Home>diy>Building & Construction>How Is Concrete Used In Construction
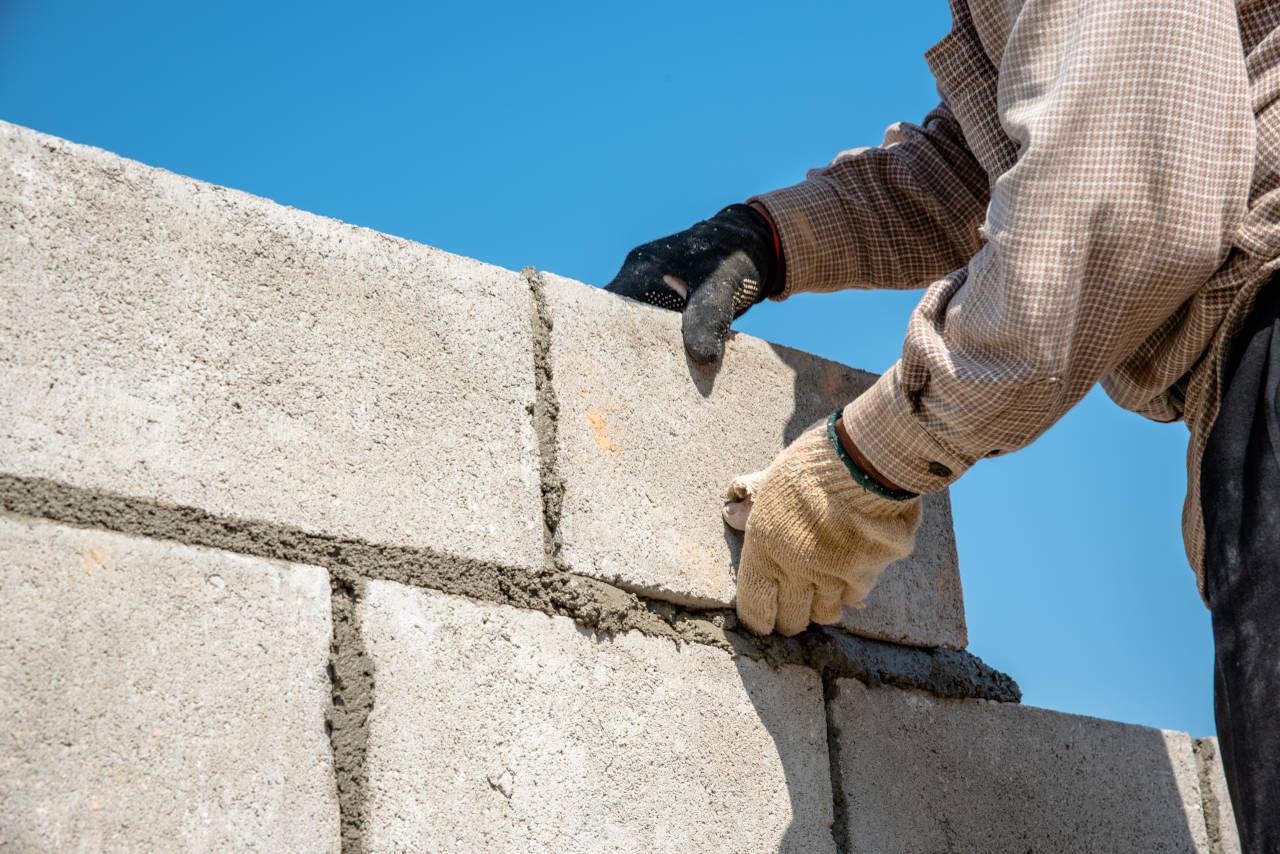
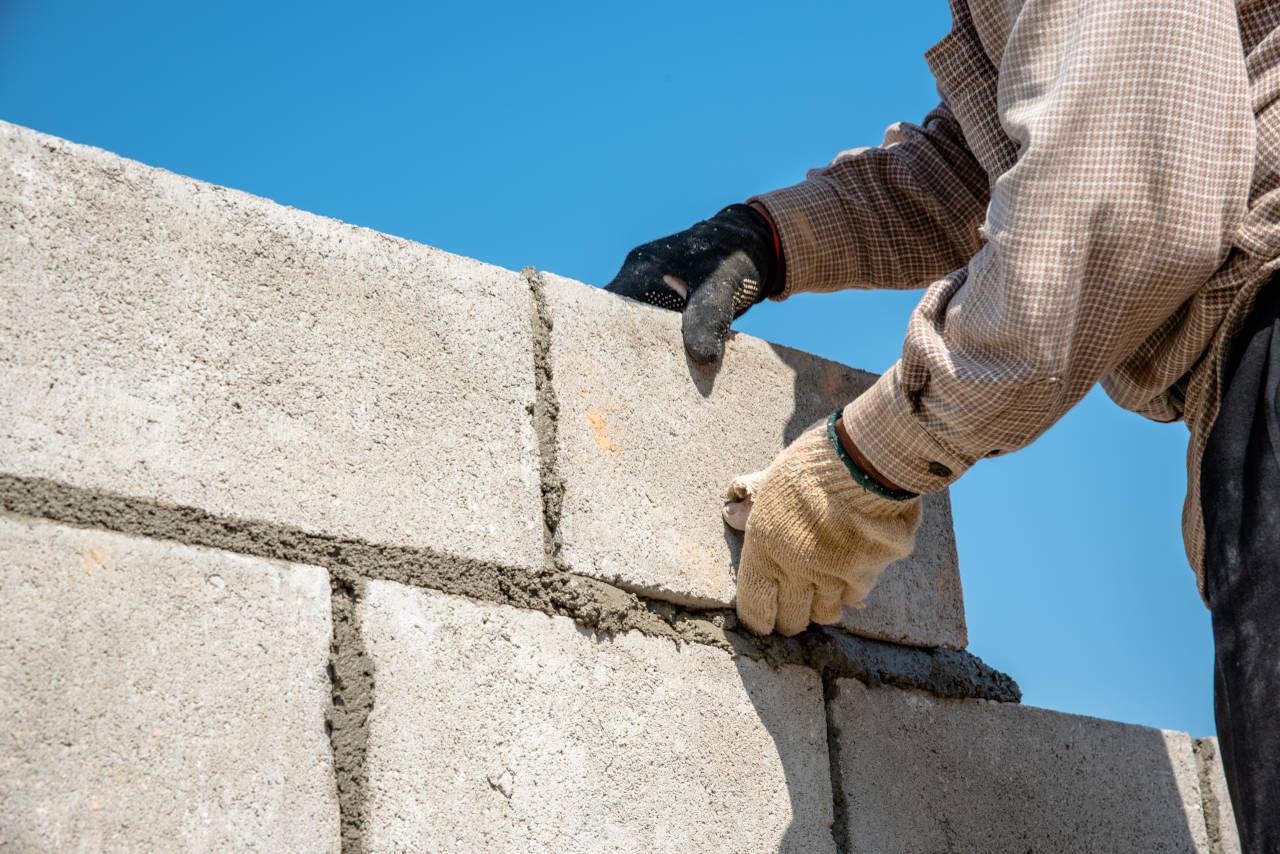
Building & Construction
How Is Concrete Used In Construction
Modified: January 21, 2024
Discover how concrete is used in building construction, including its versatility, durability, and sustainability. Explore the benefits of using concrete as a fundamental material for various construction projects.
(Many of the links in this article redirect to a specific reviewed product. Your purchase of these products through affiliate links helps to generate commission for Storables.com, at no extra cost. Learn more)
Introduction
When it comes to building construction, one material that is used extensively is concrete. Concrete has been a fundamental component of construction projects for centuries, offering strength, durability, and versatility. From towering skyscrapers to sturdy bridges and residential homes, concrete plays a vital role in shaping the built environment.
Concrete is a composite material composed of aggregates such as crushed stone, sand, or gravel, bound together by a cementitious binder, typically Portland cement. Additional additives may be incorporated to enhance certain properties of the concrete, such as workability, strength, or durability.
The use of concrete in construction offers numerous advantages. Its incredible compressive strength, fire resistance, and ability to withstand natural forces make it a desirable choice for building structures that need to stand the test of time. Additionally, concrete can be molded into various shapes and sizes, enabling architects and engineers to unleash their creativity and design innovative structures.
However, working with concrete requires careful planning and expertise. The mixing, placement, and curing processes must be executed with precision to ensure the concrete reaches its desired strength and durability. In this article, we will explore the properties of concrete, its various types, and how it is utilized in construction projects.
