Home>diy>Building & Construction>What Are Some Safety Regulations And Rules That Should Be Followed When Working In Construction?
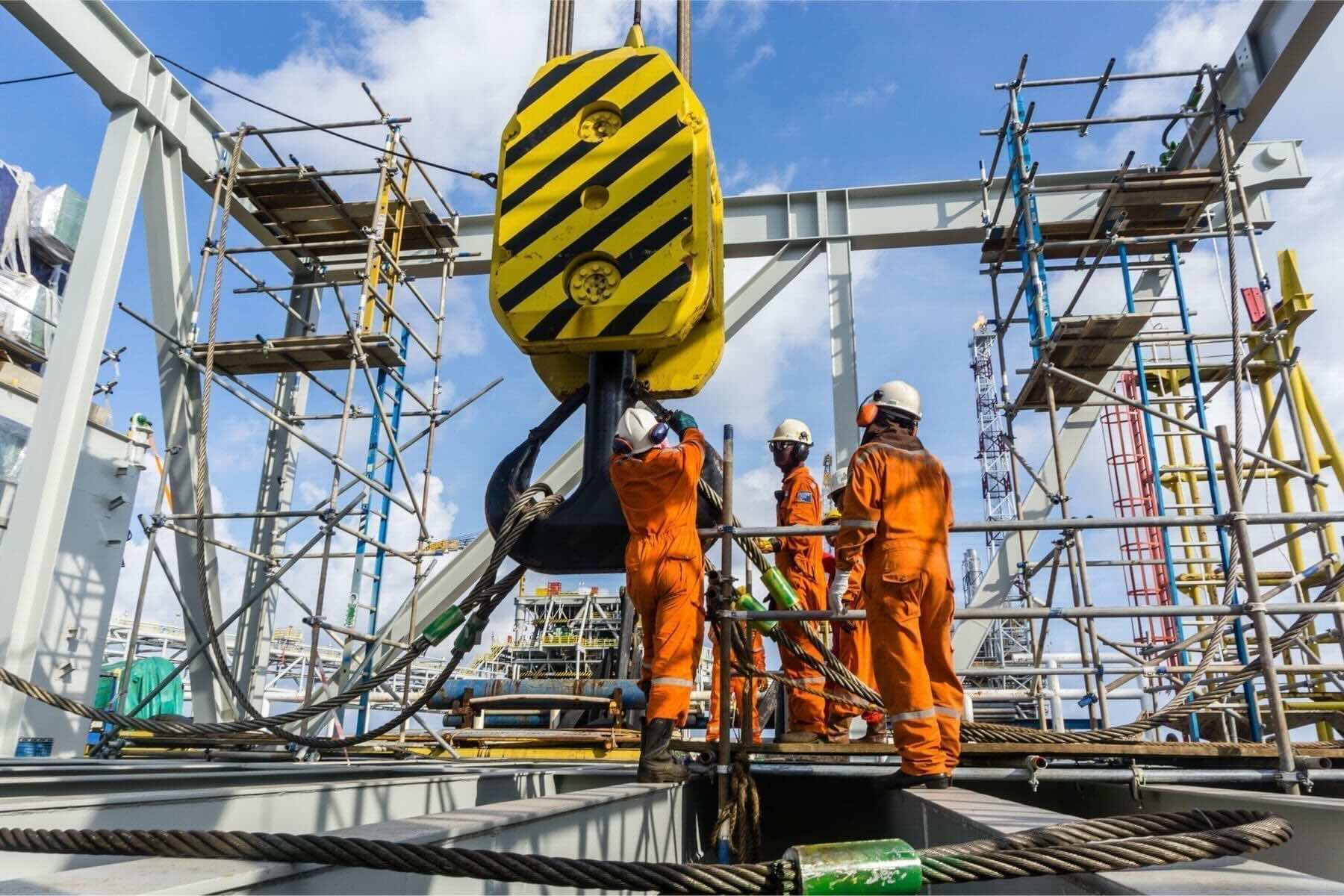
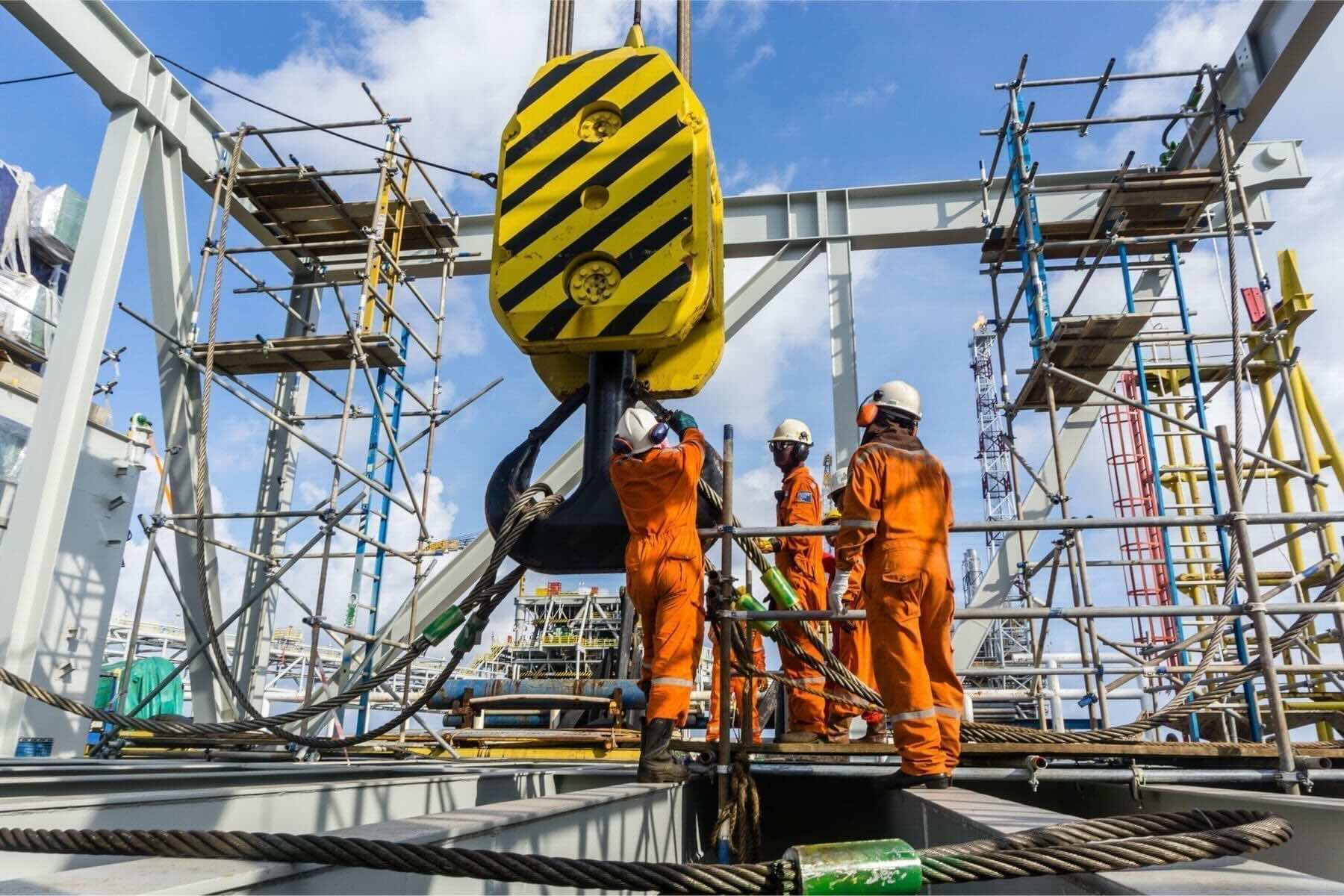
Building & Construction
What Are Some Safety Regulations And Rules That Should Be Followed When Working In Construction?
Modified: January 3, 2024
Discover the essential safety regulations and rules to adhere to when working in building construction. Protect yourself and others with proper precautions and guidelines.
(Many of the links in this article redirect to a specific reviewed product. Your purchase of these products through affiliate links helps to generate commission for Storables.com, at no extra cost. Learn more)
Introduction
Welcome to the exciting world of construction! As a construction professional, you have the opportunity to contribute to the creation of remarkable structures that shape our cities and communities. However, amidst the hustle and bustle of construction sites, it’s crucial to prioritize safety. Those working in the construction industry must adhere to stringent safety regulations and rules to ensure the wellbeing of everyone involved.
