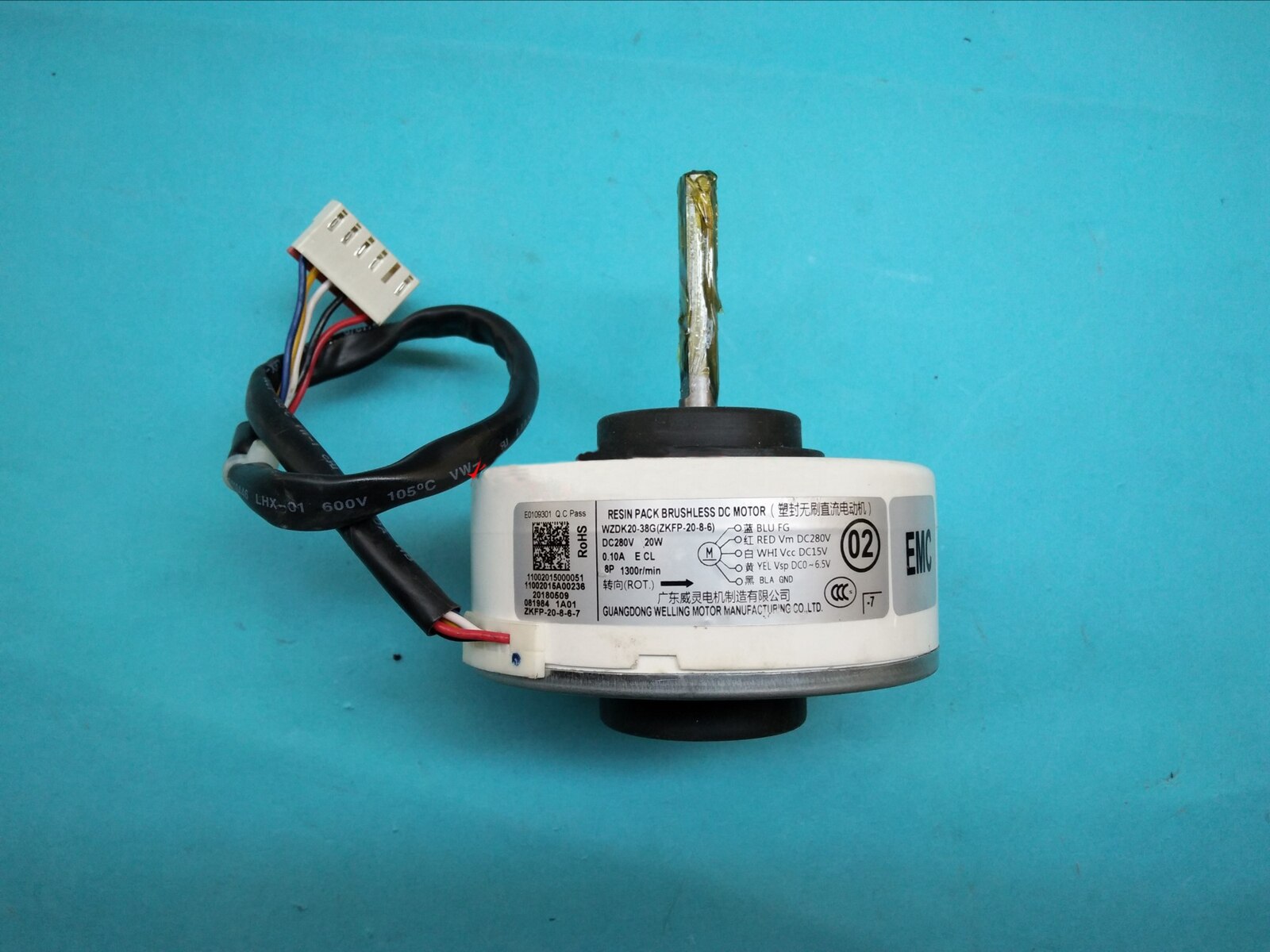
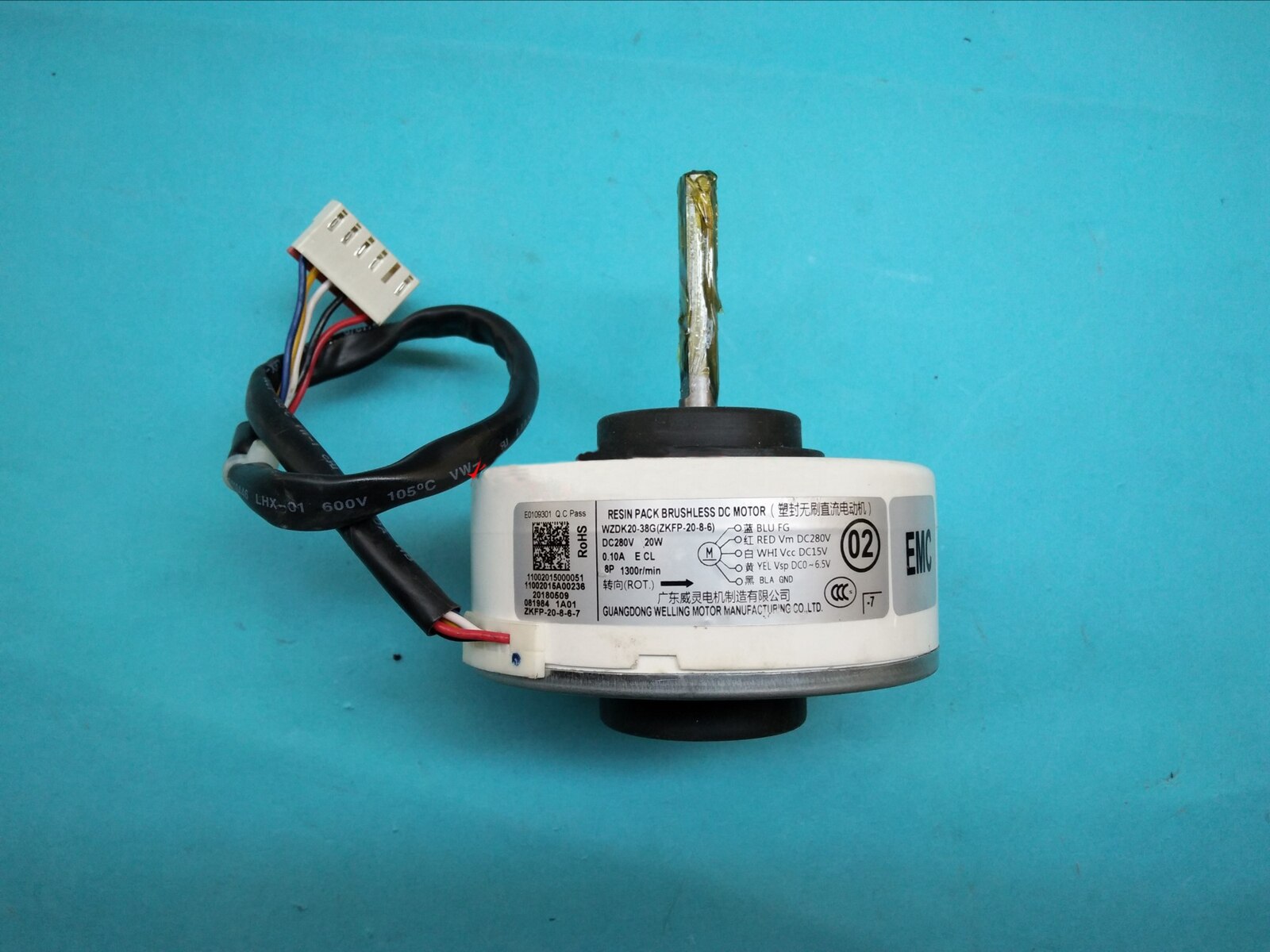
Articles
How Does an AC Motor Work
Modified: March 21, 2024
Discover how an AC motor works in this informative article. Explore the inner workings and principles behind this essential electrical device.
