Home>diy>Building & Construction>What Does Precast Mean In Construction
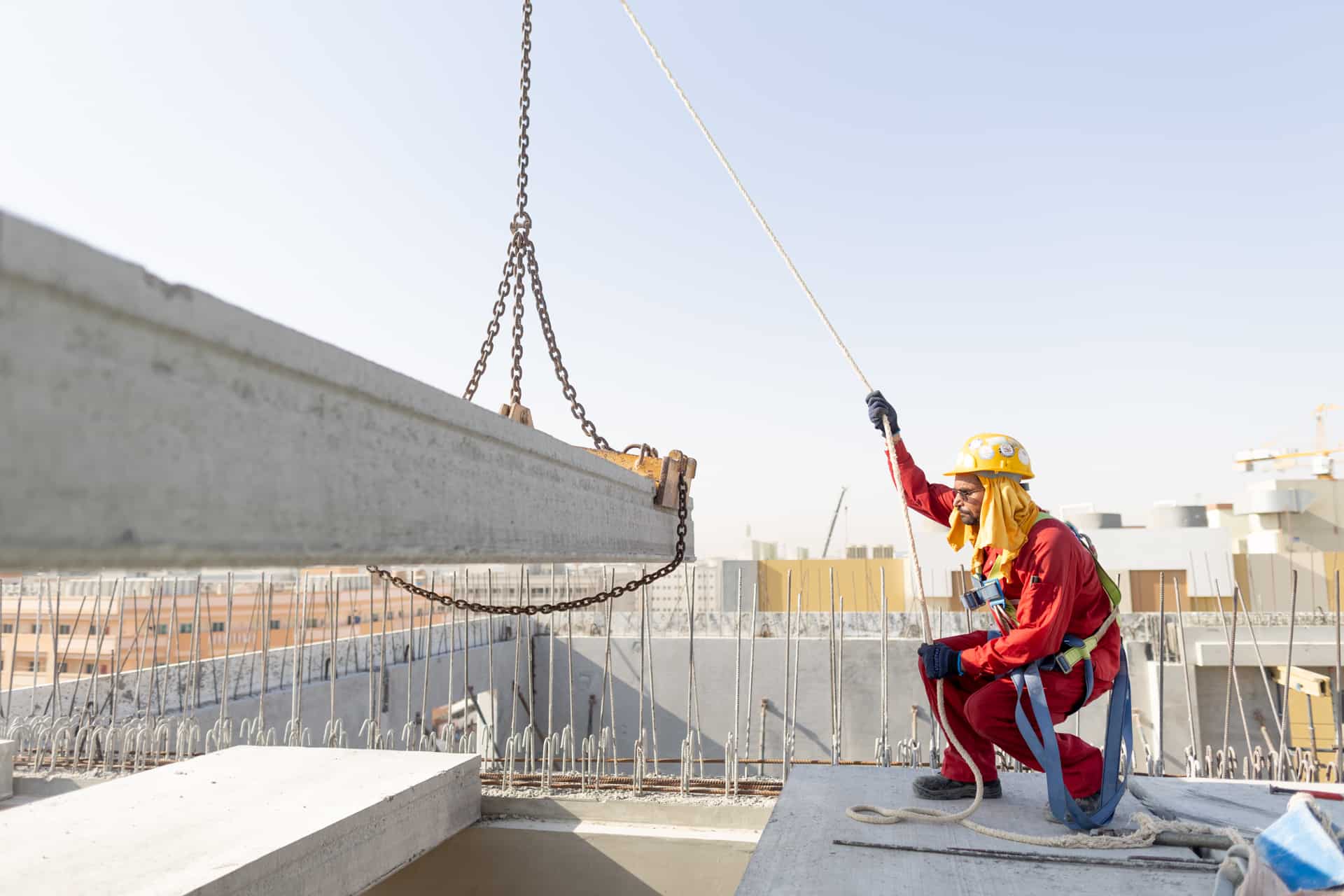
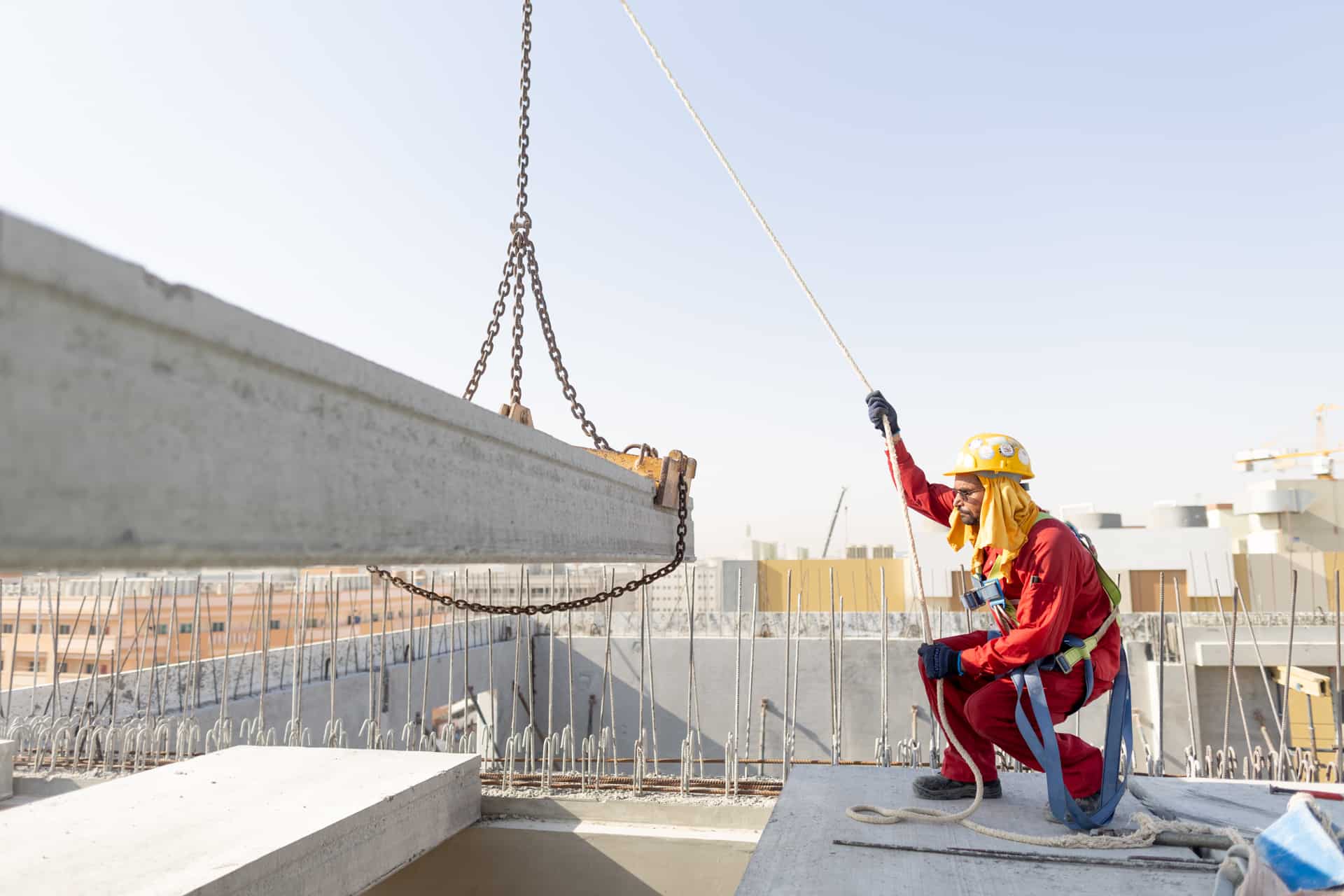
Building & Construction
What Does Precast Mean In Construction
Modified: December 7, 2023
Learn about the meaning of precast in building construction and how it benefits the construction process. Discover the advantages and applications of precast concrete.
(Many of the links in this article redirect to a specific reviewed product. Your purchase of these products through affiliate links helps to generate commission for Storables.com, at no extra cost. Learn more)
Introduction
When it comes to the construction industry, innovation and efficiency are always in high demand. One method that has gained significant popularity in recent years is precast construction. Harnessing the power of advanced manufacturing techniques, precast construction offers numerous benefits in terms of speed, quality, and sustainability.
Precast, as the name suggests, refers to the process of manufacturing building components offsite before they are transported and installed at the construction site. This method involves casting concrete or other materials into specific shapes and sizes to create highly durable and versatile elements. These precast components can range from walls, floors, and columns to facades, stairs, and even entire building modules.