Key Takeaways:
- Concrete is a versatile, durable, and fire-resistant material used in various construction projects, offering strength, sound insulation, and environmental benefits. Proper mixing, placement, and finishing techniques are crucial for optimal performance.
- While concrete provides unparalleled strength, versatility, and cost-effectiveness, it also has drawbacks such as high embodied energy, long curing time, and potential for cracking. Adhering to industry best practices and sustainable production methods is essential for maximizing its benefits.
Read more: What Is A Construction Joint In Concrete
Properties of Concrete
Concrete possesses a range of properties that make it an ideal material for construction projects. Understanding these properties is essential for engineers and construction professionals to ensure the successful implementation of concrete structures. Here are some key properties of concrete:
- Compressive Strength: Concrete is known for its exceptional compressive strength, meaning it can resist heavy loads without breaking or deforming. The compressive strength of concrete is determined by the ratio of cement to the aggregates used, as well as the curing process.
- Durability: Concrete has excellent durability, making it resistant to weathering, chemical attacks, and environmental factors. This makes it suitable for structures exposed to harsh conditions, such as bridges, dams, and coastal buildings.
- Workability: Workability refers to the ease with which concrete can be mixed, placed, and compacted. It is crucial for construction efficiency and achieving the desired finish. The workability of concrete can be controlled by adjusting the water content and using admixtures.
- Fire Resistance: Concrete is inherently fire-resistant due to its low thermal conductivity. This property makes it a preferred choice for buildings where fire safety is a priority, such as commercial complexes and high-rise structures.
- Thermal Properties: Concrete has the ability to absorb and retain heat, providing insulation against temperature variations. This thermal mass property helps regulate indoor temperatures and reduce energy consumption in buildings.
- Sound Insulation: Concrete offers effective sound insulation, reducing the transmission of noise between different areas of a building. This is especially beneficial for residential and commercial spaces that require a quiet environment.
- Density: The density of concrete depends on the type and proportions of its constituent materials. High-density concrete is used in applications where additional weight and strength are required, such as in nuclear power plant structures.
Understanding these properties allows engineers and architects to optimize the design and construction process, ensuring that concrete structures meet the specific requirements and performance expectations.
Reinforced Concrete
Reinforced concrete is a widely used construction material that combines the compressive strength of concrete with the tensile strength of steel reinforcement. The combination of these two materials creates a reinforced structure capable of withstanding heavy loads and resisting cracking or failure.
The steel reinforcement, typically in the form of bars or mesh, is embedded within the concrete to provide additional strength and flexibility. This reinforcement helps to distribute the applied loads more evenly throughout the structure, reducing the risk of localized failure.
Reinforced concrete offers numerous benefits in construction, including:
- Increased Structural Strength: The inclusion of steel reinforcement enhances the structural strength of concrete, enabling it to support larger loads and span greater distances. This makes it a suitable choice for a wide range of construction projects.
- Flexibility in Design: Reinforced concrete can be molded into various shapes and sizes, allowing architects and engineers to design complex and innovative structures. The versatility of reinforced concrete allows for the construction of aesthetically pleasing and structurally efficient buildings.
- Enhanced Durability: By incorporating steel reinforcement, reinforced concrete structures have improved resistance against cracking, shrinkage, and other deleterious effects. This extends the lifespan of the structure and reduces maintenance requirements.
- Resistance to Corrosion: The steel reinforcement in reinforced concrete is often coated with a protective layer to prevent corrosion caused by exposure to moisture or chemicals. This significantly increases the durability of the structure, particularly in environments prone to corrosion.
Reinforced concrete is commonly used in a variety of construction projects, including buildings, bridges, dams, and tunnels. Its combination of strength, durability, and versatility makes it a preferred choice for both large-scale infrastructure projects and small-scale residential constructions.
However, it is essential to design and construct reinforced concrete structures with careful attention to detail and adherence to engineering principles. Proper placement and anchoring of the reinforcement, as well as appropriate concrete mix proportions, are crucial to ensure the desired structural performance and longevity of the reinforced concrete elements.
Types of Concrete
Concrete comes in various types, each with its own specific properties and applications. The choice of concrete type depends on factors such as the intended use, environmental conditions, and desired performance. Here are some common types of concrete:
- Ordinary Portland Cement (OPC) Concrete: OPC concrete is the most widely used type of concrete. It is made by mixing Portland cement, aggregates, water, and sometimes admixtures. OPC concrete offers good strength and durability and is commonly used in general construction projects.
