Home>diy>Building & Construction>What Is Material Take Off In Construction
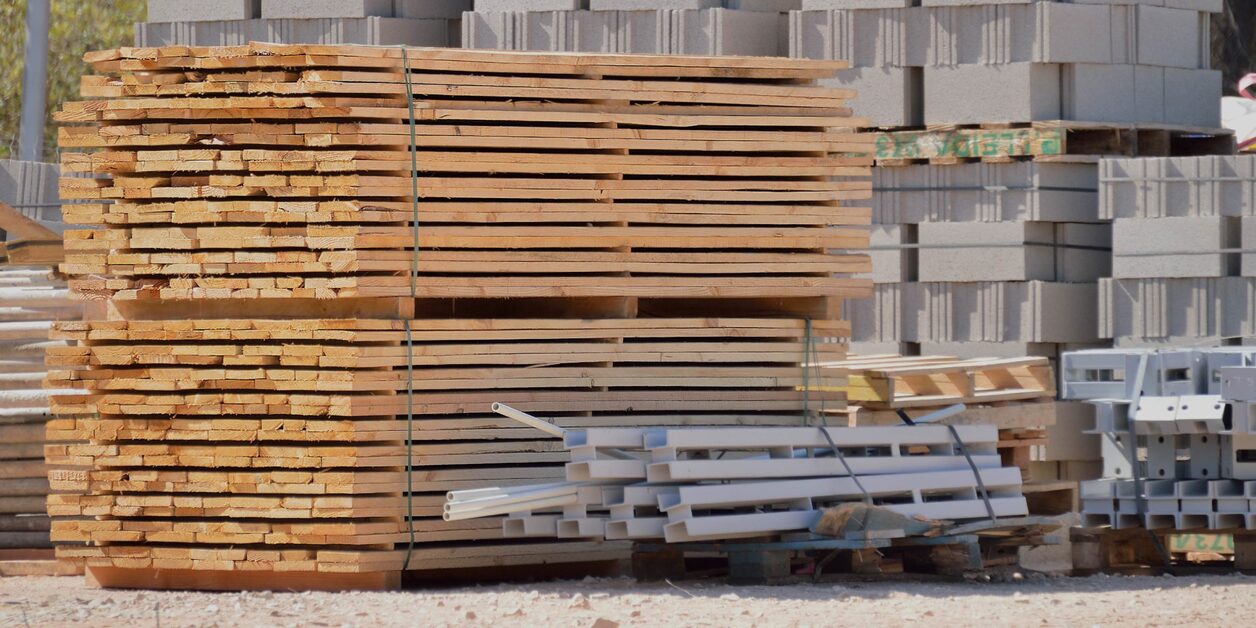
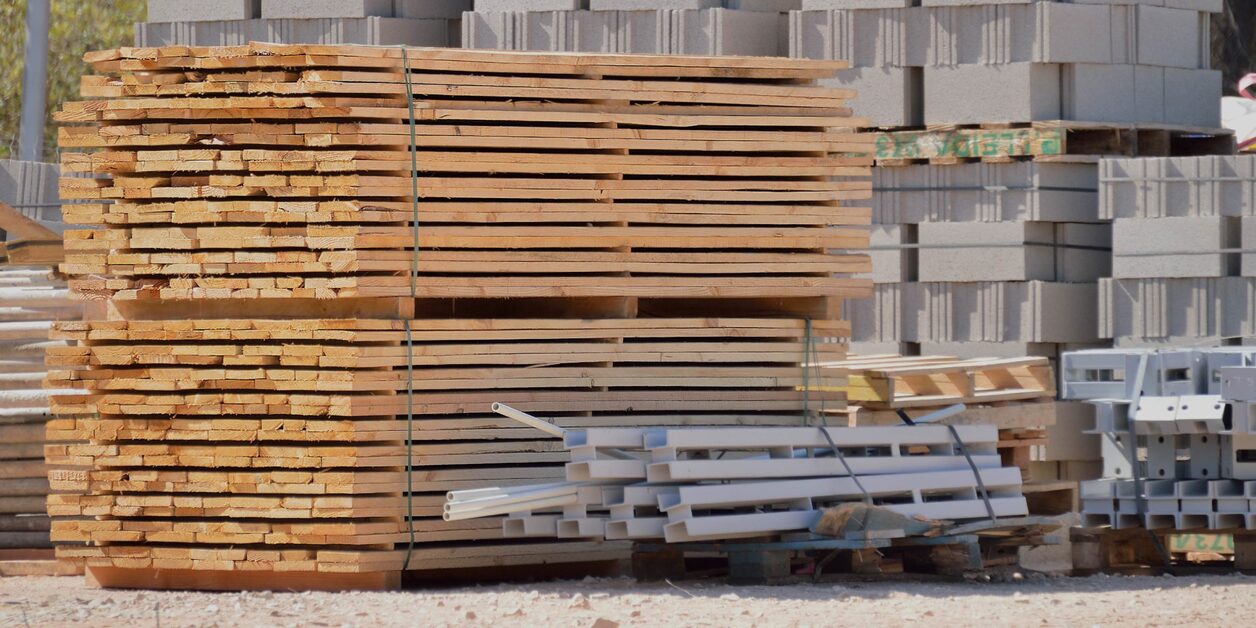
Building & Construction
What Is Material Take Off In Construction
Modified: January 9, 2024
Learn what material take off is in building construction and how it helps estimate project costs. Understand its importance in planning and resource management.
