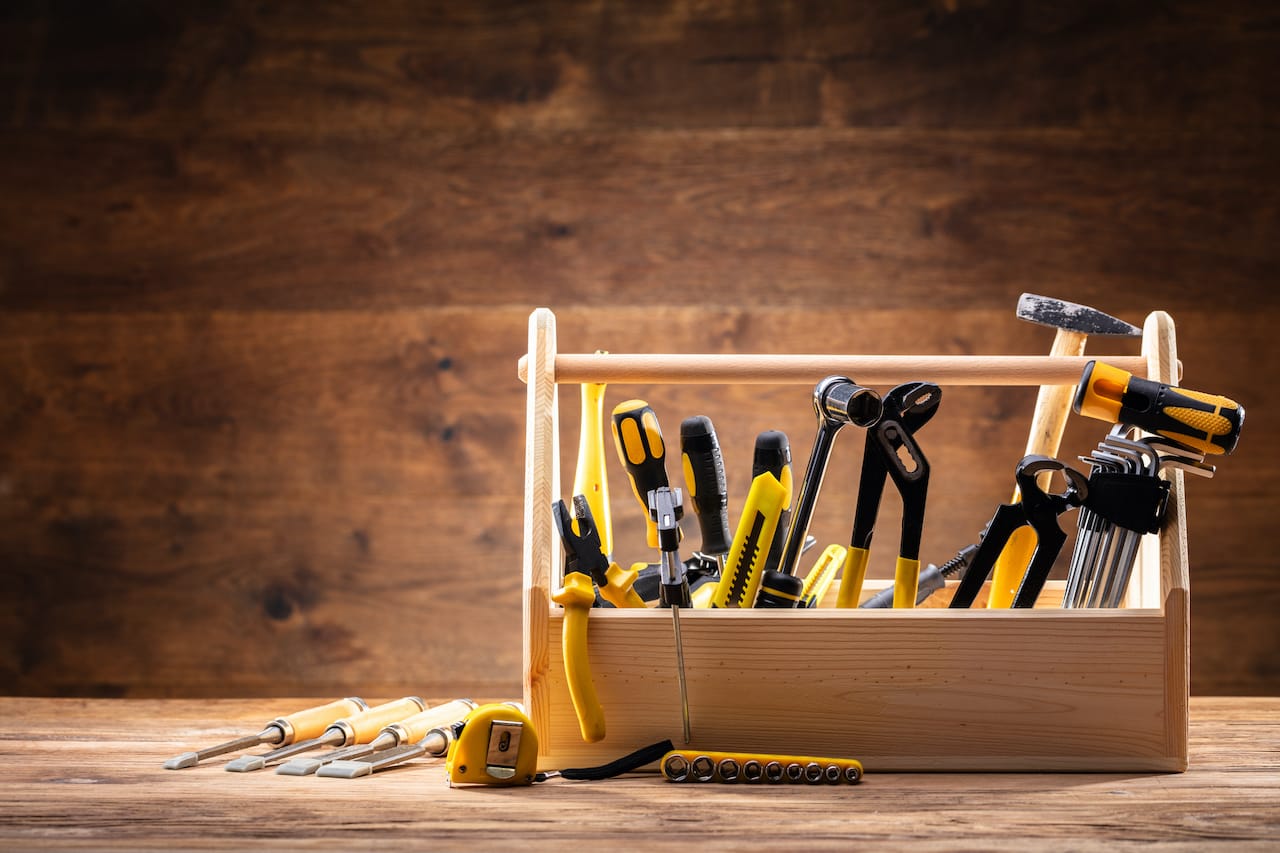
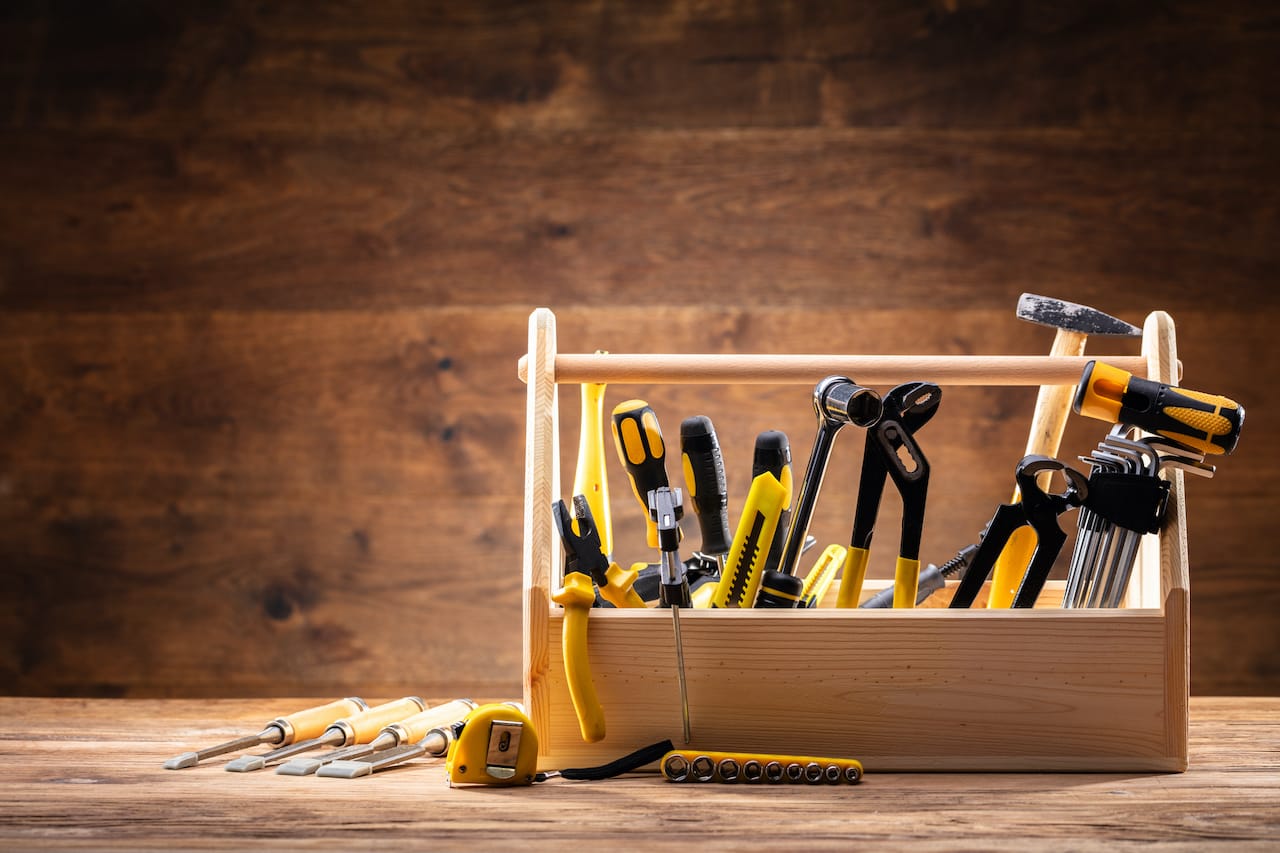
Articles
How To Test Hand Tools
Modified: January 8, 2024
Learn how to properly test and evaluate hand tools with informative articles. Enhance your knowledge and make informed choices for your projects.
(Many of the links in this article redirect to a specific reviewed product. Your purchase of these products through affiliate links helps to generate commission for Storables.com, at no extra cost. Learn more)
Introduction
Hand tools are essential for any trade or DIY project. From hammers to screwdrivers, wrenches to pliers, these tools play a crucial role in getting the job done efficiently and effectively. However, it is not enough to simply purchase a set of hand tools and assume they will perform as expected. To ensure their quality, reliability, and safety, it is important to subject these tools to rigorous testing.
In this article, we will explore the importance of hand tool testing and the different types of tests that can be conducted to evaluate their performance. Whether you are a professional tradesperson or a weekend DIY enthusiast, understanding how to test hand tools will enable you to make informed decisions when selecting and using these essential implements.
