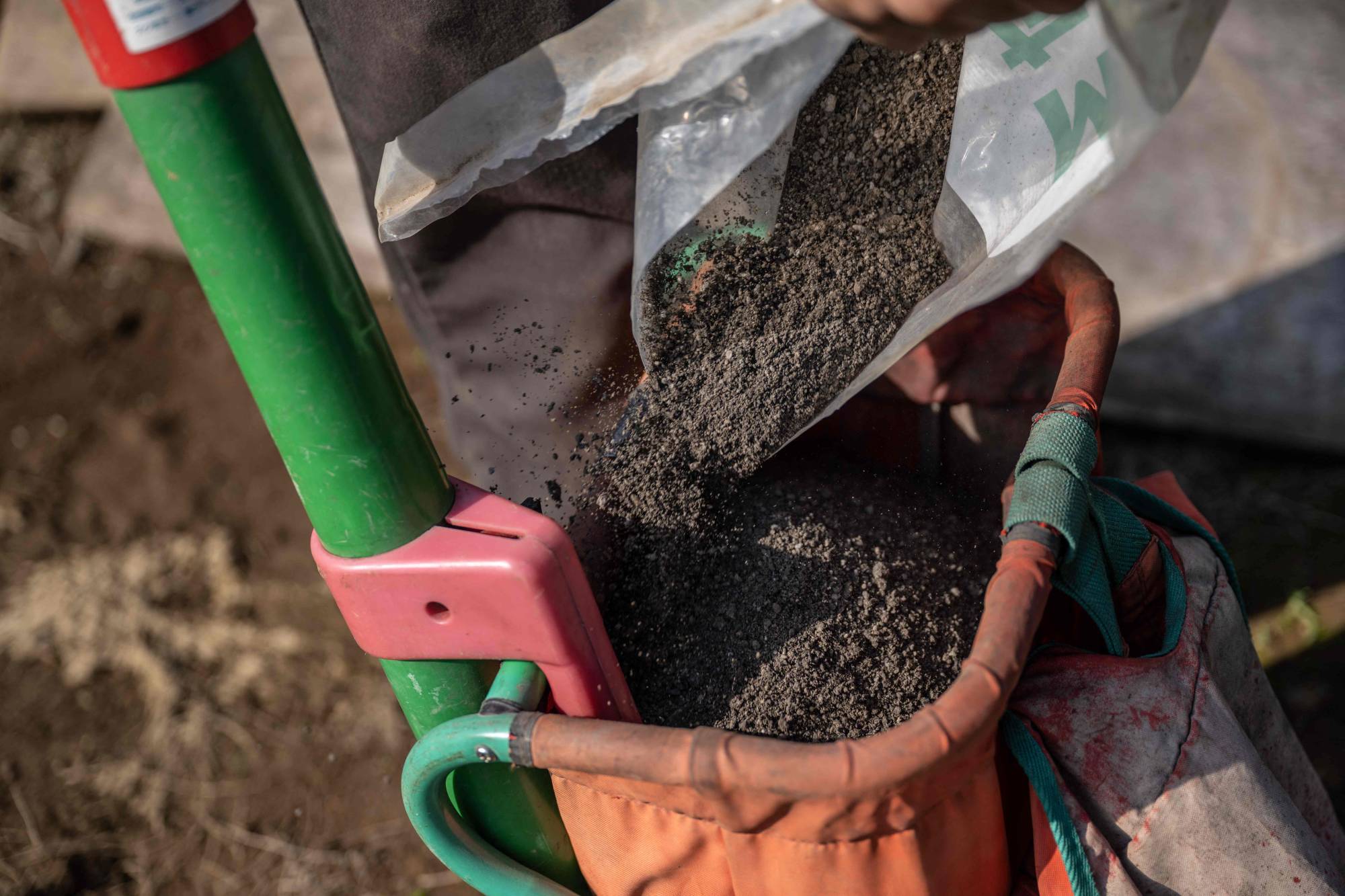
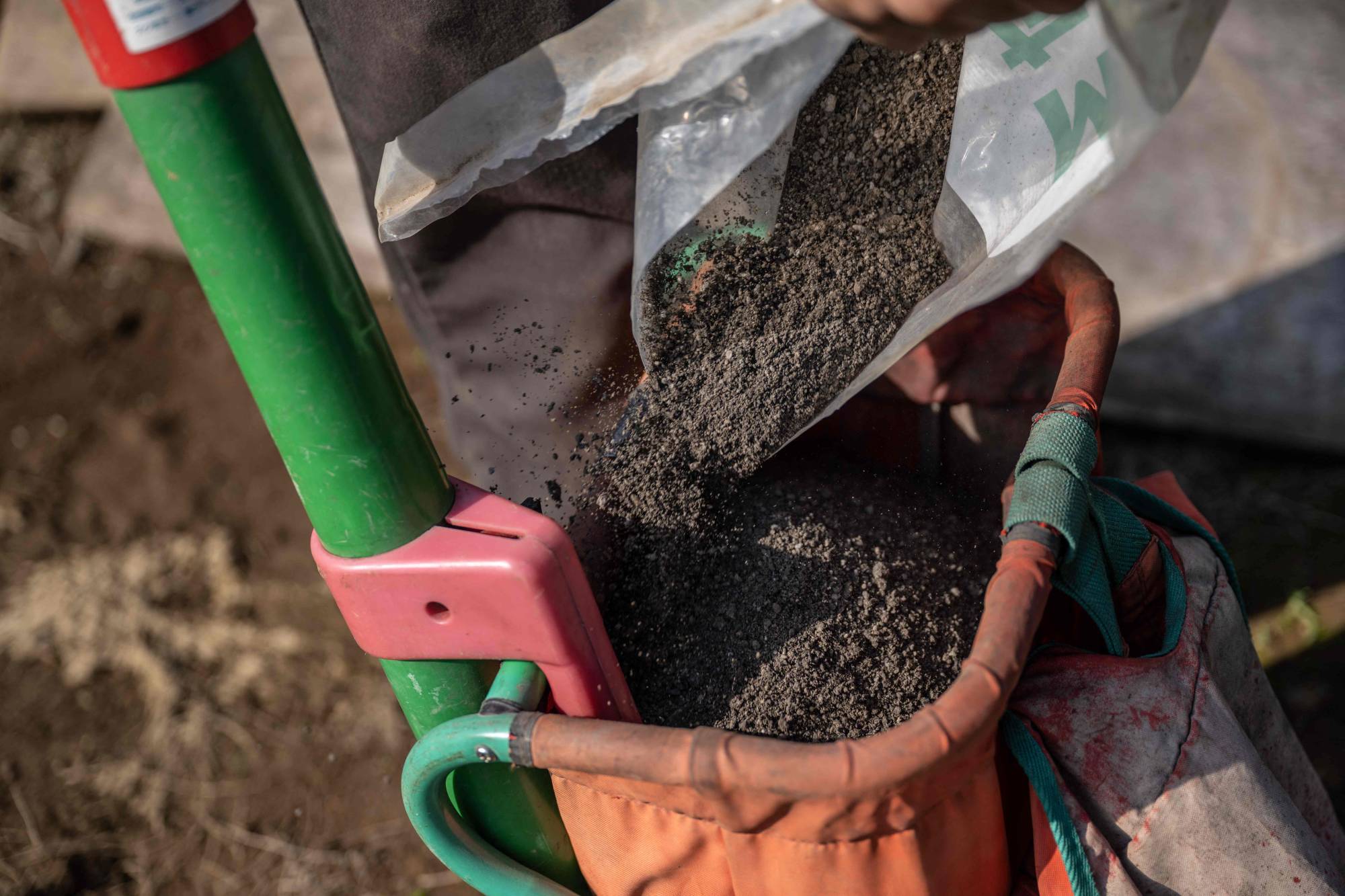
Articles
How Is Fertilizer Made
Modified: January 6, 2024
Discover the process of fertilizer production in this informative article. Learn how various ingredients are combined to create effective fertilizers for plant growth.
(Many of the links in this article redirect to a specific reviewed product. Your purchase of these products through affiliate links helps to generate commission for Storables.com, at no extra cost. Learn more)
Introduction
Welcome to the world of fertilizers, where science meets agriculture to enhance crop productivity. Fertilizers play a crucial role in providing essential nutrients to plants, ensuring healthy growth and bountiful harvests. Have you ever wondered how fertilizer is made? In this article, we will explore the fascinating process of fertilizer production, from raw materials to the final product.
As our global population continues to grow, the demand for food increases exponentially. This puts immense pressure on farmers to produce more crops in limited agricultural land. Alongside proper irrigation and pest control, the use of fertilizers allows farmers to maximize yields and meet the nutritional requirements of plants.
But what exactly is fertilizer? Simply put, fertilizers are substances that are added to the soil or plant to provide essential nutrients that may be lacking naturally. These nutrients include nitrogen (N), phosphorus (P), and potassium (K), also known as NPK, which are the primary elements necessary for plant growth.
The importance of fertilizers cannot be overstated. They help replenish nutrients that plants absorb from the soil during their growth cycle. Without adequate nutrition, plants become weak, have stunted growth, and yield low-quality produce. Fertilizers fill the nutritional gaps, promoting strong root systems, vibrant foliage, robust fruiting, and overall plant health.
There are two main sources of fertilizers: natural and synthetic. Natural fertilizers are derived from organic matter such as animal byproducts, compost, and decomposed plant material. Synthetic fertilizers, on the other hand, are chemically produced and formulated to provide specific nutrient ratios. Both types of fertilizers have their own benefits and considerations, but the focus of this article will be on the production process of synthetic fertilizers.
The process of making fertilizer involves several key steps, including raw material collection, processing and grinding, mixing and blending, granulation or prilling, drying and cooling, coating (optional), packaging, and distribution. Each step is carefully executed to ensure the production of high-quality fertilizer that meets the specific nutritional needs of different crops.
