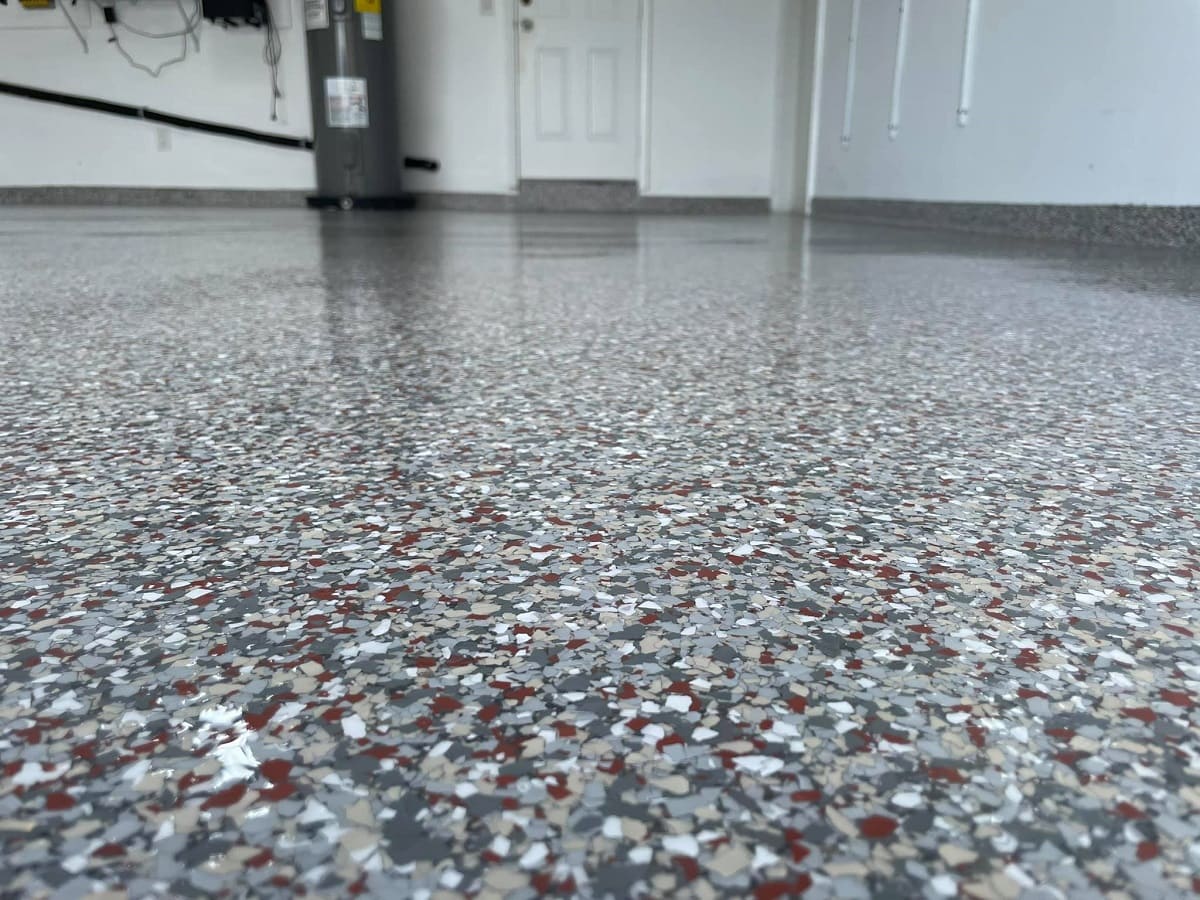
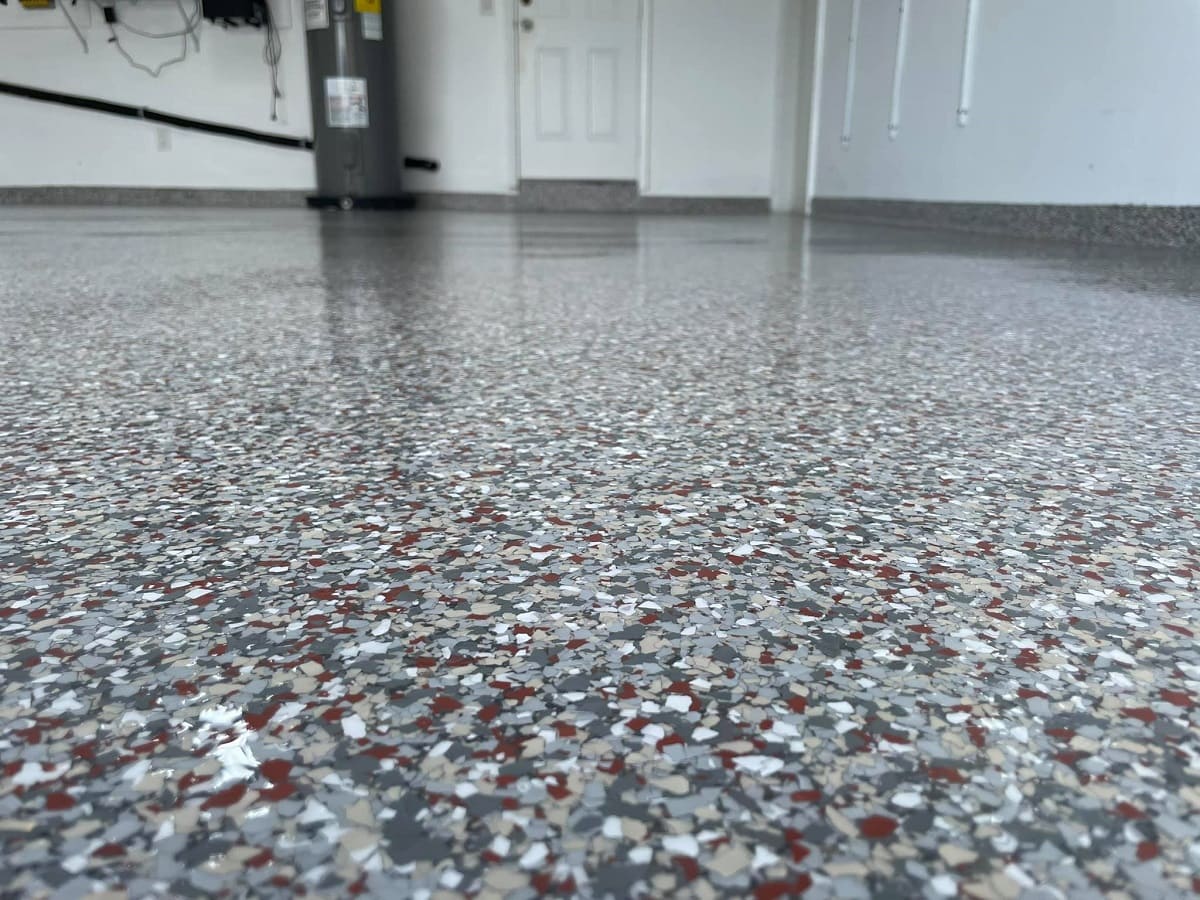
Articles
How Much Does An Epoxy Floor Cost
Modified: February 23, 2024
Discover the average cost of epoxy flooring in this comprehensive article. Explore different factors that influence pricing and get accurate estimates for your project.
(Many of the links in this article redirect to a specific reviewed product. Your purchase of these products through affiliate links helps to generate commission for Storables.com, at no extra cost. Learn more)
Introduction
Welcome to our comprehensive guide on epoxy flooring costs. If you’re considering installing an epoxy floor, it’s important to have a clear understanding of the factors that can influence its price. Epoxy flooring is a popular choice for its durability, resistance to stains and chemicals, and aesthetic appeal. Whether you’re planning to install an epoxy floor in your home, office, or commercial space, this article will provide you with valuable insights into the costs involved.
Epoxy flooring consists of a mixture of epoxy resin and a hardener that chemically reacts to form a hard, durable surface. It can be applied over various substrates, including concrete, wood, and tiles, and is commonly seen in garages, basements, showrooms, and industrial facilities.
When it comes to determining the cost of an epoxy floor, several factors come into play. In the following sections, we will delve into these factors to help you gain a better understanding of the overall cost and make an informed decision.
Key Takeaways:
- Invest in high-quality materials and experienced professionals for a durable and long-lasting epoxy floor. Cutting costs may result in subpar results and additional expenses in the long run.
- Consider various factors such as type of epoxy, materials, labor, area size, customization, and maintenance for an accurate budget and a stunning, durable epoxy floor.