(Many of the links in this article redirect to a specific reviewed product. Your purchase of these products through affiliate links helps to generate commission for Storables.com, at no extra cost. Learn more)
Introduction
An AC motor, or alternating current motor, is a type of electric motor that is widely used in various applications. It is an essential component in many devices and machinery, ranging from household appliances to industrial equipment. Understanding how AC motors work is crucial for anyone interested in the field of electrical engineering or simply curious about the technology behind everyday objects.
AC motors utilize the power of alternating current to convert electrical energy into mechanical energy. Unlike DC motors, which run on direct current, AC motors have the advantage of being able to handle high-power applications efficiently. They are used in diverse sectors, including manufacturing, transportation, HVAC systems, and more.
This article aims to provide a comprehensive understanding of the principles and components of AC motors, as well as their operation and applications. By the end of this article, you will have a solid grasp of how AC motors work and their significance in our modern world.
Key Takeaways:
- AC motors are essential for converting electrical energy into mechanical motion, powering everything from household appliances to industrial machinery. They operate based on electromagnetic induction and the interaction of magnetic fields, offering efficiency, reliability, and variable speed control.
- Induction and synchronous motors are the two main types of AC motors, each with unique characteristics and applications. While induction motors are known for their simplicity and cost-effectiveness, synchronous motors offer precise speed control and constant speed operation. Both types find widespread use in HVAC systems, industrial machinery, appliances, transportation, renewable energy systems, robotics, power tools, generators, agricultural equipment, and healthcare equipment.
Read more: How Does A Electric Motor Work
Basic Principles of AC Motors
To understand how AC motors work, it is essential to grasp the basic principles that govern their operation. At the core of an AC motor’s functionality are electromagnetic induction and the principles of magnetism.
AC motors utilize the interaction between magnetic fields and electric currents to generate rotational motion. This is achieved through a process called electromagnetic induction. According to Faraday’s Law of Electromagnetic Induction, when there is a change in the magnetic field surrounding a conductor, an electric current is induced in the conductor.
An AC motor consists of two key components: the stator and the rotor. The stator is the stationary part of the motor, while the rotor is the rotating part. These components work together to create the electromagnetic forces necessary for the motor’s operation.
The stator holds the motor’s windings, which are designed to produce a rotating magnetic field when an alternating current is supplied to them. This rotating magnetic field exerts a force on the rotor, which causes it to turn.
The rotor, on the other hand, is made up of conductive bars or coils. These conductors are placed within the magnetic field generated by the stator. As the magnetic field oscillates, the rotor experiences a change in the magnetic flux, which induces an electric current in the rotor conductors.
When the rotor conductors carry current, they create their own magnetic field. This magnetic field interacts with the stator’s rotating magnetic field, causing the rotor to rotate. This continuous interaction between the stator and the rotor produces the rotational motion in the AC motor.
It’s important to note that the speed of an AC motor is determined by the frequency of the alternating current supplied to it. The number of poles in the stator also plays a role in determining the motor’s speed. Higher frequency and more poles result in higher rotational speed.
Now that we have an understanding of the basic principles of AC motors, let’s take a closer look at the components that make up these motors and their respective roles in the overall operation.
Components of an AC Motor
An AC motor consists of several essential components that work together to convert electrical energy into mechanical energy. These components include the stator, rotor, and air gap.
Stator: The stator is the stationary part of an AC motor. It is typically made up of a laminated core, which provides structural support and reduces eddy currents. The stator holds the motor’s windings, which are coils of wire wound around the laminated core. When an alternating current is supplied to the stator windings, they create a rotating magnetic field.
