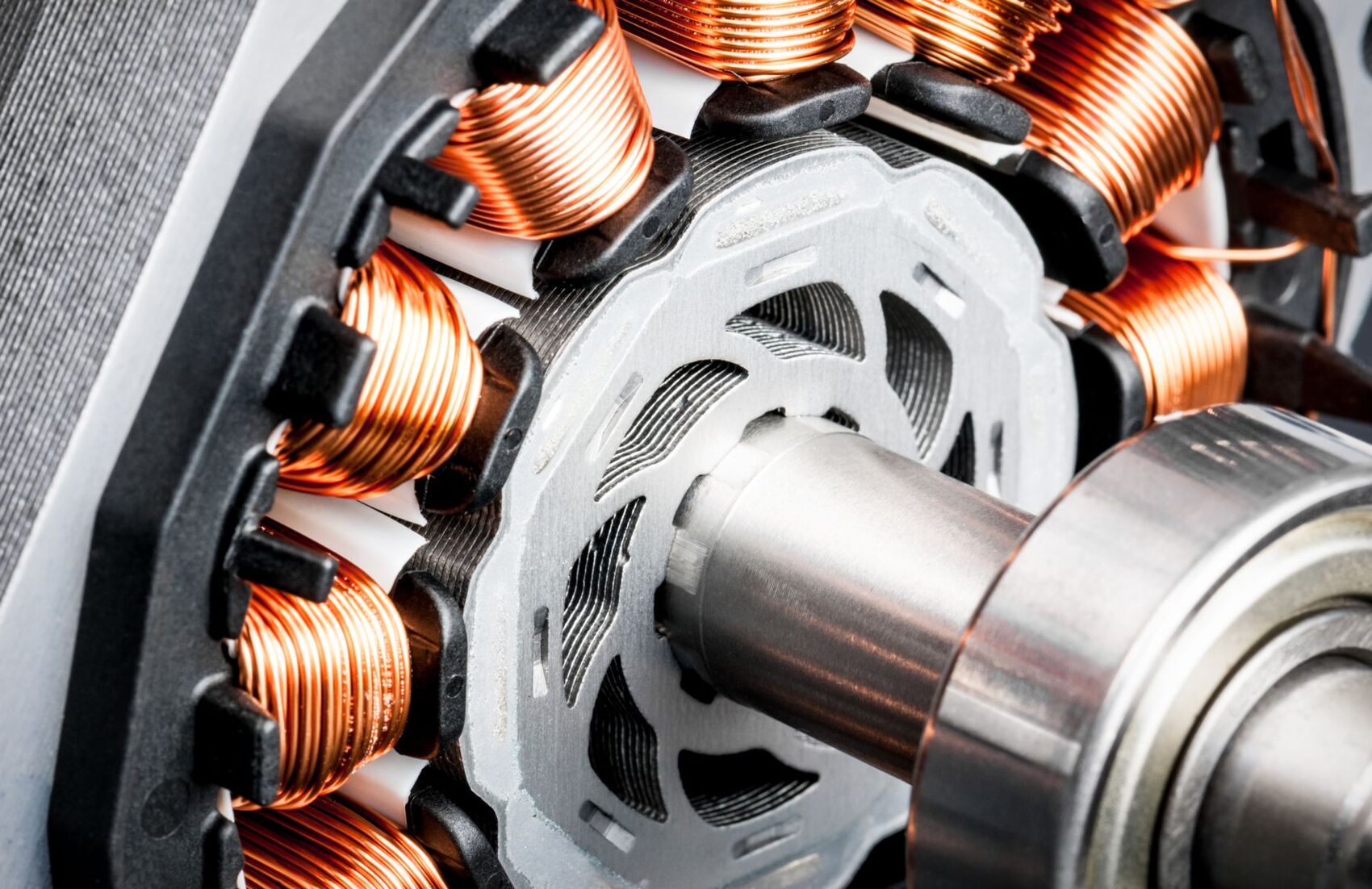
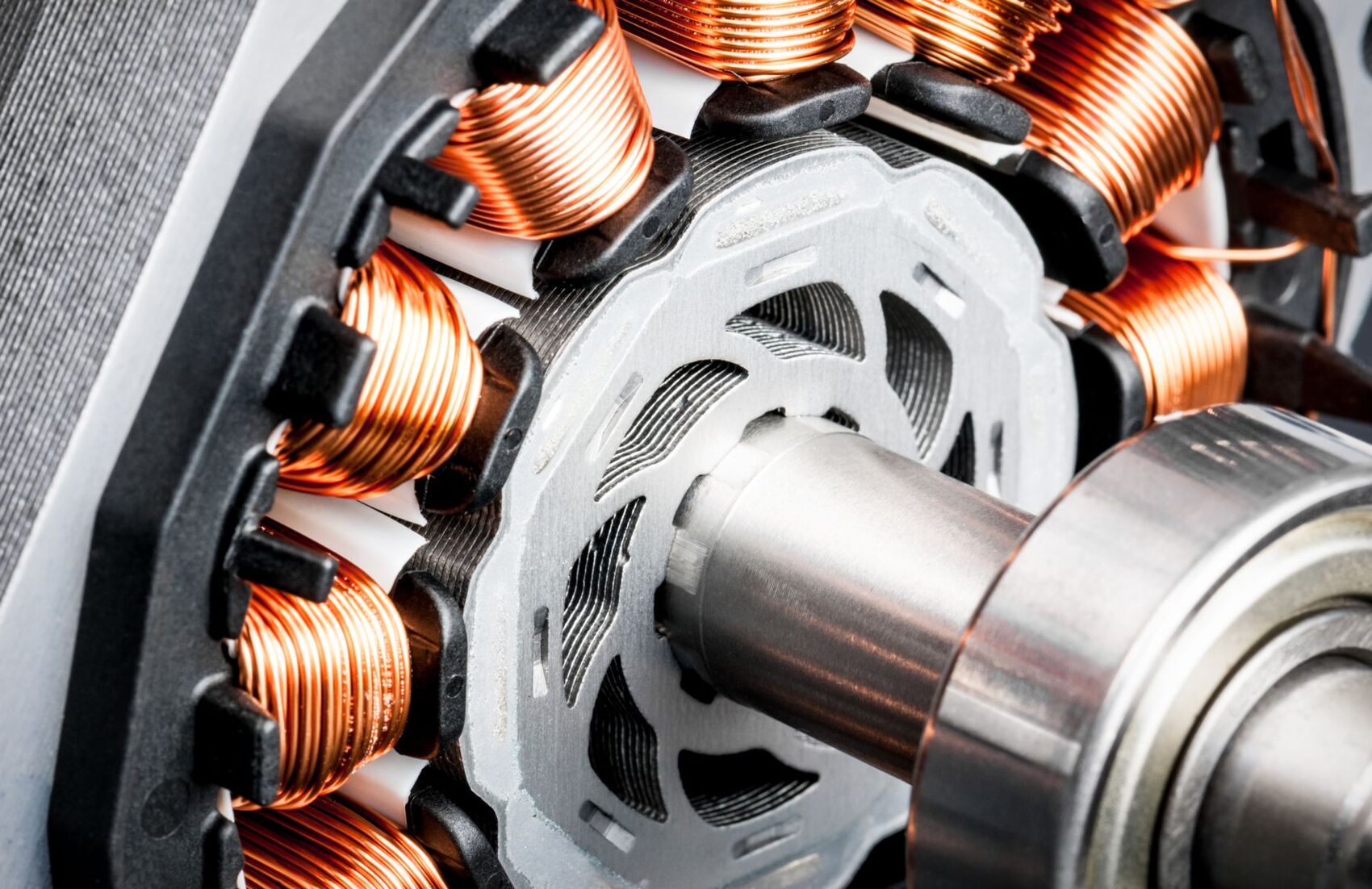
Articles
How Does A Dc Electric Motor Work
Modified: December 7, 2023
Discover how a DC electric motor works in this informative article. Learn about the inner workings and principles behind this essential component of many electrical devices.
