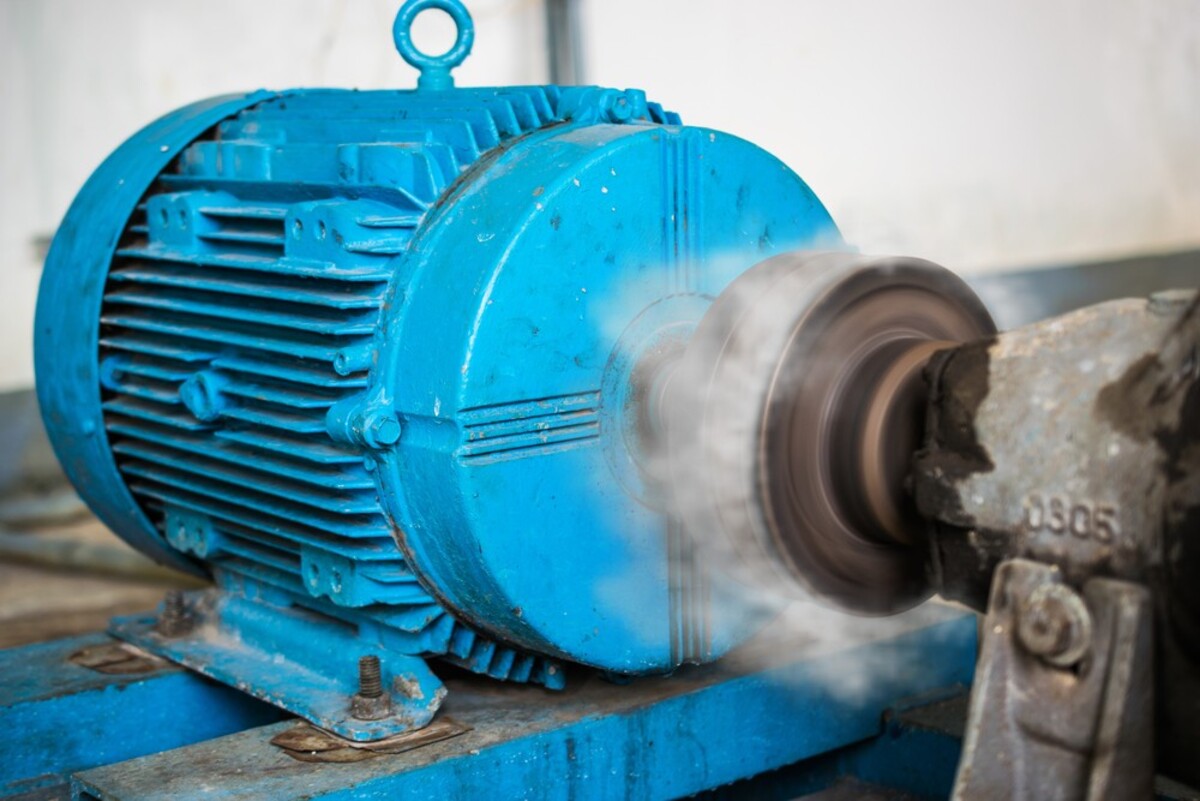
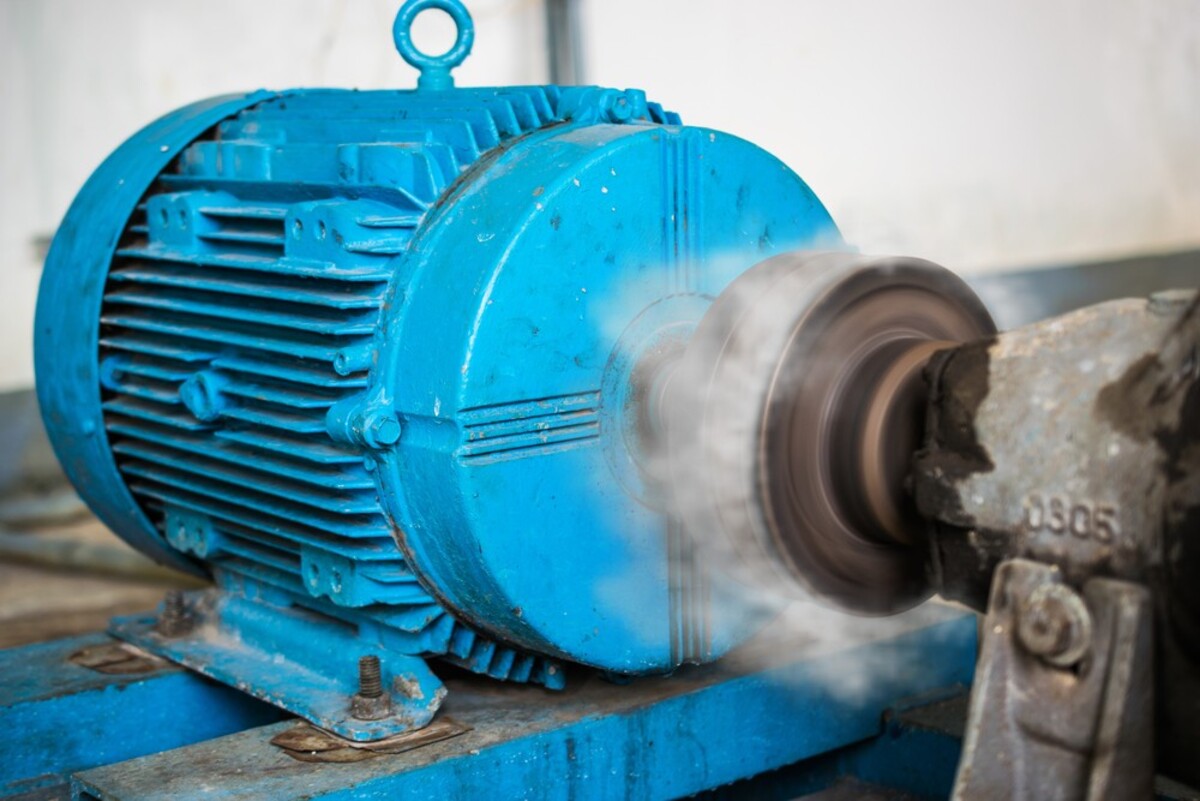
Articles
What Causes An Electric Motor To Overheat
Modified: December 7, 2023
Discover the common causes of electric motors overheating and learn how to prevent this issue. Read our insightful articles to keep your motors running smoothly.