Rotor: The rotor is the rotating part of the AC motor. It is typically made of a shaft and conductive bars or coils. The rotor is positioned inside the stator’s magnetic field, and as the magnetic field rotates, it induces an electric current in the rotor conductors. This current creates a magnetic field in the rotor, which interacts with the stator’s magnetic field to produce rotational motion.
Air Gap: The air gap is the space between the stator and the rotor. It plays a crucial role in the operation of an AC motor. The air gap ensures that there is enough space for the rotor to rotate freely without making physical contact with the stator. This separation prevents excessive friction and allows for smooth and efficient operation of the motor.
In addition to these key components, AC motors may also include auxiliary components such as bearings, fans, and cooling systems. Bearings are used to support the rotating shaft and reduce friction. Fans and cooling systems help dissipate heat generated during operation, ensuring the motor operates within the optimal temperature range.
It is worth noting that the specific design and configuration of AC motor components can vary depending on factors such as motor size, application, and efficiency requirements. However, the fundamental principles remain consistent across different types of AC motors.
Now that we have covered the key components of an AC motor, let’s explore how these components work together to enable the motor’s operation.
Stator
The stator is an essential component of an AC motor, playing a vital role in the motor’s operation. It is the stationary part of the motor that houses the stator windings and provides the foundation for generating the rotating magnetic field.
The stator is typically made up of a laminated core, which consists of layers of thin iron or steel sheets. These laminations help reduce energy losses due to eddy currents, as the insulation between the layers inhibits the circulation of current within the stator core.
The stator windings, also known as coils, are wrapped around the laminated core. These coils are typically made of insulated copper wire, although other materials with suitable electrical conductivity can also be used. The stator windings are arranged in a specific pattern that determines the type and properties of the motor.
When an alternating current (AC) is supplied to the stator windings, it generates a rotating magnetic field. The pattern and arrangement of the stator windings determine the number of poles in the motor and the speed at which the magnetic field rotates.
The number of poles in the stator is determined by the number of coil groups or phases used in the winding. A coil group consists of one or more coils connected in series or parallel. For instance, a three-phase induction motor usually has three coil groups, resulting in a three-pole stator.
The rotating magnetic field created by the stator windings interacts with the rotor, inducing a current in the rotor conductors. This interaction generates a magnetic field in the rotor, causing it to rotate. The speed of the rotating magnetic field and, consequently, the rotor depends on the frequency of the AC supply.
In some AC motors, the stator windings can be externally connected to a power source, while in others, the stator windings are connected to a rotor with brushes that provide the electrical connection. The choice depends on the specific motor design and application.
In summary, the stator is a crucial component of an AC motor, providing the foundation for generating the rotating magnetic field. Its design, including the number of poles and the arrangement of the stator windings, determines the motor’s speed, efficiency, and performance characteristics.
Next, we will explore the rotor, another vital component of an AC motor.
Rotor
The rotor is a vital component of an AC motor, responsible for converting the rotating magnetic field generated by the stator into mechanical motion. It is the rotating part of the motor that is positioned inside the stator’s magnetic field.
The rotor is typically made up of a shaft and conductive bars or coils. The design of the rotor can vary depending on the specific type of AC motor, such as induction or synchronous motors.
In an induction motor, the rotor consists of conductive bars that are shorted at the ends by end rings, forming a complete conducting loop. These bars are typically made of aluminum or copper and are placed within the stator’s rotating magnetic field.
As the stator’s magnetic field rotates, it induces an electric current in the rotor conductors through electromagnetic induction. The direction of the induced current is opposite to the direction of the magnetic field. This interaction between the rotating magnetic field and the induced rotor currents creates a torque, which causes the rotor to start rotating.
In synchronous motors, the rotor contains coils rather than bars. These coils are connected to a direct current (DC) power source, either by brushes or a separate DC exciter. The DC current in the rotor windings produces a magnetic field that locks in sync with the stator’s rotating magnetic field. This synchronization allows the synchronous motor to operate at a constant speed.
