Home>diy>Building & Construction>Where Is Aluminum Wiring Used In Construction Today
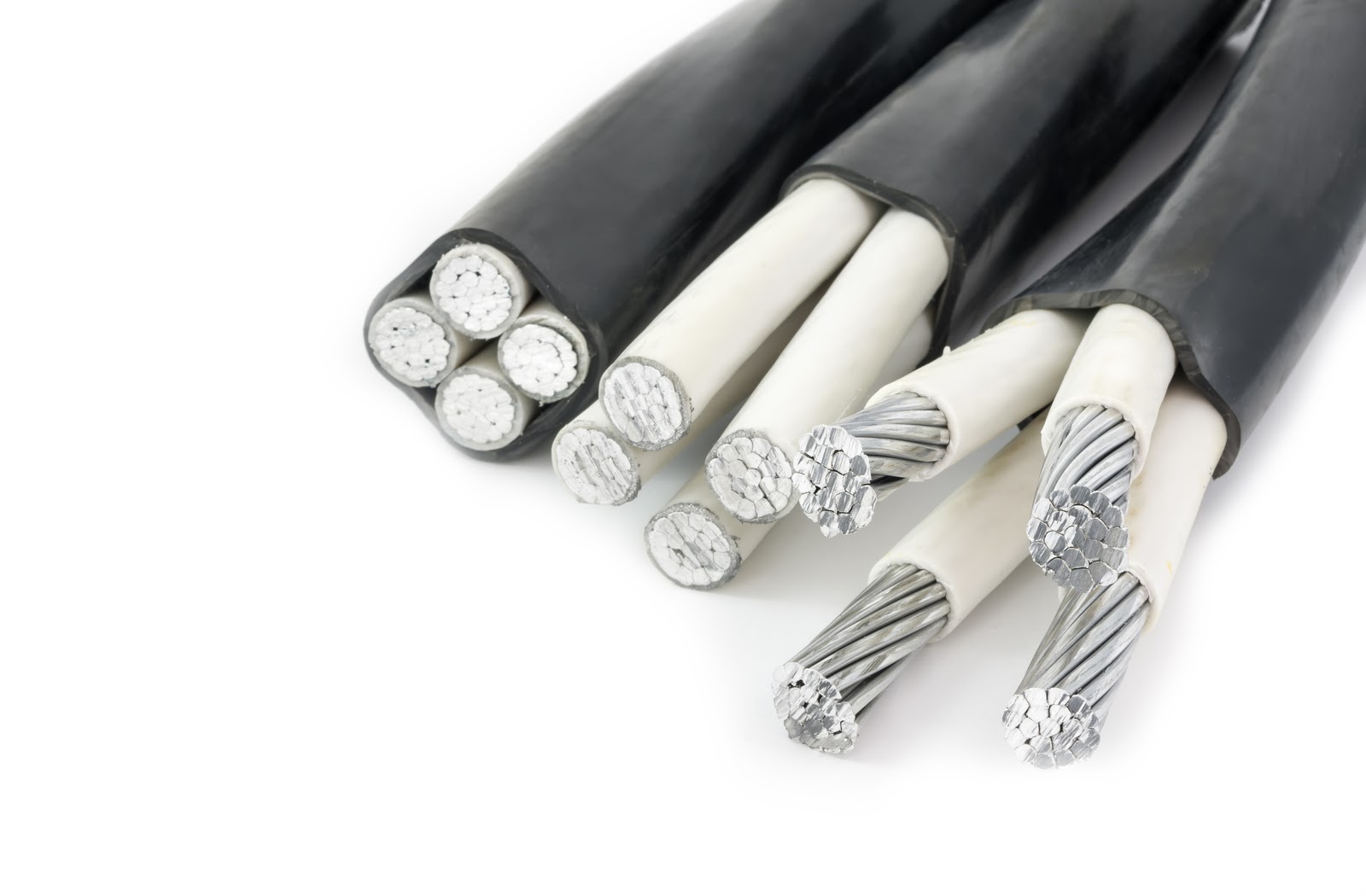
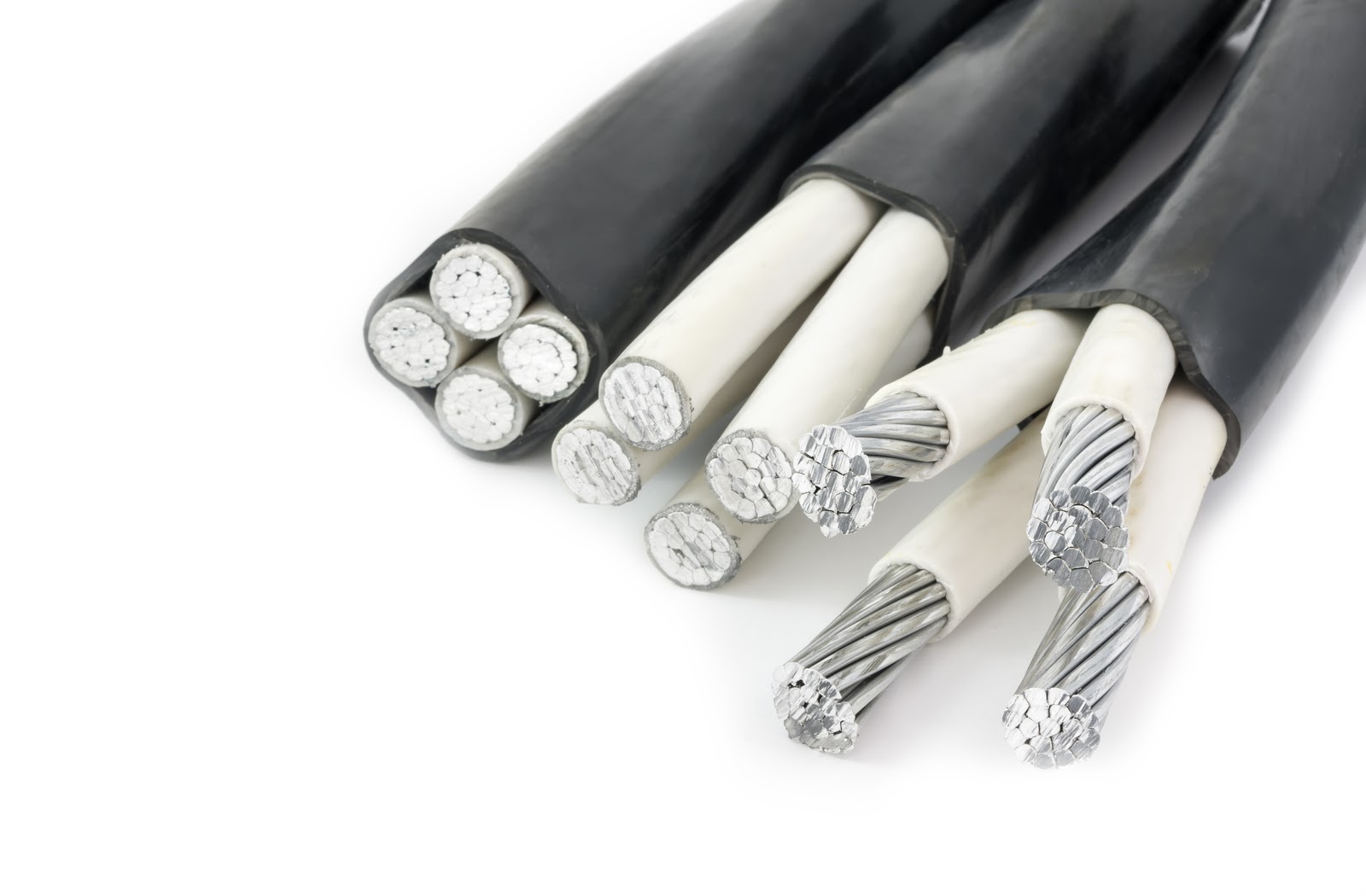
Building & Construction
Where Is Aluminum Wiring Used In Construction Today
Modified: December 7, 2023
Aluminum wiring is still used in some older buildings, but its use has been largely phased out due to safety concerns. Learn more about its application in building construction today.
(Many of the links in this article redirect to a specific reviewed product. Your purchase of these products through affiliate links helps to generate commission for Storables.com, at no extra cost. Learn more)
Introduction
When it comes to building construction, the choice of wiring material is crucial for safety and efficiency. While copper wiring has been the go-to option for many years, aluminum wiring has also made its mark in the industry. Aluminum wiring, with its unique properties and advantages, has found its place in various construction projects.
