Home>diy>Building & Construction>Why Is There A Construction Material Shortage
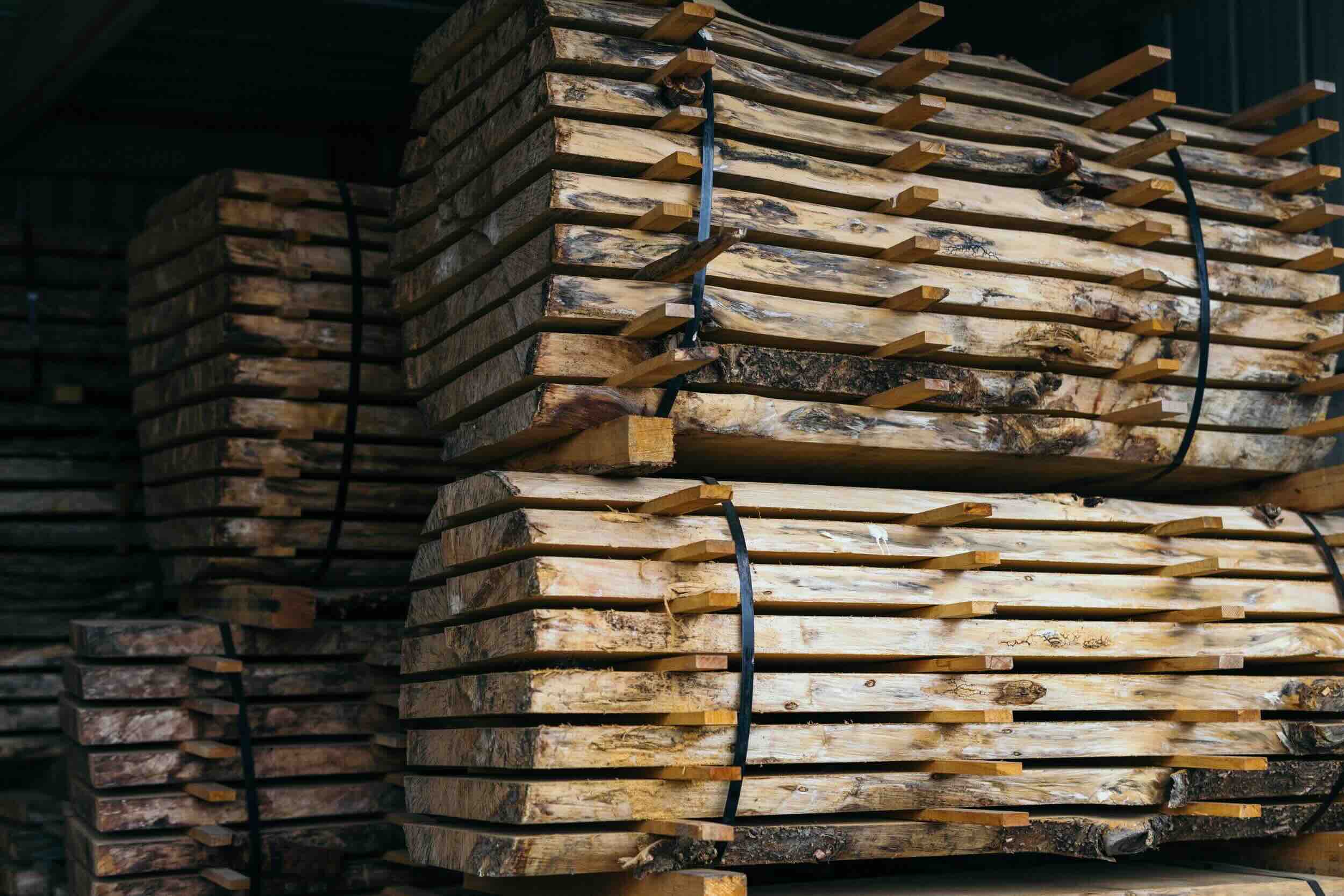
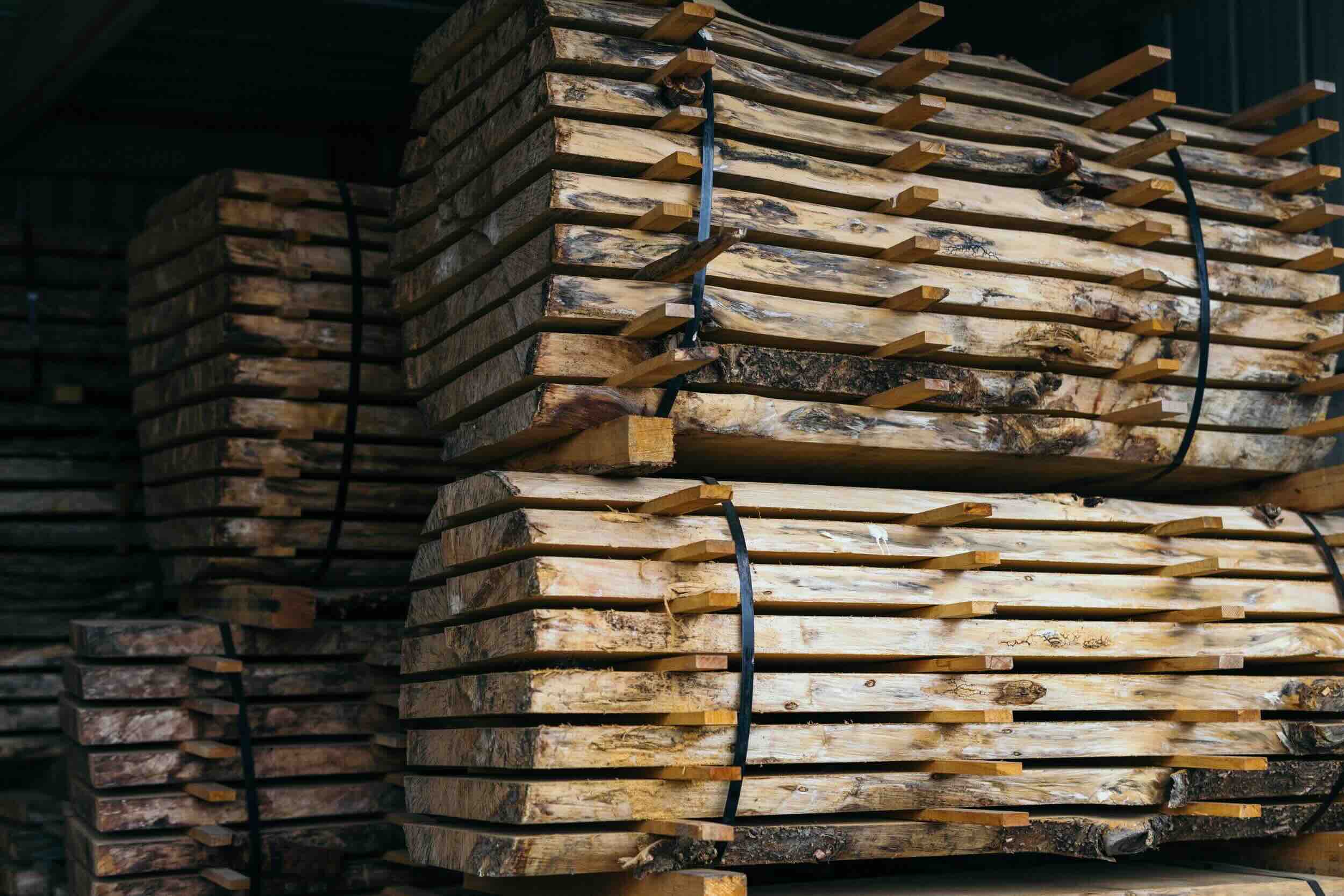
Building & Construction
Why Is There A Construction Material Shortage
Modified: December 7, 2023
Discover why the construction industry is facing a shortage of building materials and how it's impacting projects. Find ways to navigate these challenges and ensure successful construction projects.
(Many of the links in this article redirect to a specific reviewed product. Your purchase of these products through affiliate links helps to generate commission for Storables.com, at no extra cost. Learn more)
Introduction
The construction industry plays a vital role in shaping the infrastructure of our cities and communities. From towering skyscrapers to residential homes, construction projects require a vast array of materials to bring design concepts to life. However, the industry is currently facing a significant challenge – a construction material shortage.
