Home>diy>Building & Construction>What Is ERP In Construction
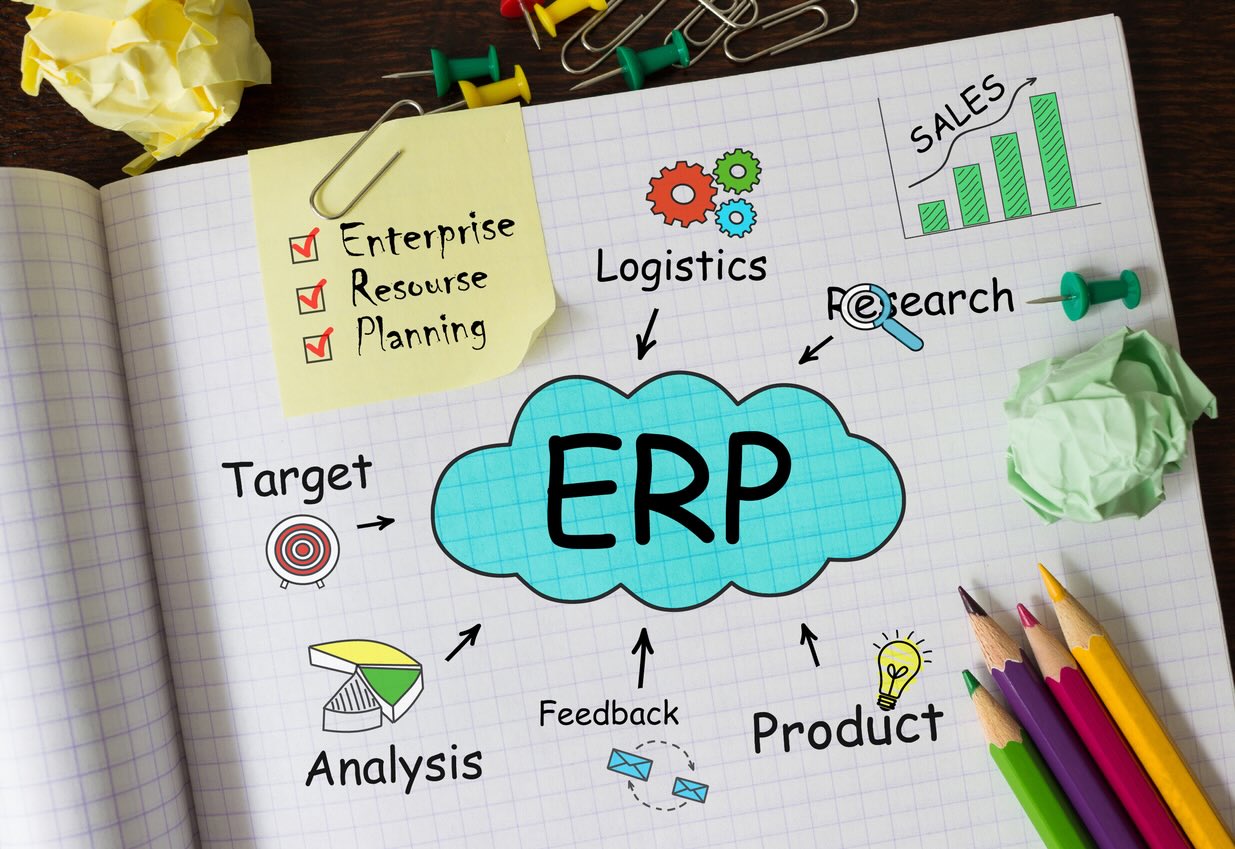
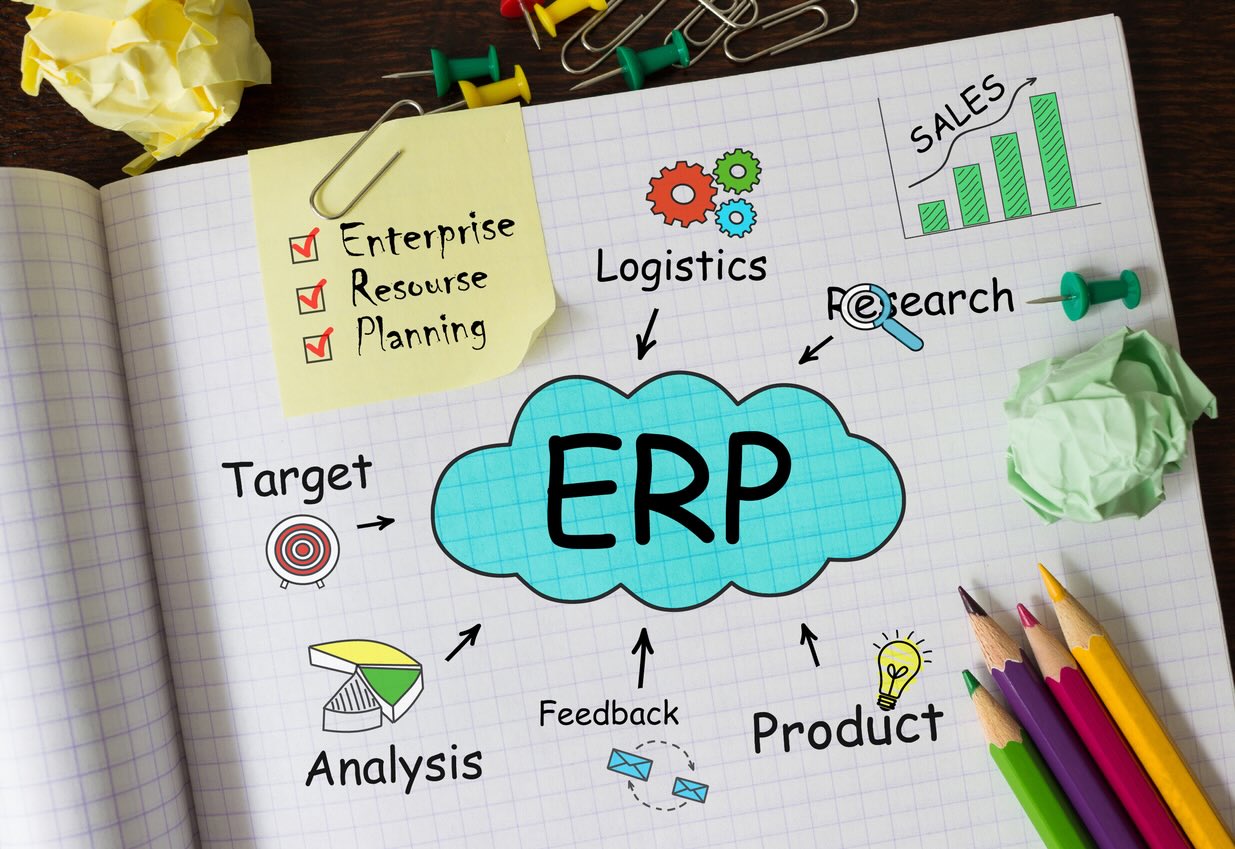
Building & Construction
What Is ERP In Construction
Modified: January 6, 2024
Discover the importance of ERP in construction and how it revolutionizes building-construction processes. Streamline operations, increase efficiency, and stay ahead in the competitive construction industry.
(Many of the links in this article redirect to a specific reviewed product. Your purchase of these products through affiliate links helps to generate commission for Storables.com, at no extra cost. Learn more)
Introduction
Welcome to the world of ERP in the construction industry. In the fast-paced and dynamic realm of construction, efficiency and productivity are paramount. As technology continues to advance, it has become imperative for construction companies to embrace innovative solutions to streamline their operations and maximize their profitability. This is where Enterprise Resource Planning (ERP) comes into play.
ERP is a comprehensive software solution that integrates various business processes and functions within an organization. It provides a centralized platform for managing and coordinating key business activities, such as project management, financial accounting, procurement, inventory management, human resources, and more. In the construction industry, ERP systems are specifically tailored to cater to the unique needs and challenges of the sector.
