Home>diy>Building & Construction>What Does “ITP” Mean In Construction
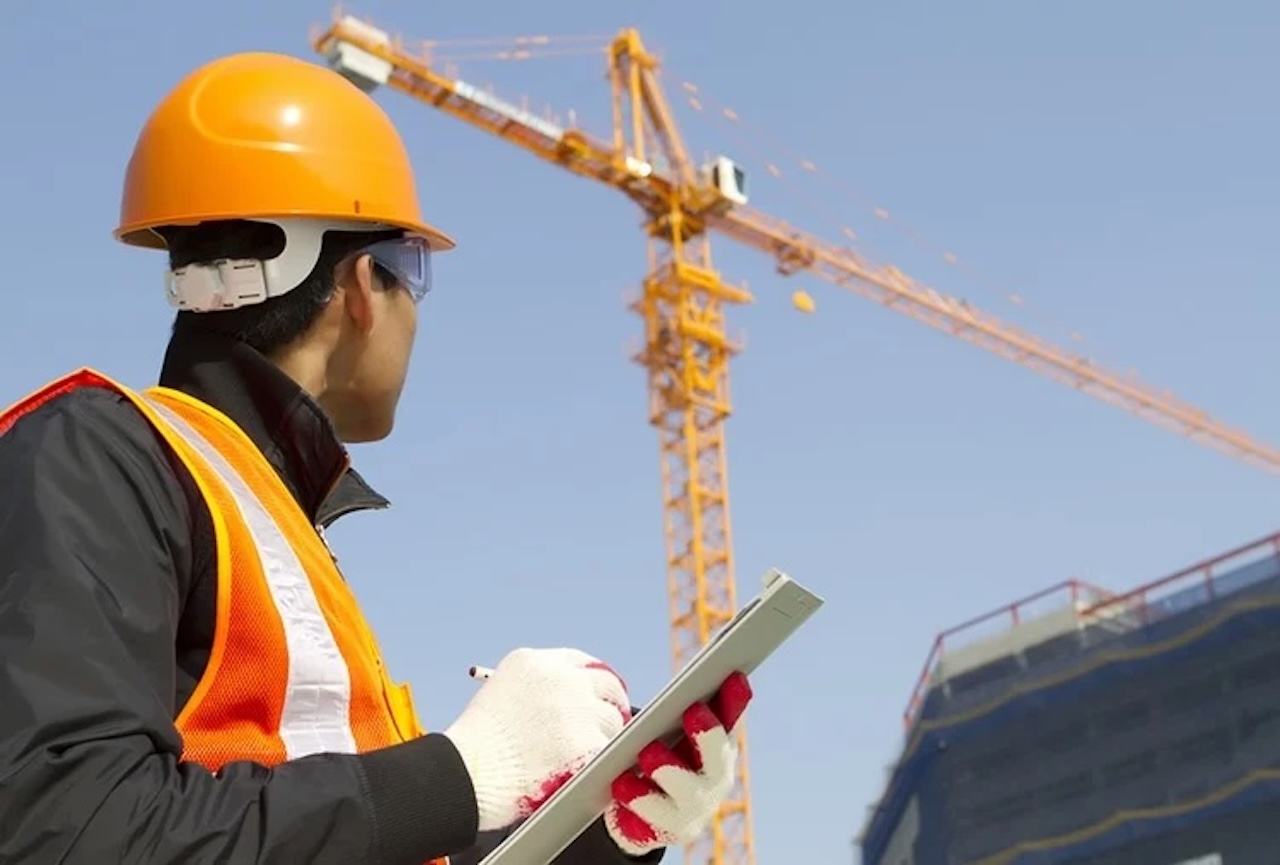
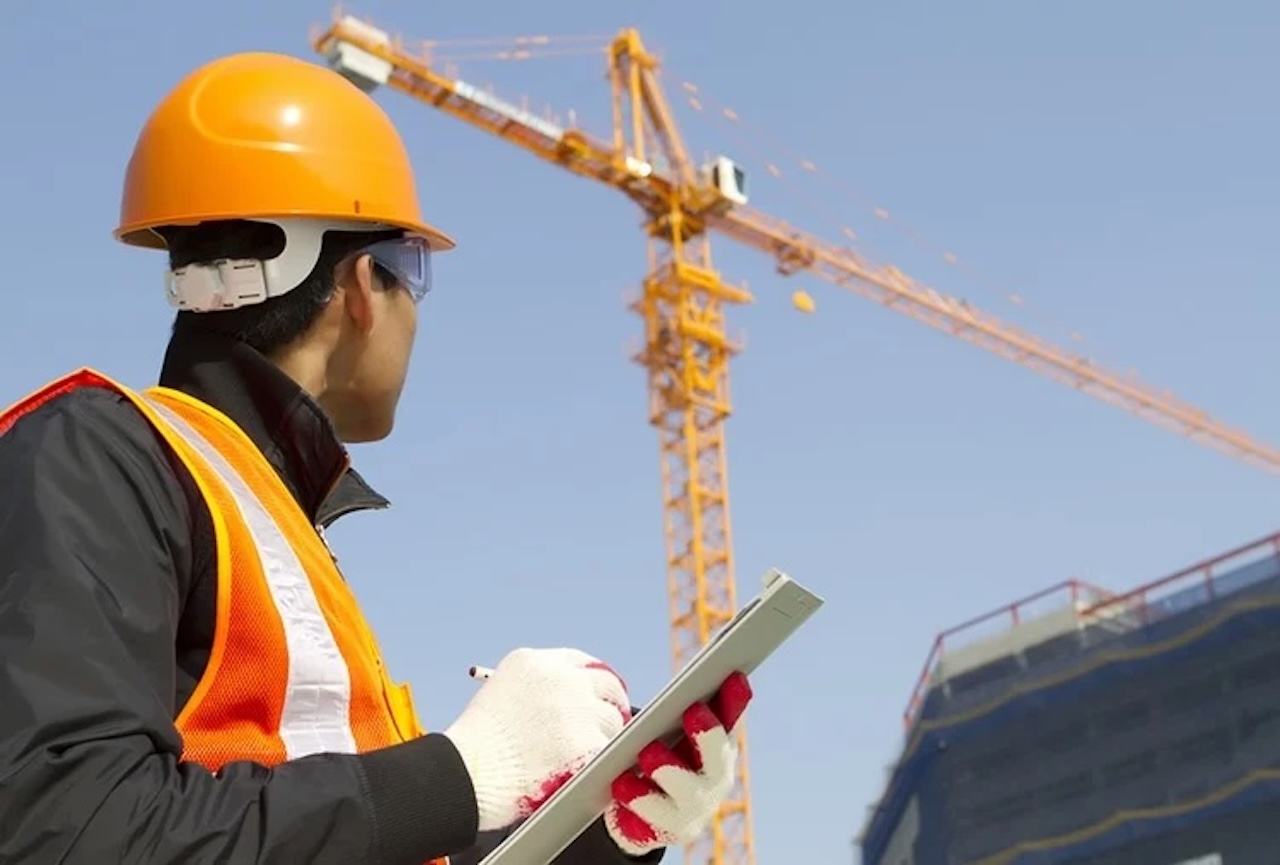
Building & Construction
What Does “ITP” Mean In Construction
Modified: December 7, 2023
Discover the meaning of "ITP" in the context of building construction. Explore the significance and implications of this term in the construction industry.
(Many of the links in this article redirect to a specific reviewed product. Your purchase of these products through affiliate links helps to generate commission for Storables.com, at no extra cost. Learn more)
Introduction
When it comes to construction projects, attention to detail is crucial for ensuring the safety and quality of the final outcome. One key aspect of this attention to detail is the implementation of an Inspection and Test Plan (ITP). In the world of construction, ITP stands for “Inspection and Test Plan,” a document that outlines the procedures and requirements for inspecting and testing various components during the construction process.
ITP is a systematic approach to quality control that aims to identify any defects or non-compliance with established standards early on in the construction project. By implementing an ITP, construction teams can mitigate risk, improve the overall quality of the project, and enhance client satisfaction.
So, what exactly does ITP entail in the context of construction projects? Let’s dive deeper into the definition of ITP and explore its importance, components, implementation, benefits, challenges, and best practices.