By testing hand tools, you can assess their durability, functionality, ergonomic design, safety features, and accuracy. This not only guarantees that the tools will perform optimally in various work situations, but it also minimizes the risk of accidents or injuries caused by malfunctioning or substandard tools.
So, if you’re ready to dive into the world of hand tool testing and discover the ins and outs of ensuring tool quality, let’s dive in!
Key Takeaways:
- Ensure safety, durability, and functionality of hand tools through rigorous testing. Visual, functional, durability, ergonomic, safety, and accuracy testing are essential for reliable, long-lasting tools.
- Thorough testing guarantees reliable, ergonomic, and accurate hand tools, enhancing work efficiency and minimizing accidents. Regular maintenance and adherence to safety guidelines ensure prolonged tool lifespan and user confidence.
Read more: How To Test Vibration In Hand Tools
Importance of Hand Tool Testing
Hand tool testing is vital for several reasons. First and foremost, it helps to ensure the safety of the users. Faulty tools can lead to accidents and injuries, posing a significant risk to the individuals operating them. By conducting thorough testing, manufacturers can identify and rectify any potential defects, ensuring that the tools meet the necessary safety standards.
Additionally, hand tool testing plays a crucial role in determining the durability and longevity of these tools. Tools that undergo rigorous testing are more likely to withstand heavy usage and harsh conditions, making them an investment that will endure over time. Knowing that your tools can withstand the demands of your work gives you peace of mind and saves you money in the long run.
Furthermore, testing hand tools helps to evaluate their functionality and performance. It ensures that the tools can carry out their intended tasks effectively and efficiently. For example, a properly tested screwdriver should grip and turn screws securely without slipping, and a hammer should strike with precision and have minimal vibration. By testing these functional aspects, users can have confidence in their tools’ capabilities, enabling them to work with greater accuracy and productivity.
Another key aspect of hand tool testing is evaluating their ergonomic design. Ergonomics refers to the study of how tools interact with the human body and aims to optimize user comfort and prevent musculoskeletal disorders. Through testing, manufacturers can assess the handle grip, weight distribution, and overall design of the tools, ensuring that they are comfortable and easy to use over extended periods without causing unnecessary strain or discomfort. This is especially important for professionals who rely on their tools for long hours of work.
Lastly, hand tool testing helps to maintain accuracy and precision. Tools that require measurements, such as rulers or calipers, need to provide accurate readings. Testing these tools ensures that they meet industry standards for accuracy, allowing users to rely on their measurements with confidence and precision.
In summary, hand tool testing is essential for ensuring safety, durability, functionality, ergonomic design, and accuracy. By putting tools through rigorous testing, manufacturers can guarantee that their products meet the necessary quality standards and provide users with reliable, long-lasting, and effective tools. This not only enhances work efficiency but also minimizes the risk of accidents or injuries caused by faulty or substandard tools. When you invest in tested and reliable hand tools, you are investing in your own safety and success in carrying out your projects.
Types of Hand Tool Testing
Hand tool testing encompasses several different types of evaluations to ensure the quality, performance, and safety of the tools. Let’s explore the various types of hand tool testing:
- Visual Inspection: One of the first steps in hand tool testing is a visual inspection. This involves carefully examining the tool for any visible defects, such as cracks, dents, or irregularities in the design or construction. It also includes verifying that all components are securely in place and that the tool has the necessary labeling or markings for identification and safety compliance.
- Functional Testing: This type of testing assesses the tool’s ability to perform its intended function. For instance, a screwdriver would be tested to ensure that the tip securely fits into a screw head and that it can effectively turn the screw without slipping. Functional testing may involve simulating real-world scenarios to evaluate the tool’s performance under various conditions.
- Durability Testing: Durability testing evaluates how well the tool withstands continuous usage, repeated impacts, and exposure to harsh environments. This testing may involve subjecting the tool to repetitive actions, applying heavy loads or forces, or subjecting it to extreme temperatures or humidity. The goal is to determine the tool’s ability to withstand wear and tear over time.
- Ergonomic Testing: Ergonomic testing focuses on evaluating the tool’s design and how it interacts with the user’s body. It includes assessing the handle grip, weight distribution, and overall comfort during use. This testing ensures that the tool is ergonomically optimized, reducing the risk of strain or injury during prolonged use.
