Home>Home Maintenance>What Is The Best Ventilation System For Welding Operations
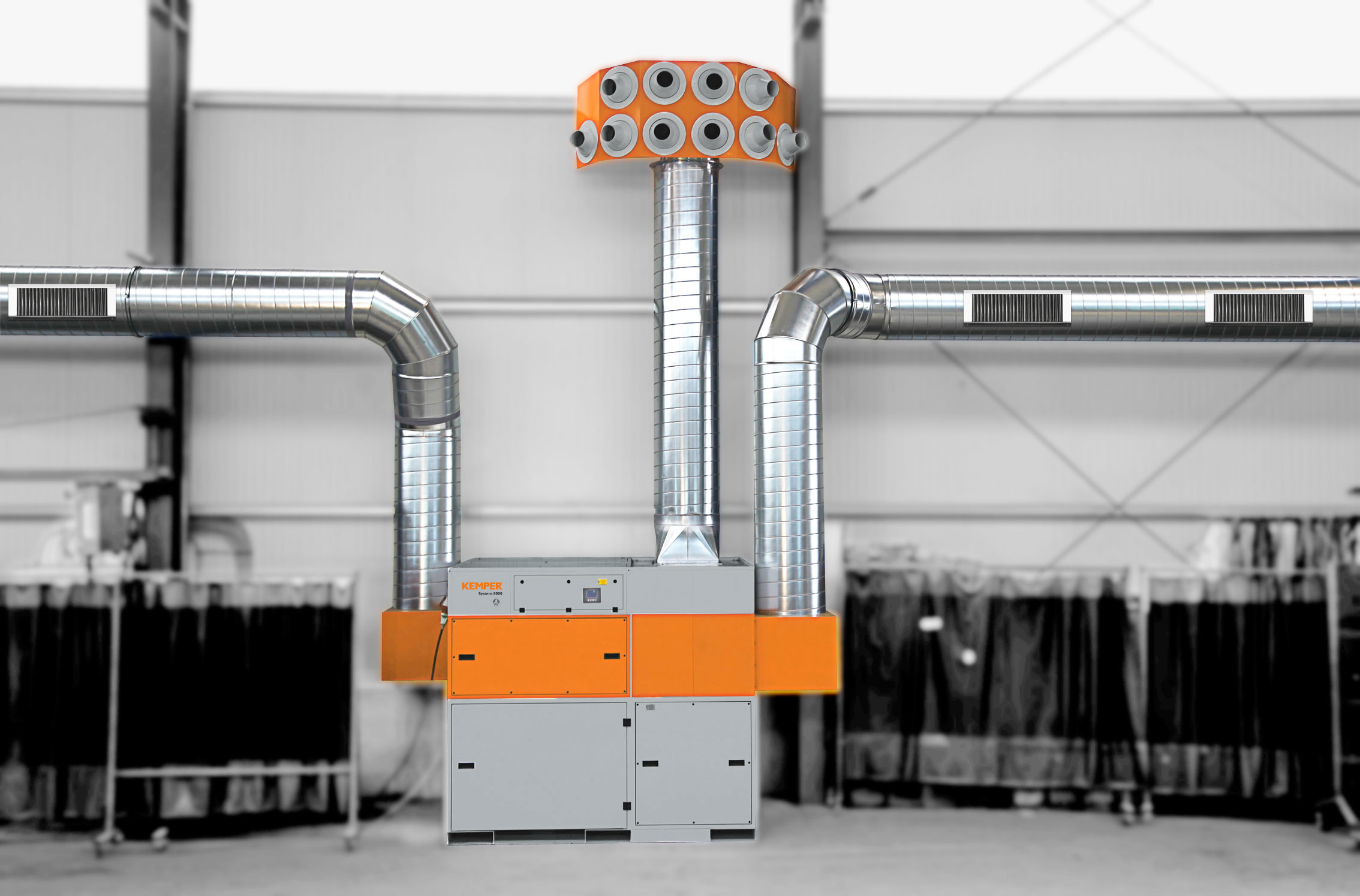
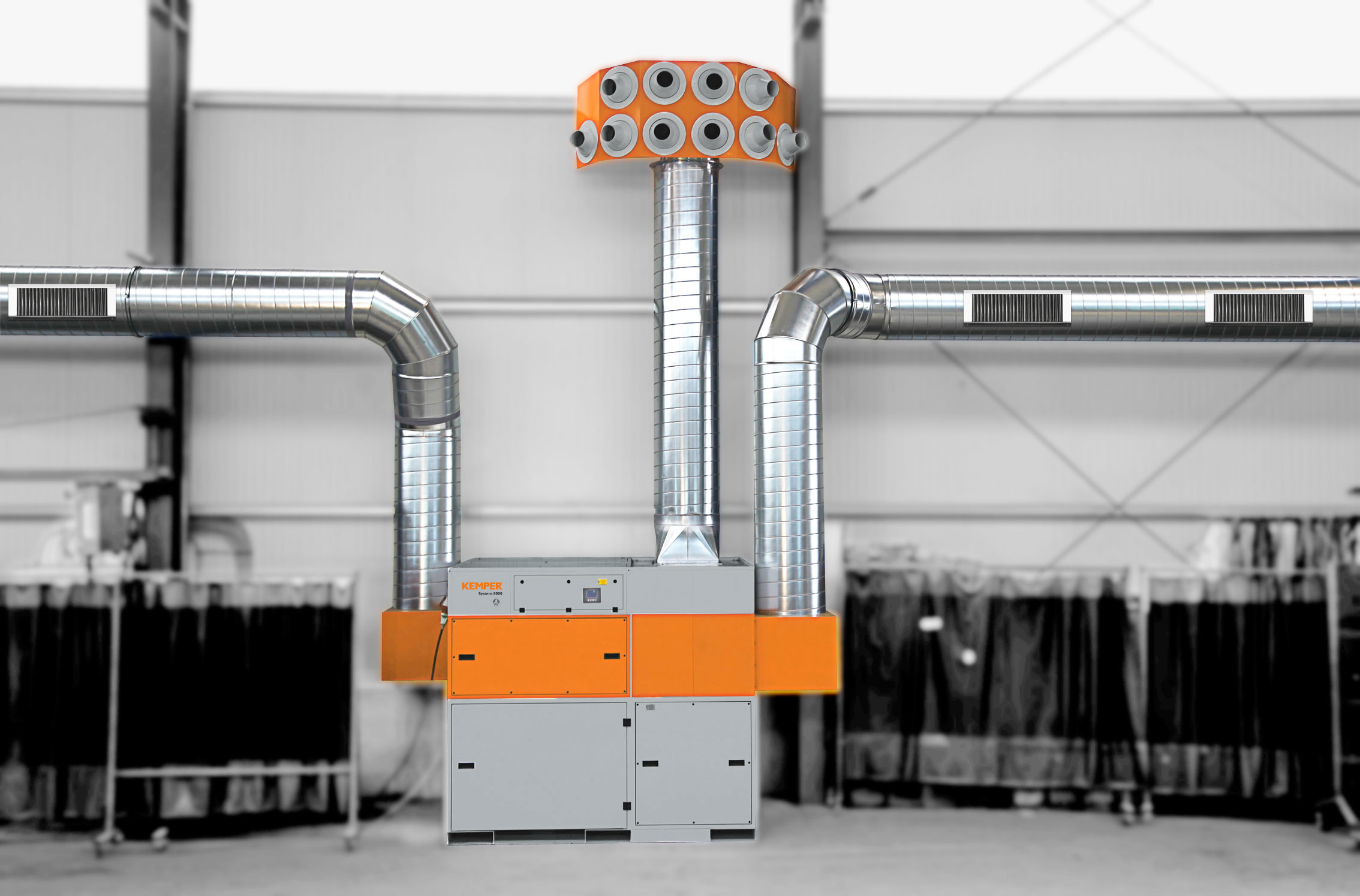
Home Maintenance
What Is The Best Ventilation System For Welding Operations
Modified: March 6, 2024
Find the best ventilation system for welding operations to ensure a safe and healthy environment at home. Optimize your home maintenance with effective ventilation solutions.