As we delve deeper into the fascinating realm of fertilizer production, we will explore each step in detail, understanding the raw materials involved, the machinery used, and the environmental considerations associated with this process. So, let’s embark on this journey and uncover the secrets behind the creation of fertilizer!
Key Takeaways:
- Fertilizer production is vital for agriculture, but environmental impacts must be managed. Sustainable practices, precision nutrient management, and innovations in production technologies are crucial for minimizing energy consumption, emissions, and nutrient pollution.
- Collaboration among stakeholders is essential for promoting sustainable fertilizer production and usage. Precision agriculture, conservation practices, and integrated nutrient management can balance agricultural productivity with environmental stewardship, ensuring a sustainable future.
What is Fertilizer?
Fertilizer is a substance that is added to the soil or plants to provide essential nutrients necessary for healthy plant growth. These nutrients are vital for plants to complete their life cycle, produce energy, and develop fruits, flowers, and seeds. Fertilizers replenish the nutrients that may be lacking in the soil, ensuring that plants have access to a balanced diet for optimal growth and productivity.
The primary nutrients found in fertilizers are nitrogen (N), phosphorus (P), and potassium (K), commonly referred to as the NPK ratio. These nutrients play different roles in plant development. Nitrogen is essential for leaf and stem growth, phosphorus promotes root development and flowering, while potassium aids in overall plant metabolism and disease resistance.
In addition to NPK, fertilizers also contain secondary and micronutrients. Secondary nutrients include calcium, magnesium, and sulfur, which are required in smaller quantities but still crucial for plant health. Micronutrients, such as iron, zinc, manganese, copper, and boron, are required in trace amounts for specific physiological functions in plants.
There are two main types of fertilizers: organic and inorganic (synthetic). Organic fertilizers are derived from natural sources, including animal manure, compost, bone meal, and fish emulsion. These fertilizers provide nutrients in a slow-release form and improve soil structure by increasing organic matter content. Organic fertilizers also enhance soil fertility and microbial activity, promoting long-term sustainability of agricultural systems.
Inorganic or synthetic fertilizers, on the other hand, are manufactured through chemical processes. These fertilizers are formulated to provide specific nutrient ratios, making them customizable for different crops’ nutritional needs. Synthetic fertilizers are highly soluble, allowing for quick nutrient uptake by plants. They are available in various forms, including granules, powders, and liquids, making them easy to apply and distribute across large areas.
