Home>diy>Building & Construction>How To Use A Benchmark In Construction
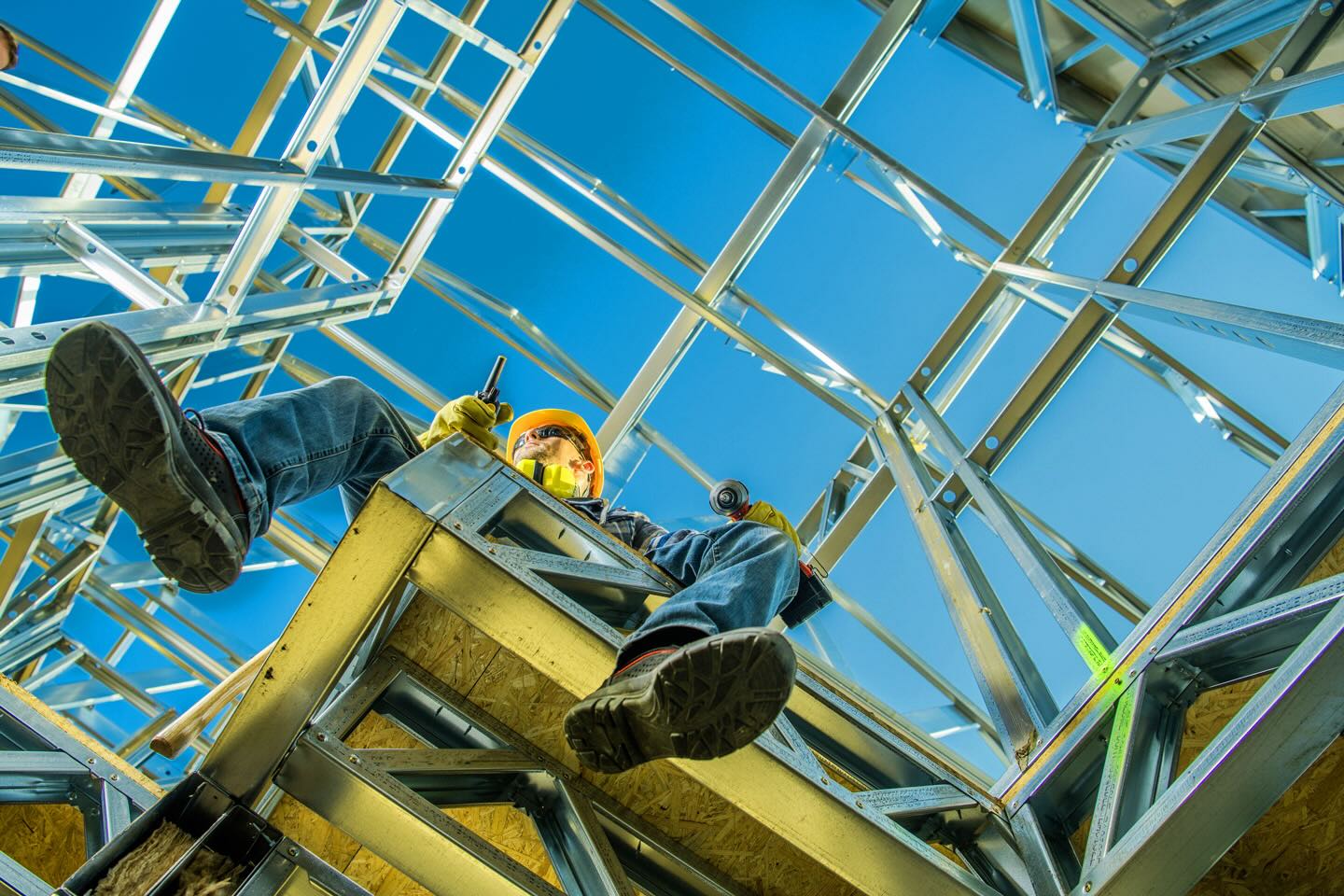
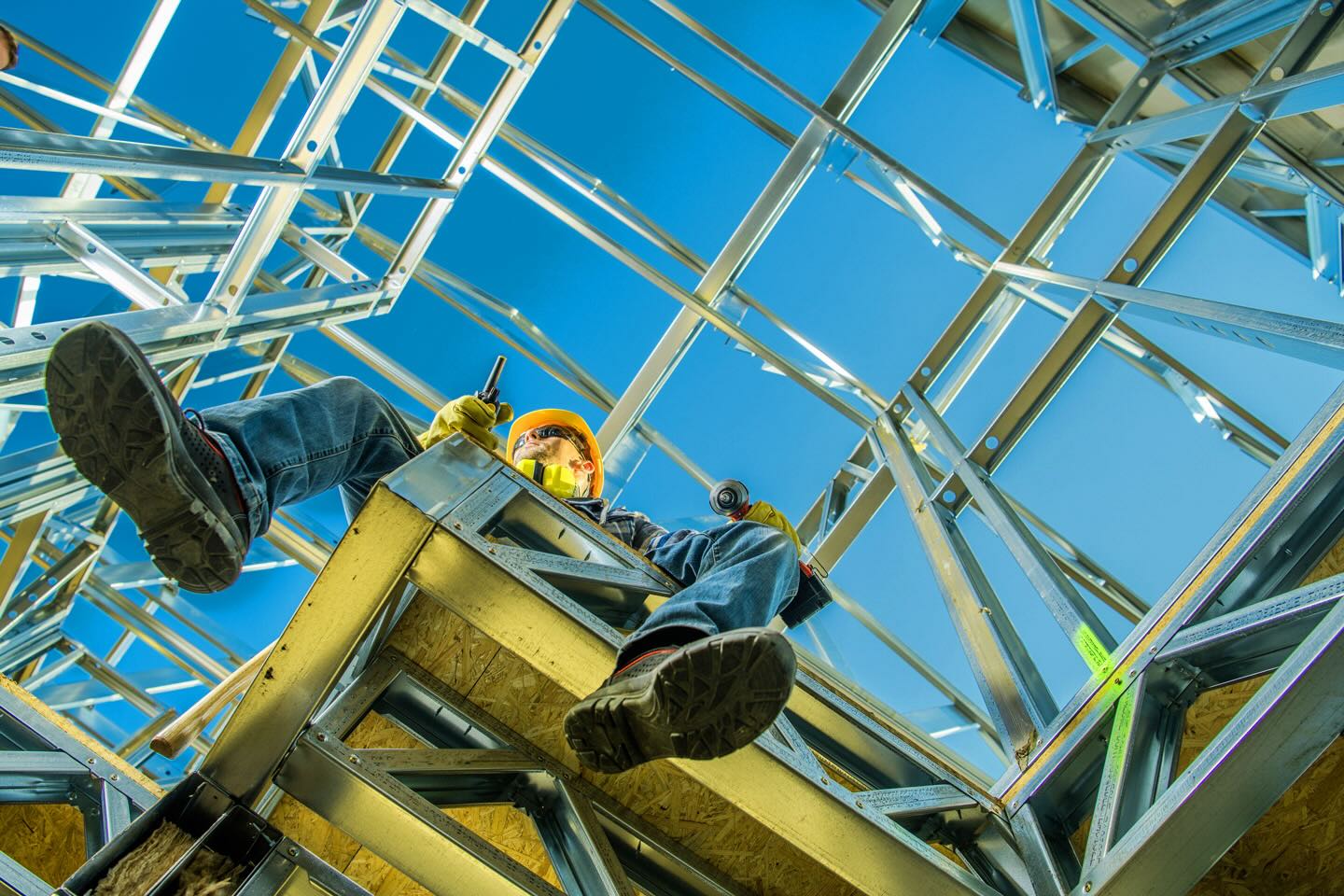
Building & Construction
How To Use A Benchmark In Construction
Modified: January 9, 2024
Learn how to effectively use a benchmark in building construction to ensure accuracy and precision in your projects. Master the art of leveling and measuring for optimal results.