(Many of the links in this article redirect to a specific reviewed product. Your purchase of these products through affiliate links helps to generate commission for Storables.com, at no extra cost. Learn more)
Introduction
When it comes to welding operations, ventilation plays a crucial role in maintaining a safe and productive working environment. Welding generates fumes, gases, and smoke that can be harmful if not managed properly. Inhaling these pollutants can lead to respiratory problems, eye irritation, and even long-term health issues. Therefore, implementing an effective ventilation system is essential to ensure the well-being of workers and maintain the quality of the work environment.
A good ventilation system helps to remove hazardous airborne contaminants, provides fresh air circulation, and controls the temperature and humidity levels in the workspace. It is essential for both the health and safety of welders and for maintaining the quality and integrity of the welding process.
In this article, we will explore the different types of ventilation systems commonly used in welding operations, consider their effectiveness, cost implications, and maintenance requirements. Additionally, we will look at the regulations and guidelines put forth by regulatory bodies to help you choose the best ventilation system for your welding operations.
Whether you are a professional welder running a fabrication shop or a DIY enthusiast working on projects at home, understanding the importance of ventilation and selecting the right system will greatly contribute to a safer and more productive welding environment.
Key Takeaways:
- Proper ventilation in welding operations is crucial for protecting workers’ health, complying with regulations, and maintaining a safe and productive work environment.
- Choosing the right ventilation system, regular maintenance, and compliance with regulations are essential for creating a safe and healthy work environment in welding operations.
Importance of Ventilation in Welding Operations
In many welding operations, the process involves the melting of metal and the generation of fumes, gases, and smoke. These airborne contaminants can pose serious health risks if not properly managed. They can contain hazardous substances such as metal oxides, ozone, and other toxic gases. Prolonged exposure to these pollutants can result in respiratory problems, eye irritation, and even chronic health conditions.
Implementing an effective ventilation system in welding operations is crucial for several reasons:
- Worker Health and Safety: The primary reason for having proper ventilation in welding operations is to protect the health and safety of workers. By removing airborne contaminants from the work area, ventilation systems help minimize the risk of respiratory illnesses caused by inhaling welding fumes and gases. It also reduces the chances of eye irritation and other health issues associated with welding operations.
- Compliance with Regulations: Many regulatory bodies, such as the Occupational Safety and Health Administration (OSHA) in the United States, have specific guidelines regarding ventilation requirements in welding operations. These regulations aim to protect workers from exposure to hazardous substances. By implementing the recommended ventilation system, you ensure compliance with these regulations and avoid potential penalties or legal issues.
- Quality of Work Environment: Adequate ventilation not only protects workers’ health but also helps maintain the quality of the work environment. Welding fumes and smoke can obstruct visibility, making it difficult for welders to perform their tasks accurately. A ventilation system that effectively removes these pollutants ensures better visibility and improves the overall quality and precision of the welding process.
- Productivity and Efficiency: A well-ventilated workspace contributes to increased productivity and efficiency. When welders are not concerned about their health or discomfort caused by poor air quality, they can focus more on their work. Proper ventilation ensures a comfortable and conducive environment, allowing welders to work efficiently without interruptions.
- Cost Savings: Implementing an appropriate ventilation system can also result in cost savings. By reducing the health risks associated with welding fumes and gases, employers can potentially avoid medical expenses, workers’ compensation claims, and downtime due to worker illnesses. Moreover, a well-ventilated workspace may also contribute to longer equipment life and reduced maintenance costs.
Considering the importance of worker health and safety, regulatory compliance, quality of work, productivity, and cost implications, it is crucial to invest in an effective ventilation system for welding operations. In the following sections, we will discuss the various types of ventilation systems commonly used in welding operations and examine their effectiveness in mitigating airborne contaminants.
Types of Ventilation Systems for Welding Operations
There are several types of ventilation systems that can be used in welding operations to effectively control and remove airborne contaminants. The choice of system depends on factors such as the size of the workspace, the type of welding being performed, and the availability of resources. Here are the common types of ventilation systems used in welding operations:
- Natural Ventilation: Natural ventilation relies on the flow of air through open doors, windows, or other openings in the workspace. While it may be the simplest form of ventilation, it is not always the most effective, especially in enclosed or indoor welding environments. Natural ventilation can help to some extent in removing fumes and smoke, but it may not provide adequate control and extraction of contaminants generated during welding.
