Home>diy>Building & Construction>What Is Stick-Built Construction
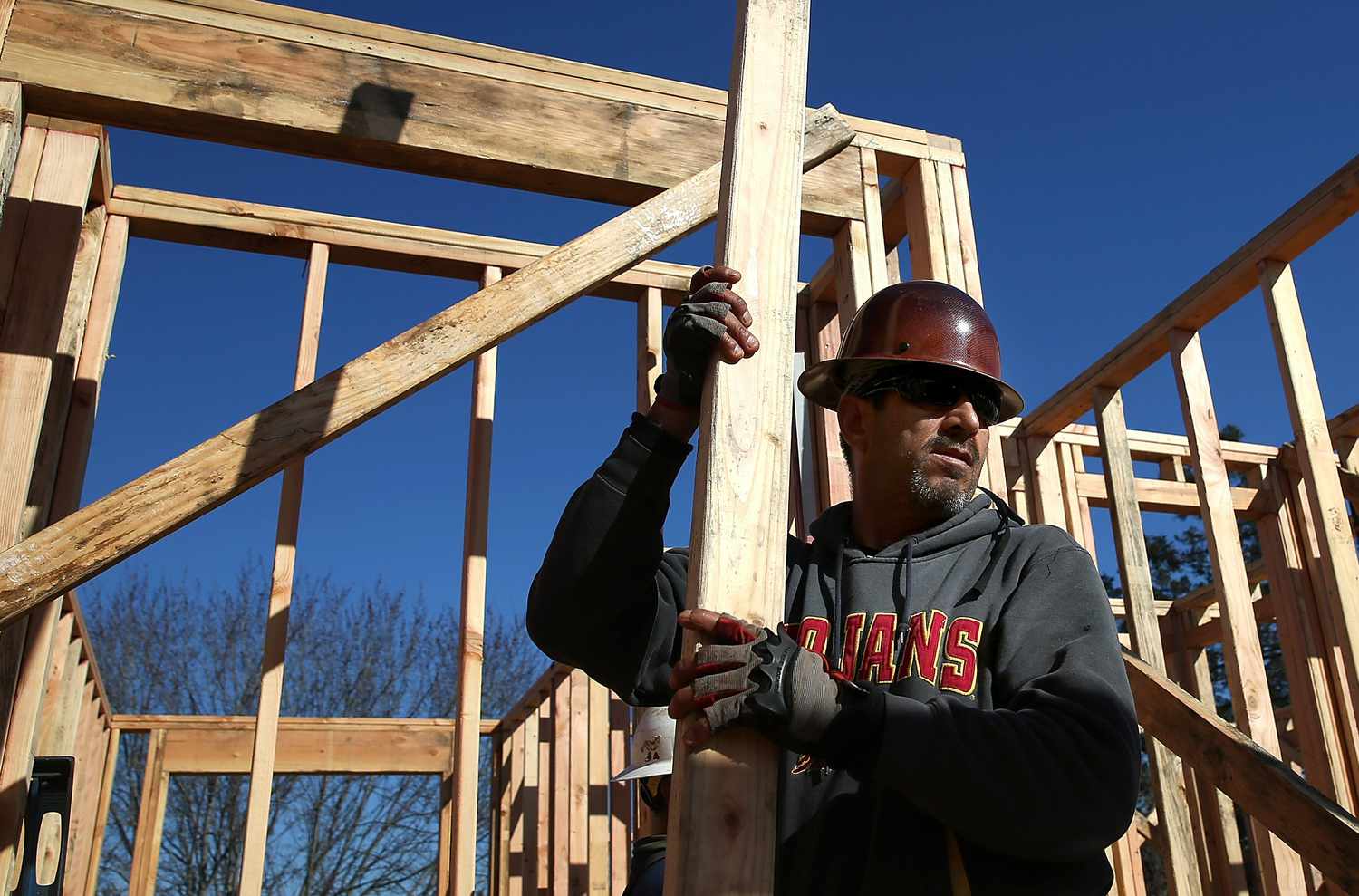
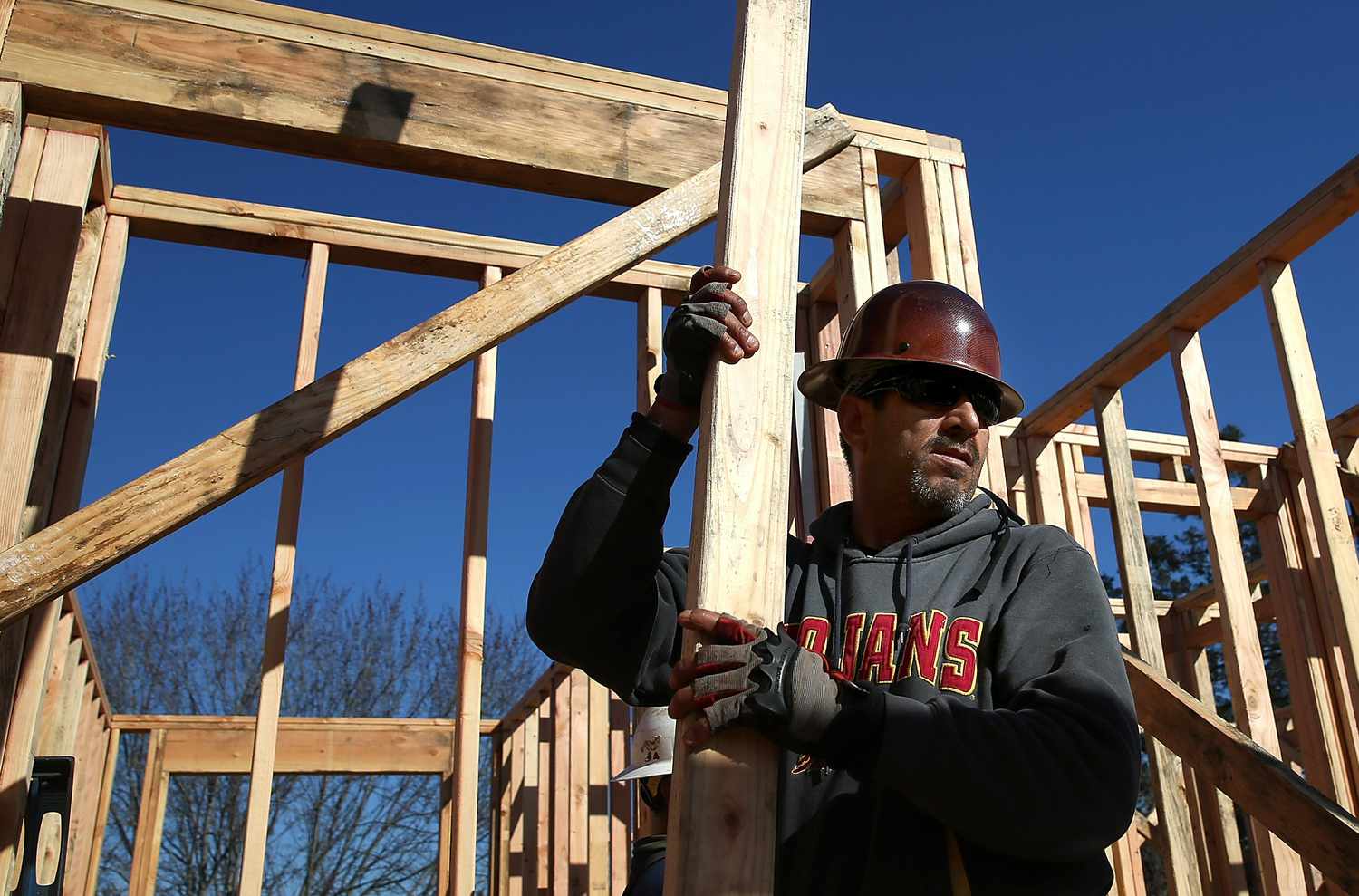
Building & Construction
What Is Stick-Built Construction
Modified: February 29, 2024
Discover the benefits of stick-built construction, a popular building construction method. Learn how this technique is used in various industries and why it is considered a cost-effective and sustainable option.
(Many of the links in this article redirect to a specific reviewed product. Your purchase of these products through affiliate links helps to generate commission for Storables.com, at no extra cost. Learn more)
Introduction
When it comes to building construction, there are various methods that can be employed. One popular method is stick-built construction. This approach has been used for centuries and continues to be a preferred choice for many construction projects.
Stick-built construction, also known as stick framing or platform framing, refers to the process of constructing a building using individual pieces of lumber or “sticks” to create the structural framework. This method involves assembling the building’s walls, floors, and roof by attaching these sticks together using nails or screws.
Stick-built construction offers numerous benefits, making it a favored choice across different sectors of the construction industry. It allows for flexibility in design, providing architects and builders with the freedom to create unique and customized structures. The method is also cost-effective, as it utilizes readily available and affordable materials. Additionally, stick-built construction offers excellent energy efficiency, as it allows for optimal insulation and air sealing.
In this article, we will delve deeper into the world of stick-built construction. We will explore the process, materials, advantages, and disadvantages, as well as its environmental impact and cost considerations. Furthermore, we will compare stick-built construction with other construction methods to understand its place in the industry. Finally, we will provide examples of notable stick-built construction projects to showcase the versatility and potential of this method.
