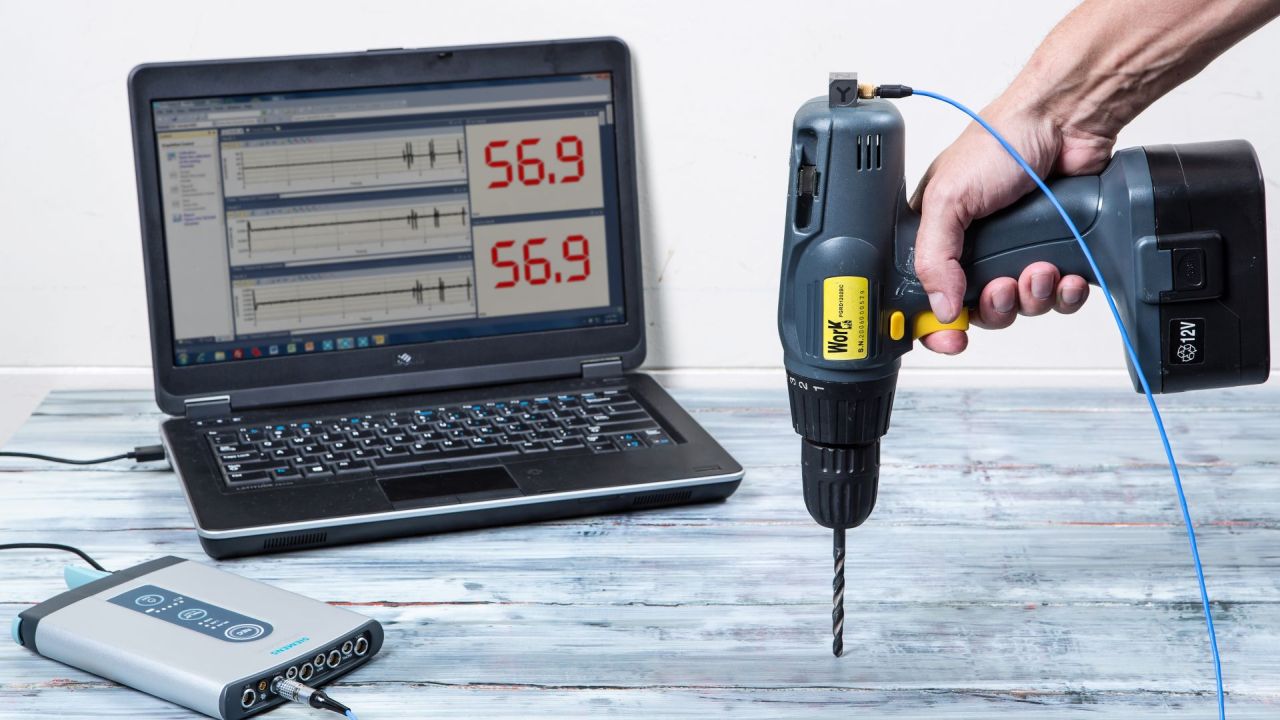
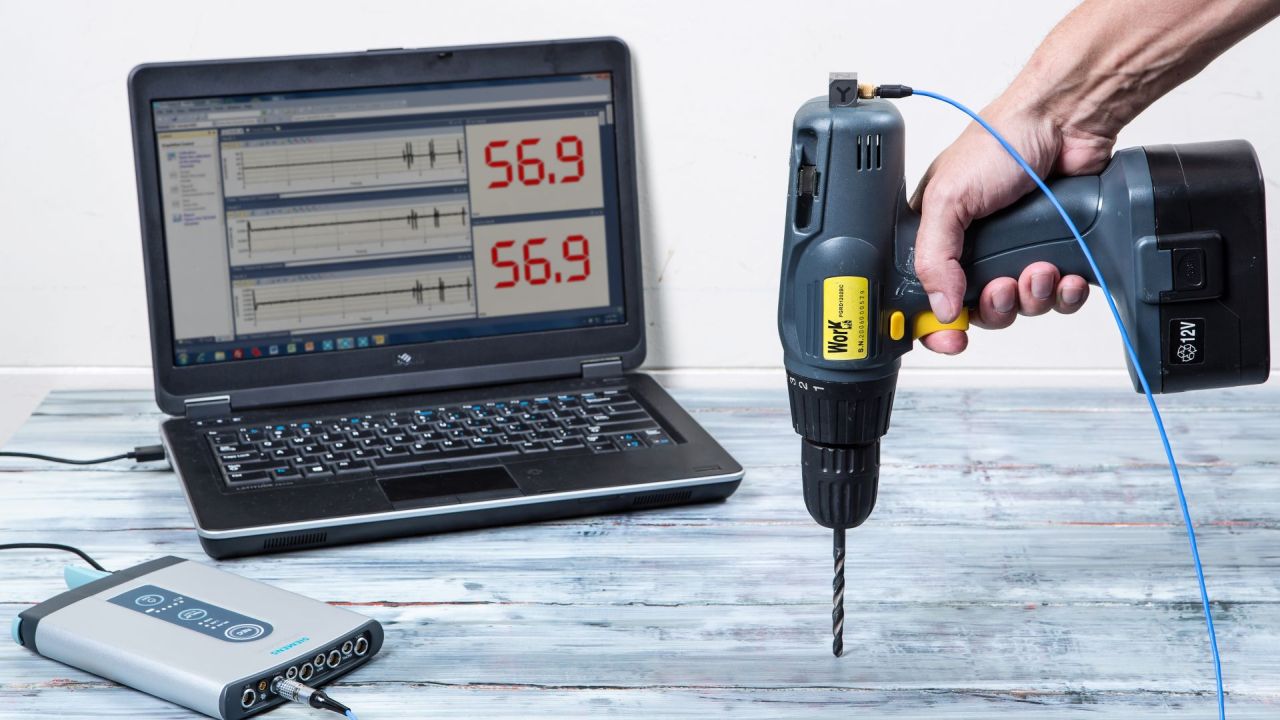
Articles
How To Test Vibration In Hand Tools
Modified: December 7, 2023
Learn how to test vibration in hand tools with our informative articles. Enhance your understanding of tool safety and prevent potential health risks.
(Many of the links in this article redirect to a specific reviewed product. Your purchase of these products through affiliate links helps to generate commission for Storables.com, at no extra cost. Learn more)
Introduction
Hand tools are essential for various tasks, from minor repairs at home to complex projects in industries. However, prolonged use of hand tools can lead to fatigue, discomfort, and even injury for the operators. One crucial factor that contributes to these issues is vibration.
Vibration in hand tools refers to the oscillation or back and forth motion generated by the tool during operation. While some level of vibration is inevitable, excessive vibrations can have detrimental effects on both the operator and the tool itself. Therefore, it is crucial to test and analyze the vibration levels of hand tools to ensure ergonomic design, minimize operator fatigue, and promote tool efficiency.
This article will discuss the importance of testing vibrations in hand tools and provide insights into the basic principles, common testing methods, and the purpose of vibration testing. Additionally, we will explore the factors affecting vibration levels in hand tools, safety precautions during testing, and the interpretation and analysis of vibration test results.
By understanding the significance of vibration testing and implementing appropriate measures, both operators and tool manufacturers can enhance safety, comfort, and productivity.
Key Takeaways:
- Vibration testing in hand tools is crucial for ensuring operator safety, optimizing tool performance, and meeting regulatory standards. It helps identify excessive vibrations and implement design modifications to reduce operator fatigue and minimize the risk of hand-arm vibration disorders.
- Factors affecting vibration levels in hand tools, such as tool design, weight, power source, and operator technique, should be carefully considered during testing and design. Addressing these factors can significantly reduce vibrations and improve tool performance and durability.
Read more: How To Test Hand Tools
Importance of Testing Vibration in Hand Tools
Testing the vibration levels in hand tools is of utmost importance for several reasons. Firstly, it ensures the safety and well-being of the operators. Prolonged exposure to high levels of vibration can lead to a condition called Hand-Arm Vibration Syndrome (HAVS), which includes symptoms such as numbness, tingling, and reduced dexterity. By conducting vibration testing, we can identify tools with excessive vibration levels and take appropriate measures to mitigate the risks.