Understanding the characteristics, applications, and potential risks associated with aluminum wiring is essential for builders, contractors, and homeowners. This article will delve into the historical use, current applications, advantages, challenges, safety measures, and future implications of aluminum wiring in the construction industry.
Key Takeaways:
- Despite its decline in residential use, aluminum wiring still serves a vital role in commercial, industrial, and specialized construction projects due to its cost-effectiveness, heat dissipation, and corrosion resistance.
- The future of aluminum wiring in construction may involve advancements in aluminum wiring systems, hybrid solutions, and alternative materials, shaping the industry’s approach to electrical systems.
Read more: Wiring Your Home For Today’s Electronics
Understanding Aluminum Wiring
Aluminum wiring is an electrical conductor made primarily of aluminum. It gained popularity in construction during the 1960s and 1970s due to its cost-effectiveness and lightweight nature. Unlike copper wiring, which is known for its high conductivity, aluminum has a lower conductivity level, making it necessary to use larger diameter wires to handle the same electrical load.
One of the key properties of aluminum wiring is its excellent heat dissipation capabilities. Aluminum is highly resistant to corrosion, which is beneficial in areas with high humidity or moisture levels. Additionally, aluminum wiring expands and contracts more than copper wiring, allowing it to better withstand temperature fluctuations without the risk of breaking or becoming loose.
However, aluminum wiring has a tendency to oxidize when it encounters certain materials, leading to increased resistance to electrical current flow. This can result in overheating, potential fire hazards, and issues with electrical connections over time. To mitigate these risks, proper installation techniques and ongoing maintenance are crucial.
It’s important to note that aluminum wiring is not inherently unsafe. When installed correctly and in compliance with relevant electrical codes and safety measures, it can provide a reliable and efficient electrical system. However, its usage requires careful consideration of its limitations and the specific requirements of the construction project.
Historical Use of Aluminum Wiring in Construction
The use of aluminum wiring in construction gained momentum during the 1960s and 1970s when copper prices were high. Builders and contractors turned to aluminum wiring as a cost-effective alternative. It was commonly used in residential, commercial, and industrial buildings.
During this time, aluminum wiring was installed in many homes across North America as it provided a more affordable option compared to copper. It was particularly popular for branch circuits, lighting fixtures, and outlets.
However, widespread concerns about the safety and reliability of aluminum wiring began to surface. Homeowners reported instances of overheating, electrical failures, and even fires. It was discovered that improper installation techniques and the incompatibility of aluminum wiring with some devices contributed to these issues.
In response to these concerns, regulatory bodies and electrical industry organizations began researching and developing guidelines and standards to address the challenges associated with aluminum wiring. These efforts aimed to improve the safety and performance of electrical systems in buildings using aluminum wiring.
As a result, the use of aluminum wiring in residential construction decreased significantly. Copper wiring became the preferred choice due to its higher conductivity and better compatibility with electrical devices.
Despite its decline in popularity, existing buildings with aluminum wiring from that era still exist today. It’s important for homeowners, contractors, and electricians to be aware of the potential risks associated with aluminum wiring and take appropriate measures to ensure its safe usage and maintenance.
Current Use of Aluminum Wiring in Construction
While the use of aluminum wiring in residential construction has diminished since the 1970s, it still finds its place in various applications within the construction industry today. Aluminum wiring is commonly used in commercial and industrial settings where its unique characteristics and cost-effectiveness make it a viable option.
One of the significant areas where aluminum wiring is still utilized is in large-scale commercial buildings. These structures often require extensive electrical systems to handle the high power demands of numerous devices and equipment. Aluminum wiring, with its excellent heat dissipation properties and cost advantages, can effectively handle the electrical load in such settings.
Aluminum wiring is also commonly used in outdoor lighting installations, such as streetlights and parking lot lights. The corrosion resistance of aluminum makes it a suitable choice for these applications, as it can withstand exposure to the elements without deteriorating or requiring frequent replacements.
Another area where aluminum wiring is utilized in construction is in electrical distribution systems. Power transmission lines and distribution networks often use aluminum conductors due to their lightweight nature and the ability to span long distances without compromising electrical performance.
