Home>Furniture & Design>Interior Design Trends>How Is Glass Manufactured
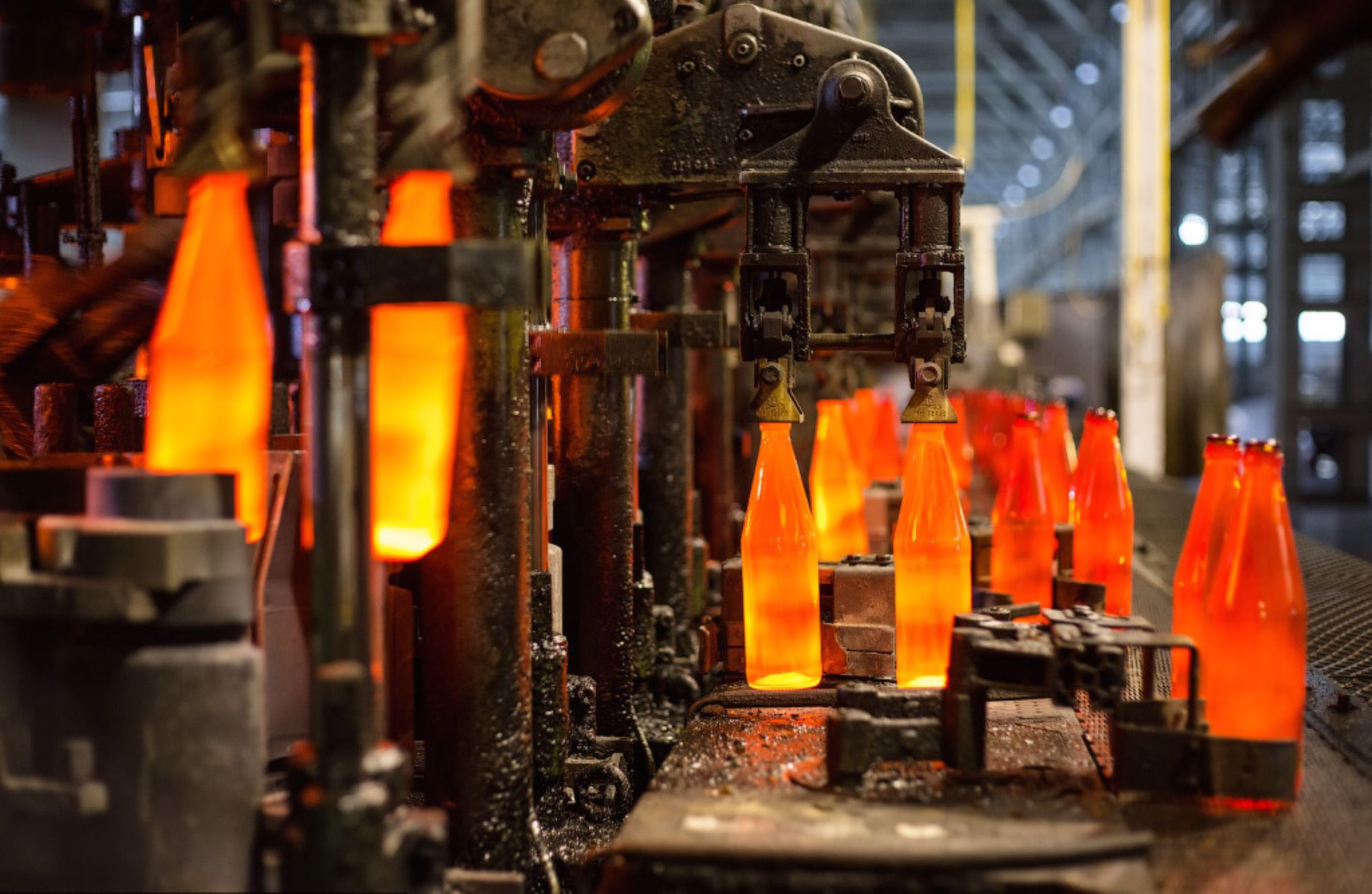
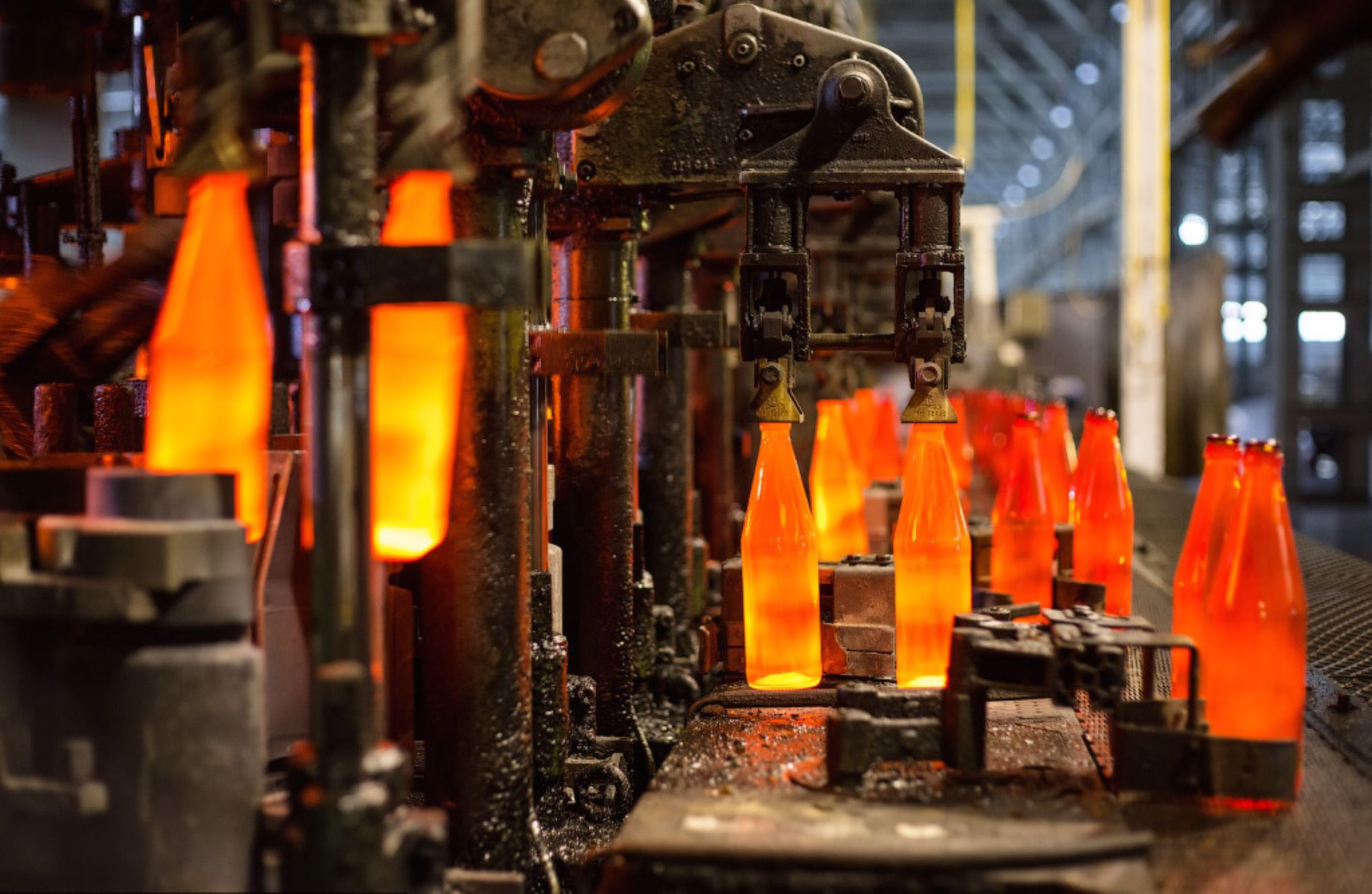
Interior Design Trends
How Is Glass Manufactured
Modified: February 18, 2024
Discover the intricate process of glass manufacturing and its impact on interior design trends. Explore the innovative techniques and materials used in creating stunning glass products.
(Many of the links in this article redirect to a specific reviewed product. Your purchase of these products through affiliate links helps to generate commission for Storables.com, at no extra cost. Learn more)
Introduction
Glass is a versatile and ubiquitous material that has been an integral part of human civilization for centuries. From the windows in our homes to the screens of our smartphones, glass is all around us, serving both functional and aesthetic purposes. Understanding the manufacturing process of glass provides insight into the intricate and fascinating journey from raw materials to the finished product.
The process of manufacturing glass involves a series of carefully orchestrated steps, each contributing to the creation of this transparent and durable material. By delving into the intricacies of glass production, we gain a deeper appreciation for the craftsmanship and technology involved in shaping this essential material.