Secondly, vibration testing helps in optimizing the design and functionality of hand tools. By analyzing the vibration patterns, manufacturers can identify areas for improvement and develop tools that offer more comfort and ergonomic benefits to the users. This, in turn, enhances user satisfaction and productivity.
Moreover, vibration testing allows manufacturers to comply with regulatory standards and guidelines. Many countries have specific regulations in place to limit the vibration exposure that workers can endure. By conducting vibration testing, manufacturers can ensure that their hand tools meet these requirements and avoid potential legal and financial consequences.
Additionally, vibration testing plays a crucial role in maintaining the durability and longevity of hand tools. Excessive vibration can cause premature wear and tear on the tool components, leading to higher chances of breakdowns and decreased tool lifespan. By testing and monitoring vibration levels, manufacturers can identify potential issues early on and make necessary design improvements to enhance the tool’s durability.
Furthermore, for industries that rely on precision and accuracy, such as construction, automotive, and manufacturing, vibration testing helps in ensuring the quality of the end products. Excessive tool vibration can affect the precision of the work, resulting in errors and rework. By testing vibration levels, manufacturers can ensure that their tools meet the required standards and deliver the desired level of accuracy.
Overall, vibration testing in hand tools is essential for promoting operator safety, improving tool design, complying with regulations, maintaining tool durability, and ensuring the quality of the end product. By investing in vibration testing, manufacturers can create hand tools that are not only efficient and reliable but also prioritize the well-being of the operators.
Basic Principles of Vibration Testing
Vibration testing is conducted to measure and analyze the vibration levels of hand tools. By understanding the basic principles of vibration testing, manufacturers can accurately assess the performance and potential issues of their tools. Here are the fundamental principles behind vibration testing:
1. Frequency: Vibration testing involves measuring the frequency of the vibrations produced by a hand tool. Frequency refers to the number of oscillations or cycles per second and is typically measured in Hertz (Hz). Different tools may produce vibrations with varying frequencies, and understanding the frequency range helps in evaluating the potential risks and determining the appropriate measures for vibration control.
2. Amplitude: Amplitude is the extent or magnitude of the vibrations generated by a hand tool. It measures the maximum displacement from the tool’s resting position to its highest point of vibration. Amplitude is usually measured in terms of acceleration, velocity, or displacement, depending on the specific testing requirements.
3. Transmissibility: Transmissibility refers to the behavior of vibrations as they transmit from the tool to the operator’s hand or arm. Various factors, such as the tool’s design, handle grip, and operator’s posture, can influence the transmissibility of vibrations. Understanding this principle helps in identifying ways to minimize the transmission of excessive vibrations and reduce the risk of hand-arm vibration disorders.
4. Measurement Equipment: Vibration testing requires the use of specialized equipment to accurately measure and analyze the vibration levels. Accelerometers are commonly used sensors that measure the acceleration of the vibrations. Vibration analyzers, data loggers, and other testing instruments are used to collect and analyze the vibration data.
5. Standards and Guidelines: Vibration testing is guided by various standards and guidelines set by regulatory bodies and industry organizations. These standards provide specific criteria for acceptable vibration levels and exposure limits for hand tools. Manufacturers must adhere to these standards to ensure the safety and well-being of operators and meet legal requirements.
6. Data Analysis: Once the vibration data is collected, it needs to be analyzed to determine the severity of vibrations and identify any potential issues. Data analysis involves comparing the measurement results with the established standards and guidelines and assessing the potential risk factors associated with the tool’s vibration levels.
By understanding these basic principles of vibration testing, manufacturers can conduct accurate and effective assessments of their hand tools. This knowledge enables them to develop tools that prioritize safety, comfort, and usability for operators, ultimately leading to enhanced user satisfaction and improved tool performance.
Common Testing Methods for Hand Tools
There are several common testing methods used to evaluate the vibration levels of hand tools. Each method has its advantages and limitations, and the choice of method depends on factors such as the type of tool, testing objectives, and available resources. Here are some of the commonly used testing methods:
1. Accelerometer Testing: This method involves attaching an accelerometer to the hand tool to measure the vibration levels. The accelerometer detects the acceleration caused by the vibrations and converts it into an electrical signal that can be analyzed. Accelerometer testing provides detailed and precise vibration data, allowing manufacturers to assess the performance of their tools accurately.
