibility: Panelized construction offers design flexibility and customization options. The panels can be tailored to meet specific architectural requirements, allowing for various finishes, aesthetics, and configurations. This flexibility enables the creation of unique and customized buildings to suit individual project needs.
- Reduced Waste: Panelized construction minimizes on-site waste generation. The panels are manufactured with precise measurements, reducing the need for on-site cutting and waste material. Additionally, any waste generated during the panel manufacturing process can be recycled or repurposed, contributing to a more sustainable construction approach.
- Simplified On-Site Construction: With panelized construction, on-site assembly is streamlined and simplified. The pre-engineered panels fit together with accuracy, reducing the need for complex on-site construction processes. This can result in faster assembly times, improved logistics, and reduced labor costs.
Panelized construction offers a balance between efficiency, quality, and customization. The standardized nature of the panels combined with the design flexibility allows for cost-effective yet unique building solutions. Additionally, the reduction in on-site labor and waste generation contribute to a more sustainable construction process.
As MMC continues to gain momentum in the construction industry, panelized construction is becoming an increasingly popular choice for projects that prioritize speed, quality, and design flexibility. Its benefits align with the goals of modern construction practices, making it a valuable technique in the pursuit of more sustainable and efficient building methods.
Volumetric Construction
Volumetric construction, also known as modular construction, is an innovative type of Modern Method of Construction (MMC) that involves the manufacturing of entire modular units or “modules” in a controlled factory environment. These modules are then transported to the construction site where they are assembled to create the final building structure.
In volumetric construction, each module is a complete and self-contained unit that encompasses various elements of a building including walls, floors, ceilings, electrical and plumbing systems, and even interior finishes. The modules can be manufactured using a variety of materials such as timber, steel, or concrete, depending on project requirements.
The process of volumetric construction begins with detailed design and engineering drawings. Once the design is finalized, the modules are manufactured offsite using advanced machinery and skilled labor. The manufacturing process follows controlled processes ensuring consistency, quality, and precision in every module.
After the completion of manufacturing, the modules are transported to the construction site where they are assembled to form the final structure. The modules are carefully connected and sealed to ensure structural integrity, durability, and weather resistance. The interior finishes, such as flooring, fixtures, and fittings, are also installed during the assembly process.
Volumetric construction brings several advantages to the construction industry:
- Rapid Construction: Volumetric construction significantly reduces construction time compared to traditional on-site building methods. While modules are being manufactured offsite, site preparation work can proceed simultaneously, allowing for parallel processes and faster project completion.
- Quality Control: Manufacturing modules in a controlled factory environment ensures strict quality control measures are implemented throughout the production process. The modules undergo rigorous inspections, ensuring consistent high-quality construction, and minimizing the risk of errors or defects often associated with on-site construction.
- Flexibility and Customization: Volumetric construction offers design flexibility and customization options. The modules can be tailored to meet specific project requirements, allowing for various configurations, sizes, and styles. This flexibility enables the creation of unique and bespoke buildings to suit individual needs.
- Reduced Disruption: Volumetric construction minimizes disruption to the construction site and the surrounding environment. The majority of the manufacturing process occurs offsite, resulting in less noise, dust, and traffic disturbances typically associated with on-site construction. This makes it particularly suitable for projects located in sensitive or densely populated areas.
- Sustainability: The controlled factory environment in volumetric construction allows for precise material usage, minimizing waste generation. Additionally, the offsite manufacturing process enables better energy efficiency, reducing the carbon footprint associated with on-site construction activities.
Volumetric construction has gained popularity for a wide range of building types, including residential homes, hotels, student accommodations, and healthcare facilities. Its benefits in terms of speed, quality, and sustainability make it an appealing choice for projects aiming for efficient and cost-effective construction solutions.
As the construction industry continues to advance, volumetric construction is expected to play a significant role in shaping the future of building practices. Its offsite manufacturing process and modular approach offer numerous advantages, making it an excellent choice for those seeking innovative and sustainable construction methods.
Benefits and Challenges of MMC
The Modern Method of Construction (MMC) offers a range of benefits that make it an attractive choice for the construction industry. However, like any construction method, it also presents certain challenges. Let’s explore the benefits and challenges of MMC:
Read more: What Is Pre-Construction In Construction
Benefits of MMC:
- Efficiency and Time Savings: MMC techniques, such as offsite construction and modular construction, allow for faster construction times compared to traditional methods. The controlled factory environment and parallel processes enable simultaneous manufacturing and site preparation, resulting in quicker project completion and earlier occupancy.
- Improved Quality Control: The offsite manufacturing process in MMC enables stringent quality control measures at every stage. Components are manufactured under controlled conditions, reducing the risk of errors and ensuring high-quality construction. This results in better overall building quality and durability.