Whether you are a construction professional, an aspiring homeowner, or simply interested in the mechanics of building construction, this article will provide you with a comprehensive overview of stick-built construction. So, let us dive in and discover the intricacies of this popular construction method.
Key Takeaways:
- Stick-built construction offers design flexibility, cost-effectiveness, and energy efficiency, making it a versatile choice for residential, commercial, and educational projects. Its adaptability allows for unique and tailored structures to meet specific needs.
- While stick-built construction has its advantages, careful consideration of potential drawbacks and environmental impact is crucial. Implementing sustainable practices and exploring eco-friendly alternatives can further reduce its environmental footprint.
Read more: What Is As-Built In Construction
Definition of Stick-Built Construction
Stick-built construction, also referred to as stick framing or platform framing, is a construction method that involves using individual pieces of lumber, known as “sticks,” to create the structural framework of a building. The term “stick-built” originates from the use of these wooden sticks as the primary building components.
This method is commonly employed in residential and commercial construction, providing a cost-effective and efficient way to build structures. Stick-built construction typically starts with the assembly of the building’s foundation, which serves as the base for the entire structure. Once the foundation is in place, the vertical and horizontal sticks, also known as studs and joists, respectively, are positioned to form the walls, floors, and roof.
The sticks used in stick-built construction are usually made of wood, as it is a versatile and readily available material. The most commonly used type of lumber is dimensional lumber, such as 2x4s or 2x6s, which are cut to specific lengths and dimensions. These sticks are then fastened together using nails, screws, or other connectors to create a sturdy and stable framework.
One of the defining characteristics of stick-built construction is its adaptability and flexibility in design. This construction method allows for a wide range of architectural styles and configurations, accommodating various floor plans and layouts. The sticks can be easily modified or adjusted on-site to meet specific design requirements and accommodate architectural features such as windows, doors, and openings.
Stick-built construction is widely recognized for its speed and efficiency in construction. The off-site fabrication of the wooden sticks allows for quick assembly on the construction site, reducing construction time and labor costs. Additionally, this method allows for easy integration of other building components, such as electrical and plumbing systems, within the framework.
Overall, stick-built construction offers a versatile and cost-effective solution for building construction. Its use of wooden sticks as the primary building components, combined with its flexibility in design and efficiency in construction, has made it a popular choice for both residential and commercial projects.
Benefits of Stick-Built Construction
Stick-built construction offers numerous advantages that make it a preferred choice for many builders and homeowners. Whether you are planning to construct a residential property or a commercial building, considering the benefits of stick-built construction can help you make an informed decision. Let’s explore some of the key advantages:
1. Versatility in Design
Stick-built construction allows for a high level of design flexibility. Since the structural framework is constructed using individual sticks, it is easier to modify and customize the building’s layout and architectural features. Whether you want to create open-concept spaces, incorporate unique design elements, or adapt to specific site conditions, stick-built construction provides the freedom to achieve your desired design vision.
2. Ease of Modifications
As buildings evolve over time, modifications and renovations may become necessary. Stick-built construction allows for easy modifications and additions. The individual sticks can be easily removed, repositioned, or replaced without significant structural alterations, making it convenient to adapt the building to changing needs and preferences.
Read more: What Will Stick To Stucco
3. Cost-Effectiveness
Stick-built construction is generally more cost-effective compared to other construction methods. The materials used, such as dimensional lumber, are readily available and affordable. The efficient assembly process also helps to reduce construction time and labor costs. Moreover, stick-built construction allows for easy integration of other building components, such as electrical and plumbing systems, without the need for complex and costly installation methods.
4. Energy Efficiency
Stick-built construction provides excellent energy efficiency. The individual sticks allow for optimal insulation, reducing heat loss or gain and improving the building’s energy performance. Additionally, stick-built construction allows for effective air sealing, minimizing drafts and improving indoor comfort. These energy-saving features contribute to lower energy consumption and reduced utility costs over the lifespan of the building.
5. Availability of Materials
Wood, the primary material used in stick-built construction, is a renewable resource and widely available. The lumber industry has implemented sustainable forestry practices to ensure responsible sourcing. Furthermore, advancements in timber technology have led to the development of engineered lumber products, such as laminated veneer lumber (LVL) and engineered wood joists (EWJs), which offer enhanced structural performance and durability.
6. Speed of Construction
Stick-built construction is known for its relatively quick construction process. Off-site fabrication of the individual sticks allows for efficient on-site assembly, reducing construction time significantly. This benefit is particularly advantageous for projects with tight timelines or commercial constructions where fast completion is crucial.
These are just some of the many benefits that stick-built construction offers. From design flexibility to cost-effectiveness and energy efficiency, this construction method provides a compelling choice for various construction projects.