(Many of the links in this article redirect to a specific reviewed product. Your purchase of these products through affiliate links helps to generate commission for Storables.com, at no extra cost. Learn more)
Introduction
Electric motors are essential components in various appliances and machinery, powering countless devices that we rely on in our daily lives. From refrigerators and air conditioners to industrial machinery and vehicles, electric motors play a crucial role in converting electrical energy into mechanical energy. However, like any mechanical device, electric motors are prone to overheating, which can result in performance issues, decreased lifespan, and even safety hazards.
Understanding the causes of electric motor overheating is essential for both homeowners and industrial operators. By identifying the root causes and implementing preventive measures, it is possible to mitigate the risks of motor failure and extend the lifespan of the motor.
In this article, we will explore the common causes of electric motor overheating and discuss preventive measures to avoid such problems. Whether you are a homeowner dealing with a malfunctioning appliance or an industrial operator responsible for the smooth operation of machinery, this article will provide valuable insights into the world of electric motor overheating.
Before we delve into the causes and prevention methods, let’s first understand how an electric motor functions. Electric motors operate on the principle of electromagnetic induction, where coils of wire within the motor generate a magnetic field when an electric current flows through them. This magnetic field interacts with permanent magnets or other coils, causing the motor’s rotor to rotate.
While electric motors are designed to withstand high temperatures, excessive heat can build up due to various factors. When an electric motor overheats, it not only affects its efficiency but also increases the risk of internal damage. Therefore, it is essential to identify and mitigate the causes of electric motor overheating promptly.
In the next sections, we will explore the common causes of electric motor overheating, including overloading, insufficient cooling, electrical imbalances, poor maintenance, and environmental factors. Additionally, we will discuss preventive measures that can help ensure the smooth and safe operation of electric motors while minimizing the risk of overheating. So let’s dive in and discover the secrets behind electric motor overheating and how to prevent it.
Key Takeaways:
- Regular inspections, proper ventilation, correct wiring, routine maintenance, and temperature monitoring are essential preventive measures to avoid electric motor overheating. Proactive maintenance ensures optimal performance and longevity of electric motors.
- Implementing effective preventive measures such as continuous monitoring, safe temperature limits, and regular data analysis helps in early detection of potential overheating risks, ensuring reliable and safe operation of electric motors.
Understanding Electric Motors
To effectively address the issue of electric motor overheating, it is important to have a basic understanding of how these motors work. Electric motors consist of several key components that work together to convert electrical energy into mechanical energy.
The main components of an electric motor include the stator, rotor, and the winding system. The stator refers to the stationary part of the motor, which consists of a series of coils wound around an iron core. These coils are typically made of copper wire and are responsible for producing a rotating magnetic field.
The rotor, on the other hand, is the moving part of the motor. It is usually composed of a shaft and a series of conductive bars or coils that interact with the magnetic field generated by the stator. As the magnetic field changes, it induces an electric current in the rotor, which in turn generates a counteracting magnetic field. This interaction causes the rotor to rotate, thus converting electrical energy into mechanical energy.
In order to power an electric motor, an external electrical power source is required. The power source supplies an electrical current to the motor, which is then distributed through the winding system. The winding system consists of multiple coils that are strategically positioned within the stator. These coils are connected to the power source through a system of wires and conductors, allowing for the flow of electricity.
When the electric current flows through the coils, it creates a magnetic field that interacts with the magnetic field produced by the stator. This interaction creates the rotational force required to drive the motor’s shaft and perform mechanical work.
Electric motors are designed to operate within specific temperature limits. Excessive heat can cause the motor to overheat, leading to a variety of problems such as decreased efficiency, insulation breakdown, and even motor failure.
In the next sections, we will explore the common causes of electric motor overheating and discuss preventive measures that can be taken to avoid such issues. By understanding the factors that contribute to motor overheating, individuals can make informed decisions and take appropriate actions to ensure the longevity and optimal performance of their electric motors.
Common Causes of Electric Motor Overheating
Electric motor overheating can be attributed to several factors, ranging from operational issues to external environmental conditions. Understanding these causes is crucial in order to implement effective preventive measures. Let’s explore the most common causes of electric motor overheating:
1. Overloading: One of the primary causes of electric motor overheating is overloading. When a motor is forced to operate beyond its designed capacity, it draws more current and generates excessive heat. This can occur when the motor is required to perform tasks that exceed its horsepower or torque rating. Overloading can occur due to excessive load demands, mechanical inefficiencies, or improper sizing of the motor. Overloading not only leads to motor overheating but can also result in sudden motor failure if not addressed promptly.
2. Insufficient Cooling: Electric motors require adequate cooling to dissipate heat generated during operation. Cooling is typically achieved through fan-driven ventilation or liquid cooling systems. Insufficient cooling, whether due to blocked vents, improper airflow, or malfunctioning cooling mechanisms, can prevent the motor from adequately dissipating heat. This can result in heat buildup within the motor, leading to overheating. It is crucial to ensure that cooling systems are properly maintained and functioning optimally to avoid overheating issues.
3. Electrical Imbalances: Electrical imbalances can cause an uneven distribution of current through the motor’s windings, resulting in increased resistive losses and heat generation. These imbalances can be caused by issues such as unbalanced power supply, uneven coil winding, or faulty connections. Electrical imbalances not only contribute to motor overheating but can also result in reduced motor efficiency and increased stress on the motor’s components.
4. Poor Maintenance: Neglecting regular maintenance can lead to a variety of issues, including motor overheating. Lack of lubrication, dirt and debris buildup, worn-out components, and loose connections can all contribute to increased friction and heat generation within the motor. It is essential to adhere to manufacturer’s maintenance guidelines, including routine inspections, cleaning, and lubrication, to ensure proper motor functioning and prevent overheating.
5. Environmental Factors: The operating environment can also contribute to electric motor overheating. High ambient temperatures, excessive dust or dirt, humid conditions, and corrosive atmospheres can all affect the motor’s performance and increase the risk of overheating. It is important to consider the environmental conditions in which the motor operates and take necessary precautions such as providing proper ventilation, using protective enclosures, or implementing cooling measures.
By identifying these common causes of electric motor overheating, individuals can take proactive measures to prevent issues before they occur. In the next section, we will discuss preventive measures that can help avoid electric motor overheating and ensure optimal performance and longevity.
Overloading
Overloading is one of the most common causes of electric motor overheating. When a motor is subjected to an excessive load beyond its capacity, it is forced to draw more current, resulting in increased heat generation. This can lead to various issues, including decreased motor efficiency, insulation breakdown, and ultimately, motor failure.