- Local Exhaust Ventilation (LEV): Local exhaust ventilation systems, also known as fume extraction systems, are designed to capture and remove welding fumes and gases at the source. They typically consist of hoods or extraction arms placed close to the welding area to directly collect the contaminants before they disperse into the surrounding air. These systems are highly effective in controlling exposure to welding fumes and gases and are commonly used in welding booths or confined spaces.
- Dilution Ventilation: Dilution ventilation involves the use of general ventilation systems, such as fans or air conditioning units, to dilute and disperse the contaminants in the workplace. This type of ventilation is more suitable for larger workshops or open-air welding operations. While dilution ventilation may not provide the same level of control as local exhaust ventilation, it can be effective in reducing the concentration of contaminants in the air and maintaining a healthier work environment.
- Filtered Air Supply: Filtered air supply systems involve the use of powered air purifying respirators (PAPRs) or supplied air respirators (SARs) to provide clean, filtered air to the welder. These systems are particularly useful in situations where it is challenging to implement other ventilation methods, such as when working in confined spaces without adequate exhaust ventilation. Filtered air supply systems provide the welder with fresh air to breathe, ensuring their safety and minimizing exposure to welding fumes and gases.
Each type of ventilation system has its advantages and limitations. Understanding the specific requirements of your welding operations and the characteristics of each system will help you make an informed decision on the most suitable ventilation system to implement. In the next section, we will delve into the factors you should consider when choosing a ventilation system for your welding operations.
Natural Ventilation
Natural ventilation is a simple and cost-effective method of providing air circulation in welding operations. It relies on the use of existing openings such as doors, windows, or vents to allow fresh air to enter and stale air to exit the workspace. While natural ventilation may not be as effective as other types of ventilation systems in controlling and removing welding fumes and gases, it still offers some benefits in certain situations.
Here are some key points about natural ventilation:
- Airflow: Natural ventilation relies on the natural movement of air due to temperature and pressure differences. By strategically positioning openings, such as doors and windows, in the workspace, you can create a continuous flow of fresh air.
- Limitations: Natural ventilation may not be suitable for all welding operations, especially in enclosed or indoor environments. It may not be sufficient to effectively remove welding fumes and gases, which can lead to health risks for workers.
- Enhancements: To improve the effectiveness of natural ventilation, you can consider adding fans to assist in airflow or installing adjustable louvers in windows or vents to control the direction and volume of air entering and exiting the workspace.
- Safety Precautions: While natural ventilation may not be as effective as other systems, it is still important to take safety precautions. Ensure that there is an adequate supply of fresh air and that workers are not exposed to excessive concentrations of harmful fumes and gases.
- Open-air Welding: Natural ventilation is more suitable for open-air welding operations, where the workspace is exposed to the outdoor environment. In such cases, natural airflow can help in dissipating welding fumes and smoke.
While natural ventilation may not be the most comprehensive method for controlling airborne contaminants in welding operations, it can still serve as a supplemental measure to improve air circulation. However, in situations where it is not sufficient to ensure worker safety and compliance with regulations, it is advisable to consider other types of ventilation systems, such as local exhaust ventilation or dilution ventilation.
It is important to evaluate the specific requirements and limitations of your welding operations and consult with ventilation experts to determine the most effective solution for your workspace. In the next section, we will explore the benefits and considerations of local exhaust ventilation, which is a commonly used ventilation system in welding operations.
Local Exhaust Ventilation
Local exhaust ventilation (LEV) is a highly effective ventilation system commonly used in welding operations to control and capture airborne contaminants directly at the source. This system utilizes hoods or extraction arms placed near the welding area to effectively capture and remove welding fumes, gases, and smoke.
Here are some key points about local exhaust ventilation:
- Capture Efficiency: Local exhaust ventilation is designed to have high capture efficiency, ensuring that welding fumes and gases are captured as close to the source as possible. This is achieved by positioning extraction hoods or arms strategically to capture contaminants before they disperse into the surrounding air.