Implementing an ERP system in the construction industry can bring about significant advantages and drive growth for companies. It enables seamless collaboration between different departments, improves project management capabilities, enhances cost control and efficiency, and provides real-time visibility into project progress and financial performance.
In this article, we will delve deeper into the importance of ERP in the construction industry, discuss the benefits of its implementation, explore the challenges that may arise, highlight key features of construction ERP systems, present case studies of successful implementations, and provide best practices for a successful ERP integration. Let’s dive in!
Key Takeaways:
- ERP systems revolutionize construction operations by providing real-time visibility, enhancing collaboration, and optimizing resource allocation. They drive efficiency, cost control, and informed decision-making for sustainable growth and success.
- Successful ERP implementation in construction requires clear objectives, stakeholder involvement, thorough vendor evaluation, comprehensive training, and continuous improvement. It empowers companies to streamline processes, improve collaboration, and drive growth in a competitive industry.
Definition of ERP
Enterprise Resource Planning, commonly known as ERP, refers to a comprehensive software system that integrates various facets of a company’s operations into a unified platform. It enables organizations to automate and streamline their business processes, enhance communication and collaboration, and improve overall efficiency.
In the context of the construction industry, ERP systems are specifically designed to cater to the unique needs and challenges of construction companies. These systems efficiently manage various aspects of construction projects, including project planning and management, resource allocation, cost control, procurement, financial accounting, and human resources.
An ERP system in the construction industry typically comprises modules that work together to provide a cohesive solution. These modules can include:
- Project Management: Allows companies to effectively plan, track, and manage all activities associated with construction projects. It includes features such as scheduling, document management, collaboration tools, and budget tracking.
- Financial Management: Handles all financial aspects of the construction projects, such as budgeting, cost estimation, invoicing, accounts payable and receivable, and financial reporting.
- Procurement and Inventory Management: Helps manage the procurement process including vendor management, purchase orders, inventory tracking, and materials management.
- Human Resource Management: Manages employee information, payroll, attendance tracking, and workforce allocation.
- Equipment and Asset Management: Tracks and manages construction equipment and assets, including maintenance schedules, utilization, and depreciation.
By integrating these modules into a single system, ERP in the construction industry enables companies to have real-time visibility and control over all critical aspects of their projects. It facilitates efficient resource allocation, cost management, project planning, and decision-making.
Furthermore, ERP systems often utilize advanced technologies such as cloud computing, mobile applications, and artificial intelligence to provide construction companies with enhanced functionality, flexibility, and accessibility. This allows key stakeholders to access relevant project information anytime, anywhere, and make informed decisions on the go.
In summary, ERP systems in the construction industry revolutionize the way construction companies operate by providing a unified platform for managing projects, finances, resources, and more. It helps companies optimize their processes, reduce costs, improve productivity, and ultimately drive success in a competitive industry.
Importance of ERP in the Construction Industry
The construction industry, with its complex and intricate processes, can greatly benefit from the implementation of an ERP system. Here are some key reasons why ERP is important in the construction industry:
- Efficient Project Management: Construction projects involve multiple tasks, stakeholders, and resources. An ERP system enables companies to effectively plan, schedule, and manage every aspect of a project, including timelines, budgets, materials, and manpower. It provides real-time updates, allowing project managers to identify and address issues promptly and ensure smooth project execution.
- Streamlined Communication and Collaboration: In construction, effective communication and collaboration are crucial for success. ERP systems facilitate seamless collaboration between various departments and stakeholders, as all relevant project information and documents are stored in a centralized database. This ensures that everyone is working with the latest information, leading to better coordination and informed decision-making.
- Improved Financial Control: Construction projects involve significant financial investments and managing project finances can be challenging. ERP systems provide robust financial management modules that enable companies to track project costs, generate accurate financial reports, control expenses, and ensure that projects stay within budget. This leads to improved cost control and better financial visibility.