- High-Strength Concrete: High-strength concrete is designed to have exceptional compressive strength, typically exceeding 6,000 psi (pounds per square inch). This type of concrete is achieved by using a lower water-to-cement ratio or incorporating supplementary cementitious materials like fly ash or silica fume. High-strength concrete is used in specialized applications where superior strength is required, such as in tall buildings or heavy-duty structures.
- Self-Consolidating Concrete (SCC): SCC is a highly flowable and easily workable type of concrete that does not require mechanical vibration for compaction. It flows easily into complex and congested reinforcement without segregation. SCC is popular in architectural concrete applications and can improve construction efficiency by reducing labor and equipment requirements.
- Ready-Mix Concrete: Ready-mix concrete is manufactured in a batching plant and delivered to the construction site in a transit mixer truck. This type of concrete allows for precise control of proportions and consistency, making it convenient for large-scale projects with consistent quality requirements.
- Pervious Concrete: Pervious concrete, also known as porous concrete, is designed with a high porosity that allows water to pass through it. This type of concrete is used in areas where water infiltration and drainage are essential, such as parking lots, sidewalks, and low-traffic roadways.
- Shotcrete: Shotcrete is concrete that is pneumatically projected onto a surface at high velocity. It is commonly used in areas where conventional concrete placement is difficult or time-consuming, such as vertical or overhead applications. Shotcrete is often used for tunnel lining, swimming pool construction, and repair work.
- Prestressed Concrete: Prestressed concrete is a type of concrete that incorporates tensioned steel strands (rebars) to counteract the tensile forces. These tensioned strands are placed before the concrete is cast, allowing for greater control over structural behavior and reducing the risk of cracking. Prestressed concrete is used in applications where high structural efficiency and resistance to applied loads are required, such as bridges, beams, and slabs.
It is important to select the appropriate type of concrete for a specific project, considering factors such as load-bearing capacity, durability, and environmental conditions. Consulting with concrete experts and engineers can help determine the most suitable type of concrete for optimal performance and longevity.
Concrete Mixing and Placement
The process of concrete mixing and placement is a critical phase in construction that requires careful planning and execution. Proper mixing and placement techniques ensure that the concrete reaches its desired strength, durability, and appearance. Here are the key steps involved in concrete mixing and placement:
- Proportioning of Ingredients: The first step in concrete mixing is determining the proportions of cement, aggregates, water, and any additives or admixtures. These proportions are based on the desired strength, workability, and other performance requirements of the concrete mix.
- Mixing: The mixing process involves thoroughly combining the dry ingredients (cement and aggregates) before adding water. Mixing can be done manually using shovels or with the help of mechanical mixers. The goal is to achieve a homogeneous mixture that ensures uniform distribution of the cement paste throughout the aggregates.
- Workability Adjustment: Depending on the specific application and construction techniques, the workability of the concrete may need to be adjusted. This can be done by adding water to increase workability, or by using admixtures to control flowability or retard setting time.
- Transportation: Once the concrete mix is ready, it needs to be transported to the construction site. For large projects, transit mixer trucks are commonly used. Care must be taken during transportation to prevent segregation or loss of workability.
- Placement: Concrete placement involves transferring the mixed concrete to its final position. This can be done using various methods, including pouring, pumping, or placing the concrete with specialized equipment like cranes or buckets. It is important to ensure proper consolidation of the concrete during placement to eliminate voids and achieve full compaction.
- Finishing: The finishing process involves treating the concrete surface to achieve the desired appearance and texture. Techniques such as screeding, floating, and troweling are used to create a smooth, level surface. Other finishing techniques, like imprinting or coloring, can be applied to enhance the aesthetic appeal of decorative concrete surfaces.
- Curing: Once the concrete is placed and finished, it needs to be cured properly to ensure optimal strength development and durability. Curing involves maintaining moisture and temperature conditions favorable for the hydration process. Curing can be done by covering the concrete with plastic sheets, spraying curing compounds, or using specialized curing membranes.
Efficient and precise concrete mixing and placement are crucial for achieving desired strength, durability, and appearance in construction projects. Following industry standards and best practices, and working with experienced concrete professionals, ensures successful execution of these critical processes.