(Many of the links in this article redirect to a specific reviewed product. Your purchase of these products through affiliate links helps to generate commission for Storables.com, at no extra cost. Learn more)
Introduction
When it comes to constructing a building, precision and accuracy are of utmost importance. One essential tool that plays a crucial role in achieving these goals is a benchmark. In the world of construction, a benchmark serves as a reference point that helps ensure the correct vertical and horizontal alignment of structures. It provides a standardized level to measure and compare various elements of a construction project.
Whether it’s setting the foundation, aligning walls, or installing utilities, using benchmarks effectively can make a significant difference in the overall quality of the building. In this article, we will explore what benchmarks are, their types, and how they are used in the construction industry. We will also discuss the importance of accurate benchmarking, the benefits it offers, challenges it presents, and best practices for utilizing benchmarks in construction projects.
Key Takeaways:
- Benchmarks are crucial in construction, ensuring precision and alignment of building components. They serve as reliable reference points, promoting consistency, quality, and efficient communication among construction professionals.
- Utilizing benchmarks offers benefits such as improved accuracy, cost efficiency, and streamlined workflows. However, challenges like accuracy maintenance and project-specific considerations require careful management and best practices implementation.
Read more: What Is Benchmarking In Construction
What is a Benchmark in Construction?
In construction, a benchmark is a fixed reference point or elevation used to establish the correct level and alignment of various components of a building. It serves as a point of comparison for measurements, ensuring accuracy and consistency throughout the construction process. Benchmarks are typically established at strategic locations on the construction site and are often permanent fixtures.
A benchmark consists of a metal or concrete slab embedded into the ground, with precise measurements marked on its surface. It provides a known elevation or level that can be used as a starting point for measuring heights, depths, and distances. Contractors and construction professionals refer to benchmarks to determine the vertical or horizontal alignment of walls, structures, and other elements of a building.
Having a benchmark is crucial in construction for several reasons. It enables contractors to ensure that different components of the building align properly, preventing issues such as uneven floors, crooked walls, or misaligned windows. It also helps architects, engineers, and construction workers maintain accurate measurements and follow design specifications, resulting in a structurally sound and visually pleasing final product.
Benchmarks are commonly used throughout all stages of a construction project, from setting the foundation to completing the finishing touches. They provide a reliable reference point that allows for precise communication and coordination among all parties involved in the construction process.
It’s important to note that benchmarks can be established both vertically and horizontally. Vertical benchmarks, also known as height benchmarks, help determine the elevation or height of different parts of a building, such as floors or doorways. Horizontal benchmarks, on the other hand, aid in achieving alignment and levelness along a specific plane, such as the ground or a wall.
Now that we have a basic understanding of what benchmarks are in construction, let’s explore the different types of benchmarks that are commonly used in the industry.
Types of Benchmarks
There are several types of benchmarks used in construction, each serving a specific purpose. Understanding these different types can help construction professionals effectively utilize benchmarks in their projects. Let’s explore some of the most common types:
- Permanent Benchmarks: These benchmarks are considered as long-term references and are typically made of durable materials like concrete or metal. Permanent benchmarks are carefully placed in strategic locations on the construction site and are meant to remain in place even after the project is completed. They provide a fixed point of reference for future construction or surveying activities.
- Temporary Benchmarks: As the name suggests, these benchmarks are established for the duration of a specific construction project. Temporary benchmarks are commonly used when a permanent benchmark is not feasible or when there is a need to establish a benchmark at a specific location that is easily accessible. These benchmarks are typically created using easily visible markers, such as wooden stakes or painted lines.
