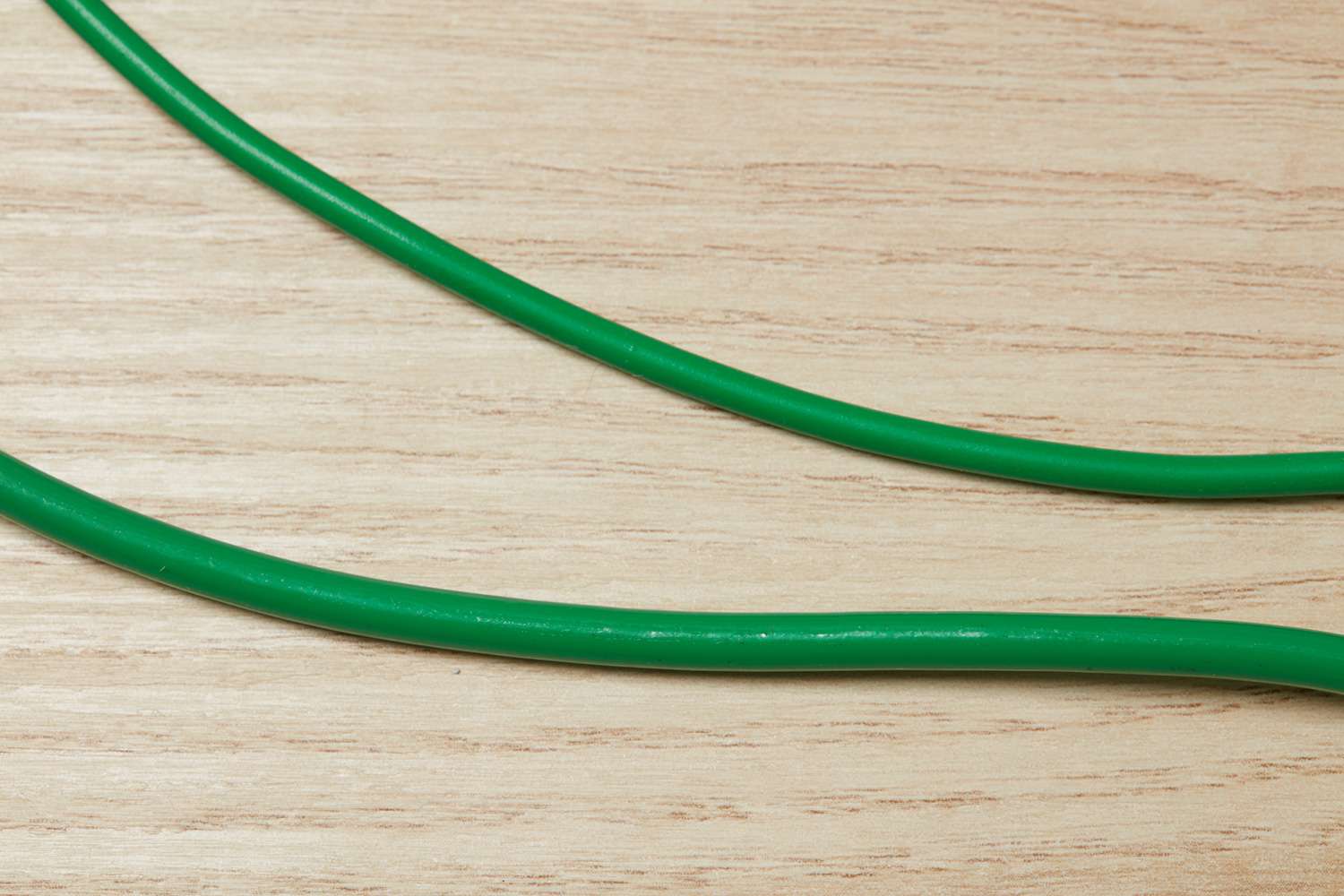
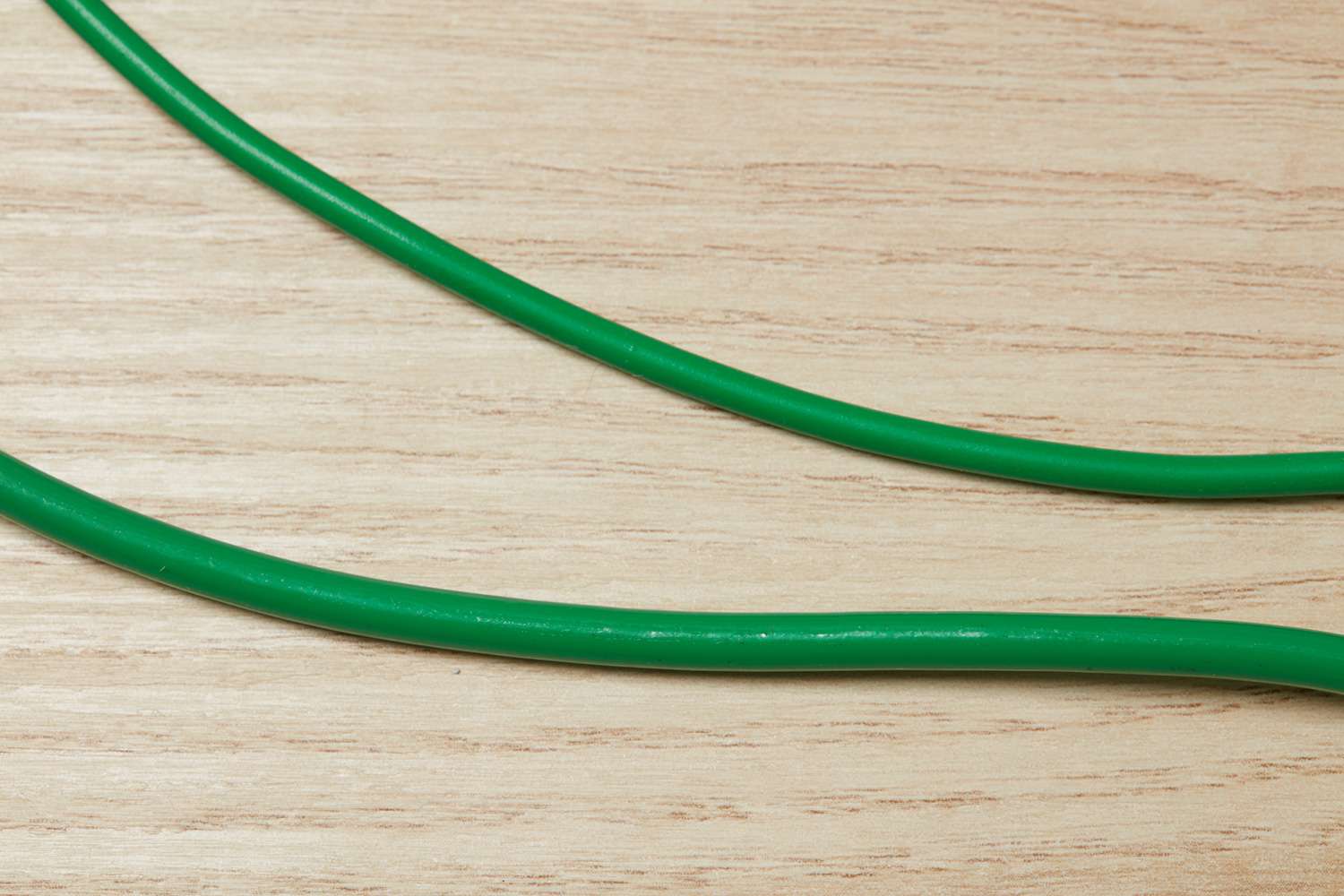
Articles
What Is Electrical Wire Insulation Made Of
Modified: October 19, 2024
Learn about the articles regarding what electrical wire insulation is made of. Find out the materials used and their importance in electrical installations.