Read more: What Will Stick To Brick
Common Materials Used in Stick-Built Construction
Stick-built construction relies on a range of materials to create the structural framework of a building. While the sticks, typically made of wood, are the primary components, there are several other materials that play a vital role in ensuring the stability, durability, and functionality of the constructed structure. Let’s explore some of the common materials used in stick-built construction:
1. Lumber
Lumber is the main material used in stick-built construction. It is typically sourced from trees and processed into dimensional lumber, such as 2x4s or 2x6s. These pieces of lumber serve as the vertical studs and horizontal joists, forming the framework of walls, floors, and roofs. The most commonly used types of lumber include Douglas fir, pine, and spruce. Lumber can be further classified based on its grade and quality, ensuring the appropriate strength and structural stability.
2. Engineered Wood Products
In addition to traditional lumber, engineered wood products are also widely used in stick-built construction. These products offer enhanced strength, stability, and dimensional consistency. Engineered wood products include laminated veneer lumber (LVL), which consists of multiple layers of thin wood veneers glued together. Additionally, oriented strand board (OSB) and plywood are commonly used as sheathing materials for walls and roofs, providing structural rigidity and a base for exterior finishes.
3. Fasteners
To secure the individual sticks together, a variety of fasteners are used in stick-built construction. Nails and screws are the most common types of fasteners. They provide the necessary strength and stability to hold the lumber in place. The choice of fasteners depends on the specific application and load requirements of the building. Different types of nails, such as framing nails and finish nails, are used for different purposes, ensuring proper installation and structural integrity.
Read more: What Is Peel And Stick Roofing
4. Insulation Materials
Insulation plays a crucial role in stick-built construction to enhance energy efficiency and provide thermal comfort. Common insulation materials include fiberglass batts, cellulose, spray foam, and mineral wool. These materials are installed between the studs, joists, and rafters to reduce heat transfer and improve the building’s thermal performance. Proper insulation helps to maintain indoor temperatures, reduce energy consumption, and create a comfortable living or working environment.
5. Exterior Finishes
Exterior finishes not only provide an aesthetically pleasing appearance but also offer protection against weather elements and enhance the durability of the structure. Common exterior finishes in stick-built construction include siding materials such as vinyl, fiber cement, wood, or brick. Roofing materials, such as asphalt shingles, metal panels, or clay tiles, are also used to create a weatherproof and durable roof system.
6. Interior Finishes
Interior finishes add the final touches to the structure, creating functional and visually appealing spaces. Drywall is commonly used for interior walls and ceilings, offering a smooth and paintable surface. Other interior finishes include flooring materials, such as hardwood, laminate, carpet, or tile, as well as trim materials, such as baseboards, crown molding, and window casings. These finishes complete the interior design and contribute to the overall aesthetic of the building.
These materials are essential components in stick-built construction, working together to create durable, functional, and visually appealing structures. The careful selection and proper installation of these materials ensure the integrity and longevity of the constructed building.
Step-by-Step Process of Stick-Built Construction
Stick-built construction follows a systematic process that involves various stages to construct a building using individual sticks or pieces of lumber. While the exact process may vary depending on the specific project and design, here is a general step-by-step guide to stick-built construction:
Read more: What Is Peel And Stick Tile
1. Site Preparation
The first step in stick-built construction is preparing the construction site. This typically involves clearing and leveling the land, ensuring it is ready for construction. Site preparation may also include laying the foundation, which serves as the base for the entire structure.
2. Layout and Foundations
Once the site is prepared, the layout of the building is marked, indicating the walls, corners, and other relevant measurements. The foundation is then constructed according to the building plans. This may involve pouring concrete footings, installing foundation walls, or utilizing a slab-on-grade foundation, depending on the design and local building codes.
3. Wall Framing
With the foundation in place, the wall framing begins. This involves erecting vertical wooden studs, typically 2×4 or 2×6 lumber, at specified intervals to create the structure’s walls. These studs are attached to the foundation and each other using nails or screws. Windows and doors can be framed within the walls during this stage as well.
4. Floor and Ceiling Framing
Once the walls are framed, the focus shifts to the construction of the floors and ceilings. Horizontal wooden joists, similar to the studs, are installed between the walls to create the floors and ceilings of each level. These joists provide structural support and create platforms for additional flooring and ceiling materials.
Read more: What Glue Sticks To Glass
5. Roof Framing
After the floors and ceilings are in place, the roof framing is next. This involves constructing the framework for the roof, including the rafters and ridge board. The rafters are attached to the top of the walls and slope up to meet at the ridge board, forming the roof’s structure. This stage also includes the installation of any necessary roof trusses if they are part of the design.
6. Installation of Sheathing and Exterior Finishes
Once the structure is framed, sheathing is applied to the exterior walls and roof. Common sheathing materials include oriented strand board (OSB) or plywood. The sheathing provides additional structural rigidity and serves as a base for the exterior finishes, such as siding or cladding materials. At this stage, windows and exterior doors are also installed.