Read more: How Much Does An Epoxy Garage Floor Cost
Factors Affecting Epoxy Floor Cost
Several factors can impact the cost of an epoxy floor installation. It’s essential to consider these factors when estimating the overall expenses. Here are the key factors to keep in mind:
- Type of Epoxy: The type of epoxy used plays a significant role in the overall cost. There are different epoxy formulations available, ranging from standard epoxy to high-performance epoxy. High-performance epoxy tends to be more expensive due to its enhanced durability and resistance.
- Quality of Materials: The quality of the epoxy materials used can affect the cost. Higher-quality materials typically come at a higher price, but they offer better performance and longevity. It’s important to choose materials that are suitable for the intended application to ensure satisfactory results.
- Complexity of Installation: The complexity of the installation process can impact the cost. Factors such as the condition of the existing floor, the need for floor preparation, and the presence of obstacles or intricate patterns can increase the labor and time required for the installation, therefore affecting the overall cost.
- Area Size: The size of the area to be covered with epoxy flooring is a significant factor in determining the cost. Larger areas will require more materials and longer installation times, resulting in higher costs. Additionally, larger spaces may require additional labor or specialized equipment.
- Additional Features: If you want to add specific features or customization to your epoxy floor, such as decorative flakes, metallic pigments, or logos, this can increase the cost. These additional features require extra materials, labor, and expertise, which contribute to the overall expenses.
- Maintenance and Warranty: While not directly related to the initial installation cost, it’s important to consider the long-term maintenance and warranty when calculating the overall cost. Some epoxy systems require periodic maintenance, and warranties may vary depending on the manufacturer and installer.
Keep in mind that the cost of an epoxy flooring project can vary significantly based on these factors. It’s always recommended to get multiple quotes from reputable epoxy flooring contractors to compare prices and ensure you’re getting the best value for your investment.
Cost of Materials
The cost of materials is a significant component when calculating the overall expense of an epoxy floor installation. Understanding the materials involved and their associated costs will help you estimate the budget for your project. Here’s what you need to know about the cost of materials:
Epoxy Resin and Hardener: The main components of an epoxy floor system are the epoxy resin and hardener. The cost of these materials can vary depending on the quality and brand. On average, expect to pay between $80 and $150 per gallon of epoxy resin and hardener. The amount required will depend on the size and complexity of the area to be covered.
Primer: A primer is often used to enhance adhesion and promote a better bond between the substrate and the epoxy. Primers typically cost between $30 and $50 per gallon, and the quantity needed will depend on the condition of the substrate.
Topcoat: A topcoat is applied as a protective layer over the cured epoxy. It provides added durability, resistance to UV rays, and enhances the overall appearance. The cost of a topcoat can range from $60 to $100 per gallon, and the quantity required will depend on the desired thickness and coverage.
Fillers and Additives: Fillers and additives, such as decorative flakes, metallic powders, or anti-slip agents, can add aesthetic appeal and functionality to the epoxy floor. The cost of these materials will depend on the specific type and brand, but typically range from $20 to $50 per pound or container.
Masking and Protection: When installing an epoxy floor, it’s important to protect surrounding surfaces and areas from potential splatters and spills. Costs for masking materials like tapes, plastic sheeting, and drop cloths will vary depending on the quantity and quality required.
Total Material Costs: Estimating the total material costs for an epoxy floor can be challenging as it depends on the size, complexity, and specific requirements of the project. On average, material costs for a standard epoxy flooring installation can range between $3 to $8 per square foot. However, this is a rough estimate, and it’s recommended to consult with epoxy flooring suppliers or contractors to get more accurate pricing based on your specific needs.
Remember, investing in high-quality materials is crucial for a durable and long-lasting epoxy floor. While it may seem tempting to cut costs on materials, opting for cheaper alternatives may result in a subpar finish and shorter lifespan.
Cost of Labor
In addition to the cost of materials, the labor involved in the installation of an epoxy floor is another significant factor to consider. Hiring professional epoxy flooring installers ensures a proper and efficient installation, but it comes with a cost. Here’s what you need to know about the cost of labor:
Experience and Expertise: The labor cost will depend on the level of experience and expertise of the installers. Experienced professionals may charge a higher rate due to their knowledge, skillset, and reputation in the industry. However, their expertise is crucial for achieving a high-quality finish and ensuring the longevity of the epoxy floor.
Hourly or Square Foot Basis: Epoxy flooring contractors may charge either an hourly rate or a square foot basis. Hourly rates typically range from $50 to $100 per hour, with the total hours required for the project depending on various factors such as the size, complexity, and condition of the substrate. On the other hand, square footage rates may range from $3 to $8 per square foot, and the total cost will depend on the size of the area.