It’s worth mentioning that some AC motors have a wound rotor, which allows for additional control over speed and torque. In a wound rotor motor, the rotor windings are not shorted but instead connected to external resistors or an external variable impedance called a rotor rheostat. By adjusting the resistance in the rotor circuit, the motor’s speed and torque characteristics can be modified.
The rotor’s design, including the number and configuration of the conductors or coils, affects the motor’s efficiency, torque, and speed capabilities. It is essential to consider the specific requirements of the intended application when selecting the appropriate rotor design.
In summary, the rotor is a key component of an AC motor, responsible for converting the rotating magnetic field into mechanical motion. Whether consisting of conductive bars, coils, or a wound configuration, the rotor’s design influences the motor’s performance and operational characteristics.
Next, let’s explore the significance of the air gap in an AC motor’s operation.
Read more: How Does An AC Unit Work
Air Gap
The air gap is a crucial component of an AC motor that plays a significant role in its operation. It refers to the space or distance between the rotor and the stator in an electric motor.
The air gap is necessary to ensure proper functioning and efficiency of the motor. It allows for the free rotation of the rotor within the stator’s magnetic field without any physical contact or interference. This separation helps minimize friction and wear, ensuring smooth and efficient operation.
The size of the air gap in an AC motor can vary depending on the specific design and requirements of the motor. It is crucial to find the right balance, as a narrow air gap may lead to increased friction and the potential for the rotor to rub against the stator, causing damage. On the other hand, a wide air gap may result in reduced magnetic field strength and decreased overall motor efficiency.
The air gap also serves to provide insulation between the rotor and stator windings, ensuring that the electric current flowing through the stator coils does not flow directly to the rotor. This insulation helps prevent electrical short circuits and ensures the efficient transfer of energy from the stator to the rotor.
In some cases, the air gap can affect the performance and characteristics of an AC motor. A larger air gap may introduce a slight lag in the motor’s response and reduce its torque output. Conversely, a smaller air gap can lead to increased magnetic flux saturation, improving motor performance and torque capabilities.
It’s worth noting that maintaining the air gap within proper tolerances is essential for the long-term reliability and performance of the motor. Over time, factors such as thermal expansion, vibration, and mechanical stress can lead to changes in the air gap. Regular maintenance and inspection are necessary to ensure the air gap remains within optimal specifications.
In summary, the air gap in an AC motor is a critical component that allows for the free rotation of the rotor within the magnetic field generated by the stator. It provides insulation, minimizes friction, and influences the motor’s efficiency and performance characteristics.
Next, let’s delve deeper into the operation of an AC motor and explore the concepts of induction and synchronous motors.
When an AC motor is connected to a power source, the alternating current creates a rotating magnetic field in the stator. This field interacts with the rotor, causing it to rotate and drive the motor’s mechanical load.
Operation of an AC Motor
The operation of an AC motor is based on the principles of electromagnetic induction and the interaction of magnetic fields. Understanding how these factors come together is key to comprehending the functioning of AC motors.
When an AC voltage is applied to the stator windings of an AC motor, it generates a rotating magnetic field due to the changing direction of the supplied current. This rotating magnetic field interacts with the rotor, consisting of conductive bars or coils, inducing an electric current in the rotor.
The interaction between the rotating magnetic field and the induced rotor current creates a torque, or twisting force, on the rotor. This torque causes the rotor to start rotating, aligning itself with the direction of the rotating magnetic field. As a result, the AC motor converts electrical energy into mechanical motion.
The speed at which an AC motor operates depends on the frequency of the supplied AC voltage. The higher the frequency, the faster the rotating magnetic field and the resulting rotor speed. Conversely, reducing the frequency will decrease the speed of the motor.
It is important to note that AC motors can be categorized into two main types: induction motors and synchronous motors.
Induction Motors: Induction motors are widely used in various applications due to their simplicity, reliability, and cost-effectiveness. In an induction motor, the rotor windings are not externally connected to a power source but rely on electromagnetically induced currents. The rotor current is induced by the changing magnetic field generated by the stator. The rotor speed in an induction motor slightly lags behind the rotating magnetic field, which is called slip. This slip allows induction motors to provide high starting torque and operate at a nearly constant speed under varying load conditions.