7. Electrical and Plumbing Installation
With the basic structure in place, the electrical and plumbing systems are installed. This includes running wiring and conduit for electrical outlets, switches, and lighting fixtures. Plumbing lines and fixtures are also installed, including water supply lines, drains, and faucets. HVAC (Heating, Ventilation, and Air Conditioning) systems may also be installed or prepared at this stage.
8. Insulation and Interior Finishes
Insulation materials, such as fiberglass batts or spray foam, are installed between the studs, joists, and rafters to improve energy efficiency and indoor comfort. Following the insulation, interior finishes are applied. This includes hanging and finishing drywall on the walls and ceilings, installing flooring materials, and adding trim, molding, and other decorative features.
Read more: What Adhesive Sticks To Glass
9. Exterior and Interior Detailing
Once the building’s shell and interior finishes are complete, attention is given to exterior and interior detailing. This involves painting or applying exterior finishes to the walls, installing cabinets, countertops, and appliances in kitchens and bathrooms, and adding any desired decorative elements both inside and outside the building.
10. Final Inspections and Completion
Before the building is considered complete, it will undergo comprehensive inspections to ensure compliance with building codes, safety regulations, and quality standards. Inspectors will check the electrical, plumbing, and HVAC systems, as well as other critical aspects of the construction. Once all inspections pass, a Certificate of Occupancy can be issued, allowing the building to be legally occupied.
The step-by-step process of stick-built construction ensures a systematic approach to creating a solid and functional structure. Skilled professionals, including architects, engineers, and contractors, are essential for successfully completing each stage and delivering a well-constructed building.
Pros and Cons of Stick-Built Construction
Stick-built construction, also known as stick framing or platform framing, offers several advantages that make it a popular choice in the construction industry. However, like any construction method, it also has its drawbacks. In this section, we will explore the pros and cons of stick-built construction to provide a balanced view of this construction approach.
Pros of Stick-Built Construction:
1. Design Flexibility:
Stick-built construction offers a high degree of design flexibility. The use of individual sticks allows for customization, enabling architects and builders to create unique and tailored designs. This flexibility in design allows for easy modifications and adjustments during construction and future renovations.
2. Cost-Effective:
Stick-built construction is generally more cost-effective compared to other construction methods. The materials used, such as dimensional lumber, are affordable and readily available. The efficient assembly process also reduces construction time and labor costs. Moreover, stick-built construction allows for easy integration of other building components, such as electrical and plumbing systems, without the need for complex and costly installation methods.
3. Energy Efficiency:
Stick-built construction provides excellent energy efficiency. The individual sticks allow for optimal insulation, reducing heat transfer and improving the building’s energy performance. Proper air sealing can also be achieved, minimizing drafts and improving indoor comfort. These energy-saving features contribute to lower energy consumption and reduced utility costs over time.
4. Versatility and Adaptability:
Stick-built construction is highly versatile and adaptable to different architectural styles and configurations. It can cater to a wide range of design preferences and accommodate unique floor plans and layouts. The individual sticks can be easily modified or adjusted on-site to meet specific design requirements and accommodate architectural features.
5. Speed of Construction:
Stick-built construction is known for its relatively quick construction process. The off-site fabrication of the individual sticks allows for efficient on-site assembly, reducing construction time significantly. This benefit is particularly advantageous for projects with tight timelines or commercial constructions where fast completion is crucial.
Read more: What Glue Sticks To Brick
Cons of Stick-Built Construction:
1. Susceptible to Moisture Damage:
Stick-built construction is more susceptible to water and moisture damage compared to other construction methods. If not properly protected from moisture intrusion, wood framing can rot, warp, or develop mold and mildew. Proper moisture management measures, such as effective insulation, vapor barriers, and drainage systems, must be implemented to mitigate these risks.
2. Limited Strength and Load-Bearing Capacity:
Stick-built construction may have limitations in terms of strength and load-bearing capacity compared to other methods, such as steel or concrete construction. While dimensional lumber is structurally adequate for most residential and light commercial structures, larger or more complex projects may require additional structural reinforcements or alternative construction methods.
3. Long-Term Maintenance:
Wood used in stick-built construction may require regular maintenance to ensure its longevity and structural integrity. This includes periodic inspections for potential issues, such as termites, rot, or decay, and timely repairs or treatments. Regular maintenance is essential to protect and extend the lifespan of the structure.
4. Environmental Impact:
The use of wood in stick-built construction raises environmental concerns due to deforestation and the depletion of natural resources. However, sustainable forestry practices and the use of engineered wood products have helped mitigate these impacts. Additionally, stick-built construction can have a lower carbon footprint compared to other methods, as wood acts as a carbon sink, storing carbon dioxide.
