Home>diy>Building & Construction>What Does Furring Mean In Construction
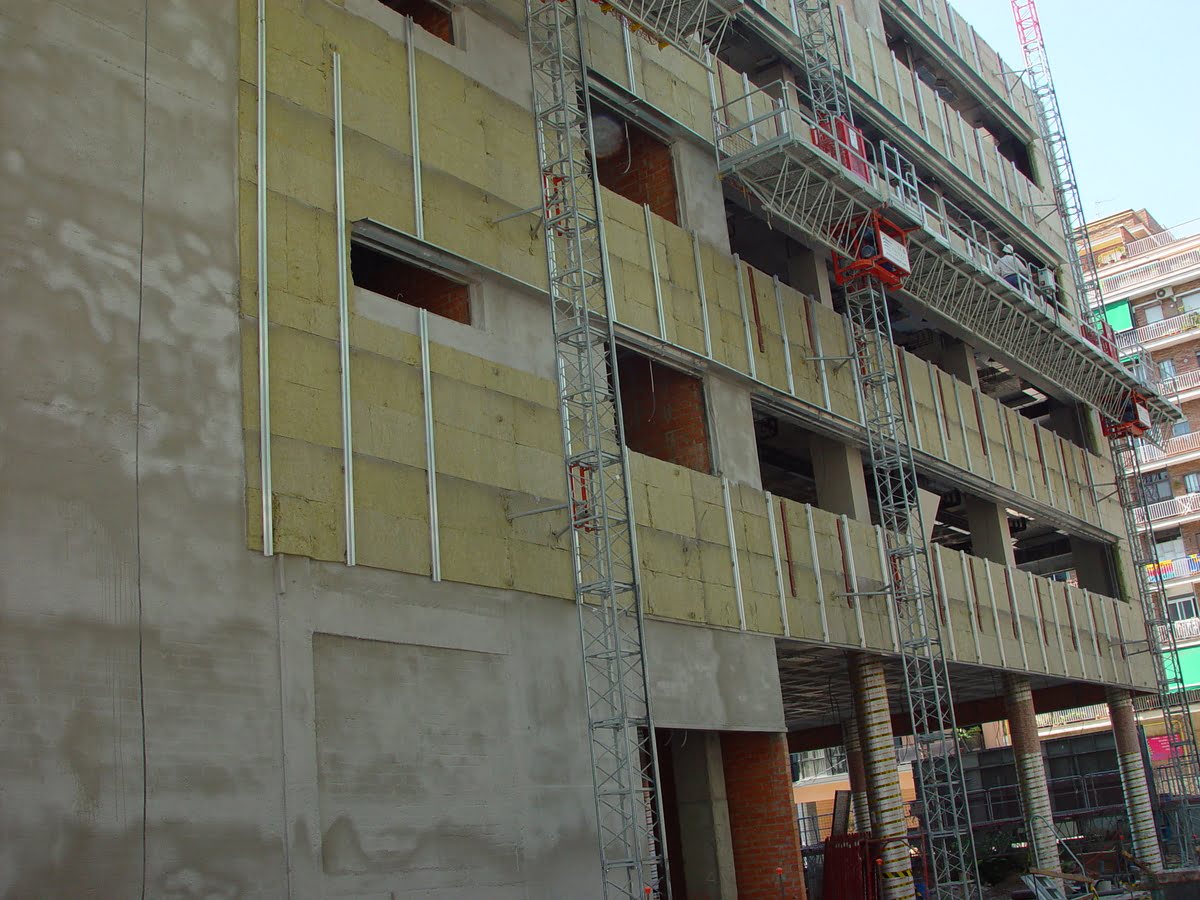
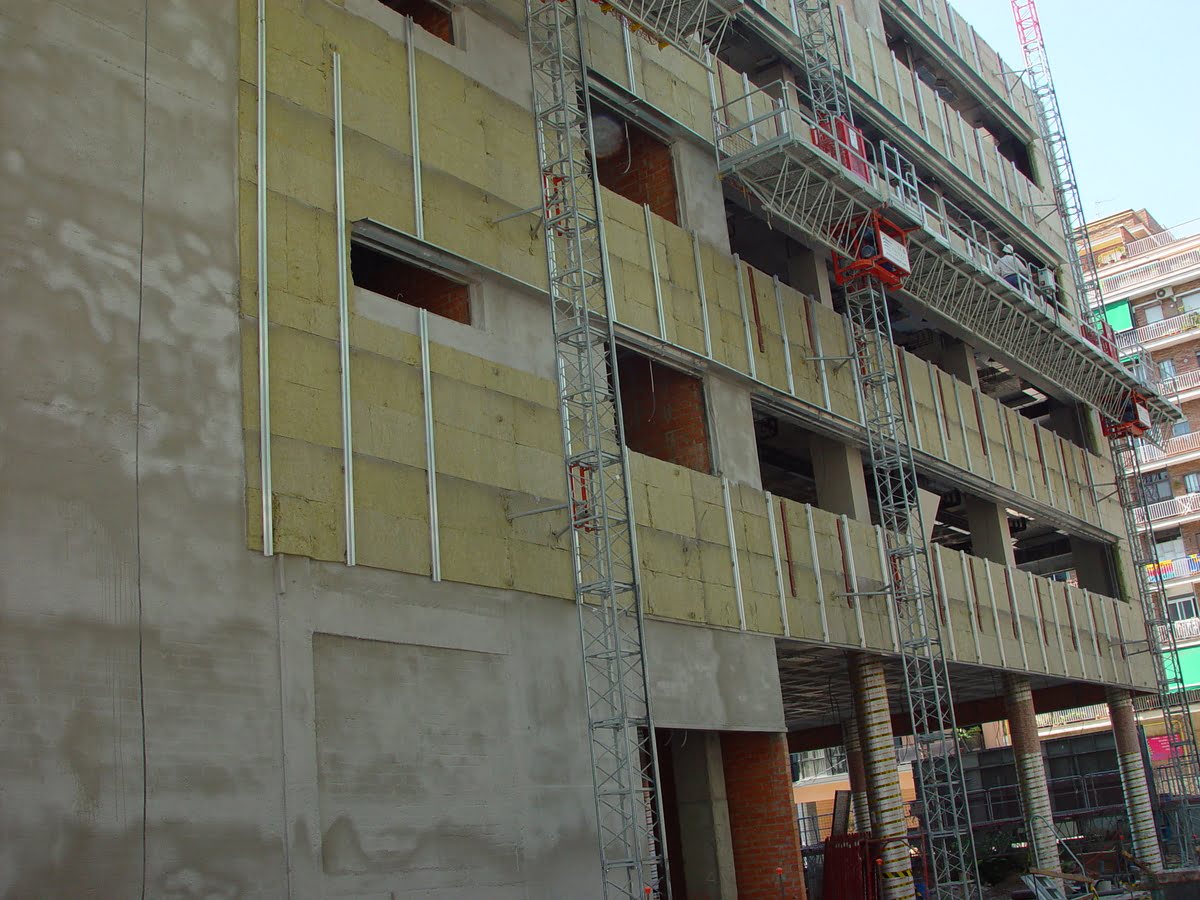
Building & Construction
What Does Furring Mean In Construction
Modified: January 6, 2024
Learn the meaning of "furring" in building construction and how it is used to create a level surface for wall installations. Discover its importance and applications in the construction industry.
(Many of the links in this article redirect to a specific reviewed product. Your purchase of these products through affiliate links helps to generate commission for Storables.com, at no extra cost. Learn more)
Introduction
In the world of construction, there are countless techniques and practices employed to ensure the durability and longevity of buildings. One such technique that plays a crucial role in achieving structural integrity is furring. While the term “furring” may not be commonly known to those outside of the construction industry, it is an essential practice that is used extensively in various building projects.
So, what exactly does furring mean in construction? In simple terms, it refers to the process of installing strips or battens to create a level surface on a wall or ceiling before adding the final finishing materials, such as drywall or paneling. These strips, known as furring strips, serve as a framework or support system for the finishing materials and provide additional benefits to the overall construction.
