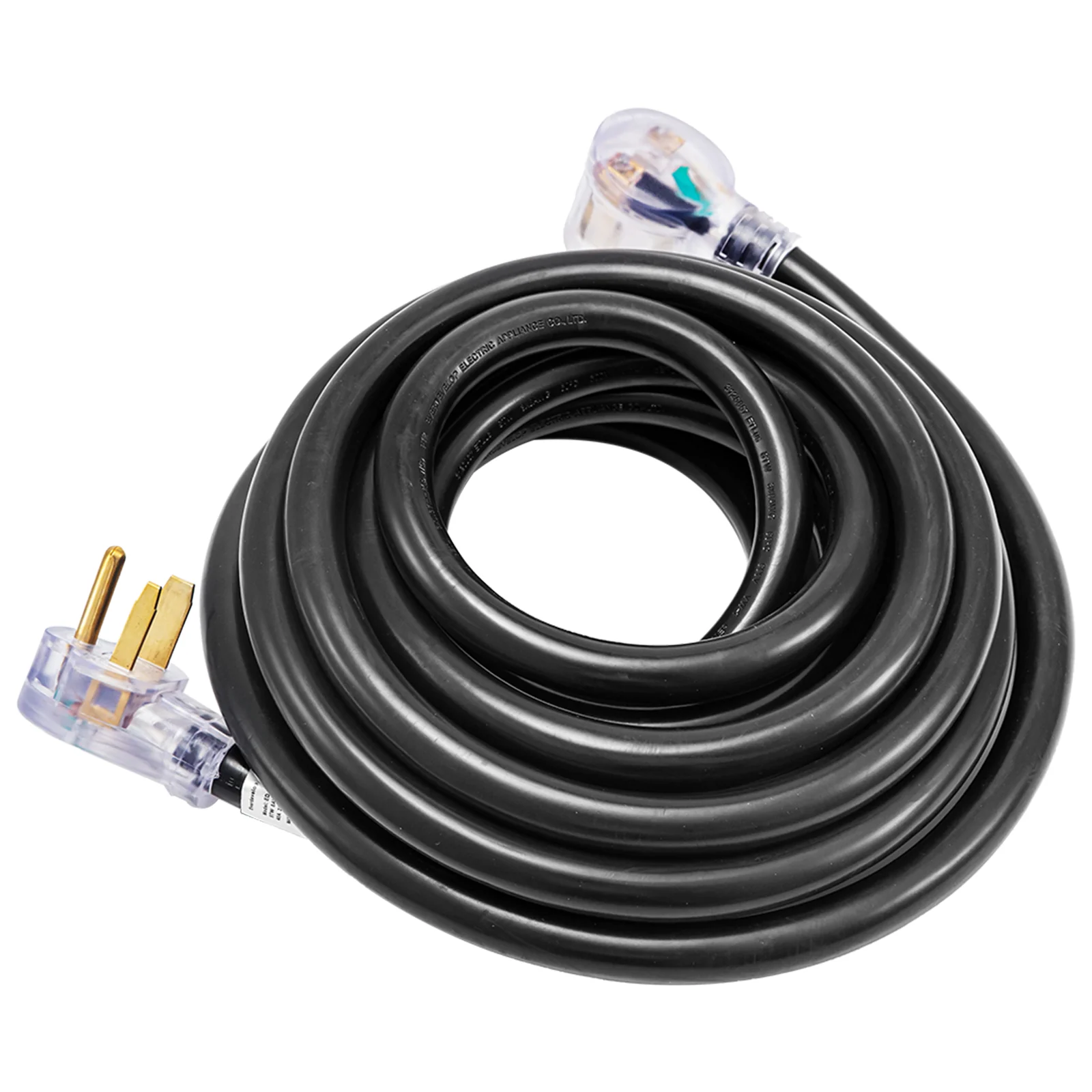
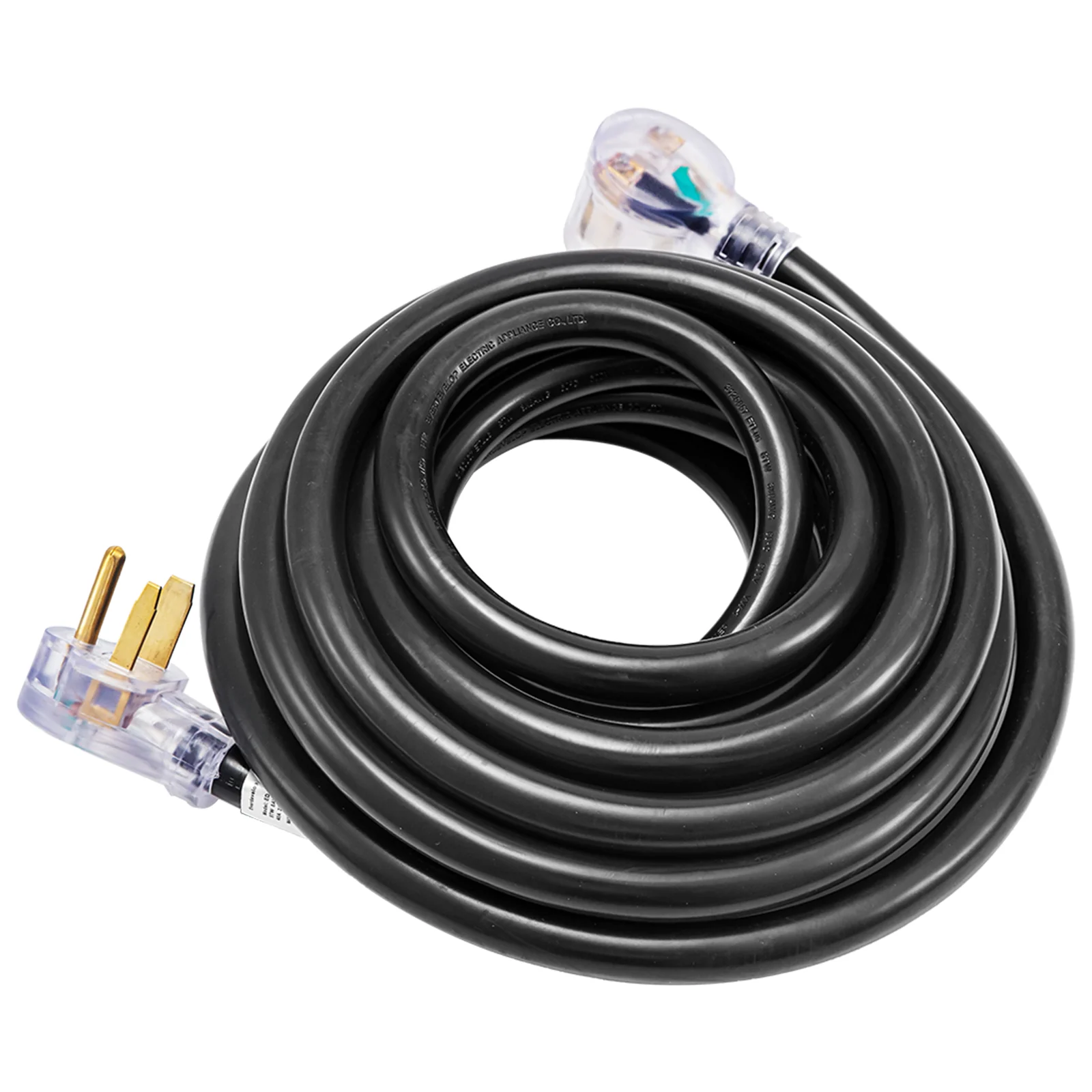
Articles
What Size Wire For Welder Extension Cord
Modified: September 2, 2024
Looking for information on what size wire to use for a welder extension cord? Read our articles for helpful tips and recommendations.
(Many of the links in this article redirect to a specific reviewed product. Your purchase of these products through affiliate links helps to generate commission for Storables.com, at no extra cost. Learn more)
Introduction
When it comes to using a welder, having a reliable and properly-sized extension cord is crucial. A high-quality extension cord ensures that your welder receives the appropriate power supply and allows for safe welding operations. One of the key factors to consider when selecting an extension cord is the size of the wire used.
Using the correct wire size for your welder extension cord is essential for maintaining efficient power delivery and preventing voltage drop. This article will guide you on how to determine the appropriate wire size for your welder extension cord, taking into account various factors such as ampacity ratings, voltage drop calculations, length of the extension cord, type of welder, type of welding application, and the material of the welding cable.
By understanding these factors and selecting the right wire size for your welder extension cord, you can optimize the welding performance and ensure the safety of both the equipment and the operator. Let’s delve deeper into each of these considerations.
Key Takeaways:
- Selecting the right wire size for your welder extension cord is crucial for efficient power delivery and safe welding operations. Consider factors such as ampacity ratings, voltage drop, and the type of welding application to optimize performance.
- Understanding the material of the welding cable, length of the extension cord, and the specific requirements of your welder will help you choose the appropriate wire gauge. By considering these factors, you can prevent voltage drop and ensure reliable power supply for your welding projects.