- Project Benchmarks: Project benchmarks are established at key stages or milestones throughout the construction project. They help track progress, ensure correct alignment, and provide a reference for measurements and evaluations. These benchmarks may include critical points like the foundation level, the height of different floors, or the alignment of walls.
- Reference Benchmarks: Reference benchmarks are used to establish a specific elevation or level that is consistent across the construction site. These benchmarks serve as a starting point for measuring heights or depths of various building elements, ensuring uniformity and accuracy. Reference benchmarks are essential for maintaining consistent levels throughout the project.
- Control Benchmarks: Control benchmarks are established to maintain precise horizontal and vertical alignment across multiple construction sites. These benchmarks are carefully positioned and measured to serve as reference points for multiple projects in the same vicinity. Control benchmarks are particularly useful in large-scale construction projects where coordination between multiple sites is required.
Each type of benchmark has its own advantages and applications, depending on the specific needs of the construction project. A combination of different benchmarks may be used to ensure comprehensive and accurate measurement and alignment throughout the construction process.
Now that we have explored the different types of benchmarks, let’s dive into how benchmarks are used in construction projects.
Using Benchmarks for Construction Projects
Benchmarks play a critical role in construction projects by providing a reliable reference point for measuring and aligning various components of a building. Let’s explore how benchmarks are used in different stages of a construction project:
- Foundation Setting: When constructing a building, one of the first steps is to set the foundation. Benchmarks are used to determine the correct depth and alignment of the foundation. By referencing the benchmark, construction professionals can ensure that the foundation is level and accurately positioned.
- Alignment of Walls: Benchmarks are crucial for aligning walls during the construction process. By measuring from a benchmark, contractors can ensure that walls are upright and properly aligned. This helps in maintaining structural integrity, avoiding issues such as leaning or crooked walls.
- Utility Installation: Benchmarks are used to maintain proper elevation and alignment when installing utilities such as plumbing, electrical conduits, and HVAC systems. These benchmarks guide contractors in positioning these utilities at the correct heights and depths, ensuring efficiency and functionality.
- Floor Leveling: Achieving even and level floors is essential for a building’s functionality and aesthetics. Benchmarks are used to determine the desired levelness of floors at different points throughout the building. Contractors can then reference these benchmarks while pouring and leveling concrete for a consistent and level surface.
- Structural Elements: Benchmarks are used to ensure the correct alignment and levelness of structural elements such as beams, columns, and trusses. By referencing benchmarks, construction professionals can accurately position these elements, maintaining the structural integrity of the building.
Throughout the construction process, benchmarks serve as a point of comparison, ensuring that different components of the building are aligned correctly and meet the required specifications. By utilizing benchmarks effectively, construction professionals can minimize errors, improve efficiency, and deliver high-quality results.
Now that we understand how benchmarks are used in construction projects, let’s explore how to set up a benchmark effectively.
Setting Up a Benchmark
Setting up a benchmark correctly is crucial to ensure its accuracy and effectiveness in construction projects. Here are the essential steps to follow when establishing a benchmark:
- Select a Suitable Location: Choose a location on the construction site that is easily accessible and will remain undisturbed throughout the project. It should also be within close proximity to the area where benchmark measurements will be frequently taken.
- Determine the Benchmark Elevation: Depending on the requirements of the project, decide on the desired benchmark elevation. This could be based on existing ground levels, design specifications, or reference benchmarks in the vicinity. Ensure the benchmark elevation is clearly defined and documented for future reference.
- Prepare the Benchmark Base: Clear the selected location of any debris, vegetation, or uneven surfaces. Level the ground and create a stable base for the benchmark. If necessary, dig a small hole to embed the benchmark into the ground.
- Install the Benchmark: Place the benchmark on the prepared base, ensuring it sits firmly and securely. The benchmark can be a metal plate, concrete slab, or any other suitable material. Make sure it is properly aligned with the desired benchmark elevation.