(Many of the links in this article redirect to a specific reviewed product. Your purchase of these products through affiliate links helps to generate commission for Storables.com, at no extra cost. Learn more)
Introduction
Electric motors play a crucial role in various industries and applications, powering everything from household appliances to heavy machinery. Among the different types of electric motors, the DC (direct current) electric motor stands out for its reliability, simplicity, and versatility. Understanding how a DC electric motor works is fundamental to grasping its potential applications and benefits.
In this article, we will delve into the intricacies of DC electric motors, exploring their basic components, working principle, construction, commutation process, and different types. We will also discuss the advantages, disadvantages, and the wide range of applications where these motors are utilized.
So, let’s dive in and unravel the inner workings of a DC electric motor.
Key Takeaways:
- DC electric motors are essential for various industries, offering high torque, precise speed control, and compact size. Their reliability and efficiency make them a cornerstone in automotive, industrial, and consumer applications.
- Understanding the working principles and applications of DC electric motors is crucial for harnessing their potential effectively. From robotics to renewable energy, these motors play a pivotal role in powering modern technologies and industries.
Read more: How Does A Electric Motor Work
Basic Components of a DC Electric Motor
A DC electric motor consists of several key components that work together to convert electrical energy into mechanical energy, resulting in rotational motion. Here are the basic components of a DC electric motor:
- Stator: The stator is the stationary part of the motor and provides the magnetic field necessary for the motor’s operation. It is typically composed of a series of electromagnets that are arranged in a specific pattern.
- Rotor: The rotor is the rotating part of the motor. It consists of a shaft and a set of windings or permanent magnets that interact with the magnetic field generated by the stator. As a result, the rotor experiences a torque, causing it to rotate.
- Brushes and Commutator: Brushes are conductive contacts that maintain electrical contact with the moving rotor. The commutator, which is a segmented ring, assists in the transfer of current between the stationary and rotating parts of the motor. This process is called commutation.
- Armature: The armature is the core component of the rotor and consists of a coil of wire wound around an iron core. When a current passes through the armature windings, a magnetic field is created, causing the rotor to rotate.
- Field Windings: Field windings are located in the stator and provide the magnetic field required for the motor’s operation. These windings can be either wound or permanent magnets.
- Frame: The frame serves as the structural support for all the motor’s components, ensuring their proper alignment and stability during operation.
- Terminal Box: The terminal box is where the external electrical connections, such as power supply and control circuitry, are made. It allows for easy connection and disconnection of the motor.
These components work together harmoniously to facilitate the conversion of electrical energy into mechanical energy, allowing the motor to perform various tasks efficiently.
Working Principle of a DC Electric Motor
The working principle of a DC electric motor revolves around the interaction between magnetic fields and electric currents. When an electric current flows through the armature windings, a magnetic field is produced. This magnetic field interacts with the magnetic field generated by the stator, resulting in a torque that initiates rotational motion.
Here is a step-by-step breakdown of the working principle of a DC electric motor:
- Motor Start: When the power supply is connected to the motor, an electric current starts flowing through the armature windings.
- Magnetic Field Generation: As the current passes through the armature windings, a magnetic field is created. The direction of this magnetic field is determined by the right-hand rule, which states that if the fingers of your right hand follow the direction of the current, the curled thumb points in the direction of the magnetic field.
- Magnetic Interaction: The magnetic field produced by the armature windings interacts with the magnetic field generated by the stator. This interaction results in a force known as the Lorentz force, which causes the rotor to experience a torque.
- Rotor Rotation: The torque applied to the rotor causes it to rotate, generating mechanical energy. The rotational motion of the rotor depends on the direction of the magnetic field and the direction of the current flowing through the armature windings.
- Commutation: In a DC motor, the direction of the current in the armature windings needs to be periodically reversed to maintain continuous rotation. This process is called commutation and is achieved through the use of brushes and a commutator.