(Many of the links in this article redirect to a specific reviewed product. Your purchase of these products through affiliate links helps to generate commission for Storables.com, at no extra cost. Learn more)
Introduction
In the world of construction, proper planning and management are essential for the successful completion of a project. One critical aspect that plays a crucial role in the overall construction process is material take off. Material take off refers to the process of quantifying and estimating the required materials for a construction project. It involves identifying, measuring, and listing all the necessary materials needed for each phase of the project, from start to finish.
Accurate material take off ensures that the right amount of materials are available at the right time, preventing delays in the project schedule and minimizing the risk of cost overruns. With the advancements in technology, the process of material take off has become more streamlined and efficient.
In this article, we will delve deeper into the definition of material take off in construction, its importance, the process involved, tools and software used, as well as the benefits, challenges, and best practices associated with it. By the end, you will have a comprehensive understanding of material take off and its significance in the construction industry.
Key Takeaways:
- Accurate material take off in construction is crucial for cost estimation, resource allocation, and project coordination. It ensures timely delivery, cost control, and enhanced productivity, contributing to successful project outcomes.
- Leveraging digital tools, collaborating with stakeholders, and adhering to best practices are essential for efficient material take off. Overcoming challenges and embracing technology leads to accurate quantification and streamlined construction processes.
Read more: What Is A Take Off In Construction
Definition of Material Take Off in Construction
Material take off, also known as quantity take off or simply take off, is a crucial process in construction that involves calculating the quantities of materials required for a specific project. It is a detailed estimation that lists and quantifies all the materials needed, ensuring that the project is adequately supplied with the necessary resources.
The process of material take off typically begins with reviewing the architectural and engineering drawings, specifications, and other project documents. By carefully analyzing these documents, construction professionals can identify the types and quantities of materials required for each component of the project, ranging from structural elements to finishes and fittings.
Material take off plays a vital role in cost estimation, as it provides accurate data for preparing material budgets and determining project costs. It helps project managers and estimators make informed decisions regarding the selection of materials, procurement, and resource allocation.
Moreover, material take off is not limited to the construction stage alone. It is an ongoing process that can be conducted at multiple stages of the project, such as during the conceptual design phase, bidding stage, or pre-construction stage. Each stage requires a detailed analysis to ensure accurate material quantities.
By conducting a thorough material take off, construction professionals can understand the scope of the project, avoid material shortages or excesses, plan logistics, and streamline the construction process. It provides a clear roadmap for material procurement, storage, and utilization throughout the project’s timeline.
Overall, material take off in construction sets the foundation for a well-executed and organized project. It aligns the construction team’s understanding of the materials required, streamlines the supply chain, and contributes to the successful delivery of the project within budget and schedule.
Importance of Material Take Off in Construction
The importance of material take off in construction cannot be overstated. It serves as a crucial step in the planning and execution of any construction project. Here are some key reasons why material take off is important:
- Accurate Cost Estimation: Material take off provides accurate data regarding the quantities of materials required for the project. This information helps in preparing detailed material budgets and estimating project costs. Accurate cost estimation is essential for securing funding, making informed business decisions, and ensuring profitability.
- Optimized Resource Allocation: By quantifying the materials needed, material take off allows for optimized resource allocation. It ensures that the right quantities of materials are procured and utilized, minimizing wastage and reducing project costs. Efficient resource allocation helps maintain a balanced inventory and prevents delays due to material shortages.
- Time Efficiency: Proper material take off enables construction professionals to plan the procurement and delivery of materials in advance. This helps in avoiding delays and ensuring a steady supply of materials, contributing to the timely completion of the project. Time efficiency is crucial to meet project deadlines and avoid costly schedule overruns.
