Home>Renovation & DIY>Home Renovation Guides>How To Organize A Stockroom
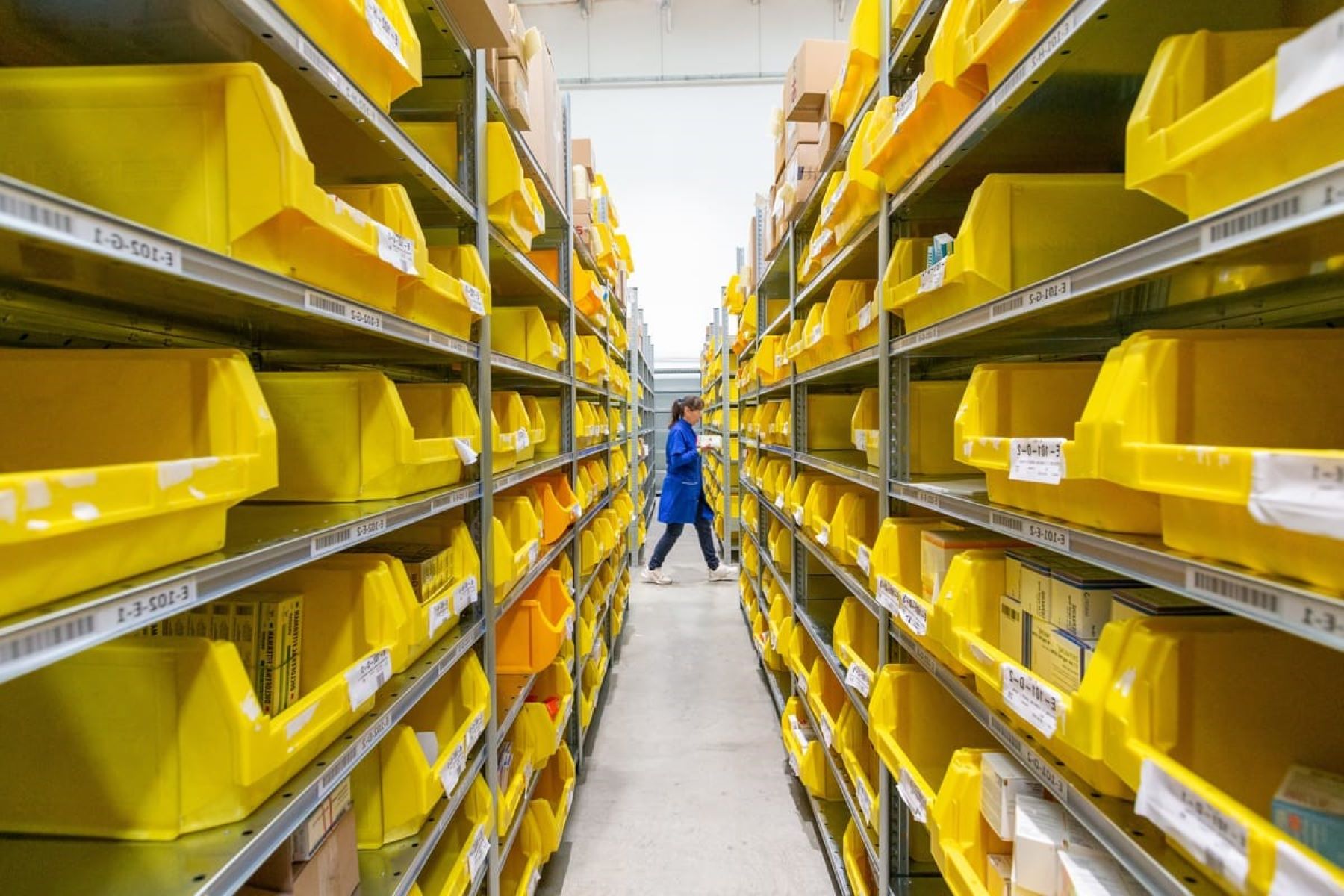
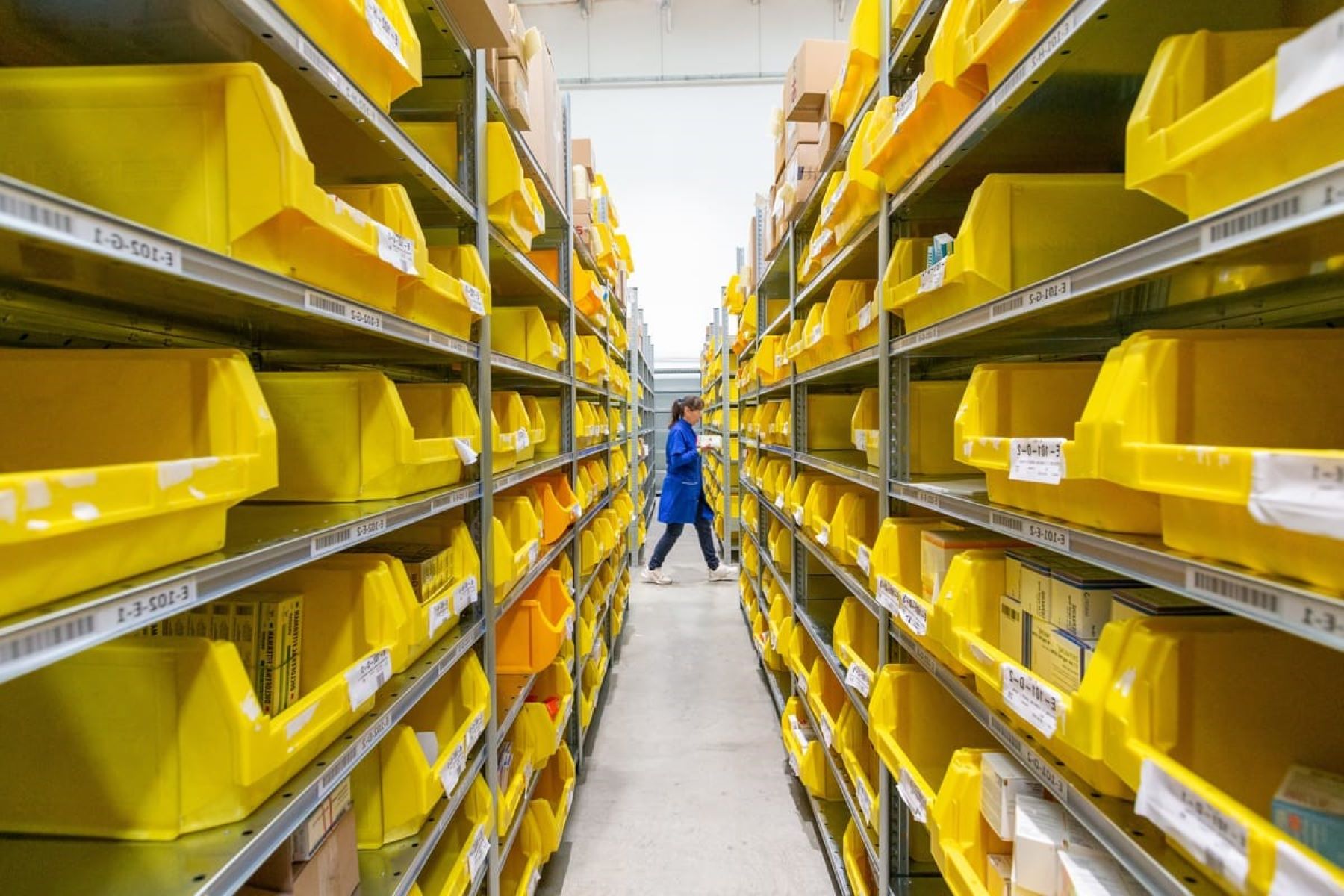
Home Renovation Guides
How To Organize A Stockroom
Published: March 2, 2024
Learn how to efficiently organize your stockroom with our comprehensive home renovation guide. Maximize space and improve workflow for a more organized and efficient stockroom.
(Many of the links in this article redirect to a specific reviewed product. Your purchase of these products through affiliate links helps to generate commission for Storables.com, at no extra cost. Learn more)
Assessing Stockroom Needs
Before diving into organizing your stockroom, it's crucial to assess its needs. This step involves evaluating the current state of your stockroom and identifying areas for improvement. Here are some key aspects to consider when assessing your stockroom needs:
-
Inventory Volume: Start by determining the volume of inventory you have and anticipate future growth. This will help you allocate the right amount of space for different items and plan for expansion if needed.
