Home>diy>Building & Construction>What Does “VE” Mean In Construction
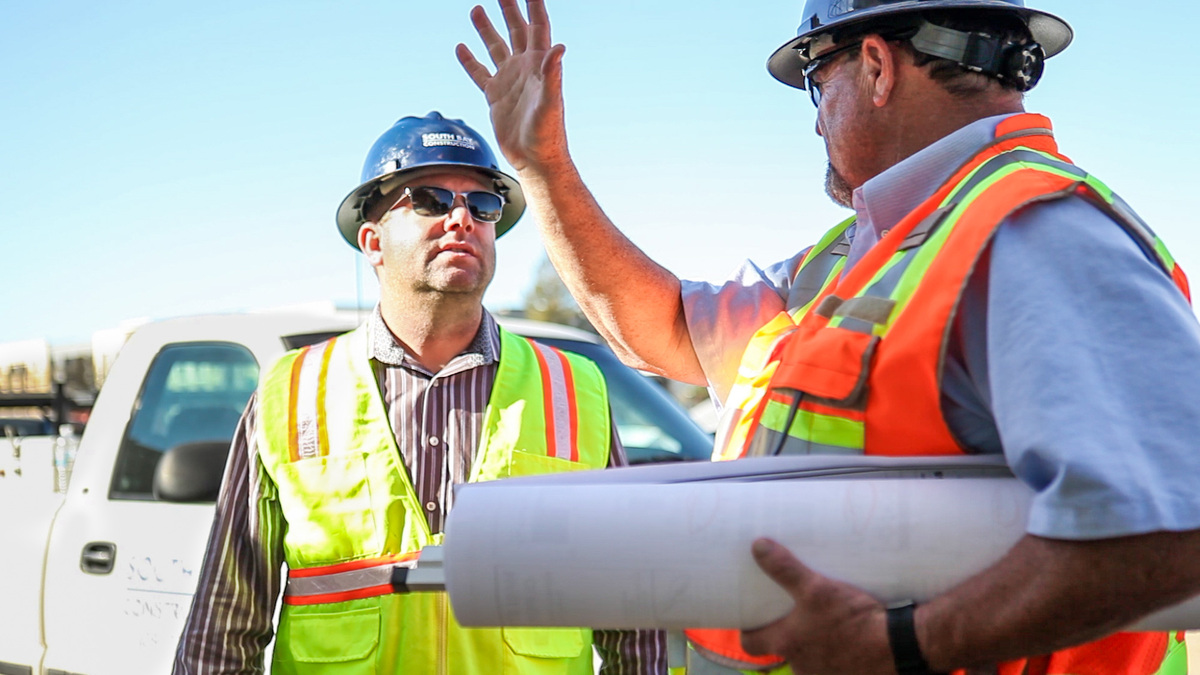
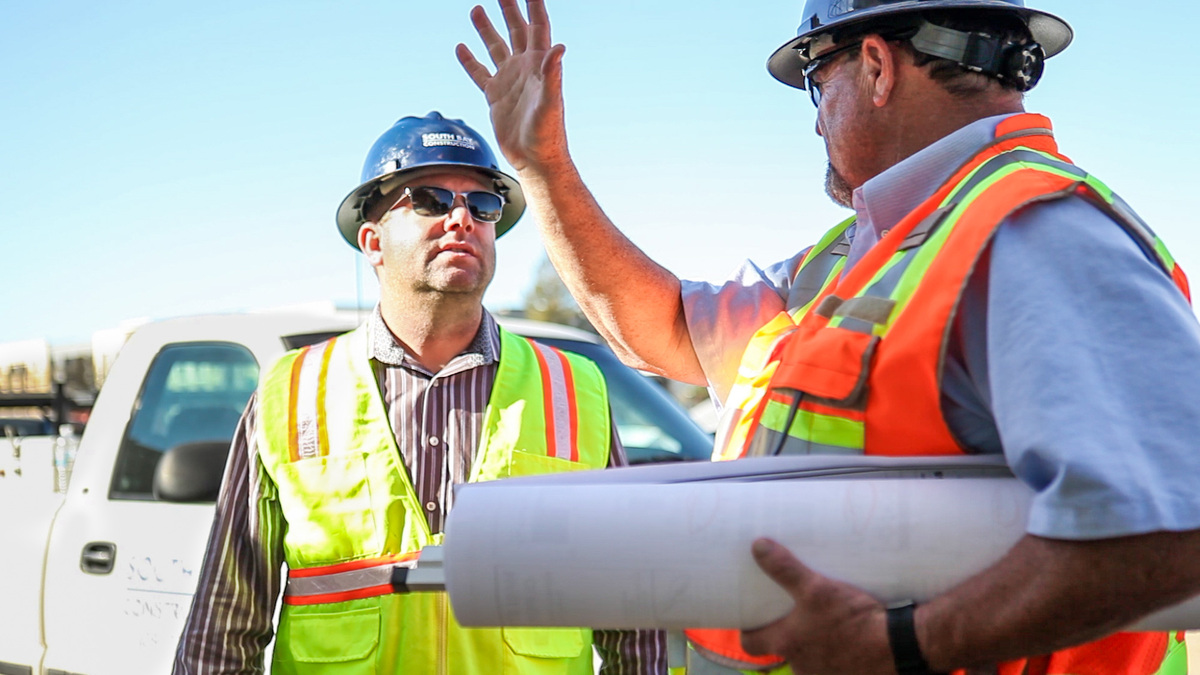
Building & Construction
What Does “VE” Mean In Construction
Modified: December 7, 2023
Discover the meaning of "VE" in construction and its significance in building-construction. Gain insights into this commonly used term in the industry.
(Many of the links in this article redirect to a specific reviewed product. Your purchase of these products through affiliate links helps to generate commission for Storables.com, at no extra cost. Learn more)
Introduction
Construction is a complex and demanding industry, requiring careful planning and meticulous execution. One crucial aspect of the construction process is Value Engineering (VE). Value Engineering is a systematic and organized approach that aims to identify and eliminate unnecessary costs while maintaining or even enhancing the quality and functionality of a project.
VE is based on the concept that value is not solely determined by the cost of a product or service, but rather by the benefits it provides. By focusing on delivering the highest value for the resources invested, VE allows construction professionals to optimize project outcomes and maximize client satisfaction.
In the following sections, we will explore the meaning of “VE” in construction, its importance, common applications, benefits, challenges, and real-life project examples. Join us on this journey as we delve into the world of Value Engineering and discover how it can revolutionize the construction industry.
Key Takeaways:
- Value Engineering (VE) in construction optimizes project value by identifying cost-saving opportunities, enhancing efficiency, and mitigating risks while maintaining quality and functionality. It revolutionizes the industry through innovation and collaboration.
