Home>Articles>How To Reverse The Flow Of Current Through An Electric Motor?
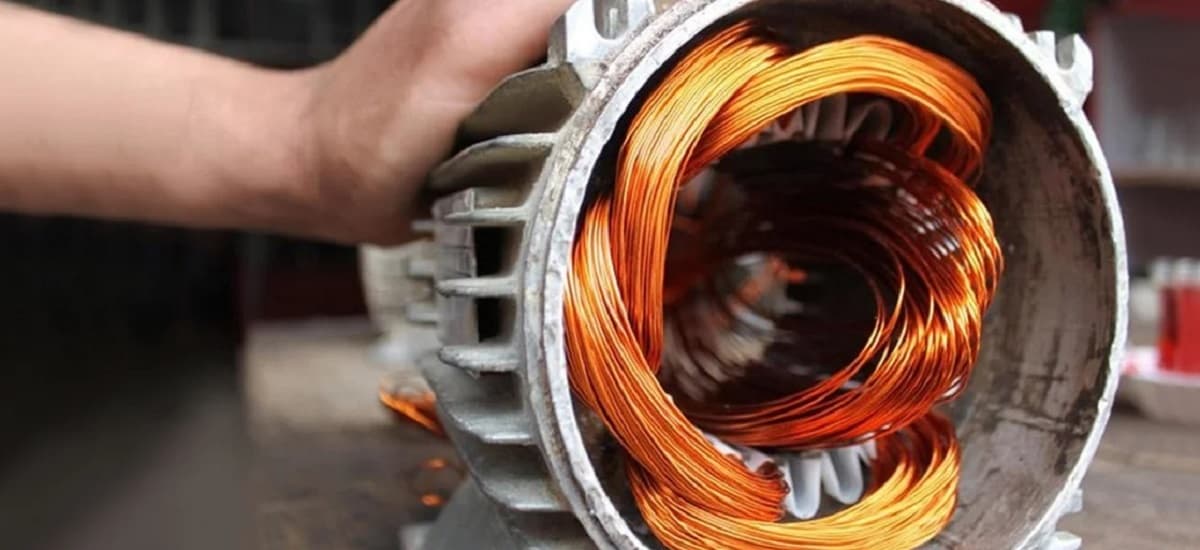
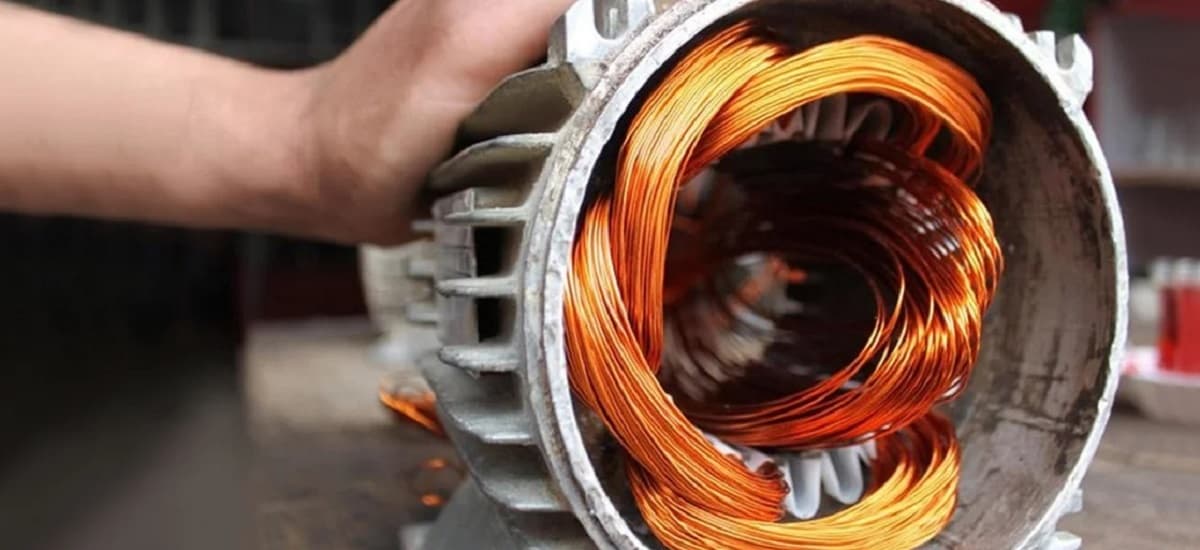
Articles
How To Reverse The Flow Of Current Through An Electric Motor?