2. Hand-Arm Vibration Meter: A hand-arm vibration meter is a specialized device designed to measure the vibrations transferred from a tool to the hand and arm of the operator. The meter typically includes an accelerometer and a display unit that provides real-time vibration readings. This method allows for on-site testing and immediate assessment of vibration levels.
3. Whole-Body Vibration Assessment: While hand-arm vibration focuses on the vibrations transmitted to the hands and arms, whole-body vibration assessment evaluates the vibrations experienced by the entire body of the operator. This method is commonly used for tools that involve whole-body contact, such as power tools used on the feet or legs. Whole-body vibration assessment helps identify potential risks for operators and provides valuable insights for design improvements.
4. ISO Compliance Testing: The International Organization for Standardization (ISO) has established specific standards and guidelines for hand-arm vibration testing. ISO compliance testing involves conducting tests according to these standards to ensure that the vibration levels of the hand tool are within acceptable limits. This method provides manufacturers with a standardized approach to assess vibration levels and meet regulatory requirements.
5. Field Testing: Field testing involves conducting vibration testing on the hand tools while they are being used in real-world scenarios. This method provides valuable data on the actual vibration levels experienced by operators during their typical tasks. Field testing allows manufacturers to evaluate the performance and efficiency of hand tools in practical environments.
6. Virtual Testing and Simulation: Virtual testing and simulation use advanced computer modeling techniques to assess the vibration levels of hand tools. By simulating the tool’s operation and analyzing the virtual vibration data, manufacturers can make informed design decisions and optimize the tool’s performance before physical prototypes are developed. This method reduces the time and costs associated with traditional testing approaches.
It is important to note that no single testing method is suitable for every situation. Manufacturers often employ a combination of methods to gain comprehensive insights into the vibration characteristics of their hand tools. By selecting appropriate testing methods and analyzing the results, manufacturers can enhance the safety, performance, and user experience of their hand tools.
Purpose and Benefits of Vibration TestingVibration testing of hand tools serves multiple purposes and offers several benefits for both manufacturers and operators. By conducting thorough vibration testing, manufacturers can ensure the quality, safety, and performance of their tools, while operators can experience improved comfort, reduced fatigue, and minimized risk of injuries. Here are the main purposes and benefits of vibration testing:
Purpose of Vibration Testing:
1. Safety Assessment: One of the primary purposes of vibration testing is to assess the safety of hand tools. Excessive vibrations can lead to musculoskeletal disorders and other occupational hazards for operators. Vibration testing helps manufacturers identify tools with high vibration levels and take necessary measures to reduce the risks associated with exposure to those vibrations.
2. Compliance with Standards: Vibration testing ensures that hand tools comply with industry standards and regulatory requirements. Many countries have specific guidelines and exposure limits for hand-arm vibrations that manufacturers must adhere to. By conducting vibration testing, manufacturers can ensure that their tools meet these standards and avoid legal and compliance issues.
3. Quality Control: Vibration testing is a crucial component of quality control for hand tool manufacturing. By testing vibration levels, manufacturers can identify any design or production flaws that might affect the tool’s performance or durability. This helps ensure that only high-quality tools reach the market, enhancing customer satisfaction and brand reputation.
Benefits of Vibration Testing:
1. Operator Safety and Well-being: Vibration testing helps protect operators from the adverse effects of excessive vibrations. By analyzing the vibrations produced by hand tools, manufacturers can identify tools that may cause hand-arm vibration syndrome (HAVS) or other musculoskeletal disorders. Minimizing vibrations through design improvements can reduce operator fatigue, discomfort, and the risk of long-term health issues.
2. Ergonomic Tool Design: Vibration testing provides valuable insights for optimizing the ergonomic design of hand tools. By understanding the vibration patterns and impact on operator comfort, manufacturers can make informed decisions about handle grips, weight distribution, and other design elements. This leads to tools that are more ergonomic, comfortable to use, and less likely to cause operator fatigue or strain.
3. Enhanced Tool Performance: Vibration testing helps identify and rectify any issues that may affect the performance of hand tools. Excessive vibrations can lead to decreased precision, accuracy, and overall tool efficiency. By reducing vibrations through design improvements, manufacturers can enhance the performance and reliability of their tools, improving work productivity and ensuring better results for operators.