This shortage has been caused by a variety of factors, including increased demand for construction materials, disruptions in the global supply chain, rising material prices, and delays in project timelines. These issues have had a profound impact on the construction industry and have led to several consequences that affect builders, contractors, and ultimately, the end consumers.
In this article, we will explore the reasons behind the construction material shortage, the impact it has on the industry, and strategies that can be implemented to mitigate these challenges.
Key Takeaways:
- Embracing alternative materials can alleviate strain on scarce resources, contribute to sustainability, and offer cost-effective solutions for the construction industry, ensuring a greener and more resilient future.
- Enhancing supply chain resilience through diversification, communication, collaboration, and technology can ensure a steady flow of materials, minimize disruptions, and support timely project completion, fostering a more robust and flexible construction industry.
Read more: How To Fix The Construction Labor Shortage
Factors contributing to the construction material shortage
Several factors have contributed to the construction material shortage that the industry is currently facing. Understanding these factors is crucial in comprehending the scope of the issue and finding effective solutions. Let’s take a closer look at the key factors:
- Increased demand for construction materials: The demand for construction materials has skyrocketed in recent years due to population growth, urbanization, and increased infrastructure development. This heightened demand has put immense pressure on the supply chain, making it difficult for manufacturers to keep up with the pace.
- Supply chain disruptions: The COVID-19 pandemic has resulted in disruptions throughout the global supply chain. Restrictions on manufacturing operations, transportation challenges, and labor shortages have all contributed to delays in the production and delivery of construction materials.
- Rising material prices: The scarcity of construction materials has led to a surge in prices. Factors such as increased demand, limited supply, and higher production costs have all contributed to this price inflation. Builders and contractors are now faced with the challenge of managing project budgets that have been stretched due to these escalating costs.
- Delays in project timelines: With limited availability of materials, construction projects are experiencing significant delays. Builders and contractors are struggling to acquire the necessary materials in a timely manner, leading to delays in project completion. This not only affects the contractors’ reputation but also incurs additional costs, further exacerbating the challenges faced by the industry.
These factors have created a perfect storm for the construction material shortage. The industry is grappling with the ramifications of this scarcity, and finding solutions to mitigate its effects has become crucial for builders, contractors, and project owners.
Impact on the construction industry
The construction material shortage has had far-reaching effects on the construction industry, impacting various stakeholders and aspects of the construction process. Let’s examine the key impacts:
- Delayed project timelines: The shortage of construction materials has resulted in significant delays in project timelines. Builders and contractors are struggling to procure the necessary materials, causing setbacks in construction progress. This has a ripple effect on the entire project schedule and can lead to increased costs and dissatisfied clients.
- Increased construction costs: The scarcity of materials has driven up prices, resulting in increased construction costs. Builders and contractors are forced to pay higher prices for the limited available materials, impacting their profit margins. These increased costs can sometimes be passed on to the clients, making construction projects more expensive.
- Disruption in supply chain management: The construction material shortage has exposed weaknesses in supply chain management. Contractors and builders are having to navigate through supply chain disruptions, including delays in deliveries and unreliable inventory availability. This challenge requires the industry to reassess and strengthen supply chain processes to ensure a steady flow of materials.
- Limited project capacity: The material shortage has constrained the construction industry’s capacity to take on new projects. With limited availability of materials, construction companies are unable to meet the demands of potential clients. This leads to missed opportunities and slower growth for the industry as a whole.
- Decline in housing affordability: The construction material shortage has also impacted housing affordability. With increased costs and delays, builders and developers are finding it challenging to offer affordable housing options to potential buyers. This exacerbates the existing housing crisis and makes it even more difficult for individuals and families to find affordable housing.
The overall impact of the construction material shortage on the industry is significant. It has disrupted construction projects, increased costs, strained supply chains, limited capacity, and hindered housing affordability. Finding solutions to address these challenges is crucial for the industry’s growth, stability, and the well-being of both construction professionals and consumers.
Increased demand for construction materials
One of the major contributing factors to the construction material shortage is the unprecedented increase in demand for these materials. Several factors have led to this surge in demand:
- Population growth and urbanization: As the global population continues to grow, urban areas are expanding rapidly. This leads to a higher demand for new construction projects, including residential buildings, commercial spaces, and infrastructure development.