- Enhanced Resource Allocation: Efficient resource allocation is crucial in construction projects to optimize productivity and minimize wastage. ERP systems provide insights into resource availability, workload, and utilization, allowing companies to allocate resources effectively. This helps in avoiding overstaffing or understaffing situations and ensures that the right resources are deployed at the right time.
- Better Regulatory Compliance: Construction companies need to comply with various regulations and industry standards. ERP systems streamline compliance processes by automating documentation, tracking permits, and ensuring adherence to safety and quality standards. This minimizes the risk of non-compliance, penalties, and legal issues.
- Real-Time Reporting and Analytics: ERP systems provide robust reporting and analytics capabilities, allowing companies to generate real-time insights into project performance, financial metrics, resource utilization, and more. This enables data-driven decision-making, helps identify trends and areas for improvement, and enables timely corrective actions.
- Business Process Optimization: ERP systems optimize business processes by eliminating manual and redundant tasks, reducing paperwork, and increasing operational efficiency. This frees up time for employees to focus on more value-added activities and enhances overall productivity.
In summary, ERP in the construction industry is instrumental in optimizing project management, fostering collaboration, improving financial control, enabling efficient resource allocation, ensuring regulatory compliance, and providing real-time insights. By leveraging an ERP system, construction companies can enhance their competitiveness, deliver projects more efficiently, and achieve greater profitability.
Benefits of Implementing ERP in Construction
The implementation of an ERP system in the construction industry offers numerous benefits that can positively impact the efficiency and profitability of companies. Here are some key benefits of implementing ERP in construction:
- Improved Project Planning and Execution: ERP systems provide comprehensive project management tools that enable companies to plan and execute construction projects with greater precision. It allows for accurate scheduling, resource allocation, and cost estimation, leading to improved project timelines, reduced delays, and increased client satisfaction.
- Streamlined Communication and Collaboration: ERP systems facilitate seamless communication and collaboration between different departments and stakeholders involved in construction projects. It provides a centralized platform where project information, documents, and updates are stored, ensuring that all parties have access to the latest information. This leads to improved coordination and better decision-making.
- Enhanced Cost Control: Cost control is critical in the construction industry, and ERP systems play a vital role in monitoring and managing project costs. By providing real-time visibility into project expenses, inventory, and financial data, companies can identify cost-saving opportunities, reduce wastage, and make informed decisions to keep projects within budget.
- Optimized Resource Management: ERP systems enable construction companies to efficiently allocate and manage resources such as labor, equipment, and materials. Companies can track resource availability, utilization, and performance, ensuring that the right resources are allocated to each project at the right time. This leads to improved productivity, reduced downtime, and better resource utilization.
- Efficient Procurement and Inventory Management: With ERP systems, construction companies can streamline their procurement processes, including vendor management, purchase orders, and invoice tracking. ERP systems also help manage inventory efficiently by tracking material quantities, managing stock levels, and automating reordering processes. This results in reduced procurement cycle times, minimized stockouts, and better inventory control.
- Real-Time Reporting and Analytics: ERP systems provide robust reporting and analytics capabilities, allowing construction companies to generate real-time insights into various aspects of their business, such as project performance, financial metrics, and resource utilization. This enables data-driven decision-making, helps identify trends, and empowers companies to take proactive measures for continuous improvement.
- Improved Compliance and Risk Management: Construction projects involve complying with various regulations and managing potential risks. ERP systems help streamline compliance processes by automating documentation, tracking permits, and enforcing safety and quality standards. This minimizes the risk of non-compliance, penalties, and potential litigation.
By leveraging the benefits of ERP in construction, companies can enhance their project management capabilities, improve communication and collaboration, optimize costs and resources, streamline procurement and inventory management, make informed decisions, and ensure compliance and risk mitigation. Ultimately, implementing an ERP system can position construction companies for sustainable growth and success in a highly competitive industry.
