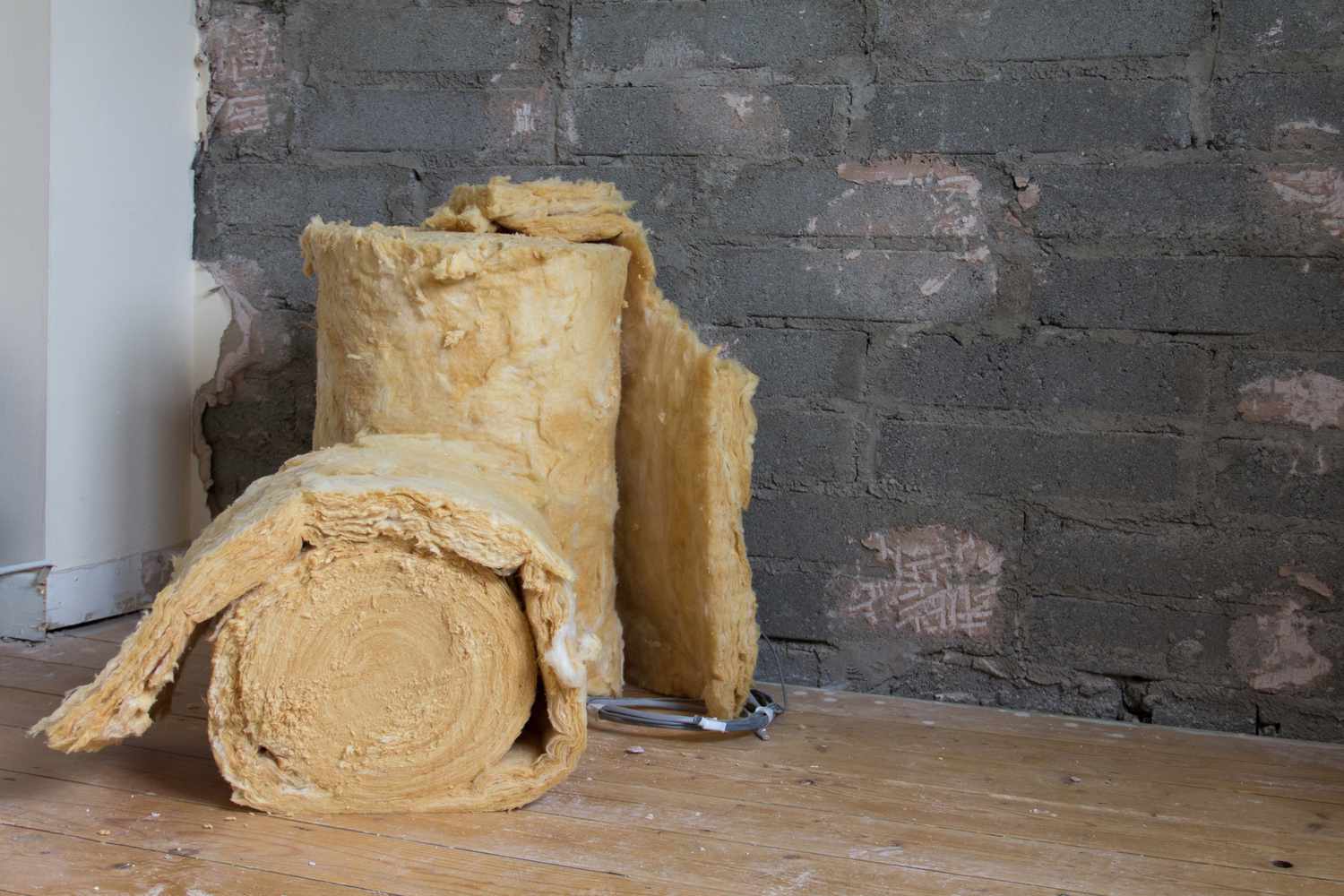
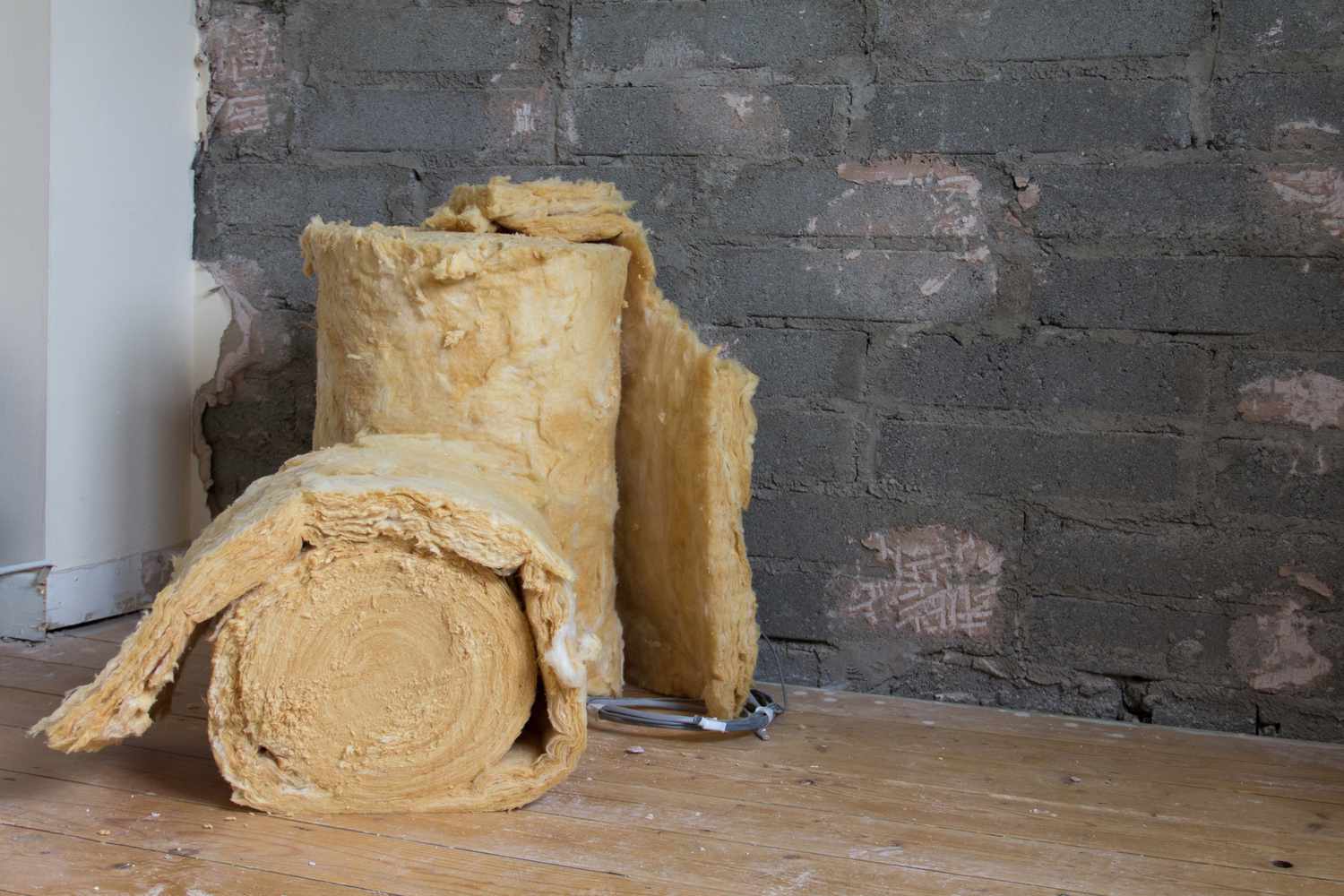
Articles
How Is Fiberglass Insulation Made
Modified: September 1, 2024
Learn about the process of manufacturing fiberglass insulation in this informative article. Gain insight into the production techniques and benefits of using this popular insulating material.