The use of fertilizers is especially crucial in modern agriculture, where intensive farming practices, including monocropping and high-yield varieties, deplete the soil of essential nutrients rapidly. Fertilizers help replenish these nutrients and prevent nutrient deficiencies, ensuring that crops have access to the nutrients they need to thrive.
It is important to note that while fertilizers provide essential nutrients, they are not a substitute for proper soil management. Soil health is paramount, and maintaining a balanced nutrient profile, organic matter content, and microbial activity is essential for sustainable and productive agriculture. Fertilizers should be used in conjunction with other soil management practices, such as crop rotation, cover cropping, and organic amendments, to maintain soil fertility over the long term.
In summary, fertilizers are substances that provide vital nutrients to plants, promoting healthy growth, increased productivity, and improved crop quality. They come in organic and synthetic forms, each with its own advantages and considerations. By using fertilizers responsibly and in conjunction with sound soil management practices, farmers can optimize their production systems and contribute to sustainable agriculture.
The Importance of Fertilizer
Fertilizers play a vital role in modern agriculture, serving as a key tool for farmers to maximize crop productivity and meet the ever-growing demand for food. The use of fertilizers is essential for several reasons, all of which contribute to the overall sustainability and success of agricultural systems.
One of the primary reasons why fertilizers are important is their ability to replenish essential nutrients in the soil. As crops grow, they extract nutrients from the soil, gradually depleting its nutrient content. This depletion can lead to nutrient deficiencies, stunted growth, and reduced yields. Fertilizers help replenish the essential nutrients, ensuring that plants have access to a balanced diet that promotes healthy growth and development.
In addition to nutrient replenishment, fertilizers also help correct nutrient imbalances in the soil. Soils naturally vary in their nutrient composition, with some being deficient in certain nutrients while being abundant in others. Fertilizers can be tailored to provide the specific nutrients that are lacking, allowing farmers to address nutrient deficiencies and optimize plant growth.
The use of fertilizers also allows farmers to adopt high-yield farming practices. As the world’s population continues to increase, farmers face the challenge of producing more food on limited agricultural land. Intensive farming methods, such as monocropping and the use of high-yield crop varieties, can deplete the soil of nutrients at a faster rate. Fertilizers help compensate for this nutrient depletion, allowing farmers to sustain high crop yields and meet the food demands of a growing population.
Fertilizers also contribute to improved crop quality. By providing adequate nutrients, fertilizers help plants develop strong root systems, robust foliage, vibrant flowers, and bountiful fruiting. This results in higher-quality crops with better taste, color, and nutritional value. In a competitive market, high-quality produce fetches better prices and improves marketability for farmers.
Furthermore, the use of fertilizers can enhance agricultural efficiency and resource conservation. By providing plants with the necessary nutrients, fertilizers promote optimal nutrient uptake and utilization by the plant. This reduces wastage and ensures that nutrients are efficiently used, minimizing the risk of nutrient runoff into water bodies. Additionally, concentrated fertilizers allow farmers to target specific areas or crops, reducing the overall amount of fertilizer used and minimizing the impact on the environment.
It is important to note that the judicious and responsible use of fertilizers is essential to prevent potential negative environmental impacts. Overuse or improper application of fertilizers can lead to nutrient runoff into water bodies, causing water pollution and eutrophication. This highlights the need for proper fertilizer management practices, including soil testing, nutrient planning, and application techniques tailored to specific crops and soil conditions.
In summary, fertilizers are of utmost importance in modern agriculture. They play a critical role in replenishing nutrients in the soil, correcting nutrient imbalances, increasing crop yields, improving crop quality, and enhancing agricultural efficiency. By using fertilizers in a responsible and sustainable manner, farmers can maximize productivity, contribute to food security, and promote the long-term sustainability of agricultural systems.
Natural Fertilizer Sources
Natural fertilizers, also known as organic fertilizers, are derived from natural sources such as plants, animals, and minerals. They serve as an alternative to synthetic fertilizers, providing a more sustainable and environmentally friendly option for nourishing crops. Here are some common natural fertilizer sources:
- Manure: Animal manure, such as cow, horse, poultry, and sheep manure, is a valuable source of nutrients for plants. Manure contains a variety of essential elements like nitrogen, phosphorus, potassium, and organic matter. It improves soil structure, enhances water-holding capacity, and promotes microbial activity. The nutrient content of manure varies depending on the animal species, diet, and handling practices.
- Compost: Compost is created through the decomposition of organic matter, including food waste, yard trimmings, and crop residues. It is a rich source of nutrients, organic matter, and beneficial microorganisms. Compost improves soil structure, increases water retention, and enhances nutrient availability to plants. It also helps suppress diseases and pests, making it an excellent natural fertilizer choice for organic farming.
- Bone Meal: Bone meal is derived from the grinding and steaming of animal bones. It is a slow-release fertilizer that is rich in phosphorus and calcium, essential nutrients for root development and overall plant growth. Bone meal is commonly used to promote flowering and fruiting in plants. It is especially beneficial for crops with high phosphorus requirements, such as tomatoes, peppers, and flowering ornamental plants.
- Fish Emulsion: Fish emulsion is made from fish waste products, such as fish carcasses, heads, and scraps. It is an excellent source of nitrogen, phosphorus, and trace minerals. Fish emulsion is easily absorbed by plants, promoting rapid growth and green foliage. It also enhances microbial activity in the soil and improves soil fertility and nutrient availability.
- Seaweed: Seaweed, harvested from oceans or seaweed farms, is a natural fertilizer rich in micronutrients, including iron, zinc, manganese, and potassium. It also contains growth-promoting hormones and beneficial enzymes that stimulate plant growth, root development, and stress resistance. Seaweed can be used as a liquid extract or incorporated into the soil as a mulch or compost amendment.
- Green Manure: Green manure refers to the practice of growing specific plants, such as legumes (clover, peas, vetch) or cover crops (rye, buckwheat, alfalfa), and then incorporating them into the soil while they are still green and actively growing. Green manure crops improve soil fertility by fixing nitrogen from the air, adding organic matter, and preventing soil erosion. They serve as a natural source of nutrients and contribute to long-term soil health.
