Home>diy>Building & Construction>What Is CIP In Construction
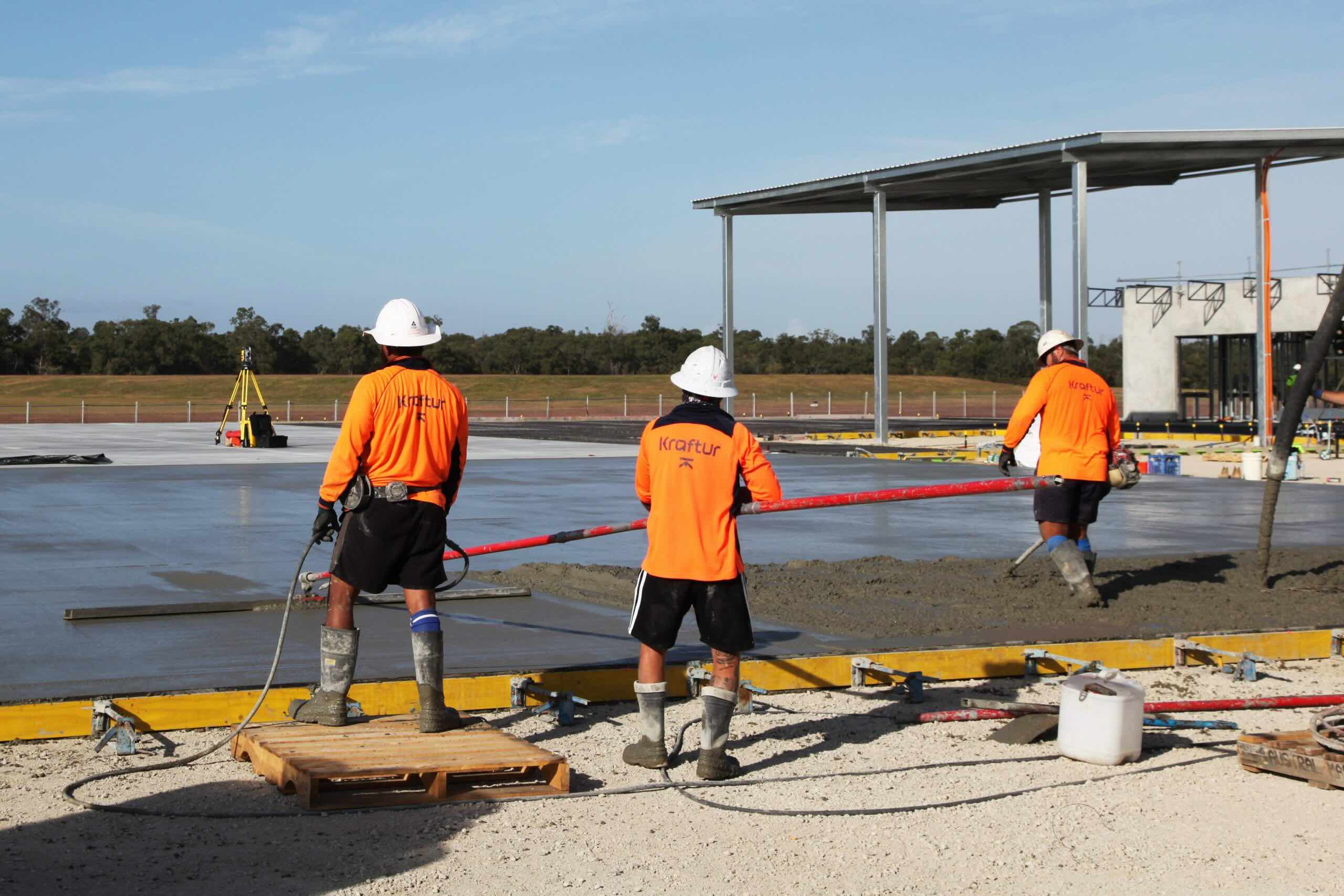
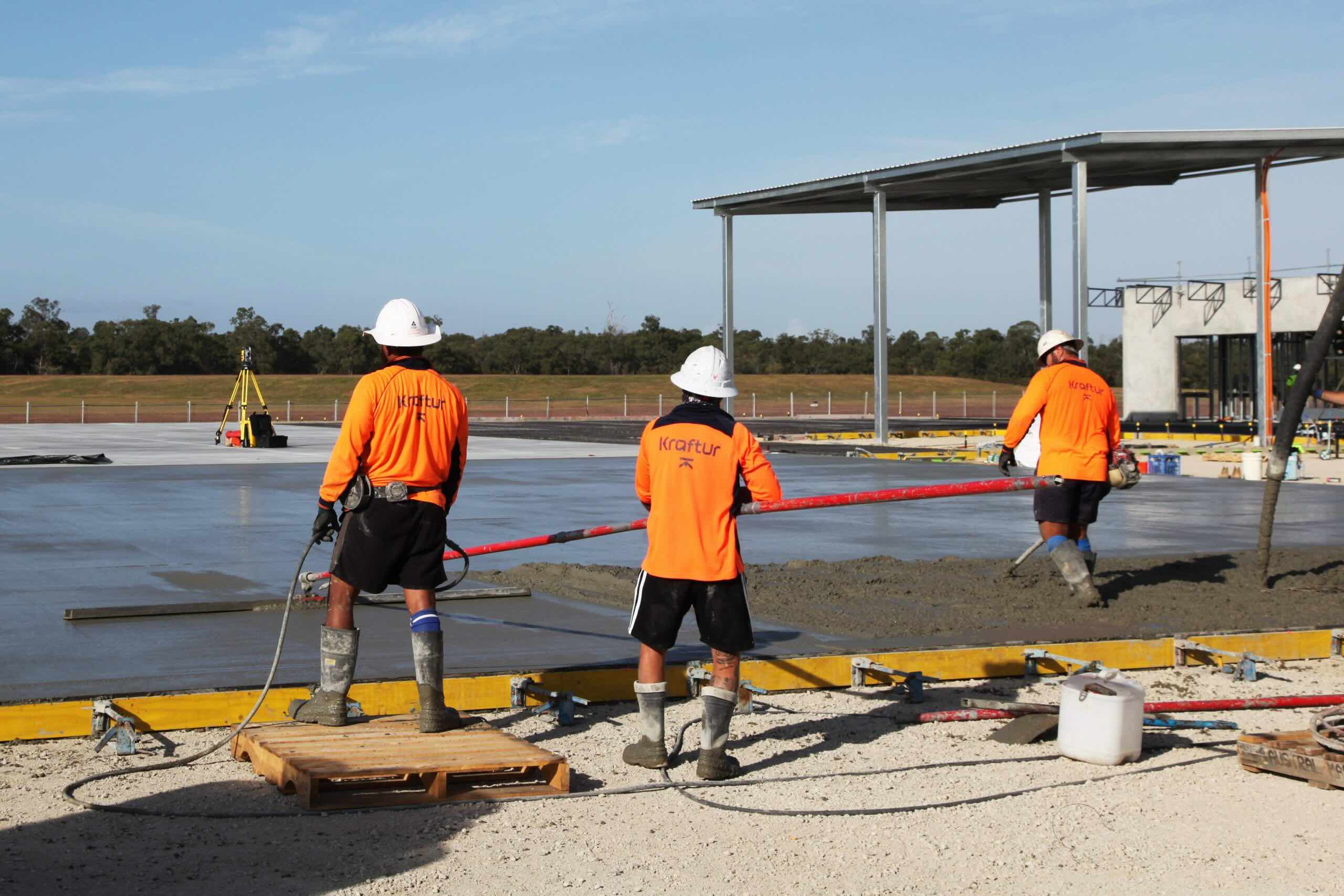
Building & Construction
What Is CIP In Construction
Modified: January 24, 2024
Learn about CIP (Cast-in-Place) in construction, a process widely used in building construction. Explore its benefits and applications.