Synchronous Motors: Synchronous motors, as the name suggests, operate at a synchronous speed, which is determined by the frequency of the supplied AC voltage and the number of poles in the motor. The rotor in a synchronous motor is magnetized by direct current (DC) and locks in sync with the rotating magnetic field produced by the stator. This synchronization enables synchronous motors to maintain a constant speed even under changing loads. Synchronous motors are commonly used in applications that require precise control of speed and power factor correction, such as industrial machinery, compressors, and generators.
In summary, the operation of an AC motor relies on the interaction between the rotating magnetic field produced by the stator windings and the induced currents in the rotor. This interaction creates a torque that drives the rotor and converts electrical energy into mechanical motion. The specific type of AC motor, whether induction or synchronous, determines the motor’s speed and performance characteristics.
Next, let’s explore the difference between single-phase and three-phase AC motors.
Induction and Synchronous Motors
Induction motors and synchronous motors are the two main types of AC motors, each with its own unique characteristics and applications. Understanding the differences between these motors is essential in choosing the appropriate type for a specific application.
Induction Motors: Induction motors are the most commonly used type of AC motor due to their simplicity, reliability, and cost-effectiveness. They are widely employed in a wide range of applications, from household appliances to industrial machinery.
In an induction motor, the rotor windings are not externally connected to a power source. Instead, they rely on electromagnetically induced currents from the stator’s rotating magnetic field. This induction of currents in the rotor gives induction motors their name.
The rotor in an induction motor can be either squirrel cage or wound rotor. A squirrel cage rotor consists of conductive bars shorted at the ends by end rings, forming a complete conducting loop. The rotating magnetic field induces currents in the squirrel cage rotor, generating a torque that drives the rotor in motion.
One significant advantage of induction motors is their ability to provide high starting torque, making them suitable for applications that require a sudden surge of power, such as starting electric motors or moving heavy loads. Induction motors also offer good efficiency and robustness, making them a popular choice for various industrial applications.
Synchronous Motors: Synchronous motors operate at a synchronous speed, which is determined by the frequency of the supplied AC voltage and the number of poles in the motor. These motors are commonly used in applications that require precise control of speed, power factor correction, and constant speed operation.
In a synchronous motor, the rotor is magnetized by a direct current (DC) power source, either through brushes or a separate DC exciter. The rotor’s magnetic field locks in sync with the rotating magnetic field generated by the stator, resulting in a constant speed of operation.
Synchronous motors offer advantages such as high efficiency, precise speed control, and the ability to operate at high power factors. They are commonly used in applications such as industrial machinery, compressors, generators, and power plants.
Compared to induction motors, synchronous motors are more complex and require additional control systems to maintain synchronization between the rotor and stator’s rotating magnetic fields.
In summary, induction motors and synchronous motors are two main types of AC motors, each suited for different applications. Induction motors are known for their simplicity, reliability, and cost-effectiveness, while synchronous motors offer precise speed control and operation at a synchronous speed.
Next, let’s compare the differences between single-phase and three-phase AC motors.
Single Phase vs. Three Phase AC Motors
AC motors can be classified into two main categories: single-phase and three-phase motors. The primary distinction between these types lies in the number of phases in the AC power supply they require and the resulting characteristics of their operation.
Single Phase AC Motors: Single-phase motors are designed to operate with a single-phase AC power supply, which is commonly found in residential and small-scale commercial applications. These motors are widely used in household appliances, small machinery, and HVAC systems.
Single-phase motors consist of a stator and a rotor, similar to three-phase motors. However, they face a significant drawback due to the absence of a rotating magnetic field that can be achieved in three-phase motors. As a result, single-phase motors typically have lower starting torque and exhibit higher levels of vibration compared to their three-phase counterparts.