These natural fertilizer sources offer numerous benefits beyond nutrient supply. They improve soil structure, increase water retention, promote beneficial microbial activity, and reduce the reliance on synthetic fertilizers. Natural fertilizers are a valuable option for organic farmers and gardeners who prioritize sustainability, soil health, and environmental stewardship.
Synthetic Fertilizer Sources
Synthetic fertilizers, also known as inorganic fertilizers, are chemically manufactured fertilizers that provide essential nutrients to plants. These fertilizers are typically formulated to specific nutrient ratios, allowing for precise and targeted nutrient delivery. Here are some common synthetic fertilizer sources:
- Ammonium Nitrate: Ammonium nitrate is a common nitrogen-based synthetic fertilizer. It contains both nitrate and ammonium forms of nitrogen, making it readily available to plants. Ammonium nitrate is highly soluble in water, allowing for quick nutrient uptake by plants. It is often used as a quick-release nitrogen source for crops that require immediate nutrient availability.
- Urea: Urea is another nitrogen-based synthetic fertilizer that is widely used in agriculture. It is a concentrated source of nitrogen and is converted into ammonium in the soil through a process called hydrolysis. Urea provides a balanced supply of nitrogen without favoring the nitrate or ammonium forms, making it suitable for a wide range of crops and soil types.
- Triple Superphosphate (TSP): TSP is a phosphorus-based synthetic fertilizer that is produced by reacting phosphate rock with phosphoric acid. It contains high levels of water-soluble phosphorus, making it readily available to plants. TSP is commonly used to promote root development and flowering in plants, especially in areas with low soil phosphorus levels.
- Potassium Chloride: Potassium chloride, or Muriate of Potash, is a widely used potassium-based synthetic fertilizer. It provides readily available potassium to plants, which is essential for overall plant health, enzyme activation, and disease resistance. Potassium chloride is often applied to crops that have high potassium requirements, such as fruits, vegetables, and grains.
- Compound Fertilizers: Compound fertilizers are synthetic fertilizers that contain a balanced combination of nitrogen, phosphorus, and potassium. These fertilizers are formulated to specific nutrient ratios, such as NPK 10-10-10 or NPK 20-10-10, based on the nutritional requirements of different crops. Compound fertilizers offer convenience and efficiency in supplying multiple nutrients in a single application.
- Micronutrient Fertilizers: Synthetic fertilizers also include those that provide essential micronutrients to plants. These fertilizers contain specific trace elements, such as iron, zinc, manganese, copper, and boron, which are required in small quantities but are essential for plant growth. Micronutrient fertilizers are used to correct micronutrient deficiencies in crops, ensuring optimal plant health and productivity.
Synthetic fertilizers offer several advantages due to their precise nutrient composition and availability. They provide readily absorbable nutrients, ensuring that plants have access to the elements they need for growth and development. Synthetic fertilizers are also highly soluble, allowing for rapid nutrient uptake by plants. Their concentrated nature makes them efficient to transport and distribute across large agricultural areas.
However, it is important to note that the use of synthetic fertilizers requires careful management to prevent potential environmental drawbacks. Overuse or improper application can lead to nutrient runoff, soil acidification, and water pollution. Therefore, responsible fertilizer application practices, such as soil testing, nutrient calculations, and appropriate timing and placement, are critical to mitigate negative impacts and promote sustainability in agriculture.
While synthetic fertilizers have their advantages, it is important to consider a balanced approach to nutrient management that integrates natural fertilizers, organic amendments, and sustainable soil management practices. This holistic approach ensures that soil fertility is maintained, environmental impacts are minimized, and crop productivity is optimized in the long term.
Read more: How Is A Mattress Made
How Fertilizer is Made
The production of fertilizer involves a carefully orchestrated process that transforms raw materials into the final products that deliver essential nutrients to plants. While the specific methods and machinery used may vary depending on the type of fertilizer being produced, the general production process typically includes the following steps:
Step 1: Raw Material Collection
The first step in fertilizer production is the collection of raw materials. These materials can include various sources, such as phosphate rock, potassium minerals, ammonia, sulfur, and other essential nutrients. Phosphate rock and potassium minerals are primarily mined from deposits in the earth’s crust, while other components might be obtained from chemical processes or waste materials.
Step 2: Processing and Grinding
Once the raw materials have been collected, they undergo a process of crushing, grinding, and sizing. This step ensures that the raw materials are in a suitable form for further processing. The materials are generally crushed into small particles to increase their surface area and make them more accessible for chemical reactions in later stages.
Step 3: Mixing and Blending
After processing and grinding, the raw materials are thoroughly mixed and blended. This step ensures that the different components are uniformly distributed, allowing for consistent nutrient content throughout the fertilizer. The mixing and blending process may also involve the addition of trace elements or other additives to achieve specific nutrient ratios or enhance fertilizer performance.
Read more: How Is Glassware Made
Step 4: Granulation or Prilling
Granulation or prilling is a crucial step in fertilizer production, where the mixed and blended materials are transformed into granules or pellets. Granulation involves the use of a granulator machine, which agglomerates the materials into larger particles. Prilling, on the other hand, utilizes a prilling tower or drum to form small spheres or droplets. These granules or prills provide controlled-release properties and facilitate the application and distribution of fertilizer.
Step 5: Drying and Cooling
Following the granulation or prilling process, the newly formed granules or prills undergo drying and cooling. Drying removes any excess moisture from the product, ensuring stability and preventing caking or clumping. Cooling helps to further stabilize the temperature of the fertilizer and prepares it for subsequent processing and packaging.
Step 6: Coating (optional)
In some cases, a coating may be applied to the fertilizer granules or prills. Coating materials, such as polymers or sulfur, can serve various purposes, including controlled-release of nutrients, improved handling characteristics, reduced dust formation, and enhanced fertilizer efficiency. Coating is an optional step and is primarily used for specialized or value-added fertilizer products.