- Sustainability and Reduced Waste: MMC promotes sustainability by reducing waste generation. The precision manufacturing process minimizes on-site wastage, and any waste produced during offsite manufacturing can be recycled or repurposed, leading to a greener construction approach. Additionally, the controlled factory environment allows for better energy efficiency and waste management.
- Flexibility and Customization: MMC techniques offer design flexibility and customization options. Builders can fabricate components and modules to precise specifications, allowing for bespoke solutions to suit unique project requirements. This flexibility extends to architectural designs, enabling a wide range of building styles and aesthetics.
- Reduced Site Disruption: MMC minimizes disruptions to the construction site and surrounding areas. With a significant portion of the construction process taking place offsite, noise, dust, and traffic disturbances are reduced. This leads to a more efficient and less disruptive construction experience.
Challenges of MMC:
- Transportation and Logistics: Transporting components or modules from the offsite manufacturing facility to the construction site can be a logistical challenge. Ensuring timely and efficient delivery while minimizing damage during transportation requires careful planning and coordination.
- Site Access and Assembly: Some construction sites may have limitations in terms of space and accessibility, which can pose challenges during the assembly of offsite manufactured components. Proper site planning and coordination between the offsite manufacturing facility and the on-site assembly team are crucial to overcome these challenges.
- Skilled Labor: While MMC techniques reduce the reliance on skilled on-site labor, they require skilled labor at offsite manufacturing facilities. Acquiring and retaining a skilled workforce proficient in MMC techniques can be a challenge, especially in regions where such techniques are less common or unfamiliar.
- Upfront Investment: Adopting MMC often requires an initial investment in specialized equipment, factory setup, and training. While the long-term cost savings may outweigh the upfront costs, builders and developers need to carefully assess the financial implications and feasibility of implementing MMC methods.
- Regulations and Building Codes: MMC may face challenges related to local regulations and building codes. Depending on specific requirements and regulations in different regions, it may be necessary to obtain approvals and certifications for the use of MMC techniques, which can add complexity and time to project timelines.
Addressing these challenges requires collaboration between project stakeholders, investment in training and skill development, and the establishment of supportive regulations and standards. By doing so, the construction industry can fully leverage the benefits of MMC while mitigating its inherent challenges.
Case Studies of Successful MMC Projects
To showcase the success and potential of Modern Method of Construction (MMC), let’s explore a few notable case studies where MMC techniques have been effectively implemented:
1. Lendlease’s Barangaroo South, Sydney, Australia:
Barangaroo South, a large-scale urban regeneration project in Sydney, Australia, utilized MMC to construct several buildings. Through the use of offsite construction, the project achieved impressive construction speed and quality control. Precast façade panels and pre-finished bathroom pods were manufactured offsite and seamlessly integrated into the buildings, resulting in faster assembly and improved overall building quality. This MMC approach helped the project meet tight deadlines while maintaining high standards of design and construction.
Read more: What Is Construction
2. Swan Housing Association’s Watts Grove, London, UK:
Watts Grove, a residential development in London, UK, showcased the efficiency and sustainability benefits of MMC. The project employed panelized construction techniques, with pre-fabricated wall, floor, and roof panels manufactured offsite. This approach significantly reduced on-site construction time, minimized wastage, and enhanced project sustainability. The use of MMC enabled faster completion of the development, meeting the growing demand for affordable housing in the city.
3. Broad Sustainable Building’s Mini Sky City, Changsha, China:
Mini Sky City in Changsha, China, is a 57-story tower that gained international attention for its record-breaking construction speed. The project employed volumetric construction, with complete modular units manufactured offsite and then stacked and interconnected on-site. This approach enabled the tower to be constructed at an astonishing rate of three floors per day. By utilizing MMC, the project significantly reduced labor requirements, increased construction efficiency, and demonstrated the potential of modular construction on a large scale.
4. Blok’s Fynblok, Cape Town, South Africa:
Fynblok, a residential development in Cape Town, South Africa, utilized MMC to address the housing shortage in the region. The project employed hybrid construction techniques, combining offsite-manufactured components with traditional on-site construction. This approach allowed for faster assembly on-site while still maintaining design flexibility and the ability to customize each unit to suit individual buyers’ needs. The use of MMC played a crucial role in delivering affordable and high-quality housing to the local community.
These case studies highlight the successful implementation of MMC techniques in diverse projects, showcasing the advantages of speed, quality control, sustainability, and flexibility offered by MMC. As MMC continues to evolve and gain recognition in the construction industry, these projects serve as inspiration and benchmarks for future MMC initiatives worldwide.