(Many of the links in this article redirect to a specific reviewed product. Your purchase of these products through affiliate links helps to generate commission for Storables.com, at no extra cost. Learn more)
Introduction
Fiberglass insulation is a commonly used material in residential and commercial buildings for its thermal and acoustic insulation properties. It is made from fine strands of glass fibers that are woven together to form a dense, lightweight, and flexible insulation material. This article will provide a comprehensive overview of how fiberglass insulation is made, from the raw materials to the final product.
Fiberglass insulation plays a crucial role in improving energy efficiency and reducing heating and cooling costs. It is widely used in walls, ceilings, floors, and attics to trap air and create a barrier against heat transfer. The manufacturing process of fiberglass insulation involves several steps that are carefully executed to produce a high-quality product.
In this article, we will delve into the ingredients used, the melting and spinning process, the addition of binding agents and additives, the formation of fiber mats, the curing and drying process, and finally, the cutting, packaging, and distribution of fiberglass insulation.
Understanding how fiberglass insulation is made will not only provide insight into the manufacturing process but also emphasize the importance of insulation in creating comfortable and energy-efficient spaces.
Key Takeaways:
- The intricate process of making fiberglass insulation involves melting and spinning glass fibers, adding binding agents and additives, and carefully forming, curing, and drying the fibers. This results in a versatile, eco-friendly, and high-performance insulation material.
- The packaging and distribution of fiberglass insulation are crucial in protecting the material and providing essential information to end-users. The collaboration between manufacturers, wholesalers, retailers, and contractors ensures efficient delivery and installation, contributing to energy-efficient and comfortable living and working environments.
Read more: Why Is Fiberglass Used In Insulation
Basic Overview of Fiberglass Insulation
Fiberglass insulation is a type of thermal insulation material that is widely used in residential and commercial buildings. It consists of long, thin glass fibers that are densely packed together to create a barrier against heat transfer. The unique structure of fiberglass insulation allows it to effectively trap air and prevent the flow of heat, making it an excellent choice for improving energy efficiency and reducing heating and cooling costs.
One of the key benefits of fiberglass insulation is its versatility. It can be used in various applications, including walls, ceilings, floors, and attics. It is available in different forms, such as batts, rolls, or loose-fill, to suit different installation requirements.
The excellent thermal properties of fiberglass insulation are due to the properties of glass fibers. Glass fibers are made from molten glass that is rapidly cooled and spun into fine strands. These strands are then woven together to form a mat-like structure, which creates air pockets that help to resist heat flow.
In addition to its thermal insulation properties, fiberglass insulation also provides soundproofing benefits. The dense structure of the fibers helps to absorb sound waves and reduce noise transmission, making it an ideal choice for areas where noise control is important, such as offices, schools, and multi-unit dwellings.
Furthermore, fiberglass insulation is non-combustible, meaning it does not contribute to the spread of fire. Its fire-resistant properties make it a safe choice for residential and commercial applications. Additionally, fiberglass insulation does not absorb moisture and is resistant to mold and mildew growth, ensuring a healthier indoor environment.
Overall, fiberglass insulation is a cost-effective and environmentally friendly solution for insulating buildings. Its energy-saving properties not only reduce energy consumption but also contribute to a greener and more sustainable future.
Ingredients Used in Fiberglass Insulation
Fiberglass insulation is primarily made from two main ingredients: silica sand and recycled glass. These ingredients are carefully selected and processed to create the fine glass fibers that form the basis of the insulation material.
Silica sand is the main component of fiberglass insulation. It is a naturally occurring mineral that is abundant and widely available. Silica sand is composed of silicon dioxide (SiO2) and is known for its high melting point and thermal stability. The sand is carefully crushed and purified to remove impurities before being used in the manufacturing process.
Recycled glass is another crucial ingredient used in fiberglass insulation. The process of recycling glass involves collecting waste glass and processing it to remove any contaminants. The cleaned glass is then crushed into small particles for further processing.
In addition to silica sand and recycled glass, other minor ingredients are added to enhance the performance and durability of the fiberglass insulation. These include:
- Binding Agents: Binders are added to help hold the glass fibers together and provide cohesion. They act as adhesives, allowing the formation of the insulation material. Common binders used include phenolic resins, acrylic resins, and formaldehyde-free binders.
