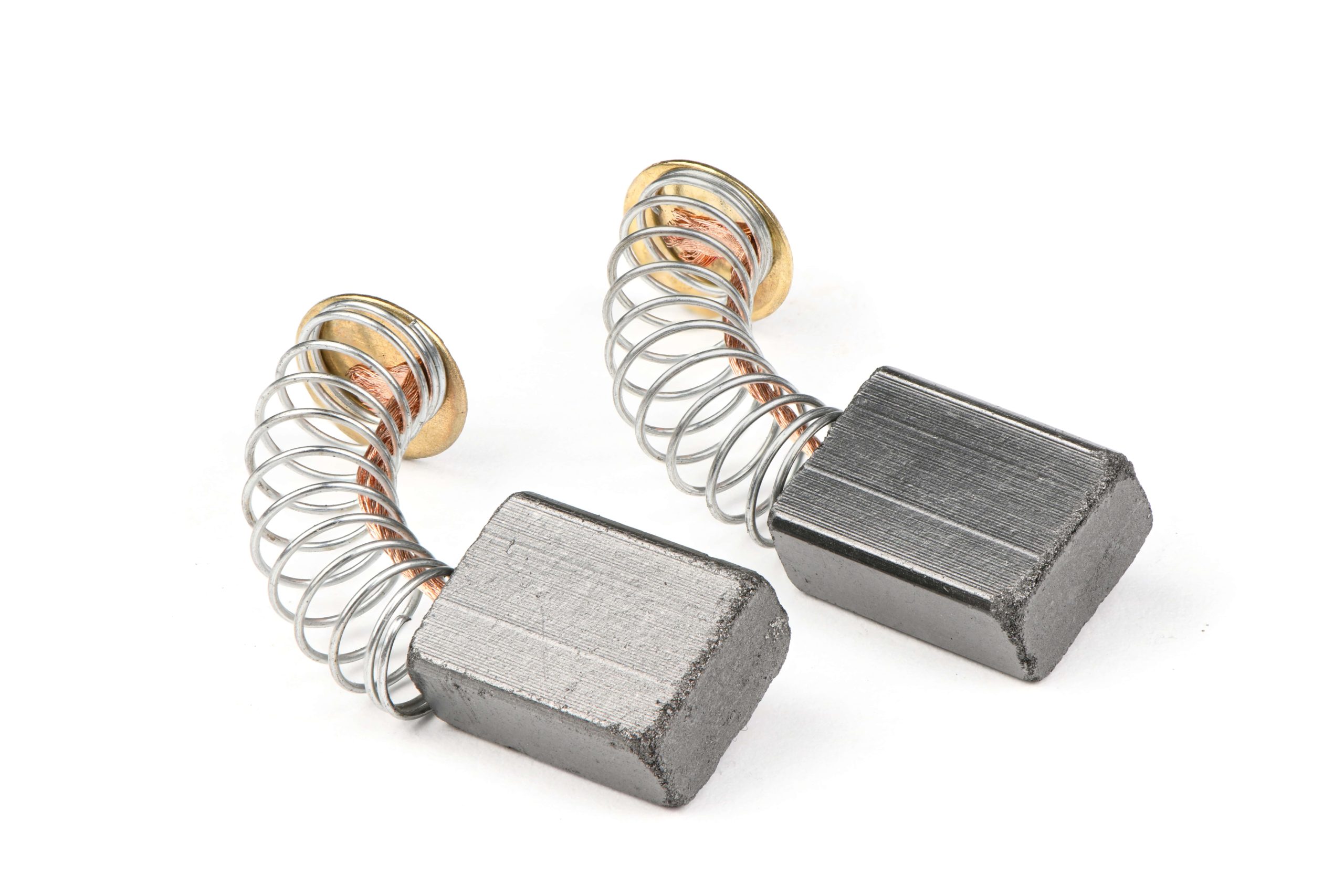
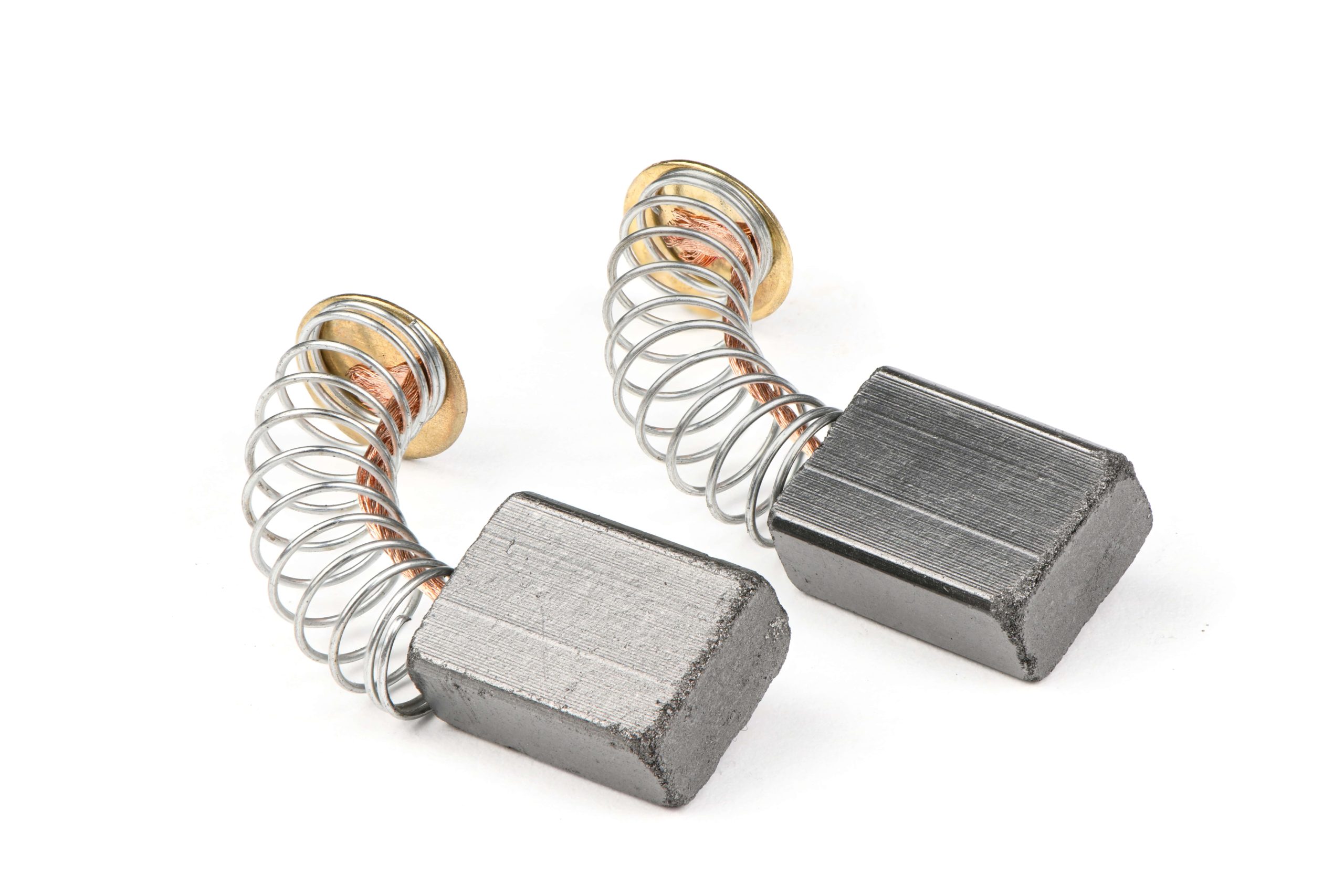
Articles
What Do Brushes Do In An Electric Motor
Modified: January 4, 2024
Discover the role of brushes in an electric motor in this informative article. Gain insights into how brushes contribute to the efficient functioning of electric motors.
(Many of the links in this article redirect to a specific reviewed product. Your purchase of these products through affiliate links helps to generate commission for Storables.com, at no extra cost. Learn more)
Introduction
Electric motors play a crucial role in countless devices and machines that power our daily lives. From household appliances to industrial equipment, electric motors provide the mechanical energy needed to drive various systems. While there are different types of electric motors, one common variation is the brushed electric motor.
