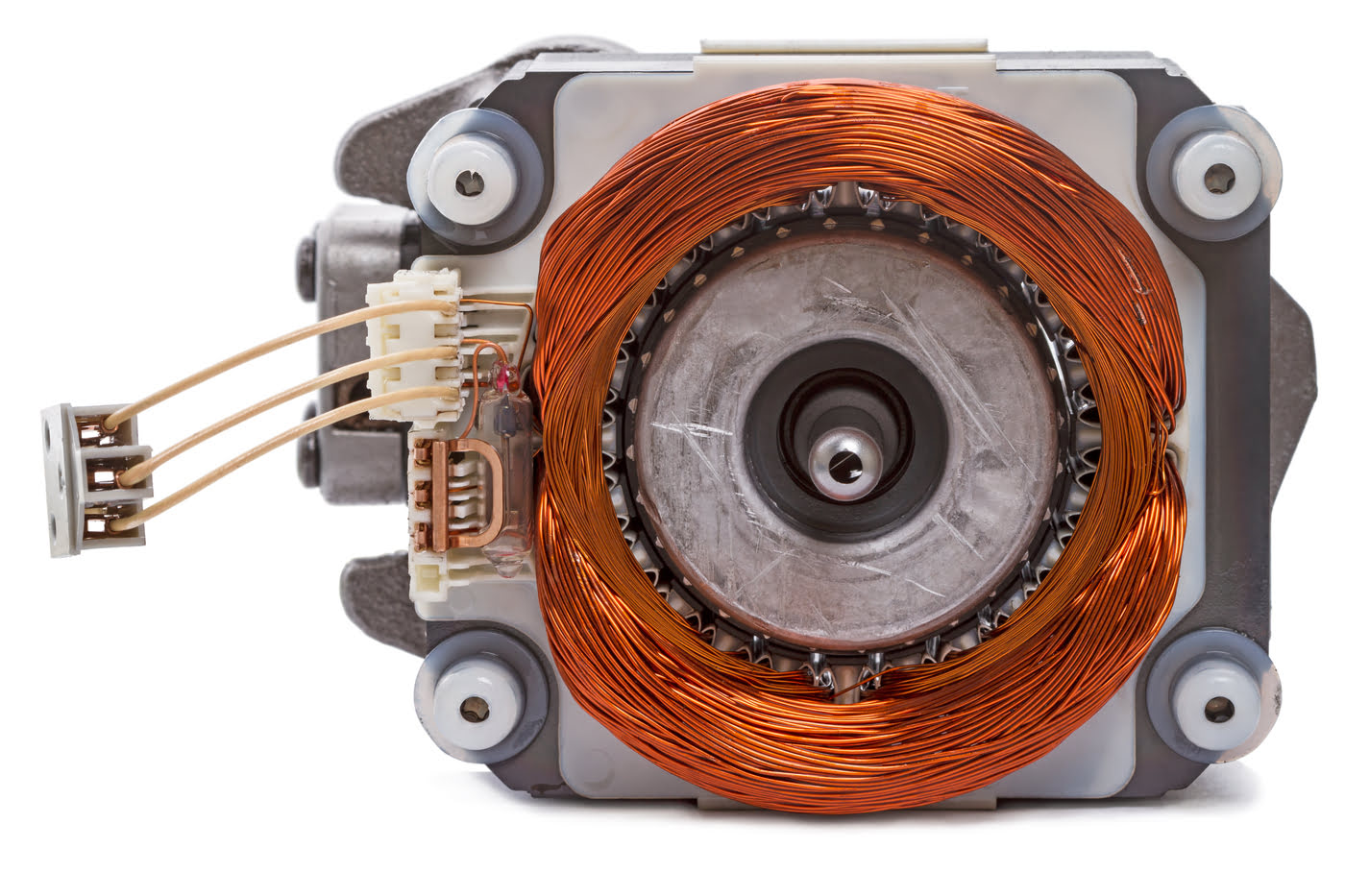
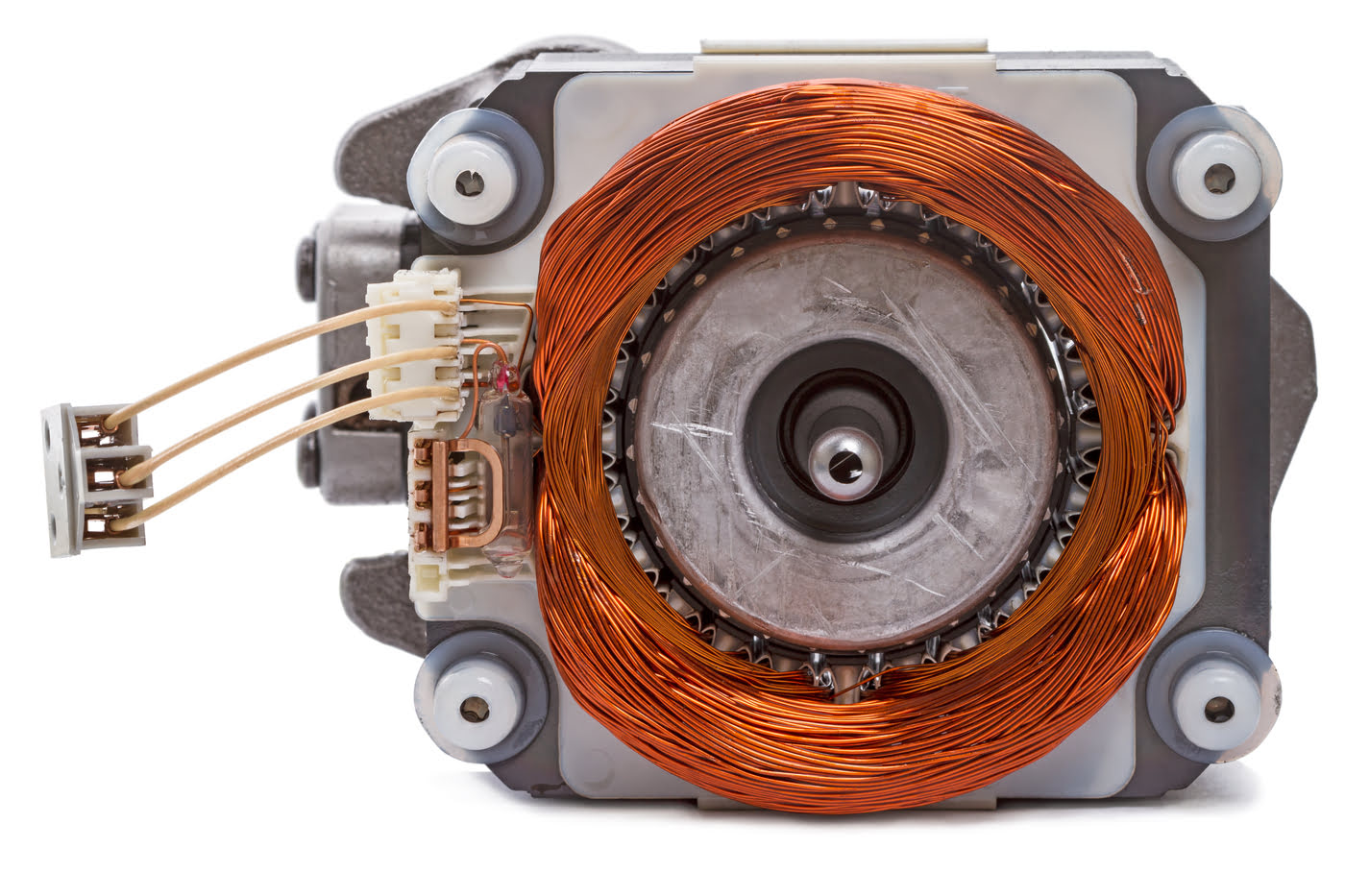
Articles
How Does A Brushless Electric Motor Work
Modified: December 7, 2023
Discover the inner workings of brushless electric motors in this informative article. Gain insights into their operation and why they are becoming increasingly popular in various industries.
(Many of the links in this article redirect to a specific reviewed product. Your purchase of these products through affiliate links helps to generate commission for Storables.com, at no extra cost. Learn more)
Introduction
Brushless electric motors have revolutionized the world of electric power, offering increased efficiency, reliability, and performance compared to their brushed counterparts. These motors are commonly found in a wide range of applications, from electric vehicles and drones to industrial machinery and power tools.