Understanding the pros and cons of stick-built construction enables builders and homeowners to make informed decisions based on their specific needs, budget, and project requirements. It is essential to evaluate these factors and consider alternative construction methods when appropriate.
Environmental Impact of Stick-Built Construction
Stick-built construction, like any other construction method, has both positive and negative environmental impacts. Understanding these environmental implications is crucial for builders and homeowners who are conscious of sustainable practices and interested in reducing their ecological footprint. Let’s explore the environmental impact of stick-built construction:
Positive Environmental Aspects:
1. Renewable Resource:
Wood, the primary material used in stick-built construction, is a renewable resource. Proper forest management practices, such as sustainable forestry and reforestation programs, ensure the continual supply of wood without depleting forests. When responsibly sourced, wood can be harvested in a way that maintains the long-term ecological balance of forest ecosystems.
2. Carbon Sequestration:
Wood acts as a natural carbon sink, helping to mitigate climate change. During the growth phase, trees absorb carbon dioxide from the atmosphere and store it as carbon in their biomass. When wood is used in construction, it continues to store carbon throughout the lifespan of the building. This can help offset greenhouse gas emissions and reduce the overall carbon footprint of a structure.
3. Energy Efficiency:
Stick-built construction can be designed and built with a focus on energy efficiency. Optimal insulation installation between the wood studs, along with other energy-efficient measures like air sealing, can result in reduced energy consumption for heating and cooling. This decreases reliance on fossil fuels and contributes to a lower environmental impact.
4. Reduced Waste in Construction:
Stick-built construction can minimize waste generation during the construction process. With precise planning and accurate cutting of wooden sticks, waste is kept to a minimum. Additionally, wood waste generated during the construction process can be recycled or repurposed for other uses, reducing the environmental impact associated with waste disposal.
Negative Environmental Aspects:
1. Logging and Deforestation:
The use of wood in stick-built construction raises concerns about logging and deforestation. Irresponsible logging practices can lead to habitat destruction, loss of biodiversity, and disruption of ecosystems. However, responsible logging practices and sustainable forestry certifications help minimize these impacts and promote the preservation and management of forests.
2. Chemical Treatments:
Wood used in stick-built construction may require chemical treatments to protect it from decay, insects, and fire. The use of chemical treatments raises environmental concerns due to the potential release of harmful substances into the environment. However, advancements in eco-friendly treatment options and the use of naturally durable or treated wood can help mitigate these impacts.
3. Moisture and Mold Concerns:
If not properly protected from moisture intrusion, wood framing in stick-built construction can be susceptible to rot, decay, and mold development. This can result in the need for repairs or replacement, leading to additional resource consumption and waste. Proper moisture management measures, such as effective insulation and drainage systems, are crucial to minimize these risks.
4. Waste Disposal:
At the end of the building’s lifespan, the disposal of wooden materials can have environmental implications. Proper waste management and recycling practices should be followed to ensure that wood waste is disposed of responsibly. This can involve recycling the wood for other uses, repurposing it, or responsibly disposing of it in accordance with local regulations.
While stick-built construction has its environmental considerations, sustainable practices and responsible material sourcing can help mitigate its negative impacts. Builders and homeowners can make conscious choices, such as using sustainably sourced lumber, selecting eco-friendly treatment options, and implementing energy-efficient design measures, to further reduce the environmental footprint of stick-built construction.
Read more: What Is Construction
Cost Considerations of Stick-Built Construction
Stick-built construction is known for its cost-effectiveness compared to other construction methods. However, it is essential to consider various factors that can impact the overall cost of a stick-built project. By understanding these cost considerations, builders and homeowners can better budget and make informed decisions. Let’s explore the key cost considerations of stick-built construction:
1. Materials:
The cost of materials is a significant factor in stick-built construction. The primary material used in stick-built construction is lumber, typically dimensional lumber such as 2x4s or 2x6s. The cost of lumber can vary depending on factors such as the type of wood, grade, and market conditions. Other materials, such as insulation, sheathing, finishes, and fasteners, also contribute to the overall material cost.
2. Labor:
The cost of labor plays a significant role in stick-built construction. Skilled labor is required for tasks such as framing, installing electrical and plumbing systems, insulation, and finishing work. The cost of labor can vary based on geographic location, labor market conditions, project complexity, and the experience and expertise of the workers involved.
3. Site Preparation and Foundation:
Site preparation, including excavation, clearing, and leveling, can incur costs. Depending on the project and location, additional costs may arise if the construction site requires extensive groundwork or is on uneven terrain. The construction of the building’s foundation, whether it is a slab-on-grade, crawl space, or full basement, also contributes to the overall cost. Dealing with challenging soil conditions or specific foundation requirements may increase costs as well.