- Successful VE projects, such as the Golden Gate Bridge retrofit and Burj Khalifa construction, demonstrate substantial cost savings, improved efficiency, and exceptional outcomes. VE fosters innovation, collaboration, and continuous improvement in construction.
Definition of “VE”
Value Engineering, commonly referred to as “VE,” is a systematic and analytical process used in the construction industry to optimize the value of a project. It involves studying the project’s requirements, functions, and objectives in order to identify opportunities for cost savings, efficiency improvements, and performance enhancements.
VE focuses on the concept of value, which is not limited to the initial cost of construction but encompasses the entire lifespan of a project. It evaluates the relationship between cost, quality, and functionality to ensure that resources are allocated effectively and efficiently.
The VE process typically consists of the following steps:
- Function Analysis: Identifying and understanding the project’s essential functions and performance requirements.
- Value Analysis: Evaluating various options and alternatives to achieve the desired functions at the lowest cost.
- Cost Analysis: Assessing the costs associated with each alternative and identifying potential cost-saving opportunities.
- Recommendation: Presenting the best-value solution that meets the project’s requirements.
- Implementation: Executing the chosen solution and monitoring its effectiveness.
It is important to note that VE is not about cutting corners or compromising quality. Instead, it aims to deliver the highest level of value by eliminating unnecessary expenses, streamlining processes, and maximizing the use of resources.
Value Engineering is typically applied during the design stage of a construction project, but it can also be integrated into other phases, including construction, operation, and maintenance.