Unlike brushed motors, which rely on physical brushes and commutators to generate electricity, brushless motors utilize a different mechanism that eliminates the need for brushes and commutation. This not only improves the overall efficiency of the motor, but also reduces maintenance requirements and extends the lifespan of the motor.
In this article, we will explore the fascinating world of brushless electric motors, delving into their principle of operation, the components used, and the advantages they offer over traditional brushed motors. So, let’s dive in and uncover the inner workings of these remarkable devices.
Key Takeaways:
- Brushless electric motors operate through electronic commutation, utilizing Hall effect sensors and an electronic speed controller to achieve precise speed control, high torque, and improved efficiency compared to brushed motors.
- The advantages of brushless electric motors include higher efficiency, longer lifespan, higher power density, smoother control, and reduced electromagnetic interference, making them ideal for a wide range of applications across various industries.
Read more: How Does A Electric Motor Work
Principle of Operation
The principle behind the operation of a brushless electric motor lies in the interaction between the stator and the rotor. The stator is the stationary part of the motor, while the rotor is the rotating component. Unlike brushed motors where the commutation is done mechanically, brushless motors rely on electronic commutation using sensors and a controller.
The stator of a brushless motor consists of multiple electromagnets arranged in a circular pattern. These electromagnets, also known as poles, are evenly spaced around the inner circumference of the motor. When electrical current flows through the windings of these poles, a magnetic field is generated.
The rotor of the brushless motor, on the other hand, is typically equipped with permanent magnets. These magnets generate a fixed magnetic field that interacts with the magnetic field produced by the stator. The orientation of the permanent magnets in the rotor determines the direction of the rotational force.
Electronic commutation is the key to the operation of a brushless motor. The rotor position is constantly monitored using Hall effect sensors placed strategically around the stator. These sensors detect the position of the rotor magnets and send signals to the electronic speed controller (ESC).
The ESC receives the signals from the Hall effect sensors and determines when to energize the electromagnets in the stator. It uses this information to create a rotating magnetic field that follows the position and speed of the rotor. By constantly adjusting the timing and sequence of the electromagnetic field, the ESC ensures smooth rotation of the motor.
This process of electronic commutation allows the brushless motor to achieve precise speed control, high torque, and improved efficiency compared to brushed motors. There is no physical contact between the stator and rotor, eliminating the friction and wear associated with brushes. This results in less heat generation, lower maintenance requirements, and a longer operational lifespan.
In the next sections, we will explore the different components involved in the operation of a brushless electric motor, such as the stator, rotor, permanent magnets, Hall effect sensors, and electronic speed controller.
Stator
The stator is a fundamental component of a brushless electric motor, providing the stationary part of the motor that generates the magnetic field. It is typically made up of a stack of laminated steel plates to reduce energy losses due to eddy currents.
The stator consists of a series of poles distributed evenly around the inner circumference of the motor. Each pole is wound with copper wire, forming an electromagnet. The number of poles can vary depending on the motor design and application.
The windings on the stator are connected to the electronic speed controller (ESC) through the motor cables. The ESC provides the necessary electrical current to energize the windings, creating a magnetic field around each pole.
When the windings are energized, the electromagnetic field generated by the stator interacts with the permanent magnets on the rotor, causing a rotational force. The direction and strength of the magnetic field are controlled by the ESC based on feedback from the Hall effect sensors.
The stator is designed to maximize the interaction between the magnetic field and the rotor, ensuring efficient conversion of electrical energy into mechanical power. The design of the stator can vary depending on the specific requirements of the motor, such as torque output, speed range, and power efficiency.
In addition to the windings, the stator may also include other components such as thermal sensors and temperature sensors to monitor the operating conditions of the motor. These sensors provide feedback to the ESC, allowing it to adjust the motor’s performance to prevent overheating and potential damage.
Overall, the stator is a critical component of a brushless electric motor, providing the necessary magnetic field for the motor’s operation. Its design and construction play a crucial role in determining the motor’s performance, efficiency, and longevity.
Rotor
The rotor is a key component of a brushless electric motor, responsible for the rotational motion and generating the output power. Unlike the stator, the rotor is the moving part of the motor, rotating in response to the magnetic field generated by the stator.