Safety regulations in construction are not mere suggestions but are vital for preventing accidents, reducing injuries, and even saving lives. These regulations are put in place to minimize hazards, promote safe work practices, and create a secure environment for workers, visitors, and the surrounding community.
In this article, we will explore some of the essential safety regulations and rules that should be followed when working in construction. Whether you’re a seasoned construction professional or just beginning your journey in the industry, understanding and implementing these regulations is of utmost importance.
From personal protective equipment to fall protection measures, electrical safety to excavation procedures, we will cover a wide range of areas to ensure a comprehensive overview of construction site safety. So, let’s delve into the details and learn how to create a safer work environment for yourself and everyone around you.
Key Takeaways:
- Prioritizing safety in construction is crucial for protecting workers, preventing accidents, and enhancing productivity and reputation. Adhering to regulations and guidelines creates a culture of awareness and responsibility.
- From personal protective equipment to fire prevention, comprehensive safety measures are essential for creating a secure working environment in construction. Prioritizing safety is a collective commitment for a safer future.
Read more: What Is The 4 To 1 Rule When Using A Ladder
Importance of Safety Regulations in Construction
Safety regulations play a vital role in the construction industry, ensuring the protection of workers and the prevention of accidents and injuries. Here are some reasons why safety regulations are of utmost importance in construction:
- Worker Safety: The primary objective of safety regulations in construction is to safeguard the wellbeing of workers. Construction sites are inherently hazardous environments, with potential risks such as falls, electrocution, and exposure to harmful substances. By implementing and following safety regulations, workers can minimize these risks and perform their tasks with greater peace of mind.
- Accident Prevention: Construction accidents not only lead to injuries and fatalities but also result in project delays, financial losses, and damage to a company’s reputation. Safety regulations act as a proactive measure to prevent accidents by identifying potential hazards and implementing necessary precautions to mitigate them. By adhering to these regulations, construction companies can significantly reduce the risk of accidents on their sites.
- Legal Compliance: Construction companies have a legal and ethical responsibility to ensure the safety and wellbeing of their workers. Safety regulations are enforced by government agencies to ensure compliance with industry standards and best practices. Failure to adhere to these regulations can result in legal repercussions, including fines, penalties, and even the suspension of construction operations.
- Productivity and Cost Savings: Implementing safety regulations can actually enhance productivity on construction sites. When workers feel safe and protected, they can focus on their tasks without distractions or anxieties about potential hazards. Additionally, by preventing accidents and injuries, construction companies can avoid costly medical expenses, workers’ compensation claims, and project delays, leading to significant cost savings in the long run.
- Enhanced Reputation: Safety-conscious construction companies are viewed favorably by clients, employees, and stakeholders. Prioritizing safety not only demonstrates a commitment to the well-being of workers but also enhances the company’s reputation as a reliable and responsible construction contractor. This can lead to increased client satisfaction, repeat business, and improved relationships with regulatory authorities and industry partners.
Overall, safety regulations are essential in the construction industry for the protection of workers, prevention of accidents, legal compliance, productivity, cost savings, and reputation enhancement. By prioritizing safety, construction companies can create a culture of awareness and responsibility, making construction sites safer and more harmonious environments for all.
Personal Protective Equipment (PPE) Requirements
When working in the construction industry, personal protective equipment (PPE) is essential for ensuring the safety and well-being of workers. PPE refers to the gear and equipment designed to protect against various hazards present on construction sites. Here are some common types of PPE and their importance:
- Hard Hats: Hard hats are a fundamental piece of PPE, providing protection against falling objects, head injuries, and electrical hazards. They should be worn by all workers on site, especially those working at heights or in areas where objects may fall or fly.
- Safety Glasses or Goggles: Eye protection is critical on construction sites to prevent injuries from flying debris, chemicals, dust, or projectiles. Safety glasses or goggles with impact-resistant lenses should be worn whenever there is a risk of eye hazards.
- Ear Protection: Construction sites can be noisy environments, exposing workers to the risk of hearing loss. Ear protection, such as earmuffs or earplugs, should be worn whenever noise levels exceed safe limits.
- Respiratory Protection: Construction activities can release harmful particles, dust, or fumes that can be hazardous to the respiratory system. Depending on the nature of the work, respiratory protection, such as dust masks or respirators, should be worn to prevent inhalation of harmful substances.
- High-Visibility Clothing: Workers in construction must be visible to others on site, especially in situations where there is vehicular traffic or potential for accidents. High-visibility clothing, such as reflective vests, enhances visibility and reduces the risk of collisions or accidents.