- Safety Testing: Safety testing is a critical aspect of hand tool evaluation. It involves assessing whether the tool meets safety standards and regulations. This may include testing for insulation properties, ensuring proper grounding, and evaluating the design to minimize the risk of accidental injuries, such as finger pinching or slipping. Safety testing is crucial to protect users from potential hazards associated with tool usage.
- Accuracy Testing: Hand tools that require measurements, such as rulers, levels, or calipers, should undergo accuracy testing. This type of testing ensures that the tools provide precise and consistent measurements. Testers may compare the tool’s readings to a known standard to verify its accuracy or use specialized equipment to assess its measurement capabilities with high precision.
By conducting these various types of hand tool testing, manufacturers can ensure that their products meet industry standards, perform optimally, and prioritize the safety and satisfaction of users. This comprehensive testing process guarantees that the tools are reliable, durable, ergonomic, and accurately perform their intended functions, enabling professionals and DIY enthusiasts to carry out their tasks with confidence and efficiency.
Visual Inspection
Visual inspection is a crucial step in hand tool testing and involves a thorough examination of the tool’s external appearance and construction. This type of inspection allows users to identify any visible defects or irregularities that may affect the tool’s performance or safety.
During a visual inspection, several key components should be evaluated:
- Overall Condition: Assess the general condition of the tool, checking for any signs of damage, such as cracks, dents, or excessive wear. Inspect the tool for any signs of rust or corrosion, which can indicate poor quality or inadequate maintenance.
- Handle Grip: Examine the handle grip, ensuring that it is securely attached to the tool. Check for any signs of damage or wear on the handle, such as fraying or cracking. The handle should offer a comfortable and ergonomic grip to prevent slipping or discomfort during use.
- Mechanical Connections: Verify that all mechanical connections, such as hinges or moving parts, are properly aligned and functioning smoothly. Ensure that there are no loose or missing components that could impact the tool’s functionality or safety.
- Markings and Labels: Inspect the tool for necessary markings and labels, such as the manufacturer’s name, model number, and safety precautions. These markings provide important information about the tool’s specifications and guidelines for safe use.
- Weight and Balance: Assess the weight and balance of the tool, ensuring that it feels balanced and comfortable in your hand. A well-balanced tool is easier to control and reduces the risk of fatigue or strain during use.
- Safety Features: Identify any safety features or mechanisms that the tool should have, such as blade guards or safety locks. Ensure that these features are present and in good working condition.
Visual inspection should be performed before every use of a hand tool, as even small defects or damage can affect its functionality or pose safety risks. It is also important to regularly inspect and clean hand tools to prevent the build-up of dirt or debris that could impact their performance.
By conducting a thorough visual inspection, users can identify and address any visible issues with their hand tools, ensuring that they are in proper working condition and safe to use. This simple yet crucial step helps to extend the lifespan of the tools and minimize the risk of accidents or injuries during operation.
Functional Testing
Functional testing is a critical aspect of hand tool testing that evaluates the tool’s ability to perform its intended function effectively and reliably. This type of testing focuses on assessing how well the tool performs its specific tasks and ensures that it meets the necessary standards for functionality and performance.
Here are some key steps involved in functional testing:
- Task Simulation: To evaluate the tool’s functionality, testers need to simulate real-world tasks that the tool is designed for. For example, if testing a screwdriver, the tester would simulate driving screws into different materials to assess how securely and efficiently the tool performs the task.
- Fit and Compatibility: Testers check how well the tool fits into the intended work area or workpiece. For example, a wrench should fit securely onto bolts of different sizes without slipping or causing damage. A properly fitting tool ensures that the task can be completed efficiently and accurately.
- Operation and Performance: Evaluate how the tool operates during specific tasks. For example, test the ergonomics and ease of use, ensuring that the tool is comfortable to handle and does not cause unnecessary strain or fatigue during extended use. Evaluate the performance of the tool, such as the amount of force or pressure required to complete a task.