What sets precast construction apart from traditional construction methods is its level of precision and efficiency. By optimizing the manufacturing process and utilizing modern technology, precast elements can be produced with exceptional accuracy and consistency. This not only ensures superior quality but also speeds up the overall construction process.
Additionally, precast construction offers several environmental benefits. The controlled manufacturing environment reduces waste generation, and the ability to reuse precast elements in different projects minimizes the use of raw materials. Moreover, the advanced techniques used in precast construction contribute to energy efficiency, making it a sustainable choice for the long term.
In this article, we will delve deeper into the world of precast construction. We will explore the various types of precast components, examine the manufacturing process, discuss the advantages and limitations of precast construction, and provide examples of successful precast projects. So, let’s dig in and uncover the wonders of precast construction!
Key Takeaways:
- Precast construction revolutionizes building with speed, quality, and sustainability. From iconic skyscrapers to modular housing, its design flexibility and durability shape the future of construction.
- Despite transportation challenges and initial investment, precast construction offers accelerated timelines, cost savings, and visually stunning structures. Its versatility and resilience drive the evolution of modern architecture.
Definition of Precast
Precast refers to a construction method where building components are manufactured offsite in a controlled environment before being transported and installed at the construction site. These components, also known as precast elements or precast concrete, are made by pouring concrete into molds or forms and allowing it to cure to achieve the desired shape and strength.
Precast elements are produced using a wide range of materials, including concrete, steel, glass-fiber reinforced concrete (GFRC), and pre-stressed concrete. The choice of material depends on the specific requirements of the project, such as load-bearing capacity, architectural design, and durability.
The use of precast elements offers several advantages over traditional construction methods. First and foremost, precast construction allows for greater precision and quality control. By manufacturing components in a factory setting, under optimal conditions, the risk of human error and environmental factors is significantly reduced. This results in higher-quality elements that are consistent in shape, size, and strength.
Furthermore, precast construction enables faster project completion. Since the components are manufactured offsite, the construction site can be prepared simultaneously, saving valuable time. Once the precast elements are ready, they can be quickly transported to the site and installed, reducing the overall construction duration.
Precast construction also offers flexibility and versatility in design. The use of molds allows for the creation of complex shapes and architectural details that would be difficult or time-consuming to achieve with traditional methods. Additionally, precast elements can be customized to meet specific project requirements, whether it’s for residential, commercial, or industrial purposes.
Overall, the definition of precast encompasses the innovative approach to construction that involves manufacturing building components offsite to achieve higher quality, efficiency, and design flexibility. By harnessing the advantages of precast construction, builders and developers can streamline their projects and deliver structures that are durable, sustainable, and visually appealing.
Benefits of Using Precast in Construction
Precast construction offers numerous benefits that make it an attractive choice for builders and developers. These advantages span across various aspects of the construction process, from design and manufacturing to installation and long-term performance. Let’s explore some of the key benefits of using precast elements:
- Speed and Efficiency: Precast construction significantly reduces project timelines. Since the components are manufactured offsite, construction activities can proceed simultaneously, minimizing delays. The precise manufacturing process ensures faster installation on-site, further accelerating project completion.
- Quality Control: The controlled environment of precast manufacturing facilities allows for rigorous quality control measures. Each element undergoes thorough testing and inspection, ensuring dimensional accuracy, strength, and durability. This results in higher quality components compared to traditional construction methods.
- Sustainability: Precast construction aligns with sustainable building practices. The manufacturing process optimizes the use of materials, minimizing waste generation. Precise production reduces excess use of resources, and the ability to reuse precast elements in different projects enhances their environmental impact.
- Design Flexibility: Precast elements offer extensive design flexibility. Molds can be customized to create intricate shapes, textures, and architectural details. This enables architects and designers to push creative boundaries and achieve unique and visually stunning structures.
- Durability and Resilience: Precast elements are known for their durability and resilience. The controlled manufacturing process ensures consistent quality, and precasting materials are selected for their strength and longevity. Precast components can withstand harsh environmental conditions, ensuring long-term structural integrity.
- Cost Savings: While the initial cost of precast construction may be higher than traditional methods, the overall cost savings are significant. Reduced construction durations lead to lower labor costs and site-related expenses. Additionally, the long-term durability and low maintenance requirements of precast elements result in reduced operational and lifetime costs.