The purpose and use of furring strips go well beyond creating a smooth surface for finishes. They have multiple functions that contribute to the structural stability and efficiency of a building. By understanding the materials used for furring, the different furring installation techniques, and the advantages and disadvantages associated with it, we can appreciate the significance of this construction practice.
So join us as we explore the world of furring in construction and uncover the valuable role it plays in building projects. Whether you are a seasoned contractor or a curious DIY enthusiast, this comprehensive guide will provide you with the knowledge and insights to understand and utilize furring techniques effectively.
Key Takeaways:
- Furring in construction involves installing strips to create a level surface, improve insulation, manage moisture, and integrate utilities, enhancing the durability and aesthetics of buildings.
- While furring offers benefits like level surfaces and improved insulation, it can also present challenges such as moisture trapping and increased cost, requiring careful planning and troubleshooting for successful construction projects.
Definition of Furring in Construction
In the construction industry, furring refers to the process of installing horizontal or vertical strips, known as furring strips, onto a wall or ceiling surface. The purpose of this technique is to create an even plane or space between the original surface and the finishing materials that will be applied, such as drywall, paneling, or insulation.
Furring strips are typically made of wood or metal and are attached to the existing surface using nails, screws, or adhesives. These strips are placed perpendicular to the wall studs or ceiling joists, creating a secondary framework or support system.
By adding the furring strips, any imperfections or irregularities in the original surface can be corrected, providing a smooth and level base for the installation of the finishing materials. This practice ensures that the final outcome appears seamless and professional.
Furring strips also serve additional purposes beyond leveling the surface. They create an air gap between the original surface and the finishing materials, helping to improve thermal and acoustic insulation. This gap allows for the circulation of air, aiding in moisture management and preventing the buildup of condensation and mold.
Furthermore, furring can help with the installation of electrical wiring and plumbing. By providing a space between the original surface and the finish materials, it becomes easier to conceal these necessary components while still maintaining accessibility for future repairs or modifications.
Overall, the primary goal of furring in construction is to create a stable and level surface for the installation of finishes, while also improving insulation, preventing moisture-related issues, and allowing for the integration of utilities.
Purpose and Use of Furring Strips
Furring strips play a crucial role in construction projects and offer numerous benefits that contribute to the overall functionality and aesthetics of a building. Let’s delve into the purpose and use of furring strips in more detail:
- Leveling the Surface: One of the primary purposes of furring strips is to create a level and smooth surface for the installation of finishing materials. By attaching the strips to the existing wall or ceiling, any irregularities or imperfections can be corrected, resulting in a professional and visually appealing finish.
- Insulation Enhancement: Furring strips help improve thermal and acoustic insulation within a building. By creating an air gap between the original surface and the finish materials, furring allows for the installation of insulation materials such as fiberglass or foam boards. This additional layer contributes to better energy efficiency, noise reduction, and overall comfort.
- Moisture Management and Ventilation: The installation of furring strips creates a space that promotes air circulation, helping to manage moisture and prevent the accumulation of condensation. This can be especially important in areas prone to high humidity, reducing the risk of mold and moisture-related damage to the walls or ceilings.
- Integration of Utilities: Furring strips provide a convenient solution for integrating electrical wiring, plumbing, and other utility systems within the walls or ceilings. The space created by the furring allows for easy concealment of these components, while still maintaining accessibility for future repairs or modifications.
- Improved Fire Resistance: In certain construction applications, furring strips can help enhance the fire resistance of a structure. By utilizing non-combustible materials for the furring strips, such as metal, the overall fire rating of the wall or ceiling assembly can be increased.
- Enhanced Durability: Furring strips provide added support and stability to the finish materials, such as drywall or paneling. This improves the overall durability and longevity of the walls or ceilings, as the furring strips help distribute the weight and impact on the surface more evenly.
- Versatility: Furring strips can be used in various construction applications, including both interior and exterior projects. Whether it’s renovating an existing space or constructing a new building, furring strips offer versatility and flexibility in achieving the desired outcome.
