Home>diy>Building & Construction>What Is Snagging In Construction
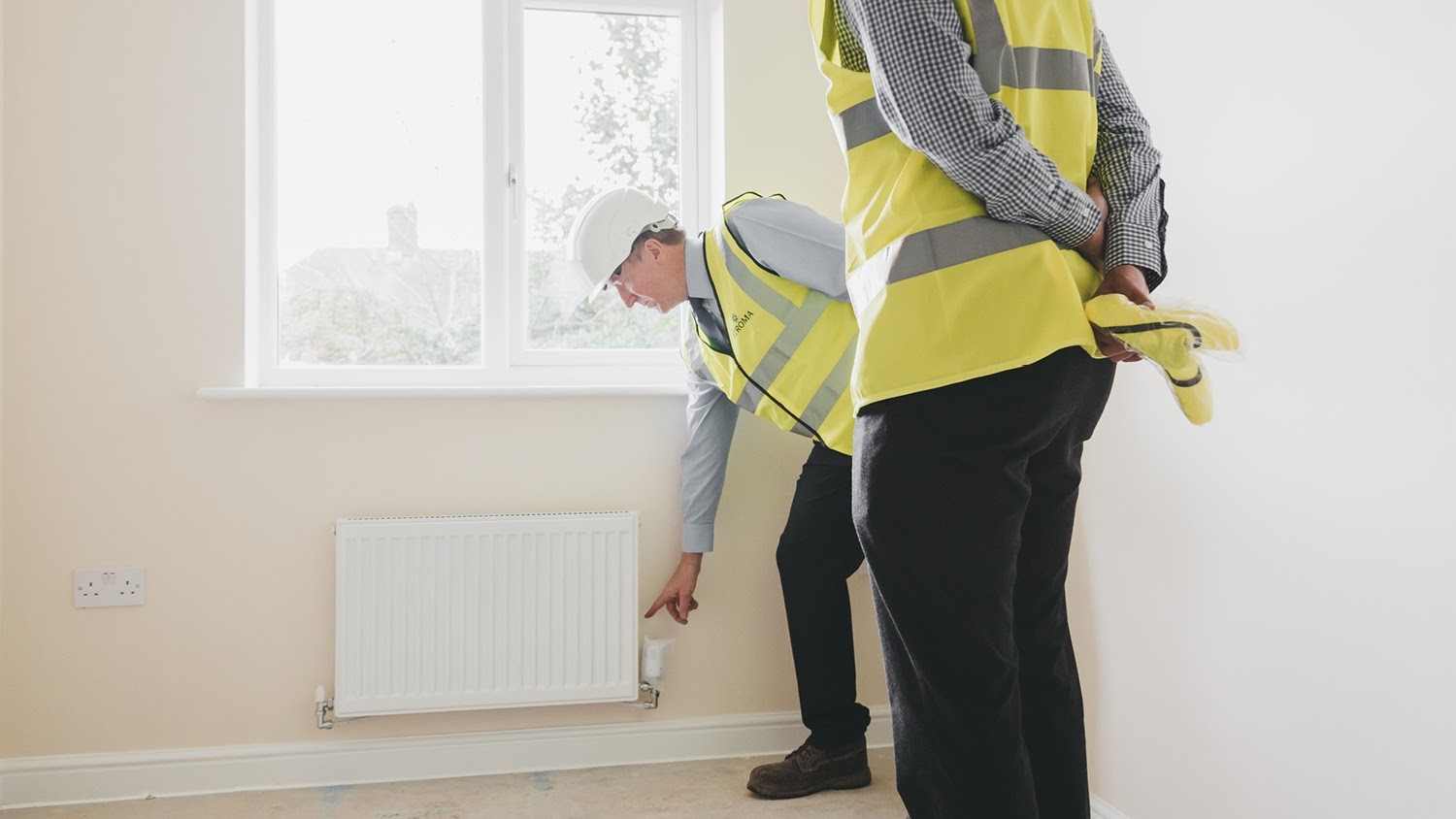
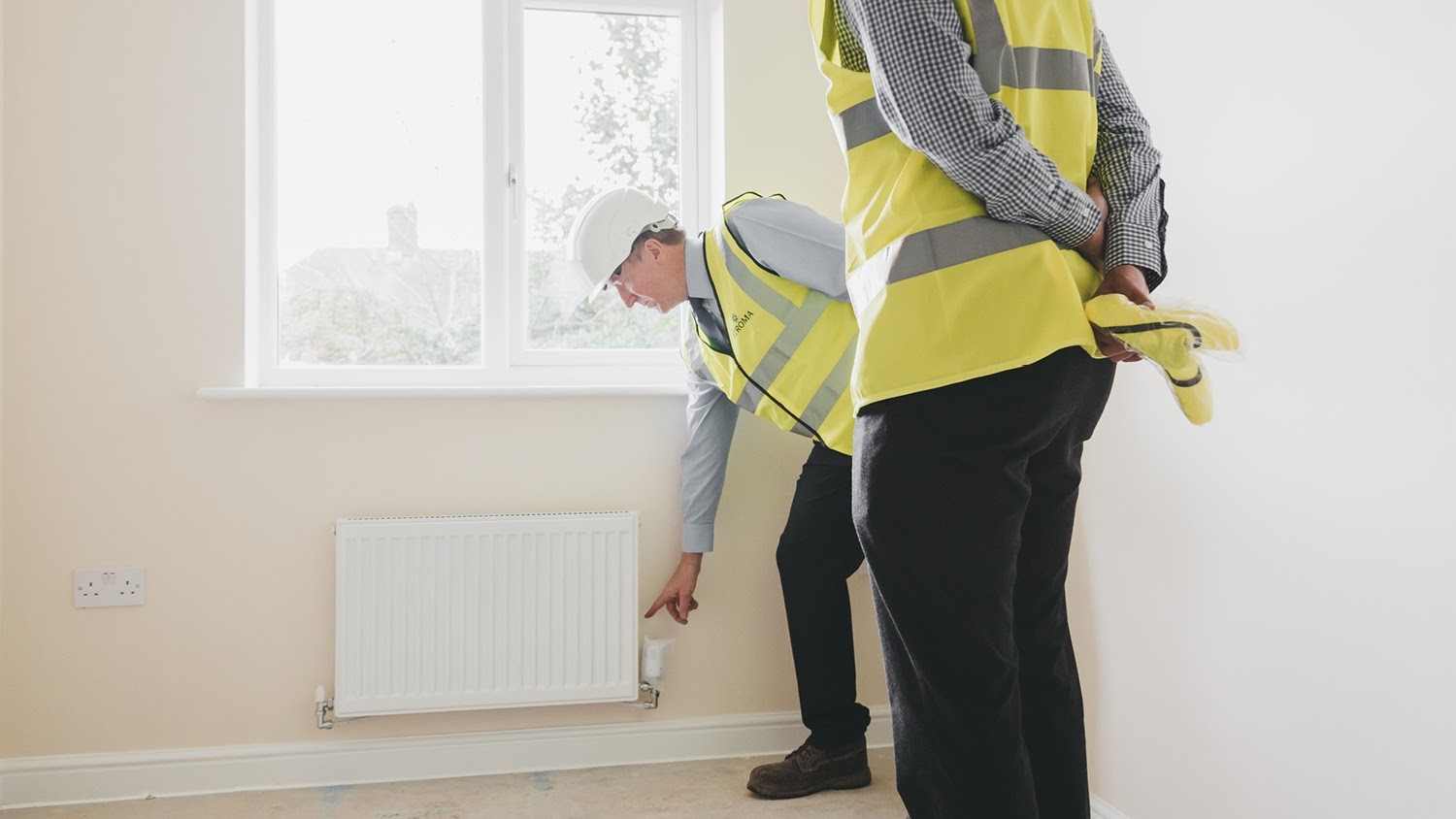
Building & Construction
What Is Snagging In Construction
Modified: October 28, 2024
Discover what snagging in building construction is and why it is crucial for ensuring quality and finishing touches. Learn the importance of snagging to avoid future issues.
(Many of the links in this article redirect to a specific reviewed product. Your purchase of these products through affiliate links helps to generate commission for Storables.com, at no extra cost. Learn more)
Introduction
When it comes to constructing a building, quality and attention to detail are of utmost importance. In order to ensure that a construction project meets the highest standards, snagging plays a crucial role. Snagging refers to the process of identifying and rectifying any defects, faults, or issues in a newly completed building or structure before it is handed over to the client.
Snagging is an essential part of the construction process as it ensures that the building is safe, functional, and meets the specifications outlined in the plans. It involves a thorough inspection of the property to identify any imperfections or areas that require adjustment or repair.
The snagging process typically occurs towards the end of the construction phase, after all major work has been completed. It involves a meticulous examination of the building, both internally and externally, to identify any issues that may affect its performance or aesthetics. These issues can range from minor cosmetic defects, such as paintwork and plasterwork, to more serious structural or mechanical problems.