Step 7: Packaging and Distribution
The final step in fertilizer production is the packaging and distribution of the finished product. The fertilizer is typically packaged in bags or bulk containers, ready for transport and sale. Proper packaging ensures product integrity, prevents moisture absorption or spillage, and provides clear labeling of nutrient content, application rates, and safety instructions. The finished fertilizer is then distributed and made available to farmers, gardeners, and agricultural industries.
Throughout the production process, it is essential to consider environmental impacts and adopt sustainable practices. This includes minimizing energy consumption, managing waste and emissions, optimizing resource utilization, and adhering to regulatory standards to ensure responsible fertilizer production.
Overall, fertilizer production involves a series of carefully controlled steps that convert raw materials into a valuable product that fuels plant growth and enhances agricultural productivity. By understanding the intricacies of the production process, we can appreciate the importance of high-quality fertilizers in supporting sustainable agriculture.
Read more: How Are Rugs Made
Step 1: Raw Material Collection
In the production of fertilizers, the first crucial step is the collection of raw materials. These materials serve as the foundation for the nutrient-rich products that will eventually nourish plants and promote their growth. The specific raw materials used may vary depending on the type of fertilizer being produced, but some common sources include phosphate rock, potassium minerals, ammonia, sulfur, and other essential nutrients.
Phosphate rock is a key raw material for producing phosphate-based fertilizers. It is primarily mined from deposits in the earth’s crust, often found in sedimentary formations. Phosphate rock contains high concentrations of phosphorus, an essential nutrient for plant growth and development. The quality and composition of phosphate rock can vary depending on its geological origin, with different deposits having different levels of phosphorus content and impurities.
Potassium minerals, such as potassium chloride or potassium sulfate, are another important raw material in fertilizer production. Potassium is a primary macronutrient required by plants for essential functions like enzyme activation, photosynthesis, and osmotic regulation. Potassium minerals are obtained through mining operations or extraction processes that concentrate the minerals from saltwater or underground deposits.
Ammonia is a critical component in the manufacturing of nitrogen-based fertilizers. It is primarily produced through the Haber-Bosch process, which combines nitrogen from the air with hydrogen derived from natural gas or coal. Ammonia serves as a concentrated source of nitrogen, an essential nutrient for plant growth. It is a key building block for the synthesis of various nitrogen fertilizers, including ammonium nitrate and urea.
Sulfur is another important raw material used in fertilizer production, particularly for sulfur-based fertilizers. Sulfur can be obtained through various sources, including natural gas, crude oil, and sulfide minerals. Sulfur is an essential component of proteins, enzymes, and vitamins in plants, and its incorporation into fertilizers helps address sulfur deficiencies in the soil.
In addition to these primary raw materials, other essential nutrients and micronutrients are often incorporated into fertilizers. These may include elements like iron, zinc, manganese, copper, and boron, which are vital for various physiological processes in plants. These micronutrients can be derived from different sources, such as mineral deposits, industrial byproducts, or chemical reactions.
Raw material collection is a critical phase in fertilizer production, as the quality and composition of the materials influence the nutrient content and characteristics of the final product. Sustainable sourcing practices and responsible mining operations are crucial to ensure the availability of raw materials while minimizing environmental impacts. Additionally, quality control measures are implemented to ensure that the collected materials meet the desired specifications and standards for fertilizer production.
By carefully selecting and collecting the appropriate raw materials, fertilizer manufacturers can lay the foundation for producing high-quality fertilizers that deliver vital nutrients to plants, contributing to improved crop yields and sustainable agriculture.
Step 2: Processing and Grinding
After the raw materials have been collected for fertilizer production, the next crucial step is processing and grinding. This step involves converting the raw materials into a suitable form for further processing and ensures that they are finely ground to enhance their reactivity and nutrient availability.
The processing and grinding stage begins with the raw materials being carefully inspected and sorted to remove any impurities, contaminants, or unwanted substances. This quality control process ensures that only high-quality materials are used in the production of fertilizers.
Once the raw materials have been inspected and sorted, they undergo grinding to reduce their particle size and increase their surface area. Grinding is typically achieved through mechanical methods, such as crushing, milling, or pulverizing. The chosen method depends on the nature of the raw materials and the desired size reduction.
The grinding process is crucial because it improves the reactivity of the raw materials, allowing them to react more efficiently with other components during subsequent stages of fertilizer production. Finely ground particles facilitate faster and more thorough mixing, providing a homogeneous blend of nutrients in the final fertilizer product.
The grinding process also helps to break down any lumps, clumps, or agglomerations that may have formed during raw material collection or storage. This is important to ensure uniformity and consistency in the final product, as large clumps could lead to uneven nutrient distribution when the fertilizer is applied to the soil.
Grinding the raw materials imparts a larger surface area for chemical reactions to occur, ensuring that the nutrients are readily available for plant uptake. The increased surface area enhances the dissolution and release of nutrients, allowing plants to absorb them more effectively.
Additionally, grinding can help improve the physical properties of the raw materials, such as flowability and bulk density. This is particularly important for the subsequent stages of fertilizer production, as well as for packaging and transportation efficiency.
It is worth noting that the grinding process must be carefully controlled to ensure that the desired particle size is achieved without compromising the integrity or composition of the raw materials. Overgrinding can lead to excessive energy consumption and produce particles that are too fine, resulting in dust generation and potential nutrient loss.
The extent of grinding required for fertilizer production may vary depending on the specific type of fertilizer being manufactured. Different fertilizers have different particle size requirements, depending on factors such as the intended method of application (granules, powders, etc.) and the desired nutrient release characteristics.
Overall, the processing and grinding stage is a critical step in fertilizer production. It prepares the raw materials by reducing their particle size, increasing their surface area, and enhancing their reactivity. This ensures that the nutrients are readily available for plant uptake, contributing to improved crop productivity and the efficient delivery of essential nutrients through fertilizers.
Step 3: Mixing and Blending
After the processing and grinding of raw materials, the next step in fertilizer production is mixing and blending. This step involves the careful combination of various ingredients to create a uniform and well-balanced fertilizer product that provides the necessary nutrients to plants.