- Flexible Design: LEV systems can be designed to fit the specific needs of your welding operation. Hoods and extraction arms can be adjustable and adaptable, allowing for effective capture of fumes and gases from various welding positions.
- Contaminant Removal: The captured contaminants are typically drawn away from the work area through ducts, filters, and exhaust fans. This ensures that the contaminants are expelled outside the workspace, preventing re-entry and reducing the risk of exposure to workers.
- Improved Air Quality: By directly removing welding fumes and gases at the source, local exhaust ventilation greatly improves the air quality in the workspace. This not only protects the health and safety of workers but also enhances visibility and overall work conditions.
- Effective Control: LEV systems are particularly effective in enclosed or indoor welding environments where natural ventilation may not be sufficient. By capturing contaminants directly at the source, local exhaust ventilation helps maintain a safe and clean work environment.
- Regulatory Compliance: Local exhaust ventilation systems are often recommended by regulatory bodies such as OSHA to ensure compliance with ventilation requirements in welding operations. Implementing LEV in your workplace helps you meet these regulations and safeguard the health of your workers.
Local exhaust ventilation offers a highly efficient and targeted approach to controlling and removing welding fumes and gases. It provides a reliable means of protecting the health and well-being of workers and maintaining a safe and productive workspace.
When designing and implementing a local exhaust ventilation system, it is important to consider factors such as the placement of extraction hoods or arms, the adequacy of airflow, and regular maintenance to ensure optimum performance. Consulting with ventilation experts or engineers can help in designing an LEV system tailored to your specific welding operations.
In the next section, we will discuss another ventilation system commonly used in welding operations – dilution ventilation.
Read more: Who Makes The Best Welding Hand Tools
Dilution Ventilation
Dilution ventilation is a type of ventilation system commonly used in welding operations, particularly in larger workspaces or open-air environments. It involves the use of general ventilation systems, such as fans or air conditioning units, to dilute and disperse welding fumes and gases in the surrounding air.
Here are some key points about dilution ventilation:
- Air Circulation: Dilution ventilation works by promoting air circulation in the workspace, ensuring a continuous flow of fresh air. This helps to dilute and disperse welding fumes and gases, reducing their concentration in the immediate vicinity of the welder.
- Applicable Situations: Dilution ventilation is particularly suitable for larger welding operations, where the workspace is spacious and open, or for outdoor welding activities. It can effectively control exposure to welding fumes and gases in such environments.
- Reduced Localized Capture: Unlike local exhaust ventilation, which captures contaminants directly at the source, dilution ventilation relies on the general circulation of air to remove fumes and gases. Therefore, it may not be as effective in controlling exposure in close proximity to the welding area.
- Enhancing Air Movement: To improve the effectiveness of dilution ventilation, additional fans or air moving devices can be strategically placed to enhance air movement and ensure better dispersion of contaminants.
- Supplemental Solution: Dilution ventilation may be used as a supplemental ventilation method in conjunction with other systems, such as local exhaust ventilation, to provide a more comprehensive approach to controlling and removing welding fumes and gases.
- Factors to Consider: When implementing dilution ventilation, factors such as the size of the workspace, the number of welders, and the ventilation system’s airflow capacity should be considered to ensure adequate dilution and proper air circulation.
While dilution ventilation may not provide the same level of control as local exhaust ventilation in terms of capturing contaminants directly at the source, it can still be an effective means of reducing the concentration of welding fumes and gases in the overall work environment. However, it is important to regularly monitor air quality and ensure that the dilution ventilation system is properly maintained to achieve optimal results.
Remember that dilution ventilation should not be solely relied upon for controlling exposure to welding fumes and gases. It is essential to assess the specific requirements of your welding operations and consider other ventilation systems, such as local exhaust ventilation, for more targeted control and capture of contaminants.
In the next section, we will discuss the factors you should consider when choosing a ventilation system for your welding operations.
Ensure that the ventilation system for welding operations includes both local exhaust ventilation at the source of the fumes and general ventilation to maintain clean air throughout the workspace. This will help to effectively remove harmful fumes and protect the health of workers.