In this article, we will take a closer look at the role of brushes in an electric motor and explore their functions and significance. We will also delve into the materials and construction of brushes, as well as the problems associated with them. Additionally, we will discuss the maintenance and replacement of brushes to ensure the optimal performance of electric motors.
Whether you are an engineer, a hobbyist, or simply curious about how electric motors work, understanding the role of brushes in these motors is essential. So, let’s dive into the world of brushed electric motors and discover the importance of brushes in their operation.
Key Takeaways:
- Brushes in brushed electric motors play a crucial role in transferring electrical current to the rotating armature, enabling the conversion of electrical energy into mechanical motion. Regular maintenance and timely replacement of brushes are essential for optimal motor performance and longevity.
- Understanding the functions and significance of brushes in electric motors is vital for ensuring the efficient and reliable operation of various devices and machines. By prioritizing the care and maintenance of brushes, we can prolong the lifespan of electric motors, improve their efficiency, and minimize the risk of unexpected failures.
Brushed Electric Motors: An Overview
Before we delve into the details of brushes in an electric motor, let’s first understand what a brushed electric motor is. A brushed electric motor, also known as a carbon brush motor, is a type of electric motor that utilizes brushes to transmit electrical current to the motor’s rotating armature.
Brushed electric motors have been widely used for many decades due to their simplicity, affordability, and reliability. They find applications in various devices such as power tools, small appliances, automotive systems, and more.
Unlike brushless motors that use electronic commutation, brushed motors rely on physical brushes to establish electrical contact between the power source and the rotating armature. These brushes are an integral part of the motor’s design, enabling the flow of current to the armature, thus generating the necessary rotating magnetic field that drives the motor’s motion.
Now that we have a brief understanding of brushed electric motors, let’s move on to the main focus of this article – the role and function of brushes in these motors.
What Are Brushes in an Electric Motor?
Brushes are essential components in a brushed electric motor that facilitate the transfer of electrical current from the power source to the rotating armature. They are typically made of carbon or graphite materials, which have excellent electrical conductivity and wear resistance.
Brushes are positioned inside the motor’s housing in such a way that they make direct contact with the commutator or the collector rings on the armature. The commutator is a segmented cylindrical structure that helps to control the direction of current flow in the motor.
When the motor is powered on, the brushes press against the commutator or collector rings, creating a connection between the power source and the armature. This allows current to flow through the brushes and into the armature windings, causing the armature to rotate.
The brushes, therefore, act as electrical conductors, transferring electric power to the rotating part of the motor. Their strategic position and continuous contact with the commutator ensure a steady supply of current to the armature, resulting in the desired motion of the motor.
It is important to note that the design and arrangement of brushes can vary depending on the specific motor design. In some cases, multiple sets of brushes may be employed to enhance performance and distribute the current evenly across the commutator or collector rings.
Now that we have a basic understanding of what brushes are in an electric motor, let’s explore their unique functions and significance in the motor’s overall operation.
Function of Brushes in an Electric Motor
The primary function of brushes in an electric motor is to establish and maintain electrical contact between the power source and the rotating armature. By transferring current to the armature winding, brushes enable the conversion of electrical energy into mechanical energy, thus driving the motor’s motion.
Here are some key functions of brushes in an electric motor:
- Conduction of Electrical Current: Brushes serve as the intermediary between the power source and the armature, allowing the flow of electrical current. The brushes make physical contact with the commutator or collector rings, ensuring a consistent and reliable supply of current to the motor.
- Allowing Directional Current Flow: The commutator, in conjunction with the brushes, helps to control the direction of current flow in the armature. As the armature rotates, the brushes maintain contact with different segments of the commutator, ensuring that the current is fed in the appropriate direction for continuous rotation.
- Transferring Power to the Armature: Through the brushes, electrical power is transferred from the power source to the armature windings. This power supply results in the generation of a rotating magnetic field, which interacts with the stationary magnets in the motor to produce mechanical motion.