- Additives: Various additives are incorporated into the mixture to improve the insulation properties and overall performance. For example, flame retardants can be added to enhance the fire resistance of the insulation. Other additives may include anti-static agents, anti-fungal agents, and coloring agents.
- Lubricants: Lubricants are used to facilitate the manufacturing process by reducing friction during the spinning and forming of the glass fibers. They help to ensure a smooth and consistent production process.
All these ingredients work together to create a durable and effective insulation material with excellent thermal and acoustic properties. The precise combination of each ingredient is carefully controlled to produce insulation that meets industry standards and regulatory requirements.
Melting and Spinning the Glass
The first step in the manufacturing process of fiberglass insulation involves melting and spinning the glass. The silica sand and recycled glass particles are combined and loaded into a furnace, where they are heated to high temperatures around 2,500°F (1,371°C). This intense heat causes the glass to melt and become molten.
Once the glass has reached the molten state, it is ready for the spinning process. The molten glass is fed into a machine called a spinner or a centrifuge. The spinner consists of a rotating drum with tiny holes or nozzles in its surface.
As the molten glass is forced through the tiny holes or nozzles, high-speed air or steam is blown onto the glass stream, causing it to stretch and form into fine strands. These strands, known as glass fibers, are extremely thin, with diameters ranging from 3 to 20 microns.
The spinner machine continuously rotates, creating a continuous stream of glass fibers that are collected on a moving conveyor belt. The fibers form a mat-like layer as they are randomly distributed and interwoven with each other.
During the spinning process, it is important to control the speed of the spinner and the blowing force to ensure the desired thickness and density of the glass fibers. The length of the fibers can also be controlled by adjusting the speed and the size of the nozzles from which the molten glass is extruded.
The spinning process is carefully monitored to maintain consistent fiber diameter and distribution. Quality control measures are implemented to ensure that the resulting glass fibers meet the required specifications for insulation performance.
Once the glass fibers have been spun and collected on the conveyor belt, they are ready for the next steps in the manufacturing process, including the addition of binding agents and the formation of the insulation material.
Binding Agents and Additives
After the glass fibers have been spun, binding agents and additives are added to enhance the performance and durability of the fiberglass insulation. Binding agents are used to hold the glass fibers together, providing structural integrity and cohesion to the insulation material.
One common binding agent used in fiberglass insulation is phenolic resin. Phenolic resin is a synthetic polymer that has excellent adhesive properties. It helps to bond the glass fibers together, creating a strong and stable insulation material. Other binders such as acrylic resins or formaldehyde-free binders may also be used depending on the specific requirements and regulations.
In addition to binding agents, various additives are incorporated into the mixture to improve the insulation properties and overall performance. Flame retardants are often added to enhance the fire resistance of the insulation. These additives help to reduce the flammability of the material, making fiberglass insulation a safer choice for applications in residential and commercial buildings.
Anti-static agents may also be added to reduce the buildup of static electricity, which can be a concern in certain environments. Anti-fungal agents may be included to prevent the growth of mold and mildew, ensuring a healthier indoor environment. These additives improve the longevity and usability of the insulation material.
Furthermore, lubricants are sometimes included in the mixture to facilitate the manufacturing process. They reduce friction during the spinning and forming of the fibers, ensuring that the process runs smoothly and consistently.
Throughout the addition of binding agents and additives, precise control is exercised to maintain the desired composition and properties of the fiberglass insulation. Proper mixing and dispersion of these components are essential to ensure uniformity and effectiveness of the insulation material.
By incorporating binding agents and additives, fiberglass insulation is not only structurally sound but also possesses additional characteristics that enhance its performance, such as improved fire resistance, mold resistance, and static control.
When making fiberglass insulation, glass fibers are heated and spun into a wool-like material. This material is then treated with a binding agent and cut into batts or blown into place.
Read more: How To Clean Up Fiberglass Insulation
Forming the Fibers
After the glass fibers have been spun and the binding agents and additives have been added, the next step in the manufacturing process of fiberglass insulation is forming the fibers into a mat-like structure. This process involves carefully arranging and aligning the glass fibers to create a dense and uniform insulation material.