Challenges of Implementing ERP in Construction
While implementing an ERP system in the construction industry offers numerous benefits, it is not without its challenges. The unique nature of the construction industry presents some specific hurdles that need to be addressed during the ERP implementation process. Here are some of the common challenges faced:
- Complexity of Construction Processes: Construction projects involve a wide range of intricate and interconnected tasks. Implementing an ERP system requires a deep understanding of these processes and the ability to map them accurately to the system. It can be challenging to capture the nuances of construction-specific workflows in the software.
- Data Integration and Migration: Construction companies often have large volumes of data spread across different systems, spreadsheets, or even paper documents. Migrating this data into the ERP system and ensuring smooth integration with existing systems can be complex and time-consuming. Data cleansing, formatting, and validation are crucial steps that need to be carefully executed.
- User Adoption: The success of any ERP system implementation depends on user acceptance and adoption. Construction employees, especially those who are accustomed to traditional manual processes, may resist the change and find it difficult to adapt to the new system. Adequate training, communication, and change management strategies are essential to address this challenge.
- Customization and Configuration: Construction companies have unique requirements and workflows that may not be fully addressed by off-the-shelf ERP solutions. Customizing and configuring the software to meet specific needs can be complex and may require technical expertise. Balancing customization with standardization is crucial to ensure a scalable and maintainable ERP system.
- Data Security and Privacy: Construction projects involve sensitive and confidential information, such as financial data, contracts, and intellectual property. Ensuring the security and privacy of this data within the ERP system is essential. Robust data security measures, user access controls, and compliance with data protection regulations are critical considerations in ERP implementation.
- Integration with Third-Party Systems: Construction companies often rely on specialized software and tools for tasks such as project design, scheduling, and building information modeling (BIM). Integrating ERP systems with these third-party systems to ensure seamless data flow and interoperability can be challenging, requiring careful planning and coordination.
- Scalability and Flexibility: The construction industry is known for its dynamic nature, with projects of varying sizes, complexities, and durations. An ERP system should be scalable and flexible enough to accommodate evolving business needs and handle multiple concurrent projects. Ensuring that the chosen ERP system can grow and adapt with the company is crucial.
Overcoming these challenges requires careful planning, stakeholder involvement, and a well-executed ERP implementation strategy. Engaging the right ERP vendor with construction industry expertise can also help address these challenges effectively.
By proactively addressing these challenges and leveraging the benefits of ERP, construction companies can overcome operational hurdles, streamline processes, improve collaboration, and drive growth and success in an increasingly competitive industry.
Read more: What Is Construction
Key Features of ERP in Construction
ERP systems in the construction industry come equipped with a range of features and functionalities tailored to meet the unique requirements of construction companies. Here are some key features to look for in an ERP system for construction:
- Project Management: A robust project management module is essential for construction ERP systems. It should enable companies to create and manage project schedules, track milestones and deliverables, allocate resources, monitor progress, and generate real-time reports. Integrated document management and collaboration tools are also important for efficient project communication and coordination.
- Financial Management: A comprehensive financial management module allows construction companies to manage their finances effectively. It should include features such as budgeting, cost estimation, expense tracking, invoicing, accounts payable and receivable, payroll management, and financial reporting. The module should provide real-time financial insights and ensure compliance with accounting regulations.
- Procurement and Inventory Management: Construction projects require effective procurement and inventory management. An ERP system should have features to manage vendor relationships, generate purchase orders, track materials and supplies, and automate inventory replenishment. Integration with suppliers and seamless communication for efficient procurement processes is a key feature to consider.
- Human Resource Management: Construction ERP systems should have a dedicated module for managing human resources. This module should handle employee information, time and attendance tracking, payroll management, workforce scheduling, and performance evaluation. It should also facilitate resource allocation and help manage labor costs.
- Equipment and Asset Management: Construction companies rely heavily on equipment and asset tracking. An ERP system should have the ability to manage equipment and asset inventory, track maintenance schedules, monitor utilization and depreciation, and generate reports on equipment performance and availability.
- Bidding and Estimating: A comprehensive ERP system for construction should include features for bidding and estimating. This includes functionality to create and manage bids, generate accurate cost estimates based on project specifications, track bid status, and analyze profitability. Integration with project management and financial modules is important to ensure seamless project execution.