Factors to Consider When Choosing a Ventilation System
Choosing the right ventilation system for your welding operations is crucial for maintaining a safe and healthy work environment. Consider the following factors to help you make an informed decision:
- Type of Welding: Different welding processes generate varying levels and types of airborne contaminants. Consider the specific welding techniques used in your operations, such as stick welding, MIG welding, or TIG welding, and the associated fumes and gases they produce. Some welding processes may require more robust ventilation systems to effectively control and capture the contaminants.
- Size and Layout of the Workspace: The size and layout of your workspace will influence the choice of ventilation system. Larger, open-air environments may benefit from dilution ventilation, while smaller, confined spaces may require local exhaust ventilation to effectively capture contaminants near the source. Assess the unique characteristics of your workspace to determine the most suitable ventilation system.
- Regulatory Compliance: Familiarize yourself with the ventilation regulations and standards set forth by relevant regulatory bodies, such as OSHA. Ensure that the chosen ventilation system aligns with these guidelines to maintain compliance and protect the health and safety of your workers.
- Worker Exposure: Consider the potential for worker exposure to welding fumes and gases. Assess the proximity of workers to the welding operations and evaluate the effectiveness of the ventilation system in controlling exposure. Prioritize systems that offer high capture efficiency and minimize the risk of direct inhalation of contaminants.
- Flexibility and Adaptability: Choose a ventilation system that can be easily adjusted and adapted to suit the changing needs of your welding operations. Consider systems with adjustable hoods or extraction arms that can be positioned to capture contaminants effectively, even as the work location or welding positions change.
- Maintenance Requirements: Evaluate the maintenance requirements of the ventilation system. Some systems may require regular cleaning, filter replacement, or duct inspections. Determine the level of maintenance that your team can handle and ensure that the chosen system is practical and manageable in terms of maintenance tasks.
- Cost Implications: Consider the financial implications of implementing a specific ventilation system. Take into account not only the initial costs of installation but also ongoing maintenance expenses. While cost is an important factor, prioritize the effectiveness and safety of the ventilation system over cost considerations.
- Consultation and Expertise: Seek consultation from ventilation experts, engineers, or professionals with knowledge of welding ventilation systems. Their expertise can help you assess the specific needs of your operations and determine the most suitable and effective ventilation solution.
By evaluating these factors, you can select a ventilation system that effectively controls exposure to welding fumes and gases, complies with regulations, and ensures the health and safety of your workers.
It is important to remember that the ventilation system should be regularly monitored and maintained to ensure its continued effectiveness. Implementing proper training and education for workers on ventilation system usage and best practices will also contribute to a safer work environment.
Next, we will discuss the effectiveness of each ventilation system in welding operations.
Effectiveness of Each Ventilation System in Welding Operations
Each ventilation system used in welding operations has its own level of effectiveness in controlling and mitigating the risks associated with airborne contaminants. Understanding the effectiveness of each system will help you make an informed decision in selecting the most suitable option for your specific welding operations.
- Natural Ventilation: While natural ventilation can provide some level of air circulation, it is generally considered the least effective method for controlling welding fumes and gases. It relies on the natural movement of air through openings in the workspace and may not provide sufficient control in enclosed or indoor environments. Therefore, it is not recommended as a standalone ventilation system for welding operations.
- Local Exhaust Ventilation (LEV): Among the various ventilation systems, local exhaust ventilation is regarded as the most effective in controlling exposure to welding fumes and gases. By capturing contaminants directly at the source, LEV systems offer high capture efficiency and ensure the removal of harmful pollutants from the immediate work area. They are particularly suitable for welding operations performed in confined spaces or indoor environments where concentrated fumes may accumulate.
- Dilution Ventilation: Dilution ventilation works by dispersing contaminants in the workspace through the circulation of fresh air. While it may not have the same capture efficiency as local exhaust ventilation, it can still be effective in reducing the concentration of welding fumes and gases in larger workspaces or open-air environments. Dilution ventilation is considered a supplemental option that can be used in conjunction with other ventilation systems to enhance overall effectiveness.
