Home>Furniture & Design>Interior Design Trends>How Are Glass Bottles Made
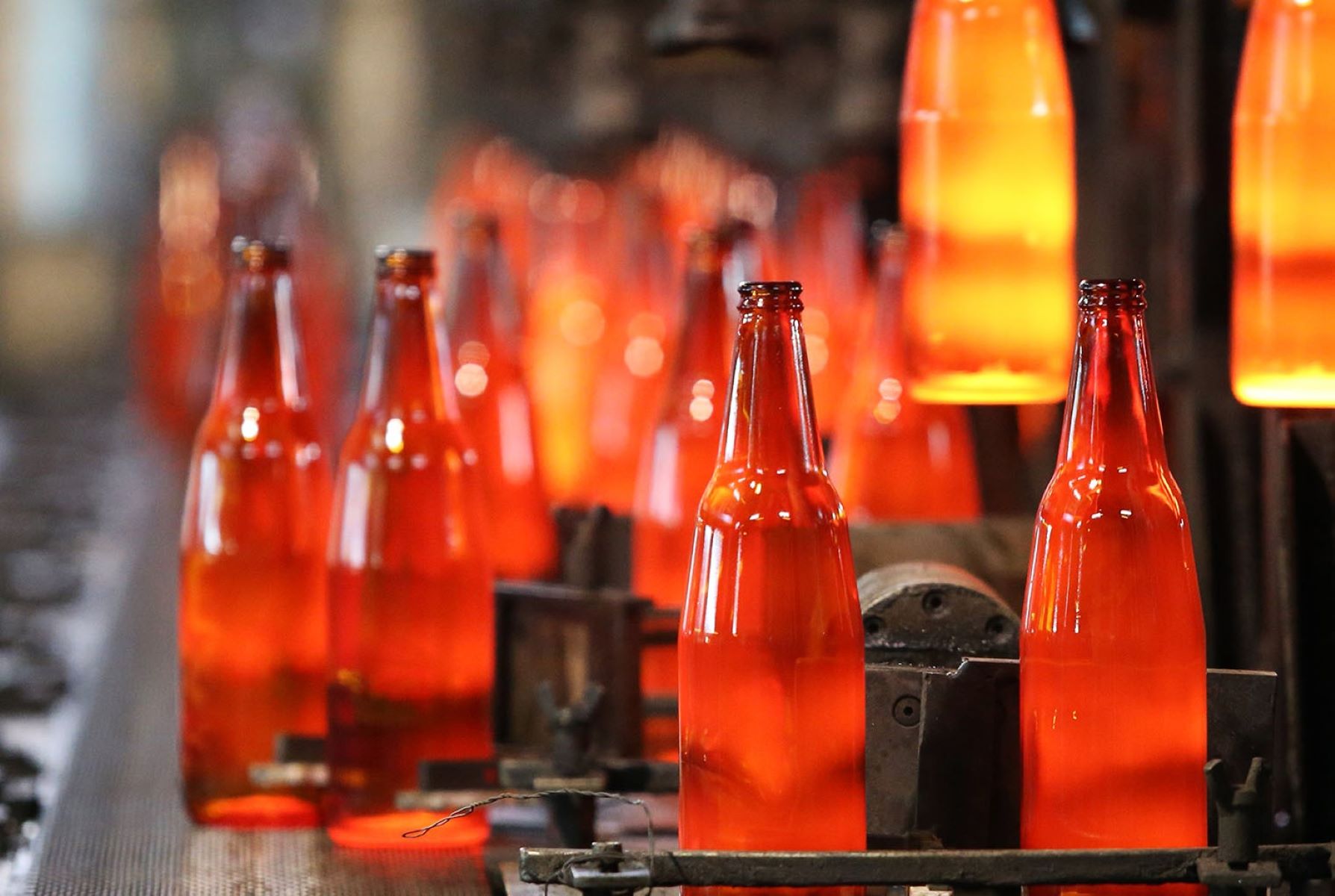
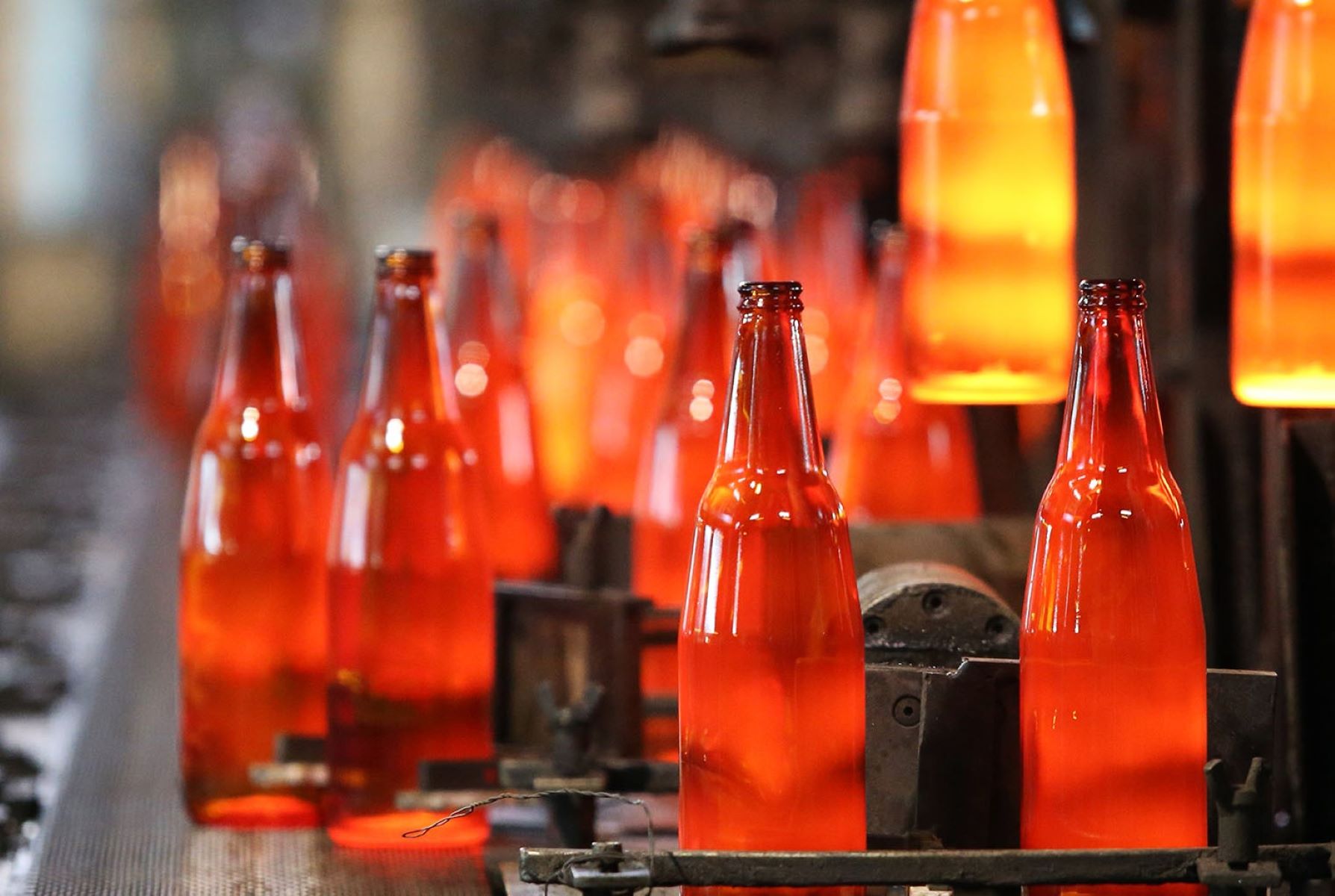
Interior Design Trends
How Are Glass Bottles Made
Published: February 3, 2024
Discover the latest interior design trends with our guide on how glass bottles are made. Explore the process and find inspiration for your next project.
(Many of the links in this article redirect to a specific reviewed product. Your purchase of these products through affiliate links helps to generate commission for Storables.com, at no extra cost. Learn more)
Introduction
Glass bottles are a ubiquitous part of our daily lives, serving as vessels for a wide array of products, from beverages to pharmaceuticals. The process of creating these essential containers is a fascinating blend of art and science, involving intricate steps that transform raw materials into the familiar, transparent vessels we encounter every day.
The production of glass bottles is a testament to human ingenuity and craftsmanship, dating back thousands of years to ancient civilizations that first discovered the transformative properties of molten sand. Over time, this knowledge has evolved into a sophisticated manufacturing process that combines tradition with cutting-edge technology.
From the initial gathering of raw materials to the meticulous quality control measures, the journey of a glass bottle encompasses multiple stages, each contributing to the final product's durability, clarity, and functionality. Understanding the intricacies of this process offers a newfound appreciation for the seemingly simple yet indispensable items that grace our shelves and tables.