There are several factors that can contribute to overloading an electric motor:
a. Excessive Load Demands: When a motor is required to perform tasks that exceed its horsepower or torque rating, it can lead to overloading. This can occur in industrial settings where heavy machinery or equipment is operated at maximum capacity for extended periods. Similarly, in residential settings, appliances such as air conditioners or refrigerators can overload the motor if they are constantly running at full power.
b. Mechanical Inefficiencies: Mechanical inefficiencies in the system can also contribute to overloading. Factors such as misalignment, inadequate lubrication, or worn-out bearings can cause the motor to require more power to perform its intended function. These inefficiencies increase the load on the motor and lead to overheating.
c. Improper Motor Sizing: Incorrectly sizing the motor for the specific application can also result in overloading. If a motor is undersized for the task it needs to perform, it will be continuously operating at or near its maximum capacity, leading to overheating. Similarly, if a motor is oversized, it may not be able to operate efficiently at lower loads, resulting in inefficient power consumption and increased heat generation.
To prevent overloading and subsequent motor overheating, it is important to consider the following preventive measures:
a. Proper Load Assessment: Ensure that the motor is appropriately sized for the load it needs to handle. Consult with a professional or refer to manufacturer guidelines to determine the correct motor size for the specific application. Consider factors such as starting torque requirements, duty cycle, and expected load variations.
b. Monitoring: Implement a monitoring system to track the motor’s load and performance. This can be done through the use of sensors and data logging equipment. Regularly analyze the collected data to identify any instances of overloading. If overloading is detected, take necessary actions to reduce the load or upgrade the motor if required.
c. Load Management: Distribute the load among multiple motors or equipment if possible. This can help prevent a single motor from being overwhelmed with excessive load demands. Additionally, consider implementing load management strategies such as load sharing or load shedding to optimize the overall system performance.
d. Regular Maintenance: Proper maintenance is crucial for identifying and addressing any mechanical inefficiencies that may contribute to overloading. Regularly inspect and lubricate the motor, ensuring proper alignment and replacing worn-out components as needed.
By taking these preventive measures, individuals can significantly reduce the risk of overloading their electric motors, thus avoiding overheating and maximizing motor efficiency and lifespan.
Insufficient Cooling
Insufficient cooling is another common cause of electric motor overheating. Electric motors generate heat during operation, and without proper cooling mechanisms, this heat can accumulate and lead to overheating. Cooling is vital to ensure that the motor stays within its optimal temperature range and operates efficiently. Let’s explore the factors that contribute to insufficient cooling and the preventive measures that can be taken.
a. Blocked Vents or Airflow: Electric motors are designed with vents or openings to facilitate airflow and dissipate heat. However, over time, these vents can become blocked by dust, debris, or other obstructions. When the proper airflow is restricted, the motor’s cooling efficiency is compromised, leading to overheating. Regularly inspect and clean the vents to ensure unobstructed airflow.
b. Malfunctioning Cooling Systems: Electric motors may use various cooling mechanisms, such as fan-driven ventilation or liquid cooling systems. If these cooling systems are not functioning properly, either due to mechanical failures or electrical issues, heat dissipation will be ineffective, resulting in overheating. Regularly inspect, maintain, and repair the cooling systems to ensure their proper functioning.
c. Insufficient Ventilation: The operating environment plays a crucial role in motor cooling. If the motor is located in an area with limited ventilation, such as a confined space or an equipment enclosure, heat dissipation can be compromised. Proper ventilation is essential to allow the dissipation of heat generated by the motor. Consider providing additional ventilation or using cooling fans to improve airflow around the motor.
d. Inadequate Heat Dissipation Surfaces: Electric motors rely on their outer surfaces to dissipate heat. If these surfaces are inadequately designed or covered with insulating materials, heat dissipation will be hindered. Ensure that the motor’s surfaces are designed to maximize heat transfer and are not obstructed by insulation or other materials.
e. High Ambient Temperatures: Operating electric motors in high-temperature environments can significantly impact their cooling efficiency. If the ambient temperature exceeds the motor’s maximum operating temperature, the heat dissipation process becomes challenging. Consider implementing additional cooling measures, such as using external fans, heat sinks, or air conditioning, to maintain a suitable operating temperature for the motor.
To prevent insufficient cooling and mitigate the risk of motor overheating, consider the following preventive measures:
a. Regular Inspection and Cleaning: Regularly inspect the motor’s vents, cooling systems, and surrounding areas to ensure they are free from obstructions, dust, and debris. Clean or clear any blockages to ensure proper airflow.
b. Cooling System Maintenance: Regularly maintain and service the cooling system, including fans, heat sinks, or liquid cooling components. Replace damaged or malfunctioning parts promptly.
c. Provide Adequate Ventilation: Ensure that the motor is installed in an area with sufficient ventilation, allowing for proper airflow and heat dissipation. Consider using ventilation fans or creating additional openings if necessary.
d. Monitor Operating Temperatures: Implement temperature monitoring systems to track the motor’s operating temperature. Set up alerts or alarms to notify when temperatures exceed acceptable limits, allowing for prompt action to address potential overheating issues.
e. Consider External Cooling Methods: In high-temperature environments, consider implementing additional cooling methods such as external fans, heat sinks, or air conditioning units to maintain the motor’s temperature within a safe range.
By implementing these preventive measures, individuals can significantly reduce the risk of insufficient cooling and mitigate the chances of electric motor overheating. This, in turn, ensures optimal motor performance, prolongs motor life, and reduces the potential for costly repairs or replacements.
Electrical Imbalances
Electrical imbalances are a common cause of electric motor overheating. These imbalances occur when there is an uneven distribution of electrical currents in the motor’s windings. Electrical imbalances can lead to increased resistive losses, which generate excessive heat and result in motor overheating. Let’s explore the factors that contribute to electrical imbalances and the preventive measures that can be taken.
a. Unbalanced Power Supply: An unbalanced power supply can cause uneven currents to flow through the motor’s windings, leading to electrical imbalances. This can occur when there are variations in voltage or phase imbalances in the electrical system feeding the motor. Factors such as unequal distribution of loads, faulty connections, or faulty electrical components can cause power supply imbalances.
b. Uneven Coil Winding: During the manufacturing process, if the coils within the motor are not wound properly or if there are inconsistencies in the number of turns or wire size, it can result in electrical imbalances. The uneven distribution of currents within the motor’s windings leads to increased resistive losses and, consequently, motor overheating.
c. Faulty Connections: Poor or faulty connections within the motor’s electrical circuit can contribute to electrical imbalances. Loose or corroded connections cause increased resistance, which leads to uneven current flow. This imbalance in currents generates excess heat and can result in motor overheating.
