Home>diy>Building & Construction>How To Prevent Falls In Construction
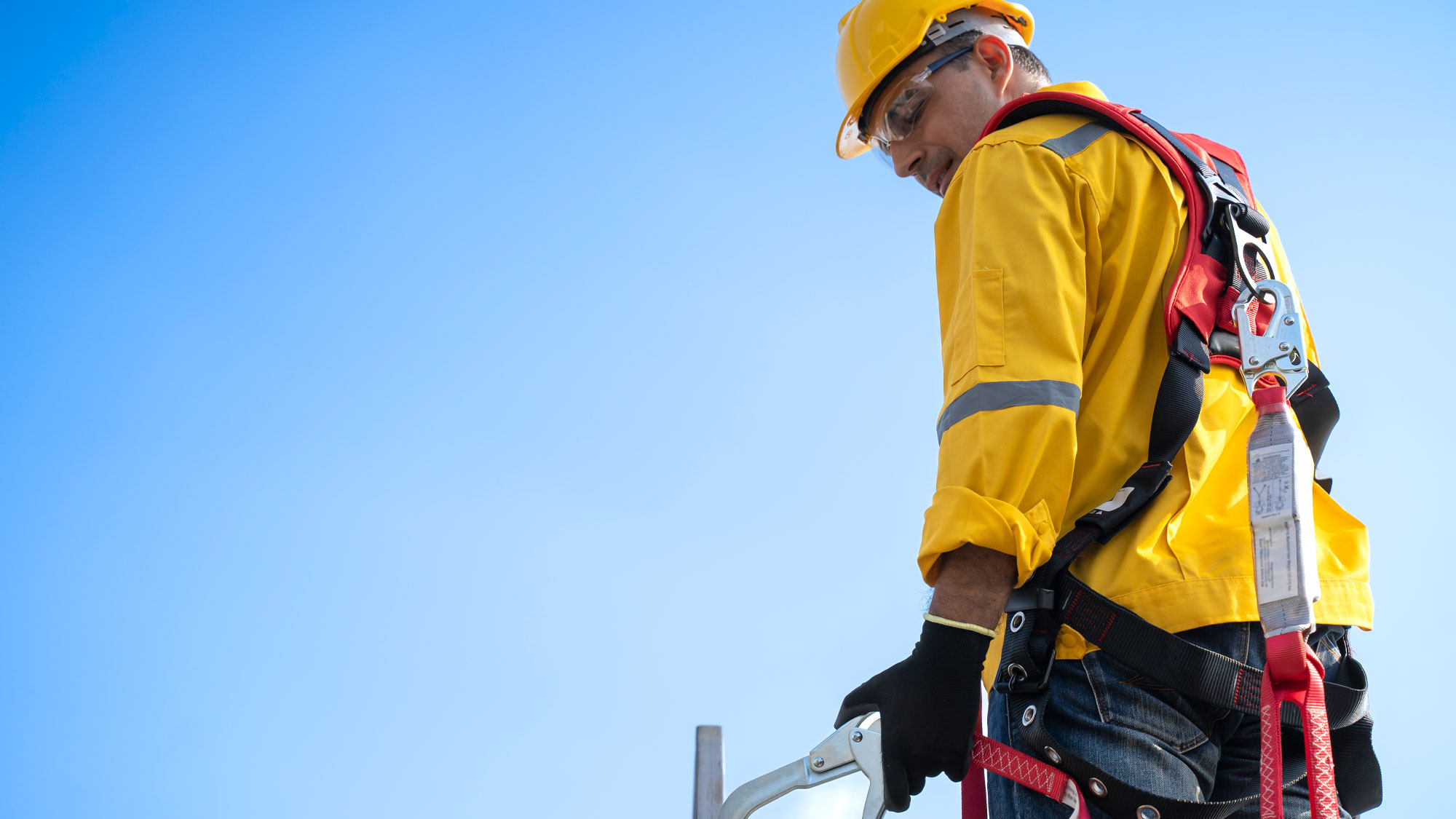
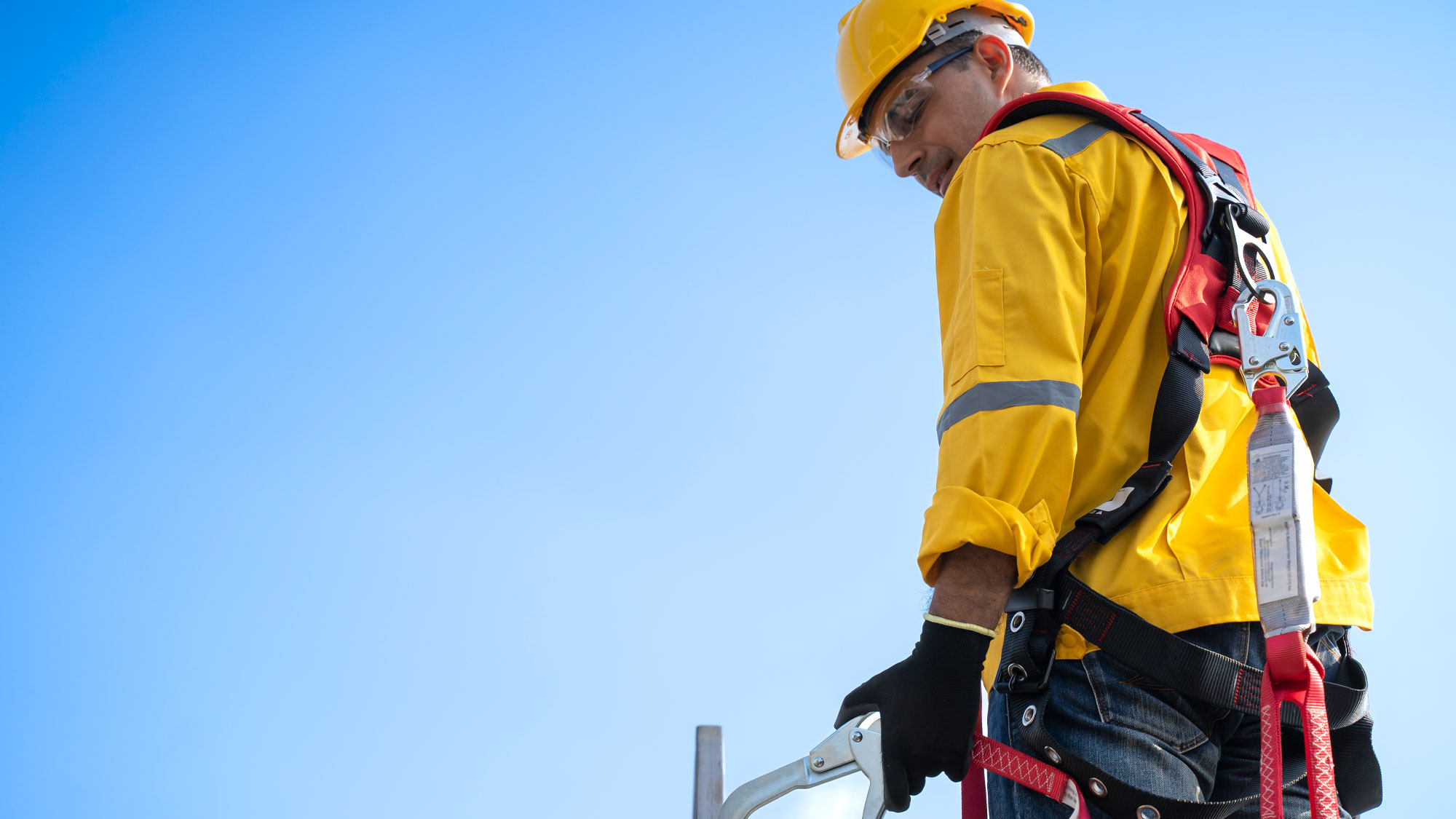
Building & Construction
How To Prevent Falls In Construction
Modified: December 7, 2023
Learn effective strategies for preventing falls in building construction with these helpful tips and techniques. Stay safe on the job and minimize the risk of accidents.
(Many of the links in this article redirect to a specific reviewed product. Your purchase of these products through affiliate links helps to generate commission for Storables.com, at no extra cost. Learn more)
Introduction
In the world of construction, safety is of paramount importance. When it comes to preventing accidents and ensuring the well-being of workers, one area that requires special attention is the risk of falls. Falls are one of the leading causes of injuries and fatalities in the construction industry. It is crucial for construction companies and workers to be proactive in taking measures to prevent falls and create a safe working environment.
This article will explore the importance of fall prevention in construction and provide practical strategies and guidelines for ensuring safety on construction sites. By understanding the causes of falls, complying with safety regulations, training workers, implementing fall protection systems, maintaining equipment, creating a safe working environment, and promoting collaboration and communication, we can significantly reduce the risk of falls in construction.