When using concrete in construction, make sure to properly cure the concrete by keeping it moist for at least 7 days. This will help to increase its strength and durability.
Read more: How To Use A Laser Level For Concrete
Curing and Finishing of Concrete
The process of curing and finishing is essential for ensuring the long-term strength, durability, and appearance of concrete. Curing is the maintenance of proper moisture and temperature conditions, allowing the concrete to achieve its maximum strength potential. Finishing techniques are then applied to enhance the surface appearance and texture. Here’s a closer look at the curing and finishing process:
Curing:
Proper curing of concrete is crucial to achieve the desired strength and durability. It involves maintaining moisture within the concrete and controlling temperature conditions during the early stages of hydration. Here are some common methods of curing:
- Water Curing: Water curing involves keeping the concrete surface constantly wet by spraying or ponding it with water. This method is effective in preventing moisture loss and maintaining a moist environment for proper hydration.
- Membrane Curing: Membrane curing involves applying a curing compound or membrane to the concrete surface. These compounds form a thin film that prevents moisture evaporation and maintains a moist environment for proper hydration.
- Steam Curing: In certain situations, such as precast concrete or accelerated curing, steam curing may be employed. Steam is applied to accelerate the hydration process, shortening the curing time while maintaining the necessary moisture and temperature conditions for proper strength development.
- Insulation Curing: Insulation curing is often used in cold weather conditions. Thermal insulation materials, such as blankets or hay, are placed over the concrete to trap heat generated during the hydration process, helping to maintain the required temperature for curing.
Finishing:
After the curing process, concrete surfaces can be finished to achieve the desired appearance, texture, and functionality. Finishing techniques are typically applied to floors, pavements, and decorative concrete surfaces. Here are some common finishing techniques:
- Screeding: Screeding is the process of leveling and smoothing the surface of freshly placed concrete. A straightedge or a screed board is used to remove excess concrete and achieve a level surface.
- Float Finishing: Float finishing is performed after screeding and involves the use of a bull float or vibrating float to compact the concrete and create a smooth surface. Float finishing eliminates surface imperfections and helps to consolidate and densify the concrete.
- Troweling: Troweling is the final step of finishing, where a steel trowel is used to achieve a smooth and glossy surface. Troweling further compacts the concrete and improves its appearance. Multiple troweling passes may be required to achieve the desired finish.
- Decorative Finishes: For decorative concrete surfaces, various techniques can be applied to create unique textures, colors, and patterns. These include stamping, staining, acid etching, and polishing.
Proper curing and finishing techniques ensure that the concrete develops its full strength potential, achieves the desired appearance, and enhances its durability. It is important for construction professionals to follow industry best practices for curing and finishing to ensure the longevity and performance of concrete structures.
Concrete Strength and Durability
Concrete is known for its exceptional strength and durability, making it a popular choice for various construction applications. Understanding concrete’s strength and durability properties is essential in ensuring the longevity and performance of structures. Here’s a closer look at concrete strength and durability:
Concrete Strength:
The strength of concrete refers to its ability to withstand applied loads without failure. Compressive strength is commonly used to evaluate the strength of concrete and is determined by conducting compression tests on concrete specimens. Various factors influence concrete strength:
- Mix Proportions: The proportions of cement, aggregates, water, and any additives or admixtures significantly affect the strength of concrete. Proper control and optimization of these proportions are crucial in achieving the desired strength.
- Curing: Adequate curing is essential for the development of concrete strength. Proper moisture and temperature conditions during the early stages of hydration promote the formation of strong cementitious bonds, leading to higher compressive strength.
- Aggregate Properties: The properties of aggregates, such as their size, shape, and strength, can impact the strength of concrete. Well-graded aggregates with a good bond to the cement paste contribute to higher concrete strength.
- Water-Cement Ratio: The water-cement ratio has a significant influence on concrete strength. A lower water-cement ratio results in a denser concrete with stronger bonds, leading to higher compressive strength.
- Admixtures: The use of chemical admixtures can enhance concrete strength by improving workability, reducing water needs, or increasing early strength gain. Admixtures like superplasticizers or accelerators can be employed to optimize concrete strength.
Concrete Durability:
Durability is a crucial aspect of concrete performance, ensuring that structures can withstand environmental conditions, aggressive agents, and long-term use. Here are some factors that contribute to concrete durability:
- Water Resistance: Concrete should have adequate resistance to water penetration to prevent moisture-related issues such as corrosion of reinforcement or freeze-thaw damage. Properly proportioned concrete with low permeability and adequate curing helps ensure good water resistance.