Preparation and Installation: The labor cost includes the time and effort required for preparing the substrate, applying the epoxy floor, and completing any necessary steps such as grinding, patching, or priming. The complexity of the installation, including any decorative or customized elements, can influence the labor cost as well.
Travel and Accommodation Expenses: If your project is located far from the contractor’s base, additional charges for travel and accommodation may be applicable. This cost consideration is essential, especially when hiring out-of-town installers.
Quotes and Estimates: To get an accurate idea of the labor cost for your epoxy floor installation, it’s recommended to obtain quotes or estimates from several reputable epoxy flooring contractors. This will help you compare prices, evaluate the level of service offered, and find the best fit for your project and budget.
DIY Considerations: While it’s possible to install an epoxy floor as a do-it-yourself project, it’s important to weigh the benefits against the challenges. DIY installations may save on labor costs, but the learning curve, potential mistakes, and lack of professional equipment can impact the quality and durability of the finished floor. It’s crucial to assess your skills, available time, and resources before deciding on a DIY installation.
Remember to factor in both material and labor costs when budgeting for your epoxy floor installation. While it may be tempting to opt for the lowest labor rates available, prioritize experience, expertise, and reputation to ensure a successful and long-lasting epoxy floor.
Size of the Area
The size of the area to be covered with epoxy flooring is an influential factor in determining the overall cost of the project. The larger the area, the more materials and labor will be required, resulting in higher expenses. Here’s what you need to know about how the size of the area affects the cost:
Total Square Footage: The total square footage of the area is a key consideration when calculating the cost. Epoxy flooring is typically priced per square foot, so the larger the area, the more epoxy materials will be needed. Measure the length and width of the space to get an accurate estimate of the square footage.
Economies of Scale: In some cases, larger areas may benefit from economies of scale. This means that the cost per square foot may decrease as the size of the area increases. Contractors may offer discounts for larger projects to incentivize clients to choose them for the job. It’s always a good idea to discuss any potential discounts or special offers with the epoxy flooring contractors.
Complexity and Layout: The complexity and layout of the area can also impact the cost. If the surface has intricate patterns, multiple rooms, or unusual shapes, additional materials and labor may be required to achieve a seamless and visually appealing epoxy floor. This can increase the overall cost compared to a simple, straightforward layout.
Accessibility: Consider the accessibility of the area when estimating costs. If the installation space is located on a higher floor, in a tight or confined area, or requires special equipment for access, additional costs may be incurred. These additional charges will be related to the time and effort required to transport materials and equipment to the site.
Surface Preparation: The condition of the existing floor and the amount of preparation needed can also affect the cost. If the surface requires extensive cleaning, patching, or repairs, it will increase the labor and time required for the project. Additionally, larger areas may need more extensive floor preparation, which can add to the overall cost.
Additional Considerations: It’s important to consider the functions and layout of the area when determining the size. High-traffic areas, such as commercial spaces or garages, may require more durable and thicker epoxy coatings, which can affect the overall cost.
When planning your epoxy flooring project, accurately measuring the size of the area is crucial for obtaining accurate quotes from contractors and estimating the cost of materials. Be sure to communicate all relevant details about the size and layout of the space to potential contractors to receive the most accurate pricing information.
When budgeting for an epoxy floor, consider the size of the area, the condition of the existing floor, and any additional customization or features. Get multiple quotes from reputable contractors to ensure you get a fair price.
Floor Preparation
Floor preparation is a critical step in the installation of an epoxy floor and can significantly impact the overall cost of the project. Properly preparing the surface ensures that the epoxy adheres correctly and provides a durable and long-lasting finish. Here’s what you need to know about floor preparation and its effect on cost:
Surface Cleaning: Before applying epoxy, the surface needs to be thoroughly cleaned to remove any dust, dirt, oil, or contaminants. Depending on the condition of the floor, this may involve sweeping, vacuuming, scrubbing, or pressure washing. The more extensive the cleaning required, the more time and labor will be involved, which can increase the cost.
Concrete Repair: If the concrete substrate has cracks, pits, or uneven areas, it may need to be repaired or patched before applying the epoxy. Concrete repairs can include filling cracks, grinding down high spots, or leveling the surface. The extent of the repairs needed will depend on the condition of the floor and can impact the labor and cost involved in the preparation phase.