Read on to discover how you can make fall prevention a top priority in the construction industry and safeguard the well-being of workers.
Key Takeaways:
- Prioritizing fall prevention in construction safeguards workers’ lives, reduces injuries, enhances productivity, improves reputation, and ensures legal compliance, making it a smart business decision with far-reaching benefits.
- Collaboration, communication, and continuous education are essential for creating a culture of safety that actively prevents falls and ensures the well-being of construction workers.
Read more: How To Prevent A Shower Rod From Falling
Importance of Preventing Falls in Construction
Falls in the construction industry pose a significant risk to the health and safety of workers. The consequences of falls can range from minor injuries to severe disabilities and even fatalities. It is crucial to prioritize fall prevention to protect the well-being of construction workers and mitigate the financial and legal implications associated with workplace accidents.
By focusing on fall prevention, construction companies can:
- Protect Workers’ Lives: The most compelling reason to prevent falls in construction is to save lives. Construction workers often perform tasks at elevated heights, such as working on roofs, scaffolding, or ladders. Without proper fall prevention measures, the risk of fatal accidents increases significantly. Taking proactive steps to prevent falls can help safeguard workers’ lives, protecting them from the devastating consequences of a fall.
- Reduce Injuries and Disabilities: Falls often result in severe injuries, including broken bones, spinal cord injuries, head trauma, and more. These injuries can lead to long-term disabilities, affecting the quality of life for workers and putting a strain on their families and the healthcare system. Preventing falls in construction can reduce injuries, minimize disabilities, and promote a safer and healthier workforce.
- Enhance Productivity: When workers feel safe and secure at their job sites, they can focus on their tasks without constant worries about potential falls. This enables them to work efficiently and enhances overall productivity. On the other hand, workplace accidents can lead to lost productivity due to medical leave, staff replacements, and consequent disruptions. Prioritizing fall prevention can help maintain a seamless workflow and keep projects running smoothly.
- Improve Reputation and Client Satisfaction: Construction companies with a strong safety record and a commitment to fall prevention gain a reputation for professionalism and reliability. Clients are more likely to hire companies that prioritize the safety and well-being of their workers, seeing it as a reflection of their overall commitment to quality. By preventing falls and maintaining a safe working environment, construction companies can improve client satisfaction and drive business growth.
- Comply with Legal and Regulatory Standards: Governments and regulatory bodies have established strict safety regulations for the construction industry. Compliance with these standards is not only a legal requirement but also a moral obligation. By implementing fall prevention measures, construction companies ensure compliance with these regulations, mitigating the risk of hefty fines, legal battles, and damaged reputation.
Preventing falls in construction is not just a moral duty; it is also a smart business decision. By prioritizing fall prevention, companies can protect their workers, improve productivity, enhance their reputation, and comply with legal requirements. In the following sections, we will explore the various strategies and measures that can be implemented to prevent falls on construction sites.
Understanding the Causes of Falls in Construction
Before we delve into the strategies for preventing falls in construction, it is crucial to understand the common causes of falls. By identifying these causes, we can develop targeted prevention measures to address the underlying risks. Here are the key factors that contribute to falls in the construction industry:
- Unprotected Edges and Openings: Construction sites often have unprotected edges, such as rooftops, floor openings, stairwells, and wall openings, which pose a significant fall hazard. Workers can easily lose their balance and fall through these openings if not properly guarded.
- Unstable Surfaces: Construction sites are dynamic environments, and workers may encounter unstable surfaces such as scaffoldings, ladders, or uneven terrain. Any instability or lack of secure footing can result in slips, trips, and falls.
- Inadequate or Faulty Equipment: The use of faulty or inadequately maintained equipment, such as harnesses, ladders, scaffolding, or personal protective equipment (PPE), can increase the risk of falls. Equipment failure or improper usage can lead to accidents and injuries.
- Lack of Training and Awareness: Insufficient training and a lack of awareness regarding fall hazards can contribute to accidents. Workers may not be familiar with proper safety protocols or fail to recognize potential dangers, increasing their vulnerability to falls.
- Improper Use of Personal Protective Equipment (PPE): PPE, including fall arrest systems, harnesses, and safety helmets, is crucial for preventing falls. However, if workers do not wear or use PPE correctly, or if it is not properly maintained, its effectiveness in preventing falls is compromised.
- Weather and Environmental Factors: Inclement weather conditions, such as rain, snow, ice, or high winds, can create slippery surfaces and reduce visibility, contributing to falls. Environmental factors like poor lighting or obstructed walkways can also pose hazards.