The mixing and blending process is crucial to ensure that the final fertilizer product has consistent nutrient composition throughout. It involves the thorough mixing of the processed raw materials, including the ground particles, trace elements, and any additional additives required to achieve the desired nutrient ratios.
The primary objective of mixing and blending is to create a homogeneous mixture of all the components. This ensures that each granule or pellet of the fertilizer contains an even distribution of essential nutrients. Homogeneity is crucial for uniform nutrient application when the fertilizer is spread in the field or garden.
There are various mixing and blending technologies and equipment employed in fertilizer production. These can range from simple batch mixers to more sophisticated and automated blending systems. The choice of mixing equipment depends on factors such as the scale of production, the type of fertilizer being produced, and the desired degree of blending precision.
Different ingredients are mixed in precise proportions to achieve the desired nutrient ratio. For example, nitrogen (N), phosphorus (P), and potassium (K), commonly referred to as NPK, are blended in specific proportions to match the nutritional requirements of different crops or soil conditions.
In addition to the primary nutrients, micronutrients and other additives may be incorporated during the blending process. These micronutrients, such as iron, zinc, boron, and manganese, are essential in small quantities for optimal plant growth and development. They are included to address specific nutrient deficiencies and ensure complete nutrient coverage in the final fertilizer product.
Blending also allows the incorporation of supplementary additives, such as anti-caking agents, colorants, or coatings. These additives serve various purposes, including preventing the formation of lumps or clumps in the final product, enhancing the visual appearance, or providing specialized functionalities like slow-release or controlled-release nutrient delivery.
Throughout the mixing and blending process, rigorous quality control measures are in place to verify that the ingredients are accurately weighed and mixed to ensure consistency and accuracy in the final product. Samples are often taken for analysis to verify nutrient content and ensure compliance with regulatory standards.
Proper mixing and blending of fertilizers are essential to provide a consistent nutrient supply to plants, promote uniform crop growth, and optimize the effectiveness of nutrient application. By achieving a uniform distribution of nutrients within the fertilizer, the mixing and blending process ensures that plants receive the appropriate balance of essential elements for healthy development and maximum yield.
Overall, the mixing and blending stage is a critical step in fertilizer production. It brings together various ingredients and additives, ensuring an even distribution of essential nutrients and micronutrients in the final product. By achieving a well-blended fertilizer, this stage ensures that plants have access to a balanced diet of nutrients required for their optimal growth and productivity.
Step 4: Granulation or Prilling
After the mixing and blending process in fertilizer production, the next step is granulation or prilling. These processes involve the transformation of the well-mixed fertilizer materials into granules or prills, which are easier to handle, store, and apply in the field or garden.
Granulation is a widely used method for creating fertilizer granules. It involves agglomerating the finely mixed fertilizer materials into larger particles or granules of specific sizes and shapes. The granulation process helps improve the physical properties of the fertilizer, making it more convenient to handle and apply.
The granulation process typically involves several steps. First, the well-mixed fertilizer material is fed into a granulator machine. This machine employs a combination of agitation, pressure, and moisture to compact the material into granules of the desired size range. The granules are formed by the cohesive forces generated during the process, binding the particles together.
Granulation offers several advantages for fertilizer production. It helps prevent segregation of the fertilizer components during storage and transportation, ensuring a consistent distribution of nutrients throughout the granules. The granules also have improved flowability, reducing the risk of clogging or clumping during application.
The size and shape of the granules can be controlled through the design and settings of the granulator machine. Different types of granulators, such as rotary drum granulators, pan granulators, or extrusion granulators, can be used depending on the specific fertilizer formulation and desired granule characteristics.
Prilling, on the other hand, is a process that forms small spherical or droplet-shaped particles known as prills. Prills are typically smaller than granules and have a more uniform size and shape. Prilling is often used for certain types of fertilizers, especially those that require slow-release or controlled-release properties.
The prilling process involves the use of a prilling tower or a prilling drum. The well-mixed fertilizer material is sprayed or dripped in the form of liquid droplets from the top of the tower or drum. As these droplets fall, they solidify and cool, forming prills that are collected at the bottom. The resulting prills have a coating or solid outer layer that helps regulate the nutrient release over time.
Both granulation and prilling processes contribute to the improved handling and application of fertilizers. The resulting granules or prills are easier to spread and distribute in the field, ensuring a more uniform coverage and nutrient release. They also provide protection to the nutrients, reducing nutrient loss through volatilization or leaching.
The specific method of granulation or prilling employed in fertilizer production depends on factors such as the desired product characteristics, nutrient release requirements, and production capacity. Manufacturers carefully control the parameters and conditions during these processes to ensure the production of high-quality fertilizer that meets the required specifications.
By transforming the well-mixed fertilizer materials into granules or prills, the granulation or prilling stage of production allows for efficient and controlled nutrient application. It helps enhance the effectiveness of fertilizers, minimizing nutrient losses and ensuring that plants receive a consistent supply of essential nutrients throughout their growth cycle.
Read more: How Carpets Are Made
Step 5: Drying and Cooling
After the granulation or prilling process in fertilizer production, the next step is drying and cooling. This stage is crucial for removing excess moisture from the newly formed granules or prills and reducing their temperature to prepare them for subsequent processing and packaging.
Drying is essential to prevent the granules or prills from clumping together and to ensure their stability during storage and transportation. Excess moisture can lead to undesirable effects such as caking, which makes the fertilizer difficult to handle and apply in the field. Drying also helps improve the flowability and shelf life of the final fertilizer product.
The drying process involves the use of specially designed dryers or drying systems. These systems employ techniques such as hot air circulation, fluidized bed drying, or rotary drying to remove moisture from the surface and interior of the granules or prills, depending on the scale of production and the specific fertilizer formulation.
The drying temperature and duration are carefully controlled during this process to ensure that the moisture is effectively evaporated while minimizing any negative effects on the nutrient content or physical properties of the fertilizer. Improper drying can cause nutrient degradation or excessive energy consumption.
Once the drying stage is complete, the granules or prills proceed to the cooling stage. Cooling allows the newly dried fertilizer to reach a lower temperature, making it safe for subsequent handling, packaging, and storage. Cooling prevents the granules or prills from sticking together and helps maintain their structural integrity.