In the following sections, we will explore the raw materials used in glass manufacturing, the intricate processes of melting and refining, the art of forming and shaping glass, the crucial steps of annealing and tempering, and the meticulous finishing and packaging that ensure the quality and safety of the final product. Each stage of the manufacturing process plays a pivotal role in producing glass that meets the diverse needs of industries and consumers worldwide.
As we embark on this journey through the manufacturing of glass, we will uncover the blend of artistry and precision that defines this industry. From the ancient techniques of glassblowing to the cutting-edge innovations in modern glass production, the evolution of glass manufacturing reflects the ingenuity and adaptability of human craftsmanship.
Join us as we unravel the captivating story of how raw materials are transformed into the transparent marvel that is glass, shaping the world around us in ways both seen and unseen.
Key Takeaways:
- The raw materials for making glass, like silica sand and soda ash, are carefully selected to create strong, clear glass suitable for various uses, from high-quality glassware to architectural glazing.
- The process of making glass involves melting, shaping, and treating the glass to ensure it’s strong and safe for everyday use. From intricate designs to durable safety glass, the possibilities are endless.
Read more: Where Is Bosch HVAC Manufactured
Raw Materials for Glass Manufacturing
The process of manufacturing glass begins with the selection and preparation of raw materials, which are essential for creating the diverse range of glass products that serve various industries and applications. The primary components used in glass manufacturing include silica sand, soda ash, and limestone, each playing a crucial role in the chemical composition and properties of the final glass product.
Silica Sand
Silica sand, also known as quartz sand, is the most abundant raw material used in glass production. It serves as the primary source of silicon dioxide (SiO2), a key component that imparts strength and durability to the glass. The high purity of silica sand is essential to ensure the clarity and transparency of the glass, making it suitable for applications where optical quality is paramount, such as in the production of high-quality glassware and optical lenses.
Soda Ash
Soda ash, or sodium carbonate, acts as a flux in the glass manufacturing process, lowering the melting point of the silica sand and facilitating the fusion of the raw materials. This fluxing agent plays a vital role in reducing the energy required for the melting process, thereby enhancing the efficiency of glass production. Additionally, soda ash contributes to the chemical stability and workability of the glass, making it an indispensable component in the creation of various glass formulations, including flat glass, containers, and fiberglass.
Limestone
Limestone, or calcium carbonate, serves as a stabilizer in the glass manufacturing process, helping to control the thermal expansion and viscosity of the molten glass. By carefully regulating these properties, limestone contributes to the workability and formability of the glass, enabling the production of intricate shapes and designs. Furthermore, limestone aids in the refinement of the glass composition, ensuring that the final product exhibits the desired mechanical and chemical properties required for specific applications, such as in architectural glass and automotive glazing.
In addition to these primary raw materials, glass production may involve the use of various additives and cullet, which are recycled glass fragments. These supplementary materials can impart specific characteristics to the glass, such as coloration, UV resistance, or thermal insulation, expanding the versatility and functionality of the final glass products.
The careful selection and precise combination of these raw materials form the foundation of glass manufacturing, influencing the optical, mechanical, and thermal properties of the finished glass products. By understanding the significance of these raw materials, we gain insight into the intricate chemistry and engineering involved in creating glass that meets the diverse needs of modern society.
Read more: Where Is Acopa Tableware Manufactured?
Melting and Refining
The process of melting and refining is a pivotal stage in the manufacturing of glass, where the carefully selected raw materials undergo a transformative journey to become the molten glass that will be shaped into the desired forms. This stage involves a delicate balance of temperature control, chemical reactions, and refining techniques to ensure the production of high-quality glass with the desired properties.
The raw materials, including silica sand, soda ash, and limestone, are meticulously measured and mixed in precise proportions before being fed into a furnace. The furnace, typically fueled by natural gas or electricity, generates intense heat, reaching temperatures exceeding 1700°C (3092°F). At these extreme temperatures, the raw materials undergo a remarkable transformation, transitioning from solid particles to a viscous, molten state.
As the raw materials melt, chemical reactions occur within the furnace, leading to the decomposition of the soda ash and the release of carbon dioxide. This process, known as decarbonation, plays a crucial role in refining the glass composition, removing impurities, and enhancing the clarity and stability of the molten glass. Additionally, the high temperatures facilitate the homogenization of the glass melt, ensuring uniformity in chemical composition and properties.