- Lack of Communication and Coordination: Ineffective communication and coordination between workers, supervisors, and contractors can lead to confusion and a lack of awareness of potential fall hazards. This breakdown in communication can increase the likelihood of accidents.
By understanding the causes of falls, construction companies can implement targeted preventive measures that address specific risks. This knowledge empowers workers to recognize and avoid potential hazards, creating a safer working environment.
In the next sections, we will explore the measures and strategies that can be employed to prevent falls in construction, including compliance with safety regulations, training and education, proper use of PPE, implementing fall protection systems, equipment inspection and maintenance, ensuring a safe working environment, and promoting collaboration and communication on construction sites.
Compliance with Safety Regulations and Standards
Compliance with safety regulations and standards is a fundamental aspect of preventing falls in construction. Governments and regulatory bodies have implemented strict guidelines to ensure the safety and well-being of construction workers. Adhering to these regulations is not only a legal requirement but also a vital step to create a safe working environment. Here are some key considerations for complying with safety regulations:
- Stay Updated with Regulations: Construction companies must stay up-to-date with the latest safety regulations in their region. This includes federal, state, and local regulations that govern construction site safety. Regularly review and understand the requirements of these regulations to ensure full compliance.
- Develop a Safety Program: Establish a comprehensive safety program that incorporates fall prevention measures. This program should outline the company’s commitment to safety, identify potential fall hazards, and provide detailed procedures for mitigating those risks.
- Train Workers on Safety Protocols: Ensure that all workers undergo proper training on safety protocols and procedures. This includes educating them on fall risks, how to use and inspect personal protective equipment (PPE), and emergency response procedures. Regularly reinforce safety training to keep workers informed and vigilant.
- Conduct Site Inspections: Regularly inspect construction sites to identify potential fall hazards. This includes checking for proper guards on edges and openings, assessing the stability of scaffolding and ladders, and inspecting the condition of PPE. Address any deficiencies or hazards promptly to maintain a safe working environment.
- Provide Adequate Signage and Warnings: Install clear and visible signage to alert workers to potential fall hazards. Use warning signs and barricades to restrict access to hazardous areas until proper safety measures are implemented.
- Keep Records: Maintain detailed records of safety inspections, incidents, and training sessions. These records can serve as documentation of compliance and provide valuable information for identifying areas that need improvement.
- Collaborate with Inspectors and Regulatory Agencies: Engage in open communication with government inspectors and regulatory agencies. Seek their guidance and advice on maintaining compliance with safety regulations. Build collaborative relationships to ensure ongoing adherence to standards.
- Emphasize Accountability and Enforcement: Hold all employees accountable for following safety protocols and regulations. Promote a culture of safety and discipline those who violate safety policies. Regularly reinforce the importance of compliance through training, communication, and workplace policies.
Compliance with safety regulations is not an option; it is an essential responsibility for construction companies. By staying updated with regulations, developing a safety program, training workers, conducting regular inspections, providing signage, keeping records, collaborating with officials, and enforcing accountability, construction companies can significantly reduce the risk of falls and create a safe working environment for all.
Continuing on, we will explore the importance of training and education for construction workers to further strengthen fall prevention measures.
Training and Education of Construction Workers
Training and education play a critical role in preventing falls in the construction industry. When workers are well-informed and trained in safety protocols, they are better equipped to recognize and mitigate fall hazards. Here are some key considerations for effectively training and educating construction workers:
- Comprehensive Safety Orientation: Start by providing all new workers with a thorough safety orientation. This should include an overview of fall hazards, safety procedures, and the proper use of personal protective equipment (PPE). Emphasize the importance of safety from day one.
- Task-Specific Training: Tailor training programs to address specific tasks and work environments. Different job roles may encompass different fall risks, so it is important to provide targeted training for each task. For example, workers involved in roof work will need specialized training on working at heights and fall arrest systems.
- Regular Refresher Training: Conduct regular refresher training sessions to reinforce safety protocols and remind workers of potential fall hazards. Keep workers updated on the latest safety regulations and best practices. This will help maintain awareness and promote a safety-conscious culture.
- Hands-On Training: Supplement classroom-style training with practical, hands-on exercises. This can include simulating fall scenarios, demonstrating the proper use of safety equipment, and practicing emergency response procedures. Hands-on training helps workers understand the importance of safety measures and reinforces proper techniques.