Overall, furring strips are a valuable tool in construction, allowing for a level surface, enhanced insulation, moisture management, integration of utilities, improved fire resistance, durability, and versatility in different building projects. As a key element in creating a functional and aesthetically pleasing space, furring strips have become an essential practice in the construction industry.
Materials Used for Furring
When it comes to furring in construction, different materials can be used for the furring strips depending on the specific needs and requirements of the project. Here are some commonly used materials for furring:
- Wood: Wood furring strips are a popular choice due to their affordability, ease of installation, and availability. Common types of wood used for furring include pine, cedar, or fir. These strips are typically 1×3 or 1×4 boards and are easily attached to the existing surface using nails or screws. Wood furring strips provide excellent insulation properties and can be stained or painted to match the desired aesthetic.
- Metal: Metal furring strips, typically made of steel or aluminum, offer durability and stability. These strips are available in various profiles, such as hat channels or resilient channels, and are designed specifically for improved sound insulation. Metal furring strips are often used in commercial and industrial applications and are resistant to moisture and rot. They are attached to the surface using screws or clips.
- Rigid Insulation: In some cases, rigid insulation materials, such as foam boards, can be used as furring. Insulation furring strips provide the dual benefit of leveling the surface while also improving energy efficiency. These strips are made from materials like extruded polystyrene (XPS) or polyisocyanurate (ISO), and they are installed directly onto the wall or ceiling surface using adhesive or mechanical fasteners.
- Composite Materials: Composite furring strips offer a combination of durability and resistance to moisture. These strips are made from a mixture of wood fibers and plastic, providing the benefits of both materials. Composite furring is rot-resistant, insect-resistant, and requires minimal maintenance. It can be installed using screws or adhesives and is suitable for both interior and exterior applications.
- Plastic: Plastic furring strips, typically made of polyethylene or PVC, are lightweight, resistant to moisture, and easy to install. They are commonly used in applications where moisture control is critical, such as basements or bathrooms. Plastic furring strips are available in various profiles and can be attached to the surface using screws or adhesives.
It’s important to choose the appropriate materials for furring based on factors such as the specific project requirements, budget, environmental conditions, and desired performance characteristics. Consulting with a construction professional or supplier can help ensure the selection of the most suitable furring materials for your specific application.
Types of Furring Techniques and Applications
Furring techniques can vary depending on the specific construction project and the desired outcome. Here are some common types of furring techniques and their applications:
- Vertical Furring: Vertical furring involves installing furring strips in a vertical orientation, parallel to the wall studs or ceiling joists. This technique is commonly used to create a straight and level surface on an uneven or masonry wall. Vertical furring can also be employed to provide an air gap for improved insulation or to incorporate utilities behind the finish materials.
- Horizontal Furring: Horizontal furring is the process of attaching furring strips horizontally, perpendicular to the wall studs or ceiling joists. This technique is often used to level uneven ceiling surfaces or to provide a stable base for the installation of finishes on walls. Horizontal furring can also aid in soundproofing or thermal insulation applications.
- Resilient Channel: Resilient channel furring involves the use of metal channels that are specially designed to improve sound insulation. The resilient channels are attached perpendicular to the studs or joists, creating an airspace between the original surface and the finish materials. This airspace helps reduce sound transmission and can be beneficial in areas where noise control is critical, such as recording studios or multi-family dwellings.
- Z-Furring: Z-furring is a technique where the furring strips are shaped like the letter “Z” and are installed vertically, creating an air gap between the existing wall or ceiling and the finish materials. This method is commonly used when adding insulation or improving thermal performance while also providing a level surface for finishes.
- Insulation Furring: Insulation furring combines the benefits of furring and insulation by using rigid insulation boards as the furring strips. This technique provides both a level surface and improved energy efficiency by reducing thermal bridging. Insulation furring is commonly used in exterior walls or roofs to enhance insulation performance.
The choice of furring technique depends on various factors such as the condition of the existing surface, the desired outcome, the type of finishes to be installed, and specific project requirements. It’s essential to assess the project needs and consult with construction professionals to determine the most suitable furring technique for your specific application.