Additionally, aluminum wiring can be found in specialized construction projects where weight constraints are a concern. Industries such as aerospace and transportation may employ aluminum wiring to reduce the overall weight of their structures without sacrificing electrical functionality.
Despite its continuing usage in certain construction applications, it’s crucial to note that the installation of aluminum wiring should be carried out by experienced professionals who are familiar with the unique characteristics and installation requirements. Adhering to proper installation techniques and following industry standards helps ensure the safety and reliability of the electrical system.
Overall, while the prevalence of aluminum wiring in residential construction has decreased, it still plays a role in specific applications where its advantages outweigh the potential risks.
Applications of Aluminum Wiring in Today’s Construction Projects
While copper wiring remains the more popular choice in residential construction, aluminum wiring continues to find applications in various construction projects today. Here are some common uses of aluminum wiring in the industry:
- Commercial Buildings: Aluminum wiring is often used in commercial buildings where cost-effectiveness is a primary consideration. It is commonly employed for lighting systems, power distribution, and electrical control systems. The heat dissipation properties of aluminum make it a suitable option for handling the electrical demands of large-scale commercial structures.
- Industrial Facilities: Aluminum wiring is frequently utilized in industrial facilities due to its cost advantages and ability to handle high power loads. It is commonly found in manufacturing plants, warehouses, and processing facilities, where a reliable and efficient electrical system is required to power heavy machinery and equipment.
- Outdoor Lighting: Aluminum wiring is a preferred choice for outdoor lighting installations, such as streetlights and parking lot lights. Its corrosion resistance allows it to withstand exposure to the elements, ensuring the longevity and reliability of the lighting system.
- Power Transmission and Distribution: Aluminum conductors are widely used in power transmission and distribution systems. The lightweight nature of aluminum makes it suitable for long-distance power transmission, reducing the strain on support structures. Aluminum wiring is commonly found in overhead power lines and underground distribution cables.
- Aerospace and Transportation: In specialized construction projects like aerospace and transportation industries, where weight considerations are crucial, aluminum wiring is employed to reduce the overall weight of structures without compromising electrical functionality. This makes it an ideal choice for applications such as aircraft wiring, trains, and ships.
It is important to note that while aluminum wiring has its applications in certain construction projects, proper installation techniques and adherence to electrical codes and safety measures are essential. Working with experienced professionals who are knowledgeable about the unique properties and installation requirements of aluminum wiring ensures the safe and efficient functioning of the electrical system.
Aluminum wiring is still used in some construction projects, particularly for large commercial and industrial buildings. It is important to ensure that proper installation techniques and maintenance are followed to prevent potential fire hazards.
Read more: Where Is BIM Used In Construction
Advantages of Aluminum Wiring in Construction
Although aluminum wiring is not as widely used as copper wiring in residential construction, it offers several advantages in certain applications. Understanding the benefits of aluminum wiring helps builders, contractors, and homeowners make informed decisions in choosing the appropriate wiring materials. Here are some advantages of aluminum wiring:
- Cost-Effectiveness: One of the primary advantages of aluminum wiring is its cost-effectiveness. Aluminum is more abundant and less expensive than copper, making it a more affordable option, especially in large-scale construction projects where significant amounts of wiring are required.
- Lightweight and Easy to Install: Aluminum wiring is lighter than copper, making it easier to handle during installation. This can reduce labor and installation costs, especially in projects that require extensive wiring.
- Excellent Heat Dissipation: Aluminum has superior heat dissipation properties compared to copper. It can effectively dissipate heat generated by the electrical current, reducing the risk of overheating and potential damage to the wiring system.
- Durability and Corrosion Resistance: Aluminum is highly resistant to corrosion, making it suitable for use in environments with high humidity or moisture levels. This durability ensures the longevity of the wiring system, especially in outdoor or industrial applications.
- Good Conductivity: While not as conductive as copper, aluminum still has a sufficient level of conductivity to carry electrical currents effectively. By using appropriately sized aluminum wires, it can handle the electrical demands of various applications, including commercial and industrial settings.
- Compatibility with Other Materials: Aluminum wiring is generally compatible with other electrical components and devices. When proper installation techniques and materials designed for use with aluminum wiring are used, it can provide reliable electrical connections without compromising safety or performance.