During the snagging process, the main goal is to ensure that the building is finished to a high standard and is ready for occupation. This includes checking that all finishes are of satisfactory quality, all fixtures and fittings are in working order, electrical and plumbing systems are functioning correctly, and there are no safety hazards present.
In the following sections, we will explore the importance of snagging in construction, common snagging issues, the snagging process itself, the benefits of effective snagging, tools and techniques used in snagging, and the challenges and solutions that arise during the snagging process.
Key Takeaways:
- Snagging is a crucial quality control process in construction, ensuring safety, integrity, and aesthetics of buildings. It prevents future costs and enhances client satisfaction by addressing defects before occupancy.
- Effective snagging involves thorough inspections, clear communication, and streamlined processes. Overcoming challenges such as time constraints and complex building designs is essential for delivering high-quality finished products.
Read more: What Is Construction
Definition of Snagging
Snagging is a term commonly used in the construction industry to describe the process of identifying and rectifying defects, faults, or issues in a newly completed building or structure. It is essentially a quality control measure that ensures the building is in adherence to the required standards and specifications before it is handed over to the client or occupants.
The term “snag” refers to any aspect of the construction that does not meet the expected or desired level of quality. This can include a wide range of issues such as cosmetic defects, structural deficiencies, faulty installations, incomplete finishes, or non-functional systems. Snagging allows these issues to be addressed and resolved before the building is occupied, preventing any inconvenience or safety risks to the future occupants.
The snagging process typically involves a comprehensive inspection of the entire building, both internally and externally. It is carried out by a team of experienced professionals, such as architects, engineers, project managers, and quality control inspectors. They meticulously check each component and system of the building to identify any shortcomings or deficiencies.
Once the snagging list is compiled, it is shared with the construction team responsible for rectifying the issues. They are given a specific timeframe to address the identified snags and ensure that they are resolved to the required standard. The team then re-inspects the building to verify that all snags have been adequately rectified.
It is important to note that snagging is not limited to new builds only. It can also be carried out during property renovations or refurbishments to ensure that the work is completed to the desired quality and standards.
Overall, the purpose of snagging is to provide assurance to the client that the building has been constructed in line with the agreed-upon plans and specifications. It helps to maintain the integrity and functionality of the building while ensuring the satisfaction of the end-users.
Importance of Snagging in Construction
The snagging process is of paramount importance in the construction industry for several reasons. It serves as a critical quality control measure that ensures the building is completed to the highest standards and meets the expectations of the client. Let’s delve into the key reasons why snagging is crucial in construction:
- Ensuring Safety: One of the primary purposes of snagging is to identify and address any safety hazards or risks within the building. This includes detecting faulty electrical connections, unstable structures, or inadequate fire safety measures. By thoroughly inspecting the building, snagging helps to ensure that the occupants will be safe once they move in.
- Maintaining Building Integrity: Snagging allows for the identification and rectification of any deficiencies that could compromise the structural integrity of the building. This includes cracks in walls, uneven flooring, or faulty roofing. By addressing these issues early on, the building’s longevity and durability are protected.
- Enhancing Aesthetics: Snagging also plays a crucial role in ensuring that the building’s aesthetics meet the desired standards. It involves checking for any cosmetic defects such as paintwork inconsistencies, chipped tiles, or uneven plastering. By rectifying these issues, the overall visual appeal and market value of the property are preserved.
- Meeting Specifications: Construction projects are typically guided by specific plans and specifications. Snagging ensures that the completed building aligns with these specifications. Any deviations or non-compliance can be identified and rectified during the snagging process, ensuring that the end result matches the client’s expectations.
- Preventing Future Costs: Addressing snags before the building is occupied helps prevent potential future costs. Fixing issues at an early stage is often more cost-effective than waiting for them to escalate and cause more extensive damage. Moreover, by rectifying snags promptly, the need for major repairs or renovations down the line can be minimized.
Overall, snagging is a crucial step in the construction process that ensures the safety, quality, and functionality of the building. It helps to identify and rectify any issues, both large and small, before the building is handed over to the client. By undertaking thorough snagging procedures, construction professionals can deliver a finished product that meets the highest standards of excellence, leading to satisfied clients and occupants.
Common Snagging Issues
During the snagging process, various issues or defects may be identified that require attention and rectification. These snagging issues can range from minor cosmetic defects to more significant structural or functional problems. Let’s explore some of the common snagging issues typically encountered in construction:
- Paintwork and Plasterwork: Issues with paintwork and plasterwork are among the most common cosmetic snagging problems. This includes uneven paint finish, flaking or peeling paint, or plaster cracks and imperfections.