Factors to Consider
Several factors should be taken into account when determining the appropriate wire size for your welder extension cord. These factors include:
- Ampacity ratings
- Voltage drop
- Length of the extension cord
- Type of welder
- Type of welding application
- Material of the welding cable
Let’s explore each of these factors in more detail:
Ampacity ratings: The ampacity rating of a wire refers to the maximum current that the wire can safely carry. It is crucial to choose a wire size that can handle the ampacity requirements of your specific welder. The higher the ampacity rating, the thicker the wire gauge should be.
Voltage drop: Over long distances, current flowing through a wire can experience a drop in voltage. This can result in a loss of power and reduced welding performance. To minimize voltage drop, it is important to select a wire size that minimizes resistance and ensures efficient power delivery.
Length of the extension cord: The length of the extension cord plays a significant role in determining the appropriate wire size. As the length increases, so does the potential for voltage drop. Longer extension cords require thicker wire gauges to compensate for the increase in resistance.
Type of welder: Different welders have varying power requirements. Some welders may require higher amperage and therefore demand thicker wire sizes. It is crucial to check the specifications provided by the manufacturer to accurately determine the wire size needed for your specific welder.
Type of welding application: The type of welding application also influences the wire size selection. For light-duty welding applications, such as DIY or hobby welding, a thinner wire gauge may be sufficient. However, heavy-duty welding applications, such as industrial or professional welding, typically require thicker wire gauges to handle the higher amperage demands.
Material of the welding cable: The material of the welding cable can affect its conductivity and flexibility. Copper is the preferred material due to its excellent conductivity, but it can be more expensive. Aluminum is a more affordable option but has lower conductivity. It is important to consider the material of the welding cable and choose a wire size that suits your requirements and budget.
Considering these factors will help you determine the appropriate wire size for your welder extension cord. In the following sections, we will discuss the specific wire sizes that are commonly recommended for various ampacity requirements and welding applications.
Wire Gauge and Ampacity Ratings
Wire gauge refers to the thickness of the wire and is typically measured using the American Wire Gauge (AWG) system. The AWG system assigns a numerical value to each wire gauge, with smaller numbers indicating thicker wires. For example, a wire with a gauge of 10 is thicker than a wire with a gauge of 12.
The ampacity rating of a wire determines the maximum current it can safely carry without overheating. The National Electrical Code (NEC) provides guidelines for ampacity ratings based on wire gauge.
Here are some common wire gauges and their corresponding ampacity ratings:
- 14 AWG: This is a common wire gauge used for light-duty applications. It has an ampacity rating of approximately 15-20 amps.
- 12 AWG: This wire gauge is suitable for medium-duty applications. It has an ampacity rating of approximately 20-25 amps.
- 10 AWG: This wire gauge is commonly used for heavy-duty applications. It has an ampacity rating of approximately 30-40 amps.
- 8 AWG: This wire gauge is ideal for high-amperage welders and industrial applications. It has an ampacity rating of approximately 50-70 amps.
It is important to note that these ampacity ratings are general guidelines, and you should always refer to the manufacturer’s specifications for your specific welder to determine the recommended wire gauge and ampacity requirements.
Next, we will discuss how to calculate voltage drop and why it is important to consider when selecting the wire size for your welder extension cord.
Calculating Voltage Drop
When using a welder, it is crucial to minimize voltage drop, as it can result in a loss of power and inefficient welding performance. Voltage drop occurs when the current flowing through a wire encounters resistance, causing a decrease in voltage.
To determine if voltage drop is a concern for your welder extension cord and to calculate the expected voltage drop, you can use the following formula:
Voltage drop (V) = (Length of the extension cord (ft) x Current (A) x Ohms per unit length) / 1000
The Ohms per unit length value is determined by the resistance per 1000 ft for the wire gauge. This value can be obtained from reference tables that provide the resistance values for different wire gauges.
For example, let’s say you have a 50-foot extension cord and your welder requires a current of 30 amps. You are using a 10 AWG wire, which has an Ohms per unit length value of 0.998 ohms per 1000 ft. Plugging these values into the formula, you would calculate the voltage drop as follows:
Voltage drop = (50 ft x 30 A x 0.998 ohms per 1000 ft) / 1000 = 1.499 volts
In this example, the calculated voltage drop is 1.499 volts. It is generally recommended to keep the voltage drop below 3% for efficient welding operations. If the calculated voltage drop exceeds the recommended threshold, you may need to consider using a larger wire gauge to minimize resistance and voltage drop.