It’s important to note that while aluminum wiring offers these advantages, it is essential to consider the specific requirements and limitations of the construction project. Proper installation techniques, ongoing maintenance, and compliance with electrical codes and safety measures are crucial to ensure the safe and efficient functioning of the electrical system.
Challenges and Risks Associated with Aluminum Wiring
While aluminum wiring has its advantages, it also poses certain challenges and risks that builders, contractors, and homeowners should be aware of. Understanding these potential issues allows for proper precautions and maintenance to ensure the safety and longevity of the electrical system. Here are some of the challenges and risks associated with aluminum wiring:
- Oxidation and Increased Resistance: Aluminum has a tendency to oxidize when it comes into contact with certain metals and materials. This oxidation creates a layer of aluminum oxide, which can increase resistance in the electrical connections over time. Higher resistance leads to heat buildup, potentially resulting in overheating, melting of insulation, and fire hazards.
- Compatibility Issues: Aluminum wiring can have compatibility issues with certain electrical devices, connection materials, and connectors designed for use with copper wiring. These compatibility issues can lead to improper connections, increased resistance, and potential hazards. It is crucial to use materials specifically meant for use with aluminum wiring and follow proper installation techniques.
- Expansion and Contraction: Aluminum expands and contracts more than copper with changes in temperature. This can lead to loosening of connections over time, increasing the risk of electrical arcing and potential fire hazards. Special attention must be given to proper installation techniques and regular maintenance to ensure secure connections.
- Breakage and Brittleness: Aluminum wiring, due to its characteristic of expanding and contracting, can become more brittle over time. This can result in the vulnerability of aluminum wires to cracking or breaking, leading to interrupted electrical flow and potential hazards.
- Improper Installation: Many issues with aluminum wiring arise from improper installation techniques. These include inadequate wire sizing, incorrect use of connectors, and failure to properly tighten connections. Improper installation compromises the safety and effectiveness of the electrical system.
- Age and Wear: Over time, aluminum wiring can become more susceptible to wear and deterioration. This includes issues such as increased resistance, loosening of connections, and oxidation. Regular inspections and maintenance are necessary to identify and address any potential issues before they escalate.
It is essential to work with professionals who are knowledgeable about the unique characteristics and installation requirements of aluminum wiring. Adherence to proper installation techniques, ongoing maintenance, and compliance with safety guidelines and electrical codes help mitigate the challenges and risks associated with aluminum wiring.
Safety Measures and Codes for Aluminum Wiring in Construction
Ensuring the safety of electrical systems using aluminum wiring in construction requires adherence to specific safety measures and electrical codes. These measures are in place to minimize the potential risks associated with aluminum wiring and promote a safe and reliable electrical system. Here are some key safety measures and codes to consider:
- Proper Installation: It is crucial to hire experienced electricians who are knowledgeable about the unique properties and installation techniques of aluminum wiring. They should follow manufacturer guidelines and recommendations to ensure correct sizing, connections, and termination methods specific to aluminum wiring.
- Quality Materials and Connectors: Using high-quality materials designed for use with aluminum wiring is essential. This includes connectors, terminals, and devices specifically manufactured and approved for aluminum wiring. These materials are designed to address the potential issues related to aluminum wiring, such as oxidation and compatibility problems.
- Regular Inspections and Maintenance: Ongoing inspections and maintenance of the electrical system are crucial to identify any signs of wear, loose connections, or other issues. Regular maintenance helps prevent potential hazards by addressing any potential problems before they escalate.
- Aluminum Wiring Retrofit: In some cases, homeowners may choose to retrofit their existing aluminum wiring systems. This involves the installation of copper pigtails or specialized connectors to improve the safety and reliability of the electrical connections. It is essential to consult with a qualified electrician to assess the feasibility and effectiveness of this approach for a particular electrical system.
- Electrical Codes and Regulations: Following the relevant electrical codes and regulations set by local authorities and regulatory bodies is crucial. These codes specify the acceptable installation practices, wire sizes, connectors, and other requirements to ensure the safe and effective use of aluminum wiring in construction projects.
- Educating Homeowners: Providing homeowners with information and education about aluminum wiring, its limitations, and the necessary safety precautions is essential. This helps homeowners understand the potential risks associated with aluminum wiring and enables them to take appropriate measures to ensure the safety and maintenance of their electrical systems.