(Many of the links in this article redirect to a specific reviewed product. Your purchase of these products through affiliate links helps to generate commission for Storables.com, at no extra cost. Learn more)
Introduction
In the world of electrical wiring, insulation plays a crucial role in ensuring safe and efficient operation. It is the protective covering that surrounds electrical wires and cables, safeguarding them from external elements, preventing electrical leakage, and reducing the risk of electrical shock or fires. Understanding the different types of electrical wire insulation and their characteristics is essential for choosing the right wiring for your specific needs.
Key Takeaways:
- The right wire insulation is crucial for electrical safety, temperature resistance, flexibility, and chemical protection. Understanding the specific needs of your application ensures optimal performance and longevity.
- Choosing insulation materials with minimal environmental impact, recyclability, and sustainability promotes a greener future while maintaining functionality and safety in electrical systems.
Read more: What Is Electrical Wire Made Of
The Importance of Electrical Wire Insulation
Electrical wire insulation acts as a barrier between the conductor (the metal wire) and the surrounding environment. It prevents the flow of electricity from coming into contact with moisture, dust, heat, chemicals, and other potentially damaging factors. Without proper insulation, wires could become exposed, leading to short circuits, power fluctuations, or even electrical fires. Insulation also helps to maintain consistent electrical conductivity by minimizing energy loss or interference.
Common Types of Electrical Wire Insulation
There are several types of insulation materials used in electrical wiring, each with its own set of characteristics and applications:
Polyvinyl Chloride (PVC) Insulation
PVC insulation is one of the most widely used types due to its affordability, flexibility, and resistance to moisture. It is a thermoplastic material that can withstand a wide range of temperatures, making it suitable for both indoor and outdoor installations. PVC insulation is commonly used in residential electrical wiring, power cords, and appliances.
Thermoplastic Insulation
Thermoplastic insulation, such as polyethylene and polypropylene, offers excellent thermal and electrical properties. It is durable, resistant to chemicals, and can handle high temperatures. Thermoplastic insulation is commonly found in automotive wiring, telecommunications cables, and industrial applications.
Read more: What Is Insulation Made Of
Cross-Linked Polyethylene (XLPE) Insulation
XLPE insulation is highly cross-linked, which enhances its thermal and mechanical properties. It has excellent resistance to temperature extremes, moisture, and chemicals. XLPE insulation is commonly used in power distribution cables, underground wiring, and high-voltage applications.
Rubber Insulation
Rubber insulation, made from natural or synthetic rubber, offers exceptional flexibility and durability. It is resistant to heat, abrasion, and chemicals. Rubber insulation is typically found in portable electrical tools, machinery, and industrial wiring.
Nylon Insulation
Nylon insulation is known for its high melting point, toughness, and resistance to impact. It is commonly used in high-temperature applications, such as motor winding wires, heating elements, and aerospace wiring.
Polyvinyl Chloride (PVC) Insulation
Polyvinyl Chloride (PVC) insulation is one of the most commonly used types of insulation in electrical wiring. It is a thermoplastic material that offers a range of benefits and is suitable for various applications.
PVC insulation is known for its affordability, making it a cost-effective choice for both residential and commercial wiring projects. Additionally, PVC insulation is highly flexible, allowing for easy installation and routing of wires. This flexibility makes it ideal for applications where wires need to be bent or maneuvered around corners.
Another advantage of PVC insulation is its excellent resistance to moisture, making it suitable for indoor as well as outdoor installations. This resistance makes PVC-insulated wires less prone to damage caused by exposure to water or other liquids.
PVC insulation also has a good thermal rating, meaning it can handle a wide range of temperatures without degrading or losing its insulating properties. This makes it suitable for use in environments with high or low temperatures, such as electrical wiring in attics or underground applications.
Furthermore, PVC insulation offers good resistance against many chemicals, making it a reliable choice for installations in industrial settings where exposure to various substances is common.
It is important to note that PVC insulation is not suitable for all applications. While it performs well in standard conditions, it may not be the best choice for extreme conditions or high-voltage applications. PVC insulation has a lower temperature rating compared to other types of insulation, so it may not be suitable for environments with very high temperatures.
Additionally, PVC insulation is not as flame-resistant as some other types of insulation materials. While it provides a certain level of fire resistance, it may not perform as well as insulation materials specifically designed for fire protection.