Future Outlook of Modern Method of Construction
The future of the construction industry is undoubtedly intertwined with the widespread adoption and further development of Modern Method of Construction (MMC) techniques. As technology continues to advance, MMC is poised to play a significant role in shaping the future of building practices. Here are some key aspects to consider regarding the future outlook of MMC:
Read more: What Is Residential Construction
1. Technological Advancements:
The constant evolution of technology presents numerous opportunities for MMC. Advancements in automation, robotics, and digital design tools will further streamline the manufacturing process, improve precision, and enhance quality control. Additionally, the integration of Building Information Modeling (BIM) and other digital technologies will enable seamless collaboration, communication, and optimization throughout the construction lifecycle.
2. Sustainability and Circular Economy:
Sustainability is a critical focus in the construction industry, and MMC aligns well with sustainable practices. As environmental concerns continue to grow, MMC techniques will play a vital role in reducing waste, minimizing carbon emissions, and promoting efficient resource utilization. The circular economy concept, which emphasizes reusing and repurposing building components, will influence the future of MMC by fostering a more sustainable and resource-efficient approach to construction.
3. Scalability and Adaptability:
MMC offers scalability and adaptability, making it well-suited for addressing the growing demand for affordable and customizable housing. As population growth and urbanization continue, MMC techniques will provide efficient solutions for rapid and sustainable construction. The ability to easily scale up production and customize designs according to specific requirements will enable MMC to meet diverse housing needs and accommodate different architectural styles.
4. Collaboration and Industry Standards:
For MMC to reach its full potential, collaboration among stakeholders is crucial. Builders, architects, manufacturers, policymakers, and regulators need to work together to establish common standards, guidelines, and certifications. By doing so, the industry can ensure consistent quality, enhance safety, and drive innovation in MMC methods. Collaborative efforts will also contribute to the development of supportive policies that facilitate the adoption of MMC and overcome any regulatory barriers.
Read more: What Is A Construction Painter
5. Workforce Development and Training:
As MMC techniques become more widespread, there will be a growing need for a skilled workforce proficient in MMC methods. Training programs and educational initiatives will play a significant role in equipping workers with the necessary skills to excel in MMC. By investing in workforce development, the industry can foster a highly skilled labor force capable of embracing and advancing MMC techniques.
The future of MMC is promising, with its potential to revolutionize the construction industry in terms of speed, quality, sustainability, and customization. As technology advances, sustainability becomes an imperative, and collaboration drives innovation, MMC will continue to evolve and shape the future of building practices, offering efficient and cost-effective solutions to meet the evolving needs of the construction industry and society as a whole.
Conclusion
The Modern Method of Construction (MMC) has emerged as a game-changer in the construction industry, offering innovative techniques, materials, and processes to build structures more efficiently, sustainably, and cost-effectively. As we explored in this article, MMC encompasses various methods including offsite construction, hybrid construction, panelized construction, and volumetric construction. Each method brings its own set of advantages and considerations.
The benefits of MMC are compelling. It offers improved construction speed, enhanced quality control, reduced waste generation, and increased design flexibility. The ability to manufacture components offsite and transport them to the construction site allows for faster project completion and earlier occupancy. Moreover, MMC techniques contribute to sustainable practices by minimizing waste, promoting energy efficiency, and reducing the carbon footprint associated with traditional construction methods.
While MMC has numerous advantages, it is important to acknowledge and address the challenges it presents. These challenges include transportation logistics, site access limitations, the need for skilled labor, upfront investment, and navigating regulations and building codes. By mitigating these challenges through collaboration, investment in training, and supportive policies, the industry can fully harness the potential of MMC and overcome any barriers to its widespread adoption.
The future outlook of MMC is bright. Continual technological advancements will further streamline the manufacturing process and improve precision. Sustainability will remain a driving force, with MMC techniques contributing to the circular economy and efficient resource utilization. Collaboration among stakeholders, the establishment of industry standards, and workforce development will play crucial roles in maximizing the potential of MMC in the construction industry.
In conclusion, MMC represents the future of construction, offering efficient, sustainable, and customizable solutions. As the industry continues to evolve, embracing MMC techniques will be instrumental in addressing the challenges of an ever-growing demand for buildings while achieving higher construction standards and minimizing environmental impact. Through innovation, collaboration, and a commitment to sustainable practices, MMC has the power to revolutionize the way we build, paving the way for a more efficient, resilient, and greener future in the construction industry.
Frequently Asked Questions about What Is The Modern Method Of Construction?
Was this page helpful?
At Storables.com, we guarantee accurate and reliable information. Our content, validated by Expert Board Contributors, is crafted following stringent Editorial Policies. We're committed to providing you with well-researched, expert-backed insights for all your informational needs.
0 thoughts on “What Is The Modern Method Of Construction?”