4. Extended Tool Lifespan: Excessive vibrations can cause premature wear and damage to hand tools. Vibration testing enables manufacturers to identify and address potential issues that could shorten the tool’s lifespan. By optimizing the design to minimize vibrations, manufacturers can enhance the durability of hand tools, reducing maintenance costs and ensuring longer tool lifespan.
5. Customer Satisfaction: The results of vibration testing lead to the development of high-quality hand tools that prioritize operator safety and comfort. This improves customer satisfaction as operators can work with tools that minimize fatigue, offer better control, and reduce the risk of injuries. Satisfied customers are more likely to recommend and repurchase tools from manufacturers with a reputation for prioritizing user well-being.
Vibration testing of hand tools plays an essential role in the development and assessment of these tools. By ensuring safety, improving design ergonomics, enhancing performance, and extending tool lifespan, vibration testing benefits both manufacturers and operators, resulting in safer, more efficient, and reliable hand tools.
When testing vibration in hand tools, use a vibration meter to measure the tool’s vibration levels. Ensure that the tool is properly maintained and that the operator follows proper usage techniques to minimize vibration exposure.
Factors Affecting Vibration Levels in Hand Tools
The vibration levels of hand tools can be influenced by various factors. Understanding these factors is crucial for manufacturers and operators to identify potential sources of excessive vibrations and implement measures to mitigate them. Here are the key factors that can affect vibration levels in hand tools:
1. Tool Design: The design of a hand tool plays a significant role in determining its vibration levels. Factors such as the handle shape, material, and grip affect how vibrations are transmitted to the operator’s hand. Poorly designed handles or grips can amplify vibrations, leading to increased operator fatigue and discomfort. Manufacturers should prioritize ergonomic design principles, such as vibration-absorbing materials and proper handle contours, to minimize vibration transmission.
2. Tool Weight: The weight of a hand tool also influences its vibration levels. Heavier tools tend to produce higher levels of vibrations, especially if the tool is not well-balanced or has excessive internal vibrations. Reducing the weight of the tool without compromising its functionality can minimize vibrations and improve operator comfort during prolonged use.
3. Tool Power Source: The type of power source used in hand tools can affect vibration levels. For example, electric-powered tools generally produce fewer vibrations compared to pneumatic or gas-powered tools. However, the specific design and construction of the tool can also impact vibration levels, regardless of the power source. Manufacturers should consider the power source and its impact on vibrations when developing hand tools.
4. Operational Speed and Load: The speed and load at which a hand tool operates can significantly impact vibration levels. Higher speeds and heavier loads tend to generate more vibrations. Manufacturers should optimize the tool’s design to handle different operational conditions and reduce the vibration intensity while maintaining adequate performance.
5. Tool Maintenance and Wear: The maintenance and wear of a hand tool can affect its vibration levels over time. Lack of maintenance, worn-out components, or damaged parts can lead to increased vibrations. Regular maintenance, including lubrication, inspection, and replacement of worn-out parts, is essential to minimize vibrations and ensure optimal tool performance.
6. Operator Technique and Grip: The way an operator holds and uses a hand tool can also impact vibration levels. Improper grip and excessive force can amplify vibrations and increase the risk of operator fatigue and injury. Operators should be trained on correct tool handling techniques to minimize the transmission of vibrations to their hands and arms.
7. Workpiece Material and Surfaces: The nature of the workpiece being operated on can influence vibration levels. Hard materials often result in higher vibrations, while softer materials may absorb some vibrations. Additionally, rough or uneven surfaces can contribute to increased tool vibrations. Manufacturers should consider these factors when designing tools for specific applications and provide guidance on suitable workpiece materials and surface conditions.
8. Environmental Factors: Environmental conditions, such as temperature, humidity, and vibration transmission from the work surface, can influence the vibration levels experienced by a hand tool operator. Extremely cold or hot temperatures, high humidity, or unstable surfaces can affect vibration transmission and increase operator discomfort. These factors should be taken into account during tool design and operator training.
By considering and addressing these factors, manufacturers can develop hand tools that minimize vibrations and prioritize operator safety and comfort. Operators, on the other hand, can adopt proper techniques and handle the tools correctly to further reduce the risk of excessive vibrations and related health issues.