- Flooring: Flooring problems are often identified during snagging. This can include uneven tiling, loose floorboards, or gaps between floor finishes. In some cases, incorrect installation of floor coverings may also be flagged as a snagging issue.
- Doors and Windows: Snagging may reveal issues with doors and windows, such as misaligned frames, defective hinges or locks, or insufficient sealing. These issues can impact functionality, security, and energy efficiency.
- Electrical Fixtures: Snagging often uncovers problems with electrical fixtures and installations. This can include non-functional switches or sockets, improper wiring, or inadequate electrical load distribution.
- Plumbing and Sanitary Installations: Snagging may identify issues with plumbing and sanitary installations, such as leaky pipes, malfunctioning faucets or toilets, or inadequate water pressure. Proper functioning of these systems is essential for the comfort and convenience of the occupants.
- Structural Deficiencies: Snagging also involves a thorough inspection of the building’s structural elements. This may reveal cracks in walls, uneven foundations, or structural deformities that need to be addressed promptly to ensure the building’s stability and safety.
- Finishes and Joinery: Snagging commonly highlights defects in finishes and joinery. This can include issues with built-in cabinets, wardrobes, or doors, such as misaligned hinges, faulty handles, or loose fittings.
- Insulation and Ventilation: Inadequate insulation or ventilation can be flagged as snagging issues. This could result in poor thermal performance, excessive condensation, or inadequate airflow within the building.
These are just a few examples of the common snagging issues encountered in construction projects. However, it’s worth noting that the specific issues can vary depending on the nature of the building, the construction materials used, and the complexity of the project. By addressing these snagging issues promptly and effectively, construction professionals can ensure that the building is in optimal condition and meets the desired quality standards before it is occupied.
Snagging Process in Construction
The snagging process is a systematic approach that involves thorough inspections and assessments of a newly constructed building or structure. It is important to follow a structured snagging process to ensure that all issues and defects are identified and rectified before the building is handed over to the client. Let’s explore the key steps involved in the snagging process:
- Preparation: Before starting the snagging process, the construction team should gather all relevant documentation, including architectural plans, specifications, and any other quality control guidelines. This information serves as a reference during the inspections.
- Initial Inspection: The snagging process begins with a comprehensive inspection of the building, both internally and externally. This includes checking each room, corridor, and common areas, as well as assessing the building’s façade, roof, and landscaping. The purpose of this inspection is to identify any cosmetic defects, structural deficiencies, or functional issues.
- Compiling the Snagging List: As issues are identified during the inspection, they are recorded and compiled into a snagging list. Each issue is clearly described, specifying the location and nature of the snag. The snagging list serves as a detailed reference for the construction team responsible for rectifying the issues.
- Review by Construction Team: Once the snagging list is prepared, it is reviewed by the construction team, including contractors, architects, and project managers. They assess the severity and priority of each snag, categorizing them based on their impact on safety, functionality, or aesthetics.
- Rectification of Snags: After the review, the construction team starts the process of rectifying the identified snags. This may involve coordinating with different tradespeople, such as painters, electricians, plumbers, and carpenters, to address each snag on the list. The team is given a specific timeframe to complete the rectification work.
- Re-inspection: Once the construction team has completed the rectification work, a re-inspection is conducted to verify that all snags have been adequately addressed. Each snag is checked off the list as it is completed, ensuring that no issues are left unresolved.
- Client Inspection and Sign-off: After the re-inspection, the client or their representative is invited to inspect the building and review the rectified snags. They have the opportunity to provide feedback and ensure that their expectations have been met. Once the client is satisfied, they sign off on the snagging process, indicating their acceptance of the building.
The snagging process is a critical part of the construction journey, ensuring that the building is completed to the required standards. By following a structured snagging process, construction professionals can identify and rectify any issues or defects, ensuring the building’s safety, functionality, and aesthetic appeal.
When snagging in construction, be thorough in inspecting the property for any defects or unfinished work before finalizing the project. Keep a detailed list and work closely with the contractor to ensure everything is completed to your satisfaction.
Read more: What Is Construction Budget
Benefits of Effective Snagging
Effective snagging brings a multitude of benefits to the construction process and the final quality of the building. By prioritizing and conducting snagging efficiently, construction professionals can ensure a high level of quality and client satisfaction. Let’s explore the key benefits of effective snagging:
- Quality Assurance: Effective snagging helps to maintain and enhance the overall quality of the building. By identifying and rectifying defects, whether they are cosmetic, structural, or functional, snagging ensures that the final product meets the desired standards.