By employing VE principles, construction professionals can identify innovative solutions, reduce project costs, enhance project performance, and ultimately satisfy the needs and expectations of clients and stakeholders.
Importance of “VE” in Construction
Value Engineering plays a crucial role in the construction industry, bringing numerous benefits to both project owners and construction professionals. Here are some key reasons why VE is important:
- Cost Savings: One of the primary objectives of VE is to identify cost-saving opportunities without compromising quality or functionality. By critically examining every component of a project, VE experts can propose alternative materials, designs, or construction methods that can lead to significant cost reductions. These savings can be substantial and have a direct impact on the project’s budget, enabling resources to be allocated more effectively.
- Optimized Value: VE is all about delivering the highest value for the investment made. By analyzing the functions and objectives of a project, VE professionals can enhance the overall value proposition. This includes improving the project’s performance, durability, sustainability, and user experience while ensuring that it remains within the desired cost parameters. By optimizing value, VE helps ensure clients receive the best possible return on their investment.
- Enhanced Efficiency: Through the VE process, construction professionals can identify inefficiencies, redundancies, and unnecessary complexities in the project’s design or construction methods. By streamlining processes and eliminating waste, VE helps improve project efficiency, resulting in reduced construction time, improved productivity, and smoother project execution.
- Better Risk Management: VE considers potential risks and challenges early in the project lifecycle. By uncovering potential issues and proposing alternative approaches, VE helps mitigate risks and improves project resilience. This proactive approach minimizes the chances of costly delays, rework, and safety incidents during construction.
- Increased Stakeholder Satisfaction: VE allows project owners to have a more significant role in decision-making and fosters collaboration between stakeholders, including designers, engineers, contractors, and end-users. By involving stakeholders in the VE process, their concerns and aspirations can be addressed, leading to a higher level of satisfaction and buy-in.
Overall, the importance of VE in construction cannot be overstated. It provides a systematic approach to optimize project outcomes, generate cost savings, enhance value, improve efficiency, mitigate risks, and ensure client satisfaction. By embracing VE principles, construction professionals can deliver successful projects that meet or exceed stakeholders’ expectations.
Common Applications of “VE”
Value Engineering (VE) can be applied to a wide range of construction projects, regardless of their size or complexity. Here are some common applications of VE in the construction industry:
- Building Design and Layout: VE can be used to evaluate and optimize the design and layout of a building. This includes analyzing the spatial organization, circulation patterns, and functional requirements to identify opportunities for cost savings and space utilization. VE can also help improve the aesthetics, functionality, and energy efficiency of buildings.
- Material Selection: VE is often employed to assess and select construction materials based on their cost-effectiveness, durability, and performance. By evaluating different materials and their suitability for the project, VE can lead to the use of more cost-effective and sustainable alternatives without compromising structural integrity or quality.
- Construction Methods: VE can be utilized to evaluate and optimize construction methods and techniques. This includes analyzing the sequence of construction activities, considering prefabrication or modular construction, and exploring innovative construction technologies. By selecting the most efficient methods, VE can help streamline construction processes and reduce labor, time, and cost requirements.
- Systems and Components: VE can assess various systems and components within a construction project, such as HVAC (heating, ventilation, and air conditioning), plumbing, electrical, and fire protection systems. By reviewing alternative options, VE can identify more effective and energy-efficient systems, resulting in lower operational costs and improved building performance.
- Sustainability and Green Building: VE is increasingly being used to promote sustainable practices and green building design. By considering energy-efficient technologies, renewable energy sources, water conservation strategies, and waste reduction measures, VE can help create environmentally friendly and cost-effective buildings.
These are just a few examples of how VE can be applied in construction. The versatility of VE allows it to be adapted to different projects and sectors, from residential and commercial buildings to infrastructure and industrial facilities. The key lies in applying the VE process systematically and involving the relevant stakeholders to ensure the best outcomes for the project.
“VE” in construction stands for “Value Engineering.” It is a systematic process used to improve the value of a project by analyzing its functions and reducing costs without sacrificing quality.