-
Traffic Flow: Assess the flow of movement within the stockroom. Identify high-traffic areas and ensure that they are easily accessible to avoid congestion and streamline operations.
-
Storage Equipment: Evaluate the existing storage equipment such as shelves, racks, and bins. Determine if they are sufficient for your current inventory and if any additional storage solutions are required.
-
Accessibility: Consider the accessibility of items based on their frequency of use. Items that are frequently accessed should be placed in easily reachable areas, while those with lower demand can be stored in less accessible spaces.
-
Safety and Compliance: Ensure that the stockroom meets safety and compliance standards. This includes proper storage of hazardous materials, adherence to fire codes, and compliance with any relevant regulations.
By thoroughly assessing these aspects, you can gain a clear understanding of your stockroom's needs and lay the groundwork for an effective organizational plan.
Key Takeaways:
- Assess stockroom needs by evaluating inventory volume, traffic flow, storage equipment, accessibility, and safety. This sets the groundwork for an effective organizational plan.
- Create a well-planned layout, sort and categorize inventory, implement storage solutions, use labeling and signage, and establish an inventory management system for an efficient and organized stockroom.
Read more: How To Organize A Library
Creating a Layout Plan
Creating a layout plan is a crucial step in organizing a stockroom effectively. A well-thought-out layout can optimize space utilization, streamline operations, and enhance overall efficiency. Here's how to create a comprehensive layout plan for your stockroom:
-
Measure and Map the Space: Begin by measuring the dimensions of the stockroom and creating a detailed map or floor plan. This map should include accurate measurements of the space, including ceiling height, as well as any permanent fixtures or obstacles.
-
Identify Zones: Divide the stockroom into distinct zones based on the nature of the inventory and operational requirements. Common zones include receiving, storage, packing, and shipping areas. Clearly delineating these zones helps in organizing and directing activities within the stockroom.
-
Consider Workflow: Take into account the workflow and operational processes when designing the layout. Ensure that the layout facilitates a logical flow of activities, from receiving goods to storage and eventual distribution. Minimize unnecessary movement and optimize the layout for efficiency.
-
Utilize Vertical Space: Maximize the use of vertical space by installing tall shelving units or utilizing mezzanine levels if feasible. This approach can significantly increase storage capacity without expanding the stockroom's footprint.
-
Allocate Storage Areas: Based on the assessment of inventory volume and traffic flow, allocate specific storage areas for different types of items. Consider factors such as item size, weight, and frequency of access when determining the placement of inventory within the stockroom.
-
Incorporate Flexibility: Design the layout to accommodate future changes and expansion. Utilize modular storage solutions and adjustable shelving to adapt to evolving inventory needs.
-
Ensure Accessibility and Safety: Place frequently accessed items in easily reachable areas and ensure that safety considerations are integrated into the layout. Keep emergency exits clear and provide clear pathways to access all areas of the stockroom.
By creating a well-planned layout, you can optimize the functionality of your stockroom, enhance productivity, and create a more organized and efficient working environment.
Sorting and Categorizing Inventory
Sorting and categorizing inventory is a fundamental aspect of stockroom organization. By systematically arranging items into specific categories, you can streamline retrieval processes, optimize storage space, and maintain a well-organized stockroom. Here's a detailed approach to sorting and categorizing inventory:
-
Inventory Assessment: Begin by conducting a comprehensive assessment of all inventory items. This involves identifying each item, checking its condition, and verifying its relevance to current operations. Discard any obsolete or damaged items to declutter the stockroom.
-
Establish Categories: Create distinct categories or groupings based on common characteristics such as item type, size, usage frequency, or departmental allocation. For example, you can categorize items into groups such as office supplies, electronics, tools, or raw materials.
-
Utilize Storage Containers: Use storage containers, bins, or crates to segregate items within each category. Clear, labeled containers make it easier to identify and retrieve specific items, reducing the time spent searching for inventory.