- Client Satisfaction: Snagging allows for client feedback and involvement in the inspection process. By promptly addressing their concerns and rectifying any issues, construction professionals can build trust, satisfaction, and positive relationships with clients, leading to greater customer retention and referrals.
- Compliance with Standards and Regulations: Snagging ensures that the building is compliant with relevant building codes, regulations, and safety standards. By identifying any deviations or non-compliance during the snagging process, necessary adjustments can be made to bring the building up to the required standards.
- Prevention of Future Costs: Identifying and rectifying issues during snagging prevents potential future costs. By addressing snags early on, construction professionals can avoid more extensive damage, minimize the need for future repairs, and reduce associated expenses for both the client and the contractor.
- Improved Building Performance: Effective snagging ensures that the building performs optimally. By rectifying issues related to insulation, ventilation, electrical systems, plumbing, and structural integrity, snagging contributes to energy efficiency, occupant comfort, and overall functionality of the building.
- Mitigation of Safety Risks: Snagging plays a crucial role in identifying and rectifying safety hazards or risks within the building. By addressing issues such as faulty electrical installations, unstable structures, or inadequate fire safety measures, snagging helps to create a safe environment for building occupants.
- Enhancement of Aesthetics: Snagging ensures that the building exhibits a high standard of visual appeal. By addressing cosmetic defects such as paintwork inconsistencies, flooring imperfections, or joinery issues, snagging helps to create a pleasing and aesthetically satisfying environment.
Ultimately, effective snagging is a vital quality control process in construction that provides numerous benefits. By ensuring the building meets the desired standards, addressing client concerns, complying with regulations, and preventing future costs, construction professionals can deliver a high-quality, safe, and satisfactory end product.
Tools and Techniques for Snagging
Snagging requires the use of various tools and techniques to effectively identify and record defects or issues in a newly constructed building. These tools and techniques aid in conducting thorough inspections, creating comprehensive snagging lists, and ensuring efficient rectification. Let’s explore some commonly used tools and techniques for snagging:
- Snagging App or Software: Utilizing a dedicated snagging app or software can streamline the snagging process. These tools allow inspectors to create digital snagging lists, capture photos or videos of the issues, and easily share the information with the construction team for rectification.
- Checklists and Templates: Preparing checklists and templates can help ensure comprehensive inspections and consistent documentation of snagging issues. These checklists cover various aspects of the building, including finishes, fixtures, electrical systems, plumbing, and structural elements. They serve as guides during inspections, ensuring that no areas are overlooked.
- Measuring and Testing Equipment: Measuring and testing equipment, such as laser levels, moisture meters, thermal cameras, and electrical testers, aid in assessing the quality and functionality of different building components. They enable inspectors to identify issues like uneven surfaces, moisture ingress, inadequate insulation, or faulty electrical connections.
- Camera or Smartphone: A camera or smartphone is essential for capturing visual evidence of snagging issues. Inspectors can take photos or videos of defects, providing clear documentation for reference and communication. These images can also be used as visual aids when discussing and clarifying the issues with the construction team.
- Lighting Equipment: Good lighting is crucial for accurate visual inspections. Inspectors may use portable lighting equipment, such as torches or spotlights, to illuminate areas with inadequate lighting conditions. This ensures that no defects or issues are missed during the inspection process.
- Communication Tools: Effective communication is key for snagging. Communication tools like walkie-talkies, smartphones, or two-way radios facilitate smooth communication between inspectors and the construction team. This ensures that the identified snags are appropriately addressed and rectified in a timely manner.
- Building Plans and Specifications: Detailed building plans and specifications serve as references during inspections. They provide vital information about the intended design, finishes, fixtures, and systems. By comparing the actual construction against these plans, inspectors can identify any deviations or non-compliance that require rectification.
These tools and techniques enhance the efficiency and effectiveness of the snagging process, leading to better identification, documentation, and rectification of issues within the building. By utilizing these resources, construction professionals can ensure that the snagging process is accurate, thorough, and well-documented, resulting in a high-quality finished product.