The spun glass fibers are collected on a conveyor belt as they are randomly distributed and interwoven with each other. To ensure proper formation, the fibers are evenly spread across the width of the conveyor belt. This is achieved through the use of oscillating devices or mechanical spreaders.
As the collected glass fibers move along the conveyor belt, the binding agents and additives within the fibers begin to interact and cure. This curing process helps to strengthen the fibers and promote adhesion between them. The formation of the fibers is guided and maintained by the conveyor belt, ensuring the desired thickness and density of the insulation material.
At this stage, the fibers may also undergo mechanical or thermal treatment to enhance their properties. For example, a needling process may be used to mechanically interlock the fibers and improve their dimensional stability. Heat treatment may also be applied to further cure and strengthen the fibers, increasing their resistance to compression and ensuring a long-lasting insulation material.
During the forming process, it is crucial to monitor and control the temperature, humidity, and speed at which the fibers are formed. This helps to maintain the integrity and consistency of the insulation material, ensuring that it meets the required specifications for thermal and acoustic performance.
Once the fibers have been properly formed and cured, they are ready for the next steps in the manufacturing process, including the curing and drying process, cutting the insulation, and packaging for distribution.
Curing and Drying Process
After the formation of the glass fibers, the next step in the manufacturing process of fiberglass insulation is the curing and drying process. This step is crucial for strengthening the fibers and ensuring the final product’s dimensional stability.
The curing process involves exposing the formed fibers to controlled heat. This heat treatment activates the binding agents that were added during the initial stages of production. As the temperature rises, the binding agents cure, creating strong bonds between the glass fibers. This curing process helps to increase the structural integrity of the insulation material and ensures its long-term durability.
Simultaneously, the curing process also aids in the drying of the insulation material. Moisture content within the fibers is gradually evaporated as the heat is applied. This drying step is essential to maintain the desired insulation performance and prevent any potential moisture-related issues such as mold growth or degradation of the material.
The curing and drying process is carefully controlled to ensure an optimal balance between strengthening the fibers and removing moisture. To achieve this, temperature and humidity levels within the curing chamber are monitored closely, and adjustments are made as necessary to maintain the ideal conditions.
Depending on the specific manufacturing requirements and product specifications, the curing and drying process can take several hours or even days. This step is crucial to ensure that the fiberglass insulation reaches its maximum performance potential and meets industry and regulatory standards.
Once the curing and drying process is complete, the fiberglass insulation is ready for the next steps in the manufacturing process, including cutting the insulation to the desired dimensions, packaging, and distribution to end-users.
Cutting the Insulation
After the fiberglass insulation has undergone the curing and drying process, it is time to proceed with cutting the material into the desired dimensions. This step is essential to ensure that the insulation fits properly and can be easily installed in various applications such as walls, ceilings, and floors.
The cutting process can be done using various methods, depending on the specific requirements and production capabilities. One common method is using automated cutting machines equipped with sharp blades or rotating knives. These machines are programmed to cut the insulation material accurately and efficiently, ensuring consistent dimensions and minimizing waste.
Prior to cutting, the fiberglass insulation may have specific markings or guidelines to indicate the appropriate measurements. This helps the operators ensure accuracy and consistency in the cutting process. The insulation may be pre-marked with lines or grids to guide the cutting process and enable precise trimming.
Once the fiberglass insulation has been cut into the desired dimensions, it is usually divided into manageable sections or rolls for packaging and distribution. The cut pieces are carefully inspected to ensure that they meet quality standards and have clean, precise edges.
The cutting process requires precision and attention to detail to ensure that each piece of fiberglass insulation is uniform in size and meets the specified dimensions. Proper cutting is essential to facilitate easy installation and efficient use of the insulation material.
After the insulation has been cut and inspected, it is ready for the final steps in the manufacturing process, which include packaging and distribution to wholesalers, retailers, and end-users.