Key Takeaways:
- The Inspection and Test Plan (ITP) is a crucial document in construction, ensuring quality control, risk mitigation, and compliance with regulations. It enhances client satisfaction and provides evidence of accountability through comprehensive documentation.
- Implementing the ITP comes with challenges such as resource allocation, coordination, and technical expertise. By following best practices and addressing these challenges, construction teams can optimize the ITP’s effectiveness and maximize project success.
Definition of ITP in Construction
In the construction industry, an Inspection and Test Plan (ITP) is a document that outlines the specific steps and activities for inspecting and testing various components of a construction project. It serves as a roadmap for quality control and provides a clear framework for ensuring that all project requirements are met.
The ITP is typically developed during the planning phase of the project and is continuously updated throughout the construction process. It is prepared by the project team, which may include contractors, subcontractors, engineers, and quality control personnel. The document serves as a reference for all parties involved in the construction project, ensuring that everyone is on the same page regarding the necessary inspections and tests.
The ITP includes detailed information about the specific tests to be conducted, the equipment to be used, the acceptance criteria, and the responsible parties for each activity. It provides a step-by-step guide to ensure that all necessary inspections are carried out at the appropriate stages of the construction project.
By having a well-defined ITP in place, construction teams can ensure that all components, materials, and systems meet the required standards and specifications. It helps identify potential issues early on, allowing for timely resolutions and preventing costly rework or delays.
Moreover, the ITP also serves as a documentation tool, providing evidence of compliance with regulatory requirements and client specifications. This documentation is important during project audits, inspections, and handover processes.
Overall, the ITP is a vital document in construction projects, ensuring that quality standards are met, and the final outcome is safe, reliable, and of high quality.
Importance of ITP in Construction Projects
The Inspection and Test Plan (ITP) plays a crucial role in construction projects by ensuring the adherence to quality standards, minimizing risks, and enhancing project success. Here are some key reasons why ITP is important:
- Quality Control: The primary goal of ITP is to ensure the quality of the construction project. By clearly defining the required inspections and tests, the ITP helps identify any defects or non-compliance with the established standards early on, enabling prompt corrective actions. This ensures that the final outcome meets the desired quality standards.
- Risk Mitigation: Construction projects involve various risks, from safety hazards to structural issues. The ITP helps identify potential risks and ensures that the necessary inspections and tests are conducted to mitigate these risks. By addressing any issues in a timely manner, the ITP helps prevent costly rework, project delays, and potential safety hazards.
- Compliance with Regulations and Standards: Construction projects are subject to numerous regulations and industry standards. The ITP serves as a roadmap for ensuring compliance with these requirements. It outlines the specific inspections and tests necessary to meet the applicable regulations and standards, ensuring that all legal and regulatory obligations are fulfilled.
- Client Satisfaction: When clients invest in construction projects, they have certain expectations regarding the quality and safety of the final outcome. The ITP helps in meeting these expectations by meticulously inspecting and testing all project components. By adhering to the ITP, construction teams can demonstrate their commitment to delivering a high-quality project, leading to greater client satisfaction.
- Documentation and Accountability: The ITP serves as a comprehensive document that provides a record of all inspections and tests conducted throughout the construction process. This documentation is crucial for proving compliance with regulatory requirements, resolving any disputes, and facilitating proper handover processes. It also holds the responsible parties accountable for their roles and obligations.
Overall, the ITP is of utmost importance in construction projects as it ensures quality control, risk mitigation, regulatory compliance, client satisfaction, and proper documentation. By implementing a well-designed ITP, construction teams can optimize project outcomes and deliver successful projects that meet the highest standards of quality and safety.
Components of ITP
An effective Inspection and Test Plan (ITP) consists of several key components, each playing a vital role in ensuring the quality and compliance of the construction project. Here are the main components of an ITP:
- Objective and Scope: This section outlines the overall objective of the ITP and defines its scope. It clarifies the purpose of inspections and tests and sets the expectations for compliance with regulations, standards, and project requirements.
- Inspection Points: In this component, the various stages of the construction project are identified, and the specific inspection points are listed. Each inspection point corresponds to a critical stage where the quality and compliance need to be assessed. For example, inspection points could include foundation inspections, structural inspections, and finishing inspections.