Despite these limitations, the affordability, flexibility, and moisture resistance of PVC insulation make it a popular choice for a wide range of electrical wiring applications. It meets the electrical safety standards and is widely available in the market, making it a convenient option for many electricians and homeowners.
Read more: What Is Foam Insulation Made Of
Thermoplastic Insulation
Thermoplastic insulation is a type of insulation commonly used in electrical wiring due to its excellent electrical and thermal properties. This type of insulation is made from polymers such as polyethylene and polypropylene, which are highly versatile and offer a range of benefits.
One of the key advantages of thermoplastic insulation is its durability and resistance to chemical corrosion. It is able to withstand exposure to various substances, making it suitable for use in environments where wires may come into contact with oils, solvents, or other chemicals.
Thermoplastic insulation also exhibits excellent thermal properties, allowing it to handle a wide range of temperatures. It is capable of maintaining its insulating properties even in extreme heat or cold conditions, making it ideal for applications in both indoor and outdoor settings.
Flexibility is another benefit of thermoplastic insulation. Wires with thermoplastic insulation can be easily bent and routed, making installation more convenient and efficient. This flexibility is especially useful in situations where wires need to be maneuvered around corners or in tight spaces.
Another advantage of thermoplastic insulation is its resistance to moisture. This makes it suitable for installations in damp environments or areas with high humidity. The moisture resistance helps prevent water damage to the wires and reduces the risk of electrical shorts or corrosion.
Thermoplastic insulation also has excellent electrical insulating properties, which ensures efficient and reliable transmission of electrical current. This, combined with its durability and resistance to wear and tear, makes it a popular choice for a variety of applications, including automotive wiring, telecommunications cables, and industrial equipment.
It is important to note that while thermoplastic insulation offers many benefits, it may not be suitable for all applications. Like any other type of insulation, it has its limitations. For example, it may not provide the same level of flame resistance as other specialized insulation materials. In situations where fire safety is a concern, it is important to consider alternative options that meet specific fire protection requirements.
Overall, thermoplastic insulation is a versatile and reliable choice for electrical wiring, offering excellent durability, chemical resistance, thermal performance, and flexibility. When selecting insulation materials for your wiring project, be sure to consider the specific needs and requirements of the installation to ensure optimal safety and performance.
Cross-Linked Polyethylene (XLPE) Insulation
Cross-Linked Polyethylene (XLPE) insulation is a popular choice for electrical wiring that requires high performance and reliability. XLPE insulation is created by chemically cross-linking polyethylene molecules, resulting in improved mechanical, thermal, and electrical properties.
One of the key advantages of XLPE insulation is its excellent thermal resistance. It can withstand high temperatures without degrading or losing its insulating properties, making it suitable for use in applications where heat resistance is crucial. XLPE-insulated wires are commonly used in power distribution cables, underground wiring, and high-voltage installations where temperature extremes can occur.
In addition to its thermal resistance, XLPE insulation offers excellent electrical properties. It provides high insulation resistance and low dielectric loss, ensuring efficient and reliable electrical transmission. This makes it suitable for applications that require long cable runs or high power transmission.
XLPE insulation is also known for its excellent mechanical properties. It is highly resistant to abrasion, impacts, and moisture, making it durable and long-lasting. This resilience to external factors helps to maintain the integrity of the insulation, reducing the risk of failure or electrical leakage.
Furthermore, XLPE insulation has good resistance to chemicals, making it suitable for installations in environments where wires may come into contact with oils, solvents, or other corrosive substances. This chemical resistance ensures the longevity and reliability of the wiring system.
Despite its many advantages, it is important to note that XLPE insulation is generally more expensive compared to other types of insulation. However, the superior performance and durability it offers make it a worthwhile investment, especially in critical applications where reliability and safety are paramount.
It is worth mentioning that XLPE insulation is not as flexible as some other types of insulation materials. The cross-linking process makes it less pliable, which can make installation slightly more challenging and may require specialized tools or techniques.