- Enhanced Project Coordination: Material take off aligns the understanding of project stakeholders, including architects, engineers, contractors, and suppliers, about the materials required. This promotes effective communication and coordination, streamlining the construction process. Clear and accurate material take off ensures that everyone is on the same page and can work harmoniously towards project completion.
- Reduced Risk of Errors: Material take off involves a detailed analysis of project documentation, ensuring that every component is accounted for. This meticulous approach reduces the risk of errors and omissions, preventing costly rework. Accurate material take off minimizes the chances of design conflicts, improves constructability, and enhances project quality.
In summary, material take off is of paramount importance in construction. It enables accurate costing, optimized resource allocation, time efficiency, enhanced project coordination, and reduced risk of errors. Incorporating material take off as a standard practice ensures successful project outcomes and client satisfaction.
Process of Material Take Off in Construction
The process of material take off in construction involves several steps to ensure comprehensive and accurate quantification of required materials. While the specific process may vary depending on the project scope and complexity, here is a general overview of the steps involved:
- Review Project Documentation: Begin by carefully reviewing all project documents, including architectural and engineering drawings, specifications, and any other relevant documents. This step helps to understand the project scope, identify the various components, and determine the materials required for each.
- Identify Material Quantities: Analyze the project documents to identify the materials needed for each component of the project. This includes structural elements, such as concrete, steel, and lumber, as well as finishes, fittings, and equipment.
- Measure and Quantify: Use measurement tools and techniques to measure the dimensions of each component and calculate the quantities of materials required. This can be done manually using measuring tapes, scales, and counting units, or through digital tools such as computer-aided design (CAD) software.
- Create a Bill of Materials: Compile a comprehensive list, known as a bill of materials, which includes all the materials needed for the project. This list should specify the type, size, and quantity of each material required.
- Apply Resource Factors: Consider resource factors such as material waste, transportation, and installation losses, and adjust the quantities accordingly. This step ensures that the material take off accounts for all potential factors that may affect the actual quantity needed.
- Validate and Verify: Double-check the material take off calculations for accuracy and completeness. Cross-reference the bill of materials with project specifications and industry standards to ensure compliance and correctness.
- Storage and Inventory Planning: Incorporate storage and inventory considerations into the material take off process. Determine how the materials will be stored and managed on-site, including any special handling requirements or storage limitations.
- Update and Revise: As the project progresses and design changes occur, periodically update and revise the material take off to reflect the latest requirements. This ensures that the construction team is always working with accurate and up-to-date information.
The process of material take off requires attention to detail, technical expertise, and thorough documentation review. It is important to involve multiple stakeholders, such as architects, engineers, suppliers, and contractors, to gather input and validate the material quantities.
By following a systematic and disciplined approach to material take off, construction professionals can ensure that the project has the necessary materials, avoid delays from shortages, improve cost estimation accuracy, and streamline the overall construction process.
Tools and Software for Material Take Off in Construction
Advancements in technology have revolutionized the process of material take off in construction. Today, there are a variety of tools and software available that streamline and enhance the accuracy of material quantification. Here are some commonly used tools and software for material take off:
- Spreadsheets: Programs like Microsoft Excel or Google Sheets are widely used for manual material take off. They allow for easy organization, calculation, and manipulation of data, making it convenient to create detailed bills of materials.
- Estimating Software: Dedicated construction estimating software, such as PlanSwift, On-Screen Takeoff, or Bluebeam Revu, offer advanced features specifically designed for material take off. These tools provide digital takeoff capabilities, automated calculations, integration with project documents, and customizable reporting.
- Building Information Modeling (BIM) software: BIM software, like Autodesk Revit or ArchiCAD, allows for virtual modeling of the entire construction project. With BIM, material take off can be performed directly from the 3D model, enabling accurate and automated calculations based on the virtual building components.
- Laser Measuring Devices: Laser measuring devices, such as laser distance meters or laser levels, offer precise measurements that contribute to accurate material take off. These devices eliminate the need for manual measuring and can quickly measure distances, areas, and volumes.
- Mobile Applications: There are mobile applications available for material take off, which allow construction professionals to perform calculations and measurements on-site using their smartphones or tablets. These apps often integrate with cloud storage, enabling seamless collaboration and access to project data.
- Online Databases: Online databases, such as RSMeans or CostX, provide access to comprehensive material cost data and libraries of commonly used construction components. These databases assist in cost estimation and material take off by offering up-to-date pricing information.
It is worth noting that selecting the right tools and software for material take off depends on the project requirements, team capabilities, and budget. Integrating digital tools and software into the material take off process can significantly improve efficiency, reduce errors, and enhance collaboration among project stakeholders.