Shot Blasting or Grinding: To ensure proper adhesion of the epoxy, the surface may need to be mechanically prepared through shot blasting or grinding. Shot blasting involves forcefully propelling small abrasive particles at the surface to remove any contaminants and provide texture for better epoxy bonding. Grinding is the process of using machinery with rotating discs to smooth and prepare the surface. The choice between shot blasting and grinding will depend on the condition of the floor and the recommendations of the epoxy flooring contractor. These mechanical preparation methods can add to the labor and cost of the project.
Priming: Priming the surface is often necessary to enhance the adhesion of the epoxy and provide a proper bond. Priming involves applying a layer of epoxy primer to the prepared floor. The cost of priming will depend on the type and quality of the primer used and the size of the area. Priming is an essential step in floor preparation and ensures a successful epoxy floor installation.
Moisture Testing: Moisture can affect the performance of epoxy flooring. Before installation, moisture testing may be required to determine if there are any moisture issues in the substrate. Moisture testing involves taking moisture readings and determining if any additional moisture barriers or mitigation measures are needed. Moisture testing, if required, can add to the overall cost of the project.
Project Specifics: The level of floor preparation required will depend on the specific project and the condition of the existing floor. Factors such as previous coatings, surface damage, or unique circumstances may necessitate additional steps or treatments during the preparation phase, which can impact the cost.
It’s important to discuss floor preparation with epoxy flooring contractors during the estimation process. They will assess the condition of your floor and provide an accurate understanding of the necessary preparation steps and associated costs. Proper floor preparation is crucial for achieving a successful epoxy floor installation and ensuring its long-term durability.
Additional Features and Customization
When installing an epoxy floor, you have the option to incorporate additional features and customization to enhance the aesthetics and functionality of the space. These features can add a unique touch to your epoxy floor but may also impact the overall cost of the project. Here’s what you need to know about additional features and customization:
Decorative Flakes: Decorative flakes are often added to epoxy floors to create a textured and colorful appearance. These flakes come in various colors and sizes, allowing you to customize the design to your preference. The cost of decorative flakes will depend on the type, quantity, and quality. Higher-quality flakes may be more expensive, but they offer better durability and visual appeal.
Metallic Pigments: Metallic pigments are another popular option for customizing epoxy floors, creating a dazzling metallic finish. These pigments can be mixed into the epoxy, creating a unique visual effect with depth and movement. The cost of metallic pigments varies based on factors such as the brand, color, and quantity needed to achieve the desired effect.
Logos and Patterns: For commercial or branding purposes, you may want to incorporate logos or specific patterns into your epoxy floor. Creating custom logos or intricate patterns requires additional time, labor, and expertise, which can impact the overall cost. The complexity of the design and the number of colors involved will also influence the final price.
Epoxy Coating Thickness: Increasing the thickness of the epoxy coating can provide added durability and protection for high-traffic areas or industrial applications. However, thicker coatings may require extra materials and time during the installation process, which can contribute to higher costs. Discussing your specific requirements with the epoxy flooring contractor will help determine the best coating thickness for your needs.
Anti-Slip Additives: If you want to increase safety and reduce the risk of slips and falls, anti-slip additives can be incorporated into the epoxy. These additives create a textured surface that provides better traction. The cost of anti-slip additives will depend on the type and quantity used.
Custom Color Matching: If you have a specific color scheme in mind for your epoxy floor, custom color matching may be available. This service allows you to achieve the exact color you desire, but it may add to the cost of the project. Custom color matching is especially useful for achieving brand consistency in commercial spaces or creating a unique design element.
Special Effects and Lighting: For a more dramatic and visually striking epoxy floor, special effects and lighting options can be incorporated. This can include features like embedded fiber-optic lighting, glow-in-the-dark pigments, or UV-reactive materials. Adding these special effects can significantly increase the overall cost due to the complexity and specialized materials involved.
When considering additional features and customization for your epoxy floor, it’s essential to communicate your preferences and budgetary constraints to the epoxy flooring contractor. They can provide recommendations and pricing options to help you achieve your desired outcome while staying within your budget.