Furring in construction refers to the process of adding strips of wood or metal to a wall or ceiling to create a level surface for finishing materials. It is commonly used to level out uneven surfaces before adding drywall or other finishes.
Read more: What Does Turnkey Mean In Construction
Furring Installation Process
The installation process of furring strips may vary depending on the specific technique and materials used. Here’s a general overview of the furring installation process:
- Prepare the Surface: Ensure that the surface where the furring strips will be attached is clean, dry, and free from any debris. Repair any damage or irregularities in the surface that could affect the installation.
- Measure and Mark: Measure and mark the location of the furring strips on the surface. Use a level to ensure accuracy and mark the positions where the furring strips will be attached.
- Choose the Fastening Method: Determine the appropriate fastening method based on the materials being used. Common options include nails, screws, or adhesives. Consider the weight of the finishing materials and the stability required to choose the most suitable fasteners.
- Attach the Furring Strips: Begin attaching the furring strips to the surface using the chosen fastening method. If using nails or screws, ensure they are driven securely into the wall studs or ceiling joists for optimal stability. If using adhesives, follow the manufacturer’s instructions and apply the adhesive evenly to the back of the furring strip before pressing it firmly against the surface.
- Ensure Level and Spacing: As you attach each furring strip, use a level to ensure they are installed horizontally or vertically, depending on the chosen technique. Check for proper alignment and spacing to maintain a level surface throughout the installation.
- Repeat the Process: Continue attaching furring strips along the marked locations until the entire surface is covered. Take care to maintain consistent spacing between the strips to ensure the stability and integrity of the final result.
- Inspect and Adjust: Once all the furring strips are installed, inspect the surface to ensure that it is level and free from any visible irregularities. Make any necessary adjustments by repositioning or replacing any furring strips that are not aligned correctly.
- Proceed with Finishing Materials: With the furring strips in place, you can proceed with the installation of the desired finishing materials, such as drywall, paneling, or insulation. Follow the appropriate installation guidelines for your chosen finishes to achieve the desired outcome.
It is important to note that the specific steps of the furring installation process may vary based on the technique and materials used. Always refer to the manufacturer’s instructions and consult with construction professionals for guidance specific to your project.
Advantages and Disadvantages of Furring in Construction
Furring in construction offers several advantages, but it also comes with some potential disadvantages. Let’s explore both the benefits and drawbacks of using furring in construction projects:
- Advantages:
- Level Surfaces: Furring strips help create a level and smooth surface, improving the overall aesthetic appeal of the finishes.
- Improved Insulation: Furring provides an air gap, allowing for the installation of insulation materials, resulting in enhanced thermal and acoustic insulation.
- Moisture Management: The space created by furring allows for air circulation, reducing the risk of condensation buildup and potential moisture-related issues.
- Utility Integration: Furring strips provide a convenient solution for concealing electrical wiring, plumbing, and other utilities within the walls or ceilings.
- Fire Resistance: Certain furring techniques and non-combustible materials can increase the fire resistance of the structure.
- Durability: Furring strips provide additional support and stability to the finishes, contributing to the overall durability and longevity of the construction.
- Versatility: Furring can be used in a wide range of construction applications, both for interior and exterior projects.
- Disadvantages:
- Increased Cost: The installation of furring strips can add additional material and labor costs to a construction project.
- Space Limitations: Furring reduces the available wall or ceiling space, which may be a concern in areas where space is limited.
- Complexity: Depending on the technique and materials used, furring installation may require additional expertise and careful planning.
- Time-consuming: The installation of furring strips can extend the construction timeline, especially for large-scale projects.
- Reduced Room Size: Furring can decrease the overall usable space within a room due to the additional thickness added by the strips.
- Potential Moisture Trapping: In some cases, improper installation of furring or inadequate moisture management can result in the trapping of moisture, leading to mold or other moisture-related issues.
It’s important to carefully evaluate the specific needs and requirements of a construction project to determine if the advantages of furring outweigh the potential disadvantages. Consulting with construction professionals can provide valuable insights and help make informed decisions regarding the use of furring in a construction project.