(Many of the links in this article redirect to a specific reviewed product. Your purchase of these products through affiliate links helps to generate commission for Storables.com, at no extra cost. Learn more)
Introduction
Welcome to the world of construction! It is a dynamic and ever-evolving industry that plays a crucial role in shaping our modern society. Behind every impressive building or infrastructure project, there is a complex web of planning, designing, and execution. To ensure successful completion of these projects, construction professionals rely on various methodologies and techniques, one of which is known as CIP.
CIP, which stands for Construction in Progress, is a term commonly used in the construction industry to describe the ongoing work on a project. It encompasses all the activities, resources, and processes involved in the construction process from start to finish. CIP is not just limited to erecting physical structures; it also includes site preparation, project management, procurement, and the integration of various systems.
Construction in Progress is an integral part of the construction industry, as it allows projects to be effectively planned and executed. It provides a framework for managing resources, timelines, budgets, and quality control. CIP is not just a generic term; it refers to a systematic approach to construction that ensures efficiency, safety, and sustainability throughout the project.
This article aims to explore the concept of CIP in construction and shed light on its importance in the industry. We will delve into the definition of CIP, its purpose, benefits, challenges, and the steps involved in the CIP process. We will also showcase some successful case studies where CIP was implemented effectively to deliver outstanding construction projects.
Whether you are a construction professional, a project manager, or simply curious about the intricacies of the construction industry, this article will provide valuable insights into the world of Construction in Progress.
Key Takeaways:
- Construction in Progress (CIP) is a comprehensive approach that ensures efficient project planning, resource allocation, cost control, and quality assurance, leading to successful and timely completion of construction projects.
- Real-life case studies demonstrate the impactful implementation of CIP in iconic projects, showcasing how effective project management, resource allocation, and quality control contribute to outstanding construction outcomes.
Read more: What Is Pre-Construction In Construction
Definition of CIP in Construction
CIP, also known as Construction in Progress, refers to the ongoing work and activities involved in a construction project. It encompasses everything from the initial planning and design stages to the final completion and handover of the project. CIP involves the coordination and integration of various resources, including manpower, materials, equipment, and technologies, to ensure the successful execution of construction projects.
In simple terms, CIP is the entire process of transforming a construction concept into a physical reality. It covers all aspects of construction, including site preparation, excavation, foundation work, structural construction, electrical and plumbing installations, interior finishes, landscaping, and more.
CIP is not limited to the physical construction of buildings and structures. It also includes the management and coordination of various activities, such as project scheduling, cost estimation, procurement, risk management, quality control, and safety protocols. This comprehensive approach ensures that the project is completed on time, within budget, and to the highest standards of quality and safety.
Moreover, CIP incorporates the use of advanced technologies and construction methodologies to streamline the construction process and enhance productivity. These technologies include Building Information Modeling (BIM), which enables the creation of detailed 3D models for better visualization and coordination, as well as construction management software, which helps in project planning, resource allocation, and communication.
It’s important to note that CIP is not a standalone process, but rather an integrated approach that involves the collaboration of various stakeholders, such as architects, engineers, contractors, subcontractors, suppliers, and clients. Effective communication and coordination among these stakeholders are critical to ensure the smooth progress of the project and successful completion.
Overall, Construction in Progress (CIP) encompasses all the activities and resources required to transform a construction concept into a tangible structure. It’s a comprehensive approach that encompasses planning, design, execution, and management to ensure the successful delivery of construction projects.
Purpose of CIP in Construction
The purpose of Construction in Progress (CIP) in the construction industry is to provide a structured and organized approach to project management and execution. It serves several important purposes that contribute to the overall success of construction projects. Let’s explore some key purposes of CIP:
- Effective Project Planning: CIP facilitates thorough project planning, ensuring that all aspects of the construction project are carefully considered and accounted for. It involves defining the project scope, identifying objectives, setting timelines, establishing budgets, and allocating resources. By having a solid plan in place, CIP helps minimize potential delays, cost overruns, and conflicts that may arise during construction.