Single-phase motors often incorporate additional components to overcome these limitations. Capacitor-start/induction-run (CSIR) or capacitor-start/capacitor-run (CSCR) designs are commonly used to improve starting torque and overall performance.
Three Phase AC Motors: Three-phase motors are designed to operate with a three-phase AC power supply, which is commonly used in commercial and industrial settings. These motors offer numerous advantages, such as higher efficiency, lower vibration, and greater starting torque, compared to single-phase motors.
The primary advantage of three-phase motors lies in their ability to generate a rotating magnetic field, which provides a more balanced torque, smoother operation, and greater power output. The rotating magnetic field is achieved by using three-phase AC power, which consists of three separate phases offset by 120 degrees from each other.
Three-phase motors are widely used in various industrial applications, including pumps, compressors, conveyor systems, and manufacturing machinery. They provide a more efficient and reliable solution for high-power requirements.
It’s important to note that three-phase motors require a specialized three-phase power supply, often delivered through the electrical grid or generated by a motor controller or drive. This can add complexity and cost to the installation compared to single-phase motors, which can be connected directly to standard residential power outlets.
In summary, single-phase and three-phase AC motors differ in terms of the number of phases in their power supply and the resulting characteristics of their operation. Single-phase motors are commonly used in residential and small-scale commercial applications, while three-phase motors are preferred for commercial and industrial applications due to their higher efficiency and power output.
Now that we have explored the differences between single-phase and three-phase AC motors, let’s examine the advantages and limitations of AC motors in general.
Read more: How Does AC Work In A Tesla
Advantages and Limitations of AC Motors
AC motors offer several advantages that make them a popular choice for a wide range of applications. However, they also have some limitations that should be considered when selecting the appropriate motor for a specific task. Let’s explore both the advantages and limitations of AC motors.
Advantages:
- Efficiency: AC motors are known for their high efficiency, converting electrical energy into mechanical energy with minimal energy loss. This efficiency translates to cost savings and reduced environmental impact.
- Compact Size: AC motors are typically compact and lightweight compared to other types of motors, making them suitable for applications where space is limited.
- Variable Speed: AC motors offer the flexibility to vary the speed of operation, allowing for precise control over the machinery or equipment they power.
- Reliability: AC motors are known for their reliability and durability. When properly maintained, they can provide years of consistent and trouble-free operation.
- Wide Range of Sizes and Capacities: AC motors are available in a wide range of sizes and capacities, making them suitable for a variety of applications, from small appliances to large industrial machinery.
- Compatibility with Power Grids: AC motors are compatible with the standard AC power grids that are prevalent worldwide, making them a convenient choice for most electrical systems.
Limitations:
- Power Factor: AC motors can have a lower power factor, which indicates the efficiency of power utilization. In some cases, power factor correction techniques or equipment may be required to improve energy efficiency.
- Complex Control Systems: Certain types of AC motors, such as synchronous motors, require more complex control systems to maintain synchronization or control speed.
- Higher Initial Cost: Compared to other types of motors, AC motors can have a higher initial cost, especially for specialized designs or high-power applications.
- Requires AC Power Supply: AC motors require a reliable AC power supply, which may require additional infrastructure or equipment for certain applications.
- Limited Starting Torque: Single-phase AC motors, in particular, may have limited starting torque, which can impact their performance in certain applications.
Despite these limitations, AC motors continue to be the preferred choice for a wide range of applications due to their numerous advantages, efficiency, and reliability. The specific advantages and limitations should be carefully considered when selecting the appropriate AC motor for a particular task.
Now, let’s explore some of the applications where AC motors are commonly used.
Applications of AC Motors
The versatility and efficiency of AC motors make them a go-to choice for a wide range of applications, from everyday household appliances to complex industrial machinery. Let’s explore some of the common applications where AC motors are widely utilized.
1. HVAC Systems: AC motors are extensively used in heating, ventilation, and air conditioning (HVAC) systems. They power fans, blowers, and compressors, which are essential components in maintaining comfortable indoor environments in homes, offices, and commercial buildings.