- Efficiency and Precision: Assess the tool’s efficiency and precision in performing its intended tasks. This includes evaluating how accurately the tool can drive screws, cut materials, or tighten bolts. A high-performing tool should provide consistent results and reduce the need for rework.
- Adaptability: Test the tool’s ability to adapt and perform in different situations or conditions. For example, a pair of pliers should be tested to ensure that it can grip various sizes and types of objects securely. Assess how well the tool adjusts to different angles or positions for optimal performance.
Functional testing is important to ensure that the tools meet the required standards of performance and effectiveness. By conducting these tests, users can have confidence that their tools will perform reliably and efficiently during various work scenarios.
It is recommended to conduct functional testing regularly, especially as you acquire new hand tools or if you haven’t used a tool for an extended period. This allows you to identify any functional issues and address them promptly, ensuring that your tools are always in optimal condition for use.
By investing time in functional testing, users can trust that their hand tools will deliver the expected results, improving productivity, and reducing the risk of errors or accidents during their projects.
When testing hand tools, always check for any signs of wear and tear, such as rust, cracks, or loose parts. Test the functionality of the tool by using it as intended to ensure it performs properly.
Durability Testing
Durability testing is an essential aspect of hand tool evaluation, as it assesses the tool’s ability to withstand continuous usage, repeated impacts, and exposure to harsh conditions. This type of testing helps determine the tool’s overall strength, resilience, and longevity.
When conducting durability testing, the following factors are typically considered:
- Strength and Sturdiness: Testers evaluate the tool’s structural integrity and its ability to withstand heavy loads or forces. They assess if the tool maintains its form and strength when subjected to significant pressure or impacts.
- Repetitive Actions: Tools that involve repetitive actions, such as staplers or ratchets, are tested to ensure they can withstand repeated use without degradation in performance. The tool should be able to maintain its functionality and reliability even after prolonged and continuous operation.
- Material Quality: Evaluate the quality of materials used in constructing the tool. Examine the strength of metal components, such as blades or jaws, to ensure that they do not bend or deform under normal usage conditions. Similarly, assess the durability of plastic or rubber parts to prevent premature wear or deterioration.
- Environmental Resistance: Tools are often exposed to various environmental factors, such as moisture, dust, or extreme temperatures. Durability testing involves subjecting the tool to these conditions to assess its ability to withstand such exposure without degradation or damage.
- Corrosion Resistance: Hand tools that are used in humid or corrosive environments should undergo corrosion resistance testing. This ensures that the tool’s materials, such as stainless steel or coated surfaces, can resist rust or corrosion, prolonging the tool’s lifespan and maintaining its performance.
Durability testing is important to ensure that hand tools can withstand the rigors of everyday use in various work environments. By subjecting the tools to these tests, manufacturers can identify any weak points or potential areas of concern and make necessary improvements to ensure the tool’s durability.
It is also important for users to carry out their own durability testing by carefully observing how the tool performs over time. Regular maintenance, such as cleaning and lubrication, can help prolong the tool’s lifespan and maintain its durability.
By conducting durability testing, users can be confident that their hand tools will continue to perform reliably, even under demanding conditions. Additionally, durable tools provide a cost-effective solution by reducing the need for frequent replacements and ensuring long-term productivity.
Ergonomic Testing
Ergonomic testing is a crucial aspect of hand tool evaluation that focuses on the tool’s design and its interaction with the user’s body. The goal of ergonomic testing is to ensure that tools are comfortable, safe, and easy to use, minimizing the risk of strain or injury during prolonged use.
When conducting ergonomic testing, the following factors are typically considered:
- Handle Grip: Evaluate the handle grip of the tool to ensure that it provides a secure and comfortable hold. The grip should be designed to reduce slipping and provide adequate cushioning to minimize the strain on the user’s hand.
- Weight Distribution: Assess the tool’s weight distribution to ensure that it is well-balanced. A well-balanced tool reduces the effort required to hold and control it, minimizing fatigue and strain on the user’s wrist and arm.
- Hand Position: Evaluate the tool’s design to ensure that it promotes a natural and ergonomic hand position during use. The tool should allow for a neutral wrist alignment and minimize awkward angles or movements that may lead to discomfort or injury.