Packaging and Distribution
Once the fiberglass insulation has been cut into the desired dimensions, it is ready to be packaged and prepared for distribution. The packaging phase is crucial for protecting the insulation during transportation and storage, as well as providing information to end-users.
The packaging of fiberglass insulation typically involves wrapping or enclosing the cut pieces or rolls in a protective cover or packaging material. The packaging material may be a plastic or polyethylene film that shields the insulation from moisture, dust, and other potential contaminants. It provides an extra layer of protection to maintain the integrity and performance of the insulation until it is installed.
During the packaging process, labels and markings are often added to the packaging material. These labels contain important information such as product specifications, insulation type, size, R-value (thermal resistance), safety instructions, and usage guidelines. This ensures that installers and end-users have access to the necessary information for proper installation and usage.
Once packaged, the fiberglass insulation is typically stacked, palletized, and prepared for distribution. The packaged insulation materials are loaded onto trucks or shipping containers, ready to be transported to wholesalers, retailers, or construction sites.
The distribution of fiberglass insulation involves a well-coordinated logistics operation to ensure that the insulation reaches its intended destination promptly and efficiently. Distributors work closely with suppliers to manage inventory, track shipments, and ensure timely deliveries. They may also provide additional services such as on-site delivery and storage solutions to meet the needs of construction projects.
Wholesalers and retailers receive the packaged insulation materials and store them in warehouses or distribution centers until they are ready for sale. They work directly with contractors, builders, and homeowners to provide the necessary insulation materials for residential and commercial projects.
End-users, such as contractors or homeowners, can purchase the packaged fiberglass insulation from wholesalers or retailers. They can then proceed with installing the insulation according to the manufacturer’s instructions and the specific requirements of the building or renovation project.
The packaging and distribution phase ensures that fiberglass insulation reaches the market in an efficient and protected manner. It plays a vital role in delivering high-quality insulation materials to end-users, contributing to energy-efficient and comfortable living and working environments.
Read more: How To Cut Fiberglass Insulation Lengthwise
Conclusion
Fiberglass insulation is a widely used and effective thermal and acoustic insulation material in residential and commercial buildings. Understanding the manufacturing process of fiberglass insulation provides insight into the intricate steps involved in creating this versatile and energy-efficient product.
From the melting and spinning of glass fibers to the addition of binding agents and additives, each stage of the manufacturing process is carefully executed to ensure the production of high-quality insulation. The proper formation, curing, and drying of the fibers, as well as the precise cutting and packaging, contribute to a durable and performance-driven end product.
Fiberglass insulation’s excellent thermal insulation properties, versatility in application, and soundproofing benefits make it a popular choice for improving energy efficiency and creating comfortable spaces. Its non-combustible nature and resistance to mold and moisture growth further enhance its safety and longevity.
The use of silica sand and recycled glass as primary ingredients highlights the eco-friendliness of fiberglass insulation. By repurposing materials and promoting energy efficiency, fiberglass insulation contributes to a greener and more sustainable future.
Throughout the manufacturing process, attention is given to quality control and adherence to industry standards. This ensures that the fiberglass insulation meets the required specifications and performs optimally in various building applications.
Packaging and distribution play a crucial role in safeguarding the insulation during transportation and storage and provide essential information to end-users. The close collaboration between manufacturers, wholesalers, retailers, and contractors ensures that the insulation materials reach their intended destinations, ready to be installed in new construction or renovation projects.
In conclusion, fiberglass insulation is a vital component in creating energy-efficient, comfortable, and environmentally friendly buildings. Its manufacturing process combines advanced technology, high-quality materials, and precise craftsmanship to produce insulation materials that contribute to reduced energy consumption and improved living and working environments.
By understanding how fiberglass insulation is made, we gain a greater appreciation for the importance of proper insulation in creating sustainable and efficient buildings.
Frequently Asked Questions about How Is Fiberglass Insulation Made
Was this page helpful?
At Storables.com, we guarantee accurate and reliable information. Our content, validated by Expert Board Contributors, is crafted following stringent Editorial Policies. We're committed to providing you with well-researched, expert-backed insights for all your informational needs.
0 thoughts on “How Is Fiberglass Insulation Made”