- Mark Measurements on the Benchmark: Use precise measuring instruments to mark the desired benchmark elevation on the surface of the benchmark. This could be in the form of engraved lines, indented measurements, or painted markings. Ensure the measurements are clear and easily visible.
- Document the Benchmark: Record all relevant information about the benchmark, including its location, elevation, and any other necessary details. This documentation is important for future reference, maintenance, and coordination with other construction professionals.
Once the benchmark is properly set up, it becomes a reliable reference point that can be used throughout the construction project. It serves as a starting point for measuring and aligning various components, ensuring accuracy and consistency.
It’s essential to periodically check and verify the benchmark’s accuracy during the construction process. Factors such as settlement, ground movement, or changes in elevation may affect the benchmark’s reliability over time. Regular monitoring and adjustment, if needed, will help maintain the benchmark’s accuracy throughout the project.
Now that we know how to set up a benchmark effectively, let’s discuss the importance of accurate benchmarking in construction.
When using a benchmark in construction, ensure it is set on stable ground and protected from disturbance. Use a leveling instrument to accurately measure and mark the benchmark’s elevation.
Read more: How Is Concrete Used In Construction
The Importance of Accurate Benchmarking
Accurate benchmarking is vital in construction projects for several reasons. It ensures precision, consistency, and adherence to design specifications throughout the construction process. Let’s explore the importance of accurate benchmarking:
- Precision and Accuracy: Accurate benchmarking provides a reliable reference point for measuring and aligning various components of a building. It helps ensure that structures, walls, and other elements are positioned correctly. This level of precision is essential for maintaining structural integrity and minimizing potential issues, such as uneven floors or misaligned structures.
- Coordination among Professionals: Benchmarking facilitates effective communication and coordination among different professionals involved in the construction process. Architects, engineers, surveyors, and contractors can all refer to the same benchmarks for consistent measurements and alignments. This reduces the chances of miscommunication and ensures a seamless workflow.
- Quality Control: Accurate benchmarking is crucial for maintaining quality control in construction projects. By referencing benchmarks, construction professionals can verify that each element meets the required specifications and standards. It allows for thorough inspections and ensures that the final product meets or exceeds expectations.
- Timely Completion: When benchmarks are accurately established and used, it helps streamline the construction process, leading to efficient workflows and timely completion. Contractors can rely on benchmarks to make precise measurements and alignments, avoiding unnecessary delays or rework caused by inaccuracies.
- Future Maintenance and Repairs: Accurate benchmarking provides a valuable reference for future maintenance and repair work. By documenting the benchmark locations and elevations, property owners and maintenance teams can easily reference them when making adjustments or repairs. This ensures consistency and helps preserve the integrity of the building over time.
- Legal Compliance: In some cases, accurate benchmarking is required by local building codes and regulations. By ensuring compliance with these codes, construction professionals can avoid legal issues and ensure the safety and structural integrity of the building.
Accurate benchmarking sets the foundation for a successful construction project. It establishes a common reference point for all involved parties, promotes precision, and ensures high-quality results. By prioritizing accurate benchmarking, construction professionals can achieve efficiency, minimize errors, and deliver buildings that meet the highest standards.
Now that we understand the importance of accurate benchmarking, let’s explore the benefits of utilizing benchmarks in construction.
Benefits of Utilizing Benchmarks in Construction
Utilizing benchmarks in construction projects offers numerous benefits that contribute to the overall success and quality of the building. Let’s explore some of the key advantages of incorporating benchmarks:
- Precision and Accuracy: Benchmarks provide a reliable and standardized reference point for measuring and aligning various components of the building. This precision ensures that structures, walls, and other elements are positioned accurately, leading to a well-built and visually pleasing final product.
- Consistency and Standardization: Benchmarks establish a consistent level of measurement and alignment across the construction site. Construction professionals can use benchmarks as a universal reference for ensuring uniformity throughout the project, leading to a cohesive and harmonious design.