In summary, XLPE insulation is a high-performance option for electrical wiring that requires exceptional thermal resistance, excellent electrical properties, and durability. Its resistance to heat, chemicals, moisture, and mechanical stress makes it a preferred choice for power distribution systems, underground wiring, and other demanding applications. Consider the specific requirements and environmental conditions of your project when choosing insulation materials to ensure optimal performance and safety.
Rubber Insulation
Rubber insulation is a popular choice for electrical wiring due to its exceptional flexibility, durability, and resistance to various environmental factors. It is a versatile insulation material that is utilized in a wide range of applications, from portable electrical tools to industrial machinery.
One of the key advantages of rubber insulation is its excellent flexibility. It can easily bend and twist without cracking or losing its insulating properties, making it ideal for applications where the wires need to be moved or routed in tight spaces. The flexibility of rubber insulation also allows for easier installation and reduces the risk of wire damage during the wiring process.
Another benefit of rubber insulation is its exceptional durability. It is highly resistant to wear and tear, making it suitable for harsh environments and applications that involve frequent movement or vibration, such as machinery or equipment. Rubber insulation can withstand the stresses of daily use, ensuring long-lasting protection for the wires.
In addition to its flexibility and durability, rubber insulation offers excellent resistance to heat and cold. It can handle a wide range of temperatures without melting or becoming brittle, making it suitable for both indoor and outdoor applications. This resistance to temperature extremes is particularly important in environments where the wiring may be exposed to high or low temperatures.
Furthermore, rubber insulation has good resistance to chemicals and oils, making it suitable for installations in areas where exposure to these substances is common. It can withstand the corrosive effects of certain chemicals and maintain its insulating properties, providing reliable protection for the wires.
One consideration with rubber insulation is its flammability. While it does offer a certain level of fire resistance, it may not perform as well as some specialized fire-resistant insulation materials. Therefore, in applications where fire safety is a significant concern, alternative options that provide enhanced fire protection may be more suitable.
It is important to note that rubber insulation is typically more expensive than other types of insulation materials. However, the added cost is justified by the superior flexibility, durability, and resistance it provides, making it a worthwhile investment in applications that require these properties.
In summary, rubber insulation is a flexible, durable, and temperature-resistant option for electrical wiring. Its ability to withstand wear and tear, along with its resistance to chemicals, makes it a preferred choice for various applications, from industrial machinery to portable tools. Consider the specific requirements of your project to determine whether rubber insulation is the appropriate choice for your wiring needs.
Nylon Insulation
Nylon insulation is a thermoplastic material commonly used in electrical wiring applications that require durability, high performance, and resistance to extreme conditions. It offers a unique set of properties that make it suitable for a variety of specialized applications.
One of the key advantages of nylon insulation is its high melting point. Nylon can withstand elevated temperatures without softening or deforming, making it an excellent choice for high-temperature applications. It is commonly used in motor winding wires, heating elements, and aerospace wiring, where temperatures can reach extreme levels.
In addition to its exceptional thermal resistance, nylon insulation is known for its toughness and durability. It is highly resistant to impact and abrasion, making it capable of withstanding harsh environments and mechanical stress. Nylon-insulated wires are often used in rugged applications where wires may be subject to vibrations, movement, or exposure to rough conditions.
Another advantage of nylon insulation is its excellent resistance to chemicals. It can withstand exposure to a wide range of substances, including oils, solvents, and certain acids. This chemical resistance ensures that the insulation maintains its integrity and reliability even in challenging industrial or automotive environments.
Furthermore, nylon insulation has good electrical insulating properties, providing reliable and efficient electrical transmission. It also offers good moisture resistance, reducing the risk of electrical shorts or corrosion caused by exposure to damp environments.
Although nylon insulation offers many benefits, it is worth noting that it is relatively stiff compared to other insulation materials. This stiffness may make it less suitable for applications that require a high degree of flexibility or where wires need to be bent or routed around tight corners.
Read more: What Is Yellow Insulation Made Of
Factors Considered in Choosing Wire Insulation
When selecting wire insulation, there are several important factors to consider:
Electrical Safety
Ensuring the chosen insulation material provides adequate electrical insulation and meets safety standards is vital. Consider the voltage rating, insulation thickness, and insulation resistance when choosing the appropriate wire insulation.