- Reporting and Analytics: An effective ERP system should provide robust reporting and analytics capabilities. This includes the ability to generate real-time reports on project progress, financial metrics, resource utilization, and more. Interactive dashboards and customizable reports enable data-driven decision-making and provide actionable insights for continuous improvement.
- Mobile Access and Integration: In the modern construction industry, remote access and integration are vital. A construction ERP system should have mobile capabilities to allow users to access project information, update data, and collaborate on the go. Seamless integration with third-party applications such as design software, BIM tools, and scheduling software is also important for efficient data exchange.
When selecting an ERP system for construction, it is important to assess the specific needs of your company and ensure that the chosen system provides the necessary features and functionality to support your business processes. A comprehensive and well-integrated ERP system that caters to the unique requirements of the construction industry can streamline operations, improve efficiency, and ultimately drive success in this competitive sector.
Tip: When implementing an ERP system in construction, ensure that it is tailored to the specific needs of the industry, such as project management, resource allocation, and compliance with regulations.
Case Studies of Successful ERP Implementation in Construction
Implementing an ERP system in the construction industry can yield significant benefits and drive success for companies. Let’s take a look at two case studies that highlight successful ERP implementations in the construction sector:
Case Study 1: ABC Construction Company
ABC Construction Company, a leading player in the construction industry, faced challenges with disparate systems and manual processes that hindered project efficiency and collaboration. They decided to implement an ERP system to streamline their operations and enhance project management capabilities.
The ERP implementation included modules for project management, financial management, procurement, and document management. The project management module allowed ABC Construction Company to centralize project data, automate scheduling, and collaborate effectively among teams and stakeholders. The financial management module enabled real-time tracking of project costs, invoicing, and financial reporting. The procurement module streamlined vendor management and automated the procurement process, resulting in cost savings and improved efficiency.
As a result of the ERP implementation, ABC Construction Company experienced significant improvements in project delivery timelines, cost control, and collaboration. They achieved greater visibility into project data, improved resource allocation, and increased financial accuracy. The ERP system provided real-time reporting and analytics, enabling data-driven decision-making and enhancing overall operational efficiency.
Case Study 2: XYZ Builders
XYZ Builders, a mid-sized construction company, struggled with manual processes and lack of integration among their systems. This led to delays, cost overruns, and challenges in tracking project financials. They decided to implement an ERP system to overcome these obstacles and achieve better project control.
The ERP implementation for XYZ Builders included modules for project management, financial management, and procurement. The project management module provided a centralized platform for planning, scheduling, and tracking project activities. The financial management module enabled accurate tracking of project costs, billing, and financial reporting. The procurement module streamlined vendor management, automated purchase orders and invoicing, and improved inventory control.
With the ERP system in place, XYZ Builders experienced improved project visibility and control. They were able to track project costs in real-time, reduce delays, and make informed decisions to keep projects within budget. The centralized platform facilitated collaboration among stakeholders, resulting in better communication, streamlined workflows, and enhanced productivity.
These case studies demonstrate the successful implementation of ERP systems in the construction industry. Through efficient project management, enhanced financial control, streamlined procurement, and improved collaboration, these companies achieved greater efficiency, profitability, and customer satisfaction.
It is important to note that the success of ERP implementations in construction depends on various factors, such as careful planning, effective change management, and selecting the right ERP system that aligns with the company’s specific needs. Thorough evaluation, proper training, and continuous support are also essential to ensure a smooth transition and ongoing success with the implemented ERP system.
Read more: What Is Retrofit In Construction
Best Practices for Implementing ERP in Construction
Implementing an ERP system in the construction industry is a significant undertaking that requires careful planning, management, and execution. To ensure a successful implementation, here are some best practices to follow:
- Define Clear Objectives and Requirements: Begin by clearly defining the objectives and specific requirements for implementing an ERP system. Identify pain points, desired outcomes, and key metrics for success. This will help in selecting the right ERP solution and setting realistic expectations.