- Filtered Air Supply: Filtered air supply systems, such as powered air purifying respirators (PAPRs) or supplied air respirators (SARs), provide a continuous supply of clean, filtered air directly to the welder. These systems offer a high level of protection by preventing the inhalation of welding fumes and gases. However, they are typically used in situations where other ventilation methods are impractical or insufficient, such as confined spaces without proper exhaust ventilation.
When considering the effectiveness of each ventilation system, it is essential to assess the specific requirements of your welding operations. Factors such as the type of welding, workspace size, proximity of workers to the welding area, and regulatory compliance should be considered. The ideal ventilation system will provide a high level of control, while also being practical and feasible for implementation within your specific work environment.
Keep in mind that regular monitoring and maintenance of the ventilation system is crucial to ensure its continuous effectiveness. This includes regular inspections, filter replacements, and cleaning of exhaust ducts to maintain optimal performance.
Next, let’s discuss the cost implications and maintenance requirements associated with different ventilation systems in welding operations.
Cost Implications and Maintenance Requirements
When choosing a ventilation system for welding operations, it is important to consider the cost implications and maintenance requirements associated with each option. Understanding these factors will help you make an informed decision while ensuring long-term efficiency and affordability.
Cost Implications:
The cost of implementing a ventilation system can vary depending on several factors, including the type of system, the size of the workspace, and the specific requirements of your welding operations. Here are some cost considerations:
- Initial Installation: Local exhaust ventilation systems generally have higher upfront costs compared to other options. They require the installation of hoods, ductwork, fans, and filters. Dilution ventilation systems may be more cost-effective initially, as they rely on general ventilation systems already present in the workspace.
- Equipment and Components: Consider the cost of equipment and components required for the ventilation system. This includes fans, filters, ductwork, hoods, or extraction arms. Local exhaust ventilation systems may require additional expenses for maintenance of hoods and filters.
- Operating Costs: Evaluate the ongoing operating costs associated with each ventilation system. This includes energy consumption for running fans or air conditioning units, filter replacements, and regular maintenance requirements. Local exhaust ventilation systems may have higher operating costs due to the need for continuous operation of fans to capture and remove contaminants.
- Long-Term Benefits: While initial costs and operating expenses should be considered, also assess the long-term benefits and potential cost savings associated with each ventilation system. Effective ventilation contributes to the health and safety of workers, reducing the likelihood of medical expenses and workers’ compensation claims. It can also prevent equipment damage and decrease maintenance costs by minimizing the exposure of welding fumes to machinery and surfaces.
Maintenance Requirements:
No matter which ventilation system you choose, regular maintenance is essential to ensure its continued effectiveness. Here are some general maintenance requirements to consider:
- Filter Replacement: Many ventilation systems, particularly local exhaust ventilation, require regular filter replacements to maintain efficient capture and removal of contaminants. Assess the frequency and cost of filter replacements for each system.
- Inspections and Cleaning: Ductwork, hoods, and fans should be inspected regularly to identify any blockages or damage. Cleaning may be necessary to remove built-up debris or contaminants. Consider the time and resources required for routine inspections and cleaning tasks.
- Training and Education: Adequate training for workers is crucial to ensure they understand how to use the ventilation system correctly and follow maintenance procedures. Allocate resources for training sessions and educate workers on the importance of proper ventilation system utilization.
- Repairs and Upgrades: Occasionally, repairs or upgrades may be necessary to maintain the functionality and effectiveness of the ventilation system. Consider the potential repair costs and the availability of spare parts for the specific system you choose.
Regular and proactive maintenance of the ventilation system is vital to prolong its lifespan, ensure optimal performance, and mitigate any potential risks associated with poor air quality. By budgeting for maintenance expenses and committing to a comprehensive maintenance plan, you can maximize the longevity and efficiency of the chosen ventilation system.
In the next section, we will discuss the regulations and guidelines that govern ventilation in welding operations.