-
Implement Color Coding: Consider employing a color-coded system to visually differentiate between various categories. Assign specific colors to different types of inventory or departments, making it effortless for staff to locate and return items to their designated areas.
-
Alphabetical or Numerical Order: For items that are frequently accessed or require quick identification, consider organizing them in alphabetical or numerical order. This method is particularly useful for documents, files, or products with specific reference codes.
-
Utilize Shelving and Racking: Allocate dedicated shelves or racks for each category of inventory. Clearly label these storage areas to indicate the contents they hold. This approach facilitates systematic placement of items and prevents mixing of unrelated inventory.
-
Consider Seasonal or Usage Patterns: Take into account seasonal or usage patterns when categorizing inventory. Store seasonal items separately and prioritize the placement of frequently used items in easily accessible locations.
-
Documentation and Inventory Lists: Maintain detailed documentation or inventory lists that correspond to the categorized inventory. This documentation should include item descriptions, quantities, and location references, aiding in efficient inventory management and stockroom audits.
By systematically sorting and categorizing inventory, you can create a structured and efficient stockroom environment, enabling seamless inventory management and retrieval processes.
Implementing Storage Solutions
Implementing effective storage solutions is essential for maximizing space utilization and maintaining an organized stockroom. By employing suitable storage solutions, you can enhance accessibility, streamline inventory management, and optimize the overall layout. Here's a detailed guide on implementing storage solutions in your stockroom:
-
Utilize Shelving Systems: Install sturdy and adjustable shelving systems to accommodate various types of inventory. Adjustable shelves allow for flexibility in storing items of different sizes and shapes, while maximizing vertical space.
-
Invest in Pallet Racking: For bulk or heavy items, consider investing in pallet racking systems. These systems provide efficient storage for large quantities of goods and are ideal for organizing items that are palletized for storage and transportation.
-
Utilize Stackable Bins and Containers: Stackable bins and containers are excellent for organizing smaller items and parts. They can be easily stacked to create compact storage arrangements, making the most of available space.
-
Implement Mobile Shelving Units: Mobile shelving units, also known as compact shelving, are mounted on tracks, allowing them to be compacted together when not in use. This system maximizes space efficiency and provides easy access to stored items.
-
Utilize Overhead Storage: Overhead storage solutions, such as suspended racks or mezzanine platforms, can effectively utilize the vertical space in the stockroom. These solutions are suitable for storing items that are not frequently accessed.
-
Consider Drawer Cabinets: Drawer cabinets are ideal for storing small parts, tools, or documents. They provide organized and easily accessible storage for items that require compartmentalization.
-
Implement Wire Shelving for Visibility: Wire shelving provides visibility and airflow, making it suitable for storing items that require ventilation or for quick visual identification of inventory.
-
Utilize Rolling Carts and Trolleys: Rolling carts and trolleys are versatile storage solutions that can be used for transporting items within the stockroom. They are particularly useful for handling items during restocking or order fulfillment processes.
-
Customize Storage Solutions: Consider customizing storage solutions to fit specific inventory requirements. Custom-built shelves, racks, or storage compartments can optimize space and cater to unique storage needs.
By implementing a combination of these storage solutions, you can effectively organize your stockroom, optimize space utilization, and create a well-structured storage environment for efficient inventory management.
Use clear labeling and a logical layout to organize your stockroom. Group similar items together and keep frequently used items easily accessible. Regularly review and update your organization system to ensure efficiency.
Labeling and Signage
Labeling and signage play a pivotal role in enhancing the organization and navigability of a stockroom. Clear and comprehensive labeling, coupled with strategically placed signage, facilitates efficient inventory management and simplifies the retrieval process. Here's a detailed exploration of effective labeling and signage practices for stockroom organization:
-
Consistent Labeling Standards: Establish consistent labeling standards for all inventory items, storage areas, and shelves within the stockroom. Utilize clear and standardized labeling formats, including item names, codes, and relevant details, to ensure uniformity and ease of identification.
-
Utilize Barcode or QR Code Labels: Implement barcode or QR code labeling for inventory items to enable quick and accurate tracking. These labels can be scanned using handheld devices, streamlining the inventory management process and providing real-time visibility of stock levels.