To prevent electrical imbalances and minimize the risk of motor overheating, consider the following preventive measures:
a. Balanced Power Supply: Ensure that the power supply feeding the motor is balanced. This involves maintaining consistent voltage levels and phase balance across all three phases. Regularly monitor the power supply and address any abnormalities promptly to minimize the risk of electrical imbalances.
b. Proper Coil Winding: During the motor’s manufacturing process or when rewinding the coils, ensure that the winding is done correctly. Follow the manufacturer’s guidelines and standards to ensure consistent and uniform coil winding. This reduces the chances of electrical imbalances and subsequent motor overheating.
c. Regular Maintenance: Implement a regular maintenance program that includes inspecting and tightening all electrical connections within the motor. Promptly address any loose or corroded connections to avoid unwanted resistances and electrical imbalances.
d. Use Surge Protection Devices: Install surge protection devices in the motor’s electrical circuit to protect against voltage spikes and fluctuations. Voltage surges can lead to electrical imbalances and cause motor overheating. Surge protection devices help to stabilize the voltage and protect the motor from potential damage.
e. Conduct Regular Electrical Testing: Regularly conduct electrical testing, such as measuring voltages and currents, to identify any imbalances or abnormalities in the motor’s electrical system. Test the motor’s insulation resistance to detect any deterioration that could lead to electrical imbalances.
By implementing these preventive measures, individuals can minimize the risk of electrical imbalances and reduce the likelihood of motor overheating. Maintaining a balanced and efficient electrical system ensures the optimal performance and longevity of the electric motor.
Poor Maintenance
Poor maintenance is a significant contributor to electric motor overheating. Inadequate or neglected maintenance practices can lead to various issues within the motor, including increased friction, insulation breakdown, and compromised cooling mechanisms. These issues can result in excessive heat generation and eventual motor overheating. Let’s explore the factors related to poor maintenance and the preventive measures that can be taken.
a. Lack of Lubrication: Proper lubrication is essential for reducing friction and heat generation within the motor. Without adequate lubrication, the motor’s moving parts, such as bearings and shafts, experience increased friction, leading to overheating. Regularly lubricate the motor’s bearings and other components as per the manufacturer’s guidelines to ensure smooth operation.
b. Dirt and Debris Buildup: Over time, dirt, dust, and debris can accumulate within the motor, obstructing airflow and impeding cooling. This buildup restricts the motor’s ability to dissipate heat, resulting in overheating. Regularly clean the motor’s exterior and internal components to prevent dirt and debris buildup.
c. Worn-out Components: Over prolonged use, various components within the motor can become worn-out or damaged. These components, such as belts, gears, or brushes, contribute to increased friction and heat generation. Periodically inspect the motor’s components and replace any worn-out or damaged parts promptly to prevent overheating.
d. Loose Connections: Loose electrical connections within the motor’s circuit can create resistance and lead to excessive heat generation. Poorly connected wires or cables can cause overheating and potentially result in electrical imbalances. Regularly inspect and tighten any loose connections to ensure a secure and efficient electrical circuit.
e. Inadequate Ventilation: Inadequate ventilation can hinder the motor’s cooling capability. Motors require proper airflow to dissipate heat effectively. If the motor is located in a confined space or an enclosure with limited airflow, heat buildup becomes a significant concern. Ensure that the motor is installed in an area with sufficient ventilation or use external cooling fans to promote airflow.
To prevent motor overheating due to poor maintenance, consider the following preventive measures:
a. Establish a Maintenance Schedule: Create a regular maintenance schedule that includes tasks such as lubrication, cleaning, and component inspection. Adhere to this schedule to ensure that maintenance activities are performed at appropriate intervals.
b. Follow Manufacturer Guidelines: Refer to the manufacturer’s guidelines and recommendations regarding maintenance practices for the specific motor. Follow these guidelines for lubrication, cleaning, and other maintenance procedures to ensure optimal motor performance.
c. Conduct Regular Inspections: Periodically inspect the motor’s components, including bearings, belts, electrical connections, and cooling mechanisms. Identify any signs of wear, damage, or loose connections and take immediate corrective action to prevent overheating.
d. Clean Regularly: Clean the motor’s exterior surfaces and internal components to remove dirt, dust, and debris that can obstruct airflow and hinder cooling. Use appropriate cleaning methods and products as recommended by the manufacturer.
e. Train Personnel: Provide appropriate training to personnel responsible for motor maintenance. Ensure they are familiar with proper maintenance procedures, safety protocols, and the importance of preventive measures. Well-trained personnel can carry out maintenance tasks effectively, minimizing the risk of motor overheating.
By implementing these preventive measures and maintaining a proactive maintenance approach, individuals can significantly reduce the risk of electric motor overheating due to poor maintenance practices. Regular maintenance not only extends the motor’s lifespan but also ensures optimal performance and energy efficiency while minimizing the chances of costly repairs or replacements.
Environmental Factors
Environmental factors can significantly impact the performance and efficiency of electric motors, leading to overheating if not properly addressed. Extreme temperatures, high levels of dust or dirt, humidity, and corrosive atmospheres can all contribute to motor overheating. Understanding and mitigating the effects of these environmental factors are essential to prevent motor overheating. Let’s explore the common environmental factors and the preventive measures that can be taken.
a. High Ambient Temperatures: Operating electric motors in high-temperature environments can strain the motor’s cooling capabilities and lead to overheating. It is important to consider the motor’s temperature rating and ensure that it is not exceeded. When possible, provide additional cooling measures such as increased ventilation, the use of external fans, or implementing air conditioning systems to maintain a suitable operating temperature.
b. Excessive Dust or Dirt: Dust and dirt can accumulate on the motor’s surfaces and cooling mechanisms, obstructing proper airflow and heat dissipation. This buildup can increase heat retention and result in motor overheating. Regularly clean the motor and its surrounding areas to remove any dust or dirt that may impact cooling efficiency.
c. Humidity: High humidity levels can affect the motor’s insulation properties, leading to moisture absorption and potential insulation breakdown. This can result in reduced motor performance and increased heat generation. Utilize proper sealing techniques, such as protective enclosures or seals, to minimize the effects of humidity. Additionally, ensure adequate ventilation to prevent moisture buildup.
d. Corrosive Atmospheres: Exposure to corrosive substances or gases can cause damage to the motor’s components, including corrosion of electrical connections and degradation of insulation materials. Corrosion can lead to increased resistance, electrical imbalances, and overheating. Place the motor in an environment that is free from corrosive substances or use protective coatings to shield the motor from corrosive atmospheres.
e. Altitude: Operating at high altitudes can impact motor performance and cooling capabilities. At higher elevations, the air density decreases, reducing the effectiveness of natural cooling mechanisms. This can lead to increased temperatures and decreased cooling efficiency. Consult the motor manufacturer’s guidelines and consider implementing additional cooling measures, such as fans or liquid cooling, when operating at higher altitudes.