By embracing precast construction, builders can experience the advantages of faster project completion, higher quality structures, sustainable practices, and cost efficiencies. These benefits make precast construction an increasingly popular choice for a wide range of construction projects, from residential and commercial buildings to infrastructure and industrial facilities.
Types of Precast Components
Precast construction offers a wide range of components that can be used in various building projects. These components are manufactured offsite and then transported to the construction site for installation. Let’s explore some common types of precast components:
- Walls: Precast walls are one of the most common precast components. They can be load-bearing or non-load-bearing and are often used in residential, commercial, and industrial buildings. Precast walls offer excellent thermal and sound insulation properties and can be customized with various finishes and textures.
- Floors and Roofs: Precast concrete floors and roofs are used to create sturdy and durable horizontal structures. They can be manufactured as solid slabs, hollow-core slabs, or double tee slabs, depending on the specific project requirements. Precast floors and roofs offer excellent fire resistance and can be quickly installed, reducing construction time significantly.
- Columns and Beams: Precast columns and beams provide structural support in buildings. They are manufactured as pre-tensioned or post-tensioned elements, ensuring high strength and load-bearing capacity. Precast columns and beams are often used in conjunction with precast floors for efficient construction.
- Stairs: Precast stairs offer a quick and efficient solution for vertical transportation within a building. They can be manufactured in various designs and configurations, including straight flights, spiral stairs, and custom shapes. Precast stairs are durable, easy to install, and can be finished with different materials like stone, wood, or tiles.
- Facades: Precast facades are widely used to enhance the aesthetic appeal of buildings. They can be manufactured with different architectural finishes, textures, and patterns to create visually striking exteriors. Precast facades are durable, weather-resistant, and require minimal maintenance.
- Modular Units: Precast modular units are complete building modules that are manufactured offsite and then transported and assembled at the construction site. These modules can include entire residential units, hotel rooms, bathrooms, or kitchens. Precast modular units offer accelerated construction time and can be easily customized to meet specific design requirements.
These are just a few examples of precast components. The versatility of precast construction allows for the creation of a wide variety of elements, tailored to the specific needs and design preferences of each project.
By incorporating precast components into their construction projects, builders can benefit from faster installation, improved quality control, enhanced design flexibility, and durable structures that stand the test of time.
Manufacturing Process of Precast Elements
The manufacturing process of precast elements involves several steps to ensure the production of high-quality and precise components. Let’s take a closer look at the typical manufacturing process:
- Design and Planning: The process begins with the design and planning phase, where architects and engineers collaborate to create detailed drawings and specifications for the precast elements. These drawings outline the dimensions, shapes, reinforcement requirements, and architectural finishes of each component.
- Mold Preparation: Once the design is finalized, molds or forms are prepared to shape the precast elements. Molds can be made of steel, fiberglass, or other materials depending on the desired finish and complexity of the component. The molds are carefully measured and prepared to ensure accurate replication of the design.
- Reinforcement Placement: Steel reinforcement bars, also known as rebar, are placed within the molds to reinforce the precast elements and provide structural strength. The placement of rebar follows the specifications outlined in the design drawings to ensure the structural integrity of the components.
- Concrete Mixing and Pouring: Next, the concrete mixture is prepared. The precise composition of the mixture depends on the specific requirements of the precast element, including strength, durability, and workability. The concrete mixture is then poured into the molds, ensuring proper compaction and removal of air voids.
- Curing: After pouring the concrete, the molds are stored in a controlled environment for the curing process. Curing involves providing specific temperature and moisture conditions to promote the hydration and hardening of the concrete. This ensures that the precast elements achieve the desired strength and durability.
- Demolding and Finishing: Once the curing process is complete, the molds are carefully removed to reveal the hardened precast elements. The components may undergo additional finishing processes, such as sandblasting, acid etching, or applying architectural finishes to achieve the desired aesthetics.
- Quality Control: Throughout the manufacturing process, strict quality control measures are implemented to ensure the dimensional accuracy, strength, and durability of the precast elements. The components are thoroughly inspected, and any defects or imperfections are addressed before they are transported to the construction site.
- Transportation and Installation: Once the precast elements pass the quality control checks, they are carefully transported to the construction site using specialized vehicles and equipment. The components are then installed by skilled workers, following the project’s specifications and design drawings.