-
Location-Based Labeling: Employ location-based labeling to clearly mark different storage zones, shelves, and aisles within the stockroom. This aids in guiding personnel to specific inventory locations and minimizes search time during item retrieval.
-
Color-Coded Labels: Utilize a color-coded labeling system to visually differentiate between various categories of inventory. Assign specific colors to different types of items or departments, enhancing visual recognition and expediting the identification of items.
-
Signage for Navigation: Install clear and visible signage at key points within the stockroom to guide personnel and visitors. Directional signs indicating different zones, exits, emergency equipment, and safety information contribute to a well-organized and safe working environment.
-
Informational Labels: In addition to item identification, incorporate informational labels that provide essential details such as item specifications, handling instructions, expiry dates (if applicable), and safety warnings. This ensures that personnel have access to crucial information at the point of use.
-
Magnetic and Adhesive Labels: Utilize magnetic or adhesive labels that can be easily affixed to shelves, bins, and containers. These labels offer flexibility in repositioning and updating as inventory configurations change, without leaving adhesive residue.
-
Digital Signage and Electronic Displays: In modern stockroom environments, consider integrating digital signage and electronic displays to convey real-time inventory information, alerts, and operational instructions. These digital solutions enhance communication and provide dynamic information dissemination.
-
Multilingual Labels: If the stockroom operates in a multilingual environment, consider incorporating multilingual labels and signage to ensure that information is accessible to all personnel, promoting inclusivity and understanding.
-
Regular Maintenance of Labels and Signage: Establish a schedule for inspecting and maintaining labels and signage to ensure their clarity and legibility. Replace damaged or faded labels promptly to uphold the effectiveness of the labeling system.
By implementing these labeling and signage practices, you can create a well-organized and navigable stockroom environment, promoting efficient inventory management and contributing to a safe and productive workplace.
Read more: How To Organize Decorations
Establishing Inventory Management System
Establishing a robust inventory management system is pivotal in maintaining control over stockroom operations and ensuring efficient inventory tracking. A well-structured inventory management system facilitates accurate stock monitoring, timely replenishment, and effective utilization of available resources. Here's a comprehensive guide to establishing an effective inventory management system for your stockroom:
-
Inventory Tracking Software: Invest in specialized inventory tracking software that offers features such as barcode scanning, real-time stock updates, and customizable reporting. Choose a software solution that aligns with the scale and complexity of your stockroom operations, providing the necessary tools for inventory control.
-
Centralized Database: Create a centralized database to store comprehensive information about all inventory items. This database should include item descriptions, quantities, storage locations, reorder points, suppliers, and historical consumption data. A centralized database serves as a single source of truth for inventory-related information.
-
Barcode or RFID Implementation: Integrate barcode or RFID (Radio-Frequency Identification) technology into the inventory management system. Assign unique identifiers to each inventory item and utilize handheld scanners or RFID readers to capture data accurately and efficiently. This technology streamlines stockroom operations and minimizes manual errors.
-
Standardized Replenishment Processes: Establish standardized processes for replenishing inventory based on predetermined reorder points and consumption patterns. Implement automated reorder triggers within the inventory management system to initiate procurement activities when stock levels reach predefined thresholds.
-
Cycle Counting and Stock Audits: Implement regular cycle counting and stock audits to verify the accuracy of inventory records. Utilize the inventory management system to schedule and conduct cycle counts, reconcile discrepancies, and maintain the integrity of stockroom inventory data.
-
Supplier Integration: Integrate supplier information and ordering processes into the inventory management system. Streamline procurement activities by establishing electronic communication channels with suppliers, automating purchase orders, and tracking inbound inventory shipments.
-
Forecasting and Demand Planning: Leverage the capabilities of the inventory management system to analyze historical consumption data and forecast future demand. Utilize demand planning tools to anticipate inventory requirements, optimize stock levels, and mitigate stockouts or overstock situations.
-
User Training and Documentation: Provide comprehensive training to stockroom personnel on the usage of the inventory management system. Develop user-friendly documentation and standard operating procedures to guide staff in utilizing the system effectively for tasks such as receiving, issuing, and transferring inventory.