- Engage Instructors with Construction Experience: Opt for trainers who have practical experience in the construction industry. Instructors who can relate to the challenges and demands of construction work can provide more relevant and effective training. They can provide real-world insights and share personal experiences that resonate with workers.
- Promote a Culture of Safety: Instill a culture of safety within the organization by fostering open communication and encouraging workers to report potential hazards. Create safety committees or teams consisting of workers from different job roles to actively participate in identifying and addressing safety concerns. Acknowledge and reward workers who actively contribute to maintaining a safe working environment.
- Encourage Continuous Learning: Promote continuous learning and professional development among construction workers. Encourage them to attend safety seminars, workshops, and conferences to stay updated on the latest industry practices. Investing in the knowledge and skills of workers shows a commitment to their growth and safety.
- Provide Multilingual Training: Recognize the diversity of the workforce and offer training materials and sessions in multiple languages to ensure that all workers can fully understand and participate in the training process.
A well-trained and educated workforce is better equipped to identify and mitigate fall risks on construction sites. By implementing comprehensive safety orientations, task-specific training, regular refreshers, hands-on exercises, engaging experienced instructors, fostering a safety-focused culture, promoting continuous learning, and providing multilingual training, construction companies can significantly reduce the risk of falls.
In the following sections, we will explore the proper use of personal protective equipment (PPE) and the implementation of fall protection systems as crucial fall prevention measures.
Read more: How To Prevent Shower Caddy From Falling
Proper Use of Personal Protective Equipment (PPE)
Personal Protective Equipment (PPE) is a crucial line of defense in preventing falls and protecting construction workers from injury. It is essential to ensure that workers understand the importance of PPE and that they use it correctly. Here are some key considerations for the proper use of PPE:
- Selection of Appropriate PPE: The first step in using PPE effectively is selecting the right equipment for the job. Consider the specific fall hazards present and ensure that the chosen PPE is designed to provide adequate protection. This may include safety harnesses, hard hats, safety goggles, gloves, and non-slip footwear.
- Proper Fitting and Sizing: Ill-fitting PPE can compromise its effectiveness and put workers at risk. Ensure that PPE items, such as harnesses and helmets, fit properly and are adjusted for individual workers. PPE should be comfortable to wear and allow for ease of movement without restricting functionality.
- Inspection and Maintenance: Regularly inspect all PPE for signs of wear and damage. Equipment that shows signs of wear, such as frayed straps or cracked helmets, should be immediately replaced. Additionally, provide proper storage and maintenance instructions to workers to keep PPE in good condition.
- Training on PPE Usage: Train workers on the proper use, care, and limitations of the specific PPE they are required to wear. Workers should understand when and how to use each item of PPE correctly. Reinforce the importance of wearing PPE at all times when exposed to fall hazards.
- Maintaining Cleanliness: PPE should be kept clean and free from contaminants to ensure its effectiveness. Regularly clean and sanitize PPE items, such as safety goggles and harnesses, to prevent any buildup of dirt or debris that may impair functionality.
- Encourage Compliance: Promote a culture of PPE compliance by encouraging workers to use PPE consistently and by leading by example. Managers, supervisors, and other leaders should make a point of wearing proper PPE during site visits to reinforce its importance.
- Provide Storage and Accessibility: Ensure that PPE is easily accessible to workers when needed. Provide designated storage areas for PPE items so that workers can easily retrieve and return them. This encourages regular use and prevents the excuse of not having access to appropriate equipment.
- Periodic Reinforcement and Evaluation: Conduct periodic training sessions to reinforce the importance of PPE usage and evaluate the effectiveness of current PPE measures. Review incident reports or near-miss reports related to improper PPE use to identify areas for improvement.
Proper use of PPE is essential in protecting construction workers from falls. By selecting appropriate PPE, ensuring proper fitting and sizing, inspecting and maintaining equipment, providing thorough training, maintaining cleanliness, encouraging compliance, providing proper storage and accessibility, and periodically reinforcing and evaluating PPE measures, construction companies can greatly reduce the risk of falls and promote a safer working environment.
In the next section, we will explore the implementation of fall protection systems as an additional layer of defense against falls in construction.
Always wear proper footwear with good traction to prevent slips and falls on construction sites. Keep your work area clean and free of debris to reduce the risk of tripping.