To further refine the molten glass, various techniques are employed to remove any remaining bubbles, stones, or other imperfections that could compromise the quality of the final product. One such technique is the use of refining agents, such as arsenic and antimony compounds, which help to facilitate the release of trapped gases and promote the removal of impurities. This refining process is essential for achieving the desired optical clarity and structural integrity of the glass.
The molten glass is then carefully monitored and sampled to assess its chemical composition and temperature, ensuring that it meets the stringent quality standards required for further processing. Once the molten glass has been refined to the desired specifications, it is ready to undergo the next stage of forming and shaping, where it will be molded and transformed into a myriad of glass products that enrich our daily lives.
The artistry and precision involved in the melting and refining of glass exemplify the intricate fusion of science and craftsmanship, shaping raw materials into a transparent marvel that serves as a cornerstone of modern industry and design. This transformative process lays the foundation for the diverse applications of glass, from architectural glazing and automotive components to exquisite glass art and innovative technological devices.
Forming and Shaping
Once the molten glass has been meticulously refined, it enters the captivating stage of forming and shaping, where it undergoes a remarkable metamorphosis into a diverse array of glass products that serve both functional and aesthetic purposes. This stage of the glass manufacturing process showcases the fusion of artistry and engineering, as the molten glass is carefully manipulated and molded into the desired forms through a series of precise techniques and innovative technologies.
One of the primary methods of forming glass is through the process of blowing, where skilled artisans, known as glassblowers, use their expertise to shape the molten glass into intricate designs. This ancient technique, dating back to the Roman Empire, involves gathering a molten glob of glass on the end of a blowpipe and skillfully inflating it to create hollow forms, such as vases, ornaments, and glassware. The art of glassblowing exemplifies the harmonious blend of tradition and innovation, as contemporary glassblowers continue to push the boundaries of creativity and craftsmanship, producing exquisite works of art that captivate the imagination.
In addition to glassblowing, modern manufacturing processes have introduced advanced techniques such as pressing, casting, and extrusion, which enable the production of complex glass shapes and structures with unparalleled precision. Pressing involves shaping the molten glass between two mold surfaces to create intricate patterns and textures, while casting utilizes molds to form glass into specific designs and dimensions. Extrusion, on the other hand, involves forcing the molten glass through a shaped opening to produce continuous lengths of glass with uniform cross-sections, commonly used in the production of glass fibers and tubing.
Furthermore, the advent of innovative technologies, such as computer-aided design (CAD) and automated manufacturing systems, has revolutionized the precision and efficiency of glass forming and shaping processes. These advancements have expanded the possibilities for creating custom-designed glass products, architectural panels, and intricate glass components for electronic devices, elevating the role of glass in contemporary design and engineering.
The stage of forming and shaping represents the transformative power of human creativity and ingenuity, as the molten glass is sculpted into an astonishing variety of products that enhance our daily experiences. Whether it's the sleek curves of a modern architectural façade, the delicate contours of a handcrafted glass sculpture, or the precision-engineered components of electronic displays, the art of forming and shaping glass continues to inspire and enrich our world with its boundless potential and enduring beauty.
Annealing and Tempering
Annealing and tempering are critical processes in the manufacturing of glass, playing a pivotal role in enhancing the structural integrity, durability, and thermal resistance of the finished glass products. These carefully controlled thermal treatments impart essential properties to the glass, ensuring that it can withstand the rigors of everyday use and meet the stringent performance requirements of diverse applications.
Annealing
Annealing is a process of controlled cooling that relieves internal stresses within the glass, enhancing its mechanical strength and resistance to thermal shock. After the glass has been formed and shaped, it retains residual stresses that can compromise its stability and durability. To alleviate these stresses, the glass is gradually cooled in a carefully regulated annealing lehr, or kiln, where it undergoes a series of temperature reductions over a specified period.
During annealing, the glass is held at a predetermined temperature, allowing the internal stresses to relax and the molecular structure to stabilize. This gradual cooling process minimizes the risk of spontaneous breakage and ensures that the glass achieves a state of equilibrium, free from internal tensions. The controlled annealing process is particularly crucial for glass products intended for architectural glazing, automotive applications, and high-precision optical components, where structural integrity and reliability are paramount.