- Infrastructure development: Governments around the world are investing heavily in infrastructure projects to improve transportation, energy, and public facilities. These large-scale projects require significant amounts of construction materials, placing additional strain on the already stretched supply chain.
- Renewable energy initiatives: The transition towards clean energy sources has led to an increased demand for materials used in renewable energy infrastructure, such as solar panels and wind turbines. As these technologies become more prevalent, the demand for necessary construction materials continues to rise.
- Building renovations and remodeling: In addition to new construction, there is also a surge in building renovations and remodeling projects. Homeowners and businesses are investing in transforming existing structures, requiring a substantial amount of construction materials in the process.
These factors have created a perfect storm where the demand for construction materials has outpaced the available supply. Manufacturers and suppliers are striving to keep up with the increasing demand, but the shortage persists due to various challenges in production and distribution.
Moreover, recent events such as the COVID-19 pandemic have further heightened the demand for construction materials. As people spend more time at home and prioritize comfort, there has been an upsurge in home improvement and renovation projects. This surge in demand, coupled with the challenges posed by the pandemic, has placed immense pressure on the construction material supply chain.
The increased demand for construction materials is a testament to the growth and development happening worldwide. However, it is imperative for the industry to find sustainable solutions to meet this demand while balancing the sourcing, production, and distribution of construction materials to avoid prolonged shortages and price volatility.
Supply chain disruptions
The construction material shortage has been exacerbated by significant disruptions in the global supply chain. Various factors have contributed to these disruptions:
- COVID-19 pandemic: The global pandemic caused widespread disruptions across industries, including construction. Lockdowns, restrictions on manufacturing operations, and travel limitations have all impacted the smooth flow of materials within the supply chain. Factory closures, reduced production capacity, and delays in transportation have resulted in bottlenecks and shortages.
- Transportation challenges: Another key factor contributing to the disruptions in the supply chain is transportation challenges. Restrictions on international and domestic travel, as well as reduced shipping capacities, have led to delays in the delivery of construction materials. Additionally, the shortage of truck drivers and logistics personnel further compounds the transportation challenges and hampers the timely distribution of materials.
- Raw material shortages: The supply chain disruptions extend to the availability of raw materials used in the production of construction materials. Delays or shortages of raw materials, such as timber, steel, and cement, impact the manufacturing process, resulting in limited production capacity and delays in fulfilling orders.
- Trade restrictions and tariffs: Trade conflicts and the imposition of tariffs on certain materials have also disrupted the supply chain. These restrictions and additional costs can limit the availability of construction materials, making it more difficult and expensive for builders and contractors to procure the necessary materials.
- Labor shortages: The shortage of skilled labor within the construction industry has further strained the supply chain. Without adequate labor to manufacture and transport materials, the production and distribution of construction materials are significantly impacted, leading to delays and shortages.
These disruptions in the supply chain have significantly affected the availability and timely delivery of construction materials. The interconnectedness of the global economy and the reliance on efficient supply chain management highlight the need for resilience and contingency planning to mitigate future disruptions.
Addressing these challenges requires collaboration among all stakeholders, including manufacturers, suppliers, distributors, contractors, and government agencies. By implementing measures to enhance supply chain resilience and finding alternative sourcing options, the construction industry can better navigate these disruptions and mitigate the impact of future supply chain challenges.
Read more: Why Construction Is Important
Rising material prices
One of the significant consequences of the construction material shortage is the sharp increase in material prices. Several factors have contributed to this surge in prices:
- Supply and demand imbalance: The scarcity of construction materials has created an imbalance between supply and demand. With limited availability, the demand for materials far exceeds the supply, leading to higher prices as businesses and individuals compete for limited resources.
- Inflation in production costs: Rising production costs have also impacted the prices of construction materials. Factors such as increased transportation costs, higher labor wages, and fluctuations in the cost of raw materials have all contributed to the overall increase in prices.
- Tariffs and trade restrictions: Trade conflicts and the imposition of tariffs on certain materials have added to the rising material prices. These additional costs make it more expensive to import or export construction materials, driving prices up for both builders and consumers.