- Improved Communication and Collaboration: Benchmarks facilitate effective communication and collaboration among architects, engineers, contractors, and other professionals. By referring to the same benchmarks, they can effectively communicate measurements and alignments, reducing misunderstandings and streamlining the construction process.
- Easier Maintenance and Repairs: Utilizing benchmarks simplifies future maintenance and repair work. Benchmarks provide a reference point for making adjustments or repairs, helping to ensure consistency and preserve the building’s structural integrity over time.
- Time and Cost Efficiency: By using benchmarks, construction professionals can work more efficiently, reducing the chances of errors, rework, and delays. This efficiency leads to cost savings and timely project completion, benefiting both the construction team and the client.
- Quality Control: Benchmarks enable effective quality control throughout the construction process. By referencing benchmarks, professionals can ensure that each element meets the required specifications, resulting in a high-quality, durable, and visually appealing final product.
- Legal Compliance: Utilizing benchmarks can help ensure compliance with local building codes and regulations. By meeting these requirements, construction professionals can avoid legal issues and ensure the safety and integrity of the building.
Incorporating benchmarks into construction projects is a valuable practice that enhances precision, consistency, and collaboration while reducing errors and delays. Construction professionals can reap the benefits of utilizing benchmarks, leading to successful projects and satisfied clients.
Now, let’s discuss the challenges and limitations associated with using benchmarks in construction.
Challenges and Limitations of Using Benchmarks
While utilizing benchmarks in construction offers considerable advantages, it is important to be aware of the challenges and limitations associated with their use. Let’s explore some of the key challenges:
- Accuracy: Ensuring the accuracy of benchmarks can be challenging, especially when factors such as ground movement, settlement, or changes in elevation occur. Regular monitoring and adjustment are essential to maintain the accuracy of benchmarks throughout the construction process.
- Surveying and Measurement: Achieving accurate and precise surveying and measurement can be a complex task, requiring skilled professionals and specialized equipment. Errors in surveying or measurement can adversely affect the reliability of benchmarks, leading to inconsistencies and inaccuracies in the construction project.
- Environmental Factors: Environmental factors such as weather conditions, terrain, and soil composition may impact the stability and longevity of benchmarks. Harsh weather conditions or unstable ground may require additional measures to protect or adjust the benchmarks to maintain their accuracy and effectiveness.
- Accessibility: Benchmarks should be easily accessible throughout the construction process for accurate measurements and alignments. However, there may be instances where benchmarks become obstructed or difficult to access due to the progression of construction. In such cases, alternative benchmarks or temporary benchmarks may need to be established.
- Topographical Variations: Construction sites can have variations in topography, including uneven surfaces or slopes. This can pose challenges when referencing benchmarks for measurements and alignments. Additional leveling or adjustment may be necessary to accommodate these variations.
- Project-Specific Considerations: Each construction project has its unique requirements and specifications. Different benchmarks may be needed for different phases or areas of the project. It’s essential to carefully consider project-specific factors and establish benchmarks accordingly.
- Maintenance: Benchmarks require regular maintenance to ensure their longevity and accuracy. This includes monitoring for any physical damage, clearing obstructions, and verifying their alignment and elevation. Failure to properly maintain benchmarks may result in inaccuracies and compromise their effectiveness.
Being aware of these challenges and limitations is crucial in effectively utilizing and managing benchmarks in construction projects. Construction professionals should continuously monitor, evaluate, and adjust benchmarks to ensure their accuracy and reliability throughout the construction process.
Now, let’s move on to explore best practices for using benchmarks in construction.
Best Practices for Using Benchmarks in Construction
To maximize the effectiveness and accuracy of benchmarks in construction projects, it is essential to follow best practices. Here are some key practices to consider:
- Establish Clear Documentation: Document all benchmark-related information, including their location, elevation, and any relevant measurements. This documentation serves as a reference for construction professionals and future maintenance teams.