- Testing Procedures: This section describes the specific tests that need to be performed at each inspection point. It includes details such as test specifications, methods, equipment, and acceptance criteria. Examples of tests may include materials testing, load testing, and non-destructive testing.
- Responsibilities and Authorities: Here, the individuals or parties responsible for conducting the inspections and tests are defined. This component clarifies the roles and responsibilities of the contractor, subcontractors, engineers, and quality control personnel involved in the project. It ensures accountability and clear lines of authority for each inspection activity.
- Acceptance Criteria: This component establishes the criteria or standards that must be met for each inspection point and test. It sets the benchmarks and thresholds for evaluating the quality and compliance of the construction project. These criteria may be based on regulations, industry standards, or project-specific requirements.
- Documentation: The ITP should specify the necessary documentation to be maintained for each inspection and test. This includes recording the results, maintaining certificates and permits, and organizing reports. Proper documentation ensures transparency, traceability, and evidence of compliance with the quality control measures.
- Audit and Review: In this component, provisions are made for regular audits and reviews of the ITP. It ensures that the ITP remains up to date, and any necessary adjustments are made based on feedback, lessons learned, or changes in regulations or project requirements. Audits and reviews help maintain the effectiveness and relevance of the ITP throughout the construction process.
These components together provide a comprehensive framework for conducting inspections and tests, ensuring the quality, compliance, and successful completion of the construction project. Adhering to the ITP’s components can help identify potential issues early on, facilitate timely resolution, and contribute to a high-quality final outcome.
Implementation of ITP in Construction Projects
The successful implementation of an Inspection and Test Plan (ITP) in construction projects requires careful planning, coordination, and execution. Here are the key steps involved in implementing the ITP:
- Developing the ITP: The first step is to develop a comprehensive ITP during the planning phase of the construction project. This involves defining the project scope, identifying critical inspection points, determining the necessary tests, and establishing acceptance criteria. All relevant stakeholders, including contractors, subcontractors, engineers, and quality control personnel, should collaborate to create the ITP.
- Communicating the ITP: Once the ITP is developed, it is crucial to communicate and distribute it to all parties involved in the construction project. This ensures that everyone is aware of the inspection and testing requirements and understands their roles and responsibilities. Effective communication helps prevent misunderstandings and ensures a smooth implementation of the ITP.
- Training and Education: It is essential to provide adequate training and education to personnel involved in implementing the ITP. This includes familiarizing them with the inspection procedures, testing methods, and acceptance criteria defined in the ITP. Training ensures that individuals understand the required quality standards and know how to conduct inspections and tests accurately.
- Implementing Inspections and Tests: Construction teams should follow the ITP guidelines meticulously and conduct inspections and tests at the designated inspection points. This involves using the specified equipment and following the prescribed procedures to evaluate the quality and compliance of the construction project. Accurate record-keeping and documentation of the inspection results are crucial during this step.
- Evaluating Results and Taking Corrective Actions: After conducting the inspections and tests, the results need to be evaluated against the acceptance criteria defined in the ITP. If any deviations or non-compliance are identified, prompt corrective actions should be taken to rectify the issues. This may involve reworking a specific component, adjusting construction methods, or addressing any other deficiencies.
- Monitoring and Auditing: Throughout the construction process, continuous monitoring and auditing of the implementation of the ITP are essential. This ensures that the ITP is being followed correctly and that the required inspections and tests are conducted timely. Audits help identify any gaps or areas for improvement and facilitate necessary adjustments to enhance the effectiveness of the ITP.
- Documentation and Reporting: Complete and accurate documentation of the inspections, tests, and results is crucial. This includes maintaining records of compliance, non-conformities, and corrective actions taken. Detailed reports should be prepared to provide evidence of adherence to quality control measures and to fulfill any regulatory and client requirements.
By following these implementation steps, construction teams can ensure the effective execution of the ITP and achieve the desired quality and compliance in the construction project. Regular communication, training, monitoring, and documentation contribute to a seamless implementation process and elevate the overall success of the project.
ITP in construction stands for “Inspection and Test Plan.” It is a document that outlines the procedures and requirements for inspecting and testing materials and workmanship on a construction project. It helps ensure that the project meets quality standards.