- Repeat Cycle: The cycle of magnetic field generation, interaction, rotor rotation, and commutation repeats continuously as long as the power supply is connected. This repetition allows the motor to generate continuous and controlled rotational motion.
By harnessing the principles of electromagnetic induction and magnetic field interaction, a DC electric motor can efficiently convert electrical energy into mechanical energy, making it a vital component in various applications.
Construction of a DC Electric Motor
The construction of a DC electric motor involves assembling the various components in a way that facilitates efficient operation and optimal performance. While the specific design and configuration may vary depending on the motor’s intended application, the general construction remains consistent. Here’s a closer look at the construction of a DC electric motor:
- Stator: The stator, typically made of iron or steel, consists of a core with a series of slots on its inner periphery. These slots house the stator windings, which are insulated copper wires wound around the core.
- Rotor: The rotor is made up of a shaft and a laminated iron core. The core is designed to hold the armature windings, which are coiled wires. In some DC motors, permanent magnets are used in place of armature windings.
- Brushes and Commutator: Brushes are typically made of carbon or graphite and are in contact with the commutator. The commutator is a segmented cylindrical structure that sits on the rotor’s shaft. It consists of copper segments insulated from one another.
- Field Windings: The field windings are located on the stator and provide the magnetic field for the motor’s operation. These windings can be wound coils or permanent magnets.
- Housing: The motor’s housing encloses and protects all the internal components. It is usually made of a durable material such as aluminum or steel and is designed to dissipate heat effectively.
- Terminal Box: The terminal box is where the motor’s electrical connections are housed. It provides easy access to the external power supply and control circuits.
When the motor is energized, the current passes through the brushes and commutator, creating a magnetic field in the armature windings. The interaction between this magnetic field and the field windings in the stator produces the required torque for rotation.
The construction of a DC electric motor is carefully engineered to ensure proper alignment and interaction of the components, efficient heat dissipation, and durability. This allows the motor to perform reliably in a wide range of operating conditions.
Commutation Process in a DC Electric Motor
In a DC electric motor, the commutation process is crucial for maintaining continuous rotational motion. Commutation refers to the process of reversing the current in the armature windings to ensure uninterrupted flow and consistent direction of torque. This process enables the motor to sustain constant rotation in a single direction. Here’s a breakdown of the commutation process:
- Brushes and Commutator: The brushes in a DC motor are responsible for transferring current between the stationary and rotating parts. They make physical contact with the commutator, which consists of insulated copper segments attached to the rotor’s shaft.
- Segment Connection: Each copper segment of the commutator is connected to the individual coils of the armature windings. These connections are made through wire leads or through the use of soldered connections.
- Armature Windings: The armature windings are arranged in a specific pattern around the rotor’s core. Each coil carries an equal amount of current, and the direction of this current determines the direction of the magnetic field it produces.
- Current Reversal: As the rotor rotates, the brushes remain in contact with different segments of the commutator. When the coil connected to one segment is aligned with the magnetic field, the current flowing through it is reversed to maintain the same direction of torque.
- Mechanical Segment Transition: As the rotor continues to rotate, the brushes transition from one segment to the next, ensuring the continuous reversal of current in the armature windings. This mechanical transition is facilitated by the geometry and design of the commutator.
- Smooth Transition: The transition from one commutator segment to another needs to be smooth to avoid interruption or sparking. Proper brush design, commutator material selection, and tensioning mechanisms are critical in achieving a seamless transition.
The commutation process ensures that the magnetic field produced by the armature windings remains in the correct alignment with the field windings in the stator, resulting in continuous and reliable motor operation. Efficient commutation minimizes power loss and reduces wear on the brushes and commutator contacts.
By effectively reversing the current in the armature windings at the right moment, the commutation process allows for the sustained rotation of the DC electric motor in a single direction for various applications.
A DC electric motor works by using a magnetic field to create motion. When an electric current is passed through the wire coils within the motor, it creates a magnetic field that interacts with the permanent magnets, causing the motor to spin.