Cooling can be achieved through various methods, including ambient air cooling, forced air cooling, or indirect cooling using chilled air or water. The specific cooling method employed depends on factors such as the production scale and the characteristics of the fertilizer being processed.
During cooling, the granules or prills are often conveyed through a cooling system, which utilizes fans, blowers, or cooling towers to control the temperature and airflow. The cooling process is carefully monitored to achieve the desired temperature range for safe handling and packaging.
Proper drying and cooling ensure that the granules or prills maintain their physical structure, preventing them from becoming brittle or susceptible to breakage. It also minimizes the potential for moisture condensation that could lead to caking or clumping during storage.
In addition to enhancing the physical properties of the fertilizer, the drying and cooling stage allows for the subsequent application of coating materials, if desired. Coatings can provide additional functionalities such as controlled-release nutrient delivery, dust suppression, or improved granule durability.
Throughout the drying and cooling process, parameters such as temperature, moisture content, and cooling time are closely monitored and controlled to ensure the production of high-quality fertilizer with optimal physical properties and nutrient stability.
By effectively removing excess moisture and cooling the granules or prills, the drying and cooling stage prepares the fertilizer for packaging and distribution. It ensures that the final product is dry, stable, and ready for application, allowing for efficient and convenient use by farmers, gardeners, and agricultural industries.
Step 6: Coating (optional)
In the fertilizer production process, Step 6 involves coating the granules or prills with a specialized layer. While coating is an optional step, it offers several advantages in terms of functionality, nutrient release control, and improved handling characteristics.
The coating process typically involves the application of a thin layer of coating material onto the surface of the granules or prills. This coating layer serves multiple purposes, depending on the specific needs of the fertilizer being produced.
One of the primary functions of coating is to provide controlled-release properties for the fertilizer. Controlled-release fertilizers release nutrients gradually over time, ensuring a steady and prolonged supply of nutrients to plants. This helps improve nutrient efficiency, reduces the risk of nutrient leaching, and minimizes the number of fertilizer applications required.
The coating material used for controlled-release fertilizers is typically formulated to dissolve slowly, allowing the nutrients to be released gradually as the coating breaks down. Common coating materials include polymers, sulfur, resins, or other specialty compounds that are chosen based on their ability to control nutrient release rates.
Coating can also help alleviate issues related to dust formation during handling and application of fertilizers. The coating layer provides a protective barrier around the granules or prills, reducing the amount of fine particles that can become airborne and cause dust. This contributes to improved worker safety, prevents loss of nutrients through dust, and eases the clean-up process during application.
Furthermore, coating can improve the physical characteristics of the fertilizer by reducing caking or clumping tendencies. The coating material acts as a lubricant between the granules or prills, preventing them from sticking together. This enhances the flowability and spreadability of the fertilizer, ensuring even distribution and coverage when applied to the soil.
Coatings may also serve aesthetic purposes. They can provide colorants to enhance the visual appearance of the fertilizer or add specific properties like UV resistance for products intended for outdoor use.
The coating process itself can be accomplished through various methods, such as fluidized bed coating, rotary drum coating, sprays, or controlled-release encapsulation techniques. The choice of coating method depends on factors such as the fertilizer formulation, production scale, and desired coating thickness or uniformity.
Quality control measures are vital during the coating process to ensure an even and consistent coating application. Proper monitoring of coating thickness, adherence, and uniformity helps maintain the desired functionality and performance of the coated fertilizers.
Overall, while optional, the coating step in fertilizer production offers numerous benefits. It provides controlled-release properties, minimizes dust formation, improves handling characteristics, and even enhances visual appearance. Coated fertilizers provide added value and specialized properties that address specific plant nutrient requirements, application needs, and environmental considerations.
By incorporating a coating layer, fertilizer manufacturers can tailor their products to meet the needs of various crops and cropping systems, while optimizing nutrient release efficiency and minimizing potential environmental impacts.
Step 7: Packaging and Distribution
After the completion of the fertilizer production process, the next and final step is packaging and distribution. This step involves packaging the finished fertilizer product and preparing it for transport to various markets and end users, including farmers, gardeners, and agricultural industries.
The packaging of fertilizers serves several important purposes. It protects the fertilizer from moisture, contaminants, and physical damage during handling and storage. It also provides convenient and efficient means of transportation, handling, and application.
Fertilizers are typically packaged in bags or bulk containers, depending on their form, weight, and the specific requirements of the market. Bagged fertilizers are commonly available in various sizes, ranging from a few kilograms to large-scale industrial-sized bags. Bulk containers, such as trucks or railcars, are used for larger quantities, allowing for efficient distribution to agricultural regions or blending facilities.
Different types of packaging materials are used depending on factors such as product characteristics, durability, and environmental considerations. Common packaging materials include plastic bags, paper bags, woven polypropylene bags, or even advanced eco-friendly packaging options made from recycled or biodegradable materials.
During the packaging process, rigorous quality control measures are implemented to verify the accuracy of filling, sealing, and labeling. The correct weight and nutrient content are ensured for each package, and proper labeling is applied to provide necessary information, including nutrient analysis, handling instructions, and safety precautions.
In addition to packaging, labeling is a crucial component of the packaging and distribution stage. Accurate and clear labeling helps users identify the type of fertilizer, the nutrient composition, recommended application rates, and any specific instructions or precautions. Proper labeling ensures that users can make informed decisions and apply the fertilizer correctly to achieve optimal results.
Once packaged, the fertilizers are ready for distribution to their intended markets. Distribution networks vary based on the scale and reach of the manufacturer, as well as the demand for the product. Distribution channels may include direct sales to farmers, wholesalers, retailers, or partnerships with agricultural cooperatives or supply chains.
Efficient logistics and transportation play a crucial role in the distribution process. Transportation methods can include trucks, trains, ships, or a combination thereof, depending on the distance and volume of fertilizer being delivered. Proper handling and storage facilities are also important to maintain product quality and prevent contamination or degradation during transport.
Overall, the packaging and distribution stage is the final step that ensures the fertilizer reaches the end users in a safe and ready-to-use condition. Well-designed packaging protects the integrity of the product, while clear labeling provides essential information for its proper and efficient application.