- Chemical Resistance: Concrete may be exposed to various chemicals, including acids, alkalis, and salts. Proper mix design and the use of chemical-resistant materials or protective coatings can enhance concrete’s resistance to chemical attack.
- Crack Resistance: The prevention of cracks is crucial for concrete durability. Proper reinforcement placement, control of drying shrinkage through proper curing and mix design, and the use of crack-resistant admixtures or fibers can help reduce the risk of cracking.
- Freeze-Thaw Resistance: Concrete in freezing and thawing environments should be designed to withstand the expansion and contraction caused by cyclic freezing and thawing. Air-entrained concrete, which incorporates microscopic air bubbles, is commonly used to improve freeze-thaw resistance.
- Fire Resistance: Concrete offers excellent fire resistance due to its low thermal conductivity. It does not burn, melt, or release toxic gases when exposed to fire, making it a suitable choice for fire-resistant structures.
Proper mix design, careful construction practices, and regular maintenance are essential to ensure the strength and durability of concrete structures. Adhering to industry standards and guidelines and consulting with concrete experts can help ensure the longevity and performance of concrete in various construction applications.
Common Concrete Applications in Construction
Concrete is a versatile and widely used construction material due to its strength, durability, and adaptability. It is employed in a wide range of applications, from small-scale projects to large-scale infrastructure developments. Here are some common applications of concrete in construction:
- Residential Construction: Concrete is extensively used in residential construction for foundations, walls, floors, and driveways. It provides a solid and stable base for buildings and can be customized to achieve different finishes and aesthetics.
- Commercial Buildings: Concrete is commonly used in the construction of commercial buildings such as offices, retail spaces, and warehouses. It offers the strength and durability required for supporting the weight of the structure and accommodating various loads and systems.
- Bridges and Highways: Concrete plays a significant role in the construction of bridges and highways, providing the necessary strength to withstand heavy traffic loads. Precast and prestressed concrete elements are often used to accelerate construction and improve cost-effectiveness.
- Water and Sewage Infrastructure: Concrete is crucial for the construction of water and sewage infrastructure, including water treatment plants, sewage treatment facilities, and reservoirs. It provides a durable and watertight structure that can withstand the corrosive effects of water and chemicals.
- Retaining Walls and Slope Stabilization: Concrete is commonly used for constructing retaining walls and stabilizing slopes. It provides stability and resistance against soil pressure and erosion, making it ideal for creating terraced landscapes, preventing landslides, and supporting embankments.
- Industrial Structures: Industries such as manufacturing, power generation, and petrochemicals rely on concrete for their structures. Concrete provides the strength, fire resistance, and durability required for these demanding environments, supporting heavy equipment, storage tanks, and machinery.
- Agricultural Facilities: Concrete is widely used in agricultural facilities such as barns, silos, and storage buildings. It offers a robust structure to protect livestock, store feed and equipment, and withstand the rigors of the agricultural environment.
- Public Infrastructure: Concrete is utilized in various public infrastructure projects, including schools, hospitals, stadiums, airports, and cultural centers. Its versatility allows for the creation of architecturally striking structures that are built to last.
- Decorative and Architectural Features: Concrete’s malleability allows for the creation of decorative and architectural elements such as facades, columns, beams, and textured surfaces. Stained, stamped, or polished concrete can be used to enhance the visual appeal of structures and create unique design features.
These are just some of the many applications where concrete is utilized in construction. The adaptability, strength, and durability of concrete make it an indispensable material in the built environment.
Advantages and Disadvantages of Using Concrete in Construction
Concrete is a widely used construction material known for its strength, durability, and versatility. While it offers numerous advantages, it also has its drawbacks. Understanding the advantages and disadvantages of using concrete in construction is essential for making informed decisions. Here’s a closer look at both sides:
Advantages of Using Concrete:
- Strength and Durability: Concrete is renowned for its exceptional strength, making it suitable for structures that need to withstand heavy loads and harsh environmental conditions. It is also highly durable and can outlast many other construction materials.
- Fire Resistance: Concrete is inherently fire-resistant, providing a significant advantage in terms of fire safety. It does not burn, melt, or release toxic gases, making it a preferred choice for structures that require high levels of fire protection.