- Limited production capacity: With the shortage of materials, manufacturers are operating at limited production capacity. This constraint on supply leads to higher prices as businesses aim to maximize their profits while meeting the growing demand.
- Fluctuating energy costs: The cost of energy, such as fuel and electricity, is a significant component in manufacturing construction materials. Fluctuations in energy prices can impact production costs, ultimately affecting the prices of construction materials.
These factors have caused significant price inflation in the construction material market, impacting builders, contractors, and consumers alike. The increased material prices have a direct impact on construction budgets, making it more challenging for builders to complete projects within allotted budgets. This, in turn, can lead to financial strain and decreased profitability for construction companies.
Furthermore, higher material prices can have a cascading effect on other sectors of the economy. For example, increased construction costs can translate to higher housing prices and reduced housing affordability. This creates challenges for individuals and families seeking to purchase homes or rent properties, exacerbating housing affordability issues.
Addressing the issue of rising material prices requires a comprehensive approach. It may involve exploring alternative materials, improving supply chain efficiency, and promoting transparency in pricing. Additionally, collaboration between industry stakeholders and policy-makers is essential to find long-term solutions that balance the interests of all parties involved.
Delays in project timelines
One of the significant consequences of the construction material shortage is the considerable delays in project timelines. The shortage of construction materials has created various challenges that have contributed to these delays:
- Difficulty in procuring materials: Builders and contractors are facing difficulties in procuring the necessary construction materials in a timely manner. Increased demand and limited availability have created a competitive market for materials, resulting in delays in securing the required quantities.
- Supply chain disruptions: Disruptions in the global supply chain, as a result of the COVID-19 pandemic and other factors, have led to delays in the production, transportation, and delivery of construction materials. These delays have a direct impact on project timelines, as builders wait for materials to arrive before work can progress.
- Material allocation challenges: In some cases, even when builders are able to procure the necessary materials, there may be limits on the quantities available. This can lead to partial deliveries or the need to source alternative materials, both of which can cause delays in the construction process.
- Rescheduling and resequencing: The shortage of construction materials often requires builders and contractors to reschedule and resequence their projects. This involves rearranging activities and adjusting the project plan to accommodate the availability of materials, leading to delays in the overall project timeline.
- Impact on subcontractors and trades: Delays in procuring materials affect not only the builders and contractors but also subcontractors and tradespeople involved in the construction process. Disruptions in the timely delivery of materials can disrupt their schedules and availability, further contributing to project delays.
These delays in project timelines have significant implications for builders, contractors, and clients. They can result in increased project costs, as extended construction periods often lead to additional labor and overhead expenses. Moreover, delays can also strain relationships with clients, damage reputations, and lead to contractual issues or legal disputes.
Successfully managing project timelines in the face of a material shortage requires effective communication, proactive planning, and flexibility. Builders and contractors need to explore alternative sourcing options, communicate with suppliers and subcontractors, and incorporate buffer time into project schedules to account for potential delays related to material availability.
Collaboration between industry professionals and all stakeholders involved in the construction process is crucial to mitigate the impact of material shortages and minimize delays. By working together and implementing strategies to address these challenges, the industry can navigate this difficult terrain and ensure projects are completed in a timely manner.
Consider using alternative construction materials such as recycled or sustainable options to mitigate the impact of the shortage. Additionally, plan ahead and secure your material supply well in advance to avoid delays.
Effects on housing affordability
The construction material shortage has had a direct impact on housing affordability, making it increasingly challenging for individuals and families to find affordable housing options. Several effects contribute to this issue:
- Increase in construction costs: The scarcity of construction materials has led to a surge in material prices, which directly affects the cost of constructing homes. Builders and developers are facing higher expenses in procuring materials, resulting in increased construction costs. These higher costs are often passed on to homebuyers, making housing less affordable for many.
- Delayed construction projects: The delays caused by the material shortage also have an impact on housing affordability. Longer construction timelines result in increased carrying costs for developers, including expenses such as financing and overhead. These costs are ultimately reflected in the final price of the homes, further contributing to affordability challenges.