- Regularly Verify Benchmarks: Periodically check and verify the accuracy of benchmarks throughout the construction process. Environmental factors, ground movement, or other variables can impact the stability and reliability of benchmarks. Adjust or recalibrate benchmarks as necessary to maintain accuracy.
- Use Reliable Surveying and Measurement Techniques: Employ experienced professionals and accurate surveying and measurement equipment to ensure precise and consistent readings. Adhere to standardized surveying practices and techniques to minimize errors and inconsistencies.
- Coordinate with all Stakeholders: Effective communication and coordination among architects, engineers, contractors, and surveyors are crucial. Ensure that all parties involved understand the benchmarks’ purpose, location, and elevation, promoting accurate measurements and alignment.
- Consider Project-Specific Requirements: Tailor the selection and placement of benchmarks to suit the specific needs of the project. Different benchmarks may be necessary for various stages or areas to ensure accurate measurements and alignments.
- Maintain Benchmarks Properly: Regularly inspect and maintain benchmarks to ensure their longevity and accuracy. Clear obstructions, perform routine maintenance, and protect benchmarks from physical damage. This helps preserve the benchmark’s effectiveness throughout the construction process.
- Utilize Benchmark Data for Quality Control: Leverage the data obtained from benchmarks for quality control inspections. Compare measurements with design specifications to ensure compliance and identify any discrepancies that need to be addressed.
- Train Construction Personnel: Provide training and guidance to construction personnel on how to effectively use benchmarks. Ensure they understand the importance of benchmarks, how to take measurements accurately, and how to use benchmarks for proper alignment and positioning.
- Continuously Monitor and Adjust: Monitor benchmarks throughout the construction process and make necessary adjustments to maintain their accuracy. Regularly assess benchmark stability and ground conditions to ensure their effectiveness.
By following these best practices, construction professionals can optimize the use of benchmarks in their projects. This leads to improved precision, accuracy, communication, and overall project success.
Now, let’s conclude our discussion on utilizing benchmarks in construction.
Read more: How Is Math Used In Construction
Conclusion
Benchmarks are an essential tool in the construction industry, providing a reliable reference point for measuring and aligning various components of a building. From setting the foundation to aligning walls and installing utilities, benchmarks play a crucial role in achieving precision, consistency, and quality throughout the construction process.
In this article, we explored what benchmarks are, the different types of benchmarks, and how they are used in construction projects. We discussed the importance of accurate benchmarking, including its role in promoting precision, coordination among professionals, quality control, and timely project completion. We also examined the benefits of utilizing benchmarks, such as improved communication, cost efficiency, and future maintenance convenience.
However, we also acknowledged the challenges and limitations associated with using benchmarks, including the need for accuracy, environmental factors, accessibility issues, and project-specific considerations. By understanding these challenges, construction professionals can employ best practices to overcome them and optimize the use of benchmarks effectively.
Key best practices for using benchmarks in construction include establishing clear documentation, regularly verifying benchmarks, utilizing reliable surveying and measurement techniques, coordinating with all stakeholders, considering project-specific requirements, and properly maintaining benchmarks.
In conclusion, benchmarks are a valuable asset in construction projects, providing a standardized reference for precise measurement and alignment. When utilized effectively and supported by accurate surveying and measurement practices, benchmarks contribute to the successful completion of high-quality buildings. With proper documentation, coordination, and maintenance, construction professionals can rely on benchmarks to ensure precision, consistency, and adherence to design specifications.
By incorporating the best practices discussed in this article, construction professionals can harness the full potential of benchmarks and enhance their construction projects, resulting in structurally sound, visually appealing, and successful outcomes.
Frequently Asked Questions about How To Use A Benchmark In Construction
Was this page helpful?
At Storables.com, we guarantee accurate and reliable information. Our content, validated by Expert Board Contributors, is crafted following stringent Editorial Policies. We're committed to providing you with well-researched, expert-backed insights for all your informational needs.
0 thoughts on “How To Use A Benchmark In Construction”