Modified: December 7, 2023
"Discover the power of brush and battery in reversing the flow of current through an electric motor. Read our articles to learn about armatures and commutators."
(Many of the links in this article redirect to a specific reviewed product. Your purchase of these products through affiliate links helps to generate commission for Storables.com, at no extra cost. Learn more)
Brush
In an electric motor, the brush plays a significant role in controlling the flow of current through the motor’s armature. The brush consists of carbon or graphite material and is positioned on the commutator, which is a segmented metal cylinder.
The primary function of the brush is to make contact with the commutator segments and transfer electrical current from the power source to the armature. As the commutator rotates, the brush maintains constant contact with the segments, ensuring a continuous flow of electricity.
The brush not only conducts electricity but also acts as a mechanical support for the armature. It exerts pressure on the commutator, providing stability and maintaining proper alignment between the two components.
To ensure effective performance, brushes are made from a material that has a lower resistance than the commutator. This helps to minimize the energy loss and heat generated during the operation of the electric motor.
As the brush rubs against the commutator, friction and wear can occur. Regular maintenance and periodic replacement of brushes are necessary to ensure the smooth functioning of the motor. Over time, the brush material may wear down, affecting the electrical contact and performance of the motor.
Some modern electric motors have adopted brushless technology which eliminates the need for brushes. Instead, these motors use electronic circuits to control the flow of current in the motor. Brushless motors offer advantages such as improved efficiency, higher power output, and reduced maintenance.
In summary, the brush in an electric motor is an essential component that enables the transfer of electrical current from the power source to the motor’s armature. It provides mechanical support, maintains proper alignment, and ensures a continuous flow of electricity. Regular maintenance and periodic replacement of brushes are crucial for the optimal performance of the motor.
Key Takeaways:
- The brush in an electric motor is essential for transferring current, providing mechanical support, and ensuring continuous electricity flow. Regular maintenance and periodic replacement are crucial for optimal motor performance.
- The commutator plays a vital role in reversing current flow, enabling continuous motor rotation. Regular maintenance and advancements in brushless technology contribute to improved motor efficiency and reduced maintenance requirements.
Read more: How To Wire A Reversible Electric Motor
Battery
A battery is a crucial component in an electric motor as it serves as the power source for the motor to function. It provides the necessary electrical energy required to drive the motor and enable its operations.
The battery consists of one or more electrochemical cells that convert chemical energy into electrical energy. Each cell is composed of a positive electrode (cathode), a negative electrode (anode), and an electrolyte that facilitates the movement of ions between the electrodes.
When a load, such as an electric motor, is connected to the battery, a chemical reaction occurs within the cells. This reaction causes the transfer of electrons from the anode to the cathode through the external circuit, resulting in the flow of electrical current.
The voltage of the battery determines the intensity of the current flowing through the motor. Different types of electric motors require different voltage levels, and it is essential to match the battery’s voltage to the motor’s specifications to ensure optimal performance.
Rechargeable batteries, such as lithium-ion or nickel-cadmium batteries, are commonly used in electric motors. These batteries can be recharged by applying an external electrical current that reverses the chemical reaction and restores the energy storage capacity of the battery.
Proper maintenance and care of the battery are necessary to ensure its longevity and efficiency. Regular charging, avoiding overcharging or deep discharging, and storing the battery in appropriate conditions are crucial practices.
In modern electric motor applications, advancements in battery technology have led to the development of high-performance and long-lasting batteries. These advancements have significantly contributed to the widespread adoption of electric motors in various industries, including automotive, aerospace, and robotics.