Most brushless motor rotors are equipped with permanent magnets, typically made of materials such as neodymium or ferrite. These magnets create a fixed magnetic field that interacts with the magnetic field produced by the stator’s electromagnets.
The orientation and arrangement of the permanent magnets on the rotor determine the direction and strength of the rotational force. By controlling the electromagnetic field generated by the stator through the ESC, the rotor can be driven to rotate in a specific direction.
In addition to the permanent magnets, the rotor may also incorporate other components, such as a shaft, bearings, and a fan. The shaft allows the rotor to rotate smoothly and transfers the rotational motion to the desired application. Bearings provide support and reduce friction between the rotor and the stator, contributing to the overall efficiency and longevity of the motor.
The fan, if present, serves the purpose of cooling the motor during operation. As the rotor spins, the fan blades push air through the motor, dissipating heat and preventing overheating. This helps to maintain optimal performance and reliability, especially in high-powered applications that generate significant heat.
The design of the rotor plays a crucial role in determining the motor’s performance characteristics, such as torque output and speed range. Factors such as the number and arrangement of the permanent magnets, as well as the overall mass and balance of the rotor, can impact the motor’s efficiency, power, and vibration levels.
In summary, the rotor is a vital component of a brushless electric motor, responsible for converting the magnetic energy from the stator into rotational motion. Its design and construction contribute to the motor’s performance, efficiency, and cooling capabilities.
Permanent Magnets
Permanent magnets are a crucial element in the operation of a brushless electric motor. They play a significant role in generating the magnetic field required for the motor’s rotation and power output.
These magnets are typically made from strong magnetic materials, such as neodymium (NdFeB) or ferrite (ceramic magnets). These materials are known for their high magnetization, allowing them to produce a strong and stable magnetic field.
The permanent magnets are mounted on the rotor of the brushless motor, securing their position in a fixed arrangement. The orientation and alignment of the magnets are carefully designed to interact with the electromagnets on the stator and create the desired rotational force.
When the windings on the stator are energized, a magnetic field is generated. This magnetic field interacts with the fixed magnetic field produced by the permanent magnets on the rotor, resulting in a torque that drives the rotation of the motor.
The strength and composition of the permanent magnets directly impact the motor’s performance characteristics, including torque output and maximum speed. High-quality permanent magnets provide a stronger magnetic field, enabling the motor to deliver increased power and efficiency.
It’s worth noting that the strength of the permanent magnets is also a factor in determining the overall size and weight of the motor. Higher strength magnets allow for the construction of smaller and lighter motors without sacrificing performance.
Furthermore, the use of permanent magnets in brushless motors eliminates the need for brushes and commutators, which are present in brushed motors. This not only improves the efficiency and reliability of the motor but also reduces the maintenance requirements and extends the operational lifespan.
In summary, permanent magnets are essential components in brushless electric motors, providing a stable and powerful magnetic field for efficient motor operation. Their strength, composition, and arrangement directly affect the motor’s performance, size, and longevity.
When using a brushless electric motor, make sure to properly size the motor for the application to ensure optimal performance and efficiency.
Read also: 12 Best Brushless Electric Motor for 2024
Hall Effect Sensors
Hall effect sensors play a vital role in the operation of brushless electric motors by providing crucial feedback to the electronic speed controller (ESC). These sensors help determine the position and speed of the rotor, enabling precise control of the motor’s operation.
Hall effect sensors are solid-state devices that utilize the Hall effect, which is the generation of a voltage in a conductor when it is subjected to a magnetic field. These sensors are typically placed strategically around the stator of the motor, near the permanent magnets on the rotor.
When the rotor rotates, the position and alignment of the permanent magnets change relative to the Hall effect sensors. As a result, the magnetic field interacting with the Hall effect sensors also changes, causing a variation in the voltage output of the sensors.
The Hall effect sensors detect these voltage variations and convert them into signals that are sent to the electronic speed controller. The ESC uses this information to determine the position of the rotor and accurately time the commutation of the stator windings.
By continuously monitoring the position and speed of the rotor, the Hall effect sensors enable the ESC to precisely control the energization of the stator windings. This results in smooth and efficient motor operation, with accurate speed control and torque output.