- Gloves: Hand injuries are common in construction, with risks ranging from cuts and abrasions to chemical exposure and thermal hazards. Gloves should be worn to protect against these hazards and must be selected based on the specific tasks and materials involved.
- Protective Footwear: Construction sites often have various hazards, including heavy objects, slippery surfaces, and sharp materials. Safety boots or shoes with reinforced toes and slip-resistant soles should be worn to protect the feet from falling objects, punctures, and slips or trips.
It is important to note that PPE alone is not sufficient to ensure safety on construction sites. Proper fit, maintenance, and regular inspection of PPE are crucial. Workers should be trained on the appropriate use, care, and limitations of their PPE. Additionally, employers must provide the necessary PPE free of charge and ensure its availability and suitability for the tasks being performed.
Personal protective equipment is a vital aspect of construction site safety. By diligently wearing and maintaining the required PPE, workers can significantly reduce the risk of injuries and illnesses, creating a safer working environment for everyone involved.
Fall Protection Measures
Falls are one of the most common and serious hazards in the construction industry. The risk of falls significantly increases when working at heights, such as on roofs, scaffolds, ladders, or elevated platforms. To prevent fall-related accidents and injuries, construction sites must implement effective fall protection measures. Here are some essential fall protection guidelines:
- Fall Arrest Systems: Fall arrest systems are designed to stop a worker’s fall mid-air and minimize the impact. They typically consist of a full-body harness, an anchor point, and a lifeline or lanyard. Workers must be trained on the proper use and inspection of fall arrest systems and should always connect themselves to a secure anchor point before working at heights.
- Scaffolding Safety: Scaffolding is commonly used in construction, but it poses significant fall risks if not properly erected and secured. Erecting scaffolding according to manufacturer instructions, inspecting it daily, and ensuring guardrails, toe boards, and mid-rails are in place can help prevent falls.
- Ladder Safety: Ladders should be used for their intended purpose and in accordance with manufacturers’ guidelines. Workers should inspect ladders for damage or defects and ensure they are stable and placed on a level surface before use. Additionally, using a ladder with the correct height and proper hand placement can help prevent falls.
- Guardrails and Barriers: Installing guardrails and barriers on elevated surfaces, open edges, and walkways can help prevent falls. These physical barriers provide a protective barrier and prevent accidental falls or unauthorized access to hazardous areas.
- Training and Education: Proper training and education are paramount in preventing falls. Workers should receive comprehensive training on fall protection measures, including hazard recognition, safe work practices, and the proper use of fall protection equipment. Regular refresher training should also be conducted to reinforce safety protocols.
- Supervision and Inspections: Site supervisors and managers should regularly inspect the work areas to ensure compliance with fall protection measures. They should also monitor workers to ensure proper usage of personal fall protection equipment and adherence to safety protocols.
It is crucial for construction companies to prioritize fall protection and consistently enforce safety regulations. By implementing comprehensive fall protection measures, providing proper training, and promoting a culture of safety, construction sites can significantly reduce the risk of falls and create a secure working environment for all.
Scaffolding Safety Guidelines
Scaffolding is a critical component in many construction projects, providing a platform for workers to access heights. However, working on scaffolds can be dangerous if proper safety precautions are not followed. To ensure the safety of workers, it is important to adhere to scaffolding safety guidelines. Here are some essential guidelines to consider:
- Scaffold Design: Scaffolds should be designed by qualified professionals and erected according to manufacturer specifications and local regulations. The structure should be capable of supporting the intended load and properly braced to prevent swaying or collapse.
- Training and Competency: Workers who erect, dismantle, and work on scaffolds should receive appropriate training and demonstrate competency in scaffold-related tasks. They should be familiar with scaffold components, inspection procedures, and safe use practices.
- Inspections: Regular inspections are necessary to ensure the integrity and stability of scaffolding. A competent person should inspect the scaffold before each work shift, looking for any signs of damage, instability, or missing components. Additionally, formal inspections should be conducted at least every 7 days or after any significant changes or adverse weather conditions.
- Platform Stability: The scaffold platform should be stable, level, and fully planked to provide a safe working surface. The platform should be free of debris, tools, or materials that may cause tripping hazards or instability.