- Reduced housing supply: The material shortage has limited the production capacity of construction projects, leading to a reduced supply of housing units. When the demand for housing exceeds the available supply, prices naturally increase. This imbalance between supply and demand further exacerbates housing affordability issues.
- High competition for housing: The limited availability of affordable housing units due to the material shortage has created intense competition among potential homebuyers. This competition drives up prices, making it difficult for individuals with limited financial resources to enter the housing market or find affordable housing options.
- Impact on rental market: The material shortage not only affects homebuyers but also impacts the rental market. Developers who are unable to construct new housing units may turn to the rental market, increasing demand and driving up rental prices. This makes it more challenging for individuals to secure affordable rental properties.
The effects of the construction material shortage on housing affordability are significant and have far-reaching consequences for individuals and communities. Accessible and affordable housing is essential for a balanced and sustainable society, and the material shortage poses a threat to achieving these goals.
To address the issue of housing affordability, it is crucial for the construction industry, policymakers, and stakeholders to collaborate and implement strategies that promote affordable housing initiatives. This may include exploring alternative construction methods, incentivizing the use of sustainable and cost-effective materials, and streamlining the approval process for affordable housing projects.
By prioritizing housing affordability and adopting innovative solutions, it is possible to mitigate the impact of the construction material shortage and create more opportunities for individuals and families to find affordable housing options.
Strategies to mitigate the construction material shortage
The construction material shortage presents significant challenges to the industry, but there are strategies that can be implemented to help mitigate these issues. By adopting proactive measures and finding innovative solutions, builders, contractors, and industry stakeholders can navigate through the shortage more effectively. Here are some key strategies:
- Embrace alternative materials: Exploring the use of alternative materials can help alleviate the pressure on scarce resources. Builders can consider sustainable and cost-effective substitutes for traditional materials without compromising on quality or safety. For example, using engineered wood products instead of scarce timber or exploring innovative composite materials can reduce reliance on limited resources.
- Enhance supply chain resilience: Strengthening and diversifying the supply chain is crucial to mitigate material shortages. Builders and contractors can cultivate relationships with multiple suppliers to ensure a more reliable and diverse source of materials. Additionally, implementing transparent and efficient supply chain management practices can help identify potential bottlenecks and proactively address them.
- Improve project planning and management: Effective project planning and management are essential in mitigating delays caused by material shortages. Builders should carefully assess project timelines, taking into account potential material availability challenges. This allows for better project sequencing, enabling timely adjustments and proactive rescheduling to minimize the impact of material scarcity.
- Collaborate with suppliers and subcontractors: Building strong partnerships with suppliers and subcontractors is crucial during material shortages. Engaging in open communication and collaboration can help prioritize and streamline material deliveries, ensuring a consistent supply of critical materials. Additionally, fostering relationships with alternative suppliers provides flexibility and options when shortages occur.
- Invest in technology and prefabrication: Embracing technological advancements and prefabrication methods can help optimize the use of available resources. Technology can assist in material tracking, inventory management, and optimizing material usage. Prefabrication allows for off-site construction and assembly, reducing the reliance on materials at the construction site and mitigating the impact of material shortages.
The implementation of these strategies requires collaboration and a proactive approach from all industry stakeholders. It is crucial for builders, contractors, suppliers, and policymakers to work together to ensure a resilient and sustainable construction industry that can effectively manage material shortages. By embracing alternative materials, enhancing supply chain resilience, improving project planning and management, collaborating with suppliers and subcontractors, and investing in technology, the construction industry can navigate through material shortages and continue to thrive.
Read more: Why Work In Construction
Embracing alternative materials
In the face of a construction material shortage, one effective strategy for mitigating the impact is to embrace alternative materials. Exploring and adopting alternative materials can help alleviate the strain on scarce resources while still meeting the requirements of construction projects. Here are some key aspects of embracing alternative materials:
- Sustainable sourcing: Alternative materials often offer a more sustainable option compared to traditional construction materials. Materials such as recycled plastics, bamboo, or reclaimed wood can be used to reduce reliance on scarce resources and minimize environmental impact. By embracing sustainable sourcing practices, builders can contribute to a greener and more environmentally friendly construction industry.