Furthermore, the Hall effect sensors provide feedback to the ESC, allowing it to adapt the motor’s performance in real-time. For example, if the motor is operating at high temperatures, the ESC can adjust the output power of the motor to prevent overheating and potential damage.
The use of Hall effect sensors in brushless motors eliminates the need for physical brushes and commutators found in brushed motors. This leads to reduced friction, wear, and maintenance requirements, as well as improved reliability and longevity of the motor.
In summary, Hall effect sensors are integral components in brushless electric motors, providing crucial feedback to the electronic speed controller. These sensors enable precise control of the motor’s operation, accurate speed control, and efficient commutation of the stator windings.
Electronic Speed Controller
The electronic speed controller (ESC) is a critical component in a brushless electric motor system. It serves as the control center, managing the power input, motor speed, and direction of rotation. The ESC receives signals from the Hall effect sensors and adjusts the current flow through the stator windings accordingly.
The main function of the ESC is to control the timing and sequence of the electromagnetic field generated by the stator. By analyzing the signals from the Hall effect sensors, the ESC determines the rotor’s position and speed, allowing it to synchronize the commutation of the stator windings.
The ESC consists of a microcontroller or a dedicated electronic circuit that processes the input signals and outputs the necessary instructions to the motor. It is typically connected to a power source, such as a battery, and the stator windings of the motor.
The ESC is responsible for delivering the appropriate amount of electrical current to the motor to achieve the desired speed and torque. It controls the timing and duration of the electrical pulses that energize the windings, effectively creating a rotating magnetic field.
Modern ESCs often come equipped with additional features, such as programmable settings, brake functions, and regenerative braking capabilities. These features allow for customization of the motor’s performance characteristics, providing flexibility and adaptability to different applications.
Furthermore, the ESC acts as a safety mechanism by monitoring the motor’s operating conditions. It can detect overcurrent, overtemperature, and other abnormal conditions, and take measures to protect the motor from damage.
The ESC also plays a crucial role in adjusting the motor’s performance based on the user’s input. It receives signals from the throttle or speed control input device, allowing the user to control the motor’s speed and direction accurately.
In summary, the electronic speed controller is the brain of a brushless electric motor system, responsible for controlling the motor’s speed and direction. It synchronizes the commutation of the stator windings based on feedback from the Hall effect sensors and ensures efficient and precise operation of the motor.
Advantages of Brushless Electric Motors
Brushless electric motors offer a range of advantages over traditional brushed motors, making them a popular choice in various industries and applications. Here are some key advantages of brushless electric motors:
1. Higher Efficiency: Brushless motors are more efficient than brushed motors due to their electronic commutation system. This means that they waste less energy as heat, resulting in improved overall efficiency and reduced power consumption.
2. Longer Lifespan: Without the brushes and commutator found in brushed motors, brushless motors experience less wear and tear. This leads to a longer lifespan and reduced maintenance requirements, saving both time and money in the long run.
3. Higher Power Density: Brushless motors have a higher power-to-weight ratio compared to brushed motors. This allows for more power output in a smaller and lighter motor package, making them ideal for applications where space and weight are critical factors.
4. Smooth and Precise Control: The electronic commutation system of brushless motors enables precise speed control and accurate position control. This makes them suitable for applications that require smooth and precise motion, such as robotics, CNC machines, and drones.
5. Higher Torque-to-Inertia Ratio: Brushless motors typically have a higher torque-to-inertia ratio, which means they can deliver more torque relative to their size and weight. This makes them suitable for applications that require high torque output, such as electric vehicles and industrial machinery.
6. Reduced Electromagnetic Interference (EMI): The electronic commutation system in brushless motors eliminates the sparking and arcing that occurs in brushed motors. As a result, they produce less electromagnetic interference, making them suitable for sensitive electronic devices and applications.
7. No Brush Maintenance: Brushless motors eliminate the need for brush maintenance, which is a common maintenance task in brushed motors. This reduces downtime and ensures consistent performance without the need for regular brush replacement or cleaning.
8. Wide Speed Range: Brushless motors can operate at a wider speed range compared to brushed motors. They can achieve higher speeds while maintaining stable operation, making them suitable for applications that require variable speed control.
Overall, brushless electric motors offer numerous advantages in terms of efficiency, lifespan, control, power density, and maintenance requirements. These advantages make them a preferred choice in many industries, including automotive, aerospace, robotics, and renewable energy.