Read more: What Is The Best Peel And Stick Flooring
4. Design Complexity:
The complexity of the design can impact the cost of stick-built construction. Intricate architectural features, unique floor plans, and complex structural elements may require additional labor, expertise, and materials, contributing to higher construction costs. Simple and straightforward designs generally involve less complexity and may result in lower costs.
5. Permitting and Inspections:
Complying with local building codes, obtaining permits, and undergoing inspections are necessary steps in stick-built construction. These processes involve additional fees that vary depending on the location and the scope of the project. Failure to obtain the required permits or address any issues identified during inspections can lead to potential delays and additional expenses.
6. Finishes and Upgrades:
The choice of finishes and upgrades can significantly impact the final cost of a stick-built project. Flooring materials, cabinetry, appliances, fixtures, and other interior and exterior features can vary in price range. Opting for high-end materials or customized finishes will incur higher costs compared to more budget-friendly options. Detailed planning and a clear understanding of the desired finishes and upgrades are crucial to managing costs effectively.
7. Contingency Funds:
It is essential to include contingency funds in the budget for unforeseen circumstances or unexpected expenses that may arise during the construction process. Contingency funds provide a buffer to address any changes, delays, or additional costs that may occur. Including a percentage of the overall budget as contingency funds helps ensure a more accurate and realistic budget estimation.
8. Time and Schedule:
The construction timeline and project schedule can impact costs. Delays in the construction process can lead to increased labor costs, extended rental fees for construction equipment, storage costs for materials, and potential penalties due to missed deadlines. Efficient project management and proper planning can help minimize schedule disruptions and associated costs.
Consideration of these cost factors and careful budgeting is essential for stick-built construction projects. Working closely with contractors, suppliers, and professionals in the industry, as well as conducting thorough cost assessments during the planning phase, can help ensure that the project stays within budget and meets financial expectations.
Stick-Built Construction vs. Other Construction Methods
When it comes to building construction, there are several methods to choose from, each with its own advantages and considerations. Two common construction methods are stick-built construction and other alternative methods such as modular construction, concrete construction, and steel frame construction. Let’s compare stick-built construction with these other construction methods to understand their differences and benefits:
Stick-Built Construction:
- Stick-built construction involves assembling individual pieces of lumber to create the structural framework of a building.
- It offers design flexibility, allowing for customization and adaptability during the construction process.
- Stick-built construction is cost-effective, utilizing readily available and affordable materials.
- It allows for good energy efficiency with optimal insulation and air sealing.
- Stick-built construction can be time-efficient when skilled labor and efficient project management practices are employed.
Modular Construction:
- Modular construction involves building pre-fabricated modules off-site in a factory setting, which are then transported and assembled on-site.
- Modular construction offers faster project completion due to concurrent off-site module fabrication and on-site preparation.
- It provides stringent quality control and reduces material waste through factory-based construction processes.
- Modular construction offers design flexibility, although it may have some limitations due to the modular nature of the building components.
- It generally requires less on-site labor compared to stick-built construction.
Read more: What Sizes Do Wall Ovens Come In
Concrete Construction:
- Concrete construction involves using concrete as the primary structural material for walls, floors, and other building elements.
- It offers excellent durability and fire resistance properties.
- Concrete construction can be time-intensive due to the curing time required for concrete to reach its optimal strength.
- It provides good sound insulation and thermal mass, contributing to energy efficiency.
- Concrete construction may require specialized equipment and skilled labor.
Steel Frame Construction:
- Steel frame construction utilizes steel columns and beams as the primary structural elements.
- It offers superior strength and can withstand high loads and extreme weather conditions.
- Steel frame construction allows for large open spaces and flexible floor plans due to its structural versatility.
- It provides excellent fire resistance and is resistant to pests and decay.
- Steel frame construction generally requires skilled labor for welding and steel installation.
Each construction method has its advantages and considerations, and the choice depends on various factors such as project requirements, budget, timeline, and desired outcomes. Stick-built construction offers design flexibility, cost-effectiveness, and energy efficiency while allowing for customization. Alternatively, modular construction provides faster project completion, enhanced quality control, and reduced waste. Concrete construction offers durability, sound insulation, and fire resistance, while steel frame construction offers strength, versatility, and open design possibilities.
It is essential to consult with professionals and evaluate the specific needs of each project to determine the most suitable construction method. Factors such as budget, timeline, site conditions, and the intended use of the building play a vital role in making an informed decision. In some cases, a combination of construction methods may also be advantageous, leveraging the benefits of each method for different aspects of the project.