Calculating the expected voltage drop can help you determine the appropriate wire size to maintain efficient power delivery for your welder. However, it is important to remember that this is just an estimate, and actual voltage drop may vary depending on factors such as temperature and the quality of the wiring components.
Next, we will consider the length of the welder extension cord and its impact on the selection of the wire size.
Length of Welder Extension Cord
The length of the welder extension cord is an important factor to consider when selecting the appropriate wire size. As the length of the extension cord increases, so does the resistance, which can result in voltage drop and reduced welding performance.
When using a longer extension cord, it is necessary to compensate for the increased resistance by using a thicker wire gauge. Thicker wires have lower resistance, allowing for more efficient power delivery and minimizing voltage drop.
It is recommended to choose a wire size that can handle the expected voltage drop within an acceptable range. As a general guideline, try to keep voltage drop below 3% to maintain efficient welding operations.
For example, if you have a 100-foot extension cord and your welder requires a current of 40 amps, using a 12 AWG wire may result in excessive voltage drop. In this case, you might consider using a 10 AWG wire to compensate for the longer distance and minimize resistance.
It is important to note that excessively long extension cords can lead to significant voltage drop, even with a larger wire gauge. If possible, it is best to keep the length of the extension cord as short as possible to reduce the likelihood of voltage drop and maintain optimal welding performance.
Next, we will discuss the type of welder and its influence on the selection of the wire size for the extension cord.
When determining the size of wire for a welder extension cord, consider the welder’s voltage and amperage requirements. Use a wire gauge that can handle the maximum amperage of the welder to ensure safe and efficient operation.
Read more: How To Wire An Extension Cord Plug
Type of Welder
The type of welder you are using is a crucial consideration when selecting the appropriate wire size for your extension cord. Different types of welders have varying power requirements, and it is essential to match the wire size to meet those requirements.
There are two primary types of welders: MIG (Metal Inert Gas) welders and Stick welders.
MIG welders are commonly used for a variety of applications and require a constant power supply. They typically have higher amperage requirements than Stick welders. Therefore, MIG welders require thicker wire gauges to handle the higher current flow.
Stick welders, on the other hand, have lower amperage requirements compared to MIG welders. As a result, they can generally operate with smaller wire gauges.
It is crucial to consult the manufacturer’s specifications for your specific welder to determine the recommended wire size and ampacity requirements. This information will help you select the appropriate wire gauge for your welder extension cord.
Additionally, it is important to consider the duty cycle of your welder. The duty cycle refers to the percentage of time a welder can operate within a given time period without overheating. Higher-duty cycle welders typically require a larger wire size to handle the increased power demand.
Understanding the type of welder you are using, its power requirements, and duty cycle will ensure that you select the appropriate wire size and optimize the performance of your welder extension cord.
Next, let’s delve into the type of welding application and its influence on the selection of the wire size.
Type of Welding Application
The type of welding application you are engaged in is an important factor to consider when determining the appropriate wire size for your extension cord. Different welding applications have varying power demands, and selecting the correct wire gauge ensures optimal performance and safety.
For light-duty or DIY welding applications, such as small repairs or hobby projects, a thinner wire gauge may be sufficient. Light-duty welders typically have lower amperage requirements, and using a smaller wire size can help save on costs without compromising performance.
However, for heavy-duty or industrial welding applications, such as structural welding or fabrication, a thicker wire gauge is generally required. Heavy-duty welders have higher amperage demands, and using a larger wire gauge ensures that the extension cord can reliably handle the increased power load.
When determining the appropriate wire size for your welding application, it is crucial to consult the manufacturer’s specifications for your welder. The manufacturer will provide specific recommendations based on the intended use of the welder.
It is also essential to consider any future growth or expansion in your welding needs. If you anticipate working on larger or more demanding projects in the future, it may be wise to select a slightly larger wire size to accommodate potential increases in power requirements.
By understanding the type of welding application you will be undertaking, you can select the appropriate wire gauge to ensure efficient power delivery and safe welding operations.
Next, we will discuss the importance of considering the material of the welding cable when selecting the wire size for your extension cord.
Material of Welding Cable
The material of the welding cable is an important consideration when selecting the appropriate wire size for your extension cord. The material affects the cable’s conductivity, flexibility, and overall performance.
Copper and aluminum are the most commonly used materials for welding cables. Copper is known for its excellent conductivity, which allows for efficient power delivery with minimal resistance. It is the preferred choice for most welding applications due to its superior electrical properties.