- Guardrails and Toe Boards: Proper guardrails, mid-rails, and toe boards must be installed on all open sides and ends of the scaffold platform that are 10 feet or higher above the ground. These barriers prevent falls and provide fall protection to workers.
- Access and Egress: Safe access and egress routes should be clearly defined and maintained. Scaffolds should have properly positioned ladders, stairs, or ramps to ensure workers can safely climb up and down without the risk of slips or falls.
- Weather Conditions: Adverse weather conditions, such as high winds, rain, or ice, can compromise the stability of scaffolding. Therefore, scaffolds should not be used during severe weather conditions, and workers should be trained to recognize and react to changing weather conditions that may affect scaffold stability.
- Personal Protective Equipment (PPE): Workers on scaffolds should wear appropriate PPE, including hard hats, high-visibility clothing, and fall protection equipment if working at heights. Additionally, tool lanyards should be used to prevent tools and equipment from falling and causing injury to workers below.
By following these scaffolding safety guidelines, construction companies can enhance the safety of workers and reduce the risk of accidents and injuries associated with working on scaffolds. Remember, safety is a collective effort, and everyone involved in the construction process must prioritize and adhere to these guidelines to create a secure working environment.
Electrical Safety Precautions
Electrical safety is of utmost importance in the construction industry due to the inherent risks associated with working with electricity. Taking appropriate precautions can prevent electrocution, electrical shocks, fires, and other electrical hazards. Here are some essential electrical safety precautions to follow on construction sites:
- Qualified Personnel: Only qualified electricians or trained personnel should perform electrical work, installations, or repairs. It is vital to have a thorough understanding of electrical systems, codes, and safety procedures when working with electricity.
- Lockout/Tagout: Before working on electrical systems or equipment, proper lockout/tagout procedures should be followed to isolate and de-energize the circuit. This ensures that unintended energization does not occur, preventing electrical accidents.
- Ground Fault Circuit Interrupters (GFCIs): GFCIs are essential in areas where electricity and water may come into contact, such as bathrooms, kitchens, or outdoor workspaces. GFCIs immediately shut off the circuit when a ground fault is detected, preventing electrical shocks and electrocutions.
- Proper Wiring and Overload Avoidance: Electrical wiring and circuits should be installed by qualified professionals and meet the appropriate codes and standards. Overloading circuits can lead to overheating, fires, or equipment damage. Proper load calculations should be performed to ensure that circuits can handle the electrical demands.
- Inspection and Maintenance: Regular inspection and maintenance of electrical systems and equipment are crucial for identifying potential hazards, damaged wiring, or faulty devices. It is essential to replace or repair any damaged or worn-out components promptly.
- Use of Grounding and Bonding: Proper grounding and bonding of electrical systems minimize the risk of electrical shocks and mitigates the potential for voltage surges. Grounding ensures that electrical faults are safely redirected to the ground, protecting workers from electric shock.
- Personal Protective Equipment (PPE): Workers engaged in electrical work or working in proximity to live electrical systems should wear appropriate PPE. This may include insulated gloves, rubber-soled shoes, arc-rated clothing, and face shields, depending on the level of electrical exposure.
- Avoiding Overhead Power Lines: Workers should be vigilant and maintain safe distances from overhead power lines. Extending equipment or conducting work near power lines increases the risk of electrical contact and can lead to severe injuries or fatalities.
- Proper Use of Tools and Equipment: Only use tools and equipment that are designed for electrical work and are in good working condition. Insulated handles and grips on tools can help protect against electric shocks. Avoid using damaged or frayed cords, and ensure all connections are secure.
- Training and Awareness: Proper training on electrical safety is essential for all construction workers. They should be aware of potential electrical hazards, know how to use electrical equipment safely, and understand emergency procedures in case of electrical accidents.
Implementing these electrical safety precautions on construction sites can significantly reduce the risk of electrical accidents and protect the well-being of workers. Construction companies should prioritize electrical safety and provide ongoing training and reminders to ensure that all workers are aware of and follow these precautions diligently.
Always wear the appropriate personal protective equipment (PPE) such as hard hats, gloves, and safety glasses. Follow all safety protocols and procedures, and never take shortcuts.
Use of Heavy Machinery and Equipment Safely
Heavy machinery and equipment are integral to construction projects, but they can pose significant risks if not operated and handled safely. To ensure the well-being of workers and prevent accidents, it is essential to follow safety guidelines when using heavy machinery and equipment. Here are some key considerations:
- Proper Training and Certification: Operators of heavy machinery and equipment should receive comprehensive training on their proper operation and safety guidelines. It is crucial to ensure that operators are certified and have a thorough understanding of the specific machine they are operating.