In summary, the battery is a vital component in an electric motor, providing the electrical energy required to drive the motor. It converts chemical energy into electrical energy, and proper management and care of the battery are essential for optimal performance. Advancements in battery technology have revolutionized the capabilities and applications of electric motors.
The commutator is the part of an electric motor that reverses the flow of current through the armature, causing the motor to change direction.
Armature
The armature is a critical component in an electric motor. It is the rotating part of the motor that converts electrical energy into mechanical energy and drives the motor’s output shaft.
The armature is typically made of laminated iron cores that are stacked together to form a cylindrical shape. The laminations help reduce energy losses by reducing eddy currents that can be generated in a solid iron core.
Wrapped around the armature are coils of wire, known as the armature winding. These coils are connected to the commutator and provide a path for the flow of electrical current. When current flows through the armature winding, a magnetic field is created, which interacts with the motor’s permanent magnets or external field coils to produce a rotational force.
The armature winding is designed to generate a magnetic field that changes direction as the motor rotates. This changing magnetic field causes the armature to rotate continuously, converting electrical energy into mechanical energy.
The number and arrangement of the armature windings vary depending on the motor’s design and intended application. Motors with multiple armature windings may have different speed or torque characteristics, allowing for greater flexibility in motor performance.
The armature brushes make contact with the commutator segments, transferring electrical current to the armature winding. As the commutator rotates, it constantly switches the electrical connections to the armature windings, allowing for continuous rotation of the armature.
The armature’s rotational speed is determined by the motor’s voltage and the load placed on the motor. As the load on the motor increases, the armature may slow down, resulting in a decrease in motor speed and torque.
In high-power electric motors, cooling systems such as fans or liquid cooling may be utilized to prevent overheating of the armature, as excessive heat can degrade the motor’s performance and longevity.
Overall, the armature is a crucial component in an electric motor, responsible for converting electrical energy into mechanical energy. Its design, winding configuration, and connection to the commutator play significant roles in the motor’s performance and efficiency.
Commutator
The commutator is a crucial component in an electric motor, specifically in motors that use brushes and a rotating armature. It plays a significant role in reversing the flow of current through the motor’s armature, enabling the motor to rotate continuously.
The commutator consists of a segmented metal cylinder made of copper or copper alloys. These segments are insulated from each other and attached to the shaft of the motor. The number of segments on the commutator corresponds to the number of armature windings in the motor.
One of the primary functions of the commutator is to switch the electrical connections between the armature and the power source through the brushes. As the armature rotates, the brushes maintain contact with the commutator segments, and the commutator changes the connection between the armature windings and the power supply, ensuring a continuous flow of current.
When a current is applied to the armature windings, a magnetic field is generated, which interacts with the motor’s permanent magnets or external field coils. This interaction creates a rotational force, causing the armature to rotate. The commutator’s role is crucial in reversing the current’s direction within the armature windings during each rotation, ensuring that the force applied to the armature remains constant and the motor continues to rotate smoothly.
Due to the mechanical nature of the armature brushes rubbing against the commutator, friction and wear can occur over time. Regular maintenance and monitoring of the commutator’s condition are necessary to ensure optimal motor performance. If the commutator becomes worn or damaged, it may need to be repaired or replaced to maintain proper electrical contact and efficient operation.
In modern motors, advancements in brushless technology have eliminated the need for a commutator. These motors use electronic circuits to control the direction and timing of the current flow, further improving motor efficiency and reducing maintenance requirements.
In summary, the commutator is a vital component in electric motors that use brushes and a rotating armature. It switches the electrical connections between the armature windings and the power supply, allowing for a continuous flow of current and enabling the motor to rotate continuously. Regular maintenance and monitoring of the commutator are necessary for optimal motor performance and longevity.
Frequently Asked Questions about How To Reverse The Flow Of Current Through An Electric Motor?
Was this page helpful?
At Storables.com, we guarantee accurate and reliable information. Our content, validated by Expert Board Contributors, is crafted following stringent Editorial Policies. We're committed to providing you with well-researched, expert-backed insights for all your informational needs.
0 thoughts on “How To Reverse The Flow Of Current Through An Electric Motor?”