Temperature Rating
The temperature range the wire will be exposed to should be taken into account. Different insulation materials have varying temperature limits, and selecting insulation with a suitable temperature rating ensures the wire can withstand the anticipated operating conditions without degradation.
Flexibility and Durability
The flexibility and durability of the insulation material are crucial considerations. If the wire needs to bend or be subjected to movement, selecting an insulation material that can withstand repeated flexing without cracking or degrading is essential.
Read also: 15 Best Insulated Electrical Wire for 2024
Chemical Resistance
Consider the environment the wire will be installed in and determine if the insulation material can withstand exposure to the chemicals present in that environment. Chemical resistance is crucial to prevent degradation or damage to the insulation.
Environmental Impact
Consider the impact of the chosen insulation material on the environment. Some insulation materials may contain hazardous substances or be difficult to recycle, so opting for more environmentally friendly options can be a responsible choice.
By carefully considering these factors, you can select the most appropriate wire insulation that meets the specific requirements of your application, ensuring optimal performance, safety, and longevity.
Electrical Safety
Electrical safety is of utmost importance when it comes to choosing the right wire insulation. The insulation material plays a critical role in preventing electrical leakage, short circuits, and the risk of electrical shock or fires. Several factors need to be considered to ensure the electrical safety of the wiring system.
Voltage Rating
One crucial consideration is the voltage rating of the wire insulation. Different insulation materials have varying voltage limits that determine their ability to withstand electrical potential. It is essential to select insulation with a voltage rating that exceeds the intended application’s voltage to ensure proper electrical safety and performance.
Read more: What Is 4 Wire Electrical Wire
Insulation Thickness
The thickness of the insulation is also an important factor in electrical safety. Thicker insulation provides increased protection against electrical leakage and reduces the risk of short circuits. The insulation should be sufficient to prevent the conductor from coming into contact with nearby conductive materials or the environment.
Insulation Resistance
The insulation resistance is a measure of how well the insulation material prevents the flow of electric current. High insulation resistance is desirable as it minimizes the risk of electrical leakage. Insulation materials with higher resistance values are more effective in maintaining the integrity of the electrical circuit and reducing the possibility of electrical accidents.
Compliance with Safety Standards
It is crucial to ensure that the selected wire insulation meets the necessary safety standards and regulations. Different countries and regions have specific safety standards that must be complied with to ensure the proper functioning and safety of electrical installations. In the United States, for example, the National Electrical Code (NEC) sets the guidelines for electrical systems, including wire insulation requirements.
Overcurrent and Short Circuit Protection
While wire insulation is an essential part of electrical safety, it should not be relied upon alone. Adequate overcurrent and short-circuit protection devices, such as circuit breakers or fuses, should be installed to safeguard the wiring system. These devices provide an additional layer of protection by interrupting the flow of current when a fault or overload occurs.
Regular inspection and maintenance of the electrical system are also crucial for ensuring ongoing electrical safety. Any signs of damage or wear on the wire insulation should be promptly addressed to prevent potential hazards. Additionally, proper installation techniques and adherence to wiring codes and guidelines are vital for maintaining electrical safety.
By considering the voltage rating, insulation thickness, insulation resistance, compliance with safety standards, and incorporating appropriate protective devices, you can ensure the electrical safety of your wiring system. Prioritizing electrical safety reduces the risk of electrical accidents, protects property, and enhances the overall reliability and longevity of the electrical installation.
Read more: What Is An Electrical Wire
Temperature Rating
The temperature rating of wire insulation is a critical factor to consider when selecting the right wiring for your application. Different insulation materials have varying temperature limits, and choosing the appropriate temperature rating ensures that the wire insulation can withstand the expected operating conditions without degrading or losing its insulating properties.
Operating Temperature
The operating temperature refers to the range of temperatures in which the wire insulation will be exposed during its normal operation. It is important to consider both the high and low extremes of the temperature range. Exceeding the maximum temperature rating can cause the insulation to melt or become brittle, compromising its ability to effectively protect the wire. Conversely, subjecting the insulation to temperatures below its minimum rating may cause it to lose flexibility or become ineffective.