Benefits of Implementing “VE” Strategies
Implementing Value Engineering (VE) strategies in construction projects can bring a wide range of benefits and advantages. Here are some key benefits of incorporating VE into the construction process:
- Cost Savings: One of the primary benefits of VE is the potential for significant cost savings. By evaluating alternative options, materials, and construction methods, VE can identify opportunities to reduce project costs without compromising quality or functionality. These cost savings can have a direct impact on the project’s budget, allowing resources to be reallocated to other areas or increasing the return on investment.
- Enhanced Value: VE focuses on maximizing the value provided by a project. By analyzing the functions and objectives, VE professionals can suggest improvements that enhance the project’s performance, durability, efficiency, and aesthetic appeal. By increasing value, project owners can enjoy better returns on their investment and end-users can benefit from improved functionality and satisfaction.
- Improved Quality: VE encourages a critical examination of the project’s design, materials, and processes. By scrutinizing every aspect, VE helps identify areas for improvement and potential risks that may impact quality. By addressing these issues early in the project, the overall quality of the construction can be enhanced, leading to higher customer satisfaction and reduced maintenance and repair costs in the long run.
- Enhanced Efficiency and Productivity: VE challenges conventional practices and encourages innovation. By considering alternative construction methods, technologies, and materials, VE can help streamline processes and improve efficiency. This leads to reduced construction time, increased productivity, and smoother project execution.
- Risk Mitigation: VE is a proactive approach to risk management. By assessing risks and proposing alternative solutions, VE helps identify and mitigate potential issues before they escalate. This helps minimize project delays, cost overruns, and safety incidents, enhancing the overall project resilience.
- Collaboration and Stakeholder Engagement: VE promotes collaboration and engages stakeholders in decision-making processes. By involving designers, engineers, contractors, and end-users, different perspectives and expertise can be incorporated into the project. This fosters a sense of ownership, improves communication, and ensures that the final solution meets the needs and expectations of all stakeholders.
Overall, implementing VE strategies brings numerous benefits to construction projects. From cost savings and improved value to enhanced quality, efficiency, and stakeholder satisfaction, VE is a valuable tool that maximizes project outcomes and delivers successful results.
Read more: What Does Furring Mean In Construction
Challenges in Implementing “VE”
While Value Engineering (VE) brings significant benefits to construction projects, there are also several challenges that must be overcome during its implementation. Here are some common challenges in implementing VE:
- Resistance to Change: Implementing VE often requires a shift in mindset and practices. Some stakeholders, including designers, contractors, and even clients, may resist changes to established processes or design decisions. Overcoming this resistance requires effective communication, education, and highlighting the potential benefits of VE.
- Limited Awareness and Understanding: Many stakeholders in the construction industry may have limited awareness or understanding of VE principles and methodologies. This can hinder the successful implementation of VE. It is important to promote awareness and provide training to ensure that all parties involved have the knowledge and skills required to engage in the VE process effectively.
- Time and Resource Constraints: Implementing VE requires time and resources for analysis, evaluation, and decision-making. In fast-track projects or projects with strict timelines and budgets, allocating adequate time and resources for VE activities can be challenging. Balancing the need for VE with project constraints requires effective project management and coordination.
- Complexity and Interdependencies: Construction projects are often complex, involving various systems, components, and processes. Analyzing the interdependencies between different aspects of a project can be challenging and time-consuming. VE professionals need to have a thorough understanding of the project and expertise in evaluating the interactions between different elements.
- Limited Data Availability: VE relies on accurate and up-to-date data for analysis and evaluation. However, in some cases, data may be limited or incomplete, making it challenging to conduct a comprehensive VE assessment. It is important to have mechanisms in place to gather and validate relevant data to ensure effective VE decision-making.
- Balancing Cost, Quality, and Functionality: VE aims to optimize cost, quality, and functionality. However, balancing these factors can be challenging, as reducing costs may impact the quality or functionality of the project. It requires careful evaluation and consideration of trade-offs to ensure that cost savings do not compromise the overall value and performance of the project.
Addressing these challenges requires a proactive and collaborative approach. Effective communication, stakeholder engagement, and a thorough understanding of the project’s requirements and constraints are key to overcoming these challenges and successfully implementing VE in construction projects.