By following this manufacturing process, builders can achieve precise and high-quality precast elements. The controlled environment, advanced materials, and rigorous quality control measures ensure that precast components meet the required standards for structural integrity, aesthetics, and durability.
With the manufacturing process for precast elements in place, construction projects can benefit from improved efficiency, reduced construction time, and consistent quality throughout the entire building process.
Read more: What Does Furring Mean In Construction
Installation of Precast Elements
The installation of precast elements is a carefully planned and coordinated process that requires skilled workers and specialized equipment. The precise installation of these components ensures the structural integrity and safety of the building. Let’s explore the typical installation process of precast elements:
- Site Preparation: Before the installation process begins, the construction site is prepared accordingly. This involves clearing the area, leveling the ground, and ensuring a stable and suitable foundation for the precast elements.
- Cranes and Lifting: Cranes and other lifting equipment are used to transport the precast elements from the delivery vehicles to their designated locations on-site. The lifting process requires careful planning to ensure the safe and accurate placement of the components.
- Placement and Alignment: Each precast element is precisely positioned and aligned according to the design drawings and specifications. Skilled workers use leveling tools and laser guides to ensure that the elements are installed with accuracy and precision.
- Connection and Jointing: Once the precast elements are in place, they are connected and jointed to ensure structural stability and integrity. This may involve the use of specialized connectors, such as bolts or welds, to secure the elements together securely.
- Grouting and Finishing: Grouting is often performed to fill any gaps or voids between the precast elements and ensure a solid connection. Additionally, finishing touches, such as applying sealants or architectural finishes, may be done to enhance the aesthetics of the installation.
- Testing and Inspection: Once the installation is complete, thorough testing and inspection are conducted to verify the structural integrity and performance of the precast elements. This may include load testing, visual inspections, and other quality assurance measures.
It is crucial to note that the installation process may vary depending on the specific project and the type of precast elements being installed. Complex installations may require additional steps or specialized techniques. Professional engineering and construction teams work closely together to ensure the safe, efficient, and accurate installation of precast elements.
By utilizing skilled labor, advanced equipment, and adherence to strict safety guidelines, the installation of precast elements can be carried out seamlessly. The systematic approach and precision in installation contribute to faster project completion, improved construction quality, and long-lasting structures.
Precast in construction refers to concrete elements that are cast in a controlled environment and then transported to the construction site for assembly. This method can save time and reduce on-site labor costs.
Advantages and Limitations of Precast Construction
Precast construction offers several advantages that make it a preferred choice in many building projects. However, like any construction method, it also has its limitations. Let’s explore the advantages and limitations of precast construction:
Advantages:
- Speed and Efficiency: Precast construction significantly reduces project timelines. The offsite manufacturing process enables parallel activities, leading to faster completion and reduced construction time.
- Quality Control: Precast elements are manufactured in a controlled environment, ensuring higher quality and consistency. The stringent quality control measures during manufacturing result in precise and durable components.
- Design Flexibility: Precast construction offers tremendous design flexibility. Complex shapes, architectural details, and a range of finishes can be easily achieved, allowing architects and designers to create unique and aesthetically pleasing structures.
- Sustainability: Precast construction aligns with sustainable building practices. The controlled manufacturing process minimizes waste and optimizes material usage. Reusing precast elements in different projects reduces the consumption of natural resources.
- Durability: Precast elements are renowned for their durability and resilience. The use of high-quality materials and advanced manufacturing techniques ensures structures that can withstand various environmental conditions and provide long-term durability.
- Cost Efficiency: While the initial cost of precast construction may be higher, the overall costs are often lower. Construction time is reduced, leading to reduced labor costs. The durability and low maintenance requirements of precast elements result in long-term cost savings.
Limitations:
- Transportation Challenges: Large precast elements require careful transportation planning and specialized equipment, which can be costly and logistically challenging, especially for long-distance projects.
- Design Limitations: While precast construction offers design flexibility, certain design complexities may be challenging or impractical to achieve with precast elements, leading to additional costs or compromises in the design.
- Limited On-site Modifications: Once precast elements are manufactured and delivered to the site, modifications are limited. This means any design changes or adjustments during construction may require additional time and expense.