- Efficient Resource Allocation: One of the primary purposes of CIP is to optimize the allocation of resources, including labor, materials, equipment, and finances. Through effective resource management, CIP ensures that the right resources are available at the right time and in the right quantity. This minimizes wastage, maximizes productivity, and helps in controlling costs.
- Timely Project Completion: CIP aims to ensure that construction projects are completed within the specified timeframe. This requires careful scheduling, sequencing of activities, and monitoring of progress. By setting realistic timelines and closely monitoring project milestones, CIP helps avoid delays and keep the project on track for timely completion.
- Quality Control: Maintaining high-quality standards is a crucial aspect of construction projects. CIP implements quality control measures throughout the construction process to ensure that the final structure meets the required specifications and regulations. This includes conducting regular inspections, enforcing quality standards, and addressing any issues that may arise during construction.
- Risk Management: Construction projects are exposed to various risks and uncertainties. CIP helps identify potential risks, assess their impacts, and develop strategies to mitigate them. This includes implementing safety protocols, addressing environmental concerns, and managing legal and regulatory compliance. By proactively addressing risks, CIP enhances the overall project safety and minimizes the likelihood of costly setbacks.
These are just a few of the key purposes of CIP in construction. By providing a structured framework for project planning, resource allocation, timely completion, quality control, and risk management, CIP contributes to the smooth execution and successful delivery of construction projects.
Benefits of CIP in Construction Projects
Construction in Progress (CIP) brings numerous benefits to construction projects, ensuring their successful completion and delivering value to all stakeholders involved. Let’s explore some of the key benefits of implementing CIP:
- Improved Project Management: CIP provides a structured approach to project management, enabling better organization and coordination of various activities. It helps in defining project objectives, setting timelines, and allocating resources effectively. With a clear plan in place, project managers can monitor progress, identify bottlenecks early on, and make necessary adjustments to keep the project on track.
- Enhanced Cost Control: Proper cost management is crucial in construction projects. CIP allows for accurate estimation and tracking of costs throughout the project lifecycle. It helps in identifying potential cost overruns or unexpected expenses, enabling timely action to prevent them. By monitoring project costs closely, CIP helps in maintaining budgetary discipline and avoiding financial setbacks.
- Streamlined Resource Allocation: Efficient resource allocation is essential to ensure optimal utilization of available resources in construction projects. CIP helps in identifying resource requirements and allocating them efficiently. It minimizes resource wastage, ensures timely availability of materials and equipment, and assigns skilled labor to appropriate tasks. This leads to improved productivity and reduced downtime.
- Effective Risk Management: Construction projects are inherently exposed to various risks. CIP promotes proactive risk management by systematically identifying potential risks, assessing their impacts, and implementing appropriate mitigation strategies. This helps in minimizing the likelihood of accidents, delays, or legal issues. By addressing risks early on, CIP improves overall project safety and reduces potential liabilities.
- Enhanced Communication and Collaboration: Successful construction projects require effective communication and collaboration among all stakeholders involved. CIP fosters clear and transparent communication channels, ensuring that everyone is updated on project progress, changes, and challenges. It promotes collaboration between architects, engineers, contractors, suppliers, and clients, fostering a more cohesive and productive working environment.
- Improved Quality and Client Satisfaction: CIP prioritizes quality control throughout the construction process. It establishes quality standards, monitors adherence to specifications, and implements rigorous inspection processes. By ensuring that the final structure meets the desired quality and safety requirements, CIP enhances client satisfaction and builds a positive reputation for the construction project.
- Timely Project Completion: CIP focuses on efficient project scheduling and monitoring, ensuring that construction projects are completed within the specified timelines. By prioritizing timely completion, CIP helps in avoiding delays, minimizing project disruptions, and meeting client expectations. This leads to increased client satisfaction and contributes to the overall success of the project.
These are just a few of the many benefits of implementing CIP in construction projects. By enhancing project management, cost control, resource allocation, risk management, communication, quality, and timely completion, CIP plays a vital role in delivering successful construction projects that meet client expectations and stand the test of time.