Applications of Brushless Electric Motors
Brushless electric motors are extensively used in a wide range of industries and applications due to their numerous advantages. Here are some of the key applications where brushless motors are commonly utilized:
1. Electric Vehicles: Brushless motors are widely used in electric vehicles (EVs) and hybrid electric vehicles (HEVs) due to their high efficiency, torque, and power density. They power the propulsion systems of EVs, including electric cars, motorcycles, buses, and trucks, enabling efficient and eco-friendly transportation.
2. Aerospace and Aviation: Brushless motors find applications in aerospace and aviation industries, where weight, reliability, and performance are critical. They are used in systems such as actuators, flight control surfaces, landing gear, and auxiliary systems, contributing to improved aircraft efficiency and performance.
3. Industrial Machinery: Brushless motors are widely utilized in industrial machinery and equipment, including pumps, compressors, conveyor systems, machine tools, and robotics. Their high torque, accurate control, and durability make them ideal for powering and controlling various industrial processes.
4. Consumer Electronics: Brushless motors are used in a range of consumer electronics, including home appliances, computer peripherals, cooling fans, and drones. Their compact size, high efficiency, and low noise make them suitable for applications that require precise control and quiet operation.
5. Renewable Energy: Brushless motors play a crucial role in renewable energy systems such as wind turbines and solar tracking systems. They convert the mechanical energy from the wind or solar power into electrical energy, facilitating the generation of clean and sustainable power.
6. Medical Devices: Brushless motors are utilized in various medical devices and equipment, including surgical tools, pumps, ventilators, and prosthetic limbs. Their precise control, compact size, and reliability make them suitable for critical medical applications.
7. HVAC Systems: Brushless motors are used in heating, ventilation, and air conditioning (HVAC) systems to drive fans, blowers, and pumps. They provide efficient and variable speed control, contributing to energy savings and improved overall performance of HVAC systems.
8. Automotive Systems: Brushless motors find applications in automotive systems such as power windows, windshield wiper systems, HVAC blowers, and electric power steering (EPS). They offer reliable and efficient performance for these automotive subsystems.
9. Marine and Boating: Brushless motors are used in marine and boating applications, powering systems such as thrusters, trim tabs, and anchor winches. Their resistance to corrosion and ability to operate in harsh environments make them suitable for marine applications.
10. Scientific Research and Lab Equipment: Brushless motors are utilized in various scientific research and laboratory equipment, including centrifuges, spectrometers, and microscopes. Their precise control and low vibration output are essential for accurate scientific measurements and experiments.
These are just a few examples of the many applications where brushless electric motors are used. The versatility, efficiency, and reliability of brushless motors make them a preferred choice in numerous industries, contributing to improved performance and energy efficiency in various systems and devices.
Read more: How Does A Dc Electric Motor Work
Conclusion
Brushless electric motors have revolutionized the world of electric power, offering improved efficiency, reliability, and performance compared to their brushed counterparts. By eliminating the need for brushes and commutators, brushless motors provide numerous advantages, making them widely used in various industries and applications.
The principle of operation for brushless motors involves the interaction between the stator and the rotor. The stator consists of electromagnets arranged around the inner circumference, while the rotor typically contains permanent magnets. Electronic commutation using Hall effect sensors and an electronic speed controller allows for precise control of the motor’s rotation and power output.
Some of the key advantages of brushless electric motors include higher efficiency, longer lifespan, higher power density, smoother control, and reduced electromagnetic interference. These advantages make brushless motors ideal for applications such as electric vehicles, aerospace, industrial machinery, consumer electronics, renewable energy, medical devices, and more.
In conclusion, brushless electric motors have transformed numerous industries by providing efficient, reliable, and high-performance electric power solutions. With ongoing advancements in motor technology, brushless motors are likely to continue evolving, enabling even greater efficiency, power, and versatility in the years to come.
Frequently Asked Questions about How Does A Brushless Electric Motor Work
Was this page helpful?
At Storables.com, we guarantee accurate and reliable information. Our content, validated by Expert Board Contributors, is crafted following stringent Editorial Policies. We're committed to providing you with well-researched, expert-backed insights for all your informational needs.
0 thoughts on “How Does A Brushless Electric Motor Work”