Read more: What Does “Level” Mean In Construction
Benefits of Following ITP Guidelines
Implementing an Inspection and Test Plan (ITP) in construction projects brings numerous benefits that contribute to the overall success of the project. Here are the key advantages of following ITP guidelines:
- Ensuring Quality Control: The primary benefit of following ITP guidelines is ensuring the quality of the construction project. By conducting thorough inspections and tests at designated inspection points, construction teams can identify potential defects, non-compliance, or deviations from desired standards. This allows for prompt corrective actions, minimizing rework, and ensuring that the final outcome meets the required quality standards.
- Minimizing Risks and Issues: Following ITP guidelines helps mitigate risks and minimize potential issues in the construction project. By identifying and addressing issues early on, construction teams can prevent costly rework, project delays, and safety hazards. This proactive approach reduces the likelihood of accidents, structural failures, and other construction-related risks that could impact project success.
- Meeting Regulatory Requirements: Construction projects are subject to various regulations and industry standards. The ITP ensures compliance with these requirements by defining the necessary inspections and tests to meet regulatory standards. Following ITP guidelines helps construction teams avoid legal and regulatory violations, potential fines, and project setbacks related to non-compliance.
- Enhancing Client Satisfaction: Implementing ITP guidelines demonstrates a commitment to quality and client satisfaction. By following the ITP, construction teams can deliver a high-quality project that meets client expectations. This enhances client satisfaction, builds trust, and increases the likelihood of future project opportunities and positive references.
- Documentation and Accountability: Following ITP guidelines ensures proper documentation of inspections, tests, and results. This provides a transparent record of compliance and quality control measures. Detailed documentation helps in audits, inspections, and handover processes, facilitating accountability among all parties involved in the construction project.
- Continuous Improvement: Following ITP guidelines encourages a culture of continuous improvement. Regular monitoring, auditing, and evaluation of the implementation process help identify areas for improvement. Lessons learned can be incorporated into future projects, enhancing construction practices, and ultimately leading to improved project outcomes.
By adhering to ITP guidelines, construction teams can maximize the benefits of quality control, risk mitigation, regulatory compliance, client satisfaction, documentation, and continuous improvement. These benefits contribute to the successful completion of construction projects, promoting long-term success and maintaining a solid reputation within the industry.
Challenges in Implementing ITP
While the implementation of an Inspection and Test Plan (ITP) brings significant benefits to construction projects, it also comes with certain challenges. Recognizing and addressing these challenges is crucial for successful ITP implementation. Here are some common challenges faced during the implementation process:
- Lack of Awareness and Understanding: One challenge is the lack of awareness and understanding of the importance and purpose of an ITP. Some members of the construction team may not fully comprehend the value of following the ITP guidelines, leading to resistance or incomplete implementation.
- Resource Allocation: Implementing the ITP requires adequate allocation of resources, including personnel, equipment, and time. Allocating the right resources and ensuring their availability throughout the project is essential for seamless implementation. Limited resources or conflicts with other project priorities may hinder effective implementation.
- Coordination and Communication: The effective coordination and communication among various stakeholders are critical for successful ITP implementation. Lack of clear communication or misalignment of expectations between contractors, subcontractors, engineers, and quality control personnel can lead to delays, misunderstandings, and errors in the implementation process.
- Monitoring and Compliance: Ensuring consistent monitoring and compliance with the ITP can be challenging, especially on large-scale construction projects. Without proper supervision, some inspections and tests may be missed or skipped, compromising the overall quality of the project. Regular monitoring and robust quality control systems are necessary to overcome this challenge.
- Adaptability to Changes: Construction projects often experience changes in design, schedules, or materials throughout the process. These changes can pose challenges in implementing the initial ITP, as adjustments may be required to accommodate new requirements. Flexibility and adaptability in modifying the ITP can help address these challenges and ensure ongoing compliance.
- Technical Expertise: Carrying out inspections and tests requires a certain level of technical expertise. Adequate training and knowledge are necessary for conducting accurate assessments and interpreting the results. If the project team lacks the required technical expertise, it can lead to improper inspections, inaccurate results, and compromised quality control.
- Documentation and Record-Keeping: Maintaining comprehensive and accurate documentation throughout the implementation process can be challenging. Multiple inspections, tests, and results need to be properly recorded and organized. Inadequate documentation can lead to difficulties in demonstrating compliance, lack of traceability, and potential issues during audits or handover processes.