- Involve Stakeholders at Every Stage: Engage all relevant stakeholders, including project managers, finance teams, IT personnel, and end-users, in the ERP implementation process. Get their inputs, address concerns, and ensure their commitment to the project. Their involvement will foster ownership and promote user adoption.
- Thoroughly Evaluate ERP Vendors: Conduct a thorough evaluation of ERP vendors and select a solution that is specifically designed for the construction industry. Look for industry-specific features, track record, customer reviews, and vendor support capabilities. Request demos and compare multiple options before making a decision.
- Plan for Data Migration and Integration: Develop a comprehensive plan for data migration from existing systems to the ERP system. Ensure data accuracy, cleanliness, and compatibility. Plan for integration with third-party applications such as design software, scheduling tools, and financial systems.
- Invest in Training and Change Management: Provide comprehensive training to all employees affected by the ERP implementation. Communicate the benefits of the new system and manage expectations. Address resistance to change and empower employees to embrace the new technology. Offer ongoing support and continuous training as needed.
- Conduct Pilot Testing: Prior to full-scale implementation, conduct pilot testing with a small group of users. Identify any issues, validate workflows, and make necessary adjustments. Use feedback from the pilot phase to refine the system and ensure a smooth transition during the broader implementation.
- Ensure User-Friendly Interface: Choose an ERP system with an intuitive and user-friendly interface. Construction professionals may not be experienced with complex software, so simplicity and ease of use are crucial for user adoption and efficiency. Consider mobile accessibility to enable on-site access and collaboration.
- Establish Continuous Improvement Processes: Implementing an ERP system is a starting point, but continuous improvement is essential. Regularly assess system performance, monitor key metrics, and seek feedback from users. Encourage user suggestions for system enhancements and prioritize system updates accordingly.
- Collaborate with ERP Vendor: Foster a strong partnership with the ERP vendor throughout the implementation process. Engage their expertise to ensure optimal configuration, address technical challenges, and leverage their support network. Regularly communicate with the vendor to address any issues or system updates.
By following these best practices, construction companies can increase the chances of a successful ERP implementation. Through careful planning, stakeholder engagement, proper training, and continuous improvement, companies can streamline operations, improve collaboration, enhance financial control, and drive growth through the efficient use of an ERP system.
Conclusion
Implementing an ERP system in the construction industry can be a game-changer for companies seeking to improve efficiency, project management, collaboration, and financial control. The benefits of ERP in construction are vast, ranging from streamlined processes and enhanced resource management to better cost control and improved decision-making.
Throughout this article, we have explored the importance of ERP in the construction industry, the key features to look for, and the challenges that organizations may face during implementation. We also examined real-life case studies of successful ERP implementations, showcasing the positive impact it can have on construction companies.
To successfully implement an ERP system in construction, it is crucial to define clear objectives, engage stakeholders, and select an ERP solution specifically tailored to the industry’s unique needs. Thorough evaluation of vendors, proper planning for data migration and integration, and comprehensive training and change management are essential for a successful implementation.
Continuous improvement should be a focus post-implementation, with regular monitoring and assessment to optimize system performance and user satisfaction. Collaboration with the ERP vendor and establishing a strong partnership will ensure ongoing support and maintenance of the system.
Ultimately, the successful implementation of an ERP system in construction can position companies for growth, increase operational efficiency, and deliver projects more effectively. It enables seamless communication, improves resource allocation, enhances cost control, and provides real-time visibility into project progress and financial performance.
As the construction industry continues to evolve, embracing technology and leveraging ERP systems will become increasingly crucial for companies to stay competitive and thrive in this dynamic sector. By leveraging the benefits of ERP in construction, organizations can streamline their operations, achieve better project outcomes, and drive success in the ever-evolving construction landscape.
Frequently Asked Questions about What Is ERP In Construction
Was this page helpful?
At Storables.com, we guarantee accurate and reliable information. Our content, validated by Expert Board Contributors, is crafted following stringent Editorial Policies. We're committed to providing you with well-researched, expert-backed insights for all your informational needs.
0 thoughts on “What Is ERP In Construction”