To prevent motor overheating caused by environmental factors, consider the following preventive measures:
a. Regular Inspection and Cleaning: Routinely inspect the motor and its surroundings for dust, dirt, or other debris that may hinder cooling. Clean the motor and its cooling mechanisms to ensure proper airflow and heat dissipation.
b. Adequate Ventilation: Ensure that the motor is installed in an area with sufficient ventilation to facilitate proper cooling. Utilize external fans or ventilation systems if necessary to enhance airflow and heat dissipation.
c. Protective Enclosures: Utilize protective enclosures to shield the motor from environmental factors such as dust, humidity, or corrosive substances. These enclosures provide an additional layer of protection and maintain a controlled environment for the motor.
d. Temperature Monitoring: Implement temperature monitoring systems to continuously monitor the motor’s operating temperature. Set up alerts or alarms to notify when temperatures approach or exceed safe limits to allow for prompt action.
e. Follow Manufacturer Guidelines: Adhere to the manufacturer’s guidelines regarding temperature tolerances, environmental conditions, and maintenance recommendations. Manufacturers typically provide specific information on how to handle environmental factors and ensure optimal motor performance.
By implementing these preventive measures, individuals can minimize the impact of environmental factors on motor overheating. Proper consideration, monitoring, and control of the environment surrounding the motor will help ensure its longevity, efficiency, and reliability.
Regular maintenance, such as cleaning and lubricating the motor, can help prevent overheating. Check for any obstructions or excessive load on the motor that may be causing it to overheat.
Preventive Measures to Avoid Electric Motor Overheating
Preventing electric motor overheating is essential to ensure optimal performance, prolong the motor’s lifespan, and minimize the risk of costly repairs or replacements. By implementing preventive measures, individuals can address common causes of motor overheating and maintain efficient motor operation. Let’s explore some effective preventive measures:
1. Regular Inspections: Conduct regular inspections of the motor to identify any potential issues or signs of overheating. Inspect components, connections, and cooling systems for wear, damage, or blockages. Promptly address any abnormalities or necessary repairs.
2. Proper Ventilation: Ensure that the motor is installed in a well-ventilated area. Proper airflow is crucial for heat dissipation. Clear any blockages in vents or cooling mechanisms and consider using external fans or ventilation systems to enhance cooling efficiency.
3. Correct Wiring and Connections: Verify that the motor’s wiring and connections are correct and secure. Loose or faulty connections can lead to excessive resistance, imbalances, and increased heat generation. Regularly inspect and tighten connections as needed.
4. Routine Maintenance: Develop and adhere to a regular maintenance schedule to keep the motor in optimal condition. This includes tasks such as lubrication, cleaning, and component inspections. Follow the manufacturer’s guidelines for maintenance practices and intervals.
5. Temperature Monitoring: Implement temperature monitoring systems to continuously monitor the motor’s operating temperature. Set up alarms or alerts to notify when temperatures approach or exceed safe limits. This allows for prompt action to prevent overheating.
6. Proper Load Management: Avoid overloading the motor by ensuring that it is appropriately sized for the load it needs to handle. Distribute loads among multiple motors or equipment when possible. Implement load management strategies such as load sharing or shedding to optimize overall system performance and prevent overloading.
7. Environmental Considerations: Take into account environmental factors such as high ambient temperatures, dust, humidity, or corrosive atmospheres. Implement measures to mitigate the effects of these factors, such as providing additional cooling, using protective enclosures, or sealing mechanisms.
8. Training and Education: Provide training to personnel responsible for motor operation and maintenance. Ensure they are knowledgeable about proper maintenance procedures, safety protocols, and the importance of preventive measures. Well-trained personnel can detect issues early and implement necessary preventive actions.
9. Timely Repairs and Replacements: Address any detected issues or potential problems promptly. Repair or replace worn-out or damaged components to prevent further deterioration and mitigate the risk of motor overheating.
10. Consult Manufacturer Guidelines: Refer to the motor manufacturer’s guidelines and recommendations for specific preventive measures tailored to the motor model. Manufacturers provide valuable information regarding maintenance, operating conditions, and temperature tolerances.
By implementing these preventive measures, individuals can significantly reduce the risk of electric motor overheating. A proactive approach to motor maintenance and addressing potential issues promptly will ensure the motor’s optimal performance, longevity, and reliability. Regular inspections, proper ventilation, correct wiring, routine maintenance, temperature monitoring, load management, environmental considerations, training, and adherence to manufacturer guidelines are key components of comprehensive preventive measures.
Read more: What Is An Electric Motor Capacitor?
Regular Inspections
Regular inspections are crucial to prevent electric motor overheating. Through inspections, potential issues and signs of overheating can be identified early, allowing for prompt action to be taken. Inspecting the motor components, connections, and cooling systems helps to ensure that the motor operates efficiently and reduces the risk of overheating. Let’s explore the importance of regular inspections and the key areas to focus on during these inspections.
During inspections, the following areas should be carefully examined:
a. Motor Components: Inspect the motor’s components, such as the rotor, stator, bearings, and shaft, for signs of wear or damage. Look for any loose or misaligned parts that may cause friction, leading to increased heat generation. Additionally, inspect the motor’s cooling mechanisms, including fans, fins, and vents, to ensure they are clean, unobstructed, and functioning properly.
b. Electrical Connections: Check all electrical connections within the motor’s circuit, including terminals, cables, and connections to the power supply. Loose or faulty connections can result in increased resistance and excessive heat generation. Ensure that connections are tight, free from corrosion, and properly insulated.
c. Insulation Integrity: Inspect the motor’s insulation system, including the insulation on wires, coils, and windings. Look for any signs of damage, deterioration, or moisture intrusion that may lead to insulation breakdown and subsequent overheating. Conduct insulation resistance tests to assess the integrity of the insulation system.
d. Lubrication Levels: Check the lubrication levels of the motor’s bearings or moving parts. Inadequate lubrication can increase friction and heat generation. Ensure that the appropriate type and amount of lubricant are being used as per the manufacturer’s recommendations.
e. Temperature Monitoring: Implement temperature monitoring systems to continuously monitor the motor’s operating temperature. This can be done through the use of thermal sensors or infrared thermography. Regularly assess temperature readings to identify any abnormal temperature spikes or trends that may indicate potential overheating.
Regular inspections provide multiple benefits in preventing motor overheating:
1. Early Detection of Issues: Inspections allow for the early detection of any signs of wear, damage, or abnormalities that may lead to overheating. Prompt action can then be taken to address these issues, preventing further damage and reducing the risk of motor failure.