2. Industrial Machinery: AC motors find extensive use in various industrial machinery, such as pumps, conveyors, mixers, centrifuges, and machine tools. Their ability to provide high torque and variable speed control makes them ideal for powering equipment in manufacturing plants, mines, and construction sites.
3. Appliances: AC motors are employed in a wide range of household appliances, including refrigerators, washing machines, dishwashers, vacuum cleaners, and fans. Their efficient and reliable operation ensures the smooth functioning of these appliances.
4. Transportation: AC motors are used in electric vehicles, trains, trams, and electric bikes. They provide the necessary propulsion, helping to reduce carbon emissions and improve energy efficiency in the transportation sector.
5. Renewable Energy Systems: AC motors play a significant role in renewable energy systems such as wind turbines and hydroelectric generators. They convert mechanical energy from wind or water into electrical energy, contributing to the development of sustainable power sources.
6. Robotics and Automation: AC motors power the machinery and robotic arms used in industrial automation. They enable precise and controlled movement, facilitating efficient manufacturing processes in industries like automotive, electronics, and pharmaceuticals.
7. Power Tools: AC motors are utilized in power tools such as drills, saws, grinders, and sanders. They provide the necessary power and torque to perform various tasks in construction, woodworking, and DIY projects.
8. Generators: AC motors are commonly used as generators in power plants, both conventional and renewable. They convert mechanical energy into electrical energy, supplying power to homes, businesses, and entire communities.
9. Agricultural Equipment: AC motors power agricultural machinery like irrigation pumps, grain augers, threshers, and milking machines. They contribute to efficient and sustainable farming practices.
10. Healthcare Equipment: AC motors are integral to medical equipment such as MRI machines, X-ray machines, ventilators, and surgical tools. They provide the necessary power and precision for critical healthcare procedures.
These are just a few examples of the diverse applications where AC motors are widely used. Their efficiency, reliability, and ability to provide variable speed control make them indispensable in various industries and everyday applications.
Now, let’s conclude our exploration of AC motors.
Conclusion
In conclusion, AC motors play a crucial role in countless applications, ranging from household appliances to industrial machinery. With their ability to efficiently convert electrical energy into mechanical motion, AC motors have become an essential component of modern-day technology.
We have explored the basic principles of AC motors, including electromagnetic induction and the interaction of magnetic fields. The components of an AC motor, such as the stator, rotor, and air gap, all work together harmoniously to facilitate the motor’s operation.
Induction motors and synchronous motors are the two main types of AC motors, each with its own unique characteristics and applications. Induction motors are widely used for their simplicity, reliability, and cost-effectiveness, while synchronous motors offer precise speed control and constant speed operation.
We have also discussed the advantages and limitations of AC motors. Some of the key advantages include high efficiency, compact size, variable speed control, and compatibility with power grids. However, AC motors may have limitations such as power factor issues, complex control systems, and higher initial costs.
AC motors find applications in various fields, including HVAC systems, industrial machinery, appliances, transportation, renewable energy systems, robotics, power tools, generators, agricultural equipment, and healthcare equipment. Their versatility and reliability make them indispensable in these sectors.
Overall, understanding how AC motors work and their applications is crucial for anyone interested in the field of electrical engineering or simply curious about the technology behind everyday objects. AC motors have undoubtedly revolutionized numerous industries and continue to drive innovation and progress.
So the next time you switch on a household appliance, marvel at a vehicle’s electric motor, or witness the smooth operation of complex machinery, you can appreciate the role that AC motors play in powering our modern world.
Frequently Asked Questions about How Does An AC Motor Work
Was this page helpful?
At Storables.com, we guarantee accurate and reliable information. Our content, validated by Expert Board Contributors, is crafted following stringent Editorial Policies. We're committed to providing you with well-researched, expert-backed insights for all your informational needs.
0 thoughts on “How Does an AC Motor Work”