- Cost-effectiveness: Alternative materials can also offer cost-effective solutions. Some alternative materials, such as engineered wood products, can be more affordable compared to traditional lumber while still providing the necessary structural integrity. Exploring cost-effective alternatives enables builders to manage costs more efficiently, particularly when traditional materials are scarce and expensive.
- Enhanced durability and performance: Alternative materials often come with improved durability and performance characteristics. For example, fiber-reinforced polymer composites offer exceptional strength-to-weight ratios and corrosion resistance, making them suitable for various construction applications. Embracing these materials can result in longer-lasting and more resilient structures.
- Innovation and design versatility: Alternative materials often offer innovative design possibilities and greater versatility in construction projects. For instance, using energy-efficient materials, such as aerogel insulation or solar panels, can enhance the sustainability and energy efficiency of buildings. Embracing these materials opens up new avenues for innovative and visually appealing designs.
- Regulatory compliance: It is essential to ensure that alternative materials comply with local building codes and regulations. Builders and contractors should familiarize themselves with the applicable standards and certifications for the alternative materials they plan to use. This ensures that the construction projects meet safety standards and obtain necessary approvals and permits.
Embracing alternative materials requires thorough research, evaluation, and collaboration among architects, engineers, builders, and suppliers. It is essential to assess the suitability of alternative materials for specific project requirements, including structural integrity, durability, and compatibility with other building components. Additionally, builders should consider the availability and reliable sourcing of alternative materials to avoid potential supply chain issues.
The construction industry has witnessed significant advancements in alternative materials, driven by the need to address sustainability goals and material shortages. By embracing these materials and incorporating them into construction projects, builders can not only navigate material shortages but also contribute to a more sustainable and resilient future for the industry.
Enhancing supply chain resilience
In the face of a construction material shortage, enhancing supply chain resilience is crucial to mitigate the impact and ensure a steady flow of materials. Here are some key strategies for enhancing supply chain resilience:
- Diversify suppliers: Relying on a single supplier can be risky as it leaves the supply chain vulnerable to disruptions. Builders and contractors should consider diversifying their supplier base by establishing relationships with multiple suppliers. This provides alternative sources of materials and reduces dependency on a single supplier, minimizing the impact of any specific supplier-related issues.
- Establish clear communication: Open and transparent communication with suppliers is vital for building a resilient supply chain. Builders should clearly communicate their material requirements, project schedules, and any potential challenges they anticipate. By maintaining a proactive line of communication, builders can help suppliers better plan and manage their inventory, ensuring a smoother supply chain flow.
- Foster collaboration: Collaboration among industry stakeholders is essential for enhancing supply chain resilience. Builders, suppliers, and subcontractors should work together to align expectations, share information, and develop contingency plans. Collaborative efforts can help identify potential bottlenecks, streamline operations, and address any challenges that arise in the supply chain.
- Invest in technology: Leveraging technology can significantly enhance supply chain resilience. Implementing inventory management systems, data analytics, and real-time tracking can provide visibility into the supply chain process. This allows builders to anticipate and respond effectively to any disruptions or changes in material availability. Technology also enables better demand forecasting, enabling builders to adjust production schedules and inventory levels accordingly.
- Strengthen supplier relationships: Building strong relationships with suppliers is key to a resilient supply chain. Regularly evaluating and monitoring supplier performance, conducting audits, and fostering trust and collaboration can help establish a reliable and responsive supplier network. Strong supplier relationships can lead to preferential treatment during material shortages and cooperation in finding alternative solutions.
- Consider local sourcing: Exploring local sourcing options can help reduce dependencies on global supply chains. Working with local suppliers can offer several advantages, including shorter lead times, reduced transportation costs, and increased control over the supply chain. Local sourcing also supports the local economy and minimizes the impact of potential international trade disruptions.
Enhancing supply chain resilience requires ongoing monitoring, evaluation, and continuous improvement. It is essential to stay informed about market trends, geopolitical factors, and potential risks in the supply chain. By adopting these strategies and proactive measures, builders can build a resilient supply chain that can withstand disruptions, navigate material shortages, and ensure the timely completion of construction projects.