Read more: How Does Electric Motor Brake Work
Types of DC Electric Motors
DC electric motors come in various types, each designed to cater to specific applications based on factors such as speed, torque requirements, and environmental conditions. Here are some common types of DC electric motors:
- Series Wound Motor: Series wound DC motors have the armature and field windings connected in series. This design enables them to provide high starting torque, making them suitable for applications that require high levels of torque, such as electric vehicles, forklifts, and winches.
- Compound Wound Motor: Compound wound DC motors combine elements of both series and shunt wound motors. They have both a series winding and a shunt winding, providing a balance between starting torque and speed regulation. Compound wound motors are commonly used in applications that require a combination of high starting torque and speed regulation, such as elevators and conveyor systems.
- Shunt Wound Motor: Shunt wound DC motors have the armature and field windings connected in parallel or “shunt.” This configuration allows for good speed regulation and control. Shunt wound motors are commonly used in applications that require precise speed control, such as fans, pumps, and machine tools.
- Permanent Magnet DC Motor: Permanent magnet DC motors utilize permanent magnets instead of field windings in the stator. These motors offer advantages such as higher efficiency, compact size, and simplified construction. They are commonly used in battery-operated devices, robotics, and small-scale applications.
- Brushless DC Motor: Brushless DC motors (BLDC) do not use brushes and commutators for current transfer. Instead, they employ electronic commutation, which provides benefits such as reduced maintenance and improved efficiency. BLDC motors are utilized in various applications, including automotive systems, industrial automation, and computer peripherals.
Each type of DC electric motor has its own advantages and is suitable for specific applications based on requirements such as torque, speed control, and efficiency. The selection of the motor type depends on the specific needs of the application and the desired performance characteristics.
It is worth noting that the advancements in motor technology and control systems have led to the development of more specialized and efficient DC motor designs. These advancements have resulted in increased performance and expanded the range of applications where DC electric motors can be used.
Advantages and Disadvantages of DC Electric Motors
DC electric motors offer several advantages and disadvantages that make them well-suited for specific applications. Understanding these pros and cons is essential for determining whether a DC motor is the right choice for a particular use case. Let’s explore the advantages and disadvantages of DC electric motors:
Advantages:
- High Torque: DC motors are known for their ability to deliver high torque at low speeds, making them suitable for applications requiring high starting torque, such as in electric vehicles and industrial machinery.
- Speed Control: DC motors offer excellent speed control capabilities, allowing for precise and efficient control over the motor’s rotational speed. This makes them ideal for applications that require varied and adjustable speeds.
- Compact Size: DC motors are typically compact in size and have a high power-to-weight ratio, making them suitable for applications where space is limited or weight needs to be minimized.
- Quick Response: DC motors have a fast response time, allowing for rapid acceleration and deceleration. This attribute makes them suitable for applications that require quick and precise movements, such as robotics and automation systems.
- Simple Construction: DC motors have a relatively simple construction, consisting of fewer components compared to other motor types. This simplicity results in lower cost, easier maintenance, and increased reliability.
Disadvantages:
- Brush Wear: Traditional DC motors that rely on brushes and commutators for current transfer experience brush wear over time. The brushes require periodic maintenance and replacement, resulting in increased maintenance costs and potential downtime.
- Limited Speed Range: DC motors have a limited speed range compared to some other motor types. Achieving very high speeds may require additional gears or mechanisms, which can increase complexity and cost.
- Electromagnetic Interference: DC motors generate electromagnetic interference (EMI) during operation, which can interfere with sensitive electronic equipment. Proper shielding and filtering are necessary to mitigate this issue in certain applications.
- Reduced Efficiency: DC motors, especially brushed types, can have lower energy efficiency compared to some alternatives, resulting in higher power consumption and operating costs.
While DC motors have their limitations, the advantages they offer in terms of torque, speed control, compact size, and simplicity make them a popular choice for various applications. The key is to carefully evaluate the specific requirements and trade-offs to determine whether a DC motor aligns with the needs of the intended application.