By adhering to these safety measures and electrical codes, construction professionals and homeowners can minimize the potential risks associated with aluminum wiring and create a safe and reliable electrical system.
Future Implications and Alternatives to Aluminum Wiring
As technology and building practices continue to evolve, the future of aluminum wiring in construction presents some implications and considerations. While aluminum wiring still has certain applications, there are alternative options that may offer improved safety and performance. Here are some future implications and alternatives to aluminum wiring:
- Improved Aluminum Wiring Systems: Advancements in technology may lead to the development of improved aluminum wiring systems that address the challenges and risks associated with traditional aluminum wiring. These systems may incorporate innovative connectors, coatings, and installation techniques to enhance safety and performance.
- Aluminum-Copper Hybrid Systems: Some construction projects may benefit from the use of hybrid systems that combine aluminum and copper wiring. These systems utilize aluminum wiring for lower voltage applications and copper wiring for higher voltage demands, taking advantage of the cost-effectiveness of aluminum and the superior conductivity of copper.
- Copper-Clad Aluminum Wiring: Copper-clad aluminum (CCA) wiring is another alternative that combines the benefits of both aluminum and copper. CCA wire consists of an aluminum core coated with a layer of copper, providing improved conductivity while still maintaining cost advantages. Proper installation techniques and compatibility with devices specifically designed for CCA wiring are necessary for optimal performance.
- Composite Wiring Systems: Composite wiring systems, which utilize a combination of different materials such as aluminum, copper, and other conductive materials, may emerge as viable alternatives in the future. These systems can provide optimized electrical performance and safety, customizing the use of different materials for specific applications.
- Technological Advances: Technological advancements in electrical systems may lead to the development of alternative materials and solutions that offer improved performance, safety, and cost-effectiveness. For example, the use of advanced polymers or fiber optics could provide alternative options for electrical wiring systems in the future.
It is important to note that as these alternatives emerge, thorough research, testing, and certifications will be necessary to ensure their reliability and compliance with electrical codes and safety standards. Building professionals should stay informed about these advancements and consult with experts to determine the most suitable and appropriate wiring options for their specific construction projects.
Ultimately, the future of aluminum wiring in construction will depend on ongoing research and development efforts, as well as the industry’s response to addressing its limitations. Embracing new technologies and alternative wiring solutions will play a crucial role in ensuring safe and reliable electrical systems in the years to come.
Read more: Where To Buy Aluminum Siding
Conclusion
Aluminum wiring has played a significant role in the construction industry, offering cost-effectiveness and unique properties that make it suitable for various applications. While historically used extensively, especially during the 1960s and 1970s, concerns regarding safety and compatibility led to its decreased usage in residential construction.
However, aluminum wiring still finds its place in today’s construction projects, particularly in commercial, industrial, and specialized applications. Its lightweight nature, heat dissipation capabilities, and corrosion resistance make it an attractive option in certain scenarios.
Understanding the advantages, challenges, and risks associated with aluminum wiring is crucial. Adherence to proper installation techniques, the use of high-quality materials designed for aluminum wiring, regular inspections, and ongoing maintenance play a vital role in ensuring the safety and efficiency of the electrical system.
Looking ahead, the future of aluminum wiring in construction may involve advancements in aluminum wiring systems, the use of hybrid systems that combine aluminum and copper, or the emergence of alternative materials and composite wiring solutions. Technological innovations will continue to shape the industry and offer improved options for builders, contractors, and homeowners.
It is important to stay informed about the latest developments in electrical wiring systems, adhere to electrical codes and regulations, and consult with professionals to make informed decisions about the wiring materials best suited for specific construction projects.
Ultimately, ensuring the safety and reliability of electrical systems is of utmost importance in construction. By understanding the characteristics and applications of aluminum wiring, addressing its challenges and risks, and considering alternative options, construction professionals can create electrical systems that meet the needs of today and the future.
Frequently Asked Questions about Where Is Aluminum Wiring Used In Construction Today
Was this page helpful?
At Storables.com, we guarantee accurate and reliable information. Our content, validated by Expert Board Contributors, is crafted following stringent Editorial Policies. We're committed to providing you with well-researched, expert-backed insights for all your informational needs.
0 thoughts on “Where Is Aluminum Wiring Used In Construction Today”