- Versatility and Flexibility: Concrete can be molded into various shapes and sizes, offering unparalleled architectural freedom and design flexibility. It allows for creative and innovative construction, making it suitable for both practical and aesthetic applications.
- Cost-Effective: Concrete is relatively cost-effective compared to other construction materials, especially considering its long lifespan and low maintenance requirements. It can also be produced locally, reducing transportation costs and environmental impact.
- Sound Insulation: Concrete provides excellent sound insulation, creating a quiet and comfortable living or working environment. It reduces the transmission of noise between spaces, making it suitable for residential, commercial, and industrial applications.
- Environmental Benefits: Concrete has a lower carbon footprint compared to other construction materials. It can incorporate recycled aggregates and by-products such as fly ash or slag, reducing waste and conserving natural resources. Additionally, concrete’s thermal mass can contribute to energy efficiency in buildings.
Disadvantages of Using Concrete:
- High Embodied Energy: The production of concrete requires a significant amount of energy and releases carbon dioxide emissions, contributing to environmental impacts. However, efforts are being made to develop more sustainable concrete production methods.
- Long Curing Time: Concrete typically requires a curing period to develop its full strength, which can extend the construction timeline. Adequate curing is crucial, and rushing the process can compromise the strength and durability of the concrete.
- Cracking and Shrinkage: Concrete is prone to cracking and shrinkage, particularly if not properly designed, mixed, and cured. Control joints and reinforcement can help mitigate these issues, but careful attention is necessary during construction.
- Heavy Weight: Concrete is a heavy material, which can pose challenges during transportation and construction. Specialized equipment and techniques may be required to handle and place concrete, leading to additional costs and logistics.
- Irreversible Changes: Once concrete is poured and cured, making changes or modifications can be difficult and costly. Precise planning and careful execution are necessary to avoid major modifications or corrections once the concrete has hardened.
- Maintenance and Repair: While concrete is durable, it still requires regular maintenance and occasional repairs to address issues such as cracks or deterioration. Neglecting maintenance can lead to the degradation of the concrete structure over time.
It is crucial to consider both the advantages and disadvantages of using concrete in construction projects. Proper planning, design, and construction practices can maximize the benefits of concrete while mitigating its drawbacks, resulting in safe, durable, and cost-effective structures.
Read more: What Sandpaper To Use On Concrete
Conclusion
Concrete is an indispensable material in the world of construction, offering unparalleled strength, durability, and versatility. Its use in a wide range of applications, from residential buildings to infrastructure projects, showcases its ability to meet the diverse needs of the construction industry.
Throughout this article, we have explored the properties of concrete, including its strength, durability, workability, and fire resistance. We have also discussed reinforced concrete, various types of concrete, and the importance of proper mixing, placement, curing, and finishing techniques. Additionally, we examined the common applications of concrete in construction, as well as its advantages and disadvantages.
Concrete’s notable advantages include its strength, fire resistance, versatility, and cost-effectiveness. It offers design flexibility, sound insulation, and environmental benefits. However, it also has its drawbacks, such as high embodied energy, long curing time, potential for cracking, and the need for maintenance and repair.
To maximize the benefits of concrete and mitigate its drawbacks, it is vital to implement proper construction practices, adhere to industry guidelines, and work with experienced professionals. Precise mix design, diligent curing, and careful finishing result in structures that exhibit optimal strength, durability, and aesthetic appeal.
As technology and innovation continue to advance, sustainable practices in concrete production are being developed to minimize its environmental impact. Efforts are being made to incorporate recycled materials, reduce carbon emissions, and improve overall sustainability throughout the lifecycle of concrete structures.
In conclusion, concrete’s exceptional properties make it a sought-after material in the construction industry. Its strength, versatility, and long-lasting durability allow for the creation of iconic structures that shape our urban landscape. By understanding and harnessing the potential of concrete, we can continue to build resilient, sustainable, and aesthetically pleasing environments for generations to come.
Frequently Asked Questions about How Is Concrete Used In Construction
Was this page helpful?
At Storables.com, we guarantee accurate and reliable information. Our content, validated by Expert Board Contributors, is crafted following stringent Editorial Policies. We're committed to providing you with well-researched, expert-backed insights for all your informational needs.
0 thoughts on “How Is Concrete Used In Construction”