2. Maintenance Planning: Inspections help in planning and scheduling maintenance activities effectively. By identifying potential issues during inspections, appropriate maintenance tasks, such as lubrication, cleaning, or component replacement, can be organized in a timely manner, ensuring optimal motor performance.
3. Performance Optimization: Regular inspections ensure that the motor is operating at its best. By identifying and addressing any mechanical or electrical issues, inspections contribute to maintaining the motor’s efficiency, reducing energy consumption, and minimizing the risk of overheating.
4. Prolonged Motor Life: Proactively inspecting the motor allows for the detection and resolution of issues before they escalate, leading to a longer motor lifespan. Regular inspections and maintenance practices extend the motor’s operational life, reducing the need for premature replacements.
To conduct effective inspections:
– Follow manufacturer recommendations: Refer to the manufacturer’s guidelines and recommendations for inspection procedures, intervals, and specific areas of focus. Manufacturers provide valuable insights into the motor’s design and potential areas of concern.
– Keep detailed records: Maintain comprehensive records of each inspection, including dates, findings, and actions taken. This documentation assists in tracking the motor’s condition over time and establishes a maintenance history for future reference.
– Engage qualified personnel: Inspections may require specialized knowledge and skills. Ensure that inspections are performed by qualified personnel with expertise in motor maintenance and diagnostics.
Through regular inspections, potential issues can be identified and addressed proactively. This helps to maintain optimal motor performance, minimize the risk of overheating, and prolong the motor’s lifespan. Inspections should be conducted at appropriate intervals and in accordance with the manufacturer’s recommendations to ensure the effectiveness of preventive measures.
Proper Ventilation
Proper ventilation is essential for preventing electric motor overheating. Adequate airflow helps dissipate the heat generated during motor operation, keeping the motor within its optimal temperature range. Without proper ventilation, heat can build up, leading to decreased motor efficiency, insulation breakdown, and potential motor failure. Let’s explore the importance of proper ventilation and key considerations to ensure effective heat dissipation.
1. Clear Obstructions: Ensure that the motor’s vents, cooling fins, and other cooling mechanisms are free from obstructions. Blockages caused by dust, debris, or other objects restrict airflow and impede heat dissipation. Regularly inspect and clean these components to maintain unobstructed ventilation paths.
2. Positioning and Location: Place the motor in a properly ventilated area. Consider the motor’s surroundings, including surrounding equipment, walls, or other structures that can hinder airflow. Allow sufficient space around the motor for airflow, ensuring that there is enough room for ambient air to circulate.
3. Natural Ventilation: Utilize natural ventilation whenever possible. Position the motor to take advantage of ambient airflow, such as placing the motor near windows or open doors. Create openings or vents in the surrounding area to improve air circulation.
4. External Fans: Install external fans or cooling systems to enhance the ventilation and heat dissipation. These fans can supplement natural ventilation or compensate for insufficient airflow in the motor’s location. Ensure that the fans are properly positioned to direct airflow towards critical motor components.
5. Forced Air Cooling: Implement forced air cooling systems to actively circulate air around the motor. This can be achieved through the use of additional fans, blowers, or ducts that direct air over the motor’s surfaces. Forced air cooling is particularly beneficial in environments with limited natural ventilation.
6. Enclosures: Use protective enclosures that have vents or cooling fans to regulate the motor’s temperature. Enclosures can provide controlled ventilation, protecting the motor from dust, moisture, or other harmful substances while ensuring proper heat dissipation.
7. Temperature Monitoring: Implement temperature monitoring systems to continuously monitor the motor’s operating temperature. This allows for real-time assessment of the cooling effectiveness. If temperature thresholds are consistently exceeded, additional ventilation measures can be taken as needed.
8. Hot Spot Detection: In addition to monitoring the overall temperature, use infrared thermography or other techniques to identify hot spots within the motor. Hot spots indicate areas of localized heat buildup and can help pinpoint ventilation issues that require attention.
Proper ventilation offers several benefits:
– Heat Dissipation: Effective ventilation facilitates the dissipation of heat generated during motor operation, preventing the buildup of excessive temperatures and reducing the risk of overheating.
– Enhanced Efficiency: Optimal operating temperatures help maintain motor efficiency. By keeping the motor within its recommended temperature range, ventilation contributes to improved energy efficiency and reduced power consumption.
– Extended Lifespan: Adequate ventilation promotes optimal motor performance and reduces the strain on motor components. By minimizing heat-related stress, proper ventilation helps extend the motor’s operational life.
– Maintenance Simplification: By preventing overheating, proper ventilation reduces the need for extensive maintenance and repairs. This leads to cost savings and minimizes downtime associated with motor failures.
To achieve proper ventilation:
– Understand Motor Requirements: Consult the motor’s documentation or contact the manufacturer to determine specific ventilation requirements. These specifications may include recommended clearances, airflow rates, or specific cooling mechanisms.
– Regularly Inspect and Clean: Perform routine inspections to check for any obstructions, dust, or debris that may hinder ventilation. Clean vents, cooling fins, and other components regularly to maintain unrestricted airflow.
– Seek Professional Advice: Consult with qualified professionals or motor technicians to assess the ventilation needs of the motor and obtain guidance on appropriate ventilation measures.
By ensuring proper ventilation, individuals can mitigate the risk of electric motor overheating. Effective heat dissipation promotes optimal motor performance, extends the motor’s lifespan, and reduces the likelihood of costly repairs or replacements. Implementing preventive measures and maintaining a well-ventilated environment are key to maximizing the motor’s efficiency and minimizing the risk of overheating.
Correct Wiring and Connections
Proper wiring and connections are vital to prevent electric motor overheating. Faulty or incorrect wiring can lead to increased resistance, imbalances, and excessive heat generation within the motor’s electrical circuit. By ensuring correct wiring and secure connections, individuals can minimize the risk of overheating and improve the motor’s overall performance and reliability. Let’s explore the importance of correct wiring and connections, as well as key considerations for achieving optimal electrical connectivity.
1. Proper Wire Sizing: Use the appropriate wire size for the motor’s current rating and length of the wiring run. Undersized wires can cause voltage drops and increased resistance, leading to heat buildup. Refer to the manufacturer’s guidelines or consult an electrician to determine the correct wire gauge for the motor’s current requirements.
2. Use High-Quality Wiring Materials: Employ high-quality wires that are suitable for the application. Use wires with adequate insulation and that are rated for the voltage and temperature requirements of the motor. Quality wiring materials ensure reliable electrical conductivity and minimize the chances of issues such as insulation breakdown or short circuits.
3. Secure and Tight Connections: Ensure that all electrical connections within the motor’s circuit are secure and tight. Loose connections create resistance, which leads to increased heat generation. Regularly inspect connections, including terminals, cable connections, and power supply connections, and tighten them if necessary.