Read more: How To Store Welding Rods
Regulations and Guidelines for Ventilation in Welding Operations
Ventilation in welding operations is regulated by various organizations and government bodies to ensure the health and safety of workers. Understanding and complying with these regulations and guidelines is essential to create a safe and compliant work environment. Here are some key regulations and guidelines to consider:
- Occupational Safety and Health Administration (OSHA) – United States: OSHA provides guidelines and standards for ventilation in welding operations. According to OSHA’s General Industry Standards (29 CFR 1910.252), ventilation systems must be in place whenever welding or cutting is performed in an enclosed space to prevent the accumulation of harmful contaminants. OSHA also specifies that local exhaust ventilation systems should be designed and used to capture and remove welding fumes and gases at the source.
- European Welding Federation (EWF): The EWF provides guidelines for ventilation in welding operations in Europe. These guidelines emphasize the importance of implementing local exhaust ventilation systems to remove welding fumes and gases. They also highlight the need for regular maintenance of ventilation systems to ensure their effectiveness.
- Canadian Welding Bureau (CWB): The CWB provides guidelines for ventilation in welding operations in Canada. Their guidelines stress the importance of capturing welding fumes and gases using local exhaust ventilation systems and ensuring proper air circulation and exhaust ventilation in the workspace.
- National Institute for Occupational Safety and Health (NIOSH): NIOSH provides recommendations for controlling welding fumes and gases through proper ventilation. Their guidelines emphasize the use of local exhaust ventilation systems and the importance of regular maintenance and inspection to ensure optimal performance.
- ISO Standards: ISO standards, such as ISO 15012-1:2016, provide guidelines for health and safety in welding and allied processes. These standards address the need for effective ventilation systems, including local exhaust ventilation, to control exposure to welding fumes and gases.
It is important to familiarize yourself with the specific regulations and guidelines applicable to your region or country. By complying with these standards, you can ensure a safe and healthy work environment for your welding operations. Failure to comply with ventilation regulations may result in penalties, legal issues, and, most importantly, the increased risk of health problems for your workers.
In addition to following regulations, it is recommended to consult with ventilation experts, engineers, and professionals who have expertise in welding ventilation systems. They can provide valuable guidance on the specific ventilation requirements for your welding operations and help you design and implement an effective system that meets the regulations and ensures worker safety.
In the concluding section, we will summarize the key points discussed throughout this article.
Conclusion
Ventilation plays a critical role in ensuring the safety and well-being of workers in welding operations. By effectively controlling and removing airborne contaminants, ventilation systems help protect workers from the health risks associated with welding fumes and gases. Choosing the right ventilation system for your specific welding operations is essential to create a safe and compliant work environment.
Natural ventilation, while simple and cost-effective, may not be sufficient in enclosed or indoor environments. Local exhaust ventilation offers a highly effective solution by capturing contaminants directly at the source, ensuring high capture efficiencies. Dilution ventilation can be effective in larger workspaces or open-air environments, helping disperse fumes and gases through air circulation. Filtered air supply systems provide clean, filtered air directly to the welder, offering a high level of protection.
When considering a ventilation system, factors such as the type of welding, size and layout of the workspace, regulatory compliance, worker exposure, flexibility, maintenance requirements, and cost implications should be taken into account. Regular maintenance, including filter replacements, inspections, cleaning, and worker training, is crucial to ensure the continued effectiveness of the ventilation system.
Compliance with regulations and guidelines set by organizations such as OSHA, EWF, CWB, NIOSH, and ISO is necessary to create a safe work environment and avoid penalties. Consulting with ventilation experts and professionals is recommended to understand the specific requirements of your welding operations and design an appropriate system.
In conclusion, prioritizing ventilation in welding operations is crucial for both worker health and regulatory compliance. By investing in the right ventilation system and maintaining it properly, you can create a safe and productive work environment, protecting the well-being of your workers and ensuring the quality of the welding process.
Frequently Asked Questions about What Is The Best Ventilation System For Welding Operations
Was this page helpful?
At Storables.com, we guarantee accurate and reliable information. Our content, validated by Expert Board Contributors, is crafted following stringent Editorial Policies. We're committed to providing you with well-researched, expert-backed insights for all your informational needs.
0 thoughts on “What Is The Best Ventilation System For Welding Operations”