Examples of Successful “VE” Projects
Value Engineering (VE) has been implemented in numerous construction projects worldwide, resulting in significant cost savings, improved efficiency, and enhanced project outcomes. Here are a few notable examples of successful VE projects:
- Golden Gate Bridge Retrofit, San Francisco, USA: The iconic Golden Gate Bridge underwent a VE study to evaluate options for seismic retrofitting. By implementing VE recommendations, such as using innovative materials and construction techniques, the project achieved cost savings of over $125 million while ensuring the bridge’s structural integrity and improved resilience against earthquakes.
- Treasure Island Redevelopment, San Francisco, USA: The redevelopment of Treasure Island, a former naval base, incorporated VE throughout the planning and design stages. VE analysis helped optimize building layouts, identify cost-saving alternatives for utilities, and enhance sustainability measures. As a result, the project achieved significant cost savings without compromising its vision for creating an environmentally friendly and vibrant community.
- Burj Khalifa, Dubai, UAE: The Burj Khalifa, the world’s tallest skyscraper, utilized VE to maximize cost efficiencies while maintaining its iconic design and structural integrity. VE experts analyzed various options for materials, construction methods, and systems, resulting in substantial cost savings during construction. This helped ensure the project was delivered within budget while achieving its remarkable height and architectural excellence.
- Panama Canal Expansion, Panama: The Panama Canal expansion project employed VE to optimize the design and construction of the new locks. Through value engineering, the project team identified innovative solutions to reduce costs and improve efficiency while meeting the project’s objectives and accommodating larger vessel sizes. The successful implementation of VE resulted in enhanced project performance and increased capacity for global maritime trade.
- London Olympic Stadium, UK: The construction of the London Olympic Stadium for the 2012 Summer Olympics involved rigorous VE analysis. VE experts collaborated with the project team to find cost-effective solutions while maintaining the stadium’s architectural vision and meeting sustainability targets. The VE process resulted in significant cost savings and value enhancements, enabling the successful delivery of the world-class stadium on schedule.
These examples highlight the diverse applications and benefits of implementing VE in construction projects. From major infrastructure projects to iconic landmarks, VE has consistently delivered cost savings, improved efficiency, and enhanced project outcomes while maintaining the desired quality and functionality. These success stories serve as inspiring examples for future projects and demonstrate the value that VE can bring to the construction industry.
Conclusion
Value Engineering (VE) is a powerful approach that has revolutionized the construction industry. By focusing on optimizing value rather than solely reducing costs, VE enables construction professionals to deliver projects that meet or exceed stakeholders’ expectations while achieving significant cost savings.
In this article, we explored the meaning of VE in construction, its importance, common applications, benefits, challenges, and real-life project examples. We discovered that VE is a systematic and analytical process that evaluates functions, materials, methods, and systems to enhance the overall value proposition of a project while minimizing costs.
Through VE, construction professionals can identify cost-saving opportunities, enhance project performance, improve efficiency, mitigate risks, and increase stakeholder satisfaction. By involving stakeholders, promoting collaboration, and challenging conventional practices, VE fosters innovation and drives continuous improvement in the construction industry.
However, implementing VE is not without its challenges. Overcoming resistance to change, addressing limited awareness and understanding, managing time and resource constraints, and balancing cost, quality, and functionality are some of the hurdles that must be overcome to reap the benefits of VE fully.
Nevertheless, the examples of successful VE projects demonstrate that the efforts are well worth it. From the Golden Gate Bridge retrofit to the Burj Khalifa, these projects have achieved remarkable cost savings, improved efficiencies, and exceptional project outcomes by employing VE methodologies.
In conclusion, Value Engineering has become an indispensable tool in the construction industry. By embracing VE principles, construction professionals can optimize project outcomes, deliver cost-effective solutions, and enhance value for clients and stakeholders. As the construction landscape continues to evolve, the importance of VE in addressing the demands for efficiency, sustainability, and innovation cannot be underestimated.
Frequently Asked Questions about What Does "VE" Mean In Construction
Was this page helpful?
At Storables.com, we guarantee accurate and reliable information. Our content, validated by Expert Board Contributors, is crafted following stringent Editorial Policies. We're committed to providing you with well-researched, expert-backed insights for all your informational needs.
0 thoughts on “What Does “VE” Mean In Construction”