When incorporating tools and software, it is essential to ensure proper training and familiarization to maximize the benefits and minimize any potential challenges. Additionally, regular updates and maintenance of the selected tools and software are necessary to keep up with industry advancements and changing project needs.
Ultimately, leveraging the power of technology in material take off enhances accuracy, saves time, and contributes to the successful execution of construction projects.
Material take off in construction is the process of calculating the quantity of materials needed for a project. It’s important to be accurate to avoid shortages or excess. Use digital tools for efficiency.
Read more: What Takes Stickers Off Glass
Benefits of Material Take Off in Construction
Material take off plays a significant role in the construction industry, offering several benefits that contribute to the success of a project. From cost savings to improved project coordination, here are some key advantages of material take off:
- Accurate Cost Estimation: Material take off provides precise quantities of materials required for the project, enabling accurate cost estimation. This helps in preparing detailed budgets, reducing the risk of cost overruns, and ensuring profitability.
- Economic Material Procurement: With accurate material take off, construction professionals can procure the exact quantities of materials needed, avoiding excess inventory or shortages. This ensures economic procurement and prevents wastage.
- Timely Resource Planning: By knowing the exact requirements of materials, material take off facilitates proper planning and timely procurement. This leads to a seamless construction process with minimal delays.
- Improved Project Coordination: Material take off enhances project coordination as all stakeholders have a clear understanding of the materials required. This minimizes miscommunications, conflicts, and delays, leading to better project outcomes.
- Enhanced Construction Productivity: Accurate material take off eliminates guesswork and promotes efficient resource allocation. This helps in optimizing construction productivity by ensuring the availability of the right materials at the right time.
- Design Optimization: Material take off allows project teams to closely analyze and review materials required for different building components. By doing so, they can explore options for design optimization, choosing materials that meet both functional and cost-effective criteria.
- Cost Control: Through accurate material take off, project managers can exercise better control over costs. By knowing the exact material quantities, they can negotiate better prices with suppliers and avoid unexpected expenses.
- Reduced Rework: Accurate material take off helps in preventing shortages or incorrect material usage, reducing the need for rework. This saves both time and money, allowing for smoother project execution.
- Improved Sustainability: By quantifying materials with precision, material take off promotes sustainable construction practices. This enables the selection and usage of environmentally friendly and energy-efficient materials, contributing to sustainable building practices.
- Client Satisfaction: Accurate material take off ensures that the project is delivered as per the client’s expectations, within the specified budget and timeline. This enhances client satisfaction and strengthens the professional reputation of the construction team.
In summary, material take off offers numerous benefits, including accurate cost estimation, economic material procurement, timely resource planning, improved project coordination, enhanced productivity, design optimization, cost control, reduced rework, improved sustainability, and client satisfaction. Integrating material take off as a standard practice in construction projects is crucial for achieving successful outcomes and maintaining a competitive edge in the industry.
Challenges and Limitations of Material Take Off in Construction
While material take off is a vital process in construction, it is not without its challenges and limitations. Construction professionals must be aware of these potential obstacles and take proactive measures to overcome them. Here are some common challenges and limitations of material take off:
- Data Accuracy: Material take off relies heavily on accurate project documentation. Inaccurate or incomplete drawings, specifications, or changes in design can lead to incorrect material quantification and subsequent issues during construction.
- Complexity and Variability: Construction projects can be complex and have diverse requirements. Material take off must consider the intricacies of various components, finishes, fittings, and equipment, which can be challenging and time-consuming.
- Changing Project Scope: It is not uncommon for construction projects to experience changes in scope during the course of execution. These changes can significantly impact material requirements and necessitate ongoing updates to the material take off.
- Limited Project Information: Sometimes, project documentation may not provide all the necessary details for accurate material take off. Insufficient or ambiguous information can lead to assumptions and potential errors in quantity calculations.
- Vendor Availability and Pricing: Material take off relies on accurate data regarding material availability and pricing from suppliers. Unforeseen changes in vendor availability or price fluctuations can disrupt the procurement process and impact project budgets.
- Human Error: Despite technological advancements, human error can still occur during the material take off process. Mistakes in measurement, calculation, or data entry can lead to inaccuracies in the final material quantities.
- Technological Limitations: The adoption of digital tools and software for material take off may require a learning curve and technical expertise. Additionally, the initial investment in software licenses and training can be a limitation for some construction companies.
- Time Constraints: Material take off requires careful analysis and calculation, which can be time-consuming, especially for large or complex projects. Time constraints may prevent a thorough and meticulous material take off, potentially leading to errors and omissions.
While these challenges and limitations exist, construction professionals can mitigate their impact through proactive measures. This includes ensuring thorough documentation review, utilizing advanced software and tools, collaborating closely with vendors, continuously updating and validating the material take off, and fostering effective communication among project stakeholders.