Implementing Fall Protection Systems
Implementing fall protection systems is key to preventing falls in construction and providing an additional layer of defense for workers. These systems are designed to minimize the risk of falls and protect workers when working at elevated heights. Here are some essential considerations for implementing fall protection systems:
- Identify Fall Hazards: Conduct a thorough assessment of the construction site to identify potential fall hazards. This includes identifying areas where workers may be at risk of falling, such as rooftops, scaffolding, elevated platforms, or edges.
- Hierarchy of Fall Protection: Follow the hierarchy of fall protection, which prioritizes the use of preventive measures in the following order: elimination (eliminating the fall hazard entirely), passive protection (guardrails and barriers), fall restraint (preventing workers from reaching a fall hazard), and fall arrest (protecting workers from falling using safety harnesses and anchors).
- Guardrails and Barriers: Install guardrails and barriers in areas where workers are at risk of falling, such as edges or openings. Ensure these protective structures meet the required height and strength regulations to prevent falls and provide a physical barrier.
- Fall Restraint Systems: Implement fall restraint systems to prevent workers from reaching a fall hazard. This may involve using restraint harnesses, lifelines, and anchor points to restrict workers’ access to areas where they could fall.
- Fall Arrest Systems: When fall hazards cannot be eliminated or controlled through other means, employ fall arrest systems. These systems consist of safety harnesses, lifelines, and anchor points that arrest the fall and minimize injury in the event of a fall.
- Anchorage Points: Ensure that adequate anchorage points are available and properly installed to support the fall arrest system. Anchorage points should be designed to withstand the potential impact forces of a fall and should be regularly inspected to ensure their integrity.
- Periodic Inspection and Maintenance: Regularly inspect all fall protection systems to ensure they are in good working condition. This includes checking harnesses, lifelines, guardrails, and anchor points for signs of wear, damage, or any malfunctions. Replace or repair any faulty or worn-out components immediately.
- Worker Training: Train workers on the proper use and limitations of fall protection systems. Ensure they understand how to inspect, set up, and use these systems correctly. Encourage workers to report any concerns or issues with the fall protection equipment promptly.
- Supervision and Compliance: Have experienced supervisors oversee work activities to ensure compliance with fall protection systems. Monitor workers to make sure they are using the systems correctly and are following the established safety protocols.
Implementing fall protection systems is crucial for reducing the risk of falls in the construction industry. By identifying fall hazards, following the hierarchy of fall protection, installing guardrails and barriers, using fall restraint and arrest systems, ensuring proper anchorage points, conducting periodic inspections, providing worker training, and promoting supervision and compliance, construction companies can effectively mitigate the risk of falls and prioritize the safety of their workers.
In the next section, we will discuss the importance of regular inspection and maintenance of equipment to further ensure the prevention of falls in construction.
Regular Inspection and Maintenance of Equipment
Regular inspection and maintenance of equipment is vital in preventing falls in the construction industry. Faulty or improperly maintained equipment can pose serious risks to workers and increase the likelihood of falls. Here are key considerations for ensuring the regular inspection and maintenance of equipment:
- Create an Equipment Maintenance Schedule: Establish a structured maintenance schedule that outlines when and how equipment should be inspected. This includes both regular maintenance tasks and more in-depth inspections. Adhere to the schedule to ensure all equipment is regularly assessed for safety.
- Document and Track Maintenance: Keep detailed records of equipment inspections and maintenance activities. Create a system to track when inspections were conducted, what issues were identified, and the actions taken to address them. This documentation provides a valuable reference and helps demonstrate adherence to maintenance protocols.
- Train Staff on Equipment Inspection: Provide training to staff members responsible for equipment inspection, ensuring they understand proper inspection protocols. Train them on identifying signs of wear, damage, or any potential hazards associated with equipment. This enables them to conduct thorough and effective inspections.
- Inspect All Safety Equipment Regularly: Pay special attention to equipment directly related to fall prevention, such as harnesses, lifelines, ladders, scaffolding, and guardrails. Regularly check their integrity, functionality, and suitability for their intended purpose. Replace any damaged or worn-out equipment immediately.
- Monitor Manufacturer Guidelines: Follow the manufacturer’s guidelines for maintenance and inspection of all equipment. These guidelines offer specific instructions and recommendations for ensuring the optimal performance and safety of the equipment. Adhering to these guidelines helps maintain the longevity and effectiveness of the equipment.
- Implement Preventive Maintenance: In addition to regular inspections, perform preventive maintenance tasks to address potential issues before they become more severe. This includes routine cleaning, lubrication, and adjustments to keep equipment in optimal working condition.