By ensuring proper packaging and secure distribution, fertilizer manufacturers contribute to the successful utilization of their products by farmers, enabling them to provide crops with the necessary nutrients for optimal growth, yield, and overall agricultural productivity.
Environmental Impacts of Fertilizer Production
Fertilizer production plays a crucial role in sustaining agricultural productivity and feeding the growing global population. However, it is essential to recognize and address the potential environmental impacts associated with fertilizer production to ensure sustainable and responsible agricultural practices. Here are some key environmental considerations:
Read more: How To Fertilize Mums
1. Energy Consumption:
The production of fertilizers requires significant energy inputs, particularly during processes such as raw material extraction, processing, and drying. Energy-intensive operations can contribute to greenhouse gas emissions and the depletion of fossil fuel resources. Efforts to improve energy efficiency and explore alternative energy sources can help mitigate these impacts.
2. Emissions:
Fertilizer production, particularly for nitrogen-based fertilizers, can result in the release of greenhouse gases, including carbon dioxide (CO2) and nitrous oxide (N2O). CO2 emissions may occur during the manufacturing processes, while N2O emissions can result from the microbial breakdown of nitrogen-based fertilizers in the soil. These emissions contribute to climate change and global warming. Implementing advanced technologies and management practices can minimize these emissions.
3. Nutrient Runoff and Water Pollution:
Excessive or improper use of fertilizers can lead to nutrient runoff into water bodies, causing eutrophication. Nutrient runoff, particularly nitrogen and phosphorus, can lead to excessive algal growth, depleting oxygen levels in water, and endangering aquatic life. Proper nutrient management practices, including precise application methods, soil testing, and nutrient planning, can help reduce nutrient runoff and water pollution.
4. Soil and Land Degradation:
Unbalanced or excessive fertilizer application can lead to soil and land degradation. Overuse of certain nutrients, such as nitrogen, can disrupt soil microbial activity and alter soil pH, affecting soil health and fertility. Careful nutrient management, including following recommended application rates and incorporating organic matter, can help maintain soil fertility and minimize the risk of degradation.
Read more: How Is Candy Glass Made
5. Resource Depletion:
The extraction of raw materials for fertilizer production, such as phosphate rock and potassium minerals, can contribute to resource depletion. These materials are finite and non-renewable resources. Sustainable mining practices, recycling of nutrients, and exploring alternative sources can help minimize resource depletion and promote resource conservation.
6. Air and Water Quality:
The release of dust, particulate matter, and emissions during fertilizer production can impact air quality. Contaminant discharge from manufacturing processes, if not properly managed, can also contribute to water pollution. Implementing proper emission control measures, wastewater treatment, and waste management practices are vital to protect air and water quality.
To address these environmental impacts, the fertilizer industry has been actively working on improving environmental performance through innovations in production technologies, efficient nutrient management practices, and the development of environmentally friendly fertilizers. This includes the adoption of cleaner production processes, the use of precision agriculture techniques, and the promotion of sustainable farming practices.
Additionally, farmers, policymakers, and agricultural stakeholders can contribute to minimizing the environmental impacts of fertilizer production through responsible fertilizer use, including proper nutrient management, balanced fertilization, erosion control measures, and sustainable soil management practices.
By adopting a holistic approach to fertilizer production, including considering the environmental impacts and implementing sustainable practices, the industry can help balance agricultural productivity with environmental sustainability, ensuring the long-term viability of food production systems.
Fertilizer is made through a process called the Haber-Bosch process, which combines nitrogen from the air with hydrogen from natural gas to create ammonia. This ammonia is then used to produce various types of fertilizers.
Conclusion
Fertilizer production plays a vital role in modern agriculture, providing the essential nutrients necessary for healthy plant growth and increased crop productivity. However, it is crucial to understand and address the potential environmental impacts associated with fertilizer production. By implementing sustainable practices and promoting responsible fertilizer use, we can ensure the long-term sustainability of agricultural systems while minimizing negative environmental effects.
Throughout the fertilizer production process, from raw material collection to packaging and distribution, steps are taken to optimize nutrient content, improve handling characteristics, and enhance efficiency. Natural and synthetic fertilizers offer different benefits and considerations, allowing farmers to choose the best approach for their specific needs.
Environmental impacts must be carefully managed throughout fertilizer production. Energy consumption, emissions, nutrient runoff, and soil degradation are among the key concerns. By investing in energy-efficient technologies, exploring alternative energy sources, and implementing precision nutrient management practices, we can minimize energy consumption, reduce greenhouse gas emissions, and mitigate the risk of nutrient pollution in water bodies.
Appropriate nutrient management practices, such as soil testing, balanced fertilization, and controlled-release formulations, help optimize nutrient use efficiency, preventing overuse and minimizing the risk of nutrient runoff. Adhering to recommended application rates and incorporating organic matter into soils contribute to maintaining soil health, minimizing soil degradation, and improving long-term fertility.
The fertilizer industry is continuously striving to develop and adopt environmentally friendly solutions. Innovations in production technologies, improvements in resource management, and the development of specialized fertilizers, including controlled-release formulations and micronutrient supplements, offer ways to reduce the environmental footprint of fertilizer production.
Collaboration among farmers, policymakers, researchers, and industry stakeholders is crucial to promote sustainable fertilizer production and use. Encouraging and supporting initiatives such as precision agriculture, conservation agriculture, and integrated nutrient management can contribute to balancing agricultural productivity with environmental stewardship.
In conclusion, fertilizer production is essential for meeting the global food demand, but it must be approached with environmental sustainability in mind. By adopting responsible fertilizer production and usage practices, we can ensure that agriculture remains productive while protecting the environment, preserving natural resources, and supporting a sustainable future for generations to come.
Frequently Asked Questions about How Is Fertilizer Made
Was this page helpful?
At Storables.com, we guarantee accurate and reliable information. Our content, validated by Expert Board Contributors, is crafted following stringent Editorial Policies. We're committed to providing you with well-researched, expert-backed insights for all your informational needs.
0 thoughts on “How Is Fertilizer Made”