By recognizing and addressing these challenges, construction teams can enhance the accuracy, efficiency, and effectiveness of material take off, leading to improved project outcomes and client satisfaction.
Best Practices for Material Take Off in Construction
To ensure accurate material quantification and streamline the construction process, it is essential to follow best practices for material take off. By implementing these practices, construction professionals can maximize efficiency, minimize errors, and improve project outcomes. Here are some key best practices for material take off in construction:
- Thoroughly Review Project Documentation: Begin the material take off process by carefully reviewing all project documentation, including architectural and engineering drawings, specifications, and any relevant documents. This helps in understanding the project scope and identifying all required materials.
- Engage Stakeholders: Involve all relevant project stakeholders, such as architects, engineers, contractors, and suppliers, in the material take off process. Collaborating with the team ensures comprehensive and accurate identification of materials and fosters a shared understanding of project requirements.
- Utilize Digital Tools and Software: Consider using advanced software and digital tools specifically designed for material take off. These tools automate calculations, enable digital measurements, and improve accuracy and efficiency. They also facilitate collaboration and real-time updates among project team members.
- Validate Measurements and Quantities: Double-check all measurements and quantities during the material take off process. Validate the accuracy of measurements using precise tools such as laser measuring devices and ensure that quantities are correctly quantified, accounting for any resource factors or adjustments.
- Regularly Update the Material Take Off: As the project progresses and design changes occur, update the material take off regularly. This ensures that the quantities of materials are always up-to-date, minimizing errors and discrepancies that can arise due to outdated information.
- Collaborate with Suppliers: Maintain close communication with suppliers to obtain accurate pricing, availability, and delivery timelines. Collaborating with suppliers helps in aligning the material take off with the availability of materials in the market, ensuring optimized procurement.
- Cross-Check with Industry Standards: Cross-reference the material take off with industry standards, codes, and specifications. Ensure that the selected materials and quantities comply with the required standards, avoiding conflicts and ensuring proper functionality and durability.
- Document Changes and Revisions: Document any changes or revisions made to the material take off throughout the project. This ensures transparency and allows project stakeholders to trace the modifications made, preventing confusion and potential disputes.
- Invest in Training and Skill Development: Provide training to construction professionals involved in the material take off process. This includes training on tools, software, measurement techniques, and industry best practices. Enhancing skills and knowledge improves accuracy and efficiency.
- Continuous Improvement and Evaluation: Regularly evaluate and assess the material take off process to identify areas for improvement. Learn from past projects and implement feedback, making adjustments to enhance the accuracy and efficiency of future material take off processes.
By following these best practices, construction professionals can ensure accurate material quantification, streamline procurement processes, and minimize errors and delays. Implementing robust material take off practices contributes to the success of construction projects, leading to improved project outcomes and client satisfaction.
Conclusion
Material take off is a vital process in the world of construction. It involves quantifying and estimating the required materials for a project, ensuring accurate cost estimation, optimized resource allocation, and timely project delivery. By carefully reviewing project documentation, identifying material quantities, and utilizing tools and software, construction professionals can streamline this process and improve the overall construction process.
The benefits of material take off are numerous. Accurate cost estimation enables informed decision-making and ensures project profitability. Timely resource planning and improved project coordination contribute to smoother project execution and enhanced productivity. Design optimization, cost control, and reduced rework are additional advantages that material take off provides.
However, material take off does come with its challenges and limitations. Issues such as data accuracy, complexity, changing project scope, and limited project information can hinder the material take off process. It is crucial to address these challenges through thorough documentation review, advanced tools and software, and collaborative efforts among project stakeholders.
To achieve accurate and efficient material take off, construction professionals should adhere to best practices. Thoroughly reviewing project documentation, utilizing digital tools, validating measurements and quantities, and collaborating with suppliers are some key practices to follow. Regular updates to the material take off, cross-checking with industry standards, and investing in training and skill development are also essential for success.
In conclusion, material take off is a critical aspect of the construction process that cannot be overlooked. It ensures accurate material quantities, cost control, and efficient resource allocation. By incorporating best practices and leveraging technology, construction professionals can overcome challenges, optimize the construction process, and deliver successful projects within budget and schedule.
Frequently Asked Questions about What Is Material Take Off In Construction
Was this page helpful?
At Storables.com, we guarantee accurate and reliable information. Our content, validated by Expert Board Contributors, is crafted following stringent Editorial Policies. We're committed to providing you with well-researched, expert-backed insights for all your informational needs.
0 thoughts on “What Is Material Take Off In Construction”