- Enforce Equipment Repair Policies: Establish clear policies for reporting and addressing equipment damage or malfunctions. Encourage workers to promptly report any issues they notice during operations. Develop a system for addressing repairs in a timely manner to prevent further risks associated with faulty equipment.
- Coordinate with Equipment Manufacturers and Suppliers: Maintain communication with equipment manufacturers and suppliers. Stay updated on any recalls, safety advisories, or recommended maintenance procedures for the equipment used on the construction site. This collaboration ensures that you have the most current information about the equipment in use.
Regular inspection and maintenance of equipment are essential components of preventing falls in construction. By creating an equipment maintenance schedule, documenting and tracking maintenance, training staff on inspection techniques, regularly inspecting safety equipment, monitoring manufacturer guidelines, implementing preventive maintenance, enforcing equipment repair policies, and coordinating with manufacturers and suppliers, construction companies can reduce the risks associated with faulty equipment and maintain a safe working environment.
In the next section, we will discuss the importance of ensuring a safe working environment to further enhance fall prevention measures in construction.
Ensuring a Safe Working Environment
Creating a safe working environment is crucial for preventing falls in construction. A well-designed and well-maintained work environment significantly reduces the risk of accidents and injuries. Here are key considerations for ensuring a safe working environment:
- Housekeeping and Clutter Control: Maintain a clean and organized work area to minimize tripping hazards and ensure clear paths for movement. Regularly remove debris, tools, and other materials from walkways and work areas to prevent slips, trips, and falls.
- Lighting: Ensure adequate lighting throughout the construction site, both indoors and outdoors. Well-lit work areas improve visibility, reducing the risk of falls caused by poor visibility or obscured hazards. Regularly inspect and replace any malfunctioning or dim lighting fixtures.
- Flooring and Surface Conditions: Inspect flooring and walking surfaces regularly to identify and address any hazards, such as uneven or slippery surfaces. Repair or replace damaged flooring promptly to prevent tripping and falling incidents.
- Weather Conditions: Take weather conditions into account when planning work activities. Inclement weather, such as rain, snow, or high winds, can create dangerous conditions, including slippery surfaces and reduced visibility. Implement appropriate safety measures and consider rescheduling work if conditions pose a significant hazard.
- Access and Egress Routes: Provide clear and safe access and egress routes throughout the construction site. Ensure that stairs, ramps, and walkways are properly designed, well-maintained, and free from obstructions. Install handrails and guardrails where necessary to enhance safety.
- Fall Hazard Signage: Use clear and visible signage to alert workers to fall hazards throughout the construction site. Signage should indicate areas where fall protection is required or where work at heights is taking place. This helps workers remain aware and attentive to potential fall risks.
- Emergency Response Preparedness: Establish and communicate an emergency response plan to all workers. This plan should include evacuation procedures, first aid protocols, and contact information for emergency responders. Conduct drills periodically to ensure everyone is familiar with the procedures.
- Communication and Reporting Processes: Encourage open communication among workers and provide mechanisms for reporting safety concerns or near-miss incidents. Implement an anonymous reporting system if necessary to ensure workers feel safe reporting potential hazards and near-misses without fear of retaliation.
- Regular Inspections and Audits: Conduct regular inspections and safety audits to identify potential hazards and address them promptly. Involve workers in the inspection process and encourage them to report any safety concerns they notice. This proactive approach helps maintain a safe working environment for all.
Ensuring a safe working environment is a shared responsibility among all levels of the construction team. By prioritizing housekeeping and clutter control, maintaining proper lighting, monitoring flooring and surface conditions, considering weather conditions, providing clear access and egress routes, using fall hazard signage, preparing for emergencies, fostering communication and reporting processes, and conducting regular inspections and audits, construction companies can create a work environment that minimizes the risk of falls and promotes the overall safety and well-being of workers.
In the final section, we will explore the importance of collaboration and communication on the construction site as a crucial factor in fall prevention.
Read more: How To Prevent A Fall When Climbing Stairs
Collaboration and Communication on the Construction Site
Collaboration and communication on the construction site are vital for preventing falls. By fostering a culture of teamwork and open communication, construction workers can effectively identify and address fall hazards, share important information, and work together to maintain a safe working environment. Here are key considerations for promoting collaboration and communication:
- Effective Job Site Planning: Involve all stakeholders, including workers, supervisors, and contractors, in the planning phase of construction projects. Foster collaboration by encouraging the exchange of ideas and insights regarding fall prevention strategies, potential hazards, and safety measures.