Challenges in Implementing CIP in Construction
While Construction in Progress (CIP) offers numerous benefits to construction projects, its implementation does come with certain challenges. It’s important to be aware of these challenges in order to effectively address them and ensure a successful CIP implementation. Let’s explore some common challenges:
- Complex Project Coordination: Construction projects involve multiple stakeholders, including architects, engineers, contractors, subcontractors, suppliers, and clients. Coordinating and managing the activities of these diverse parties can be challenging, as each group may have different priorities, schedules, and communication styles. Effective project coordination and communication are essential to ensure that everyone is aligned and working towards the project’s goals.
- Uncertainty and Change: Construction projects are dynamic in nature, and changes are almost inevitable. These changes can result from design modifications, unexpected site conditions, or client revisions. Handling these changes effectively while minimizing disruptions to the project’s timeline and budget requires careful planning, proactive communication, and effective change management processes.
- Resource Constraints: Availability and allocation of resources are often a challenge in construction projects. This includes skilled labor, materials, equipment, and finances. Limited availability of resources can lead to delays or compromises in quality if not planned and managed properly. Project managers must carefully assess and plan for resource requirements to ensure smooth project execution.
- Technical Challenges: Construction projects often involve complex designs, advanced technologies, and intricate systems. Implementing and integrating these technical aspects can be challenging, requiring specialized knowledge and expertise. It’s important to have a team with the right skills and experience to handle the technical challenges that may arise during the construction process.
- Regulatory Compliance: Construction projects are subject to various regulations, permits, and codes. Ensuring compliance with these requirements can be complex, as regulations can differ based on project location, size, and type. Staying updated with the latest regulations and obtaining necessary permits and approvals is crucial to avoid potential legal and financial issues.
- Health and Safety: Construction sites are inherently hazardous environments. Maintaining high safety standards and ensuring the well-being of workers and visitors are top priorities. Implementing robust safety protocols, providing adequate training, and regularly conducting safety inspections are essential to mitigate the risks associated with construction activities.
- Budgetary Constraints: Construction projects are often governed by strict budgets. Staying within budget while meeting project requirements can be challenging, as unexpected costs may arise during the construction process. Accurate cost estimation, rigorous cost control practices, and proactive management of potential cost overruns are crucial to ensure the financial viability of the project.
Although implementing CIP in construction projects may present challenges, addressing these challenges with proper planning, communication, project management, and collaboration can lead to successful project outcomes. By identifying potential challenges and developing strategies to overcome them, construction professionals can navigate the complexities of CIP implementation and deliver exceptional construction projects.
CIP in construction stands for “Cast-In-Place,” which refers to concrete that is poured and formed on-site, as opposed to precast concrete elements. This method allows for greater flexibility and customization in construction projects.
Read more: What Is Construction
Steps in the CIP Process
The Construction in Progress (CIP) process involves a series of steps that guide the successful execution of construction projects. These steps provide a structured framework for project management, resource allocation, and timely completion. Let’s explore the key steps in the CIP process:
- Project Initiation: This is the initial phase where the project’s feasibility, objectives, and constraints are assessed. It involves conducting a thorough project feasibility study, which includes analyzing the site, market conditions, regulatory compliance, and financial considerations. This step helps in determining the viability of the project and setting the foundation for further planning.
- Project Planning: In this phase, a comprehensive plan is developed to outline the project’s scope, schedule, and budget. It involves defining project deliverables, identifying key stakeholders, and establishing clear communication channels. The project plan also includes risk assessment, quality control measures, and procurement strategies. This step lays the groundwork for the successful execution of the project.
- Design Development: The design development phase involves transforming the project concept into detailed design plans. It includes architectural, structural, electrical, and mechanical design, as well as coordination with engineers and specialists. Design development ensures that all aspects of the project are carefully considered and integrated into the final construction plans.
- Procurement and Resource Allocation: Once the design plans are finalized, the procurement process begins. This involves sourcing and procuring materials, equipment, and subcontracted services. Effective resource allocation is crucial at this stage to ensure timely availability of resources and maintain project schedules. This step also includes establishing contracts, negotiating prices, and managing supplier relationships.