- Enabling Speed Control: By adjusting the pressure or tension on the brushes against the commutator, the speed of the motor can be regulated. Increasing or decreasing the brush pressure allows for a fine-tuning of motor speed within certain limits.
- Facilitating Smooth Operation: Brushes help to maintain a smooth and continuous electrical connection with the commutator or collector rings. They need to be properly aligned and in good condition to minimize sparking, arcing, or excessive friction, which can cause motor performance issues.
Without brushes, the flow of electrical current to the armature would be disrupted, resulting in the motor’s inability to function. The brushes play a crucial role in ensuring the efficient and reliable operation of brushed electric motors.
When using brushes in an electric motor, make sure to regularly check and replace them if necessary to maintain optimal performance and prevent potential damage to the motor.
Brush Materials and Construction
The materials used for brushes in an electric motor are carefully selected to ensure optimal conductivity, durability, and compatibility with the motor’s operation. Carbon and graphite are the most commonly used materials for brush construction due to their excellent electrical properties.
Carbon brushes are composed of a mixture of graphite and carbon, which forms a conductive material capable of withstanding the harsh conditions within an electric motor. They are typically manufactured by combining these materials with a binder, such as resin, and then molded into the desired shape.
The construction of brushes involves several key elements:
- Brush Body: The brush body is the main structural component that houses the conductive material. It is designed to fit within the motor’s brush holders or guides and maintain the proper alignment and contact with the commutator or collector rings.
- Carbon/Graphite Material: The carbon or graphite material used in the brush composition provides excellent electrical conductivity and heat resistance. It is chosen for its low friction properties, allowing smooth contact with the commutator or collector rings. The composition and density of the material may vary depending on specific motor requirements.
- Lead Wires: To establish an electrical connection between the brush and the motor’s power source, lead wires are attached to the brush body. These wires transmit the current from the brush to the external circuit.
- Spring Mechanism: Brushes are often equipped with a spring mechanism or tensioning device to exert a controlled and consistent pressure against the commutator or collector rings. This ensures proper contact and helps reduce excessive wear and sparking.
It is worth mentioning that the selection of brush materials and construction can vary depending on the specific motor design, voltage requirements, operating conditions, and desired performance characteristics.
Overall, the materials and construction of brushes in an electric motor are carefully engineered to provide the necessary electrical conductivity, mechanical strength, and durability for reliable motor operation over an extended period of time.
Read more: How To Replace Brushes In Electric Motor
Problems Associated with Brushes in Electric Motors
While brushes play a critical role in facilitating the operation of an electric motor, they are not without their challenges. Over time, brushes can experience various issues that may affect the performance and efficiency of the motor. Here are some common problems associated with brushes in electric motors:
- Brush Wear: Due to the nature of their contact with the commutator or collector rings, brushes can wear down over time. Continuous friction and arcing can cause the brush material to degrade and reduce its effectiveness in transferring current. Brush wear can result in increased resistance, reduced efficiency, and even motor failure if not addressed.
- Brush Dust and Debris: As brushes wear down, they can generate dust and debris that may accumulate on the commutator or collector rings. This buildup can cause insulation problems, disrupt the electrical contact, and ultimately lead to motor malfunction. Regular cleaning and maintenance are necessary to prevent excessive dust accumulation.
- Spark and Arc Formation: During the operation of an electric motor, brushes can generate sparks and arcs due to the intermittent contact with the commutator or collector rings. Excessive sparking can cause heat buildup, damage the brushes and commutator surfaces, and result in electrical shorts or other performance issues. Proper maintenance and monitoring are essential to minimize sparking.
- Brush Alignment Issues: Brushes need to be properly aligned with the commutator or collector rings to ensure even contact and current distribution. Misalignment can lead to uneven wear, increased resistance, and reduced motor efficiency. Regular inspection and adjustment of brush alignment are necessary to maintain optimal performance.
- Brush Spring Tension: The tension of the brush springs plays a crucial role in maintaining proper contact and pressure against the commutator or collector rings. Insufficient or excessive spring tension can result in poor electrical contact, increased wear, and potential motor failure. Regular checks and adjustments of brush spring tension are important for optimal performance.