- Regular Safety Meetings: Conduct regular safety meetings where workers and supervisors can discuss safety concerns, review procedures, and share updates on fall prevention measures. These meetings provide an opportunity to address any issues and ensure that everyone is aligned on safety protocols.
- Open Communication Channels: Establish clear channels for communication, ensuring that workers can easily report safety concerns, hazards, or near-miss incidents. Encourage workers to speak up and provide anonymous reporting options if required. Foster an environment where workers feel comfortable discussing safety-related matters without fear of retribution.
- Collaborative Hazard Identification: Engage workers in the identification and reporting of fall hazards. They are often at the forefront of the work and have firsthand knowledge of potential risks. Encourage workers to actively participate in hazard identification programs and provide feedback on proposed control measures.
- Joint Safety Inspections: Conduct joint safety inspections that include workers, supervisors, and safety professionals. This collaborative approach ensures that all perspectives are considered, and potential fall hazards are thoroughly evaluated and addressed.
- Training and Orientation Programs: Promote collaboration and communication during training and orientation programs. Use group discussions, interactive activities, and case studies to encourage workers to share their experiences and insights. This allows for the cross-pollination of knowledge and the development of a collective understanding of fall prevention strategies.
- Encourage Reporting of Near-Miss Incidents: Emphasize the importance of reporting near-miss incidents related to falls. Near-miss incidents provide valuable insights into potential hazards and can serve as opportunities for proactive prevention. Encourage workers to report near-misses without fear of consequences, fostering a culture of continuous improvement and prevention.
- Peer-to-Peer Mentoring: Facilitate peer-to-peer mentoring and regular communication among workers. Experienced workers can mentor newer employees, sharing their knowledge and experience regarding fall prevention. This encourages the transfer of best practices and enhances overall safety awareness among the workforce.
- Recognize and Reward Safety Contributions: Acknowledge and celebrate individuals or teams who contribute to fall prevention and safety initiatives. Recognitions and rewards can motivate workers to actively engage in communication, collaboration, and proactive safety practices.
Collaboration and communication are powerful tools in preventing falls in construction. By promoting effective job site planning, conducting regular safety meetings, establishing open communication channels, encouraging collaborative hazard identification, conducting joint safety inspections, facilitating collaborative training programs, encouraging reporting of near-miss incidents, fostering peer-to-peer mentoring, and recognizing safety contributions, construction companies can create a culture of safety that actively works to prevent falls and ensures the well-being of all workers.
And with that, we conclude our comprehensive guide on preventing falls in construction. By implementing these strategies and measures, construction companies can prioritize safety, reduce accidents, and create a work environment that protects the lives and well-being of construction workers.
Conclusion
Falls are a significant risk in the construction industry, but with the right strategies and measures in place, they can be effectively prevented. By prioritizing fall prevention, construction companies demonstrate their commitment to the safety and well-being of their workers. Through compliance with safety regulations and standards, training and education, proper use of personal protective equipment (PPE), implementing fall protection systems, regular equipment inspection and maintenance, ensuring a safe working environment, and fostering collaboration and communication, construction companies can significantly reduce the risk of falls on their job sites.
Preventing falls in construction not only protects workers’ lives but also reduces injuries, enhances productivity, improves reputation, and ensures compliance with legal and regulatory standards. By investing in comprehensive safety programs, providing adequate training, frequently inspecting equipment, maintaining an organized work environment, and promoting open communication, construction companies can create a culture of safety that permeates every aspect of their operations.
It is crucial to remember that fall prevention is an ongoing effort. It requires regular evaluation and adjustment to address emerging risks and changing circumstances. Workers must be continuously educated on the latest safety protocols, equipment, and procedures to ensure their skills and knowledge remain up to date. Additionally, fostering a collaborative and communicative work environment enables workers to actively identify and report hazards, contributing to a continuous improvement culture.
By implementing these strategies and measures, construction companies can minimize the risk of falls and prioritize the safety and well-being of their workers, ultimately creating a safer and more productive work environment. Let us collectively commit to preventing falls in construction and ensure that every worker goes home safely at the end of the day.
Frequently Asked Questions about How To Prevent Falls In Construction
Was this page helpful?
At Storables.com, we guarantee accurate and reliable information. Our content, validated by Expert Board Contributors, is crafted following stringent Editorial Policies. We're committed to providing you with well-researched, expert-backed insights for all your informational needs.
0 thoughts on “How To Prevent Falls In Construction”