- Ambidextrous Design: Consider whether the tool is suitable for both left-handed and right-handed users. Tools that can be comfortably used by individuals of either hand preference ensure inclusivity and versatility in the workplace.
- Vibration Reduction: Assess the tool’s ability to minimize vibrations. Hand tools that generate high levels of vibration can cause hand-arm vibration syndrome or contribute to musculoskeletal disorders. Testing for effective vibration reduction ensures user comfort and safety.
- Ease of Adjustment: Evaluate how easily the tool can be adjusted to accommodate different user preferences or work requirements. Adjustable features, such as handle length or grip size, allow users to customize the tool to their specific needs, enhancing comfort and usability.
Ergonomic testing is vital because it helps to prevent musculoskeletal disorders and work-related injuries caused by prolonged or awkward tool use. By ensuring that tools are ergonomically optimized, manufacturers can enhance user comfort, productivity, and safety in various work environments.
Users can also contribute to ergonomic testing by providing feedback on the tool’s comfort and usability during their own use. This valuable input allows manufacturers to continually improve the design and ergonomics of their tools.
By incorporating ergonomic features and conducting thorough ergonomic testing, hand tool manufacturers can enhance user satisfaction and well-being. A tool that is comfortable, safe, and easy to use minimizes the risk of work-related injuries and promotes efficiency and productivity in various professional and DIY applications.
Safety Testing
Safety testing is a critical aspect of hand tool evaluation that focuses on assessing the tool’s safety features and ensuring that it complies with industry regulations and standards. The goal of safety testing is to minimize the risk of accidents and injuries during tool use and promote a safe working environment.
When conducting safety testing, the following factors are typically considered:
- Insulation Properties: Testers evaluate whether the tool has adequate insulation to protect users from electrical shock or other hazards. Tools that come into contact with electrical components or work in energized environments should possess proper insulation properties to prevent electrical accidents.
- Guarding and Shielding: Evaluate whether the tool has sufficient guarding or shielding mechanisms to protect users from potential hazards. For example, a power saw should have a blade guard to prevent accidental contact with the rotating blade.
- Slip Resistance: Assess the tool’s grip to ensure that it offers slip-resistant features, especially in wet or slippery conditions. Slip-resistant handles provide users with a secure hold on the tool, minimizing the risk of accidents caused by the tool slipping from their grip.
- Locking Mechanisms: Evaluate the tool’s locking mechanisms, if applicable, to ensure that they are reliable and secure. Locking mechanisms, such as blade locks on utility knives or adjustable wrenches, should hold the tool in place during use, preventing accidental collapse or movement that may lead to injuries.
- Impact Resistance: Test the tool’s ability to withstand impact without breakage or deformation. This ensures that the tool remains intact and safe to use even when subjected to accidental drops or impact during operation.
- Sharpness and Cutting Efficiency: Assess the sharpness of cutting tools, such as knives or shears, to ensure that they are not overly sharp or dull. Dull tools may require excessive force to cut, increasing the risk of slips or accidents, while overly sharp tools may pose injury hazards.
- Proper Labeling and Instructions: Verify that the tool has accurate, visible, and proper labeling, including safety warnings and instructions for use. Clear instructions help users understand the tool’s intended use and any precautions required for safe operation.
Safety testing is crucial to protect users from potential hazards associated with the use of hand tools. By ensuring that tools meet safety standards and regulations, manufacturers can provide users with tools that are reliable, safe, and minimize the risk of work-related accidents or injuries.
Users should also follow the manufacturer’s instructions and recommendations for safe tool handling and maintenance. Regular inspections, proper storage, and adhering to safety guidelines contribute to a safe work environment and promote injury prevention.
By conducting comprehensive safety testing, hand tool manufacturers prioritize the well-being and safety of the users, providing them with tools that can be used confidently and without unnecessary risks.
Accuracy Testing
Accuracy testing is an important aspect of hand tool evaluation, especially for tools that involve measurements or precise tasks. This type of testing ensures that the tools provide accurate and reliable results, enabling users to work with confidence and precision.