Environmental Factors
Environmental factors can significantly impact the temperature that the wire insulation will be exposed to. For example, outdoor installations may be subject to fluctuating temperatures, extreme heat from direct sunlight, or extreme cold in frost-prone regions. Industrial or automotive environments may have high-temperature machinery or exposure to chemicals that can affect the temperature rating requirements. All these factors must be considered to ensure the wire insulation can withstand the environmental conditions it will be exposed to.
Insulation Material
Each insulation material has its own specific temperature rating. Common insulation materials, such as PVC, thermoplastic, XLPE, rubber, and nylon, have different maximum temperature limits. It is crucial to select an insulation material with a temperature rating that is appropriate for the expected operating temperatures of the wiring system. Additionally, it is important to verify that the chosen insulation material can handle temperature variations and maintain its insulation properties over time.
Read more: How Is Fiberglass Insulation Made
Derating Factors
It is worth noting that the maximum temperature rating of an insulation material may need to be derated depending on factors such as the number of wires bundled together, the presence of nearby heat sources, or the confined nature of the installation. Derating factors provide a safety margin to ensure that the insulation material can effectively handle the heat generated under these conditions.
Ensuring that the wire insulation has the appropriate temperature rating is crucial for the safe and reliable operation of the electrical system. Choosing insulation materials that can withstand the expected temperature range, considering environmental factors, and accounting for derating factors will help prevent insulation degradation, electrical failures, and potential hazards.
Flexibility and Durability
When choosing wire insulation, two critical factors to consider are flexibility and durability. The insulation material must be able to withstand the demands of the application while providing the necessary protection for the conductors.
Flexibility
The flexibility of the wire insulation is essential, especially in applications where the wire needs to be bent or routed around corners. Flexible insulation allows for easier installation, as it can maneuver through tight spaces and conform to the shape required. It also reduces the risk of the insulation cracking or becoming damaged during the installation process. Flexible insulation is particularly important in applications where the wire may be subject to movement or vibration over time.
Flexible insulation materials include PVC, certain thermoplastic materials, and rubber. These materials have properties that allow them to maintain their flexibility and elasticity even when bent or twisted. It is important to choose an insulation material that can withstand repeated flexing without compromising its insulation properties.
Durability
The durability of wire insulation is crucial for the long-term performance and reliability of the electrical system. The insulation material must be able to withstand various environmental factors, such as temperature fluctuations, exposure to moisture, chemicals, UV radiation, and mechanical stress. Durability ensures that the insulation remains intact and continues to protect the wires from damage or degradation throughout the lifespan of the installation.
Durable insulation materials include rubber, thermoplastic materials, and cross-linked polyethylene (XLPE). These materials have a high resistance to wear and tear, impact, abrasion, and chemical corrosion. They are often used in demanding applications where the wires may be subject to harsh conditions or frequent movement.
It is important to consider the specific requirements of the application when choosing the appropriate level of flexibility and durability for wire insulation. For example, in industrial settings where there is heavy machinery or equipment, the insulation must be able to withstand the vibrations and movements associated with their operation. In outdoor or marine applications, the insulation should be able to resist exposure to moisture and UV radiation.
By selecting wire insulation that offers the right balance of flexibility and durability, you ensure that the electrical system remains protected and reliable over time. It reduces the risk of insulation damage, electrical leakage, and potential hazards. Carefully evaluate the environmental conditions and demands of the application to choose the most appropriate insulation material for optimal flexibility and durability.
Read more: What Is Red In Electrical Wire
Chemical Resistance
Chemical resistance is a crucial factor to consider when choosing wire insulation, especially in environments where the wires may come into contact with various substances. The insulation material should be able to withstand exposure to chemicals without deteriorating, ensuring the integrity and reliability of the wiring system.
Type of Chemicals
The specific chemicals that the wire insulation may encounter depend on the application and the environment. It is important to identify the types of chemicals that the insulation material may come into contact with in order to select an insulation material with suitable chemical resistance. Common chemicals include oils, solvents, fuels, acids, alkalis, and cleaning agents. Each insulation material has different levels of resistance to various chemicals, so choosing the appropriate material is essential.