- Read and Follow Manufacturer’s Instructions: Each piece of heavy machinery and equipment comes with specific operating instructions and safety guidelines from the manufacturer. It is essential to read and understand these instructions before use and follow them diligently to ensure safe operation.
- Pre-Use Inspections: Conduct thorough inspections of heavy machinery and equipment before each use. Check for any signs of damage, malfunction, or wear and tear. Ensure that all safety features and controls are in working order.
- Maintain Safe Clearances: Maintain safe distances from other workers, obstacles, overhead power lines, and other hazards when operating heavy machinery. Be mindful of blind spots and use designated signals or communication systems to ensure the safety of everyone on the construction site.
- Use Personal Protective Equipment (PPE): Operators of heavy machinery should wear appropriate PPE, including high-visibility clothing, hard hats, safety glasses, and gloves. Additionally, operators should secure the seat belt or harness provided in the machine for added protection.
- Follow Load Capacity Guidelines: Heavy machinery and equipment have specific load capacity limits. Exceeding these limits can lead to loss of control, tipping, or structural failure. Always ensure that loads are within the approved limits and properly secured before moving or lifting.
- Safe Exiting and Parking: When leaving or parking heavy machinery, ensure that it is on stable ground, the engine is turned off, and the parking brake is engaged. Lower any lifting arms, buckets, or attachments to the ground and secure the equipment to prevent accidental movement.
- Regular Maintenance and Inspection: Regular maintenance and inspections are crucial to ensuring the safe and efficient operation of heavy machinery and equipment. Follow the manufacturer’s recommended maintenance schedules, and promptly address any issues or malfunctions to prevent potential accidents.
- Communication and Awareness: Maintain clear and effective communication between operators, ground workers, and other personnel on the construction site. Use hand signals, radios, or other forms of communication to ensure everyone is aware of the movements and actions of the machinery.
- Adhere to OSHA and Regulatory Standards: Construction companies must be familiar with and adhere to the Occupational Safety and Health Administration (OSHA) and other regulatory standards pertaining to the safe operation of heavy machinery and equipment. These standards provide guidelines and best practices to ensure worker safety.
By following these safety guidelines, construction companies can promote a culture of safety and minimize the risk of accidents when using heavy machinery and equipment. Regular training, inspections, and maintenance, along with effective communication and adherence to regulatory standards, are essential in creating a safe working environment.
Hazard Communication and Material Safety Data Sheets (MSDS)
Hazard communication is a crucial aspect of construction site safety, ensuring that workers are informed about the hazards associated with the materials and substances they encounter. Material Safety Data Sheets (MSDS), also known as Safety Data Sheets (SDS), are an integral part of the hazard communication program. Here’s what you need to know:
Hazard Communication:
Hazard communication refers to the systems and processes in place to identify, evaluate, and communicate information about the hazards of chemical substances and materials in the workplace. It aims to provide workers with the necessary knowledge and understanding of potential hazards, safe handling procedures, and appropriate precautions to minimize risk.
Construction companies should have a comprehensive hazard communication program that includes:
- Chemical Inventory: Maintain an inventory of all chemicals and substances used on the construction site. This inventory should include information about the chemical composition, associated hazards, and specific handling requirements.
- Labeling: All containers with hazardous substances should be properly labeled, indicating the contents and any pertinent hazard warnings. Labels should be clear, visible, and easy to understand to ensure workers can identify potential hazards at a glance.
- Employee Training: Provide training to employees on the hazards associated with the chemicals they may encounter. This training should cover the proper use, handling, storage, and disposal of hazardous substances, as well as the use of personal protective equipment (PPE) when required.
- MSDS/SDS: Material Safety Data Sheets (MSDS) or Safety Data Sheets (SDS) are documents that provide detailed information about hazardous substances. These sheets contain information on the chemical composition, physical and health hazards, protective measures, emergency response procedures, and first aid considerations.
- Access to MSDS/SDS: Ensure that MSDS/SDS are readily accessible to all workers on the construction site. This can be in physical or digital format, but it is important that workers can easily access the information when needed.