As we delve into the world of glass bottle production, we will uncover the raw materials that form the foundation of this craft, the mesmerizing transformation of molten glass, the crucial role of annealing in ensuring structural integrity, the artistry of surface treatment, and the rigorous quality control measures that uphold industry standards. Join us on this captivating exploration of the art and science behind the creation of glass bottles.
Key Takeaways:
- Glass bottles are made from silica sand, soda ash, limestone, and cullet, showcasing the harmonious blend of natural elements and human ingenuity. The process involves melting, shaping, annealing, surface treatment, and rigorous quality control measures.
- The art and science of glass bottle production embody a seamless fusion of tradition and innovation, culminating in the creation of enduring symbols of functionality, elegance, and quality. Each bottle undergoes meticulous craftsmanship and precision to ensure excellence.
Read more: What Are Glass Bottles Made Of
Raw Materials
The production of glass bottles commences with the careful selection and preparation of raw materials, primarily consisting of silica sand, soda ash, limestone, and cullet. These elements form the essential components that undergo a remarkable transformation into the transparent, versatile material we recognize as glass.
Silica sand, a key ingredient, serves as the primary source of silicon dioxide, imparting the glass with its fundamental strength and heat resistance. Soda ash, also known as sodium carbonate, acts as a flux, lowering the melting point of the silica to facilitate the fusion process. Limestone, rich in calcium carbonate, aids in stabilizing the chemical composition of the glass, contributing to its durability and clarity.
In addition to these primary components, cullet, which refers to recycled glass, plays a pivotal role in sustainable glass production. By incorporating cullet into the mix, manufacturers reduce energy consumption and raw material usage while minimizing waste. This eco-friendly approach aligns with the growing emphasis on environmental responsibility within the manufacturing industry.
The meticulous blending of these raw materials is a critical step in achieving the desired glass composition, as variations in the proportions can significantly impact the physical and chemical properties of the final product. Once the raw materials are carefully measured and mixed, they undergo a rigorous process of melting and forming, where the alchemy of heat and precision craftsmanship transforms them into the iconic vessels that grace our daily lives.
The careful selection and harmonious fusion of these raw materials lay the foundation for the remarkable journey of glass bottle production, showcasing the seamless integration of natural elements and human ingenuity. This harmonious blend of tradition and innovation underscores the enduring allure of glass as a material that has stood the test of time, evolving from ancient craftsmanship to modern manufacturing excellence.
Melting and Forming
The mesmerizing transformation of raw materials into molten glass marks the commencement of the captivating process of melting and forming. This pivotal stage harnesses the power of intense heat and precision shaping to mold the viscous liquid into the desired bottle shape, embodying the seamless fusion of artistry and engineering.
The raw materials, meticulously blended to achieve the desired glass composition, undergo a remarkable metamorphosis within the fiery embrace of the furnace. The mixture, typically heated to temperatures exceeding 1700 degrees Celsius, transitions into a molten state, where it exhibits a mesmerizing fluidity that enables skilled artisans to shape it into various forms.
The shaping process, often facilitated by skilled glassblowers or advanced machinery, involves the careful manipulation of the molten glass to achieve the specific dimensions and contours required for the intended bottle design. This intricate dance of heat and craftsmanship demands precision and expertise, as the molten glass responds to the slightest touch, yielding to the vision of the artisans guiding its transformation.
As the molten glass takes on its defined shape, whether through blowing, pressing, or molding techniques, it captures the essence of creativity and technical finesse, embodying the convergence of human artistry and scientific principles. The fluid nature of the molten glass allows for the creation of a diverse range of bottle designs, from sleek and symmetrical to intricately textured, reflecting the boundless possibilities inherent in this versatile material.
The art of glassblowing, an ancient craft that has transcended centuries, continues to inspire modern techniques, seamlessly integrating tradition with technological advancements. Advanced manufacturing processes, including automated forming machines and precision molds, further enhance the efficiency and precision of shaping molten glass, underscoring the evolution of glass bottle production in response to technological innovation.
The stage of melting and forming stands as a testament to the harmonious interplay of human creativity and scientific precision, encapsulating the essence of glass as a medium that transcends functionality to embody artistry. This transformative process sets the stage for the subsequent steps in glass bottle production, laying the foundation for the meticulous annealing, surface treatment, and quality control measures that culminate in the creation of the iconic vessels that grace our daily lives.