4. Follow Wiring Diagrams: Refer to wiring diagrams provided by the motor manufacturer. Wiring diagrams offer guidance on the correct connection points and configurations. Follow these diagrams precisely to ensure accurate and efficient electrical connectivity.
5. Check for Faulty or Damaged Wires: Regularly inspect the motor’s wiring for any signs of damage, wear, or deterioration. Look for frayed, cracked, or melted insulation, as this can lead to short circuits or electrical faults. Replace any faulty or damaged wires promptly to maintain proper electrical connectivity.
6. Verify Phase Connections: Ensure that the correct phases are connected to the motor according to the designated labels. Incorrect phase connections can result in electrical imbalances and lead to overheating. Validate the phase connections during installation and double-check when troubleshooting or performing maintenance.
7. Proper Grounding: Ground the motor appropriately to ensure electrical safety and minimize the risk of electrical faults. Follow local electrical codes and guidelines for grounding practices. Effective grounding also helps prevent voltage irregularities that can contribute to motor overheating.
8. Regular Inspections: Include regular inspections of the motor’s wiring and connections as part of a maintenance routine. Inspect for loose, damaged, or corroded wires and connections. Promptly address any issues identified during inspections.
By ensuring correct wiring and connections, individuals can reap several benefits:
– Improved Efficiency: Proper electrical connectivity minimizes resistance, which leads to more efficient power transmission. By reducing resistance, the motor operates with less heat generation and improves efficiency.
– Reduced Energy Loss: Correct wiring and connections minimize energy loss due to resistive losses. With efficient power transmission, energy wastage is reduced, resulting in cost savings over time.
– Enhanced Motor Performance: Proper electrical connectivity contributes to smoother motor operation, allowing the motor to function at its intended capacity. Improved performance leads to decreased wear and tear, longer lifespan, and reliable motor operation.
– Prevention of Overheating and Damage: By avoiding excessive resistance or imbalances caused by incorrect wiring or loose connections, the risk of motor overheating decreases significantly. Proactive measures ensure the motor remains within safe operating temperatures, preventing damage and premature motor failure.
To achieve correct wiring and connections:
– Consult Manufacturer Guidelines: Follow the manufacturer’s instructions and recommendations for wiring and connection specifications. The manufacturer provides specific guidelines to ensure optimal motor operation and prevent overheating.
– Engage Qualified Professionals: Seek assistance from qualified electricians or motor technicians who possess expertise in electrical connectivity. Qualified professionals can ensure that wiring and connections are executed correctly and in compliance with safety standards.
– Maintain Documentation: Create and maintain thorough documentation of the motor’s wiring details, including any modifications or repairs made over time. This documentation serves as a valuable reference for future inspections, troubleshooting, or maintenance activities.
Ensuring proper wiring and connections is vital in preventing overheating and optimizing the performance of electric motors. By maintaining correct electrical connectivity, individuals can mitigate the risk of overheating, improve motor efficiency, and enhance the reliability and lifespan of the motor.
Routine Maintenance
Routine maintenance is a key preventive measure to avoid electric motor overheating. Regularly inspecting and maintaining the motor ensures its optimal performance, minimizes the risk of issues such as excessive friction or wear, and extends the motor’s lifespan. This proactive approach helps prevent motor overheating and promotes efficient operation. Let’s explore the importance of routine maintenance and key aspects to consider for effective motor care.
1. Lubrication: Proper lubrication is crucial for minimizing friction and heat generation within the motor. Follow the manufacturer’s recommendations for the type and amount of lubricant to use. Regularly lubricate the motor’s bearings, shafts, and other moving parts as per the specified intervals to ensure smooth operation and reduce heat buildup.
2. Cleaning: Regularly clean the external surfaces of the motor to remove dust, dirt, and debris. Buildup on the motor’s surfaces can impede heat dissipation and contribute to overheating. Pay particular attention to cooling fins, vents, and other cooling mechanisms to maintain unobstructed airflow.
3. Component Inspection: Conduct regular inspections of motor components to identify any signs of wear, damage, or abnormalities that could lead to overheating. Inspect elements such as bearings, seals, belts, brushes, and electrical connections. Promptly replace or repair any worn-out or damaged components to maintain optimal motor performance.
4. Electrical Circuit Inspection: Inspect the motor’s electrical circuit, including wires, cables, terminals, and connections, for any signs of loose or corroded components. Loose connections can result in increased resistance and heat generation. Tighten connections, repair any faults, and ensure proper insulation to prevent overheating risks.
5. Bearing Maintenance: Bearings are critical components for proper motor operation. Regularly inspect bearings for wear, noise, or excessive play. Lubricate bearings as recommended by the manufacturer and replace them, if necessary, to avoid excessive friction and overheating.
6. Belt Maintenance: If the motor operates with belts, regularly inspect them for signs of wear, tension, and alignment. Loose or worn-out belts can create excessive friction and lead to overheating. Adjust or replace belts as needed to maintain proper tension and alignment.
7. Motor Alignment: Misaligned motors can cause increased friction, leading to overheating and reduced efficiency. Regularly check the motor’s alignment and adjust it as necessary to ensure proper alignment with the driven equipment. Proper alignment reduces strain on the motor and minimizes heat generation.
8. Thermal Protection: Install thermal protection devices, such as temperature sensors or protective relays, to monitor the motor’s operating temperature. These devices provide early warning signals or automatically shut down the motor if temperatures exceed safe limits, preventing potential overheating and damage.
9. Follow Manufacturer Guidelines: Adhere to the manufacturer’s maintenance guidelines and recommendations. Manufacturers provide specific instructions on maintenance activities, intervals, and techniques tailored to their motors. Consult the manufacturer’s documentation for comprehensive guidance on maintenance practices.
10. Recordkeeping: Maintain detailed records of all maintenance activities, including dates, inspections, repairs, and replacements. This documentation helps track the motor’s maintenance history and identify any patterns or recurring issues that may contribute to overheating risks.
By implementing routine maintenance practices:
– Early Detection: Regular maintenance allows for the early detection of potential issues before they lead to overheating or motor failure. Identifying and addressing problems early on helps prevent costly repairs or replacements.
– Improved Efficiency: Well-maintained motors operate more efficiently, minimizing energy wastage and reducing heat generation. Effective maintenance ensures the motor performs optimally, thus improving energy efficiency.
– Prolonged Motor Lifespan: Proper maintenance prevents excessive wear and tear, reducing the likelihood of premature motor failure. Regular inspections, lubrication, and component replacements extend the motor’s operational life.