Addressing these challenges requires a proactive approach, effective communication, ongoing training, and robust quality control systems. By recognizing and mitigating these challenges, construction teams can successfully implement the ITP, ensuring quality, compliance, and project success.
Best Practices for ITP in Construction
To ensure the effective implementation of an Inspection and Test Plan (ITP) in construction projects, certain best practices can be followed. These practices help maximize the benefits of the ITP and contribute to the overall success of the project. Here are some key best practices for ITP in construction:
- Early Planning and Development: Begin the development of the ITP early in the project planning phase. Involve all relevant stakeholders, including contractors, subcontractors, engineers, and quality control personnel, to ensure comprehensive input and alignment of expectations.
- Clear and Comprehensive Documentation: Create a clear and comprehensive ITP document that outlines the specific inspections, tests, procedures, acceptance criteria, and responsible parties. Clearly communicate the requirements, as well as the roles and responsibilities of each individual involved.
- Effective Communication and Collaboration: Establish open and effective communication channels among all stakeholders. Regularly communicate and collaborate to ensure a shared understanding of the ITP, address any concerns or uncertainties, and promote cooperation throughout the implementation process.
- Training and Education: Provide adequate training and education to personnel involved in implementing the ITP. Ensure that they fully understand the inspection processes, testing methods, and acceptance criteria. Regularly update training to keep up with changes in regulations and industry standards.
- Consistent Monitoring and Auditing: Continuously monitor the implementation of the ITP to ensure compliance with the established guidelines. Regularly conduct internal audits to identify gaps, make necessary improvements, and ensure ongoing compliance with quality control measures.
- Adaptability to Changes: Remain flexible and adaptable to changes that may occur throughout the construction project. Review the ITP and make necessary adjustments to accommodate new requirements, design modifications, or schedule changes. Maintain clear communication with all stakeholders regarding any updates to the ITP.
- Proper Record-Keeping: Maintain comprehensive and accurate documentation of all inspections, tests, and results. Use a standardized system for record-keeping to ensure consistency and ease of access. This documentation serves as evidence of compliance, assists in audits, and facilitates handover processes.
- Continuous Improvement Culture: Foster a culture of continuous improvement within the construction project. Encourage feedback from all stakeholders and incorporate lessons learned into future projects. Regularly review and update the ITP based on feedback, technological advancements, and changes in regulations or industry best practices.
By following these best practices, construction teams can optimize the implementation of the ITP, ensure quality control, mitigate risks, and enhance project success. Effective planning, clear communication, ongoing training, and continuous improvement contribute to a seamless and effective ITP implementation.
Conclusion
The implementation of an Inspection and Test Plan (ITP) is critical in the construction industry to maintain quality, mitigate risks, and achieve project success. The ITP serves as a roadmap, guiding construction teams through the necessary inspections and tests to ensure compliance with regulations, adherence to standards, and the delivery of a high-quality final outcome.
By following ITP guidelines, construction teams can identify potential issues early on, address non-compliance promptly, and minimize costly rework and project delays. The ITP also helps meet regulatory requirements, enhances client satisfaction, and provides documented evidence of compliance and accountability.
However, implementing the ITP does come with challenges. Overcoming these challenges requires awareness, effective communication, resource allocation, monitoring, technical expertise, and comprehensive documentation. By addressing these challenges and following best practices, construction teams can optimize the implementation of the ITP, ensuring its effectiveness and maximizing project success.
In conclusion, the ITP is a valuable tool in construction projects, central to ensuring quality control, risk mitigation, compliance, and client satisfaction. By meticulously following the ITP guidelines, construction teams can achieve a safe, reliable, and high-quality final outcome, establishing a solid reputation within the industry and setting the stage for future success.
Frequently Asked Questions about What Does "ITP" Mean In Construction
Was this page helpful?
At Storables.com, we guarantee accurate and reliable information. Our content, validated by Expert Board Contributors, is crafted following stringent Editorial Policies. We're committed to providing you with well-researched, expert-backed insights for all your informational needs.
0 thoughts on “What Does “ITP” Mean In Construction”