Read more: Where Are Levolor Blinds Manufactured
Tempering
Tempering, also known as toughening, is a thermal treatment that further enhances the strength and safety of the glass by inducing surface compression and internal tension. This process involves heating the glass to a high temperature, followed by rapid and uniform cooling, creating a state of balanced internal stresses within the glass. The resulting tempered glass exhibits exceptional resistance to mechanical impact, bending, and thermal fluctuations, making it an ideal choice for applications requiring enhanced safety and durability.
Tempered glass is widely used in architectural and interior design, as it provides superior protection against breakage and reduces the risk of injury due to its characteristic behavior when fractured. Additionally, tempered glass is a fundamental component of automotive safety systems, serving as a crucial element in the construction of windshields, side windows, and rear windows. The remarkable strength and resilience of tempered glass have also made it a preferred choice for consumer electronics, furniture, and household appliances, where safety and durability are essential considerations.
The annealing and tempering processes exemplify the meticulous attention to detail and engineering precision that define the production of high-quality glass. By subjecting the glass to these specialized thermal treatments, manufacturers ensure that the finished products exhibit the desired strength, safety, and reliability, meeting the diverse needs of industries and consumers worldwide. The art of annealing and tempering represents a testament to the enduring legacy of glass as a material that seamlessly combines functionality, safety, and aesthetic appeal in the modern world.
Finishing and Packaging
The final stages of the glass manufacturing process encompass the crucial steps of finishing and packaging, where meticulous attention to detail and quality control ensures that the finished glass products meet the highest standards of excellence. From surface treatments that enhance functionality and aesthetics to the careful packaging that safeguards the integrity of the glass, these concluding processes play a pivotal role in delivering glass products that inspire confidence and admiration.
Surface Treatments
After the glass has undergone forming, shaping, and thermal treatments, it may undergo various surface treatments to enhance its functionality and visual appeal. One common surface treatment is the application of coatings or films that provide specific properties, such as UV protection, glare reduction, or thermal insulation. These specialized coatings not only improve the performance of the glass in diverse environments but also contribute to energy efficiency and sustainability in architectural and automotive applications.
In addition to coatings, the process of finishing may involve techniques such as polishing, grinding, or etching to achieve desired surface textures and optical clarity. Polishing and grinding refine the surface of the glass, removing imperfections and creating a smooth, lustrous finish that enhances transparency and light transmission. On the other hand, etching introduces decorative patterns or frosted effects, adding a touch of elegance and privacy to glass surfaces in interior design and artistic applications.
Quality Inspection
Before the glass products are packaged for distribution, they undergo rigorous quality inspection to ensure that they meet the specified standards for dimensional accuracy, visual clarity, and structural integrity. Advanced optical inspection systems and precision measurement tools are employed to scrutinize the glass for any defects, such as surface irregularities, optical distortions, or dimensional variations. This meticulous quality control process is essential for identifying and rectifying any imperfections, guaranteeing that only flawless glass products reach the hands of consumers and businesses.
Read more: Where Is Oxbox HVAC Manufactured
Packaging and Logistics
The final step in the manufacturing process involves the careful packaging of the glass products to protect them during transportation and storage. Depending on the type and size of the glass products, specialized packaging solutions, such as crates, pallets, or custom-designed containers, are employed to ensure secure handling and minimize the risk of damage. Additionally, protective padding and cushioning materials are utilized to safeguard the glass against impact and vibration, maintaining its pristine condition until it reaches its destination.
Furthermore, efficient logistics and supply chain management play a vital role in coordinating the packaging, labeling, and distribution of the glass products to their intended markets. From custom orders for architectural glazing to mass-produced glassware for retail, the seamless coordination of packaging and logistics ensures that the glass products are delivered on time and in optimal condition, ready to enrich the lives of consumers and contribute to the built environment.
In essence, the processes of finishing and packaging represent the culmination of precision engineering, craftsmanship, and quality assurance that define the art of glass manufacturing. By meticulously attending to the surface treatments, quality inspection, and packaging requirements, manufacturers uphold the legacy of glass as a material of enduring beauty, functionality, and reliability, ensuring that it continues to shape our world with its timeless allure and indispensable utility.
Frequently Asked Questions about How Is Glass Manufactured
Was this page helpful?
At Storables.com, we guarantee accurate and reliable information. Our content, validated by Expert Board Contributors, is crafted following stringent Editorial Policies. We're committed to providing you with well-researched, expert-backed insights for all your informational needs.
0 thoughts on “How Is Glass Manufactured”