- Construction Execution: This is the phase where the physical construction of the project takes place. It involves site preparation, excavation, foundation work, structural construction, installation of systems, and interior finishes. Proper project management, coordination, and supervision are essential during this phase to ensure that construction activities are carried out accurately, safely, and within the defined quality standards.
- Quality Control and Inspections: Throughout the construction process, regular quality control measures should be implemented to ensure compliance with project specifications and industry standards. This includes inspections, testing, and verification of materials, workmanship, and systems. Quality control is vital to ensure that the final structure meets the desired quality and safety requirements.
- Project Monitoring and Control: This step involves continuous monitoring of project progress, including tracking milestone achievements, monitoring project costs, and addressing any issues or deviations from the planned objectives. It includes regular progress meetings, performance evaluations, and adjustments to the project plan as needed. Effective project control ensures that the project stays on track and within budget.
- Project Handover and Closeout: The final step in the CIP process is the project handover and closeout. This involves formalizing the completion of the project, conducting final inspections, and addressing any outstanding issues or deficiencies. It also includes the handover of project documentation, warranties, and manuals to the client. Proper project closeout ensures a smooth transition from construction to the operational phase.
These steps provide a structured approach to the CIP process, ensuring effective project management, resource allocation, and timely completion. By following these steps, construction professionals can navigate the complexities of construction projects and deliver successful outcomes.
Key Components of CIP
Construction in Progress (CIP) comprises various key components that work together to ensure the successful execution of construction projects. These components encompass the essential elements necessary for effective project management, resource allocation, and timely completion. Let’s explore the key components of CIP:
- Project Scope and Objectives: Defining the project scope and objectives is a crucial component of CIP. It involves clearly outlining the desired outcomes, deliverables, and expectations of the project. This component helps in setting the direction for the project and ensuring alignment between stakeholders.
- Project Planning and Scheduling: This component involves developing a comprehensive plan and schedule to guide the project’s execution. It includes determining project timelines, milestones, and critical path activities. Effective planning and scheduling ensure that resources are allocated efficiently, and project activities are completed on time.
- Resource Allocation: Resource allocation involves the proper assignment and utilization of resources, including labor, materials, equipment, and finances. This component helps in optimizing resource utilization and minimizing wastage. Effective resource allocation ensures that the right resources are available when and where they are needed.
- Cost Estimation and Control: The cost estimation and control component involves accurately estimating the costs associated with the project and implementing measures to control and monitor expenses. It includes budgeting, tracking costs, managing change orders, and implementing cost control strategies. This component ensures that the project stays within the defined budget.
- Risk Management: Risk management is a critical component of CIP. It involves identifying potential risks, assessing their impact, implementing mitigation strategies, and regularly monitoring and managing risks throughout the project. Effective risk management minimizes the likelihood of disruptions, delays, and costly setbacks.
- Communication and Collaboration: Effective communication and collaboration among project stakeholders are vital for successful project execution. This component entails establishing clear communication channels, promoting transparency, and fostering collaboration between architects, engineers, contractors, suppliers, and clients. Open communication facilitates decision-making, issue resolution, and timely progress updates.
- Quality Control and Assurance: Ensuring high-quality standards is an essential component of CIP. It involves establishing quality control measures, conducting inspections, and implementing quality assurance processes throughout the construction process. This component ensures that the project meets the required specifications and complies with industry standards and regulations.
- Safety Protocols and Compliance: Safety is a paramount component of CIP. It involves implementing safety protocols, adhering to regulations, and creating a safe working environment for all project participants. This component includes conducting regular safety inspections, providing necessary training, and integrating safety measures into every aspect of the project.
- Change Management: Change is inevitable in construction projects. The change management component involves effectively managing and addressing changes that may arise during the project lifecycle. It includes a systematic approach to evaluating proposed changes, assessing their impact, and implementing necessary adjustments while minimizing disruptions to the project’s timeline and budget.
These key components collectively form the foundation of Construction in Progress (CIP). They provide a comprehensive framework for project management, resource allocation, risk mitigation, quality control, and collaboration, ensuring the successful execution of construction projects.