Annealing
Following the mesmerizing transformation of molten glass into the desired bottle shape, the crucial process of annealing takes center stage, playing a pivotal role in ensuring the structural integrity and durability of the glass bottles. Annealing, a meticulously controlled cooling process, serves as a vital step in tempering the glass, relieving internal stresses, and fortifying it against potential brittleness or breakage.
As the newly formed glass bottles emerge from the intense heat of the shaping process, they carry residual internal stresses that, if left unaddressed, could compromise their strength and resilience. The annealing process, therefore, becomes a critical safeguard, allowing the glass to gradually cool at a carefully regulated pace, mitigating the risk of structural flaws that could compromise its functionality.
The annealing process typically involves carefully transferring the newly formed glass bottles to a temperature-controlled annealing lehr, a specialized furnace designed to facilitate the gradual cooling of the glass. Within this controlled environment, the bottles undergo a meticulously orchestrated cooling regimen, where they are subjected to descending temperatures over a predetermined duration, allowing the internal stresses to dissipate without inducing surface imperfections.
The gradual cooling within the annealing lehr serves as a transformative journey for the glass bottles, allowing them to undergo a gradual transition from their molten state to a state of enhanced strength and resilience. This controlled cooling process imparts a balanced internal structure to the glass, minimizing the risk of spontaneous breakage and ensuring that the bottles possess the requisite durability to withstand the rigors of handling and storage.
The art of annealing embodies the delicate balance between heat and time, harnessing the principles of material science to fortify the glass bottles against potential vulnerabilities. This meticulous process underscores the commitment to quality and precision within glass bottle production, ensuring that each vessel emerges with the resilience and structural integrity necessary to fulfill its intended purpose.
In essence, the annealing process stands as a testament to the meticulous craftsmanship and scientific rigor that underpin the creation of glass bottles, elevating them from mere vessels to enduring symbols of functionality and elegance. This transformative stage sets the foundation for the subsequent surface treatment and quality control measures, culminating in the creation of glass bottles that embody the perfect fusion of artistry and engineering.
When making glass bottles, it’s important to use high-quality raw materials like sand, soda ash, and limestone. These materials are melted together at high temperatures and then molded into the desired bottle shape.
Surface Treatment
The stage of surface treatment marks a pivotal juncture in the journey of glass bottle production, where the inherent clarity and smoothness of the glass undergo a transformative enhancement, elevating the bottles from functional vessels to captivating works of art. This intricate process encompasses a range of techniques aimed at refining the visual appeal, texture, and functionality of the glass bottles, culminating in a seamless fusion of aesthetics and practicality.
One of the primary methods employed in surface treatment is the application of coatings or finishes designed to impart specific characteristics to the glass bottles. These coatings may serve diverse purposes, ranging from enhancing the bottles' resistance to scratches and abrasions to bestowing them with a lustrous sheen that captivates the eye. Advanced coating technologies have enabled the creation of specialized finishes, such as matte, glossy, or iridescent effects, allowing for a diverse array of visual and tactile experiences.
In addition to coatings, surface treatment may involve processes such as etching, engraving, or embossing, which introduce intricate patterns, logos, or text onto the glass bottles. These embellishments not only add a touch of individuality and branding but also contribute to the tactile and visual allure of the bottles, transforming them into captivating artifacts that engage the senses.
Furthermore, the process of surface treatment extends to the realm of functionality, encompassing techniques to enhance the bottles' grip, stability, and pourability. Textured or contoured surfaces may be meticulously crafted to facilitate a secure hold, while precision-engineered openings and spouts ensure effortless dispensing of the bottle's contents, enhancing the overall user experience.
The artistry of surface treatment represents a harmonious marriage of creativity and functionality, where the glass bottles transcend their utilitarian essence to embody elements of design and craftsmanship. This transformative stage serves as a testament to the enduring allure of glass as a medium that seamlessly integrates form and function, captivating the eye while fulfilling practical needs.
As the glass bottles emerge from the realm of surface treatment, they bear the imprint of meticulous artistry and thoughtful design, embodying a synthesis of visual appeal, tactile elegance, and functional excellence. This transformative process sets the stage for the final phase of quality control, where the bottles undergo rigorous assessments to ensure that they meet the exacting standards of durability, clarity, and aesthetic refinement.