Material Safety Data Sheets (MSDS):
Material Safety Data Sheets (MSDS) or Safety Data Sheets (SDS) provide workers with detailed information about hazardous substances, allowing them to understand the potential risks, proper handling procedures, and necessary protective measures. Key elements typically included in an MSDS/SDS are:
- Identification: Information about the substance, including its chemical name, synonyms, and common uses.
- Hazard Identification: Detailed information about the physical and health hazards associated with the substance, including potential effects of exposure and any special precautions to be taken.
- Composition: A breakdown of the chemical ingredients and composition of the substance.
- First Aid Measures: Instructions on appropriate first aid procedures for different types of exposures or accidents involving the substance.
- Fire-Fighting Measures: Recommendations on firefighting techniques and suitable extinguishing agents in case of a fire involving the substance.
- Handling and Storage: Specific instructions for the safe handling, storage, and disposal of the substance.
- Personal Protection: Recommended personal protective equipment (PPE) and precautions to be taken when working with or around the substance.
- Emergency Measures: Instructions on emergency response procedures, including spillage, leak, or accidental release of the substance.
- Regulatory Information: Information about regulations and standards applicable to the substance and its use.
MSDS/SDS provide vital information for workers to understand and mitigate the hazards associated with chemicals and substances used on construction sites. It is essential for construction companies to ensure that workers have access to and understand the information provided in the MSDS/SDS, enabling them to work safely and take appropriate precautions to protect themselves and others on site.
Excavation and Trenching Safety Procedures
Excavation and trenching are common activities in the construction industry but can be highly hazardous if proper safety procedures are not followed. It is important to implement specific safety measures to prevent cave-ins, falls, and other accidents that can occur during excavation work. Here are some key excavation and trenching safety procedures to help mitigate these risks:
- Proper Planning: Thoroughly plan the excavation project in advance, including assessing the soil conditions, determining the depth and width of the trench, and identifying any potential hazards. Develop an excavation plan that includes safety measures and strategies to mitigate risks.
- Protective Systems: Use appropriate protective systems, such as sloping, shoring, or shielding, to prevent cave-ins. The protective system should be based on the soil type and stability, and it should be designed by a competent person. Follow OSHA regulations and guidelines for protective systems.
- Trench Access and Egress: Ensure that safe means of access and egress are provided for workers in the trench. This may include ladders, ramps, or stairways placed within safe distances. Adequate lighting should be provided if work is being conducted during low-light conditions.
- Inspect the Trench: Regularly inspect the trench and surrounding areas, especially after rain, excavation activity, or any other events that may affect stability. Look for signs of water accumulation, soil movement, cracks, or other indications of potential hazards.
- Spoil and Materials: Keep excavated materials and other equipment at a safe distance from the trench edge to prevent collapse or falls. Follow proper procedures for disposing of excavated materials and ensure that they do not interfere with the safety of workers or the stability of the trench.
- Utility Awareness: Prior to excavation, identify and mark the location of underground utilities to prevent accidental damage. Contact the appropriate utility companies or utilize utility location services to ensure that underground utilities are located and properly protected.
- Safe Work Practices: Establish and enforce safe work practices for excavation and trenching. This includes the use of personal protective equipment (PPE), such as hard hats, high-visibility vests, and protective footwear. Train workers on proper excavation procedures, emergency protocols, and how to recognize and address potential hazards.
- Competent Personnel: Ensure that individuals involved in excavation and trenching work are competent and trained in the specific tasks they are performing. Competent workers should have a clear understanding of the hazards associated with excavation work and the necessary safety precautions to mitigate those risks.
- Emergency Response: Have a clearly defined emergency response plan in place for excavation and trenching work. This includes procedures for rescue operations in case of a cave-in or other emergencies. Keep emergency contact numbers visible and accessible to all workers on site.
- Regular Inspections and Documentation: Perform regular inspections of the excavation site and document the findings. This helps identify and address potential hazards promptly. Additionally, keep records of training, permits, inspections, and any incidents related to excavation and trenching work.
By following these excavation and trenching safety procedures, construction companies can significantly reduce the risk of accidents and ensure the safety of workers involved in these activities. Remember, excavation work requires careful planning, attention to detail, and adherence to safety guidelines to create a secure working environment.