Precautions and Safety Measures during Vibration Testing
When conducting vibration testing on hand tools, it is essential to prioritize safety measures to protect both the testing personnel and the integrity of the testing process. Here are some precautions and safety measures to consider during vibration testing:
1. Personal Protective Equipment (PPE): Ensure that all personnel involved in the vibration testing wear appropriate personal protective equipment. This may include safety goggles, gloves, ear protection (in case of loud vibrations), and any other necessary protective gear. PPE helps minimize the risk of injury or exposure to potentially harmful vibrations.
2. Training and Certification: Provide adequate training to the testing personnel on vibration testing procedures, equipment operation, and safety protocols. Properly trained and certified personnel are essential for accurate and safe testing practices, ensuring reliable results and mitigating potential risks.
3. Secure Testing Environment: Conduct vibration testing in a controlled environment that is free from distractions and potential hazards. Ensure that the testing area is well-lit, properly ventilated, and adequately equipped with safety devices like fire extinguishers and first aid kits.
4. Equipment Calibration: Regularly calibrate the vibration testing equipment to ensure accurate and reliable measurements. Calibration should be performed by trained professionals and comply with industry standards. Properly calibrated equipment provides accurate data and minimizes errors in the testing process.
5. Proper Instrumentation Setup: Ensure that the accelerometers or other vibration sensors are correctly installed and securely attached to the hand tools being tested. Faulty or loose sensor setup can lead to inaccurate measurements and compromise the validity of the results. Follow the manufacturer’s guidelines for proper sensor installation.
6. Controlled Testing Parameters: Set and maintain consistent testing parameters throughout the testing process. This includes controlling the test duration, load conditions, and any other variables that may affect vibration levels. Consistency in testing parameters allows for accurate comparisons and reliable analysis of vibration data.
7. Monitoring Operator Fatigue: During vibration testing, it is important to monitor the testing personnel for signs of fatigue or discomfort caused by prolonged exposure to vibrations. Regular breaks should be provided to minimize the risk of overexertion and ensure the well-being of the personnel involved in the testing process.
8. Documentation and Reporting: Maintain thorough documentation of the testing process, including test setup, parameters, results, and any observations. This documentation helps ensure traceability and allows for proper analysis and interpretation of the results. It also facilitates future comparisons and reference during product development or quality control processes.
9. Regular Equipment Maintenance: Perform regular maintenance and inspection of the vibration testing equipment to ensure its proper functioning and accuracy. Follow the manufacturer’s guidelines for maintenance, calibration, and any necessary repairs. Regular equipment maintenance minimizes potential risks and ensures reliable testing results.
10. Compliance with Regulatory Standards: Adhere to applicable regulatory standards and guidelines for vibration testing. Ensure that the testing processes and equipment comply with industry-specific regulations to maintain safety standards and to avoid potential legal and compliance issues.
By implementing these precautions and safety measures during vibration testing, manufacturers can create a safe and controlled testing environment, minimize risks to personnel, and produce accurate and reliable testing results. Prioritizing safety not only protects individuals involved in the testing process but also contributes to the overall quality and effectiveness of the hand tools being tested.
Interpretation and Analysis of Vibration Test Results
Interpreting and analyzing the vibration test results is a crucial step in understanding the performance and potential risks associated with hand tools. The analysis process helps manufacturers identify areas of improvement, enhance tool design, and optimize the performance and safety of the tools. Here are key steps for interpreting and analyzing vibration test results:
1. Reviewing Vibration Data: Begin by reviewing the collected vibration data from the testing process. This data typically includes measurements of vibration amplitude, frequency, and other relevant parameters. Ensure that the data is accurate, properly labeled, and recorded in a standardized format for easy analysis.
2. Comparing with Standards: Compare the measured vibration levels against relevant industry standards, regulations, or internal guidelines. This allows you to determine if the hand tool complies with acceptable vibration limits and exposure guidelines. If the vibration levels exceed the specified limits, it indicates that further action or modifications are required to reduce the risks associated with excessive vibrations.
3. Identifying High Vibration Areas: Analyze the data to identify specific areas or components of the hand tool that produce higher vibration levels. This helps in pinpointing potential design flaws, material imbalances, or other factors contributing to excessive vibrations. Understanding the specific high vibration areas allows for targeted improvements to mitigate the issue effectively.