When conducting accuracy testing, the following factors are typically considered:
- Measurement Accuracy: Evaluate the tool’s ability to provide accurate measurements. For example, rulers, tape measures, or calipers should be tested against a known standard to verify their accuracy. This ensures that the tools provide precise measurements, minimizing errors in tasks that require precise dimensions.
- Cutting or Drilling Precision: Assess tools that involve cutting or drilling tasks, such as saws or drills, to ensure they perform precise cuts or holes. These tools should be able to maintain accurate angles, depths, or lengths, allowing users to achieve the desired results consistently.
- Level or Alignment Accuracy: Evaluate tools such as levels, plumb bobs, or laser alignment devices to ensure they provide accurate readings for leveling or alignment tasks. These tools should deliver reliable results, enabling users to achieve straight, level, or properly aligned surfaces or structures.
- Stability and Repeatability: Assess the tool’s stability and repeatability in providing consistent results. Tools that rely on measurements or precise actions should be tested to ensure that they deliver the same results over multiple uses or in various work environments.
- Function Specific Accuracy: Evaluate tools with specific functions, such as torque wrenches or angle finders, to ensure they provide accurate readings or adjustments. These tools should be calibrated and tested to deliver precise results within the specific range or parameters.
- Sensor or Detector Accuracy: Test tools with sensors or detectors, such as electronic stud finders or moisture meters, to verify their accuracy in detecting or measuring specific properties. These tools should provide reliable and accurate information to guide users in their tasks or assessments.
Accuracy testing is important, especially when precise measurements or tasks are required, as it ensures that the tools deliver consistent and reliable results. By using accurate tools, users can achieve better quality outcomes, reduce rework, and minimize errors or inconsistencies in their projects.
Regular calibration and maintenance of tools that involve accuracy are essential to preserve their accuracy over time. Following the manufacturer’s instructions and guidelines for calibration and maintenance can help users ensure the tools’ ongoing accuracy and reliability.
By conducting thorough accuracy testing and maintaining accuracy throughout the lifespan of the tools, manufacturers provide users with tools that can be trusted for precise measurements and tasks, ultimately enhancing productivity and the quality of work.
Read more: How To Hand Form Body Panels With Hand Tools
Conclusion
Hand tool testing is a crucial process to ensure the quality, reliability, and safety of these essential implements. By subjecting hand tools to various types of testing, manufacturers can assess their performance, durability, functionality, ergonomic design, safety features, and accuracy.
Visual inspection allows users to identify any visible defects or irregularities that may affect the tool’s performance or safety. Functional testing evaluates how well the tool performs its intended tasks and ensures that it meets the necessary standards for functionality and performance.
Durability testing assesses the tool’s ability to withstand continuous usage, repeated impacts, and exposure to harsh conditions. Ergonomic testing focuses on evaluating the tool’s design and how it interacts with the user’s body to minimize strain or injury during use.
Safety testing ensures that the tool meets safety standards and regulations, protecting users from potential hazards. Accuracy testing evaluates the tool’s ability to provide accurate and reliable measurements or perform tasks with precision.
By conducting these comprehensive tests, hand tool manufacturers can provide users with reliable, durable, ergonomic, and safe tools that deliver accurate and consistent results. This not only enhances work efficiency but also minimizes the risk of accidents or injuries caused by faulty or substandard tools.
Users are encouraged to follow the manufacturer’s guidelines for tool safety, maintenance, and proper use. Regular inspections, cleaning, and maintenance of hand tools contribute to their longevity, performance, and safety. A well-maintained and tested tool ensures that users can work with confidence, precision, and comfort.
In conclusion, understanding how to test hand tools is essential for professionals and DIY enthusiasts alike. By investing in thoroughly tested and reliable hand tools, users can ensure their safety, enhance their productivity, and achieve quality results in their projects.
Frequently Asked Questions about How To Test Hand Tools
Was this page helpful?
At Storables.com, we guarantee accurate and reliable information. Our content, validated by Expert Board Contributors, is crafted following stringent Editorial Policies. We're committed to providing you with well-researched, expert-backed insights for all your informational needs.
0 thoughts on “How To Test Hand Tools”