Applications of DC Electric Motors
DC electric motors find widespread use in countless applications across diverse industries. Their unique characteristics and versatility make them an ideal choice for various tasks that require rotational motion. Here are some common applications where DC electric motors play a crucial role:
- Automotive Industry: DC motors are widely used in the automotive sector for various purposes, including powering electric windows, windshield wipers, cooling fans, and electric power steering systems. Additionally, DC motors are employed in electric and hybrid vehicles for propulsion and regenerative braking.
- Industrial Machinery: DC electric motors are commonly found in industrial machinery, such as conveyors, pumps, compressors, and machine tools. Their high torque capabilities and precise speed control make them suitable for these heavy-duty applications.
- Aerospace and Aviation: DC motors are utilized in various aerospace applications, including flight controls, landing gear mechanisms, and fuel management systems. Their compact size, light weight, and reliable performance make them well-suited for these critical applications.
- Robotics and Automation: DC motors are extensively used in robotics and automation systems to provide precise and controlled motion. They are employed in robotic arms, actuators, grippers, and other robotic components, enabling smooth and accurate movement.
- Consumer Electronics: Many consumer electronics devices rely on DC motors for their operation. Examples include electric toothbrushes, hairdryers, DVD players, and computer disk drives. DC motors provide compact and efficient solutions for these portable and household devices.
- Medical Equipment: DC motors are employed in various medical equipment, including surgical robots, infusion pumps, dental handpieces, and diagnostic machines. Their precise and controllable motion is essential for performing delicate and precise procedures.
- Renewable Energy: DC motors, such as those used in wind turbines, play a crucial role in converting wind energy into electrical energy. They are also used in solar tracking systems to maximize the efficiency of solar panels by tracking the sun’s position.
- Marine Applications: DC electric motors are used in marine applications, such as electric boats, underwater remotely operated vehicles (ROVs), and winches. Their high torque and compact sizes are well-suited for demanding marine environments.
These are just a few examples of the numerous applications that rely on the reliable and efficient performance of DC electric motors. The versatility and adaptability of DC motors make them a fundamental component across a wide range of industries and technologies.
Conclusion
DC electric motors play a pivotal role in countless industries and applications, providing reliable and efficient solutions for converting electrical energy into mechanical motion. Understanding the basic components, working principle, construction, commutation process, types, advantages, and applications of DC motors is essential for harnessing their potential effectively.
From their high torque capabilities and precise speed control to their compact size and simple construction, DC motors offer numerous benefits that make them suitable for a wide range of tasks. Whether it’s powering industrial machinery, enabling precise movements in robotics, or supporting critical functions in automotive and aerospace applications, DC motors provide the necessary power and control.
However, it’s important to consider the disadvantages of DC motors as well. Brush wear, limited speed range, and electromagnetic interference are factors that need to be considered in certain applications. Additionally, advancements in motor technology have led to the development of brushless DC motors, which offer even greater efficiency and reduced maintenance needs.
Nonetheless, the versatility and adaptability of DC electric motors continue to make them an integral part of various industries. Their usage in automotive systems, industrial machinery, robotics, consumer electronics, and renewable energy systems demonstrate their fundamental importance in modern society.
In conclusion, DC electric motors stand as a reliable and efficient solution for converting electrical energy into mechanical motion. Their wide range of applications, along with their ability to provide high torque, precise speed control, and compact size, make them a cornerstone in numerous sectors. As technology advances, so too will the capabilities and efficiencies of DC motors, ensuring their continued relevance and importance in powering our world.
Frequently Asked Questions about How Does A Dc Electric Motor Work
Was this page helpful?
At Storables.com, we guarantee accurate and reliable information. Our content, validated by Expert Board Contributors, is crafted following stringent Editorial Policies. We're committed to providing you with well-researched, expert-backed insights for all your informational needs.
0 thoughts on “How Does A Dc Electric Motor Work”