-
Integration with ERP Systems: If applicable, integrate the inventory management system with broader Enterprise Resource Planning (ERP) systems. This integration enables seamless data exchange between inventory management, finance, and other operational functions, ensuring alignment across the organization.
-
Continuous Improvement and Adaptation: Regularly review the performance of the inventory management system and seek opportunities for continuous improvement. Adapt the system to evolving business needs, technological advancements, and changes in stockroom operations to maintain its effectiveness.
By establishing a comprehensive inventory management system, you can enhance the efficiency of stockroom operations, minimize inventory discrepancies, and lay the foundation for proactive inventory control and optimization.
Maintenance and Regular Audits
Maintaining the organized state of the stockroom and ensuring the accuracy of inventory records require a proactive approach to maintenance and regular audits. By implementing scheduled maintenance tasks and conducting systematic audits, you can uphold the efficiency of stockroom operations and mitigate potential issues. Here's a detailed exploration of the key elements involved in maintenance and regular audits for stockroom organization:
-
Scheduled Cleaning and Organization: Establish a routine schedule for cleaning and organizing the stockroom. Regularly remove any debris, dust, or clutter to maintain a clean and orderly environment. This practice not only enhances the visual appeal of the stockroom but also contributes to a more hygienic and safe working space.
-
Equipment Maintenance: Regularly inspect and maintain storage equipment such as shelves, racks, and material handling tools. Ensure that all equipment is in good working condition, free from damage or structural issues. Address any maintenance requirements promptly to prevent disruptions in stockroom operations.
-
Inventory Reconciliation: Conduct periodic reconciliations of physical inventory with the records in the inventory management system. This process involves physically counting and verifying the quantities of items in stock against the system's recorded quantities. Reconcile any discrepancies and investigate the root causes to maintain accurate inventory data.
-
Safety Inspections: Perform regular safety inspections to identify and address potential hazards within the stockroom. Check for proper storage of hazardous materials, ensure the stability of shelving units, and verify the functionality of safety equipment such as fire extinguishers and emergency exits. Address any safety concerns promptly to maintain a secure working environment.
-
Quality Control Checks: Implement quality control checks for perishable or sensitive inventory items. Monitor the condition and expiration dates of products, ensuring that any expired or compromised items are promptly removed from stockroom inventory. This practice helps prevent the storage of unusable or unsafe items.
-
Documentation Review: Review and update documentation related to stockroom procedures, safety protocols, and inventory management practices. Ensure that all documentation is current, easily accessible to personnel, and aligned with regulatory requirements. Regularly update any procedural changes or safety guidelines to reflect evolving best practices.
-
Staff Training and Feedback: Provide ongoing training to stockroom personnel on maintenance procedures, safety protocols, and audit processes. Encourage staff to provide feedback on potential maintenance issues or operational inefficiencies they encounter during their daily activities. Incorporate staff feedback into the continuous improvement of maintenance practices.
-
Audit Scheduling: Plan and schedule regular audits of the stockroom, encompassing physical inventory checks, safety assessments, and compliance evaluations. Establish a structured audit calendar to ensure that audits are conducted at appropriate intervals, considering factors such as inventory turnover rates and regulatory requirements.
-
Root Cause Analysis: In the event of inventory discrepancies, safety concerns, or maintenance issues identified during audits, conduct thorough root cause analyses. Identify the underlying reasons for any observed issues and implement corrective actions to prevent their recurrence. Document the findings and actions taken for future reference.
-
Continuous Improvement Initiatives: Emphasize a culture of continuous improvement within the stockroom environment. Encourage personnel to propose ideas for enhancing maintenance practices, streamlining audit processes, and optimizing stockroom operations. Implement improvement initiatives based on feedback and observations from audits.
By prioritizing maintenance tasks and conducting regular audits, you can uphold the organization, safety, and efficiency of the stockroom, fostering a well-maintained and compliant operational environment.
Frequently Asked Questions about How To Organize A Stockroom
Was this page helpful?
At Storables.com, we guarantee accurate and reliable information. Our content, validated by Expert Board Contributors, is crafted following stringent Editorial Policies. We're committed to providing you with well-researched, expert-backed insights for all your informational needs.
0 thoughts on “How To Organize A Stockroom”