Addressing these problems promptly and implementing regular maintenance practices can help mitigate the impact of brush-related issues in electric motors. Understanding the signs of brush wear or malfunction and taking appropriate action can extend the lifespan and reliability of the motor.
Maintenance and Replacement of Brushes
To ensure the smooth and efficient operation of an electric motor, regular maintenance and timely replacement of brushes are essential. Here are some maintenance practices and considerations for brushes in electric motors:
- Regular Inspection: Conduct routine inspections of the brushes to check for signs of wear, damage, or misalignment. Look for any build-up of dust or debris on the commutator or collector rings. Regular inspection helps identify potential issues before they escalate.
- Cleaning: Keep the brushes and commutator or collector rings clean. Remove any dust or debris build-up with a soft brush or compressed air. Be cautious not to damage the brushes or other sensitive components during the cleaning process.
- Brush Replacement: When the brushes have worn down to a certain level, it is necessary to replace them. Consult the manufacturer’s guidelines or specifications to determine the appropriate brush replacement interval based on the motor type, usage, and operating conditions.
- Proper Brush Alignment: Ensure that the brushes are aligned correctly with the commutator or collector rings. Misalignment can lead to uneven wear, poor contact, and reduced motor performance. Adjust the brush alignment if necessary, following the manufacturer’s guidelines.
- Spring Tension Adjustment: Monitor and adjust the tension of the brush springs as needed. The proper spring tension ensures consistent pressure and contact between the brushes and commutator or collector rings. Refer to the motor’s documentation or seek professional assistance for accurate spring tension adjustment.
- Quality Brushes: When replacing brushes, choose high-quality brushes that are compatible with the motor’s specifications. Using approved or recommended brushes ensures optimal performance and longevity.
- Professional Assistance: For complex motor systems or if you’re uncertain about maintenance procedures, it’s advisable to seek the assistance of a qualified technician or electrician. They can provide expert guidance, perform necessary adjustments, and ensure proper brush replacement.
By following these maintenance practices and addressing brush-related issues promptly, you can extend the lifespan of the brushes and maximize the performance and longevity of the electric motor.
Remember, regular maintenance not only improves the efficiency of the motor but also reduces the risk of unexpected failures and costly repairs. It is crucial to prioritize the care and maintenance of brushes to ensure the reliability and smooth operation of the electric motor.
Conclusion
Brushes are integral components in brushed electric motors, facilitating the transfer of electrical current to the rotating armature. By establishing and maintaining electrical contact with the commutator or collector rings, brushes enable the conversion of electrical energy into mechanical energy, driving the motor’s motion. They play a fundamental role in the efficient and reliable operation of numerous devices and machines, from power tools to automotive systems.
Understanding the functions and significance of brushes in electric motors allows us to appreciate their vital role in powering various applications. However, brushes are not without their challenges. Issues such as brush wear, dust accumulation, sparking, alignment problems, and spring tension can impact motor performance over time.
To mitigate these problems, regular maintenance of brushes is crucial. Regular inspections, cleaning, and alignment adjustments are essential to ensure optimal brush performance. Timely replacement of brushes is also necessary to maintain the efficiency and longevity of the motor. It is important to consult the manufacturer’s guidelines and seek professional assistance, if needed, to ensure proper maintenance practices.
By prioritizing the care and maintenance of brushes, we can prolong the lifespan of electric motors, improve their efficiency, and minimize the risk of unexpected failures. Regular maintenance not only saves costs in the long run but also enhances the performance and reliability of brushed electric motors.
In conclusion, brushes in electric motors are critical components that enable the transfer of electrical energy into mechanical motion. Their functions in conducting current, directing current flow, and enabling speed control are essential for motor operation. By properly maintaining and replacing brushes, we can ensure optimal performance and prolong the lifespan of electric motors, benefiting a wide range of applications in our daily lives.
Frequently Asked Questions about What Do Brushes Do In An Electric Motor
Was this page helpful?
At Storables.com, we guarantee accurate and reliable information. Our content, validated by Expert Board Contributors, is crafted following stringent Editorial Policies. We're committed to providing you with well-researched, expert-backed insights for all your informational needs.
0 thoughts on “What Do Brushes Do In An Electric Motor”