- High Initial Investment: The establishment of a precast manufacturing facility requires a significant initial investment in equipment, molds, and skilled labor, which may not be feasible for small-scale projects or organizations.
- Dependency on Skilled Labor: Precast construction relies heavily on skilled labor for mold preparation, reinforcement placement, and installation. The availability of skilled labor and their expertise may vary depending on the region or project location.
Despite the limitations, precast construction offers numerous advantages that outweigh the challenges. By carefully considering project requirements, design complexities, and budget, builders and developers can leverage the benefits of precast construction and achieve efficient, durable, and visually appealing structures.
Read more: What Does Masonry Construction Mean
Examples of Precast Projects
Precast construction has been successfully implemented in a wide range of building projects worldwide. Here are a few notable examples that demonstrate the versatility and effectiveness of precast construction:
- Burj Khalifa, Dubai: The Burj Khalifa, the tallest building in the world, utilized precast concrete panels for its facade. The precast panels were manufactured offsite to achieve the intricate design features and were seamlessly installed during the construction process, contributing to the iconic aesthetic of the building.
- Parkview Square, Singapore: Parkview Square is a prominent commercial building renowned for its art-deco architecture. Precast concrete panels were used to create the intricately designed exterior facades, incorporating elaborate sculptural elements and intricate detailing.
- One Central Park, Sydney: This residential and commercial complex in Sydney features an innovative precast facade system. The precast glass-fiber reinforced concrete (GFRC) panels were manufactured to mimic natural stone and were installed to create an aesthetically pleasing and energy-efficient building envelope.
- London Aquatics Centre, UK: The London Aquatics Centre, built for the 2012 Olympic Games, utilized precast concrete elements for its curved roof structure. This precast solution allowed for fast and efficient construction, while maintaining the intricate geometry of the roof design.
- Taipei 101, Taiwan: Taipei 101, once the tallest building in the world, incorporated precast concrete mega-columns for its seismic stabilization. These massive precast columns were fabricated offsite, reducing construction time and enhancing the building’s structural resilience.
- Modular Housing Projects: Precast modular construction has gained popularity in the housing sector, offering efficient and sustainable solutions. Projects such as the Stackt Market in Toronto and the Carmel Place micro-apartments in New York City showcase the benefits of offsite manufacturing and ease of assembly for fast and affordable housing solutions.
These examples highlight the successful implementation of precast construction in various types of projects, including high-rise buildings, iconic structures, and housing developments. Precast construction’s ability to deliver quality, speed, and design flexibility has made it a go-to choice for creating remarkable and practical buildings around the world.
From skyscrapers to cultural landmarks to housing solutions, precast construction has proven its value in meeting the demands of modern architecture and construction practices.
Conclusion
Precast construction has revolutionized the building industry, offering a host of advantages in terms of speed, quality, sustainability, and design flexibility. The process of manufacturing precast elements offsite, in a controlled environment, has transformed the way buildings are constructed and has led to the successful completion of numerous remarkable projects.
The benefits of precast construction, such as accelerated construction timelines, enhanced quality control, reduced environmental impact, and cost savings, make it an appealing choice for builders and developers across various sectors. The ability to customize precast components for specific design requirements further adds to its appeal, allowing architects and designers to unleash their creativity and create visually stunning structures.
However, precast construction does come with certain limitations, such as transportation challenges, design limitations, and the need for skilled labor. It is important for project stakeholders to carefully consider these limitations and weigh them against the benefits before embarking on a precast construction project.
Looking ahead, precast construction is poised to continue its growth and innovation. Advancements in technology, such as Building Information Modeling (BIM) and 3D printing, are further enhancing the capabilities of precast construction and opening up new possibilities in terms of design, efficiency, and sustainability.
In conclusion, precast construction offers a myriad of benefits that drive efficiency, quality, and sustainability in the ever-evolving construction industry. With its ability to deliver faster construction, durable structures, and design flexibility, precast construction is undoubtedly shaping the future of building construction and playing a vital role in constructing the cities and structures of tomorrow.
Frequently Asked Questions about What Does Precast Mean In Construction
Was this page helpful?
At Storables.com, we guarantee accurate and reliable information. Our content, validated by Expert Board Contributors, is crafted following stringent Editorial Policies. We're committed to providing you with well-researched, expert-backed insights for all your informational needs.
0 thoughts on “What Does Precast Mean In Construction”