Read more: How To Dispose Of Glass Bottles
Quality Control
The culmination of the glass bottle production journey converges upon the pivotal stage of quality control, where meticulous assessments and stringent measures are employed to uphold the exacting standards of durability, clarity, and aesthetic refinement. This critical phase serves as the ultimate safeguard, ensuring that each glass bottle that emerges from the manufacturing process embodies the pinnacle of craftsmanship and precision.
Quality control encompasses a multifaceted approach, encompassing both automated inspections and meticulous human assessments to scrutinize every aspect of the glass bottles. Advanced technologies, including automated vision systems, are deployed to conduct comprehensive examinations, scrutinizing the bottles for imperfections, irregularities, and dimensional accuracy. These automated inspections leverage cutting-edge algorithms and high-resolution imaging to detect even the most minute flaws, ensuring that each bottle meets the stringent criteria for visual clarity and structural integrity.
In parallel, skilled inspectors, equipped with a discerning eye for detail, conduct manual examinations to complement the automated assessments. Their expertise allows them to identify nuanced imperfections that may elude automated detection, ensuring that each bottle undergoes a comprehensive evaluation that encompasses both technological precision and human discernment.
The quality control process extends beyond visual assessments, encompassing rigorous tests to evaluate the bottles' resistance to impact, temperature differentials, and environmental stressors. These tests simulate real-world scenarios, subjecting the bottles to varying conditions to ascertain their resilience and reliability. By undergoing these exhaustive trials, the glass bottles demonstrate their ability to withstand the rigors of transportation, storage, and usage, affirming their suitability for diverse applications.
Furthermore, the assessment of dimensional accuracy and consistency plays a pivotal role in quality control, ensuring that each bottle adheres to precise specifications. From the uniformity of wall thickness to the exactness of the bottle's dimensions, these assessments guarantee that every bottle meets the prescribed standards, reflecting the unwavering commitment to precision and excellence.
In essence, the stage of quality control encapsulates the unwavering dedication to perfection that defines the art and science of glass bottle production. Through a harmonious blend of advanced technologies, skilled craftsmanship, and uncompromising standards, this transformative phase ensures that each glass bottle emerges as a flawless embodiment of functionality, elegance, and enduring quality.
Conclusion
The journey of glass bottle production is a captivating odyssey that intertwines tradition, innovation, and meticulous craftsmanship. From the careful selection and blending of raw materials to the mesmerizing transformation of molten glass, the art and science of creating glass bottles embody a harmonious fusion of artistry and engineering. The pivotal stages of annealing, surface treatment, and quality control serve as testaments to the unwavering commitment to excellence that defines this intricate process.
As the molten glass takes on its defined shape, whether through blowing, pressing, or molding techniques, it captures the essence of creativity and technical finesse, embodying the convergence of human artistry and scientific principles. The fluid nature of the molten glass allows for the creation of a diverse range of bottle designs, from sleek and symmetrical to intricately textured, reflecting the boundless possibilities inherent in this versatile material.
The art of annealing embodies the delicate balance between heat and time, harnessing the principles of material science to fortify the glass bottles against potential vulnerabilities. This meticulous process underscores the commitment to quality and precision within glass bottle production, ensuring that each vessel emerges with the resilience and structural integrity necessary to fulfill its intended purpose.
The transformative stage of surface treatment elevates the glass bottles from functional vessels to captivating works of art, where the inherent clarity and smoothness of the glass undergo a transformative enhancement. This intricate process encompasses a range of techniques aimed at refining the visual appeal, texture, and functionality of the glass bottles, culminating in a seamless fusion of aesthetics and practicality.
The culmination of the glass bottle production journey converges upon the pivotal stage of quality control, where meticulous assessments and stringent measures are employed to uphold the exacting standards of durability, clarity, and aesthetic refinement. This critical phase serves as the ultimate safeguard, ensuring that each glass bottle that emerges from the manufacturing process embodies the pinnacle of craftsmanship and precision.
In essence, the art and science of glass bottle production represent a timeless testament to human ingenuity and creativity, showcasing the seamless integration of natural elements and technological innovation. The resulting glass bottles stand as enduring symbols of functionality, elegance, and enduring quality, embodying the perfect fusion of artistry and engineering.
Frequently Asked Questions about How Are Glass Bottles Made
Was this page helpful?
At Storables.com, we guarantee accurate and reliable information. Our content, validated by Expert Board Contributors, is crafted following stringent Editorial Policies. We're committed to providing you with well-researched, expert-backed insights for all your informational needs.
0 thoughts on “How Are Glass Bottles Made”