– Cost Savings: Routine maintenance helps avoid unexpected breakdowns and the associated costs of emergency repairs or replacements. By investing in regular maintenance, individuals minimize overall maintenance expenses and downtime.
Developing a maintenance schedule and following it consistently is crucial for effective motor care. Adhere to manufacturer guidelines, conduct regular inspections, and perform necessary maintenance tasks to prevent overheating risks. By prioritizing routine maintenance, individuals can optimize motor performance, reduce the risk of overheating, and ensure the reliable operation of electric motors.
Temperature Monitoring
Temperature monitoring is a critical preventive measure to avoid electric motor overheating. Monitoring the motor’s operating temperature allows for real-time assessment and early detection of any potential overheating issues. By implementing effective temperature monitoring systems and strategies, individuals can take timely action to prevent motor failure, optimize performance, and ensure safe operation. Let’s explore the importance of temperature monitoring and key considerations for effective implementation.
1. Continuous Monitoring: Implement temperature monitoring systems that provide continuous monitoring of the motor’s operating temperature. These systems can use various techniques such as thermal sensors, infrared thermography, or digital temperature indicators. Continuous monitoring assists in identifying any abnormal temperature variations or trends that may indicate potential overheating.
2. Set Safe Temperature Limits: Establish safe temperature limits for the motor based on the manufacturer’s specifications. These limits typically represent the temperature range within which the motor can safely operate. Set up alarms or alerts to notify when temperatures approach or exceed these limits, allowing for prompt action to prevent overheating.
3. Thermocouples or RTDs: Install thermocouples or resistance temperature detectors (RTDs) at critical points on the motor to measure and monitor temperature accurately. Place these devices at locations prone to heat buildup, such as near bearings, windings, or other components that may experience increased temperatures during operation.
4. Data Logging: Utilize data logging systems to record temperature data over time. This provides valuable information for analyzing temperature trends and patterns, facilitating an understanding of the motor’s thermal behavior. Analyzing recorded temperature data allows for proactive decision-making and early detection of potential overheating risks.
5. Thermal Imaging: Implement thermal imaging or infrared thermography to visualize and evaluate the heat distribution across the motor’s surfaces. Thermal imaging helps identify hot spots or areas with higher temperatures that may indicate potential issues, such as insufficient cooling or abnormal heat generating components.
6. Regular Data Analysis: Regularly analyze temperature data collected from monitoring systems to identify any deviations or patterns that may indicate overheating risks. Establish trends and correlate temperature changes with motor performance to develop proactive maintenance strategies.
7. System Integration: Integrate temperature monitoring systems with supervisory control and data acquisition (SCADA) systems or other automation platforms. This allows for centralized monitoring and control of temperature data, enabling remote alerts and notifications for prompt response.
8. Maintenance Actions: Establish clear protocols and procedures for handling temperature alarms or alerts. Define steps to be taken in response to temperature deviations or overheating risks, such as interrupting operation, conducting inspections, or scheduling maintenance activities.
9. Calibration and Validation: Regularly calibrate and validate temperature monitoring devices to ensure accurate and reliable temperature measurements. Calibration ensures that temperature readings are precise and aligned with the established safe temperature limits.
10. Personnel Training: Train personnel responsible for monitoring and responding to temperature alerts. Ensure they are familiar with monitoring systems, data analysis techniques, and maintenance protocols. Trained personnel can effectively interpret temperature data and take appropriate actions to prevent motor overheating.
By implementing temperature monitoring:
– Early Detection: Continuous monitoring enables early detection of any temperature deviations, allowing for prompt action to prevent overheating and mitigate potential motor damage.
– Prevention of Catastrophic Failures: Timely identification of overheating risks helps to prevent catastrophic motor failures that can result in costly repairs and extended downtime due to motor replacement.
– Optimization of Maintenance: Temperature data analysis facilitates better understanding of motor behavior, allowing for optimized maintenance planning and resource allocation. Maintenance actions can be prioritized based on temperature trends and criticality.
– Enhanced Safety: Temperature monitoring contributes to the overall safety of motor operation. Monitoring systems provide real-time visibility into temperature variations, reducing the risk of unsafe operating conditions.
Implementing effective temperature monitoring systems and strategies ensures proactive management of motor temperatures, avoiding the detrimental effects of overheating. Continuous monitoring, safe temperature limits, data logging, thermal imaging, regular analysis, integration with SCADA systems, calibration, personnel training, and appropriate maintenance actions form a comprehensive approach to temperature monitoring. With these measures in place, individuals can optimize motor performance, prevent motor failure, and maintain a safe operating environment.
Conclusion
Electric motor overheating can lead to a range of issues, from reduced efficiency and performance to motor failure and safety hazards. Preventing motor overheating is crucial to ensure optimal motor operation, longevity, and cost savings. By understanding the common causes of motor overheating and implementing preventive measures, individuals can mitigate the risks and maintain reliable motor performance.
Throughout this article, we have explored various factors that contribute to motor overheating. Overloading, insufficient cooling, electrical imbalances, poor maintenance, and environmental factors all play a role in increasing heat generation within motors. However, with proactive measures, these causes can be addressed and minimized.
Preventive measures such as regular inspections, proper ventilation, correct wiring and connections, routine maintenance, temperature monitoring, and adherence to manufacturer guidelines are essential. Regular inspections help identify potential issues, allowing for timely repairs or replacements. Proper ventilation ensures effective heat dissipation, while correct wiring and connections minimize resistance and imbalances. Routine maintenance, including lubrication, cleaning, and component inspections, keeps the motor in optimal condition. Temperature monitoring allows for real-time assessment and early detection of overheating risks, enabling prompt action.
Implementing these preventive measures offers numerous benefits. It not only prevents motor overheating but also improves motor efficiency, extends motor lifespan, and reduces the risk of costly repairs or replacements. Routine maintenance practices, data analysis from temperature monitoring, and adherence to manufacturer guidelines enhance motor performance, safety, and energy efficiency.
In conclusion, preventing electric motor overheating requires a holistic approach that combines regular maintenance, effective monitoring, and adherence to best practices. By implementing the preventive measures outlined in this article, individuals can ensure the smooth and reliable operation of their electric motors, minimizing the risk of overheating and maximizing motor longevity and performance. Taking proactive steps today will result in more efficient operation, reduced downtime, and cost savings in the long run.
Frequently Asked Questions about What Causes An Electric Motor To Overheat
Was this page helpful?
At Storables.com, we guarantee accurate and reliable information. Our content, validated by Expert Board Contributors, is crafted following stringent Editorial Policies. We're committed to providing you with well-researched, expert-backed insights for all your informational needs.
0 thoughts on “What Causes An Electric Motor To Overheat”