Challenges and Solutions in Snagging
The snagging process in construction can present various challenges that need to be addressed to ensure a smooth and effective completion of the project. By being aware of these challenges and implementing appropriate solutions, construction professionals can overcome obstacles and optimize the snagging process. Let’s explore some common challenges in snagging and their corresponding solutions:
- Time Constraints: One of the main challenges in snagging is the pressure to complete the process within a limited timeframe, especially when there are tight project deadlines. To overcome this challenge, it is crucial to allocate sufficient time for snagging in the project schedule. Early planning and clear communication with the construction team can help prevent unnecessary delays and ensure adequate time for comprehensive inspections and rectification.
- Communication and Coordination: Effective communication between inspectors, contractors, and subcontractors is essential for successful snagging. However, miscommunication or lack of coordination can hinder the efficient resolution of snags. To address this challenge, regular meetings and clear channels of communication should be established. Project management software or dedicated snagging apps can also facilitate better communication and collaboration, ensuring that information flows seamlessly between parties involved.
- Complexity of Buildings: Modern buildings are becoming increasingly complex in design and construction, which can present challenges during snagging. Complicated systems, advanced technologies, and intricate finishes may require specialized knowledge and expertise for identification and rectification. Engaging professionals with the necessary skills and experience in dealing with complex buildings can help overcome this challenge and ensure effective snagging.
- Subjectivity of Defects: Assessing and categorizing defects during snagging can be subjective, leading to disagreements between the inspector and the construction team. To address this challenge, clear guidelines should be established for differentiating between minor cosmetic defects and more significant functional or structural issues. Regular training and alignment between the inspection team and contractors can help mitigate subjective differences and ensure consistent standards for defect evaluation.
- Rectification Delays: After identifying snags, delays in rectification can occur due to resource constraints, logistical challenges, or conflicting priorities. To minimize rectification delays, it is important to establish clear communication channels with the construction team and have regular progress reviews. Setting realistic deadlines, providing clear instructions for rectification, and ensuring contractors have the necessary resources can help expedite the resolution of snags.
- Client Expectations: Striving to meet client expectations can be a challenge as different clients may have varied subjective preferences. To address this challenge, thorough communication and documentation throughout the snagging process are essential. Regular updates, discussions, and obtaining client feedback during inspections can help manage expectations and ensure that the final result aligns with the client’s vision.
By understanding and proactively addressing these challenges, construction professionals can improve the efficiency and effectiveness of the snagging process. Clear communication, effective coordination, proper planning, and collaboration among all stakeholders are key to overcoming these challenges and ensuring successful completion of the snagging process.
Conclusion
The snagging process is a critical step in ensuring the quality, safety, and functionality of a newly constructed building. By conducting thorough inspections, identifying and rectifying defects or issues, construction professionals can deliver a high-quality finished product that meets the expectations of the client.
Throughout this article, we have explored the definition and importance of snagging in construction. We have learned that snagging is a quality control measure that involves identifying and rectifying any defects, faults, or issues before the building is handed over to the client or occupants. Effective snagging plays a crucial role in ensuring safety, maintaining the integrity of the building, meeting specifications, and preventing future costs.
We have also discussed common snagging issues that can arise, including cosmetic defects, structural deficiencies, and functional problems. These issues can range from paintwork imperfections and flooring problems to electrical or plumbing malfunctions. Effective snagging enables these issues to be addressed before they escalate, ensuring the building’s quality and durability.
The snagging process itself involves a structured approach, including preparation, initial inspections, compiling snagging lists, rectification of snags, re-inspections, and client sign-off. By following this process and utilizing tools and techniques such as snagging apps, checklists, measuring equipment, and effective communication tools, construction professionals can streamline the snagging process and deliver a high-quality finished product.
However, the snagging process also presents several challenges, including time constraints, communication and coordination issues, complex building designs, subjective defect assessment, rectification delays, and managing client expectations. Addressing these challenges requires proper planning, clear communication, regular progress reviews, and a collaborative approach among all stakeholders.
In conclusion, effective snagging is a vital part of the construction process that ensures the building meets the desired standards and ensures client satisfaction. By prioritizing quality control, addressing snagging issues efficiently, and continuously improving the snagging process, construction professionals can deliver buildings that are safe, durable, and aesthetically pleasing.
By prioritizing quality control, addressing snagging issues efficiently, and continuously improving the snagging process, construction professionals can deliver buildings that are safe, durable, and aesthetically pleasing.
Frequently Asked Questions about What Is Snagging In Construction
Was this page helpful?
At Storables.com, we guarantee accurate and reliable information. Our content, validated by Expert Board Contributors, is crafted following stringent Editorial Policies. We're committed to providing you with well-researched, expert-backed insights for all your informational needs.
0 thoughts on “What Is Snagging In Construction”