Importance of CIP in the Construction Industry
Construction in Progress (CIP) plays a crucial role in the construction industry, offering numerous benefits that contribute to the successful execution of construction projects. Let’s explore why CIP is important in the construction industry:
- Effective Project Management: CIP provides a structured approach to project management, ensuring that construction projects are planned, executed, and monitored effectively. It helps in defining project objectives, setting timelines, allocating resources, and managing risks. Effective project management ensures smooth project progress, minimizing delays, cost overruns, and conflicts.
- Optimized Resource Allocation: CIP allows for efficient allocation of resources, including labor, materials, equipment, and finances. By accurately assessing resource requirements and managing their allocation, construction professionals can optimize resource utilization, reduce wastage, and increase productivity. This maximizes the project’s efficiency and ensures timely project completion.
- Enhanced Cost Control: Construction projects are often governed by strict budgets. CIP helps control costs by identifying potential cost drivers, accurately estimating project expenses, and closely monitoring project expenditures. By implementing effective cost control measures, CIP helps in staying within budget and avoiding financial constraints that can jeopardize project success.
- Timely Project Completion: Meeting project timelines is a key priority in the construction industry. CIP emphasizes timely project completion by setting realistic schedules, identifying critical path activities, and closely monitoring project milestones. By proactively managing project timelines, CIP helps in minimizing delays, meeting client expectations, and maintaining a competitive edge.
- Quality Control and Assurance: CIP prioritizes rigorous quality control measures throughout the construction process. It involves implementing quality standards, conducting inspections, and ensuring compliance with regulations and industry best practices. By emphasizing quality assurance, CIP helps in delivering construction projects that meet or exceed client expectations and enhance the industry’s reputation.
- Enhanced Safety: Construction sites are inherently hazardous, and safety should always be a top priority. CIP promotes the implementation of robust safety protocols, training programs, and regular inspections to ensure a safe working environment. By prioritizing safety, CIP helps in mitigating risks, protecting workers’ well-being, and reducing the likelihood of accidents or injuries.
- Effective Communication and Collaboration: Successful construction projects rely on effective communication and collaboration among project stakeholders. CIP fosters clear communication channels, facilitates collaboration, and encourages information sharing. By enhancing communication, CIP enables better coordination, issue resolution, and timely decision-making, leading to smoother project progress.
- Continual Improvement and Lessons Learned: CIP promotes a culture of continual improvement in the construction industry. It encourages project teams to reflect on past projects, identify lessons learned, and implement improvements in future projects. This component allows for the accumulation of industry knowledge and best practices, leading to increased efficiency, reduced risks, and improved project outcomes.
The importance of Construction in Progress (CIP) in the construction industry cannot be overstated. By emphasizing effective project management, optimized resource allocation, cost control, timely completion, quality assurance, safety, communication, and continual improvement, CIP plays a pivotal role in delivering successful construction projects that meet client expectations and contribute to the industry’s growth and development.
Case Studies on Successful CIP Implementations
Real-life case studies provide valuable insights into the successful implementation of Construction in Progress (CIP) in the construction industry. Let’s explore a few examples of projects where CIP was effectively utilized to deliver exceptional outcomes:
- Case Study 1: The Burj Khalifa, Dubai: The Burj Khalifa is an iconic skyscraper and the tallest structure in the world, located in Dubai, United Arab Emirates. The construction of this architectural marvel involved meticulous planning and CIP implementation. The project team utilized advanced technologies like Building Information Modeling (BIM) to optimize the project’s design, coordination, and resource allocation. Through effective project management, cost control, and quality assurance, the Burj Khalifa was completed on schedule, standing as a testament to the successful implementation of CIP.
- Case Study 2: The Panama Canal Expansion Project: The expansion of the Panama Canal was a massive infrastructure project aimed at increasing the canal’s capacity to accommodate larger vessels. The project involved complex engineering, resource management, and coordination. CIP played a crucial role in the successful completion of this project, enabling effective project planning, timely procurement of materials and equipment, and efficient resource allocation. Additionally, stringent quality control measures were implemented to ensure compliance with international standards. The completion of the Panama Canal expansion project demonstrates the importance of CIP in delivering large-scale infrastructure projects.