Common Issues and Troubleshooting with Furring
While furring is a widely used technique in construction, it can come with a few common issues that may require troubleshooting. It’s important to be aware of these potential problems and their solutions to ensure the success of your furring project. Here are some common issues and troubleshooting tips:
- Uneven or Unlevel Surface: One of the main purposes of furring is to create a level surface for the installation of finishes. If you encounter an uneven or unlevel surface, it can be due to improper installation or the original condition of the wall or ceiling. To troubleshoot this issue, carefully measure and reposition the furring strips, ensuring they are level and properly aligned.
- Moisture Trapping: Improper installation or inadequate moisture management can result in moisture being trapped behind the furring strips. This can lead to mold growth or other moisture-related problems. To troubleshoot this issue, ensure proper ventilation and drainage systems are in place. Use moisture-resistant materials and insulation with proper vapor barriers to mitigate moisture issues.
- Insufficient Fastening: Inadequate fastening of the furring strips can lead to instability and poor durability. Troubleshoot this issue by ensuring proper fasteners, such as nails, screws, or adhesives, are used and properly secured into the underlying wall studs or ceiling joists.
- Noise Transmission: Furring strips can sometimes transmit sound if not properly addressed. To troubleshoot this issue, consider using resilient channels, which can help reduce sound transmission through the furring system. Additionally, installing insulation between the furring strips can further improve soundproofing capabilities.
- Inadequate Insulation: Furring strips provide an opportunity to add insulation, improving thermal performance. However, inadequate insulation installation can lead to energy efficiency issues. Troubleshoot this issue by ensuring the insulation materials are properly installed, with no gaps or voids. Follow manufacturer guidelines for specific insulation products.
- Material Compatibility: Choosing incompatible materials for furring can result in issues such as warping, rotting, or poor performance. Troubleshoot this issue by selecting materials that are compatible with the specific application and environment. Consult with construction professionals or material suppliers to determine the appropriate materials for your project.
- Cost and Time Management: Furring installation can add to the overall cost and construction timeline. To troubleshoot cost and time management issues, plan the project carefully, considering the labor, materials, and additional time required for furring. Proper project management and communication can help mitigate potential delays and cost overruns.
Remember, each construction project is unique, and troubleshooting may require specific solutions based on the circumstances. When encountering issues with furring, it’s essential to consult with construction professionals or seek expert advice to ensure the proper resolution and successful completion of the project.
Conclusion
Furring is a fundamental technique in the construction industry that plays a crucial role in achieving a level, durable, and aesthetically pleasing finish. By installing furring strips, construction professionals can create a smooth surface, improve insulation, manage moisture, integrate utilities, enhance fire resistance, and provide added stability to the final construction project.
Throughout this comprehensive guide, we have explored the definition of furring in construction, the purpose and uses of furring strips, the materials commonly used, various furring techniques and applications, the furring installation process, as well as the advantages, disadvantages, common issues, and troubleshooting with furring.
While furring offers numerous benefits, it is important to be aware of potential challenges such as uneven surfaces, moisture management, noise transmission, insulation issues, material compatibility, and cost and time management. By understanding and addressing these issues, construction professionals and DIY enthusiasts can successfully navigate the furring process and achieve exceptional results.
Whether you are renovating a space or embarking on a new construction project, incorporating furring techniques can enhance the structural integrity, energy efficiency, and overall aesthetics of your building. Consult with construction professionals, follow industry guidelines, and choose the appropriate materials and installation techniques to ensure a successful furring project.
By harnessing the benefits of furring, you can create a solid foundation for your finishes, improve insulation and moisture management, and achieve a long-lasting and visually appealing structure. Embrace the versatility and flexibility that furring offers, and confidently embark on your construction journey, knowing that you have the tools and knowledge to create a space that is functional, comfortable, and built to last.
Frequently Asked Questions about What Does Furring Mean In Construction
Was this page helpful?
At Storables.com, we guarantee accurate and reliable information. Our content, validated by Expert Board Contributors, is crafted following stringent Editorial Policies. We're committed to providing you with well-researched, expert-backed insights for all your informational needs.
0 thoughts on “What Does Furring Mean In Construction”