Maintenance and Repairs
Maintenance and occasional repairs are vital for preserving the longevity and appearance of your epoxy floor. While these aspects may not directly impact the initial installation cost, it’s important to consider them when estimating the overall expenses and ensuring the continued performance of your epoxy floor. Here’s what you need to know about maintenance and repairs:
Cleaning and Routine Maintenance: Regular cleaning is essential for keeping your epoxy floor looking its best. It’s recommended to sweep or vacuum the surface regularly to remove loose dirt and debris. Mopping with a mild detergent or epoxy floor cleaner is typically sufficient for routine maintenance. Avoid using abrasive materials or harsh chemicals that may damage the epoxy finish.
Stain and Chemical Resistance: Epoxy flooring is known for its resistance to stains and chemicals, but it’s still important to address spills and accidents promptly. Any spills should be wiped up immediately to prevent staining. Using a pH-neutral cleaner can help remove tough stains without harming the epoxy surface. Follow the manufacturer’s guidelines for cleaning and maintenance to ensure the longevity of your floor.
Regular Inspections: Regular inspections of your epoxy floor can help identify any areas that may require repairs. Look out for any cracks, chips, or areas where the epoxy has worn away. Promptly addressing these issues can prevent further damage and more costly repairs down the line.
Repairs and Touch-Ups: Over time, your epoxy floor may require repairs or touch-ups to maintain its appearance and functionality. Small repairs, such as filling in minor cracks or chips, can often be done by the homeowner or a professional epoxy floor installer. However, larger or more extensive repairs may require the expertise of a professional. The cost of repairs will depend on the extent and complexity of the damage.
Periodic Maintenance: Depending on the type of epoxy flooring system installed, periodic maintenance may be required to ensure its long-term performance. This may include reapplying a topcoat or maintenance coat to restore the shine and protective properties of the epoxy, or addressing any areas of the floor that have experienced excessive wear or damage. The frequency and cost of periodic maintenance will vary based on factors such as the type of epoxy and the level of foot traffic or use.
Warranty and Guarantees: When choosing an epoxy flooring system, inquire about the warranty and guarantees offered by the manufacturer and installer. A warranty can provide peace of mind by covering certain issues or defects within a specified period. It’s important to review the terms and conditions of the warranty to understand any maintenance or upkeep requirements that may be necessary to maintain its validity.
Regular maintenance and addressing repairs promptly are key to prolonging the life and appearance of your epoxy floor. Allocating a budget for routine cleaning, occasional repairs, and periodic maintenance will help ensure your epoxy floor continues to shine and withstand the test of time.
Conclusion
Installing an epoxy floor can be a fantastic investment in your space, offering durability, aesthetic appeal, and ease of maintenance. However, it’s essential to consider various factors that can influence the overall cost of the project. By understanding these factors, you can make informed decisions and effectively budget for your epoxy floor installation.
We discussed several key factors that can affect the cost of an epoxy floor. These include the type and quality of materials, the complexity of the installation, the size of the area to be covered, the extent of floor preparation required, additional features and customization options, and the need for maintenance and repairs. Each of these factors contributes to the overall expense, and it’s crucial to evaluate them for a comprehensive estimation.
When planning an epoxy flooring project, it’s recommended to consult with reputable epoxy flooring contractors. They can provide detailed quotes, explain the different options available, and guide you through the decision-making process. Comparing multiple quotes will help ensure you’re getting a fair price and the best value for your investment.
Remember to prioritize quality when it comes to materials and labor. While it may be tempting to cut costs, opting for lower-quality materials or inexperienced labor can result in subpar results and additional expenses in the long run. Investing in high-quality materials and experienced professionals will help ensure a beautiful, durable, and long-lasting epoxy floor.
Lastly, don’t forget about ongoing maintenance. Regular cleaning, inspections, and occasional repairs are essential for maintaining the appearance and functionality of your epoxy floor. Allocating a budget for routine maintenance and addressing any issues promptly will help extend the life of your epoxy floor and protect your investment.
In conclusion, estimating the costs of an epoxy floor involves considering multiple factors. By taking into account the type of epoxy, materials, labor, size of the area, floor preparation, customization options, and maintenance needs, you can develop an accurate budget and enjoy the benefits of a stunning and durable epoxy floor for years to come.
Frequently Asked Questions about How Much Does An Epoxy Floor Cost
Was this page helpful?
At Storables.com, we guarantee accurate and reliable information. Our content, validated by Expert Board Contributors, is crafted following stringent Editorial Policies. We're committed to providing you with well-researched, expert-backed insights for all your informational needs.
0 thoughts on “How Much Does An Epoxy Floor Cost”