Resistance Properties
The chemical resistance properties of an insulation material can vary depending on its composition and manufacturing process. Some insulation materials, such as PVC (polyvinyl chloride) and certain thermoplastic materials, offer good resistance to a wide range of chemicals. These materials can withstand exposure to oils, solvents, and many acids and alkalis. Other insulation materials, such as rubber and certain fluoropolymers, provide even higher resistance to specific chemicals while maintaining their insulating properties.
Environmental Considerations
The environment in which the wire insulation is installed also plays a role in chemical resistance. Factors such as temperature, humidity, and exposure duration can affect the performance of the insulation material. It is important to consider the specific conditions of the environment and select an insulation material that can withstand the expected chemical exposure and environmental factors.
Read more: What Is SOOW Electrical Wire
Application-Specific Requirements
Depending on the industry or application, there may be specific standards or regulations for chemical resistance. Electrical systems in industries such as chemical manufacturing, oil and gas, or automotive sectors may require wire insulation that meets specific chemical resistance standards. It is crucial to understand the requirements of the application and choose the insulation material accordingly.
By selecting wire insulation with proper chemical resistance, you can ensure the longevity and reliability of the electrical system. It minimizes the risk of corrosion, degradation, or breakdown of the insulation when exposed to chemicals, protecting the wires and maintaining the integrity of the electrical circuit. Consider the specific chemical exposure and environmental factors when choosing the insulation material to ensure optimal chemical resistance for your application.
Environmental Impact
Considering the environmental impact of wire insulation is becoming increasingly important as sustainability and eco-consciousness gain prominence. Choosing insulation materials that have minimal negative impact on the environment can help reduce pollution, conserve resources, and promote a greener future.
Sustainable Materials
Opting for insulation materials that are made from sustainable or recyclable sources can significantly reduce the environmental footprint. Some manufacturers offer insulation materials that are produced from renewable resources or utilize recycled materials. These sustainable options help minimize the use of non-renewable resources and reduce waste.
Recyclability
Choosing insulation materials that are recyclable when their useful life is over can greatly reduce landfill waste. Insulation materials that can be easily recycled and converted into new products help maximize the use of resources and minimize environmental impact. Look for insulation materials that can be recycled through local recycling programs or specialized recycling facilities.
Read more: What Is A White Electrical Wire
Low Toxicity
Consider the toxicity of the insulation material and its impact on human health and the environment. Some insulation materials may contain harmful chemicals or compounds that can leach into the environment over time. Opting for insulation materials with low toxicity, such as those that are free from hazardous substances or have low volatile organic compound (VOC) emissions, can help create a safer and healthier living or working environment.
Energy Efficiency
Energy efficiency should also be considered when selecting wire insulation. Some insulating materials have higher thermal conductivity, meaning they provide better insulation and reduce energy consumption. Choosing insulation materials that have higher energy efficiency ratings can contribute to reducing energy usage and promoting sustainability.
Insulation Lifespan
Considering the lifespan of the insulation material is important for reducing the environmental impact. Insulation materials that have longer lifespans require fewer replacements, reducing waste and resource consumption. Additionally, selecting durable insulation materials that can withstand wear and tear helps to maintain the integrity of the electrical system for longer periods, reducing the need for frequent repairs or replacements.
Conclusion
When choosing wire insulation, it is essential to consider the environmental impact of the insulation material. Opting for sustainable materials, recyclability, low toxicity, and energy efficiency can help minimize the environmental footprint and promote a greener future. Additionally, considering the lifespan and durability of the insulation material contributes to reducing waste and resource consumption. By making informed choices that prioritize both functionality and environmental responsibility, we can create a more sustainable and eco-friendly electrical system.
Frequently Asked Questions about What Is Electrical Wire Insulation Made Of
Was this page helpful?
At Storables.com, we guarantee accurate and reliable information. Our content, validated by Expert Board Contributors, is crafted following stringent Editorial Policies. We're committed to providing you with well-researched, expert-backed insights for all your informational needs.
0 thoughts on “What Is Electrical Wire Insulation Made Of”