However, copper welding cables can be more expensive compared to their aluminum counterparts. If budget is a concern, aluminum cables can be a more affordable option. However, it is important to note that aluminum has lower conductivity compared to copper, which may result in slightly higher resistance and a small increase in voltage drop.
When it comes to selecting the appropriate wire size, the material of the welding cable should be taken into account. Copper cables generally have lower resistance compared to aluminum cables of the same gauge, allowing for better power transmission and minimizing voltage drop.
If you decide to use an aluminum welding cable, you may need to select a slightly larger wire gauge to compensate for the higher resistance and potential increase in voltage drop.
It is important to consult the manufacturer’s recommendations for your specific welder and consider the material of the welding cable when selecting the appropriate wire size for your extension cord. This ensures that you choose a wire size that is compatible with the cable’s material and optimizes the performance of your welding equipment.
Considering the material of the welding cable, along with the other factors we discussed earlier, will help you make an informed decision when selecting the wire size for your welder extension cord.
Next, we will provide specific recommendations for appropriate wire sizes based on different ampacity requirements and welding applications.
Appropriate Wire Sizes for Welder Extension Cords
The appropriate wire size for your welder extension cord depends on various factors, including the ampacity requirements, length of the extension cord, type of welder, type of welding application, and material of the welding cable. Here are some general recommendations:
- For light-duty welding applications with lower amperage requirements, such as DIY or hobby welding, a 14 AWG wire may be sufficient for shorter extension cords (up to 25 feet). For longer extension cords, consider using a 12 AWG wire.
- For medium-duty welding applications, such as general repairs or light fabrication, a 12 AWG wire is typically recommended. This wire size can handle higher amperage requirements and is suitable for extension cords up to 50 feet. For longer extension cords, consider using a 10 AWG wire.
- For heavy-duty welding applications, such as industrial or professional welding, a 10 AWG wire is often necessary to handle the higher amperage demands. This wire size is suitable for extension cords up to 100 feet. For longer extension cords or high-amperage welders, consider using an 8 AWG or larger wire.
These are general guidelines, and it is important to check the manufacturer’s specifications for your specific welder to determine the recommended ampacity requirements and wire gauge. Additionally, factor in the length of the extension cord and the material of the welding cable to ensure efficient power delivery and minimize voltage drop.
Remember to consider any future growth or expansion in your welding needs. If you anticipate working on larger projects or using higher-amperage welders in the future, it may be wise to select a slightly larger wire size to accommodate potential increases in power requirements.
By choosing the appropriate wire size for your welder extension cord, you can ensure reliable power supply, prevent voltage drop, and optimize the performance of your welding equipment.
Next, we will conclude our discussion on selecting the right wire size for your welder extension cord.
Read more: What Type Of Electrical Cord Has Copper Wire
Conclusion
Selecting the appropriate wire size for your welder extension cord is essential for maintaining optimal power delivery, preventing voltage drop, and ensuring safe and efficient welding operations. Throughout this article, we have discussed the various factors to consider when determining the right wire size, including ampacity ratings, voltage drop calculations, length of the extension cord, type of welder, type of welding application, and material of the welding cable.
By considering these factors, you can make an informed decision and select the wire gauge that best suits your specific needs. It is important to consult the manufacturer’s specifications for your welder to determine the recommended ampacity requirements and wire gauge, as well as to ensure compliance with safety standards.
Remember that different welding applications and power demands may require different wire sizes. Light-duty projects may only require a 14 or 12 AWG wire, while heavy-duty or industrial welding applications typically necessitate thicker wire gauges such as 10 AWG or even 8 AWG.
Additionally, it is vital to consider the length of the extension cord and the material of the welding cable. Longer extension cords will have higher resistance, increasing the need for a thicker wire gauge to minimize voltage drop. Copper cables offer superior conductivity compared to aluminum cables, but they may come at a higher cost.
By carefully assessing these factors and selecting the appropriate wire size, you can optimize the performance of your welder, minimize voltage drop, and ensure a safe and efficient welding experience.
Remember, it is always advisable to consult with a professional electrician or refer to the manufacturer’s guidelines if you have any concerns or uncertainties regarding your specific welding equipment and extension cord requirements.
With the right wire size, your welder extension cord will provide a reliable power supply, enabling you to tackle your welding projects with confidence and precision.
Frequently Asked Questions about What Size Wire For Welder Extension Cord
Was this page helpful?
At Storables.com, we guarantee accurate and reliable information. Our content, validated by Expert Board Contributors, is crafted following stringent Editorial Policies. We're committed to providing you with well-researched, expert-backed insights for all your informational needs.
0 thoughts on “What Size Wire For Welder Extension Cord”