Read more: What Should Follow Potatoes In Crop Rotation
Fire Prevention and Emergency Response Plans
Fire prevention and effective emergency response plans are crucial in construction sites to ensure the safety of workers, minimize property damage, and mitigate potential risks. Construction sites are susceptible to fire hazards due to the presence of flammable materials, electrical systems, and various ignition sources. Here are key considerations for fire prevention and emergency response:
- Fire Prevention Measures:
- Implement a fire prevention program that includes regular inspections, proper storage and handling of flammable materials, and adherence to local fire codes and regulations.
- Ensure there are properly maintained fire extinguishers and fire detection systems in accessible locations throughout the construction site.
- Properly dispose of flammable waste and debris to minimize fire risks.
- Conduct regular equipment maintenance to prevent electrical malfunctions and potentially hazardous situations.
- Establish clear protocols for smoking areas and ensure proper disposal of cigarette butts.
- Emergency Response Planning:
- Create an emergency response plan that includes procedures for evacuating construction workers and nearby personnel in case of a fire or other emergencies.
- Designate evacuation routes and assembly areas that are clear of potential hazards and easily accessible to all workers.
- Provide training to workers on emergency response procedures, including the proper use of fire extinguishers and the location of emergency exits and equipment.
- Establish communication protocols to promptly alert all workers to the emergency situation and facilitate a rapid response.
- Collaborate with local emergency services and inform them about the construction site’s location and potential hazards.
- Fire Safety Equipment and Systems:
- Ensure that fire safety equipment, such as fire extinguishers, fire suppression systems, smoke detectors, and fire alarms, are properly installed, regularly inspected, and maintained.
- Provide training to workers on how to operate fire extinguishers and additional fire suppression systems that may be present on the construction site.
- Regularly test fire alarm systems to ensure they are functional and immediately respond to any signals indicating fire or smoke.
- Clearly mark and maintain access to firefighting equipment and emergency exits, ensuring they are always accessible and unobstructed.
- Communication and Reporting:
- Encourage a culture of reporting and open communication regarding potential fire hazards. Workers should feel comfortable reporting any concerns or observations related to fire safety.
- Establish a designated person or team responsible for overseeing fire safety and ensuring compliance with fire prevention measures.
- Regularly review and update the fire prevention and emergency response plans as necessary to account for changes in the construction site layout, materials, or operational procedures.
By implementing comprehensive fire prevention measures, creating clear emergency response plans, and ensuring the availability and maintenance of fire safety equipment, construction companies can minimize the risk of fires and respond effectively in emergency situations. Prioritizing fire safety not only protects the construction site but also safeguards the lives of workers and contributes to the overall success of the project.
Conclusion
Safety is of paramount importance in the construction industry. Following the proper safety regulations and guidelines is essential to protect the well-being of workers and ensure a secure working environment. Throughout this article, we have explored various safety regulations and rules that should be followed when working in construction.
From personal protective equipment (PPE) requirements to fall protection measures, scaffolding safety guidelines to electrical safety precautions, and excavation and trenching safety procedures to fire prevention and emergency response plans, each topic is a crucial aspect of construction site safety.
Implementing these safety measures is not only a legal requirement but also a moral and ethical responsibility. Construction companies should prioritize the well-being of their workers, invest in comprehensive safety training, and enforce strict adherence to safety regulations. By doing so, they can create a culture of safety, reduce the risk of accidents, and enhance the overall productivity and success of construction projects.
Furthermore, effective communication, regular inspections, and ongoing training are key components of maintaining a safe working environment. Workers must be properly educated and trained on the potential hazards they might encounter in their daily tasks, as well as the appropriate safety protocols and procedures to follow.
Ultimately, construction sites can be challenging and high-risk environments, but with the right safety measures in place, accidents and injuries can be minimized or even prevented. By prioritizing safety at every stage of the construction process, we can ensure the well-being of workers, the completion of successful projects, and the continued growth and development of the construction industry.
Remember, safety is not just a checklist or a box to be ticked. It is a mindset, a commitment, and a responsibility that we all share in the construction industry. Let’s build a safer future, one construction site at a time.
Frequently Asked Questions about What Are Some Safety Regulations And Rules That Should Be Followed When Working In Construction?
Was this page helpful?
At Storables.com, we guarantee accurate and reliable information. Our content, validated by Expert Board Contributors, is crafted following stringent Editorial Policies. We're committed to providing you with well-researched, expert-backed insights for all your informational needs.
0 thoughts on “What Are Some Safety Regulations And Rules That Should Be Followed When Working In Construction?”