- Case Study 3: The High Line, New York City: The High Line is an elevated linear park built on a historic freight rail line in New York City. This project involved repurposing an existing structure into a public park, requiring careful planning, design development, and construction execution. CIP was utilized to manage the transformation of the rail line, project scheduling, resource allocation, and quality control. The success of the High Line project highlights how CIP can be effectively employed in adaptive reuse projects to revitalize urban spaces and create sustainable public amenities.
- Case Study 4: The Terminal 5, Heathrow Airport: Terminal 5 at Heathrow Airport in London is one of the world’s busiest airport terminals. The construction of this massive transportation hub involved multiple phases and diverse stakeholders. CIP played a vital role in managing the complex construction process, resource allocation, and project coordination. By implementing robust safety measures, ensuring quality control, and prioritizing effective communication, the Terminal 5 project was successfully completed, enhancing passenger experience and airport efficiency.
- Case Study 5: The Olympic Stadium, Beijing: The construction of the Olympic Stadium, also known as the Bird’s Nest, for the 2008 Beijing Olympics exemplifies successful CIP implementation. The project showcased advanced engineering, innovative design, and effective management of resources. CIP was instrumental in coordinating the construction activities, optimizing resource allocation, and maintaining a tight project schedule. The Bird’s Nest stands as an architectural masterpiece and a testament to the successful implementation of CIP in delivering high-profile sports facilities.
These case studies illustrate the successful utilization of CIP in various construction projects, ranging from iconic skyscrapers to infrastructure expansions and adaptive reuse projects. Through effective project management, resource allocation, cost control, quality assurance, and collaboration, these projects demonstrate the importance of CIP in delivering outstanding construction outcomes.
Read more: What Is A Buyout In Construction
Conclusion
Construction in Progress (CIP) is a fundamental concept in the construction industry, encompassing the entire lifecycle of construction projects. From the initial planning and design stages to the final completion and handover, CIP provides a structured framework for project management, resource allocation, and timely execution.
Throughout this article, we have explored the various components and benefits of CIP in the construction industry. We have learned that CIP plays a vital role in effective project planning, resource allocation, cost control, and quality assurance. It facilitates efficient communication, collaboration, and risk management. Moreover, CIP ensures the timely completion of construction projects while maintaining the highest standards of safety and compliance.
By implementing CIP, construction professionals can optimize resource utilization, minimize delays, and control costs, all while delivering projects that meet client expectations. CIP enables better project coordination, effective communication, and collaboration among stakeholders, resulting in successful outcomes.
The case studies discussed further highlight the significance and impact of CIP in real-life construction projects. From the Burj Khalifa to the Panama Canal expansion, these examples demonstrate how CIP has been successfully employed to manage diverse projects, ranging from iconic skyscrapers to large-scale infrastructure developments. Through proper project planning, resource management, and quality control, these projects have set new benchmarks for the construction industry.
In a constantly evolving and competitive industry, the importance of CIP cannot be overstated. By embracing a structured and systematic approach, construction professionals can overcome challenges, minimize risks, and deliver projects of the highest standards. CIP serves as a guiding principle to ensure that construction projects are executed efficiently, safely, and with a focus on quality.
In conclusion, Construction in Progress (CIP) is not just a term; it is a fundamental concept that drives the success of construction projects. By incorporating CIP into project management practices, construction professionals can achieve efficiency, transparency, and client satisfaction, while contributing to the growth and development of the construction industry as a whole.
Frequently Asked Questions about What Is CIP In Construction
Was this page helpful?
At Storables.com, we guarantee accurate and reliable information. Our content, validated by Expert Board Contributors, is crafted following stringent Editorial Policies. We're committed to providing you with well-researched, expert-backed insights for all your informational needs.
0 thoughts on “What Is CIP In Construction”