Examples of Stick-Built Construction Projects
Stick-built construction has been utilized in various construction projects, ranging from residential homes to commercial buildings. Here are a few examples that showcase the versatility and potential of stick-built construction:
1. Single-Family Homes:
The majority of residential homes are built using stick-built construction. Whether it’s a cozy cottage or a sprawling mansion, stick-built construction provides the flexibility to create unique designs and floor plans. From classic architectural styles to modern and contemporary designs, stick-built homes offer homeowners the ability to express their personal style and preferences. These homes often feature detailed interior finishes, customized features, and energy-efficient designs that cater to the needs and tastes of their occupants.
Read more: What Goes Under Peel And Stick Tile
2. Multi-Story Apartment Buildings:
Stick-built construction is commonly used for multi-story apartment buildings. The ability to efficiently assemble the structural framework and customize the design makes it an appealing option for developers. Stick-built apartment buildings can vary in size and style, from mid-rise structures to high-rise towers. The design flexibility enables developers to create diverse layouts and unit configurations, meeting the demands of the rental market while optimizing space utilization and maximizing profitability.
3. Office Buildings:
Stick-built construction is increasingly being utilized for office buildings. The versatility in design allows for the creation of functional and visually appealing workspaces. Office buildings constructed through stick-built methods can be customized to meet the specific needs of businesses, whether it’s an open-concept layout for collaborative work or specialized rooms for meetings and conferences. The efficient construction process helps reduce project timelines, allowing businesses to occupy their office spaces sooner.
4. Retail and Commercial Buildings:
Stick-built construction is widely used for retail and commercial buildings, such as shopping centers, restaurants, and entertainment venues. These structures can range from small independent shops to large-scale retail complexes. Stick-built construction provides the flexibility to create interesting architectural features and accommodate unique requirements, such as high ceilings and open spaces. The cost-effectiveness and efficient construction process also make stick-built construction an attractive choice for retail and commercial developers.
5. Educational Facilities:
Stick-built construction is commonly employed for educational facilities, including schools, colleges, and university buildings. These structures need to accommodate classrooms, laboratories, offices, and other specialized spaces. Stick-built construction offers the ability to customize the layout and design to meet the specific requirements of educational institutions. The cost-effectiveness and design flexibility contribute to the creation of functional and inspiring learning environments.
These examples highlight the wide range of applications for stick-built construction. From residential homes to commercial buildings and educational facilities, stick-built construction offers the versatility, cost-effectiveness, and design flexibility necessary to meet the unique demands of different construction projects. The ability to create customized designs, in combination with its efficient construction process, makes stick-built construction an appealing choice for many developers, builders, and homeowners.
Conclusion
Stick-built construction is a widely-used and versatile method in building construction. Its use of individual wooden sticks to create the structural framework provides design flexibility, cost-effectiveness, and energy efficiency. From residential homes to commercial buildings, stick-built construction offers numerous benefits that cater to the diverse needs of different construction projects.
The design flexibility of stick-built construction allows architects and builders to create unique and tailored structures. Whether it’s a single-family home, a multi-story apartment building, or a commercial complex, stick-built construction offers the freedom to customize designs and adapt to specific requirements. This adaptability enables the creation of functional and visually appealing spaces that meet the needs and preferences of the inhabitants.
Stick-built construction is also cost-effective, utilizing readily available and affordable materials such as dimensional lumber. The efficiency in the assembly process helps reduce construction time and labor costs. Additionally, stick-built construction provides excellent energy efficiency, thanks to optimal insulation and air sealing, resulting in lower energy consumption and reduced utility costs over time.
While stick-built construction has its advantages, it is essential to consider the potential drawbacks and environmental impact. Proper moisture management, maintenance, and responsible material sourcing are critical for minimizing risks such as moisture damage, waste generation, and deforestation. Implementing sustainable practices and exploring eco-friendly alternatives can further reduce the environmental footprint of stick-built construction.
When comparing stick-built construction to other methods, such as modular construction, concrete construction, and steel frame construction, each approach offers unique benefits and considerations. The choice of construction method depends on project requirements, budget, timeline, and desired outcomes. In some cases, a combination of construction methods may provide the best solution, leveraging the advantages of each approach for different aspects of the project.
In conclusion, stick-built construction continues to be a preferred choice for many construction projects due to its design flexibility, cost-effectiveness, and energy efficiency. With proper planning, skilled labor, and responsible construction practices, stick-built construction can deliver structurally-sound, visually appealing, and functional buildings that meet the needs of both builders and occupants.
Frequently Asked Questions about What Is Stick-Built Construction
Was this page helpful?
At Storables.com, we guarantee accurate and reliable information. Our content, validated by Expert Board Contributors, is crafted following stringent Editorial Policies. We're committed to providing you with well-researched, expert-backed insights for all your informational needs.
0 thoughts on “What Is Stick-Built Construction”