4. Assessing Risks: Assess the potential risks associated with the measured vibration levels. Consider factors such as the duration of tool use, operator exposure, and the potential for hand-arm vibration-related health effects. Evaluate the severity and duration of vibration exposure to determine if any action is necessary to reduce the risks for operators and comply with regulatory requirements.
5. Root Cause Analysis: Perform a root cause analysis to identify the underlying factors contributing to excessive vibrations. This involves examining the design, construction, and operating conditions of the hand tool. Look for potential sources of vibrations, such as imbalances, loose components, or inadequate damping mechanisms. Determine the root causes to guide future improvements and design modifications.
6. Design Improvements: Based on the analysis and root cause identification, work on implementing design improvements to minimize vibrations. This may involve redesigning components for better balance, optimizing the grip design for enhanced ergonomics, using vibration damping materials, or incorporating vibration isolation mechanisms. Prioritize measures that aim to reduce vibrations at their source for effective long-term results.
7. Performance Evaluation: Evaluate the impact of design improvements or modifications on vibration levels and overall tool performance. Conduct follow-up testing to measure the effectiveness of the implemented changes. This helps in assessing if the desired reduction in vibration levels has been achieved and if any further adjustments are needed to optimize the tool’s performance.
8. Documentation and Continuous Monitoring: Document the analysis process, including specific findings, improvements made, and any ongoing monitoring plans. Maintain records of the vibration test results, analysis reports, and design iterations for future reference. Continuously monitor vibration levels, conduct periodic testing, and assess feedback from operators to ensure that the hand tools consistently meet acceptable vibration criteria and user requirements.
By following these steps for interpreting and analyzing vibration test results, manufacturers can make data-driven decisions, improve hand tool designs, and minimize risks associated with excessive vibrations. This helps create safer and more efficient tools that prioritize operator comfort and well-being.
Conclusion
Vibration testing in hand tools is a critical aspect of ensuring operator safety, optimizing tool performance, and meeting regulatory standards. By understanding the importance of testing vibrations, manufacturers can develop hand tools that prioritize ergonomic design, minimize operator fatigue, and enhance overall efficiency.
Through the application of vibration testing, manufacturers can identify excessive vibration levels and take appropriate measures to mitigate the risks. This includes optimizing tool design, incorporating vibration-absorbing materials, and implementing effective grip and handle designs.
Vibration testing also helps manufacturers comply with regulatory standards and guidelines, ensuring that their hand tools meet the required limits for operator exposure to vibrations.
By analyzing and interpreting vibration test results, manufacturers can identify areas for improvement and implement design modifications to reduce vibrations at their source. This leads to hand tools that provide enhanced comfort, reduce operator fatigue, and minimize the risk of hand-arm vibration disorders.
The factors affecting vibration levels in hand tools, such as tool design, weight, power source, operational speed, and operator technique, should be carefully considered during the testing and design process. By addressing these factors, manufacturers can significantly reduce vibrations and improve the overall performance and durability of the hand tools.
It is crucial to prioritize precautions and safety measures during vibration testing to protect the testing personnel and maintain the integrity of the testing process. Adequate training, the use of personal protective equipment, and regular equipment maintenance are essential for a safe testing environment.
Interpreting and analyzing vibration test results allow manufacturers to make informed design decisions, optimize tool performance, and minimize the risks associated with excessive vibrations. Root cause analysis and continuous monitoring help drive continuous improvement and ensure that hand tools evolve to meet the changing needs and expectations of users.
In conclusion, vibration testing in hand tools plays a vital role in improving operator safety, enhancing tool design, and optimizing performance. By incorporating vibration testing into the development process, manufacturers can create hand tools that prioritize operator well-being, ultimately leading to safer and more efficient work practices across various industries.
Frequently Asked Questions about How To Test Vibration In Hand Tools
Was this page helpful?
At Storables.com, we guarantee accurate and reliable information. Our content, validated by Expert Board Contributors, is crafted following stringent Editorial Policies. We're committed to providing you with well-researched, expert-backed insights for all your informational needs.
0 thoughts on “How To Test Vibration In Hand Tools”