Improving project planning and management
In the face of a construction material shortage, improving project planning and management is crucial to mitigate the impact and minimize delays. Here are some key strategies to enhance project planning and management:
- Thorough project assessment: Conducting a comprehensive project assessment is essential to identify potential material shortages and challenges. Builders should carefully analyze the project requirements, including the quantity and availability of materials, and factor in possible delays caused by the material shortage. A thorough assessment helps in developing a realistic project timeline and identifying alternative sourcing options.
- Collaborative project planning: Involving all stakeholders, including architects, engineers, suppliers, and subcontractors, in project planning is crucial for success. Collaborative planning sessions allow for early identification of potential material shortages, enabling proactive measures such as alternative material selection or sourcing options. Regular communication and coordination among the project team help align expectations and minimize surprises.
- Flexibility in project sequencing: Flexibility in project sequencing is vital when facing material shortages. Builders should develop agile project plans that allow for adjustments and rearrangements in the construction timeline. By prioritizing areas of work that are less reliant on scarce materials, builders can keep the project moving forward while awaiting the availability of critical materials.
- Contingency planning: Developing contingency plans is essential to mitigate the impact of material shortages. Builders should identify alternative sourcing options, establish backup suppliers, and explore substituting alternative materials whenever possible. Having predefined contingency plans in place helps reduce project delays and ensures a smoother transition when faced with unexpected material shortages.
- Effective communication and coordination: Communication is key to managing material shortages and mitigating delays. Regular communication with suppliers regarding material availability and lead times helps builders align project schedules accordingly. Transparent and open communication with the project team, subcontractors, and clients fosters understanding and allows for proactive planning and adjustments as needed.
- Efficient inventory management: Implementing robust inventory management practices helps builders optimize material usage and reduce waste. Maintaining accurate inventory records, closely monitoring material consumption, and avoiding excessive stockpiling can help ensure that available materials are utilized efficiently. Effective inventory management minimizes the risk of running out of critical materials and helps identify shortages early on.
Improving project planning and management requires a proactive and adaptive approach. By conducting thorough project assessments, collaborating with stakeholders, maintaining flexibility, developing contingency plans, and enhancing communication and inventory management, builders can better navigate through material shortages and minimize project delays.
It is important to remember that construction projects are dynamic, and adjustments may need to be made as the circumstances evolve. An agile and proactive mindset, coupled with effective project planning and management, can help builders successfully complete projects within the constraints posed by material shortages.
Conclusion
The construction material shortage is a significant challenge facing the construction industry, impacting builders, contractors, and the availability of affordable housing. Several factors, including increased demand, supply chain disruptions, rising material prices, and delays in project timelines, have contributed to this shortage. However, by implementing proactive strategies, the industry can mitigate the impact and navigate through these challenges.
Embracing alternative materials is one effective strategy to alleviate the strain on scarce resources. By exploring sustainable and cost-effective alternatives, builders can reduce reliance on traditional materials and contribute to a greener and more resilient construction industry.
Enhancing supply chain resilience is crucial in managing material shortages. Diversifying suppliers, strengthening relationships, improving communication and collaboration, and leveraging technology can help create a more robust and flexible supply chain. This ensures a steady flow of materials and minimizes the impact of disruptions on project timelines.
Improving project planning and management is essential to mitigate delays caused by material shortages. Thorough project assessments, collaborative planning, flexibility in sequencing, and effective communication and coordination among stakeholders help identify potential challenges early on and allow for proactive measures to adapt to material availability issues.
Addressing the construction material shortage requires a collaborative effort from all industry stakeholders, including builders, contractors, suppliers, and policymakers. By working together, exploring alternative materials, enhancing supply chain resilience, and improving project planning and management, the construction industry can overcome the challenges posed by material shortages and continue to deliver quality projects.
It is crucial to remain adaptable, innovative, and proactive in addressing material shortages and seeking long-term solutions. By doing so, we can build a more sustainable, resilient, and affordable future for the construction industry and the communities it serves.
Frequently Asked Questions about Why Is There A Construction Material Shortage
Was this page helpful?
At Storables.com, we guarantee accurate and reliable information. Our content, validated by Expert Board Contributors, is crafted following stringent Editorial Policies. We're committed to providing you with well-researched, expert-backed insights for all your informational needs.
0 thoughts on “Why Is There A Construction Material Shortage”